1. The Indispensable Role of Train and Rolling Stock Cleaning
The regular and thorough cleaning of trains and rolling stock is a multifaceted discipline that extends far beyond simple aesthetics. It is a critical component of operational integrity, safety assurance, and financial stewardship within the railway industry. The implications of cleanliness, or the lack thereof, resonate through passenger experiences, cargo safety, asset longevity, brand reputation, and regulatory adherence.
Ensuring Passenger and Cargo Safety, and Comfort
Contact us!
For passenger rail services, the cleanliness of carriages is a primary determinant of comfort and perceived safety, directly influencing passenger satisfaction. However, the importance of cleaning is equally, if not more, critical in the freight sector. Railcars are frequently used to transport a diverse array of goods, ranging from food products and agricultural goods to chemicals, raw materials, and industrial equipment.
The residue from a previous load can pose a significant risk of cross-contamination to subsequent cargo. For instance, a railcar that previously transported scrap metal or waste materials must be meticulously cleaned before it can safely carry food items or sensitive electronic components. Proper cleaning procedures ensure that no harmful residues are left behind, thereby safeguarding the integrity and safety of the goods being transported and preventing potentially hazardous reactions or spoilage.
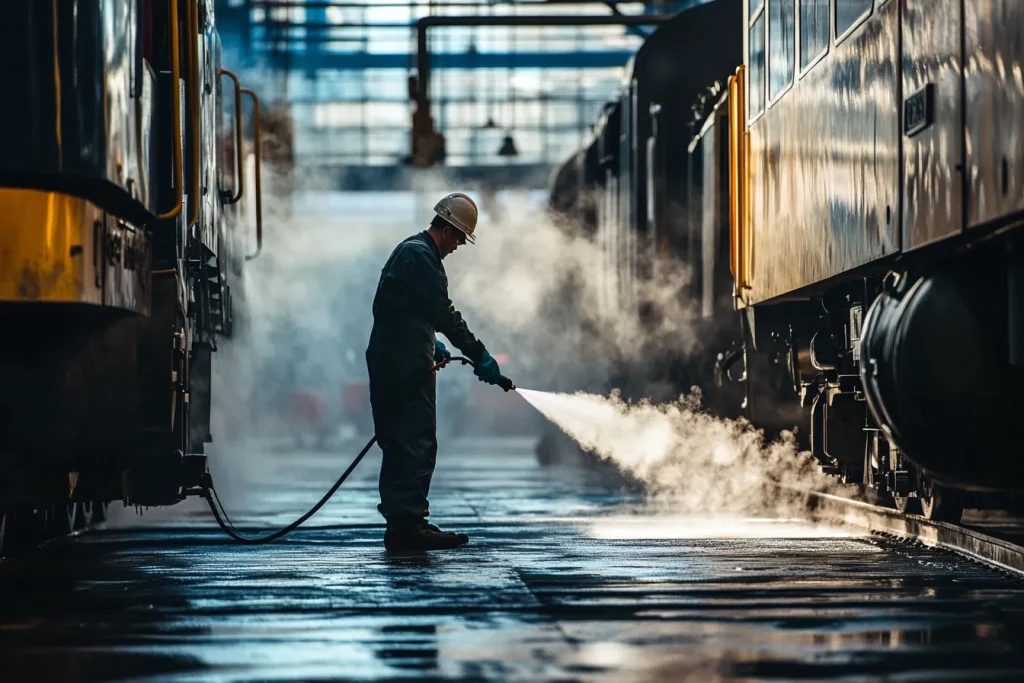
Railcar cleaning and inspections are fundamental to preventing accidents and cross-contamination, ensuring that each load is protected. This diligence is crucial for maintaining the quality of products, particularly in industries like food and pharmaceuticals where strict quality standards are paramount.
The interconnectedness of these cleaning facets is significant. Failure to prevent cross-contamination due to inadequate cleaning can lead to compromised cargo, resulting in direct financial losses for shippers and carriers. More seriously, contaminated food products can pose severe public health risks. Such incidents can trigger regulatory investigations, fines, and lasting damage to the reputation of both the carrier and the businesses whose goods were affected. Thus, cleaning is not merely a janitorial task but a critical control point in the complex logistics chain, impacting safety, regulatory standing, and financial outcomes.
Maintaining Asset Value and Longevity
Rolling stock represents a substantial capital investment for railway operators. Regular and comprehensive cleaning is an integral part of preventative maintenance, playing a vital role in preserving the value and extending the operational lifespan of these assets. Exposure to environmental pollutants, de-icing salts, industrial emissions, brake dust, and cargo residues can lead to corrosion and material degradation if not systematically removed.
For example, the accumulation of grime and corrosive substances can damage paintwork, leading to rust and erosion of the metalwork on locomotives and carriages. By removing these harmful buildups, cleaning helps to mitigate the risk of corrosion, structural fatigue, and mechanical issues, thereby delaying the need for costly repairs or premature replacement of components.
The practice of regular cleaning and inspection serves as a proactive risk mitigation strategy. During the cleaning process, personnel or automated systems can identify early signs of wear, damage, or potential mechanical failures, such as loose, broken, or worn parts. Addressing these issues promptly, as highlighted during a cleaning inspection, can prevent minor problems from escalating into major failures that could lead to service disruptions, accidents, or more extensive and expensive repairs. This “early warning system” aspect of thorough cleaning contributes significantly to operational reliability and safety, offering a higher long-term value than simply addressing visible dirt.
Upholding Brand Image and Public Perception
In the competitive passenger transport sector, the cleanliness of a train is a powerful, tangible indicator of an operator’s commitment to customer service and quality. A clean, well-maintained train interior—free of litter, stains, and odors—significantly enhances the passenger experience, fostering a sense of comfort, safety, and well-being.
Conversely, a dirty or poorly maintained train can quickly lead to passenger dissatisfaction, complaints, and a negative perception of the operator’s brand. For freight operations, clean and well-maintained railcars project an image of professionalism, reliability, and care to clients, reinforcing trust in the carrier’s ability to transport goods safely and efficiently.
Compliance with Health, Safety, and Industry Regulations
The railway industry is governed by a stringent framework of health, safety, and operational regulations. These standards often include specific requirements for the cleanliness of rolling stock, particularly when used for passenger transport or for carrying sensitive goods such as food products or hazardous materials. Regulatory bodies may impose detailed cleaning protocols to minimize risks associated with the transportation of such goods.
For example, specialized cleaning procedures are sometimes required to meet religious cleanliness standards, such as those for kosher or halal products, ensuring that food items are transported in compliance with these specific dietary laws. Adherence to these regulations is not optional; it is a fundamental aspect of responsible and legal railway operation, and failure to comply can result in penalties, operational restrictions, and reputational damage.
The economic ripple effect of cleanliness, or its absence, can be substantial. Unclean railcars that are taken out of service for unscheduled cleaning reduce equipment availability. This can lead to delays in shipping schedules, particularly if the railroad owns the equipment and alternative railcars are not readily available.
Such disruptions can have cascading effects throughout the supply chain, impacting manufacturers awaiting raw materials, retailers expecting finished goods, and ultimately, consumers. These delays can result in contractual penalties for carriers and shippers, and potentially lead to lost business if service reliability is consistently compromised. Therefore, maintaining a high standard of railcar cleanliness is not just an operational detail but a factor contributing to broader economic efficiency and supply chain integrity.
2. Mastering Exterior Cleaning: A Comprehensive Approach
The exterior of a train is constantly exposed to a barrage of environmental and operational contaminants, including dirt, dust, mud, engine exhaust, brake dust, industrial pollutants, and in colder climates, de-icing salts. Effective exterior cleaning is essential not only for maintaining a positive public image but also for preserving the structural integrity and operational efficiency of the rolling stock. This involves a range of methods from large-scale automated systems to meticulous manual techniques.
Automated Exterior Washing Systems
For railway operators with extensive fleets, automated washing systems offer an efficient, consistent, and cost-effective solution for exterior cleaning. These systems are designed to handle high volumes of rolling stock, reducing manual labor and ensuring a standardized level of cleanliness.
They generally fall into two main categories: drive-thru (or passage) systems and gantry (or rollover) systems.
- Drive-Thru vs. Gantry Systems: Mechanisms and Applications
- Drive-Thru Systems (Passage Wash): In these systems, the train moves at a controlled speed through a stationary wash installation comprising a series of arches and brush stations. Whiting Systems’ SmartWash® Sprite is an example of a drive-thru system, featuring sensors that allow the washing equipment to follow the contours of the locomotive for optimal cleaning with water jets and optional rotary brushes. Christ AG offers the C1000 SOA, a stationary passage wash system suitable for trains of any length, with or without current collectors, cleaning side surfaces and optionally roof slopes. NEU Train Wash also provides drive-through configurations. InterClean designs drive-through systems that can be touchless, friction-based, or a hybrid of both. These systems are generally favored for mainline trains and long consists where rapid throughput is a priority.
- Gantry Systems (Rollover Wash): With gantry systems, the train remains stationary while a mobile gantry, equipped with brushes, spray nozzles, and sometimes drying equipment, travels along the length of the train. Christ AG’s C5400 SOA and C7000 SOA models can operate in semi-stationary or overrun modes, effectively functioning as gantry systems, suitable for trains with or without current collectors and capable of washing all zones, including front and rear. InterClean’s Ultra Gantry system is another example, featuring vertical and top brushes that move over the parked rail cars. Gantry systems may be preferred when more intensive, targeted cleaning is required per section or for fleets with varying train lengths.
- The Automated Wash Cycle: Pre-Rinse, Detergent Application, Brushing, Rinsing, and Drying
A typical automated train wash cycle involves several distinct stages to ensure comprehensive cleaning:- Pre-Rinse: The process usually begins with a powerful pre-rinse where high-pressure water jets spray the train’s exterior from multiple angles. This initial stage is designed to loosen and dislodge heavy, caked-on dirt, grime, and other debris. NEU systems, for instance, incorporate an arch equipped with water spraying nozzles for pre-wetting.
