The chimney system, encompassing fireplaces, stoves, and their venting mechanisms, is a critical component of many homes, providing warmth and ambiance. However, without diligent and professional maintenance, these systems can pose significant risks, including devastating house fires and exposure to harmful gases such as carbon monoxide.
The Indispensable Role of Chimney Maintenance
Regular chimney sweep and maintenance services are paramount for several interconnected reasons, primarily revolving around safety, operational efficiency, and the structural longevity of the chimney system and the home itself. Neglecting chimney care can lead to severe consequences.
Contact us!
Fire Prevention: The foremost reason for chimney maintenance is the prevention of chimney fires. Burning wood and other solid fuels produces byproducts, most notably creosote, a tar-like, highly flammable substance that accumulates inside the chimney flue. If this buildup is not regularly removed, it can ignite, leading to intense fires that can rapidly spread to the rest of the structure. Chimney inspections identify this creosote accumulation, and professional sweeping removes it, significantly mitigating fire risk. Furthermore, chimneys can become obstructed by bird or squirrel nests, leaves, and other debris, which can also be flammable and contribute to fire hazards.
Carbon Monoxide Safety: Carbon monoxide (CO) is an odorless, colorless, and highly toxic gas produced during the incomplete combustion of fuel. A well-maintained chimney ensures that CO and other combustion byproducts are safely vented out of the home. However, blockages from debris or creosote, or structural damage within the chimney, can impede this process, potentially forcing these dangerous gases back into living spaces. This is often referred to as the “silent killer” due to its insidious nature. Regular inspections and cleaning ensure the chimney flue is clear and structurally sound, facilitating proper ventilation and protecting occupants from CO poisoning. Even with diligent chimney maintenance, the installation of carbon monoxide detectors near fireplaces is a crucial secondary safety measure.
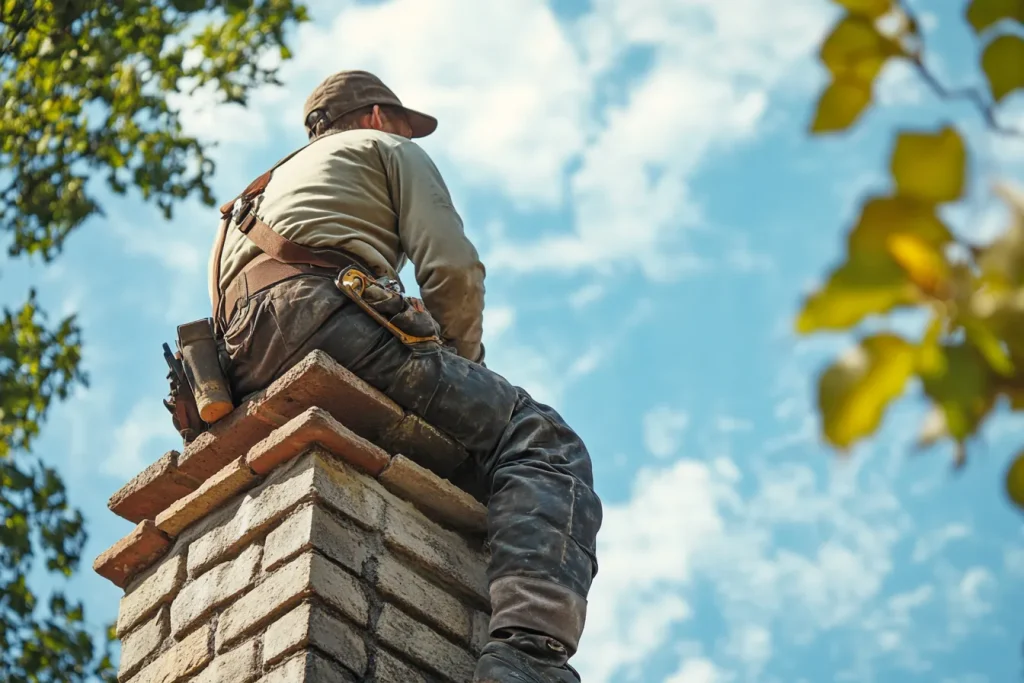
Heating Efficiency: A clean and unobstructed chimney promotes a proper draft, which is essential for the efficient combustion of fuel in fireplaces and stoves. When creosote and soot accumulate, they restrict airflow, compelling the heating appliance to work harder and less efficiently to produce the desired warmth. This not only wastes energy but can also lead to increased fuel consumption and higher heating costs. Regular cleaning helps maintain optimal appliance performance and efficiency.
Early Detection of Structural Issues: Chimneys are constantly exposed to harsh weather conditions and extreme temperature fluctuations, which can lead to the deterioration of masonry, flue liners, and other components over time. Inspections conducted by certified professionals can identify structural problems such as cracks in bricks or mortar, damaged flue liners, and issues with the chimney crown or flashing in their nascent stages. Addressing these problems early can prevent them from escalating into more significant and costly repairs, such as water leaks that compromise the chimney’s structural integrity or even lead to collapse.
Compliance with Safety Standards and Insurance Requirements: Many local building codes and homeowner’s insurance policies mandate regular chimney inspections and maintenance. Adhering to these requirements not only ensures compliance with safety regulations but may also be necessary to maintain insurance coverage. The National Fire Protection Association (NFPA) is a key organization that develops codes and standards related to fire safety, including those for chimneys, fireplaces, and venting systems. Their recommendations are widely adopted and form the basis for professional chimney service practices.
The National Fire Protection Association (NFPA) recommends that chimneys, fireplaces, and vents be inspected at least once a year, with cleaning performed as needed. This annual inspection is considered the primary method for preventing potential damage to the home or, in worst-case scenarios, loss of life resulting from a compromised chimney system.
It is important to note that inspections are necessary even if a fireplace or stove is not used frequently, as animals can build nests, debris can accumulate, and weather-related wear can still cause issues requiring attention. The “as needed” cleaning frequency is determined by the findings of these annual inspections.
Understanding Chimney Inspections: Levels and Technologies
The National Fire Protection Association’s Standard 211 (NFPA 211), “Standard for Chimneys, Fireplaces, Vents, and Solid Fuel-Burning Appliances,” is the recognized professional standard that outlines the protocols for chimney inspections. This standard, adopted in its current tiered format on January 13, 2000, defines three distinct levels of inspection: Level 1, Level 2, and Level 3. Chimney sweeps certified by the Chimney Safety Institute of America (CSIA) are tested on their knowledge and application of these three inspection levels.
It is a standard practice that if a chimney is found to be dirty (e.g., with significant creosote buildup), it must be swept before a proper and thorough inspection can be completed, as deposits can obscure underlying defects. Homeowners should always receive a copy of the inspection report detailing the findings.
NFPA 211 Chimney Inspection Levels Explained
The appropriate level of inspection is determined by the specific circumstances of the chimney and venting system.
Level 1 Inspection: Routine Check-up
- When Performed: A Level 1 inspection is conducted annually for a chimney system that is under continued service, with no changes to the appliance or venting system, and where there are no apparent signs of problems or operational concerns. It is the minimum required inspection under these conditions.
- Scope: This inspection involves a visual examination of the readily accessible portions of the chimney’s exterior and interior, as well as the accessible parts of the connected appliance and the chimney connection. The technician assesses the basic soundness of the chimney structure and flue, and verifies that the chimney is free from obstructions and combustible deposits like creosote. A Level 1 inspection is often performed in conjunction with a routine chimney sweeping. Some service providers note that a Level 1 inspection may only cover a few main fireplace components, such as the hearth, firebox, and smoke chamber, and may not be considered sufficiently thorough for all situations.
- Key Components Assessed: Readily accessible areas including the chimney structure, flue, basic appliance installation and connections, presence of obstructions, and combustible deposits.
Level 2 Inspection: In-Depth Assessment
- When Performed: A Level 2 inspection is more comprehensive and is required under several specific circumstances:
- When any changes are made to the system. This includes modifications such as a change in fuel type, alterations to the shape or material of the flue (e.g., relining), or the replacement or addition of an appliance of a dissimilar type, input rating, or efficiency.
