Ultrasonic cleaners are rapidly emerging from specialized industrial and medical settings into the broader consumer consciousness, offering a powerful and precise method for tackling challenging cleaning tasks. These advanced devices utilize high-frequency sound waves within a liquid bath to meticulously dislodge contaminants from a vast array of items, particularly those with intricate surfaces.
While primarily known for cleaning smaller objects such as jewelry, medical and dental instruments, electronics, and various industrial components, larger systems are also available for more substantial cleaning needs.
Contact us!
The growing availability of smaller, more affordable units for home use, for applications like jewelry care, signals a broader trend: a desire among consumers for professional-level cleaning results that go beyond traditional methods. This shift indicates an increasing appreciation for the effectiveness and precision that advanced cleaning technologies can offer in everyday life.
The Science of Sparkle: How Ultrasonic Cleaning Works
The magic behind ultrasonic cleaning lies in a fascinating interplay of physics and chemistry, primarily driven by high-frequency sound waves and a phenomenon called cavitation.
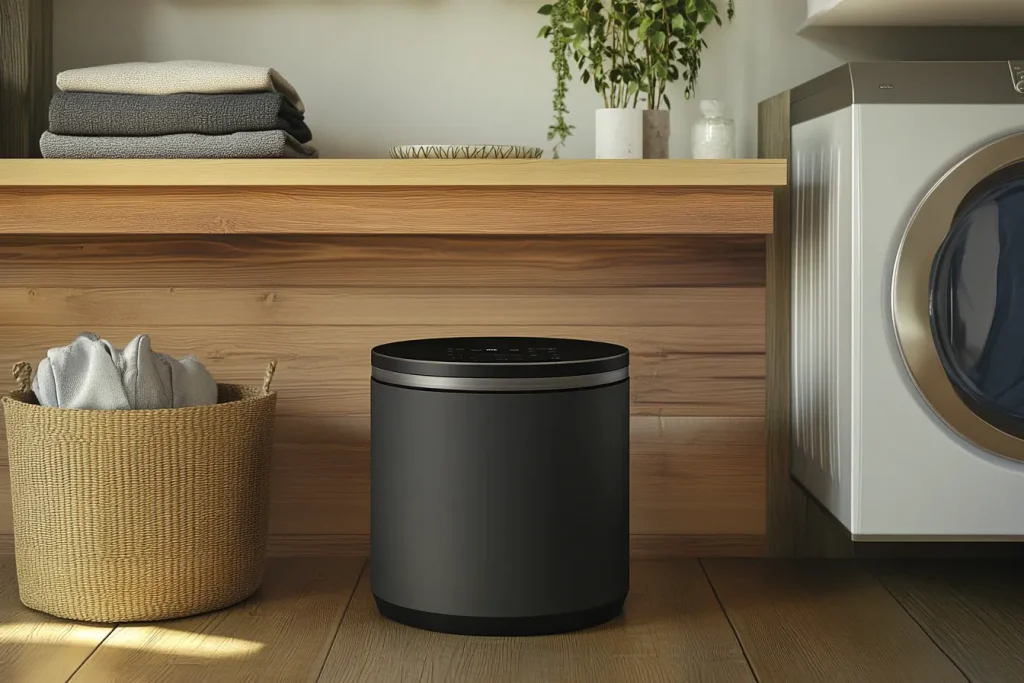
Demystifying High-Frequency Sound Waves
At its core, ultrasonic cleaning employs sound waves at frequencies typically ranging from 20 to 40 kilohertz (kHz), well above the range of human hearing, which is generally between 20 Hertz (Hz) and 20,000 Hz (or 20 kHz). These potent sound waves are not just any sound; they are meticulously generated by components called transducers.
These transducers are marvels of material science, converting electrical energy supplied by the cleaner’s generator into high-frequency mechanical vibrations. As these vibrations propagate through the cleaning liquid held within the machine’s tank, they create rapidly alternating cycles of high and low pressure. It’s these pressure changes that set the stage for the primary cleaning action.
Cavitation Explained: The Power of Microscopic Bubbles
The true workhorse of ultrasonic cleaning is a process known as cavitation. As the sound waves create those cycles of high and low pressure within the cleaning solution, something remarkable happens. During the low-pressure phase (also called the rarefaction cycle), the liquid is effectively ‘torn apart’ at a microscopic level, leading to the formation of millions of tiny ‘voids’ or partial vacuum bubbles. These are not ordinary air bubbles but are filled with vapor from the surrounding liquid or a near vacuum.
When the subsequent high-pressure phase (compression cycle) of the sound wave arrives, these microscopic bubbles become unstable and collapse, or “implode,” with incredible force. This implosion is the heart of cavitation. Despite their minuscule size, the collapse of these bubbles generates immense localized energy.
Temperatures at the point of implosion can reach an astonishing 5,000 Kelvin (K), and pressures can spike to around 135 Megapascals (MPa). However, because these events are so tiny and short-lived, they do no more than powerfully clean the surfaces they encounter, without causing damage to the underlying material when parameters are correctly set.
How Contaminants are Gently Yet Effectively Dislodged
The violent implosion of these cavitation bubbles creates a highly effective scrubbing action. Think of it as millions of microscopic, high-energy jets bombarding the surface of the item being cleaned. This intense agitation produces strong forces that dislodge and carry away a wide variety of contaminants, including dirt, oils, grease, rust, pigments, fingerprints, and even biological matter.
A key advantage of this process is its ability to penetrate and clean areas that are virtually impossible to reach with manual scrubbing or other conventional cleaning methods. This includes blind holes, intricate crevices, complex internal passages, and the spaces between tightly packed components. The cleaning action is pervasive, reaching every part of the object submerged in the solution.
The frequency of the ultrasonic waves plays a critical role in the nature of the cleaning. Higher frequencies tend to produce smaller, more numerous cavitation bubbles. These smaller bubbles are less aggressive individually but can penetrate finer, more intricate details and are generally gentler on delicate surfaces. For instance, frequencies in the 80-130 kHz range are often used for cleaning highly sensitive microelectronics or delicate jewelry.
Conversely, lower frequencies, such as 20-25 kHz or 27-40 kHz, generate larger, more powerful cavitation bubbles. This makes them more suitable for removing coarse, tenacious contaminants from robust items like large automotive parts or heavy industrial components.
Thus, the choice of frequency is not arbitrary; it’s a fundamental operational parameter that must be matched to the specific cleaning task, the type of contamination, and the sensitivity of the item being cleaned to achieve optimal results without causing damage. This understanding allows users to “dial in” the right level of cleaning aggressiveness and precision.