- Detergent Application: Following the pre-rinse, specially formulated cleaning agents or detergents are applied to the train’s surfaces. These detergents are designed to break down stubborn dirt, oils, and grime, softening their adhesion to the bodywork. NEU systems feature arches with detergent spraying nozzles , while InterClean systems may employ a two-step chemical application, often involving an acid and an alkaline cleaner. Companies like Whiting Systems even develop custom cleaning soaps tailored to specific operational needs and climates.
- Brushing/Scrubbing: This is a critical stage where physical agitation removes the loosened dirt. Automated systems use robust brushes of various configurations – vertical brushes for sides, horizontal brushes for roofs and eaves, and sometimes specialized skirt brushes for lower areas. Whiting Systems and Christ AG highlight the use of rotary and contour-following brushes. InterClean details options for slanted, vertical, and eaves brush modules, with counter-rotating side brushes for comprehensive cleaning. Some systems, particularly touchless ones, may rely on high-pressure oscillating jets instead of or in addition to brushes.
- Rinsing: After the scrubbing stage, the train is thoroughly rinsed with high-pressure water jets to remove all traces of detergent and dislodged contaminants, leaving the surfaces clean. NEU systems may use softened water for rinsing to prevent spotting , and InterClean systems include a fresh water rinse stage.
- Drying: The final stage often involves high-powered blowers or air knife systems that direct controlled bursts of air across the train’s surfaces to remove residual moisture. This meticulous drying process helps to prevent water spots and streaks, ensuring an immaculate appearance. NEU offers blow-dry fans for a perfect finish , and InterClean lists blowers as a feature for their gantry systems.
The development and adoption of these sophisticated automated washing systems are driven by multiple pressures. The sheer volume of rolling stock in many fleets makes manual washing impractical from a time and labor cost perspective. Automation offers consistency in cleaning quality, which can be difficult to achieve with manual methods across a large workforce. Furthermore, automated systems can enhance worker safety by minimizing direct exposure to cleaning chemicals and the potentially hazardous environment of a rail yard. Environmental regulations concerning water usage and wastewater discharge also play a significant role, as many modern automated systems are designed for controlled water consumption and can incorporate water reclamation technologies.
Table 1: Comparison of Selected Automated Train Wash Systems
System Manufacturer/Model | Type | Key Cleaning Mechanisms | Drying Method | Water Reclaim Option | Notable Features |
---|---|---|---|---|---|
Whiting Systems SmartWash® Sprite | Drive-Thru | Water jet sprayers, optional rotary brushes, contour-following sensors, custom soaps | Not specified | Not specified | Sensors follow locomotive contours, custom soap formulation. |
Christ AG C1000 SOA | Stationary Passage (Drive-Thru) | Brush pairs for sides (optional roof brushes), spray and rinsing stands | Stationary blowers (opt) | Not specified | Unlimited wash length, PLC controller, intelligent transfer measurement for lateral brushes. |
Christ AG C5400 SOA | Semi-Stationary Passage / Overrun | Self-propelled lateral wash system, optional horizontal brushes, skirt brushes, inclined brushes | Stationary blowers (opt) | Not specified | PLC controller, all wash zones possible, suitable for trains without current collector. |
Christ AG C7000 SOA | Passage / Semi-Stationary / Overrun | Split horizontal brush (cleans front/rear, accommodates current collector), lateral brushes, optional spoiler/3D brushes | Stationary blowers (opt) | Not specified | Cleans with current collector out, active power measurement for lateral brushes, suitable for trams and trains. |
NEU Train Wash | Drive-Thru or Gantry | Pre-wetting nozzles, detergent nozzles, brushing stations (sides, eaves, skirts, roof), softened water rinse | Blow-dry fan | Yes (total/partial) | Modular design, tailored to rolling stock profiles and speeds. |
InterClean Systems | Drive-Thru or Rollover/Gantry | Touchless (Centri® Spinners, flat spray nozzles), Friction (brushes), or Hybrid. Two-step chemical application | Blowers (gantry) | Not specified | Custom engineered, single or bi-directional, automatic or manual process, Centri® Spinners for touchless front/rear cleaning. |
Manual Exterior Cleaning Techniques
Despite the efficiency of automated systems, manual cleaning remains indispensable for several reasons: for smaller operators without automated facilities, for targeted cleaning of heavily soiled areas missed by automated washes, for intricate components inaccessible to machines, and for specialized tasks like detailed window or undercarriage cleaning.
- Essential Tools and Equipment: A well-equipped manual cleaning operation will utilize a variety of tools. These include high-pressure washers, such as the Hydroblaster models, for dislodging stubborn grime and for rinsing. Specialized brushes with varying bristle stiffness and lengths, including extension poles for reaching high areas, are crucial for scrubbing different surfaces. Mops, microfiber cloths, and sponges are used for applying cleaning solutions and wiping surfaces. Appropriate cleaning agents, ranging from general detergents to specialized chemicals for specific contaminants, are also necessary. Finally, comprehensive Personal Protective Equipment (PPE), including gloves, eye protection, waterproof clothing, and potentially respirators, is vital for worker safety.
- Step-by-Step Procedures for Body, Windows, and Undercarriage:
- Body: The general approach involves pre-wetting the surface, applying a suitable cleaning agent, allowing for dwell time, agitating the surface with brushes or cloths to loosen dirt, and then thoroughly rinsing with clean water. For specific issues like iron staining from brake dust, products like Oxalwash can be used. For daily washing, a gentler product like Ecowash Autoshine might be appropriate. Clinex S5 is a universal cleaner for external train fabric, applicable with sponges, brushes, cloths, or pressure washers.
- Windows: Achieving clear, streak-free windows is paramount for driver visibility and passenger experience. This typically involves applying a specialized glass cleaner, such as Clinex Glass , and then wiping with a clean, lint-free microfiber cloth or using a professional squeegee technique. Working from the top down helps prevent drips onto already cleaned areas. For very delicate surfaces or minor touch-ups, some model train cleaning techniques, like using highly diluted dishwashing liquid or even the condensation from breath wiped with a soft lens tissue, can offer insights into gentle cleaning methods.
- Undercarriage: This area is prone to heavy accumulation of grease, oil, mud, brake dust, and other debris. Cleaning often starts with the manual removal of large, caked-on materials using tools like shovels. This is followed by the application of degreasers and intensive washing, typically with high-pressure water jets. PNR Italia offers a specialized system for underbody cleaning, which involves manifolds with high-impact flat jet nozzles installed on the tracks, delivering a three-stage process of degreasing, rinsing, and finishing as the train passes over them.
Specialized Exterior Cleaning Considerations
- Undercarriage Cleaning: Tackling Tough Grime: The undercarriage and bogies are critical operational areas that accumulate some of the most challenging contaminants. Regular, even daily, cleaning of the undercarriage is recommended, particularly in regions prone to cold weather, as accumulated mud and debris can freeze, potentially causing damage to components or impeding their function. The cleaning process must be robust enough to remove hardened materials, oil, grease, and corrosive substances like de-icing salts. While the body and windows are visibly important for aesthetics and immediate passenger perception, neglecting undercarriage cleaning can lead to severe long-term consequences. The buildup of corrosive materials can accelerate rust and structural degradation, potentially masking cracks or wear in critical components like axles, braking systems, or suspension parts. If undetected and unaddressed, these issues can escalate into costly repairs or, more critically, compromise the safety of the rolling stock. This makes thorough undercarriage cleaning a vital, albeit less visible, aspect of preventative maintenance and safety assurance.
- Window Cleaning: Achieving Streak-Free Clarity: Clean windows are non-negotiable for the safe operation of trains, providing unobstructed views for drivers, and for enhancing the travel experience for passengers. Professional window cleaning techniques aim for maximum clarity without streaks or residue. This typically involves using high-quality, non-streaking glass cleaners and appropriate tools such as microfiber cloths or squeegees with rubber blades. For exterior train windows, which can be subject to harsh environmental conditions and stubborn grime, a multi-step process might be necessary, including pre-washing to remove loose dirt, application of the cleaning solution, gentle scrubbing if needed (avoiding abrasive materials that could scratch the glass), and meticulous wiping or squeegeeing to dry.
Eco-Friendly Exterior Cleaning Solutions
The railway industry, like many others, is increasingly focusing on sustainability, leading to a growing demand for environmentally friendly cleaning agents and practices for exterior maintenance.
- Sustainable Detergents and Practices: This involves the use of cleaning chemicals that are biodegradable, pH-neutral, and free from harsh or persistent pollutants. Arrow Solutions offers products like Oxalwash, formulated to remove iron staining without mineral acids, making it less harmful to concrete infrastructure like sleepers and platforms. Their Ecowash Autoshine is a pH-neutral daily exterior wash suitable for use in water reclaim units. More broadly, eco-friendly pressure washing chemicals often feature non-toxic formulations, biodegradable soaps, and active ingredients derived from plant sources, such as citric acid or oxalic acid. VLS Environmental Solutions is another company that reports using eco-friendly cleaning solutions in their railcar maintenance services.
- Water Reclamation and Conservation: Water consumption is a significant environmental concern in large-scale washing operations. Many modern automated train wash systems, such as those offered by NEU Train Wash, can be equipped with total or partial water reclamation systems. These systems collect, filter, and reuse wash water, significantly reducing fresh water intake and wastewater discharge. This practice is not only environmentally responsible but also driven by increasingly stringent regulations regarding wastewater. For example, in the United States, the Environmental Protection Agency (EPA) has regulations concerning the discharge of wash water, which can contain pollutants like diesel exhaust residues, heavy metals from brake dust, and chemicals from cleaning agents; such discharge may need to be collected and treated, potentially as hazardous waste if not managed correctly. The adoption of eco-friendly cleaning solutions and water recycling technologies is therefore influenced by both a desire for sustainability and the need to comply with environmental laws, which can also lead to cost savings through reduced water usage and avoidance of fines for improper discharge.