- Upon the sale or transfer of a property. This requirement underscores the significance of chimney condition as a factor in home value and safety, highlighting that a standard home inspection may not adequately assess the chimney system. Sellers and buyers should be cognizant of this mandate, as the chimney’s state can become a point of negotiation or a critical safety disclosure during a real estate transaction.
- After an operational malfunction or an external event that is likely to have caused damage to the chimney. Such events include building fires, chimney fires, seismic activity, or severe weather events.
- Many professionals recommend a Level 2 inspection as a baseline for thoroughness.
- Scope: A Level 2 inspection encompasses all aspects of a Level 1 inspection, plus an examination of accessible portions of the chimney exterior and interior, including areas within attics, crawl spaces, and basements. It addresses proper clearances from combustible materials in these accessible locations. Crucially, a Level 2 inspection includes a visual inspection by video scanning or other means to examine the internal surfaces and joints of all flue liners within the chimney. Some professionals note that a Level 2 inspection will cover all nine primary fireplace components (hearth, firebox, smoke chamber, flue, ash dump, exterior masonry, flashing, crown, and cap), providing photographic and written documentation. Importantly, a Level 2 inspection does not require the removal or destruction of permanently attached portions of the chimney or building structure or finish to gain access.
- Key Components Assessed: All components covered in Level 1, plus accessible attics, crawl spaces, and basements; clearances from combustible materials; and a detailed examination of the internal flue liner surfaces and joints, typically conducted via video scan.
Level 3 Inspection: Investigating Hidden Hazards
- When Performed: A Level 3 inspection is recommended when a Level 1 or Level 2 inspection suggests a hidden hazard, and the evaluation of this suspected hazard cannot be performed without special tools or access to concealed areas of the chimney or flue. This level is invoked when serious hazards are suspected that cannot be confirmed through less invasive means.
- Scope: This is the most comprehensive and invasive type of inspection. It includes all areas and items checked in Level 1 and Level 2 inspections. Additionally, a Level 3 inspection involves the removal or destruction, as necessary, of permanently attached portions of the chimney or building structure to gain access to concealed areas that are the subject of the inspection. This could involve removing components such as the chimney crown, or portions of an interior chimney wall. This level of inspection addresses the proper construction and the condition of these concealed portions of the chimney structure and flue.
- Key Components Assessed: All components covered in Levels 1 and 2, plus concealed portions of the chimney structure and flue. This requires the removal of components (e.g., chimney crown, interior chimney wall) as needed to gain access to the areas under investigation.
The progression from Level 1 to Level 3 inspections illustrates a clear diagnostic pathway. A basic, routine check (Level 1) might reveal indicators that necessitate a more thorough and technologically aided examination (Level 2, often including a video scan). The findings from a Level 2 inspection could, in turn, uncover signs of severe, hidden problems that require partial demolition for a complete assessment (Level 3). This structured escalation demonstrates an evolving approach to chimney assessment, where the level of invasiveness is dictated by the evidence gathered at each preceding stage, ensuring that the most appropriate and comprehensive evaluation is performed.
The following table summarizes the key aspects of the NFPA 211 Chimney Inspection Levels:
Inspection Level | When Performed (Triggers) | Scope of Work | Key Areas/Components Inspected | Tools/Methods Used |
---|---|---|---|---|
Level 1 | Annually for systems with no changes and no apparent issues; routine maintenance. | Visual check of readily accessible areas. | Basic soundness of chimney structure & flue, appliance connections, freedom from obstructions & combustible deposits. May only cover hearth, firebox, smoke chamber. | Visual examination; often performed with a sweep. |
Level 2 | Property sale/transfer; system changes (fuel, relining, new appliance); after chimney fire, malfunction, or damaging event (seismic, weather). | All of Level 1, plus accessible portions of attics, crawl spaces, basements; internal flue examination. No destructive measures. Covers all 9 fireplace components with documentation. | All of Level 1, plus: accessible attics, crawl spaces, basements; clearances from combustibles; internal surfaces and joints of all flue liners. | Visual examination, video scan of flue interior. |
Level 3 | When Level 1 or 2 suggests a hidden hazard requiring access to concealed areas; serious hazards suspected. | All of Level 1 & 2, plus removal of components (e.g., chimney crown, walls) as necessary to access and inspect concealed areas. | All of Level 1 & 2, plus: concealed portions of chimney structure and flue, requiring removal of components like chimney crown or interior chimney wall to gain access. | Visual examination, video scan, partial demolition/removal of components. |
Video Scan Inspections: Seeing Inside Your Chimney
A chimney video scan inspection represents a significant advancement in diagnostic capabilities, offering the most effective method for accurately assessing the interior condition of a chimney and identifying hidden defects or damage. This technology utilizes specialized, high-resolution cameras that are maneuvered through the chimney flue. Video inspections are a routine and integral component of NFPA Level 2 and Level 3 inspections.
Purpose and Process: The primary purpose of a video scan is to detect problems that are not visible during a standard, external visual check or a basic look up the flue. The process typically involves a certified technician inserting a camera system into the chimney. Some advanced systems employ dual cameras: one providing a 360-degree horizontal view to cover the entire cross-section of the flue, and another fixed camera offering a vertical view up or down the flue.
The technician carefully analyzes the live or recorded footage to identify issues such as cracks in the flue liner, deteriorated mortar joints, blockages from debris or animal nests, excessive creosote buildup, or structural damage like collapsed flue tiles. Following the scan, the homeowner receives a detailed report of the findings, often including images or video, and recommendations for any necessary repairs or maintenance.
Benefits: The advantages of video scan inspections are manifold:
- Detection of Hidden Damage: They precisely identify cracks, breaks, spalling, deterioration, and other internal structural issues that would otherwise go unnoticed.
- Enhanced Fire Prevention: By accurately locating and assessing the extent of creosote buildup, video scans play a crucial role in preventing chimney fires.
- Ensuring Proper Ventilation: Obstructions such as animal nests, fallen debris, or collapsed flue tiles, which can lead to dangerous backdrafting of smoke and carbon monoxide, are clearly identified.
- Aid in Real Estate Transactions: A detailed video inspection report provides invaluable, objective information about the chimney’s condition for both buyers and sellers of a property.
- Support for Insurance Claims: Visual documentation from a video scan can serve as crucial evidence when filing insurance claims for chimney damage resulting from events like chimney fires or lightning strikes.
The increasing prevalence and technological sophistication of video scan equipment signify a broader shift towards more accurate, objective, and evidence-based diagnostics in chimney care. This reliance on visual proof moves chimney assessments beyond subjective interpretations or purely verbal reports. Homeowners are empowered with clearer, demonstrable information regarding the condition of their chimney, allowing for more informed decisions about maintenance and repairs.
This transparency fosters greater trust and understanding between the service professional and the homeowner.
Chimney Sweeping and Cleaning: Clearing the Way for Safety
Chimney sweeping is the process of removing accumulated hazardous materials from the interior of the chimney flue, primarily soot and creosote, as well as any blockages. This service is fundamental to preventing chimney fires and ensuring the efficient and safe operation of fireplaces and heating stoves.
The Science of Soot and Creosote: Understanding Buildup
When wood is burned, the combustion process is rarely complete, leading to the production of smoke containing various unburned, volatile substances. As this smoke ascends a relatively cooler chimney, these substances condense on the interior surfaces of the flue, forming deposits known as creosote.
Creosote can manifest in several forms, from a fine, flaky soot to a sticky, tar-like glaze, or a hard, brittle deposit. Regardless of its form, creosote is highly flammable and is the primary fuel for most chimney fires. Soot, another byproduct of incomplete combustion, also contributes to flue blockages and can be flammable, though generally less so than creosote.
The Chimney Safety Institute of America (CSIA) recommends that chimneys be swept when there is 1/8 inch of sooty buildup, and even sooner if any glaze (a particularly hazardous form of creosote) is present in the system. Fire safety experts consider this level of accumulation sufficient to cause a chimney fire capable of damaging the chimney structure or spreading to the home.