Furthermore, the effectiveness of ultrasonic cleaning stems from its “no-touch” power. Unlike manual methods that rely on brushes, cloths, or abrasive compounds, the cleaning is performed by the energy of the imploding bubbles.
This non-abrasive nature, when combined with appropriate frequencies and solutions, is particularly beneficial for delicate items or those with complex geometries where physical scrubbing could cause wear, scratches, or miss hard-to-reach spots. This method not only enhances cleaning thoroughness but also reduces the risk of operator-induced damage and ensures more consistent cleaning outcomes.
Inside the Machine: Key Components of an Ultrasonic Cleaner
An ultrasonic cleaner might seem like a simple box, but it’s a sophisticated system where several key components work in concert to deliver its powerful cleaning action. Understanding these parts and their roles is crucial to appreciating how the technology functions and how to use it effectively.
- Ultrasonic Generator: This is the brain and powerhouse of the system. The generator takes standard AC electrical energy from a wall outlet and transforms it into a high-frequency, high-voltage electrical signal or series of pulses. This specialized electrical output is precisely what’s needed to energize the transducers. More advanced generators, particularly in industrial settings, offer greater control over the cleaning process. They might include features like power intensity control, allowing the user to adjust the ultrasonic energy output, and “sweep frequency”. Sweep frequency continuously and slightly varies the ultrasonic frequency around a central point. This helps to create a more uniform cavitation field throughout the tank, eliminating “dead spots” (areas of low cavitation activity) and “hot spots” (areas of intense activity), thereby ensuring more consistent and even cleaning across all surfaces of the items. Some generators also support simultaneous multi-frequency operation for enhanced versatility.
- Transducers: These are the heart of the ultrasonic action, responsible for converting the electrical energy supplied by the generator into mechanical vibrations – the high-frequency sound waves. Most modern transducers are made from piezoelectric materials, such as lead zirconate titanate (PZT) or barium titanate. Piezoelectric materials have the unique property of changing shape (expanding and contracting) when an electrical voltage is applied to them. When the generator sends its high-frequency electrical signal to the transducers, they vibrate rapidly, causing the surface they are attached to (usually the tank bottom or sides) to vibrate as well. This vibration is then transmitted into the cleaning liquid, creating the ultrasonic waves. Transducers can be directly bonded to the cleaning tank, typically on the bottom or, for deeper or specially shaped tanks, on the sides. Alternatively, for very large tanks, custom setups, or retrofitting existing tanks, transducers can be housed in immersible stainless-steel containers that are placed directly into the cleaning solution. The number, placement, and type of transducers significantly impact the cleaning efficiency and uniformity.
- Tank: The tank is the container that holds the cleaning solution and the items to be cleaned. It needs to be robust enough to withstand the constant vibrations and the chemical nature of various cleaning solutions. For this reason, tanks are almost universally made from stainless steel, which offers good durability, corrosion resistance, and is relatively inert to most cleaning chemistries. The thickness and polish of the stainless steel can also contribute to the tank’s stability and the efficiency of sound wave transmission. Tank size (length, width, depth) and overall volume are critical design considerations, as they dictate the size and quantity of parts that can be cleaned at one time. Some tanks incorporate design features like coved corners for easier cleaning or V-shaped bottoms to help collect debris away from the transducer surfaces and facilitate draining.
- Cleaning Basket/Rack: This is a seemingly simple but essential accessory. The primary purpose of the basket or rack is to suspend the items being cleaned within the solution, preventing them from resting directly on the bottom of the tank. Direct contact with the tank bottom is detrimental for several reasons: it can dampen the ultrasonic vibrations, leading to poor cleaning on the contact surfaces; it can cause items to scratch or abrade against the tank, potentially damaging both the item and the tank surface; and over time, the concentrated vibrational energy can cause wear and tear on the tank itself, potentially leading to leaks. Baskets ensure that items are held at an optimal level within the cavitation field for maximum exposure to the cleaning action and allow the solution to freely circulate around all surfaces. They are typically made of stainless steel mesh or round rod material, designed to minimize obstruction of the ultrasonic waves. The mesh size is important when cleaning very small parts to prevent them from falling through. For extremely delicate items, plastic baskets might be used, though plastic can absorb some ultrasonic energy and slightly reduce cleaning efficiency.
- Heater: Many ultrasonic cleaners are equipped with a built-in heating element to warm the cleaning solution. Heat plays a significant role in enhancing the cleaning process for many applications. Warmer solutions generally have lower viscosity, which can improve cavitation efficiency. Heat also accelerates the chemical activity of detergents and cleaning agents, making them more effective at breaking down and dissolving contaminants like oils, greases, and waxes. The optimal temperature varies widely depending on the specific cleaning solution being used, the type of contaminant, and the material of the item being cleaned. For example, while heat is beneficial for oils, it can cause proteins like blood to denature and become harder to remove if the temperature is too high (e.g., above approximately 100°F or 38°C for biological soils). Most general-purpose ultrasonic cleaning units operate in a temperature range of 130°F to 180°F (approximately 54°C to 82°C), though some specialized processes may use lower or higher temperatures. It’s often noted that peak cleaning effectiveness for many aqueous solutions is achieved between 50-65°C (122-149°F).
- Cleaning Solution: This is the liquid medium in which the ultrasonic waves propagate and cavitation occurs. While water can be used, it’s often not effective enough on its own, especially for stubborn or non-water-soluble contaminants. The cleaning solution is a critical component, and its chemistry is tailored to the specific cleaning task – the type of material being cleaned and the nature of the contaminants to be removed. These solutions typically contain detergents, surfactants (wetting agents), and other chemical agents that perform several functions: they help to dissolve or emulsify contaminants, they reduce the surface tension of the liquid (which allows for better penetration into crevices and enhances cavitation), and they can help to prevent re-deposition of loosened soils. The choice of cleaning solution is paramount and will be discussed in greater detail in the next section.
The effective operation of an ultrasonic cleaner is not just due to one superior component, but rather the result of a carefully engineered system where each part plays a vital role and interacts with the others.
The generator must provide the correct electrical energy to the transducers; the transducers must efficiently convert this into mechanical vibrations; the tank must effectively contain the solution and transmit these vibrations; the cleaning solution must have the right chemical properties for the task and be at the optimal temperature (if heated); and the basket must position the items correctly for maximum exposure to the cavitation action.