Table 2: Selected Eco-Friendly Cleaning Agents for Train Exteriors
Product Name/Type | Key Eco-Friendly Features | Primary Use | Contaminants Targeted | Source/Brand (Example) |
---|---|---|---|---|
Oxalwash | Contains no mineral acids, will not damage concrete, rinses freely | Exterior train wash, iron stain removal | Dirt, oil, rust, brake/iron dust | Arrow Solutions |
Ecowash Autoshine | pH neutral, suitable for reclaim units, helps build soil-resistant finish | Daily exterior train wash, degreasing | General dirt, grime | Arrow Solutions |
Plant-Based Detergents | Biodegradable, derived from renewable resources, often non-toxic | General purpose exterior cleaning | Dirt, grime | Various (General Type) |
Citric Acid-Based Cleaners | Natural ingredient, biodegradable, bleach-free | Mineral deposit removal, siding cleaning | Mineral deposits, general dirt | Various (General Type) |
Oxalic Acid Cleaners | Non-toxic (when formulated as eco-friendly), effective on tough stains | Rust removal, tough stain removal | Rust, tough stains | Various (General Type) |
Blue Gold Spray Wash | Biodegradable, non-caustic, ingredients on EPA accepted list | Degreasing, general rail cleaning | Hydrocarbons, grease, oil | Modern Chemical Inc. |
RailX® | Partially biodegradable, non-toxic, non-corrosive, organic solvent | Heavy oil & petroleum contaminant removal | Heavy oil, asphalt, wax, fuels | BioChem Systems |
Safety Protocols for Exterior Cleaning Crews
Ensuring the safety of personnel involved in exterior train cleaning is paramount, given the potential exposure to chemicals, high-pressure equipment, electrical hazards (if working near overhead lines or on electric trains), and the dynamic environment of a rail yard.
- Chemical Handling and PPE: Workers must receive thorough training on the hazards associated with the cleaning chemicals being used, including how to read and understand Safety Data Sheets (SDS). The use of appropriate PPE is mandatory and typically includes chemical-resistant gloves, safety glasses or goggles, protective clothing or coveralls, and, depending on the chemicals and application method (e.g., spraying), respiratory protection. Employers are responsible for providing this PPE and ensuring workers are trained in its proper use, limitations, maintenance, and disposal.
- Working with Automated Systems and High-Pressure Equipment: When working with or around automated wash systems, strict adherence to operational safety procedures is essential. This includes lockout/tagout procedures during maintenance or repair to prevent accidental startup. For manual operations involving high-pressure washers, workers must be trained in the safe operation of the equipment to prevent injuries from high-pressure water streams or from slips and falls on wet surfaces.
- General Site Safety: Cleaning crews often work in active rail yards or maintenance depots, which present inherent risks. Training should cover general rail yard safety, including awareness of train movements, maintaining safe distances from tracks, understanding clearance points , and procedures for working near electrified lines if applicable. Environmental conditions, such as snow and ice, can create additional slip, trip, and fall hazards, requiring careful management and clearing of walking areas and tracks.
3. Revitalizing Interiors: From Seats to Driver’s Cab
The interior of a train is a high-contact environment, demanding meticulous and regular cleaning to ensure passenger and crew health, comfort, and a positive travel experience. Cleaning protocols must address a wide variety of surfaces and potential contaminants, from everyday litter and grime to biohazards.
Systematic Interior Cleaning Strategies
An effective interior cleaning program relies on a structured and systematic approach, tailored to the intensity of use and type of service.
- Daily, Intermediate, and Periodic Cleaning Schedules: The frequency and depth of interior cleaning are typically tiered.
- Pre-Service/Daily Cleans: Conducted before a train enters service or at the end of each day, these focus on removing visible litter, wiping down high-touch surfaces (seats, handrails, door buttons), and basic floor cleaning. The aim is a quick spruce-up to prepare the train for passengers.
- Intermediate Cleans: These are quick, strategic cleaning interventions performed during operational hours, especially on high-turnover services like tube lines or commuter trains during peak periods. They target high-traffic areas and touchpoints to maintain an acceptable level of cleanliness between more thorough cleans.
- Periodic Deep Cleans: These are comprehensive cleaning operations performed at set intervals, which can range from every few days on some busy networks to monthly or quarterly schedules. Deep cleaning involves thoroughly scrubbing all interior surfaces, including seats, walls, floors, ceilings, windows, and restrooms, often using specialized equipment and more intensive cleaning agents.
- Top-Down Cleaning Approach: A fundamental principle in interior cleaning is to work from the top downwards. This means cleaning overhead compartments and higher surfaces first, then moving to seats and ledges, and finally cleaning the floors. This logical sequence prevents dislodged dirt and debris from contaminating already cleaned lower surfaces.
The intense time pressures inherent in train operations, particularly for commuter services where trains must adhere to strict schedules, can create a challenge in balancing speed with thoroughness. This operational reality sometimes leads to compromises in cleaning practices, such as infrequent changing of mop heads, which can inadvertently spread contaminants rather than remove them. This tension underscores the need for highly efficient cleaning methods and technologies, such as the Kaivac No-Touch Cleaning® system for floors, or well-planned, targeted intermediate cleans to maintain hygiene standards during periods of high passenger flow.
Cleaning Specific Interior Components
Train interiors are composed of a multitude of materials, each requiring specific cleaning methods and agents to ensure effectiveness without causing damage.
- Seats: Fabric, Vinyl, and Leather Care:
- Fabric Seats: These are prone to absorbing spills and harboring dirt. Cleaning typically involves thorough vacuuming to remove loose debris, pre-treatment of visible stains with an appropriate stain remover, followed by the application of an upholstery cleaner (e.g., Clinex Textile SHP for general cleaning or Clinex Textile EXT for greasy stains). Gentle scrubbing with a soft-bristle brush helps lift dirt, after which the area may be wiped or extracted. Steam cleaning is also an effective method for deep cleaning and sanitizing fabric seats.
- Vinyl Seats: Vinyl is generally durable and easier to clean. Most dirt can be removed with a solution of mild dish soap and water, applied with a soft cloth or sponge. For more stubborn stains or ground-in dirt, specialized vinyl cleaners or a diluted ammonia mixture (one tablespoon ammonia, ¼ cup hydrogen peroxide, ¾ cup water) can be used with gentle scrubbing. It is crucial to avoid abrasive cleaners or tools that could scratch or damage the vinyl surface.
- Leather Seats: Leather requires careful cleaning to maintain its appearance and prevent drying or cracking. Specialized leather cleaners should be used, applied gently with a soft cloth. After cleaning, a leather conditioner helps to restore moisture and protect the material. It is important to avoid harsh chemicals; for example, isopropyl alcohol should not be used on leather seats or leather steering wheels as it can damage the finish.
- Floors: Tackling Various Materials (Carpet, Rubber, Vinyl):
Train floors endure constant foot traffic, spills, and tracked-in dirt. Daily vacuuming and mopping are standard procedures.29- Carpeted Floors: Require regular and thorough vacuuming to remove surface debris. Periodic deep cleaning using hot water carpet extractors is essential to remove embedded dirt, allergens, and stains. Spot cleaning of spills should be done promptly to prevent permanent staining.
- Rubber Floors: These are durable and offer good slip resistance. Cleaning should be done with a neutral pH cleaner and a nylon or microfiber mop to avoid leaving lint. It’s important to vacuum the floor first to remove loose debris and to avoid soaking the rubber, especially if it’s non-vulcanized, as water can permeate it. Aggressive scouring pads or solvent-based cleaners should be avoided as they can damage the rubber surface.
- Vinyl/Linoleum Floors: These surfaces can often be cleaned effectively with a simple solution of vinegar and water. For more robust cleaning, specialized floor cleaners like Clinex M6 Medium (for general dirt) or Clinex M9 Strong (for stubborn, dried-on dirt and stains like tar or paint) can be used, typically applied with a mop. The Kaivac No-Touch Cleaning® system, which applies cleaning solution, rinses, and then vacuums up the soiled water and contaminants, has been noted as a particularly efficient and effective method for cleaning train car floors, overcoming the limitations of traditional mopping.
- Walls, Ceilings, and Interior Windows:
- Walls and Ceilings: These surfaces are typically wiped down during deep cleaning schedules to remove accumulated dust, grime, and scuff marks. If interior panels are made of plastic or similar synthetic materials, gentle cleaners like Clinex Fast Plast are recommended to effectively clean without causing damage or dulling the surface; such products may also offer antistatic properties to reduce future dust accumulation.
- Interior Windows and Ledges: Clean interior windows are essential for passenger views and overall ambiance. They should be cleaned with a quality glass cleaner (e.g., Clinex Glass ) and wiped with a lint-free microfiber cloth or squeegee to achieve a streak-free finish. Window ledges should be scrubbed during deep cleans to remove built-up dirt and grime.
- Restrooms: Hygiene and Sanitization:
Train restrooms are critical areas requiring frequent and meticulous cleaning and disinfection due to the high potential for bacterial and viral contamination. All surfaces, including toilets, urinals, sinks, countertops, floors, door handles, and dispenser surfaces, must be addressed.
The process involves applying disinfectant cleaners (e.g., Clinex W3 Multi for ceramic surfaces, toilet bowls, urinals, and washbasins 16), toilet bowl cleaners specifically for the inside of bowls, and ensuring all high-touch surfaces are thoroughly wiped and sanitized. Regular restocking of essential supplies such as hand soap, paper towels, and toilet tissue is also a crucial part of restroom maintenance. General restroom cleaning protocols suggest spraying the exterior of toilets and urinals first, allowing disinfectant dwell time, then cleaning dispensers, light switches, and doorknobs, before tackling the interior of fixtures and finally mopping the floor with a disinfectant solution. - Driver’s Cab: Maintaining a Clean and Functional Workspace:
The driver’s cab is the operational heart of the train, and its cleanliness is vital for driver health, comfort, and unimpeded, safe operation. Cleaning protocols should cover seats, control panels, windows, and floors.
All frequently touched surfaces, including steering controls, levers, buttons, touch screens, communication equipment, and door handles, should be regularly wiped down with appropriate cleaning and disinfecting agents. For sensitive electronic components and touch screens, manufacturer’s cleaning instructions should be followed; if unavailable, alcohol-based wipes or sprays containing at least 70% alcohol can be used cautiously, ensuring liquids are not sprayed directly onto devices. Cab floors must be kept free from oil, water, waste, or any obstruction that could create a slipping, tripping, or fire hazard, and should be properly treated to provide secure footing. The cab’s HVAC system also requires regular inspection and maintenance to ensure it operates correctly and provides a healthy environment.