Several factors influence the rate of creosote and soot buildup, including the frequency of fireplace or stove use, the type of wood burned (unseasoned or “green” wood produces more creosote than dry, seasoned hardwood), the appliance’s burning efficiency, and the chimney’s draft characteristics.
The “1/8 inch rule” for sweeping provides a tangible and useful metric for homeowners. However, this guideline is nuanced by the type of deposit observed. For instance, glazed creosote is significantly more hazardous and difficult to remove than flaky soot, and can pose a severe fire risk even if its accumulation is less than 1/8 inch thick. Furthermore, usage patterns, such as frequent, slow-burning fires, can accelerate creosote formation.
This implies that relying solely on a fixed cleaning timeframe or a simple depth measurement by an untrained individual is insufficient. A professional assessment by a certified chimney sweep, who can accurately identify the type and severity of creosote buildup, is crucial for determining the appropriate cleaning schedule.
Professional Chimney Sweeping Methods
Professional chimney sweeps employ a range of specialized tools and techniques to effectively and safely remove creosote, soot, and other debris from chimney flues.
Mechanical Cleaning: Brushes, Rods, Rotary Systems
The cornerstone of mechanical chimney cleaning involves the use of chimney brushes. These brushes are available in a wide variety of shapes (round, square, rectangular to match flue dimensions), sizes, and materials. Metal bristle brushes are typically used for robustly scraping off hard, stubborn creosote deposits from durable masonry flues, while softer nylon or polypropylene brushes are employed for lighter cleaning tasks or in chimneys with more delicate liners, such as stainless steel, to prevent scratching or damage. Selecting the correct brush size and type for the specific flue is critical for effective cleaning; a brush that is too large can become lodged, while one that is too small will not clean thoroughly.
These brushes are attached to flexible or rigid rods and extenders, which allow the sweep to reach and clean the entire length of the chimney flue, from the firebox or appliance connection to the chimney top. For heavily soiled chimneys or those with particularly tenacious deposits, professionals may utilize rotary cleaning systems. These systems consist of motorized rotating brushes or chains (sometimes called whips) that provide a more aggressive and thorough cleaning action.
Chemical Creosote Removers
In some cases, particularly with stubborn glazed creosote (often referred to as Stage 3 creosote), mechanical cleaning alone may not be sufficient or could risk damaging the flue liner. In such instances, chemical creosote removers can be employed. These products typically work by catalyzing chemical reactions that alter the composition of the creosote, breaking it down or converting it into a less adherent, more powdery substance that can then be more easily removed by mechanical sweeping. Some chemical treatments are applied during a fire, while others are sprayed or applied directly onto the deposits.
It is important to note that these are professional-grade products, and their use should be followed by a thorough sweeping and inspection to ensure all treated creosote is removed and to verify the condition of the flue. A simple DIY alternative for loosening minor creosote involves a paste made from equal parts water and baking soda, though this is generally less potent than commercial chemical removers.
Specialized Vacuum Systems (HEPA filters)
A critical aspect of professional chimney sweeping is the containment and removal of dislodged soot, creosote, and debris. Professional sweeps utilize high-powered industrial vacuum systems specifically designed for this purpose.
These vacuums are often equipped with High-Efficiency Particulate Air (HEPA) filters, which are capable of trapping very fine airborne particles, including soot and creosote dust, preventing them from contaminating the home environment and posing respiratory health risks. Standard household vacuums are not suitable for this task, as their filters are typically not fine enough to capture these microscopic particles, and their motors may not be robust enough to handle the volume of debris.
Debris and Blockage Removal
Beyond creosote and soot, chimney sweeping also addresses the removal of various types of obstructions that can accumulate within the flue. These include animal nests (birds, squirrels, raccoons), fallen leaves, twigs, and other debris. Such blockages are not only fire hazards themselves but also significantly impede the proper drafting of the chimney, which can lead to smoke and carbon monoxide entering the home.
Recommended Cleaning Frequency (NFPA/CSIA Guidelines)
The consensus among leading safety organizations is that chimneys should be inspected annually, with cleaning performed as needed based on the inspection findings. The NFPA advocates for annual inspections of all chimneys, fireplaces, vents, and solid fuel-burning appliances. The CSIA provides a more specific benchmark for cleaning, recommending that it occur when creosote or soot buildup reaches a thickness of 1/8 inch, or sooner if glazed creosote is present.
The actual frequency of “as needed” cleaning can vary significantly based on several factors:
- Usage: Homeowners who use their fireplaces or wood stoves frequently (e.g., more than three times per week during the heating season, or as a primary heat source) will likely require more frequent cleaning, possibly more than once a year.
- Fuel Type: The type of wood burned has a substantial impact. Burning unseasoned, wet, or softwoods (like pine) produces significantly more creosote than burning dry, seasoned hardwoods and may necessitate more frequent sweeping.
- Appliance Type and Burning Habits: Modern, high-efficiency stoves generally produce less creosote than older, less efficient models or open fireplaces. Consistently burning fires at too low a temperature (smoldering fires) can also increase creosote production. Some sources offer additional guidelines, such as cleaning after every 50 to 70 uses, or after burning a specific quantity of wood, like a face cord. Ultimately, the annual inspection by a qualified professional is the most reliable way to determine the appropriate cleaning schedule for a specific chimney system.
Essential Chimney Repair and Maintenance Services
Beyond inspection and cleaning, a variety of specialized repair and maintenance services are often necessary to keep a chimney system functioning safely and efficiently, and to protect the structural integrity of the chimney and the home.
Chimney Waterproofing: Protecting Your Masonry from Moisture Damage
Masonry chimneys, constructed from materials like brick, stone, and mortar, are inherently porous and can absorb significant amounts of water from rain and snow. This moisture penetration is a primary cause of chimney deterioration.
Purpose and Benefits: The main purpose of chimney waterproofing is to create a barrier that prevents water from being absorbed into the masonry, thereby protecting it from damage. The benefits are numerous: it helps prevent bricks from cracking and spalling (flaking or peeling) due to freeze-thaw cycles (where absorbed water freezes, expands, and breaks the masonry), reduces the likelihood of leaks into the home, helps maintain the structural integrity of the chimney, and ultimately extends its service life.
Effective waterproofing can protect a chimney for 15 to 20 years, provided it is accompanied by proper overall chimney maintenance. Common signs indicating water damage and the need for waterproofing include efflorescence (a white, powdery salt deposit on the brick surface), cracked or spalling bricks, and deteriorating mortar joints.
Methods and Types of Water-Repellent Sealants: The most common method of waterproofing is the application of a specialized water-repellent sealant to the exterior masonry surfaces of the chimney. It is crucial that these sealants are vapor-permeable. This means that while they prevent liquid water from penetrating from the outside, they allow water vapor (moisture that may already be in the masonry or that wicks from the interior of the home) to escape or “breathe” out. If a non-permeable sealant is used, it can trap moisture within the masonry.
This trapped moisture can then freeze and expand during cold weather, leading to spalling and potentially causing more damage than if no sealant had been applied at all. This underscores the critical importance of selecting and applying the correct professional-grade waterproofing product, a task best handled by experienced technicians.
Several types of sealants are available, though not all are ideal for chimneys:
- Polyurethane sealants: While effective for wood, they often remain tacky and are generally not recommended for masonry chimneys.
- Silicone sealants: These can be suitable for masonry and synthetic materials, offering good water repellency.
- Water-based sealants: These typically have lower volatile organic compounds (VOCs) and are often breathable, making them a good choice for chimneys.
- Silane/siloxane sealers: These are penetrating sealers that react chemically within the masonry to form a hydrophobic barrier. They are highly effective for concrete and masonry surfaces, offering deep protection while maintaining breathability. These are often the preferred choice for professional chimney waterproofing.
Chimney Crown Repair and Rebuilding: The First Shield Against the Elements
The chimney crown (also known as a chimney wash) is the cement or masonry slab that covers the top of the chimney, surrounding the flue opening(s). Its primary function is to shed water away from the chimney structure and prevent it from entering the space between the flue liner and the chimney walls.