A deficiency in any one of these areas—such as using an incorrect or depleted cleaning solution, setting the wrong temperature, overloading the basket, or having failing transducers—can significantly compromise the overall cleaning performance. This interdependency means that optimizing or troubleshooting an ultrasonic cleaning process requires a holistic understanding of how all these components work together.
To provide a clearer overview, the following table summarizes these key components and their functions:
Table 1: Key Components of an Ultrasonic Cleaner and Their Functions
Component | Primary Function | Key Considerations/Features |
---|---|---|
Ultrasonic Generator | Converts AC electrical power into high-frequency electrical signals to power the transducers. | Power output, frequency control (fixed, sweep, multi-frequency), power intensity control, timer. |
Transducers | Convert high-frequency electrical energy from the generator into mechanical vibrations (ultrasonic waves). | Piezoelectric material (e.g., PZT), bonding type (direct, immersible), number, placement, operational frequency. |
Tank | Holds the cleaning solution and the items to be cleaned; transmits ultrasonic vibrations. | Material (typically stainless steel), size, shape, construction quality, drain design. |
Cleaning Basket/Rack | Suspends items in the solution, preventing contact with the tank bottom and ensuring optimal cleaning exposure. | Material (stainless steel mesh/rod, plastic), mesh size, load capacity, proper fit for the tank. |
Heater | Warms the cleaning solution to enhance cleaning effectiveness for certain contaminants. | Temperature control (fixed or adjustable thermostat), heating speed, safety cut-offs. |
Cleaning Solution | Liquid medium for cavitation; contains chemical agents to dissolve/dislodge contaminants and enhance cleaning. | Type (aqueous, alkaline, acidic, neutral, enzymatic, solvent), pH, compatibility with item and contaminant, concentration, temperature range. |
The Perfect Potion: Choosing and Using Ultrasonic Cleaning Solutions
The cleaning solution in an ultrasonic cleaner is far more than just a passive liquid; it’s an active and essential partner in the cleaning process. While the ultrasonic waves provide the mechanical energy, the solution provides the chemical action needed to break down, dissolve, or suspend contaminants, and to optimize the cavitation process itself. Using plain water is often remarkably ineffective for many cleaning tasks.
The right solution can dramatically enhance cavitation energy, reduce the liquid’s surface tension for better penetration, and specifically target the types of soils on the items being cleaned. Conversely, an improper or depleted solution can lead to poor cleaning results, potential damage to the items, or even harm to the ultrasonic cleaner itself.
Types of Solutions
A wide variety of cleaning solutions are available, each formulated for different materials and contaminants:
- Aqueous (Water-Based) Solutions: These are the most common type and form the base for many specialized formulations. They are generally considered eco-friendlier and safer to handle than solvent-based options and are versatile enough for a wide range of materials including metals, plastics, glass, and ceramics. Aqueous solutions typically contain detergents, wetting agents (surfactants), and other additives. Surfactants are particularly important as they reduce the surface tension of the water, allowing the solution to penetrate microscopic crevices and improving the efficiency of cavitation bubble formation and collapse.
- Alkaline Solutions (pH > 7): Characterized by a pH level above 7, alkaline cleaners are highly effective at removing organic soils such as grease, oils, fats, waxes, and some proteins. They often work by a process called emulsification, where they break down fats and oils into smaller particles that can be suspended in the solution, or through saponification, which converts fats into soap and glycerol in the presence of an alkali. Mildly alkaline solutions are suitable for general degreasing and cleaning on many metals (including properly formulated solutions for aluminum), zinc, and stainless steel. Strongly alkaline, or caustic, solutions (pH typically 12 or higher) are reserved for heavy-duty cleaning tasks, such as stripping burned-on carbon deposits, thick grease, or tough residues from robust parts.
- Acidic Solutions (pH < 7): With a pH below 7, acidic cleaners are primarily used for removing inorganic contaminants like rust, scale, mineral deposits, and oxides. They must be chosen and used with considerable care, as acids can be corrosive to certain materials, particularly soft metals like aluminum or brass if not properly inhibited or if exposure is prolonged. For some applications, an acid-resistant plastic tub may be used inside the main stainless steel tank (which contains water) to hold the acidic solution and the parts, allowing the ultrasonic energy to pass through.
- Neutral Solutions (pH ≈ 7): These solutions have a pH close to neutral (around 7) and are the gentlest option. They are typically used for light cleaning tasks or for cleaning delicate materials that might be sensitive to more aggressive acidic or alkaline chemistries.
- Enzymatic Solutions: Specifically designed for applications where biological soils are prevalent, such as in the medical, dental, or food processing industries. Enzymatic cleaners contain specific enzymes that target and break down proteins (like blood and tissue), fats, and carbohydrates. These solutions are often temperature-sensitive, as the enzymes have optimal working temperature ranges for maximum efficacy.
- Solvent-Based Solutions: For contaminants that are not easily removed by water-based solutions, such as heavy oils, greases, waxes, flux residues from electronics, or when cleaning moisture-sensitive components, solvent-based cleaners may be necessary. These can include petroleum distillates, specialized hydrocarbons, or alcohols like isopropyl alcohol (IPA). It is critically important to note that flammable solvents like IPA, gasoline, or acetone should never be used in standard ultrasonic cleaners not specifically designed and certified as explosion-proof. The ultrasonic energy can create vapors, and any spark (from the electronics or static discharge) could lead to a fire or explosion. Specialized ultrasonic systems exist for use with flammable solvents, incorporating safety features like vapor containment and intrinsically safe electronics.
Matching Solutions to Contaminants and Materials
The selection of the correct cleaning solution is a critical decision that directly impacts cleaning effectiveness and the safety of the items being cleaned. Key factors to consider include:
- Type of Material Being Cleaned: Different materials react differently to various chemical agents. For example, stainless steel is quite robust and can tolerate a wide range of solutions, whereas aluminum is sensitive to highly alkaline solutions and can be etched or discolored. Brass and copper may tarnish with certain chemistries. Plastics, glass, and ceramics also have their own sensitivities.
- Type of Contaminant: The nature of the soil dictates the type of chemistry needed. Oils and greases typically require alkaline or solvent-based degreasers. Rust and scale need acidic solutions. Biological matter is best tackled by enzymatic cleaners. Fingerprints or light dust might only need a neutral or mildly alkaline solution.
- Level of Cleaning Required: Critical cleaning applications, such as for medical implants or precision optics, demand solutions that not only clean effectively but also rinse completely, leaving no residue.