The diverse range of materials found in train interiors—from various seat upholsteries and floor coverings to plastic wall panels, glass, and sensitive electronic equipment in the driver’s cab—necessitates a correspondingly diverse array of cleaning agents and techniques. This complexity underscores the importance of well-trained cleaning staff who understand material compatibility and the correct application of different products to avoid causing damage, such as using ethanol-only cleaners on certain soft trims or avoiding isopropyl alcohol on leather 34, and employing gentle cleaners for plastic surfaces. This intricate requirement for specialized knowledge and a broad range of cleaning products often makes professional cleaning services a more effective and reliable option.
Table 3: Interior Cleaning Guide by Surface Type
Interior Component/Surface | Recommended Cleaning Method(s) | Recommended Cleaner Type(s) | Key Considerations/Precautions |
---|---|---|---|
Seats – Fabric | Vacuum, stain pre-treatment, upholstery cleaner application, gentle scrubbing, extraction/steam clean | Fabric/upholstery cleaner (e.g., Clinex Textile SHP/EXT), stain remover, steam (water) | Test in inconspicuous area, follow manufacturer instructions, ensure adequate drying to prevent mildew. |
Seats – Vinyl | Wipe with mild soap & water, specialized vinyl cleaner for tougher stains, gentle scrubbing | Mild dish soap, specialized vinyl cleaner, diluted ammonia solution (for very tough stains) | Avoid abrasive compounds/tools, do not use undiluted bleach or solvents like petroleum distillates. |
Seats – Leather | Gentle wiping with specialized leather cleaner, apply leather conditioner | pH-neutral leather cleaner, leather conditioner | Avoid excessive moisture, do not use harsh solvents or isopropyl alcohol. Test cleaner first. |
Floors – Carpet | Vacuum regularly, spot clean stains, periodic hot water extraction | Carpet shampoo, spot removers, extraction solution | Ensure thorough extraction to prevent residue buildup, allow complete drying. |
Floors – Rubber | Vacuum, mop with neutral pH cleaner and microfiber/nylon mop | Neutral pH cleaner | Avoid soaking, aggressive scouring, solvent-based cleaners, or cotton mops (lint). |
Floors – Vinyl/Linoleum | Sweep/vacuum, mop with vinegar solution or specialized cleaner | Diluted white vinegar, commercial vinyl/linoleum cleaner (e.g., Clinex M6 Medium/M9 Strong), Kaivac system solution | Use sparingly on linoleum, rinse if necessary to remove residue. |
Walls/Ceilings – Plastic | Wipe down with gentle cleaner | Gentle all-purpose cleaner, specialized plastic cleaner (e.g., Clinex Fast Plast) | Avoid abrasive cleaners that can scratch or dull the surface. |
Windows – Glass (Interior) | Spray with glass cleaner, wipe with microfiber cloth or squeegee | Ammonia-free glass cleaner (e.g., Clinex Glass) | Ensure streak-free finish, clean ledges as well. |
Restroom Fixtures | Clean and disinfect toilets, urinals, sinks, surfaces with appropriate agents | Disinfectant cleaner (e.g., Clinex W3 Multi), toilet bowl cleaner, general purpose cleaner | Ensure proper contact time for disinfectants, use separate cloths for toilet areas to prevent cross-contamination, restock supplies. |
Driver Cab Controls/Displays | Wipe with manufacturer-approved cleaner or 70% alcohol wipes (carefully) | Electronics-safe cleaner, 70% alcohol wipes (for non-sensitive surfaces, test first) | Follow manufacturer guidance, do not spray liquids directly on electronics, ensure power is off if specified. Keep floors clear and safe. |
Specialized Interior Cleaning Equipment
Achieving a high standard of interior cleanliness in trains often requires more than basic manual tools. Professional operations utilize a range of specialized equipment:
- Industrial Vacuums: Heavy-duty vacuum cleaners, including backpack models for enhanced mobility and efficiency, are equipped with various attachments (crevice tools, upholstery brushes) to thoroughly remove dirt and debris from seats, floors, carpets, and hard-to-reach areas.
- Carpet Extractors: These machines are essential for deep cleaning fabric upholstery and carpeted floors. They work by spraying a cleaning solution into the fibers and then extracting the solution along with dissolved dirt, grime, and allergens, providing a much deeper clean than vacuuming alone.
- Steam Cleaners: Steam cleaners use high-temperature steam to clean and sanitize a variety of surfaces, including seats, floors, interior panels, and even restroom fixtures. Steam is effective at loosening stubborn dirt and killing bacteria and viruses, often reducing the need for harsh chemical disinfectants.
- Air Purifiers and Foggers: While air purification is often handled by the train’s HVAC system (which itself requires maintenance, including filter changes ), portable air purifiers can be used in specific situations. More commonly for disinfection, fogging devices (such as hydrostatic foggers) are used to disperse disinfectant solutions as a fine mist, ensuring comprehensive coverage of surfaces, including those that are difficult to reach by manual wiping.
- Kaivac No-Touch Cleaning® System: This is a specific example of an integrated cleaning system designed for floors and restrooms. It applies cleaning solution, allows for dwell time, pressure rinses surfaces, and then vacuums away the dirty water and contaminants, offering a more hygienic and efficient alternative to traditional mopping.
Choosing the Right Interior Cleaning Agents
The selection of cleaning agents must be carefully matched to the surface material, the type of soil, and whether cleaning, sanitizing, or disinfecting is the primary goal.
- Disinfectants: For high-touch surfaces, restrooms, and areas where pathogen control is critical, EPA-registered disinfectants are essential. Common active ingredients effective against a range of bacteria and viruses include quaternary ammonium compounds (“quats”), alcohol (ethyl or isopropyl), chlorine-releasing agents (like sodium hypochlorite, or bleach), and improved hydrogen peroxide formulations. The correct dilution and contact time, as specified by the manufacturer, are crucial for disinfectant efficacy.
- Upholstery Cleaners: These are specifically formulated to clean and refresh fabric or specialized seat materials without causing damage or discoloration. Examples include products like Clinex Textile SHP for general fabric cleaning and Clinex Textile EXT for tackling greasy stains on upholstery.
- Hard Surface Cleaners: For general cleaning of walls, ledges, tables, and other hard surfaces, all-purpose or specialized cleaners are used. Clinex M6 Medium is suitable for general floor and corridor cleaning, while Clinex Fast Plast is designed for more delicate plastic surfaces.
- Glass Cleaners: Ammonia-free formulations are often preferred for interior windows and mirrors to prevent streaking and potential damage to surrounding materials. Clinex Glass is an example of a professional preparation for such surfaces.
- Eco-Friendly Alternatives for Interior Surfaces:
There is a growing emphasis on using cleaning products that are less harmful to human health and the environment.- General Principles: This involves avoiding products containing harsh chemicals such as chlorine bleach, formaldehyde, perchloroethylene (PERC), ammonia, certain quaternary ammonium compounds, and synthetic fragrances, which can be irritants or have other adverse health effects. Instead, preference is given to plant-based cleaners, biodegradable detergents, and simple DIY solutions using ingredients like white vinegar, baking soda, and lemon juice for certain applications.
- Upholstery: Eco-friendly options include plant-based cleaners formulated with botanical extracts, essential oils, and enzymes, as well as biodegradable detergents. For DIY stain removal on fabric, a paste of baking soda and water can be effective, or a mild solution of liquid dish soap and warm water for general cleaning.
- Floors (Vinyl/Linoleum): A solution of white vinegar and water is a common eco-friendly option for cleaning these types of floors.
- Restrooms & General Disinfection: Electrolyzed water, which produces hypochlorous acid (HOCl) as a disinfectant and sodium hydroxide (NaOH) as a cleaner/degreaser, is presented as a non-toxic, eco-friendly, and broad-spectrum antimicrobial solution that can be generated on-site. It is effective against bacteria, fungi, and viruses and can be used on both hard and soft surfaces without producing harmful VOCs. Steam cleaning also offers a chemical-free method of sanitization.
Safety Guidelines for Interior Cleaning Crews
Cleaning train interiors involves potential exposure to a range of hazards, requiring robust safety protocols.
- Managing Biohazards and Chemical Exposure:
- Biohazards: Cleaning crews may encounter biohazardous materials such as bodily fluids (blood, vomit), used needles, or other contaminated waste. Handling these requires specific training, the use of appropriate PPE (including gloves, masks, and sometimes eye protection or gowns), and adherence to protocols for safe containment and disposal in designated puncture-resistant containers, following local regulations. Companies may have GBAC-Trained Technicians specifically certified for biohazard crisis response and infection control.
- Chemical Exposure: Many cleaning and disinfecting agents can be hazardous if not handled correctly. Comprehensive training on chemical hazards (often part of Hazard Communication or HAZCOM programs), understanding Safety Data Sheets (SDS), ensuring proper dilution of concentrates, maintaining adequate ventilation in enclosed train cars, and consistent use of appropriate PPE (gloves, goggles, respirators if spraying or using volatile chemicals) are all essential. It is critical to never mix different cleaning chemicals, particularly those containing bleach with ammonia-based products or acids, as this can create dangerous toxic gases.
- Confined Space Entry Procedures:
Certain areas within a train, such as under-seat compartments, maintenance access points, or even densely packed carriages during out-of-service cleaning, could potentially be classified as confined spaces. These spaces may pose risks due to poor ventilation leading to oxygen deficiency or the buildup of toxic fumes from cleaning agents, as well as risks of entrapment or difficulty in egress during an emergency.
Work in such spaces, if they meet the criteria for a permit-required confined space, necessitates specialized procedures. These include obtaining entry permits, conducting atmospheric testing before and during entry, ensuring continuous ventilation, having trained attendants stationed outside, and having a well-defined emergency rescue plan in place. Cleaning crews, like those from Pitbull, may receive specific training in confined space entry protocols. OSHA provides detailed regulations and guidance for working in permit-required confined spaces.54
The driver’s cab, while a part of the interior, merits special consideration due to its direct link to operational safety. Beyond general tidiness, the cleanliness of controls, displays, and windows is crucial for the driver’s ability to operate the train safely and effectively. Sensitive electronic equipment in the cab requires specific cleaning methods to prevent damage, often detailed by the equipment manufacturers.