Common Issues: Chimney crowns are highly susceptible to damage due to their exposed position. Common issues include:
- Cracking: This is the most frequent problem, often resulting from poor initial construction (e.g., using standard mortar mix instead of a proper concrete mix, insufficient thickness, or lack of reinforcement), shrinkage of materials as they cure, the natural aging process and wear from weather exposure, and stresses from freeze-thaw cycles.
- Deterioration: Over time, the crown material can crumble or erode.
Dangers of a Damaged Crown: A damaged or cracked crown is a significant vulnerability for the entire chimney system. It serves as a primary entry point for water infiltration, which can then lead to a cascade of further problems. These include:
- Rusting of metal components like dampers or prefabricated fireboxes.
- Damage to the flue liner.
- Deterioration of the chimney’s masonry (bricks and mortar) from the inside out.
- Growth of mold and mildew within the chimney structure or adjacent parts of the home.
- Potential structural damage to the chimney, possibly causing it to lean or, in severe cases, collapse.
- Increased fire risk if heat and embers can escape through cracks into combustible parts of the chimney structure, or if carbon monoxide can leak into the home. The chimney crown’s condition is pivotal; its failure often initiates a sequence of more extensive and costly damages throughout the chimney system. Therefore, maintaining a sound crown is a high-leverage preventative measure.
Repair Techniques & Preventative Measures: The approach to repairing a chimney crown depends on the extent of the damage:
- Minor Cracks: Small, hairline cracks can often be sealed with a high-quality waterproof masonry sealant or a specialized crown coating product to prevent water entry.
- Moderate Cracks: If the cracks are more significant but the crown remains structurally sound, a flexible crown coating material (often an elastomeric sealant) can be applied over the entire surface. This fills larger cracks and provides a durable, waterproof membrane.
- Severe Damage: If the crown is severely cracked, crumbling, or improperly constructed, it will likely need to be partially or fully rebuilt. A proper rebuild involves using a high-quality, weather-resistant concrete mix (not standard brick mortar), ensuring adequate thickness, proper reinforcement (like wire mesh), an overhanging drip edge to direct water away from the chimney sides, and a correct slope to facilitate water runoff. Preventative measures include regular inspections, application of waterproof sealants to a sound crown, and the installation of a chimney cap, which can help protect the crown from direct weather exposure.
Chimney Cap Installation and Repair: Keeping Unwanted Elements Out
A chimney cap is a protective covering installed at the very top of the chimney, over the flue opening(s).
Functions: Chimney caps serve multiple important functions:
- Water Barrier: They prevent rain and snow from entering the chimney flue, thereby protecting the flue liner, damper, and firebox from moisture damage, and reducing freeze-thaw damage to the masonry.
- Debris Blocker: They keep leaves, twigs, and other windblown debris from falling into the chimney and creating blockages or fire hazards.
- Critter Deterrent: Most caps include a mesh screen that prevents birds, squirrels, raccoons, and other animals from entering the chimney to nest or seek shelter. Animals in chimneys can cause blockages, unpleasant odors, and can become trapped.
- Spark Arrester: The mesh screen also functions as a spark arrester, catching hot embers that may be carried up the flue with the smoke and preventing them from landing on the roof or nearby combustible materials, thus reducing the risk of external fires.
- Downdraft Reduction: Some specialized caps, like wind-directional caps, are designed to help reduce or prevent downdrafts caused by wind patterns around the chimney.
Types of Caps: Chimney caps are available in various types, materials, and styles:
- Mounting Types:
- Flue-Mount (Inner/Outer Mount): These caps attach directly to the exposed portion of the flue liner(s) using clamps, pressure-fit springs, or set screws. They are typically used for single, round flues.
- Top-Mount (Crown-Mount): These caps are larger and attach to the chimney crown itself, often covering multiple flues or the entire top surface of the chimney.
- Specialized Types:
- Wind-Directional Caps: Designed to pivot with the wind or use turbines to improve draft and combat downdrafts in windy locations.
- Air-Cooled Chimney Caps: Specifically designed for air-cooled (double or triple-wall) factory-built chimney systems.
- Custom Caps: Fabricated to fit uniquely shaped or sized chimney tops.
- Materials: Stainless steel and copper are highly recommended for their durability and resistance to rust and corrosion, often coming with lifetime warranties. Galvanized steel caps are less expensive but prone to rusting over time. Aluminum caps should generally be avoided as they are less sturdy and can be damaged or removed by animals like raccoons.
Installation, Maintenance, and Common Repairs: While simple flue-mount caps might be a DIY task for some homeowners comfortable working on a roof, top-mount caps typically require drilling into the masonry crown and sealing the attachment points, a job often best left to professionals to ensure a secure and watertight fit. Professional installation guarantees the correct type and size of cap is chosen and properly secured.
Maintenance is generally minimal, especially for stainless steel or copper caps. It involves periodically checking for accumulated leaves or debris around the cap, ensuring any moving parts (on wind-directional caps) are functioning correctly, and inspecting the mesh screen for any holes or damage that could allow animal entry. Galvanized or painted caps should be inspected for rust; rust stains on the chimney exterior are a sign that the cap is deteriorating and needs replacement. Caps can also be damaged by high winds, falling tree limbs, or severe weather.
The following table offers a comparative overview of common chimney cap types:
Cap Type | Material Examples | Primary Functions | Typical Installation Method | Best Suited For |
---|---|---|---|---|
Flue-Mount | Stainless Steel, Copper | Water/debris/animal barrier, spark arrester | Clamps/screws to flue liner | Single, exposed flue liners (often round). |
Top-Mount/Crown-Mount | Stainless Steel, Copper | Water/debris/animal barrier, spark arrester; covers entire crown/multiple flues | Screws into chimney crown, sealed | Chimneys with multiple flues or where full crown coverage is desired. |
Wind-Directional | Stainless Steel | All standard functions, plus downdraft reduction, draft enhancement | Mounts to flue or crown | Chimneys in windy areas or those experiencing downdraft issues. |
Custom Cap | Stainless Steel, Copper | Tailored protection for unique chimney designs | Varies based on design; professional install | Non-standard chimney tops, aesthetic considerations. |
Chimney Liner Repair and Installation (Relining): Ensuring a Safe Passage for Smoke
The chimney liner, or flue liner, is a critical safety component of the chimney system. It is the passageway within the chimney structure through which smoke, gases, and combustion byproducts are vented from the fireplace or appliance to the outside. A sound liner protects the chimney walls from heat and corrosion and prevents toxic gases like carbon monoxide from leaking into the home and heat from transferring to combustible materials surrounding the chimney.
Reasons for Relining: Chimney liners can deteriorate or become damaged over time due to several factors, necessitating repair or replacement (relining) :
- Cracked or Damaged Flue Tiles: Clay tile liners can crack, break, or spall due to thermal shock (rapid temperature changes), chimney fires, seismic events, or settling of the house.
- Mortar Joint Deterioration: The mortar joints between clay tiles can erode or crumble, creating gaps that compromise the liner’s integrity.
- Vertical Cracks: These can occur due to structural movement or severe temperature fluctuations.
- Chimney Fires: The intense heat of a creosote-fueled chimney fire can severely damage most types of liners.
- Animal and Debris Blockages: Nesting animals or accumulated debris can physically damage the liner or create conditions (like moisture buildup) that accelerate deterioration.
- Improving Safety and Efficiency: An old, unlined chimney, or one with a severely damaged liner, is unsafe. Relining brings the chimney up to current safety standards (e.g., NFPA 211) and can improve the draft and performance of the connected appliance.
- Appliance Change: When installing a new heating appliance, the existing flue liner may not be the correct size or type for the new unit, requiring a reline.
Signs that a chimney may need relining include visible cracks or gaps in the flue (often seen during a video inspection), evidence of a past chimney fire, excessive creosote buildup, smoke or unusual odors entering the home from the fireplace, poor draft or difficulty starting/maintaining a fire, water damage or rust stains inside the chimney, or finding bits of crumbly terracotta or liner material in the firebox.