- pH Considerations: As a general guide, acidic solutions (pH < 7) are for rust and mineral deposits; neutral solutions (pH ≈ 7) for delicate items and light soils; alkaline solutions (pH 8-11) for general degreasing; and highly caustic solutions (pH > 11-12) for heavy-duty removal of stubborn contaminants like carbon or polishing compounds.
While household dish soap can sometimes be used in a pinch for very light duties, it’s generally not recommended for consistent or critical cleaning, as it may not be formulated for optimal cavitation, can leave residues, and might even cause corrosion on some metals when combined with water and ultrasonic energy. Specialized ultrasonic cleaning solutions are almost always a better choice as they are designed to work synergistically with the ultrasonic process.
Safety and Environmental Considerations
Handling cleaning solutions requires attention to safety and environmental impact:
- Personal Protective Equipment (PPE): Always consult the Safety Data Sheet (SDS) for the specific solution being used. Generally, wearing gloves and eye protection is recommended to prevent skin and eye irritation, especially with concentrated, acidic, or alkaline solutions.
- Ventilation: Ensure adequate ventilation, particularly when using solvent-based solutions or those that may produce strong fumes, to avoid inhalation of vapors.
- Storage and Disposal: Store cleaning solutions in properly labeled, closed containers as per manufacturer recommendations. Dispose of spent solutions according to local, state, and federal regulations. Many modern aqueous solutions are biodegradable, which simplifies disposal, but accumulated contaminants in the solution may still classify it as hazardous waste.
- Flammability: Reiteration is crucial: never use flammable solvents (e.g., alcohol, gasoline, acetone) in a standard ultrasonic cleaner unless it is explicitly designed and rated as explosion-proof for such use. The risk of fire or explosion is significant.
The cleaning solution is not a set-and-forget component. Its effectiveness diminishes over time as it becomes saturated with contaminants, its chemical composition changes due to the ultrasonic energy, or through evaporation.
Therefore, managing the solution is an ongoing task. This includes regular monitoring of its condition, skimming off floating oils or debris, filtering (in systems equipped for it), checking and adjusting concentration (if applicable), and ultimately, complete replacement when it no longer cleans effectively. This “solution management” represents an often-overlooked aspect of the operational commitment and cost associated with using ultrasonic cleaners.
The synergy between the ultrasonic energy and the cleaning solution cannot be overstated. The solution doesn’t just fill the tank; it actively participates in and optimizes the cleaning process by enhancing cavitation, reducing surface tension to allow penetration into the smallest crevices, and chemically interacting with the contaminants to loosen or dissolve them.
The ultrasonic energy then provides the mechanical force to sweep these mobilized contaminants away. Using an inappropriate solution is akin to having a high-performance engine (the ultrasonic cleaner) but fueling it with the wrong type of gasoline – the performance will be severely hampered, or damage could result. Success in ultrasonic cleaning hinges on this vital partnership.
To assist in navigating these choices, the following table provides a general guide to ultrasonic cleaning solutions:
Table 2: Guide to Ultrasonic Cleaning Solutions
Solution Type | Approx. pH Range | Best For (Contaminants) | Suitable Materials (General) | Not Recommended For (General) | Key Considerations |
---|---|---|---|---|---|
Aqueous – Neutral | ~7 | Light dust, fingerprints, some water-soluble soils. | Most materials, including delicate ones, glass, some plastics, sensitive metals. | Heavy oils, grease, rust, baked-on carbon. | Gentle; good for general maintenance cleaning. |
Aqueous – Alkaline (Mild) | 8 – 11 | Oils, grease, fats, cutting fluids, general grime, some biological soils. | Most metals (inc. steel, stainless steel, some aluminum with inhibitors), ceramics, glass. | Highly sensitive aluminum or zinc without proper inhibitors. | Good general-purpose degreaser; temperature often enhances action. |
Aqueous – Alkaline (Caustic/High) | >12 | Heavy oils, grease, carbon deposits, waxes, paint, tough baked-on residues. | Iron, steel, stainless steel (robust materials). | Aluminum, zinc, magnesium, copper, brass, plastics, painted surfaces. | Very aggressive; handle with care (PPE); ensure material compatibility. |
Aqueous – Acidic | <7 | Rust, scale, mineral deposits, oxides, tarnish. | Ferrous metals (iron, steel), some stainless steel; use with caution. | Aluminum, magnesium, zinc, copper, brass, chrome, many plastics. | Can be corrosive; test compatibility; may require acid-resistant tubs; handle with care (PPE). |
Enzymatic | Neutral to Mildly Alkaline | Blood, tissue, proteins, food residues, other biological soils. | Medical/dental instruments (stainless steel), labware, items with organic contamination. | Materials incompatible with water or specific enzymes. | Temperature-sensitive (enzymes have optimal ranges); biodegradable. |
Solvent-Based | N/A | Heavy oils, greases, waxes, flux residues, adhesives, inks, moisture-sensitive cleaning. | Metals, some plastics, electronics (PCBs). | Materials sensitive to specific solvents. | Check flammability (use only in explosion-proof units if flammable); ensure good ventilation; may have environmental/disposal concerns. |
Note: Always consult manufacturer recommendations for both the ultrasonic cleaner and the specific cleaning solution, as well as the item being cleaned.
A Universe of Uses: Diverse Applications of Ultrasonic Cleaners
The unique ability of ultrasonic cleaners to reach into the tiniest nooks and crannies and gently but powerfully remove contaminants has led to their adoption across a remarkably diverse range of fields. From sterile processing in hospitals to the intricate work of jewelers and the robust demands of industrial manufacturing, this technology offers solutions where traditional cleaning methods fall short.
- Medical & Dental: In healthcare settings, cleanliness is paramount. Ultrasonic cleaners provide an automated and highly effective method for cleaning surgical and dental instruments, especially those with complex designs like lumens (internal channels), fine serrations, box lock joints, and crevices that are difficult to access manually. They excel at removing biological soils such as blood, tissue, and other organic materials before sterilization. A significant benefit is the prevention of “heat baking” where residual debris on instruments can become hardened during the high temperatures of sterilization, making them much harder to remove later. Furthermore, ultrasonic cleaning reduces the need for manual scrubbing of sharp or contaminated instruments, thereby enhancing safety for sterile processing staff. Specific protocols exist for delicate items like ophthalmic instruments, where even minute contamination can cause serious issues like Toxic Anterior Segment Syndrome (TASS); these may involve using only treated water without detergents. Beyond instruments, ultrasonic cleaners are also used for cleaning dentures, orthodontic retainers, dental molds, and implants. Adherence to the instrument manufacturer’s Instructions For Use (IFUs) regarding cleaning chemistries and processes is crucial.