Furthermore, regulatory bodies like the Federal Railroad Administration (FRA) in the U.S. have standards concerning the condition of the driver’s cab, including requirements for floors to be free of hazards and properly treated for secure footing, and for HVAC systems to be maintained. This elevates cab cleaning from a simple housekeeping task to an integral part of operational safety and regulatory compliance.
4. Deep Cleaning and Disinfection: Ensuring a Hygienic Environment
Deep cleaning and disinfection are intensive processes that go significantly beyond routine daily cleaning. They are designed to thoroughly sanitize all interior surfaces, including hard-to-reach nooks and crannies, and to eliminate a broad spectrum of microorganisms such as bacteria, viruses, and fungi. These procedures are critical for maintaining public health within the high-traffic environment of public transportation, a need that was sharply underscored during and after the COVID-19 pandemic.
The Importance of Deep Cleaning and Disinfection Protocols
The primary goal of deep cleaning and disinfection is to reduce the microbial load on surfaces, thereby minimizing the risk of disease transmission among passengers and crew. The frequency of these intensive cleanings can vary depending on the operational context; some networks may perform deep cleans every 3-4 days, while others might schedule them on a monthly or quarterly basis. However, during public health crises or outbreaks, the frequency and intensity of disinfection protocols are significantly increased.
For example, during the COVID-19 pandemic, the Metropolitan Transportation Authority (MTA) in New York moved to disinfecting stations twice daily and ensuring the entire rolling stock fleet was disinfected at least every 72 hours. BNSF Railway reported that a deep clean of each train set, which includes electrostatic sanitizing and steam cleaning, takes approximately two and a half to three days to complete. Amtrak also enhanced its protocols to include daily deep cleaning and disinfection of trains prior to service, using highly effective disinfectants.
The public health crisis triggered by the COVID-19 pandemic served as a significant catalyst, fundamentally evolving hygiene standards and accelerating the adoption of advanced disinfection technologies within the public transport sector. What was once considered an ancillary service has transformed into a critical aspect of public health assurance. This shift is evident in the increased frequency of sanitization , the investment in technologies like electrostatic spraying and UV-C disinfection , and a greater emphasis on verifiable cleanliness. These changes suggest a lasting elevation of hygiene expectations, driven by heightened public awareness and potential regulatory scrutiny.
Advanced Disinfection Technologies
To achieve comprehensive and efficient disinfection, particularly across large and complex train interiors, operators are increasingly turning to advanced technologies that supplement manual wiping and cleaning.
- Fogging/Electrostatic Spraying: These technologies disperse disinfectant solutions in the form of a fine mist (fogging) or as electrostatically charged droplets (electrostatic spraying). The electrostatic charge causes the disinfectant to be attracted to and wrap around surfaces, ensuring more uniform and comprehensive coverage, even on complex shapes and in hard-to-reach areas, compared to manual spraying or wiping. BNSF utilizes electrostatic sanitizing as part of its deep cleaning regimen. Metra employs hydrostatic foggers for disinfecting its rail cars. General industry best practices also recognize electrostatic sprayers as an advanced cleaning technology that can cover more area in less time while providing a deeper clean.
- UV-C Light Disinfection Systems: Ultraviolet-C (UV-C) light is a form of electromagnetic radiation with germicidal properties. When microorganisms are exposed to UV-C light at specific wavelengths (typically around 254 nm), their DNA and RNA are damaged, rendering them incapable of reproduction and effectively inactivating them. UV-C disinfection systems are being increasingly developed and deployed for both air and surface disinfection in various settings, including public transportation. Aqua Innovation, for example, provides UV-C disinfection systems for treating water in train dining cars, ensuring a safe supply for passengers and crew. Techinn has introduced UV-C LED-based air disinfection systems specifically designed for trams and subway cars, which can purify the air while vehicles are in operation and have been implemented in cities like Prague and Cairo. These systems offer a chemical-free method of disinfection, though their efficacy on surfaces is dependent on direct line-of-sight exposure and sufficient dosage.
Table 4: Overview of Deep Cleaning & Disinfection Technologies for Trains
Technology | Mechanism of Action | Advantages | Disadvantages/Limitations | Typical Applications in Trains |
---|---|---|---|---|
Fogging (Cold/Thermal) | Disperses disinfectant as fine mist/aerosol to cover surfaces. | Good coverage of large areas and complex surfaces, can be relatively quick. | Can leave surfaces wet, requires evacuation during/after application, potential inhalation risk without proper PPE, may not reach all shadowed areas. | Broad disinfection of carriage interiors, seating areas, restrooms. |
Electrostatic Spraying | Applies electrostatically charged disinfectant droplets that wrap around surfaces. | Excellent 360-degree coverage, improved adhesion to surfaces, potentially uses less disinfectant than fogging. | Requires specialized equipment, surfaces must be relatively clean for optimal efficacy, potential for residue if not wiped post-application (product dependent). | Comprehensive surface disinfection of entire interiors, high-touch points, complex equipment in cabs. |
UV-C Light (Air) | UV-C radiation damages microbial DNA/RNA in air passing through the system. | Chemical-free, can operate continuously in occupied spaces (if shielded), effective against airborne pathogens. | Efficacy depends on airflow rate and UV dosage, regular maintenance of lamps/LEDs needed. | HVAC integrated systems or standalone units for air purification in passenger carriages and crew areas. |
UV-C Light (Surface) | Direct UV-C radiation damages microbial DNA/RNA on exposed surfaces. | Chemical-free, no residue, rapid for direct line-of-sight. | Requires direct line-of-sight (shadowing is an issue), potential material degradation with prolonged exposure, safety precautions needed to prevent human exposure. | Disinfection of surfaces in unoccupied carriages, potentially for restrooms or specific high-touch zones using mobile or fixed units. |
Steam Cleaning | High-temperature steam loosens dirt and kills microorganisms through heat. | Chemical-free (or reduced chemical use), effective on porous and non-porous surfaces, good for deep cleaning. | Can leave surfaces damp requiring drying time, may not be suitable for all heat-sensitive materials, can be labor-intensive for large areas. | Deep cleaning and sanitizing seats, carpets, floors, restroom surfaces, interior panels. |
Effective Disinfectants: Types and Application
The choice of disinfectant is critical and should be based on its proven efficacy against relevant pathogens, surface compatibility, safety for users and the environment, and regulatory approval.
- Virucidal and Bactericidal Agents: Disinfectants used in public transport settings must be effective against a broad spectrum of microorganisms, including common bacteria and viruses such as influenza and coronaviruses (like SARS-CoV-2). It is widely recommended to use disinfectants that are registered by relevant authorities, such as the Environmental Protection Agency (EPA) in the United States, for their claimed efficacy against specific pathogens.
Common active ingredients found in effective disinfectants include:- Ethanol and Isopropyl Alcohol: Typically at concentrations of 60-95%. Ethanol, for example, has demonstrated significant viral infectivity reduction against coronaviruses with contact times ranging from 15 seconds to several minutes, depending on concentration and test conditions.
- Quaternary Ammonium Compounds (QACs or Quats): A broad class of disinfectants effective against many bacteria and enveloped viruses.
- Chlorine-Releasing Agents: Sodium hypochlorite (household bleach) is a common example. A 1:100 dilution of household bleach (approximately 600 ppm) can be used for disinfecting surfaces, with a recommended contact time of at least 3-5 minutes.
- Improved Hydrogen Peroxide: These formulations are effective disinfectants that break down into water and oxygen, offering a more environmentally benign profile than some other chemicals.
- Proper Application, Contact Times, and Surface Compatibility: For any disinfectant to be effective, it must be applied correctly and according to the manufacturer’s instructions. This includes ensuring that surfaces are pre-cleaned to remove organic matter (which can inactivate some disinfectants), applying the disinfectant at the correct dilution, and, crucially, allowing the surface to remain visibly wet for the specified contact time (or dwell time). Different disinfectants have different required contact times to achieve their claimed kill rates for various microorganisms. Compatibility with the surfaces being treated is also essential to prevent corrosion, discoloration, or other damage.
Eco-Friendly Disinfection Methods
The demand for effective disinfection must be balanced with concerns for human health and environmental impact, leading to interest in more sustainable disinfection approaches.
- Electrolyzed Water (Hypochlorous Acid – HOCl): This technology involves passing an electric current through a solution of water and salt (sodium chloride) to produce hypochlorous acid (HOCl), a potent disinfectant, and sodium hydroxide (NaOH), a cleaning agent/degreaser. HOCl is recognized as a non-toxic, broad-spectrum antimicrobial effective against bacteria, fungi, and viruses, including influenza, norovirus, and COVID-19. It can be generated on-site, reducing the need to transport and store conventional chemical disinfectants. It is considered safe for workers, does not produce harmful volatile organic compounds (VOCs), and is environmentally friendly as it reverts to salt and water.
- Steam Cleaning: As mentioned previously, steam cleaning utilizes high temperatures to kill microorganisms and is an inherently chemical-free method of disinfection. It is particularly useful for porous surfaces like upholstery and carpets, as well as hard surfaces.
- Careful Product Selection: This involves opting for disinfectants with lower environmental toxicity profiles, such as those based on hydrogen peroxide (which decomposes into water and oxygen) or, where available and proven effective, plant-derived disinfectants. While “SPS Greenclean” is an ecolabelled alkaline cleaner , its primary function is cleaning, and its broad-spectrum disinfection capabilities would need separate verification.
Verifying Cleanliness: The Role of ATP Testing
Traditionally, the effectiveness of cleaning was often judged by visual inspection. However, a surface can appear clean but still harbor significant microbial contamination. Adenosine Triphosphate (ATP) testing provides a rapid, scientific method to verify the thoroughness of cleaning and sanitation procedures by detecting the presence of organic matter, which is an indicator of potential microbial presence. ATP is an energy molecule found in all living (and once-living) cells.