Types of Liners and Repair Methods:
- Clay/Terracotta Tiles: Traditionally used in masonry chimneys, these are durable but can crack or deteriorate over time. When damaged, individual tiles can sometimes be removed and replaced if the damage is localized and accessible, though this can be labor-intensive.
- Stainless Steel Liners: These are a very common and highly recommended option for relining, especially when replacing damaged clay tile liners or lining previously unlined chimneys. Stainless steel liners are durable, resistant to heat and corrosion, and can be installed as flexible or rigid sections to fit various chimney configurations. They often come with a lifetime warranty when professionally installed.
- HeatShield® (Ceramic/Refractory Resurfacing/Slip Casting): This is a proprietary system designed to repair and restore existing clay tile liners without complete removal and replacement. The process typically involves cleaning the flue, then applying a specialized ceramic or refractory mortar mixture to the interior surface of the liner. This coating seals cracks and gaps, smooths the flue surface, and reinforces the existing liner. It is described as “slip casting” or “chimney resurfacing” and can be a less invasive and more cost-effective solution for certain types of liner damage. The development of such liner repair systems indicates a trend towards providing homeowners with more options beyond full replacement, though the suitability of these repair methods depends heavily on the nature and extent of the existing liner damage, necessitating a thorough professional diagnosis.
- Cast-in-Place Liners: These liners are created by pouring a special cement-like refractory mix around an inflatable or removable form positioned inside the chimney. Once cured, it forms a seamless, smooth, and highly insulated flue. (While mentioned in the initial outline, detailed information was less prevalent in the provided snippets; this method is generally used for significant restoration or when a very durable, insulated liner is required.)
Repair and Installation Process: The process always begins with a thorough inspection, typically a Level 2 video scan, to accurately assess the condition of the existing liner and determine the best course of action.
- If relining with stainless steel, the process involves selecting the appropriate diameter and type of liner for the appliance and chimney, carefully inserting it into the chimney (often from the top), connecting it to the appliance, and securing it at the top with a new top plate and chimney cap. Insulation is often installed around the liner for improved performance and safety.
- If repairing with HeatShield® or a similar resurfacing system, the flue is first thoroughly cleaned. The proprietary coating material is then applied according to the manufacturer’s specifications, often using a specialized applicator that ensures an even coat.
- If replacing clay tiles, damaged sections are carefully removed, and new tiles of the correct size are mortared into place.
NFPA/CSIA Recommendations: Both the NFPA (specifically NFPA 211) and the CSIA emphasize that any cracks, gaps, or other significant damage to a chimney flue liner render it unsafe and necessitate its repair, relining, or complete replacement to ensure the safety and structural integrity of the chimney system. Professional services will adhere to these standards.
Masonry Repair: Restoring Strength and Beauty
The masonry structure of a chimney is constantly under assault from weather, temperature changes, and the byproducts of combustion. Over time, bricks and mortar can deteriorate, requiring professional repair to maintain the chimney’s safety and appearance.
Tuckpointing/Repointing: Process, Steps, Materials
- Purpose: Tuckpointing (or more accurately, repointing in most repair contexts) is the process of removing deteriorated, cracked, or crumbling mortar from the joints between bricks and replacing it with fresh, sound mortar. This is essential to prevent water from seeping into the chimney structure (which can lead to further damage, including interior leaks and freeze-thaw spalling of bricks), maintain the chimney’s structural integrity by ensuring even load distribution, and restore its aesthetic appeal. While often used interchangeably, “repointing” is the general term for renewing mortar joints. “Tuckpointing” technically refers to a more specialized decorative technique using two different colors of mortar to create the illusion of very fine joints, though the repair cost is similar to repointing.
- Process:
- Mortar Removal: The damaged mortar is carefully removed from the joints to a consistent depth, typically about 3/4 to 1 inch, or until sound mortar is reached. This is often done using specialized grinders with diamond blades (equipped with dust collection systems) or by hand with masonry chisels and hammers, taking care not to damage the adjacent bricks.
- Joint Cleaning: The cleaned-out joints are thoroughly brushed or blown out with compressed air to remove all dust and loose debris, ensuring a good bond for the new mortar. The joints may also be lightly dampened.
- Mortar Preparation: New mortar is mixed. Ideally, the new mortar should match the strength, composition, and color of the original mortar as closely as possible, especially for older or historic chimneys. Using a mortar that is too hard can damage softer, older bricks. The mix typically consists of Portland cement, lime, sand, and water. Color pigments can be added if needed for matching.
- Mortar Application: The fresh mortar is carefully packed into the prepared joints in layers using specialized pointing trowels, ensuring there are no voids.
- Tooling: Once the mortar has reached its initial set (become “thumbprint hard”), the joints are “tooled” or “struck” with a jointing tool. This compacts the mortar, creates a smooth and neat appearance, and shapes the joint profile (e.g., concave, V-joint) to effectively shed water.
- Curing: The newly repointed mortar must cure properly, which can take several days. During this time, it may need to be protected from rapid drying (e.g., by light misting with water) to achieve maximum strength and durability.
- Materials: Mortar mix (Portland cement, hydrated lime, masonry sand, water), possibly color pigments.
Brick Replacement: Process, Steps, Materials
- Purpose: When individual bricks in the chimney are severely damaged – cracked through, spalled (face broken off), or missing – they need to be replaced to restore the chimney’s structural integrity and weather resistance.
- Process:
- Mortar Removal: The mortar surrounding the damaged brick(s) is carefully chiseled or ground out.
- Brick Extraction: The damaged brick(s) are gently tapped and removed, trying not to disturb adjacent sound bricks.
- Cavity Cleaning: The resulting cavity is cleaned of all old mortar and debris using a wire brush.
- Brick Preparation: New replacement bricks are selected to match the existing bricks in size, color, and texture as closely as possible. The new bricks are often soaked in water for a few minutes before installation to prevent them from absorbing too much moisture from the fresh mortar too quickly, which could weaken the bond.
- Mortar Mixing & Application: Mortar (similar to that used for repointing) is mixed to a firm, workable consistency. A layer of mortar (a “bed joint”) is applied to the bottom of the cavity, and mortar (“head joints”) is applied to one or both ends of the replacement brick or the sides of the cavity.
- Brick Setting: The new brick is carefully positioned into the cavity and pressed firmly into the mortar bed, ensuring it is aligned with the existing brickwork. A level may be used to check for evenness.
- Joint Filling & Tooling: Additional mortar is applied around the edges of the new brick to fill all gaps completely. The joints are then tooled to match the existing joints.
- Cleanup & Curing: Excess mortar is wiped from the brick faces before it hardens. The new mortar is allowed to cure properly, similar to repointing.
- Materials: Replacement bricks, mortar mix.
Parge Coating (Smoke Chamber Parging): Purpose, Process, Materials
- Purpose: Parging the smoke chamber involves applying a layer of specialized, insulating refractory mortar to the walls of the smoke chamber (the area above the firebox and damper that funnels smoke into the flue). The purpose is to smooth out rough, corbeled (stepped) brickwork, seal any small cracks or gaps, and improve the chamber’s shape for better smoke flow. A smooth, properly shaped smoke chamber enhances draft, reduces turbulence, minimizes creosote accumulation in this critical area, and insulates the chamber to prevent excessive heat transfer to surrounding combustible framing.
- Process:
- Inspection & Cleaning: The smoke chamber and flue are thoroughly inspected and cleaned to remove all soot, creosote, and debris.
- Surface Preparation: The masonry surface is prepared, which may involve pre-wetting and sometimes cutting small cracks or roughening the surface to improve mortar adhesion.
- Mortar Mixing & Application: A special refractory mortar mix (often containing Portland cement, sand, lime, and other aggregates or proprietary insulating materials) is prepared to a plastic-like, mud-like consistency. This mortar is then applied to the smoke chamber walls using a trowel or specialized spraying equipment, building it up to create a smooth, streamlined surface.