- Laboratory: Laboratories rely on impeccably clean glassware and equipment for accurate experimental results. Ultrasonic cleaners are widely used for cleaning items such as beakers, test tubes, slides, pipettes, and various analytical instruments, effectively removing chemical residues, dirt, and grime. Beyond simple cleaning, laboratory sonicators (another term for ultrasonic baths in this context) are invaluable tools for sample preparation. This includes tasks like dissolving powders, dispersing nanoparticles, mixing solutions, emulsifying liquids, extracting active pharmaceutical ingredients (APIs) from matrices, and degassing solvents for techniques like High-Performance Liquid Chromatography (HPLC). Many official pharmacopeia monographs (e.g., USP) specifically recommend ultrasonic baths for sample dissolution prior to analysis.
- Electronics: The manufacturing and repair of electronic components, particularly Printed Circuit Boards (PCBs), demand meticulous cleaning. Ultrasonic cleaners are employed to remove contaminants such as flux residues left after soldering, dust, oils, and other debris that can interfere with performance or lead to corrosion. When used with appropriate frequencies (often higher frequencies like 68 kHz, 170 kHz, or in the 80-130 kHz range for delicate components) and compatible cleaning solutions (e.g., specialized flux removers), the process is gentle enough not to damage sensitive electronic components while being thorough enough to clean complex parts, connectors, and the tiny through-holes on PCBs.
- Industrial & Manufacturing: This is a vast area where ultrasonic cleaning shines due to its power and versatility.
- Degreasing: A primary application is the removal of oils, grease, cutting fluids, lubricants, and shop dirt from a wide array of machined parts, castings, engine components, and tools. This is crucial for preparing parts for subsequent processes like plating, painting, or assembly.
- Mold & Die Cleaning: In industries like plastics injection molding, rubber molding, and extrusion, molds and dies accumulate residues from mold release agents, outgassing of materials, and the materials themselves. Ultrasonic cleaning effectively removes these contaminants without abrading or damaging the critical surfaces of the molds, which helps to extend their operational life, maintain part quality, and reduce production downtime.
- Parts Finishing: Before plating, coating, or other finishing processes, surfaces must be impeccably clean. Ultrasonics are used to remove buffing and polishing compounds, fine metal chips, and other residues.
- Aerospace: The aerospace industry demands extremely high standards of cleanliness for aircraft components to ensure safety and reliability. Ultrasonic cleaning provides the precision needed for these critical parts.
- Large-Scale Systems: While many associate ultrasonic cleaners with smaller benchtop units, large industrial systems with tank capacities exceeding 100 gallons are common. These are designed for cleaning large, heavy components like engine blocks, diesel particulate filters (DPFs), heat exchangers, or for high-volume batch processing. Such systems often incorporate features like automated part handling, agitated immersion (where parts are mechanically moved within the tank to enhance cleaning), advanced filtration systems to prolong solution life, and multi-stage processes that can include wash, rinse, passivation, and drying stages all in one line.
- Jewelry: One of the most well-known consumer applications is jewelry cleaning. Ultrasonic cleaners can restore the sparkle and brilliance to rings, necklaces, earrings, and bracelets by removing accumulated dirt, oils, lotions, and grime from intricate settings and surfaces that are difficult to reach with a cloth or brush. However, caution is advised: not all gemstones are suitable for ultrasonic cleaning. Porous stones (like pearls, opals, coral, turquoise, lapis lazuli), organic gems, stones with surface-reaching fractures that have been filled (e.g., some emeralds), and gems whose color has been enhanced by heat treatment can be damaged. Jewelry made from solid gold, platinum, sterling silver, and most diamonds (natural and lab-grown) are generally considered safe for ultrasonic cleaning.
- Firearms: For firearm enthusiasts and armorers, ultrasonic cleaning offers a thorough method for maintaining firearm components. It effectively removes lead shavings, powder residue, old lubricants, and other fouling from slides, frames, barrels, and small intricate parts, reaching into areas that manual cleaning might miss. The process often involves two steps: first, cleaning in a specialized gun cleaning solution, followed by a second ultrasonic bath in a lubricating solution to displace water and leave a protective film. Wooden or ivory grips and other sensitive materials should always be removed before cleaning.
While ultrasonic cleaners are primarily designed for immersing items to clean complex surfaces and small parts, it’s important to note that they are generally not intended for cleaning large, flat surfaces like countertops or floors in the way a steam cleaner or pressure washer might be used [User Query]. The technology excels where immersion and cavitation can work on all submerged surfaces.
The sheer breadth of these applications underscores a key aspect of ultrasonic cleaning: it’s not a one-size-fits-all technology. Different tasks and industries have driven the development of specialized machines, frequencies, cleaning solutions, and process steps.
For example, medical cleaning has stringent requirements for detergents and adherence to IFUs , while electronics cleaning often favors higher frequencies and specific flux-removing chemistries. Industrial degreasing might utilize robust alkaline solutions and lower, more aggressive frequencies , whereas jewelry cleaning has a specific list of gemstones that must be avoided.
This inherent specialization means that users must carefully select or configure an ultrasonic cleaning system and its associated consumables to be appropriate for their specific task to achieve effective and safe results.
The following table offers a quick guide to some common applications:
Table 3: Ultrasonic Cleaner Application Quick Guide
Application Area | Common Items Cleaned | Typical Contaminants | Key Considerations (Examples) |
---|---|---|---|
Medical & Dental | Surgical/dental instruments, lumens, endoscopes (parts), dentures, implants. | Blood, tissue, proteins, saliva, debris, polishing compounds. | Enzymatic or specialized medical-grade detergents; adherence to IFUs; specific protocols for delicate items (e.g., ophthalmic). |
Laboratory | Glassware (beakers, flasks, slides), lab instruments, mixing, degassing, sample prep. | Chemical residues, biological matter, particulate, oils. | Neutral, alkaline, or specialized lab detergents; solvent use for degassing/extraction; temperature control for sensitive samples. |
Electronics | Printed Circuit Boards (PCBs), connectors, electronic components. | Flux residues, solder paste, dust, oils, fingerprints. | Higher frequencies (e.g., 40-130 kHz); specialized flux removers or IPA (in appropriate equipment); deionized water for rinsing. |
Industrial Degreasing | Machined parts, engine components, tools, castings, bearings. | Oils, grease, cutting fluids, lubricants, coolants, metal fines, shop dirt. | Alkaline or heavy-duty degreasers; lower frequencies (e.g., 25-40 kHz) for robust parts; heat often beneficial. |
Mold & Die Cleaning | Injection molds, extrusion dies, tooling. | Mold release agents, plastic/rubber residues, outgassing deposits, light rust. | Alkaline or specialized mold cleaning solutions; non-abrasive to preserve mold surface integrity. |
Jewelry | Rings, necklaces, bracelets, earrings (solid metals, hard gemstones like diamonds). | Dirt, oils, lotions, tarnish, grime from settings. | Mild detergents or specialized jewelry solutions; AVOID porous/treated/soft gemstones (pearls, opals, emeralds, etc.). |
Firearms | Gun barrels, slides, frames, triggers, small metal parts. | Powder residue, lead, carbon fouling, old lubricants, rust. | Specialized gun cleaning solutions (often followed by ultrasonic lubrication); remove wood/plastic grips. |
The Bright Side: Unpacking the Benefits of Ultrasonic Cleaning
The growing adoption of ultrasonic cleaning technology across various sectors is driven by a compelling set of advantages that address many limitations of traditional cleaning methods.