The ATP testing process involves swabbing a surface, then inserting the swab into a handheld luminometer (e.g., Hygiena’s EnSURE® Touch luminometer with UltraSnap® or SuperSnap® test devices ). The luminometer measures the amount of light generated by a chemical reaction with any ATP present on the swab, providing a quantitative result in Relative Light Units (RLUs) within seconds.
Lower RLU scores indicate cleaner surfaces, while higher scores suggest that cleaning was inadequate and that corrective action is needed. ATP testing is used across various industries, including food safety and healthcare, to monitor hygiene, validate cleaning protocols, and ensure compliance with standards like HACCP.
Its adoption in the transport sector allows for immediate feedback on cleaning effectiveness, enabling rapid remediation and providing objective data to build passenger confidence. This shift from subjective visual assessment to objective, measurable data represents a significant advancement in hygiene management, particularly crucial in maintaining public trust in the safety of shared transport environments.
Safety Measures for Deep Cleaning and Disinfection Crews
The intensive nature of deep cleaning and disinfection processes, often involving potent chemicals and specialized equipment, necessitates stringent safety measures to protect cleaning personnel.
- Personal Protective Equipment (PPE): Comprehensive PPE is non-negotiable. This typically includes chemical-resistant gloves, protective gowns or coveralls, eye protection (goggles or face shields), and respiratory protection (e.g., N95 respirators or higher, depending on the chemicals and application method, especially when using foggers, electrostatic sprayers, or volatile disinfectants). Metra’s deep cleaning crews, for instance, are shown wearing PPE during their operations.
- Ventilation: Adequate ventilation must be ensured during and after the application of disinfectants, particularly in the enclosed environment of train carriages, to minimize crew exposure to chemical vapors and aerosols.
- Chemical Handling: Strict adherence to manufacturer’s instructions for disinfectant dilution, application, and contact times is crucial. Proper training in chemical hazard communication (understanding SDS), safe storage, and compliant disposal of chemical waste is essential.
- Equipment Safety: Crews must be trained in the safe operation of all specialized equipment, including foggers, electrostatic sprayers, UV-C disinfection units (which require shielding to prevent direct human exposure to UV-C radiation), and steam cleaners.
The development and interest in eco-friendly disinfection methods like electrolyzed water and the continued application of steam cleaning reflect a growing trend towards solutions that are both highly effective against pathogens and possess a more favorable environmental and human health impact compared to some traditional chemical disinfectants.
This aligns with broader sustainability goals and addresses concerns about prolonged worker exposure to harsh chemicals and the ecological footprint of cleaning operations. As regulations on certain chemical agents become stricter and consumer demand for “green” and “safe” environments intensifies, these alternative disinfection methods are likely to see increased adoption.
5. Specialized Treatments: Graffiti, Livery, and Corrosion
Beyond general cleaning and disinfection, rolling stock requires specialized treatments to address persistent issues like graffiti, maintain the appearance and integrity of exterior livery and graphics, and protect against the pervasive threat of corrosion. These treatments are crucial for upholding brand image, ensuring the longevity of assets, and maintaining safety.
Graffiti Removal and Prevention
Graffiti vandalism is a significant and costly problem for transport operators worldwide. It defaces property, can obscure important information or safety warnings, and creates a negative perception of the environment. Effective management involves both reactive removal strategies and proactive preventative measures.
- Effective Graffiti Removal Techniques and Products:
The approach to graffiti removal depends on the type of graffiti (spray paint, markers, etc.), the nature of the surface (painted metal, plastic, glass), and the age of the graffiti. Manual application of chemical removers is a common method.
Several specialized products are available:- Protectcoat Graffiti Remover Train-N: This is a gel-formulated remover specifically designed for the exteriors of trains, metros, trams, and buses. It has gained approval from numerous European train manufacturers. Application is typically done with a brush or roller, allowing a dwell time of 5 to 25 minutes depending on the severity of the graffiti, followed by thorough rinsing with warm water under appropriate pressure. For stubborn paint, agitation with a non-scratching nylon scouring pad may be necessary.
- Autoglym Professional Graffiti Remover: A citrus oil-based product that works quickly to remove graffiti and other contaminants from various vehicle surfaces, including OEM paintwork, without causing damage. It is applied with a cloth or applicator sponge, allowed to dwell for up to 3 minutes, and then wiped over with a clean damp cloth or sponge. An Autoglym Magic Sponge may be used for more persistent marks.
- Hydron AG3: Mentioned as a specialist remover for metal surfaces, designed to break down graffiti compounds effectively. The general procedure for chemical removal involves testing the product on an inconspicuous area first to ensure compatibility, applying the remover to the affected area, allowing the recommended dwell time for the chemical to work, gently agitating the graffiti if needed (using soft brushes or non-abrasive pads to avoid damaging the underlying surface), and finally, rinsing the surface thoroughly with clean water to remove all residues.
- Eco-Friendly Graffiti Removers:
Recognizing the environmental and health concerns associated with harsh solvents, there is a growing market for eco-friendly graffiti removal solutions that utilize biodegradable ingredients and have lower Volatile Organic Compound (VOC) content.- Transgel Graffiti Remover (MuralShield): Marketed as a powerful, environmentally friendly gel solution effective against aged, hardened, or sun-baked spray paint on diverse surfaces, including trains. Its gel consistency allows for prolonged contact time, aiding in the delamination of heavy vandalism. It is suitable for sensitive removals where pressure washing might not be appropriate.
- TAGINATOR® and TAGAWAY®: These products are promoted as 100% biodegradable graffiti removers. TAGINATOR® is designed for unpainted masonry surfaces, while TAGAWAY® is formulated for smooth and painted surfaces, including stainless steel buses and trains. They claim to be effective in all climates and compliant with EPA and CARB VOC limits.
- MPEI’s Eco Range: Products such as OFF Graffiti Remover Eco Gel, OFF Graffiti Remover Eco (liquid), and OFF Graffiti Wipes are presented as sustainable options. MPEI advises using thickened gel products for larger areas to minimize chemical usage and wipes or sprays for smaller tags for more targeted application.
- Application of Anti-Graffiti Coatings and Films (Permanent vs. Sacrificial):
Proactive protection is often more cost-effective in the long term than repeated graffiti removal. Anti-graffiti coatings and films create a barrier that either prevents paint from adhering properly or makes its removal significantly easier, often with just mild detergents or low-pressure water. These systems fall into several categories:- Sacrificial Coatings: These are typically clear, thin-film emulsions or solutions applied to the surface. When the surface is defaced with graffiti, the sacrificial coating itself, along with the graffiti, is removed (often using hot water blasting or specific cleaners). A new layer of the sacrificial coating is then reapplied. This method protects the underlying substrate from direct contact with graffiti and harsh removal agents.
- Semi-Sacrificial Coatings: These are generally higher-build coatings (often acrylics) that are designed to shed a few microns of their surface layer each time graffiti is scrubbed off. After several cleaning cycles, and before the coating is entirely worn away, additional coats are reapplied to restore the protective layer.
- Permanent (Non-Sacrificial) Coatings: These are highly durable coatings, often two-pack systems like fluoropolymers or polyurethanes, designed to withstand multiple graffiti removal cycles without needing reapplication. They form a hard, non-porous surface that is resistant to solvents and makes it difficult for graffiti paint to bond. Some permanent treatments are invisible surface modifiers that alter the surface tension of the substrate, lowering the adhesion of graffiti, which can then be removed relatively easily. Dulux, for example, offers a range of Surfaceshield® products and clearcoats like Acrathane® IF and Durethane® that fall into this category. MPEI’s OFF Zeus and MPE Firstcoat are also marketed as graffiti protection products.
- Anti-Graffiti Films: While not extensively detailed for trains in the provided materials, transparent anti-graffiti films are commonly used, especially on windows and other smooth surfaces. These films act as a sacrificial barrier; when vandalized, the film is simply peeled off and replaced, protecting the original surface underneath.
The ongoing challenge of graffiti vandalism fuels an “arms race” between those who deface property and those who protect it. This dynamic drives continuous innovation in both reactive removal products and proactive protective coatings. As vandals experiment with different types of paints and markers, removal solutions must evolve to be effective against a wider array of substances.
Simultaneously, the high cost and labor involved in frequent graffiti removal push operators towards investing in more durable and effective anti-graffiti coatings. Compounding this is the increasing awareness of health hazards associated with traditional aggressive solvents , which in turn stimulates demand for safer, more eco-friendly alternatives for both removal and protection. This cyclical process of problem, solution, new challenge (e.g., harshness of the solution), and newer, improved solution characterizes a constantly evolving field in surface maintenance.
- Safety During Graffiti Removal (Chemicals, PPE):
Graffiti removal often involves the use of aggressive chemical agents that can pose significant health risks to workers if not handled correctly. Many removers contain solvents like d-limonene, ethylene glycol ethers (some of which can have reproductive and hematological toxicity), or other volatile organic compounds that can cause respiratory irritation, skin allergies, dermatitis, headaches, dizziness, or more severe effects with prolonged exposure. Some anti-graffiti coatings may contain isocyanates, which are powerful respiratory and skin sensitizers.
Therefore, strict safety precautions are essential:- Personal Protective Equipment (PPE): Workers must wear appropriate PPE, including chemical-resistant gloves, safety goggles or face shields to protect against splashes, and respiratory protection (e.g., organic vapor respirators) when working with solvent-based products or in poorly ventilated areas.
- Ventilation: Good ventilation is crucial to minimize the concentration of chemical vapors in the breathing zone, especially when working in enclosed or semi-enclosed spaces like inside buses or train cars.
- Chemical Handling: Always read and follow the manufacturer’s Safety Data Sheet (SDS) and product instructions. Test the remover on a small, inconspicuous area first. Avoid direct skin and eye contact. Wash hands thoroughly after use and before eating, drinking, or smoking.