- Smoothing & Finishing: The parged surface is smoothed to an even, flat finish. Once dried, it may be sanded or coated with an additional specialized sealant to further improve efficiency and resist creosote.
- Curing: The parging material must be allowed to cure properly, typically for at least 24 hours, before the fireplace is used.
- Materials: Specialized refractory/insulating mortar mix, pointing/parging trowels, sweeping equipment, protective gear.
Rebuilding Damaged Chimney Sections
- Purpose: When a chimney has suffered extensive damage – such as severe spalling across a large area, numerous loose or crumbling bricks, significant structural cracks, or if the chimney is leaning – repointing or isolated brick replacement may not be sufficient. In such cases, a partial or complete rebuild of the damaged section(s) is necessary.
- Techniques: This is a major structural repair that involves carefully dismantling the unsound portion of the chimney down to solid masonry. The section is then rebuilt using new bricks and mortar, following sound masonry practices. This includes ensuring proper brick bonding, consistent mortar joints, and structural stability. If the rebuild involves the portion of the chimney passing through the roofline, new flashing will need to be installed. The chimney crown will also need to be rebuilt or replaced. The integrity of the flue liner within the rebuilt section must also be addressed, potentially requiring extension or replacement. This complex work requires significant masonry skill and knowledge of chimney construction principles and codes, and should always be performed by qualified professionals.
It is important to recognize that masonry repairs are often interconnected. For example, if a significant section of a chimney needs to be rebuilt , this work will almost invariably necessitate the installation of new chimney flashing where the rebuilt section meets the roofline.
Similarly, the top of the rebuilt section will require a new or properly repaired chimney crown , and the flue liner within that section must be assessed and potentially repaired, extended, or replaced. This interconnectedness highlights the necessity of a holistic assessment by a professional who can identify all related issues and ensure that repairs are comprehensive and address the root causes of deterioration, rather than just isolated symptoms.
Damper Repair and Replacement: Controlling Your Fireplace’s Airflow
The chimney damper is a movable plate located in the chimney that controls airflow. When the fireplace is not in use, a closed damper prevents heated indoor air from escaping up the chimney and cold outdoor air (downdrafts) from entering the home. When a fire is burning, the damper is opened to allow smoke and combustion gases to exit.
Types of Dampers:
- Throat Dampers: These are the most traditional type, located in the “throat” of the chimney, just above the firebox and below the smoke chamber. They are typically made of cast iron or metal and are operated by a handle, poker, or chain mechanism accessible from the firebox.
- Top-Sealing Dampers (Chimney-Top Dampers): These are installed at the very top of the chimney, sealing the flue opening from above. They usually feature a silicone rubber or metal gasket that creates a much tighter seal than most throat dampers. Top-sealing dampers are operated by a stainless steel cable that runs down the flue to a handle mounted in or near the firebox. They are generally considered more energy-efficient due to their superior seal.
Common Problems: Dampers can experience various issues over time:
- Warping, Cracking, or Breakage: The damper plate can warp or crack from repeated exposure to high heat and subsequent cooling, or from rust.
- Off-Track or Dislodged Plate: The damper plate can become dislodged from its frame or hinges.
- Rust and Corrosion: Metal dampers, especially older ones, are prone to rust, which can cause them to stick or not seal properly.
- Debris Blockage: Soot, creosote, or fallen debris can accumulate around the damper, preventing it from opening or closing fully.
- Broken Handle, Chain, or Cable: The operating mechanism can break or become detached.
- Improper Seal: Even if functional, older throat dampers often do not provide an airtight seal, leading to significant heat loss in winter and cool air loss in summer.
Repair and Replacement Procedures:
- Cleaning and Adjustment: Minor issues can sometimes be resolved by thoroughly cleaning the damper and its frame to remove debris and rust. If a throat damper plate is merely off-track, it may be possible to reposition it.
- Damper Plate Replacement: If a throat damper plate is warped, cracked, or severely rusted, it may need to be replaced. This involves removing the old plate (often by loosening a nut on a control rod), cleaning the frame, and installing a new plate of the correct size.
- Top-Sealing Damper Cable Replacement: The stainless steel cables for top-sealing dampers can break over time and will require replacement.
- Full Damper Replacement: If the damper frame is damaged, if the entire throat damper assembly is beyond repair, or if an upgrade to a more energy-efficient top-sealing damper is desired, a full replacement is necessary. Installing a top-sealing damper is a common upgrade that can significantly reduce energy loss.
Upgrading from a leaky or inefficient throat damper to a modern top-sealing damper can represent a sound investment. While there is an upfront cost for the new damper and installation , the improved seal can lead to noticeable long-term energy savings by preventing the loss of conditioned (heated or cooled) indoor air up the chimney when the fireplace is not in use. This makes the replacement more than just a repair; it’s an enhancement to the home’s overall energy efficiency.
Firebox Repair and Rebuilding: The Heart of Your Fireplace
The firebox is the chamber where the fire burns. It is constructed to withstand extremely high temperatures and to direct smoke and heat upwards into the smoke chamber and flue.
Common Damages: Due to intense heat, thermal cycling, and physical impact from logs, fireboxes can sustain damage over time:
- Cracked, Broken, or Spalling Firebricks: The specialized bricks lining the firebox can crack, break apart, or have their faces spall off.
- Deteriorated or Missing Refractory Mortar Joints: The high-temperature mortar used to bond the firebricks can crumble, erode, or fall out, creating gaps.
- Gaps or Holes: Openings in the firebox walls can allow excessive heat to reach combustible parts of the surrounding chimney structure or building framing, creating a severe fire hazard.
- Loose Bricks: Bricks may become loose due to mortar failure. Damaged fireboxes can lead to reduced fireplace efficiency, increased risk of house fires due to heat transfer to combustibles, and leakage of smoke or toxic gases into living spaces.
Professional Repair/Rebuilding Methods & Materials: The repair or rebuilding of a firebox requires specialized materials and techniques due to the extreme conditions it must endure.
- Materials:
- Firebricks: These are dense, specially formulated bricks designed to withstand very high temperatures (often 1800∘F or higher) and thermal shock without degrading. They are the primary structural component of the firebox lining.
- Refractory Mortar: This is a high-temperature bonding mortar, also designed to withstand extreme heat. It is used to lay the firebricks and fill the joints. Standard masonry mortar is not suitable and will fail quickly under firebox conditions.
- Refractory Panels: For some prefabricated fireplaces or as an alternative to individual bricks in certain repair scenarios, prefabricated refractory panels can be used. These are large, molded panels made from refractory materials.
- Repair Process:
- For minor cracks in individual firebricks, it may be possible to fill them by working refractory cement or mortar into the crack.
- For deteriorated mortar joints, the old, damaged mortar is carefully ground or chiseled out, and the joints are repointed with fresh refractory mortar.
- Rebuilding Process: If the damage is extensive, a partial or complete rebuild of the firebox lining is necessary:
- Removal of Damaged Materials: The old, damaged firebricks and mortar are carefully removed.
- Cleaning: The underlying area is thoroughly cleaned, often with a HEPA vacuum to control dust.
- Brick Preparation: New firebricks are selected. They are often pre-wetted before installation to prevent them from drawing too much moisture from the refractory mortar too quickly, which can affect the cure and bond strength.
- Mortar Mixing: Refractory mortar is mixed according to manufacturer specifications, typically to a thick, oatmeal-like consistency.
- Laying Bricks: The firebricks are laid in a specific pattern (commonly a running bond, but herringbone or other patterns can be used for aesthetic purposes), ensuring full mortar coverage on all joints. The back and sides of the firebox are often angled or sloped (sometimes incorporating a “Franklin Curve” at the top of the back wall) to optimize heat reflection into the room and improve draft.
- Joint Tooling: Mortar joints are tooled for a neat appearance and proper compaction.
- Curing: The newly rebuilt firebox must be allowed to cure completely (typically 24-48 hours or as per mortar manufacturer’s instructions) before a fire is built.