- Unmatched Cleaning Thoroughness, Especially for Complex Shapes: This is perhaps the most significant benefit. The cavitation process generates microscopic bubbles that can penetrate the smallest crevices, blind holes, internal channels, and intricate geometries that are simply inaccessible to brushes, sprays, or manual wiping. This ensures a level of cleanliness that is difficult, if not impossible, to achieve by other means, providing uniform cleaning across all submerged surfaces.
- Efficiency in Time and Labor: Ultrasonic cleaning is remarkably fast compared to manual methods. Cleaning cycles that might take hours of meticulous hand scrubbing can often be completed in minutes. For instance, automotive parts can be thoroughly cleaned in as little as three minutes, a task that could take hours by hand. This speed, combined with the ability to clean multiple parts simultaneously in a batch process, drastically reduces the labor required for cleaning tasks, freeing up personnel for other duties and increasing overall productivity.
- Gentle on Many Delicate Items (When Parameters are Correct): Despite the immense localized energy of cavitation, the overall process is non-abrasive when the correct frequency, cleaning solution, and cycle time are employed. Unlike scrubbing or blasting, which can cause wear, scratches, or other surface damage, ultrasonic cleaning relies on the implosion of bubbles to lift contaminants away. This gentle action helps to preserve the integrity of delicate items and can extend the functional lifespan of precision parts, tools, and equipment by minimizing wear during cleaning. The key is to match the cleaning parameters to the item’s sensitivity.
- Often Reduces the Need for Harsh Chemicals: The powerful mechanical cleaning action provided by cavitation can significantly lessen the reliance on aggressive or hazardous chemical solvents. In many cases, milder, water-based detergents or even just plain water (for some applications) can be effective when combined with ultrasonic energy. This not only makes the cleaning process safer for operators but also reduces the environmental impact associated with the use and disposal of harsh chemicals. The availability and effectiveness of biodegradable and eco-friendlier cleaning solutions further enhance this benefit.
These benefits collectively point towards a broader shift in cleaning philosophies. The ability to achieve superior cleanliness with less manual effort, often using milder and more environmentally friendly chemistries, aligns with increasing demands for sustainability, operator safety, and operational efficiency. Ultrasonic cleaning, therefore, is not just about achieving a better clean; it’s about enabling smarter, safer, and more sustainable cleaning practices across a multitude of applications.
Know Before You Go: Limitations and Safe Operating Practices
While ultrasonic cleaning offers remarkable advantages, it’s not a universal panacea, and like any powerful technology, it comes with limitations and requires careful operation to ensure safety and efficacy. Understanding these aspects is crucial for anyone considering its use.
Not a Universal Solution: Material Compatibility is Key
One of the most critical considerations is material compatibility. Not all items can withstand the forces of cavitation or the chemistry of certain cleaning solutions.
- Gemstones and Jewelry: Certain gemstones are particularly vulnerable. Porous stones like pearls, opals, emeralds (especially if fracture-filled), turquoise, coral, and lapis lazuli can be damaged. Jewelry with enamel details, stones that have been surface-oiled, or those whose color has been enhanced by heat treatment may also be adversely affected. Antique or vintage jewelry, which might be fragile, and gold-plated items (where the plating can be worn away) should generally be avoided or cleaned with extreme caution and expertise.
- Medical and Technical Instruments: Some chrome-plated instruments may experience plating removal. Powered instruments can suffer internal damage if fluid invades sensitive components. Delicate adhesive seals on some endoscopic lenses or fiber optic light cables can also be compromised by the vibrations.
- Electronics: While effective for PCBs, highly delicate electronic components such as certain ceramic-based parts or Micro-Electro-Mechanical Systems (MEMS) like gyroscopes, accelerometers, or microphones can be susceptible to damage, especially at lower, more aggressive frequencies.
- Other Materials: Soft plastics may deform under the ultrasonic waves. The technology is also less effective for soft, absorbent materials that dampen the ultrasonic energy rather than allowing it to dislodge contaminants, or for situations where contaminants are chemically bonded to the surface (like a strong paint layer) rather than merely adhering to it.
Potential for Damage if Used Incorrectly
Even with compatible materials, incorrect operation can lead to damage:
- Frequency Selection: As discussed, lower frequencies generate larger, more energetic cavitation bubbles, which are more aggressive. Using too low a frequency on a delicate item can cause pitting or surface damage.
- Cleaning Solution Choice: Using a chemically incompatible, overly aggressive, or incorrectly diluted solution can lead to etching, corrosion, discoloration, or other damage to the items being cleaned. For instance, highly alkaline solutions can damage aluminum.
- Direct Contact with Tank: Allowing items to rest directly on the tank bottom, or allowing hard particles to accumulate there, can lead to abrasion of the items and the tank itself. This can also impede the cleaning process.
- Over-Exposure: Excessively long cleaning cycles, especially with aggressive solutions or temperatures, can sometimes be detrimental. There can be a point of diminishing returns, and prolonged exposure might affect certain finishes.
- Cross-Contamination: As contaminants are removed, they accumulate in the cleaning solution. If the solution becomes heavily soiled, there’s a risk that these loosened contaminants can redeposit onto subsequently cleaned items. Regular solution maintenance or a final rinse in fresh solution can mitigate this.
Essential Safety Precautions
Operating an ultrasonic cleaner requires adherence to several safety measures:
- Solution Handling:
- Never use flammable solutions such as alcohol, gasoline, or acetone in a standard ultrasonic cleaner unless it is specifically designed and rated as explosion-proof for such use. The ultrasonic energy can vaporize these solvents, and any spark could cause a fire or explosion. Only use water-based solutions or those explicitly approved by the cleaner manufacturer.