Table 5: Selected Graffiti Removal Product Overview
Product Name | Chemical Basis/Type | Suitable Surfaces | Application Method | Dwell Time | Eco-Friendly Claim | Key Features |
---|---|---|---|---|---|---|
Protectcoat Train-N | Gel form | Train, metro, tram, bus exteriors | Brush, paintbrush, roller | 5-25 minutes | Not specified | Approved by many European train manufacturers, quick result. |
Autoglym Graffiti Remover | Citrus oil based | Trains, buses, coaches, OEM paintwork, other surfaces | Cloth, applicator sponge | Up to 3 minutes | Not specified | Gets to work quickly, does not damage OEM paintwork. |
Transgel (MuralShield) | Gelled solvent | Masonry, metal, asphalt, wood, trains, buildings | Thick layer, brush | Min. 20 mins (can be overnight) | Yes | Environmentally friendly, minimal odor, non-toxic, good for aged/hardened paint. |
TAGAWAY® | Blend of biodegradable ingredients | Smooth/painted surfaces (street signs, stainless steel buses/trains, glass) | Not specified | Not specified | Yes (100%) | Removes spray paint, lacquers, markers; works in hot/cold temps; VOC compliant. |
OFF Graffiti Remover Eco Gel / Eco / Wipes | Not specified (marketed as “Eco”) | General surfaces (trains implied) | Gel: Not specified; Spray/Wipes | Not specified | Yes | Sustainable options; thickened gel for large areas, spray/wipes for smaller tags to minimize chemical use. |
Table 6: Anti-Graffiti Coatings Overview
Coating Type | Example Product(s) (if specified) | Mechanism | Durability | Reapplication Needs | Cleaning Method Post-Graffiti |
---|---|---|---|---|---|
Sacrificial | Not specified by brand in snippets | Thin clear film; coating is removed with graffiti, protecting substrate. | Low (single defacement) | After each graffiti removal. | Hot water blast, specialized cleaners (removes coating). |
Semi-Sacrificial | Not specified by brand in snippets (often acrylics) | Higher build; sheds a few microns with each cleaning. | Medium (several cleaning cycles) | After several cleaning cycles / before full wear-through. | Scrubbing (removes thin layer of coating). |
Permanent (Non-Sacrificial) | Dulux Surfaceshield® types, Acrathane® IF Clearcoat, Durethane® | Durable, non-porous surface (e.g., fluoropolymers, polyurethanes) or surface tension modification. | High (withstands repeated cleanings) | Normally not required after graffiti removal. | Medium to high-pressure hot water wash, mild detergents. |
Livery and Graphic Cleaning and Maintenance
A train’s livery—its distinctive paint scheme, logos, decals, and vinyl wraps—is a core part of its brand identity and often carries essential passenger information or advertising. Proper cleaning and maintenance are vital to preserve its appearance, legibility, and longevity.
- Cleaning Painted Surfaces, Decals, and Vinyl Wraps:
- General Approach: The primary rule for cleaning livery and graphics is to use gentle methods and non-abrasive materials. For general cleaning of surfaces protected with finishes like Signshine (a protective varnish for graphics), a mild liquid detergent and water solution applied with a non-abrasive rag or sponge is recommended. It is crucial to avoid harsh chemicals or high-pressure washing that could lift the edges of decals or vinyl wraps, or damage the paint.
- Painted Surfaces: For routine washing of painted train exteriors, pH-neutral cleaners like Ecowash Autoshine are suitable as they are not detrimental to properly applied paintwork and can help build a soil-resistant finish. Products like Oxalwash, while designed for tougher contaminants like iron stains, also claim to enhance the shine on paintwork.
- Vinyl Wraps and Decals: These require regular washing with mild, non-abrasive soap and water to remove dust, dirt, and pollutants that can degrade the vinyl over time. Stains from bird droppings, tree sap, or insects should be addressed immediately by soaking the affected area with warm, soapy water and gently wiping them away, as these substances can be corrosive. Hand washing is the preferred method for vehicles with vinyl wraps or decals. If an automatic car wash must be used, a touchless option is recommended to minimize the risk of peeling or lifting the vinyl edges. Prolonged exposure to direct sunlight should be minimized where possible, as UV radiation can cause fading and degradation over time, even with UV-protective layers. Regular inspection for lifting edges, scratches, or fading allows for timely repairs.
The maintenance of train livery involves a careful balance. On one hand, the aesthetic appeal is paramount for brand image and passenger perception. On the other, the materials used (paints, vinyls) must be durable enough to withstand harsh operational environments and frequent cleaning. Specialized protective finishes like Signshine or the careful selection of gentle yet effective cleaning agents demonstrate that livery is not merely applied but must be actively managed as an asset. The choice of livery material and the subsequent cleaning regimen are thus interconnected decisions that significantly impact the long-term appearance, durability, and maintenance costs associated with the rolling stock.
- Precautions to Prevent Damage:
Several precautions should be taken to avoid damaging livery and graphics during cleaning:- Avoid using abrasive brushes, flails, or scouring pads, especially in automated wash systems, as these can catch loose edges of graphics, dull the finish, or scratch the paint or vinyl.
- Do not use harsh chemicals, petroleum-based solvents (like gasoline or oil), or acid-based cleaners on vinyl wraps or decals, as these can degrade the material and adhesive. If accidental contact occurs, rinse the area immediately with water.
- Always test any cleaning solution on a small, inconspicuous area of the livery first to ensure compatibility and prevent widespread damage.
- When using pressure washers on vinyl-wrapped surfaces, avoid directing the high-pressure spray directly at the edges of the vinyl, as this can cause it to lift or peel.
- Eco-Friendly Cleaners for Livery:
Eco-friendly options are available for cleaning train livery, minimizing environmental impact while maintaining effectiveness.- Blue Gold Spray Wash: This product is described as a non-caustic, biodegradable industrial cleaner that is safe for use on aluminum and other metals. Its ingredients are reported to be on an EPA accepted list, and it does not contain silicone defoamers, metal compounds, or halogenated hydrocarbons.
- RailX®: Formulated as an organic solvent for removing heavy oil, asphalt, wax, and other hydrocarbon-based contaminants from railcar components and surfaces. It is promoted as non-hazardous, partially biodegradable, non-corrosive, and non-toxic. While primarily for degreasing, its properties suggest it could be suitable for spot cleaning specific types of contamination on livery.
- Previously mentioned products like Ecowash Autoshine (pH neutral, suitable for reclaim units) and Oxalwash (no mineral acids) also offer gentler, more environmentally considerate profiles for exterior cleaning.
Corrosion Protection: Safeguarding Rolling Stock Integrity
Corrosion is a relentless threat to the structural integrity, safety, and operational lifespan of railway vehicles. It is exacerbated by exposure to moisture, atmospheric pollutants, cargo residues, and particularly by de-icing chemicals (such as sodium chloride, calcium chloride, and magnesium chloride) used in winter conditions. Effective corrosion protection is a critical aspect of rolling stock maintenance.
- Identifying Corrosion-Prone Areas:
Certain areas of a train are more susceptible to corrosion than others. These include the undercarriage and bogies, which are constantly exposed to track debris, water spray, and contaminants. Couplers, welds, and areas where moisture can collect or become trapped are also vulnerable. Components directly exposed to de-icing salts sprayed from the track or roads are at high risk. Specific parts like track bases, pins, collars connecting rails to ties, and the support ties themselves (whether wood, concrete, or plastic) also require protection.74 - Protective Coatings and Treatments: Types and Application:
A multi-faceted approach involving various types of coatings and treatments is typically employed for robust corrosion protection.- Primers: Proper surface preparation, including cleaning and sometimes sanding, is essential before applying any protective coating. Epoxy primers are often applied to cleaned metal surfaces, especially inside structural parts like rails and pillars, before assembly to provide a foundational layer of protection. Weld-through primers, which are generally zinc-based, are applied to mating surfaces prior to welding. The zinc acts as a sacrificial anode, corroding preferentially to protect the steel.
- Anti-Corrosion Compounds: For enclosed areas such as the interior of rails, pillars, and rocker panels, anti-corrosion compounds are applied. These are often waxy or oily substances delivered as a mist coat using specialized wands inserted through access holes. They are designed to creep into seams and flange areas, displacing moisture and sealing off the metal from corrosive elements. Some vehicle makers recommend a double application for enhanced protection.
- Specialized Protective Coatings:
- Rust Grip®: This is a one-coat polyurethane system that reportedly penetrates into the pores of rusted or clean metal (and even concrete), locks down the surface, and stops further corrosion. It has been tested and certified to encapsulate existing lead-based paints after power washing, eliminating the need for costly and hazardous sandblasting. It is used on various railway applications including track components, support ties, bridges, locomotive bodies, and passenger car roofs.
- Moist Metal Grip: A coating specifically designed for application on metal and concrete surfaces that are constantly wet or periodically submerged, providing protection against weathering, water, and chemicals.
- Enamo Grip®: Often used as a durable, high-gloss topcoat over other protective systems like Rust Grip® or thermal insulation coatings (like Super Therm®). It provides an aesthetic finish, can be tinted to various colors, and offers additional protection, including resistance to graffiti.
- Fluid Film®: This is a lanolin-based (wool wax) rust inhibitor and lubricant that penetrates metal surfaces, displaces water, and provides long-lasting corrosion protection. It is solvent-free and does not dry out. While commonly marketed for automotive undercoating, trucks, and machinery, its properties make it suitable for analogous applications on rolling stock components exposed to corrosive environments.
- Application Methods: The application method depends on the specific product and the area being treated. Primers and coatings can be applied by spraying, brushing, or rolling. Anti-corrosion compounds for enclosed sections are typically sprayed using wands. Fluid Film® can be applied via spray gun, brush, or roller. Regular cleaning to remove corrosive agents like road salts is also a crucial preventative measure before or in conjunction with applying protective coatings.
Effective corrosion control on rolling stock is rarely achieved with a single product or a one-time application. It is typically a systematic process involving multiple layers and strategies. For instance, protecting enclosed structural members might involve applying an epoxy primer to the cleaned metal before assembly, followed by an application of an anti-corrosion compound after assembly.
For exterior surfaces, a system might include a penetrating and encapsulating coating like Rust Grip® to address existing rust and provide a strong base, followed by a durable topcoat like Enamo Grip® for color, gloss, and additional environmental resistance. The specific combination of products and methods chosen will depend on factors such as the location on the train (e.g., undercarriage vs. exterior body), the substrate material, the severity of the corrosive environment (e.g., high exposure to de-icing salts ), and the desired lifespan of the protection.