The use of specialized refractory materials (firebricks and refractory mortar) is absolutely critical for firebox construction and repair. Standard building bricks and conventional masonry mortar cannot withstand the intense heat generated in a firebox. They will crack, spall, and deteriorate rapidly, leading to a breach in the firebox lining and creating an extreme fire hazard by allowing high temperatures to reach combustible materials in the surrounding structure. This underscores why professional expertise in material selection, preparation, and application is vital for any firebox work.
Chimney Flashing Repair and Replacement: Preventing Roof Leaks
Chimney flashing refers to the sheet metal components installed at the intersection of the chimney and the roof. Its purpose is to create a watertight seal that prevents rainwater and snowmelt from leaking into the building at this vulnerable junction. Properly installed and maintained flashing is crucial for protecting the roof structure, attic, and interior spaces from water damage.
Importance and Common Issues: Flashing failures are a very common source of roof leaks. Issues that can compromise flashing include:
- Rust and Corrosion: Metal flashing (especially older galvanized steel) can rust or corrode over time, developing holes or weak spots.
- Physical Damage: Flashing can be damaged by wind, falling tree limbs, animal activity, or improper roof work. This can result in splits, holes, torn sections, or bent pieces.
- Improper Installation: Incorrect installation is a frequent cause of flashing failure. This can include using the wrong type or size of flashing, insufficient overlap between pieces, inadequate integration with roofing materials, or improper sealing.
- Deteriorated Sealant: Caulk or roofing cement used to seal flashing edges can dry out, crack, and pull away over time, creating openings for water.
- Loose Flashing: Fasteners can become loose, or the flashing can pull away from the chimney or roof surface. Failed flashing allows water to penetrate, leading to rotted roof decking and framing, damaged attic insulation, water stains on interior ceilings and walls, mold growth, and potentially significant structural weakening over time.
Methods for Professional Repair/Replacement & Materials:
- Types of Flashing Components: A complete chimney flashing system is typically composed of several interconnected parts:
- Base Flashing (or Apron Flashing): This is the piece that runs along the bottom (downslope) edge of the chimney where it meets the roof. A similar piece is often used at the back (upslope) side, sometimes integrated with a cricket or saddle if the chimney is wide.
- Step Flashing: These are individual L-shaped pieces of metal that are interwoven with each course of shingles along the sloping sides of the chimney. Each piece overlaps the shingle below it and extends up the side of the chimney.
- Counter Flashing (or Cap Flashing): This is the final layer that covers the top edges of the base and step flashing. The counter flashing is typically embedded into a groove (a “reglet”) cut into the chimney’s masonry mortar joints and then folded down over the base/step flashing. This creates a durable, mechanical seal.
- Materials: Common flashing materials include galvanized steel, copper, aluminum, lead-coated copper, and terne-coated stainless steel. Copper is very durable and long-lasting but more expensive. Stainless steel is also an excellent choice. It is crucial that dissimilar metals are not used in direct contact where moisture is present, as this can lead to galvanic corrosion, which accelerates the deterioration of the less noble metal.
- Repair/Replacement Process:
- Removal: Old, damaged flashing and surrounding shingles (as needed) are carefully removed.
- Surface Preparation: The roof deck and chimney surface are cleaned and inspected for any damage (e.g., rotted wood), which must be repaired before new flashing is installed. An underlayment (like rosin paper or roofing felt, depending on the metal type) is often laid on the roof deck beneath the flashing.
- Installation: New flashing components are installed in a specific sequence, starting with the base/apron flashing, followed by the step flashing interwoven with the shingles, and finally the counter flashing. Each piece must overlap the piece below it correctly to shed water. Counter flashing is secured into reglets in the mortar joints using wedges and then sealed with fresh mortar or a high-quality, UV-resistant caulk. The U.S. General Services Administration (GSA) provides detailed technical procedures for flashing installation, particularly for historic structures, which outline best practices.
- Sealing: All seams, edges, and fastener penetrations are meticulously sealed with appropriate roofing cement or caulk.
The installation of chimney flashing is a complex, multi-layered process that requires precision and a thorough understanding of roofing and masonry principles. The various components – base, step, and counter flashing – must be correctly sized, shaped, overlapped, and integrated with the specific roofing material being used. Incorrect installation is a very common reason for premature flashing failure and subsequent leaks. This complexity and the critical importance of a watertight seal make professional installation by experienced roofing or chimney technicians highly advisable. DIY attempts at flashing repair or replacement are often risky and can lead to persistent or even worsened leakage problems.
Animal and Nest Removal: Humane Solutions for Unwanted Guests
Chimneys can appear as inviting shelters for various animals, including birds (especially Chimney Swifts, which are federally protected and have specific nesting habits), squirrels, raccoons, and even bats. While seeking refuge, these animals can create significant problems.
Risks Associated with Animal Presence:
- Blockages and Fire Hazards: Nesting materials (twigs, leaves, grass, etc.) are often highly combustible and can completely block the flue. If a fire is lit in the fireplace or appliance below, these materials can ignite, causing a dangerous chimney fire. Blockages also prevent smoke and carbon monoxide from venting properly, forcing them back into the home.
- Health Risks: Animal droppings, parasites (like mites or fleas), and decaying animal matter can accumulate in the chimney, posing health risks to occupants from bacteria, fungi, and allergens.
- Structural Damage: Animals, particularly raccoons and squirrels, can cause physical damage to the chimney liner, damper, or masonry by chewing or clawing.
- Unpleasant Odors: Decaying nests, droppings, or deceased animals can create strong, unpleasant odors in the home.
- Trapped Animals: Animals can become trapped in the chimney and die if they cannot escape, leading to odor and sanitation issues.
Safe and Humane Removal Methods: Professional animal removal services prioritize humane methods that ensure the safety of both the animals and the home’s occupants.
- Inspection: The first step is always a thorough inspection to identify the type of animal present, whether there are young, and the extent of the nesting or blockage.
- Species-Specific Strategies:
- Birds (excluding Chimney Swifts during nesting season): Often, opening the damper and providing an escape route from the firebox to the outside (e.g., an open door or window in a darkened room) will allow a trapped bird to fly out on its own. Careful netting may also be used. (Note: Chimney Swifts are a special case; if they are actively nesting, federal law protects them, and removal must typically wait until the young have fledged. Professionals are aware of these regulations.)
- Squirrels: Similar methods to birds can be used, or a baited live trap can be placed inside the sealed-off fireplace. Once caught, the squirrel can be released outdoors.
- Raccoons: If a mother raccoon has young in the chimney, it’s often best to allow her to raise them until they are old enough to leave with her (usually a few weeks). This can be encouraged by humane hazing techniques, such as placing a bright light and a radio playing talk radio in the fireplace, to make the den site less appealing. Professionals use specialized tools and techniques for safe and humane removal, especially if young are present.
- Crucial Considerations: It is vital to ensure that all animals, especially young, are removed before sealing the chimney. Trapping animals inside will lead to their death and further problems. Attempting to “smoke out” animals by lighting a fire is dangerous, inhumane, and can cause a chimney fire or force panicked animals (including babies) into the home.
Cleanup, Sanitization, and Preventative Measures:
- Debris Removal: After the animals are gone, all nesting materials, droppings, and any other debris must be completely removed from the chimney.
- Sanitization: The chimney should then be cleaned and sanitized to eliminate odors, bacteria, fungi, and parasites left behind by the animals.
- Prevention: The most effective way to prevent future animal intrusions is to install a sturdy, well-fitted chimney cap with a mesh screen. The cap should be made of durable material like stainless steel or copper (not flimsy aluminum, which raccoons can often damage or remove). Mesh screens can also be installed over other potential entry points. Regular chimney inspections can help detect and address any new vulnerabilities early.
The humane removal of wildlife is not merely a matter of preference. Depending on the species and local regulations, there can be legal requirements governing how certain animals are handled. Professionals in wildlife removal or certified chimney sweeps who offer this service are more likely to be aware of and adhere to these regulations, ensuring that removals are conducted ethically and legally, avoiding harm to protected species and potential legal repercussions for the homeowner.