- Avoid using mineral acids directly in unprotected stainless steel tanks, as they can cause corrosion and damage the tank. If acidic cleaning is necessary, use an appropriate acid-resistant insert (like a glass beaker or plastic tub) placed within the main tank containing water.
- Do not use solutions containing chlorine bleach, as this can also damage stainless steel tanks.
- Always wear appropriate Personal Protective Equipment (PPE), such as gloves and safety goggles, when handling cleaning solutions, especially concentrates or aggressive chemistries, to prevent skin and eye irritation.
- Operational Safety:
- Do not place hands or fingers directly into the cleaning solution while the unit is operating. The solution can become hot, and the cavitation energy, while generally safe on intact skin for brief periods, can cause discomfort, tingling, or potential skin irritation with prolonged exposure. The energy can also pass through the skin and potentially affect underlying tissues or even the bloodstream with very intense or prolonged exposure.
- Ensure the ultrasonic cleaner is properly grounded to prevent electrical shock hazards.
- Do not operate the cleaner with the solution level too low (e.g., below the fill line indicated by the manufacturer, often specified as not more than 3/8 inch below the operating level line). This can lead to inefficient cleaning and potentially damage the heaters or transducers.
- Never operate the cleaner dry (without any solution in the tank), as this can quickly overheat and permanently damage the transducers.
- Keep the control panel and the area around the cleaner clean and dry. Spilled solution near electrical components is a hazard.
- Ensure adequate ventilation in the work area, especially if using solutions that may produce fumes.
- Do not allow the cleaning solution temperature to exceed the limits specified by the manufacturer or those safe for the items being cleaned (e.g., a general caution is often not to exceed 70°C or 160°F unless specified otherwise).
- Noise: Ultrasonic cleaners, particularly those operating at lower frequencies (e.g., 20-45 kHz), can generate audible noise due to the vibration of the tank and components. For prolonged exposure, hearing protection may be advisable. Using the tank lid can help reduce noise levels as well as minimize solution evaporation and heat loss.
Successfully using an ultrasonic cleaner involves a careful balance. The goal is to harness its significant cleaning power (efficacy) to remove contaminants thoroughly. However, this power, if misapplied through incorrect frequency selection, incompatible cleaning solutions, excessive time, or improper loading, can lead to damage to the item being cleaned (item safety).
Furthermore, the operator must adhere to safety protocols when handling chemicals, operating the machine, and considering factors like heat and noise (operator safety).
Achieving optimal results requires understanding these interconnected variables and how they influence the outcome. It’s not merely a matter of turning the machine on; it often involves a learning curve and diligent adherence to guidelines to navigate this power-safety-efficacy dynamic effectively.
Long-Lasting Performance: Maintaining Your Ultrasonic Cleaner
An ultrasonic cleaner is a sophisticated piece of equipment, and like any precision instrument, it requires regular maintenance to ensure it continues to perform effectively and to prolong its operational lifespan. Neglecting maintenance can lead to diminished cleaning power, damage to the unit itself, and ultimately, costly repairs or premature replacement. Consistent upkeep should be viewed as an investment in preserving the machine’s value and reliability, not merely a chore.
- Regular Tank Cleaning and Solution Changes:
- The cleaning solution is the lifeblood of the process, but it doesn’t last forever. As items are cleaned, the solution becomes saturated with dislodged contaminants, and its chemical properties can degrade over time due to the ultrasonic energy and heat. It’s crucial to drain and replace the cleaning solution when it loses its effectiveness or becomes visibly soiled. For production environments, a more structured schedule might involve daily skimming of floating contaminants, weekly filtering (for systems with recirculation), and complete solution replacement monthly or based on throughput.
- When disposing of spent solution, always follow local, state, and federal environmental regulations. Even if the original detergent was biodegradable, the accumulated contaminants might render the used solution hazardous.
- After draining the tank, it should be thoroughly rinsed with clean water to remove any adhering residues, sludge, or particles that have settled on the bottom. Never use abrasive scouring pads or powders to clean the tank, as these can scratch the stainless steel surface and create sites for corrosion or cavitation erosion.
- Over time, especially with hard tap water, mineral deposits (“furring”) or rust films (often transferred from ferrous parts being cleaned, not from the stainless steel itself) can form on the tank interior. These can typically be removed by cleaning the tank with a suitable descaling or mild cleaning agent recommended by the manufacturer (e.g., elma tec clean S1 is mentioned for removing oxide films, lime, and mineral deposits). Running the ultrasound while heating a fresh cleaning solution can also help ensure even temperature distribution and minimize hot spots that might contribute to discoloration.
- Preventing Tank Damage:
- The stainless steel tank, while robust, is susceptible to damage over time, primarily from cavitation erosion (wear caused by the imploding bubbles, especially near transducers) and mechanical abrasion.
- Always use a cleaning basket or rack to suspend items in the solution. Never place parts directly on the tank bottom. This prevents items from scratching the tank and, more importantly, stops hard particles dislodged during cleaning from being vibrated against the tank bottom, where they can act like tiny drills, eventually causing pitting or even pinholes.
- Regularly clean the tank (as described above) to remove any abrasive particles that have settled.
- Maintain the cleaning solution at the proper level as indicated by the manufacturer. Operating with too little solution can lead to inefficient cleaning and potentially damage the heaters or transducers due to improper loading or overheating.
- Inspecting Components:
- Periodically inspect the transducers (usually bonded to the tank exterior) for any signs of physical damage, such as cracks or chips, or signs of debonding. Transducer issues can significantly reduce cleaning power. Repair or replacement of transducers is a specialized task and should typically be performed by qualified technicians.
- Ensure the ultrasonic generator is functioning correctly, producing the appropriate frequency and power output. Some users perform periodic checks like the “aluminum foil test” to gauge cavitation intensity, or monitor electrical power consumption.
- For medical-grade ultrasonic cleaners, a more rigorous maintenance schedule is often required and may be mandated by facility protocols or regulations. This can include daily checks (e.g., drain/irrigation filters, detergent levels, running test strips to verify ultrasonic activity), weekly checks (e.g., irrigation tube connections, O-rings, detergent tube mesh screens), monthly checks (e.g., drain screen housing, cabinet stability, lid sensor functionality), semi-annual checks (e.g., for leaks, fitting tightness, transducer rod tightness), and a comprehensive annual preventive maintenance (PM) service by a qualified technician.