This complexity and the need for careful surface preparation and application underscore the value of specialized expertise in implementing corrosion protection measures.
- Safety and Environmental Considerations in Corrosion Protection:
The application of corrosion protection products involves handling chemicals and requires attention to safety and environmental impact.- Chemical Handling and PPE: Many industrial coatings, primers, and inhibitors contain chemicals that can be hazardous. Workers involved in their application must be trained in safe handling procedures, understand the risks outlined in Safety Data Sheets (SDS), and use appropriate PPE. This typically includes gloves, eye protection, and respiratory protection, especially when spraying solvent-based materials or working in confined areas (general principles from are applicable).
- VOC Content: The Volatile Organic Compound (VOC) content of coatings is an environmental concern due to their contribution to air pollution. Regulations often limit VOC levels, and there is a trend towards using lower-VOC or VOC-free formulations where possible.
- Waste Disposal: Proper management and disposal of used containers, leftover materials, and any waste generated during surface preparation (e.g., old paint chips, blasting media) are essential to comply with environmental regulations.
- Environmental Impact of Related Materials: De-icing agents, which contribute to corrosion, also have their own environmental impacts. The selection and application of de-icers should consider their corrosive properties and potential harm to water bodies and soil. Railway operators are advised to have written plans for de-icing activities, including details on product storage, application methods, site drainage, and an assessment of potential environmental impacts. Some corrosion inhibitors, like Fluid Film®, are marketed as environmentally friendly due to their lanolin base.
Table 7: Selected Corrosion Protection Methods and Products for Rolling Stock
Protection Method/Product Type | Example Product(s) | Primary Application Area | Key Protective Properties | Application Notes |
---|---|---|---|---|
Epoxy Primer | Generic two-part epoxy primers | Cleaned interior surfaces of structural parts (rails, pillars) before assembly. | Adhesion base for further coatings, initial corrosion barrier. | Requires thoroughly cleaned (mechanically and chemically) surface for proper adhesion. |
Anti-Corrosion Compound | Generic cavity wax / rust-proofing compounds | Inside enclosed areas (rails, pillars, rocker panels) after assembly. | Displaces moisture, creeps into seams, seals off metal from corrosive elements. | Applied as a mist coat using a wand through access holes; some recommend double application. |
Penetrating Rust Inhibitor | Fluid Film® | Undercarriage, all metals, moving parts, heavily corroded/frozen parts. | Penetrates existing rust, displaces water, long-lasting lubrication, solvent-free, lanolin-based. | Can be sprayed, brushed, or rolled. Good for undercoating vehicles exposed to salt. |
Encapsulating Coating | Rust Grip® | Rusted or clean metal, concrete, lead-based paint; tracks, ties, bridges, locomotives. | Penetrates pores, locks down surface, stops continued corrosion, encapsulates lead paint, high surface tensile strength. | Applied over power-washed surfaces (no sandblasting needed for lead paint encapsulation). |
Protective Topcoat | Enamo Grip® | Over Rust Grip® or Super Therm®; exterior body, roofs, areas needing color/gloss. | Durable, high gloss, color options, graffiti protection, chemical resistance. | Used as a topcoat for aesthetics and additional protection. |
Coating for Wet Areas | Moist Metal Grip | Metal and concrete in constantly wet or periodically submerged areas. | Protects from weathering, water, and chemicals in wet environments. | Specifically for high-moisture exposure. |
Regular Washing | Water, acidic or neutral cleaner | Trailer/vehicle undercarriage and frame. | Removes corrosive de-icing salts and chemicals. | Essential in winter; alkaline cleaners may not effectively remove salt. Rinse thoroughly. Apply protective coating afterward. |
6. The Professional Advantage: Why Expert Cleaning Services Matter
Maintaining the cleanliness, hygiene, and operational readiness of train and rolling stock is a complex and demanding undertaking. While some level of in-house cleaning is common, engaging specialized professional cleaning services often presents the most effective, efficient, and ultimately valuable approach for railway operators. The decision to outsource this critical function is supported by compelling arguments related to expertise, advanced technology, regulatory compliance, safety, and long-term cost-effectiveness.
Expertise and Specialized Knowledge
Professional cleaning companies dedicated to the transport sector bring a depth of expertise that is challenging and costly for non-cleaning businesses to replicate and maintain internally. Their personnel are typically trained in the specific requirements for cleaning various types of railcars—from passenger coaches and locomotives to specialized freight cars like tankers and hoppers.
They possess knowledge of different materials used in train construction, understand the nature of diverse contaminants (from common grime to hazardous waste or hardened residues), and are proficient in applying the most appropriate cleaning techniques and chemical agents. This includes skills in using specialized cleaning and sanitizing equipment effectively and safely.
Furthermore, staff at reputable professional cleaning firms often undergo rigorous and ongoing training programs. This can encompass certifications for OSHA compliance, detailed chemical handling protocols, procedures for safe entry into confined spaces, and protocols for managing biohazardous materials. Some firms even offer highly specialized services, such as cleaning to meet specific religious dietary requirements for cargo. This level of specialized knowledge ensures that cleaning is not only thorough but also tailored to the unique demands of each railcar and its intended use.
The “hidden overhead” associated with attempting to manage such a specialized function in-house can be substantial. Beyond direct labor, railway operators would need to invest in recruiting individuals with the right aptitude, developing and delivering comprehensive training programs (and retraining, given the often high turnover in cleaning roles ), managing these specialized staff, procuring and maintaining a diverse inventory of cleaning equipment and chemicals , and ensuring ongoing compliance with complex chemical management and waste disposal regulations. Professional cleaning services are structured to absorb these overheads efficiently due to their scale and focus, often providing a more cost-effective solution when the total cost of operation is considered.
Efficiency and Advanced Technology
Professional cleaning services are often at the forefront of adopting and implementing advanced cleaning technologies to enhance efficiency, precision, and effectiveness. This can include the use of robotic systems for certain tasks 1, sophisticated automated train washing systems for exteriors 3, and advanced disinfection technologies like electrostatic sprayers.
These technologies can significantly reduce cleaning times, improve consistency, and ensure more thorough coverage than purely manual methods. For example, innovative automated wash systems like the Orange Train Wash claim the ability to clean an eight-car train in under four minutes, demonstrating radical productivity benefits.
Beyond technology, professional firms develop streamlined processes and optimized workflows based on industry best practices and experience. They are adept at managing cleaning schedules to minimize railcar downtime, a critical factor for operational efficiency. Some services offer mobile railcar cleaning, bringing their equipment and expertise directly to the client’s site, which further reduces downtime and eliminates the costs associated with relocating railcars to a fixed cleaning facility.
Regulatory Compliance and Safety Standards
The railway industry operates under a stringent regulatory environment covering health, safety, and environmental protection. Professional cleaning services are typically well-versed in these regulations and make it their business to adhere to them. This includes compliance with standards set by bodies like OSHA (Occupational Safety and Health Administration), the EPA (Environmental Protection Agency), and, where applicable, the FDA (Food and Drug Administration). They ensure the proper handling, storage, and disposal of cleaning chemicals and any waste generated, including potentially hazardous materials found in railcars.
By engaging qualified professionals, railway operators can also transfer a significant portion of the risks associated with cleaning operations. Professional cleaning companies are expected to have robust safety management systems, well-trained staff who understand and implement safety protocols, and appropriate insurance coverage.
This reduces the railway operator’s liability exposure related to worker injuries (e.g., from chemical exposure, slips and falls, or confined space incidents), environmental non-compliance (such as improper waste disposal or wastewater discharge violations ), and potential damage to rolling stock caused by incorrect cleaning methods or materials. This risk mitigation aspect provides tangible financial and operational value.
Cost-Effectiveness and Long-Term Value
While outsourcing cleaning services involves a direct contractual cost, it can prove more cost-effective in the long term compared to managing the function in-house. Professional cleaning helps prevent costly damage that can arise from improper cleaning techniques or the use of incompatible chemicals.
By effectively removing corrosive substances and identifying potential issues early, regular professional cleaning contributes to extending the operational life of expensive rolling stock, delaying the need for major repairs or premature replacement. Reduced railcar downtime, achieved through efficient cleaning processes, translates directly into better asset utilization and revenue-generating potential.
Furthermore, a consistently high standard of cleanliness, as delivered by trained professionals, enhances passenger experience, which can lead to increased ridership and positive brand perception. For freight operations, clean and well-maintained railcars ensure product integrity and project reliability to customers. Avoiding regulatory penalties for non-compliance with cleanliness or safety standards also contributes to overall cost savings.
While some analyses point to profit leakage through outsourcing , these often do not fully account for the potentially higher or less efficient costs of an under-resourced or inexpertly managed in-house operation. The key lies in selecting a reputable, efficient, and professional service provider whose value proposition extends beyond mere labor cost.
Focus on Core Business Operations by Outsourcing Cleaning
For most railway companies, transportation is their core business, not cleaning. Cleaning, while essential, is a specialized, non-core activity. Outsourcing this function allows railway operators to dedicate their managerial attention, financial resources, and personnel to their primary mission of moving passengers and freight safely and efficiently. Professional cleaning companies take on the burden of recruiting, training, and managing cleaning staff, investing in and maintaining specialized equipment and supplies, and staying abreast of evolving cleaning technologies and regulatory requirements. This significantly reduces the administrative and operational load on the railway operator.
Ultimately, efficient and effective cleaning, particularly when delivered by skilled professionals, is an enabler of higher asset utilization and superior service quality. Quicker turnaround times mean railcars are available for service more consistently.
A clean and hygienic environment is a fundamental component of passenger service quality , while for freight, it is essential for maintaining cargo integrity and meeting shipper expectations. Therefore, investing in professional train and rolling stock cleaning is not merely a cost center; it is a strategic investment that supports revenue generation, operational excellence, safety, compliance, and the long-term value of critical railway assets.
The comprehensive nature of train cleaning, encompassing diverse materials, specialized equipment, stringent safety protocols, and complex regulatory landscapes, strongly indicates that the expertise and dedicated resources of professional cleaning services offer a distinct advantage.