- Proper Storage:
- When the ultrasonic cleaner is not in use for extended periods, it should be emptied, cleaned, dried thoroughly, and stored in a cool, dry place, away from direct sunlight and moisture, to prevent corrosion or damage to electronic components.
- General Care:
- Keep the exterior of the unit clean using a damp cloth. Do not spray cleaning agents directly onto the casing, especially near vents or control panels.
- If the unit has a cooling fan, periodically check and clean any ventilator grills to remove accumulated dust, ensuring proper airflow and preventing overheating.
- Regularly inspect power cords for any signs of wear, fraying, or damage, and replace them if necessary.
- Crucially, always refer to and follow the specific operating and maintenance instructions provided by the manufacturer of your ultrasonic cleaner model. These manuals contain vital information tailored to your unit’s design and features.
By diligently following these maintenance practices, users can significantly extend the life of their ultrasonic cleaner, ensure consistent and optimal cleaning performance, and avoid unexpected breakdowns.
DIY vs. The Pros: When to Call for Professional Cleaning Expertise
Ultrasonic cleaners are incredibly powerful and versatile tools, empowering many to achieve a high level of cleanliness for a variety of items at home or in small businesses. However, they are not magic wands, and there are situations where the complexity of the task, the nature of the contaminants, the value or sensitivity of the items, or regulatory requirements make calling in professional cleaning services the wiser, safer, and ultimately more effective choice.
Understanding when to tackle a job yourself and when to rely on expert help is key.
- Complexity and Scale of the Job:
- Professionals Shine: For large-scale industrial cleaning operations, cleaning a high volume of parts consistently, or tackling highly intricate jobs that require specialized setups (like multi-stage automated cleaning lines with wash, rinse, and dry stations), professionals are equipped with the infrastructure, larger and more powerful machinery, and logistical expertise.
- DIY Suitability: DIY ultrasonic cleaning is generally best suited for smaller, manageable tasks where benchtop or smaller floor-standing units are adequate – for example, cleaning jewelry, hobbyist parts, small tools, or limited batches of components.
- Presence of Hazardous Materials:
- Professionals are Essential: This is a critical area where professional intervention is often non-negotiable. Dealing with biohazards (blood, bodily fluids), unknown chemical spills, asbestos, lead paint dust, significant mold remediation (beyond minor surface spots), or specific industrial chemicals requires specialized training, advanced Personal Protective Equipment (PPE), containment procedures, and knowledge of safe disposal methods according to OSHA and public health regulations. Professionals are equipped and certified to handle these dangerous situations safely and effectively.
- DIY Limitations: DIY cleaning should be strictly limited to common household or workshop contaminants where the risks are well understood, the cleaning solutions are relatively benign, and standard safety precautions are sufficient.
- High-Value, Delicate, or Irreplaceable Items:
- Professionals Recommended: If an item is extremely valuable, an irreplaceable antique, a highly delicate piece of art, or a complex piece of equipment where the risk of damage from an incorrect DIY attempt is high, consulting a professional is prudent. They possess specialized knowledge of material interactions, appropriate (and sometimes proprietary) cleaning chemistries, and techniques for handling such items. This also applies to certain types of jewelry or electronics that are known to be unsuitable for standard ultrasonic cleaning methods.
- DIY Considerations: DIY is appropriate for items where the user fully understands the material compatibility, the operational parameters of their cleaner, and the potential risks, and where the cost of accidental damage is acceptable.
- Need for Specialized Equipment & Deep Expertise:
- Professionals Offer More: Professional cleaning services typically have access to a much wider range of industrial-grade ultrasonic systems, including those with varying frequencies, larger tank capacities, advanced features like high-flow filtration, turbulation, oil removal systems, and agitated immersion. They also command a broader arsenal of cleaning chemistries and possess deeper scientific knowledge about contaminant removal, material science, and process optimization gained through experience across diverse and challenging cleaning problems.
- DIY Constraints: DIY users are generally limited to the capabilities of consumer or prosumer-grade ultrasonic cleaners and the range of cleaning solutions readily available to the public.
- Time, Convenience, and Labor:
- Professionals Save Time: Outsourcing cleaning tasks to professionals frees up significant personal or business time and effort, allowing individuals or companies to focus on their core activities, work, family, or leisure. Professionals handle the entire process from setup to cleanup.
- DIY Investment: DIY cleaning requires a personal investment of time for researching the correct methods and solutions, setting up the equipment, performing the cleaning cycle, monitoring the process, cleaning the cleaner itself, and properly disposing of used solutions.
- Ensuring Regulatory Compliance (Especially for Businesses):
- Professionals Ensure Adherence: For businesses operating in regulated industries such as healthcare (instrument reprocessing), food service (hygiene standards), or certain manufacturing sectors (quality control, safety standards), professional cleaning services are often crucial for meeting and documenting adherence to strict health, safety, and cleanliness regulations. These services understand and operate within these legal frameworks.
- DIY Challenges for Businesses: Achieving and maintaining commercial regulatory compliance with a DIY approach can be challenging and may require significant investment in specialized equipment, training, and process validation.
- Long-Term Cost-Effectiveness:
- Professionals Can Be Economical: While hiring professionals involves an upfront service fee, it can often be more cost-effective in the long run. This is achieved by preventing costly damage to items or equipment that might result from incorrect DIY attempts, avoiding the need for businesses or individuals to purchase expensive specialized ultrasonic systems or chemicals for occasional or highly specific tasks, and ensuring a level of thoroughness that can prevent larger problems down the line (e.g., preventing mold growth from incomplete drying, or averting equipment failure due to persistent contamination).
- DIY Hidden Costs: The initial cost of a DIY ultrasonic cleaner might seem lower, but ongoing expenses for cleaning solutions, maintenance of the cleaner, potential replacement of damaged parts, and the cost of ineffective cleaning leading to bigger issues can add up over time.
- Peace of Mind:
- Professionals Provide Assurance: Engaging expert services often brings peace of mind, knowing that the cleaning task is being handled correctly, safely, and thoroughly by trained and experienced individuals.
- DIY Responsibility: With DIY cleaning, the user bears the full responsibility for the outcome and any potential issues that may arise.
In essence, while ultrasonic cleaners are powerful and accessible tools that bring professional-grade cleaning capabilities within reach for many, they are not a substitute for specialized knowledge and experience in all situations.
The decision to call a professional should be based on a realistic assessment of the cleaning challenge, the risks involved, the resources available, and the desired outcome. Recognizing the limits of DIY and the value of expert intervention is key to leveraging cleaning technologies responsibly and effectively.