Stove and Insert Services: Specialized Care for Modern Appliances
Modern heating appliances like wood stoves, pellet stoves, and gas fireplaces/inserts require specific maintenance distinct from traditional open masonry fireplaces. While they share the need for a clean and sound chimney, their internal components and fuel delivery systems have unique service requirements.
Wood Stove Cleaning and Maintenance:
Annual professional cleaning and maintenance are strongly recommended for wood stoves to ensure safety and efficiency. Key tasks include:
- Ash Removal: Ashes should be removed from the firebox regularly, typically every few days during periods of full-time heating, as excessive ash buildup can impede proper operation and airflow. Cooled ashes should be placed in a metal container with a tight-fitting lid and disposed of safely away from combustible materials, as embers can remain hot for extended periods.
- Firebox Cleaning and Inspection: The firebox interior, including firebricks and the baffle plate (a plate at the top of the firebox that extends the flame path), should be inspected for cracks, wear, or damage. Damaged or excessively worn firebricks or baffles should be replaced, as they protect the stove body from extreme heat. Secondary air tubes, which introduce air for more complete combustion, should also be checked and replaced if damaged or bent.
- Stovepipe (Chimney Connector) Inspection and Cleaning: The stovepipe connecting the wood stove to the chimney must be regularly inspected for soundness and cleaned of creosote buildup. This is often done in conjunction with chimney sweeping. Joints in the stovepipe should be secure.
- Gasket and Seal Inspection: The braided rope gaskets around the stove door and glass provide an airtight seal. These should be inspected for wear, looseness, or compression. Damaged gaskets should be replaced using high-temperature gasket cement to maintain combustion efficiency and prevent smoke leakage.
- Glass Cleaning: The stove’s glass door should be cleaned frequently to remove soot and creosote stains, allowing for a clear view of the fire and better heat radiation. Specialized wood stove glass cleaners or a paste of damp newspaper dipped in wood ash can be used. Abrasive cleaners should be avoided.
- Exterior Cleaning and Paint Touch-up: The exterior surfaces can be wiped clean with a soft, damp cloth. Over time, the paint finish may need touching up with high-temperature stove paint to maintain appearance and prevent rust.
- Other Components: Hinges, air controls, and the overall structural integrity of the stove body (checking for metal fatigue or cracks) should be inspected.
Pellet Stove Cleaning and Maintenance:
Pellet stoves, which burn compressed wood or biomass pellets, have more complex mechanical and electrical components than wood stoves and require diligent maintenance. A thorough professional cleaning and service is generally recommended annually or after every ton of fuel burned. Using low-grade pellets may necessitate more frequent cleaning.51
- Service Includes: A professional service typically involves inspecting the electrical system (wiring, sensors), vacuum and pressure switches, the igniter, the hopper (pellet storage bin), and the auger system (which feeds pellets to the burn pot). Glass, hopper, and internal components are cleaned. Moving parts are lubricated, and any worn parts are replaced. The firewalls, burn pot, and combustion chambers are inspected and cleaned. Key cleaning tasks include cleaning the combustion fan housing, removing and cleaning the baffle, and cleaning the heat exchanger tubes. Thermocouples and ignition systems are tested.
- Ongoing Homeowner Maintenance: Regular tasks for the homeowner include cleaning ash from the firebox and ash pan, scraping the burn pot to remove clinkers (hardened ash deposits), raking or brushing heat exchanger tubes, and keeping vital components like the airwash system and venting pathways free of ash.
- Parts Repair/Replacement: Professionals can repair or replace a wide range of pellet stove parts, including auger motors, ignitors, burn pots, various switches (hopper, high-limit, snap discs), blowers and fans, control modules/computer boards, wiring harnesses, gaskets, seals, thermocouples, flame sensors, and thermostats.
Gas Fireplace/Insert Cleaning and Maintenance:
Gas fireplaces and inserts, while generally cleaner burning than wood appliances, still require annual professional cleaning and inspection to ensure safe and efficient operation.
- Service Includes: A technician will typically clean and test the pilot light assembly and/or electronic ignition system. Burners are adjusted and cleaned to ensure proper flame quality and combustion. Gas pressure is tested, and gas lines and connections are inspected for leaks and integrity. The venting system is checked to ensure it is clear and functioning correctly. The glass front is cleaned (often a specialized process for sealed units), and the firebox and control compartment are cleaned. All safety controls, sensors (like oxygen depletion sensors), and thermopile/thermocouple components are tested. For gas inserts, proper venting, seal integrity, and secure connections are specifically verified. Decorative elements like ceramic logs and embers may be cleaned and replenished.
The detailed checklists and specific components mentioned for wood stoves (ash management, creosote in stovepipe, door gaskets ), pellet stoves (augers, hoppers, electronic sensors, burn pot cleaning ), and gas fireplaces (pilot assemblies, burners, gas valves, electronic controls ) clearly demonstrate that “stove and insert services” are not a one-size-fits-all proposition. Each fuel type and appliance design incorporates unique components, operational characteristics, and, consequently, distinct maintenance requirements.
This necessitates specialized knowledge and diagnostic skills from the servicing technician. A professional who is an expert in traditional wood stoves might not possess the intricate knowledge required for troubleshooting pellet stove electronics or adjusting gas fireplace valve pressures. Therefore, homeowners should seek service professionals who have demonstrable experience and certification for their particular type of appliance to ensure it receives the correct and comprehensive care.
Why Call a Professional? The Case for Expert Chimney Services
While some minor maintenance tasks can be undertaken by a diligent homeowner, the overwhelming majority of chimney inspection, cleaning, and repair services are best left to trained, certified, and insured professionals. The reasons for this are compelling and multifaceted, centering on safety, expertise, specialized equipment, regulatory compliance, and long-term cost-effectiveness.
Safety First: Mitigating Risks of Fire and Carbon Monoxide
This is the paramount reason. Chimney work inherently involves dealing with flammable substances like creosote and potential exposure to carbon monoxide. Professionals possess the equipment, training, and expertise to thoroughly remove all traces of creosote, soot, and hazardous obstructions (like flammable nests), significantly reducing the risk of chimney fires and ensuring the system is safe for use.
They understand the dynamics of combustion and ventilation, enabling them to identify and mitigate conditions that could lead to carbon monoxide leakage into the home. Lighting a fire inside one’s home is a serious undertaking, and ensuring the appliance and chimney are in safe working condition is not a task to be taken lightly. Attempting complex chimney work without proper knowledge or equipment can easily miss critical hazards or even create new ones.
Expert Diagnosis: Comprehensive Inspections and Identifying Hidden Issues
Professional chimney sweeps and technicians do more than just clean; they conduct comprehensive inspections as part of their service. Their training and experience allow them to “read” a chimney and identify subtle signs of potential problems that an untrained eye would invariably miss.
These can include hairline cracks in the flue liner, early-stage masonry deterioration, issues with the chimney crown or flashing, improper clearances to combustibles, or signs of previous, unreported chimney fires. Early detection of such issues is crucial for preventing them from escalating into major, costly repairs or severe safety hazards.1
Specialized Tools and Equipment: Ensuring a Thorough and Correct Job
Effective chimney maintenance requires an array of specialized tools and equipment that are typically not owned by homeowners and require skill to use correctly.
These include various types of chimney brushes and rods suited for different flue sizes and materials, powerful rotary cleaning systems for stubborn deposits, high-powered HEPA vacuum systems for dust and debris control, video inspection cameras for internal flue examination, flue draught gauges to assess chimney performance, smoke pellets for leak detection, and tools for masonry repair, liner installation, and component replacement. Professionals are trained in the correct methods to use these tools to remove debris and deposits thoroughly without causing damage to the chimney structure or liner.
Knowledge of Codes and Standards (NFPA, CSIA, Local Regulations)
Professional chimney service providers, particularly those certified by organizations like the CSIA, operate in accordanceance with established industry best practices and safety standards, such as NFPA 211. They are knowledgeable about national and local building codes pertaining to chimneys and venting systems.
This ensures that any work performed is not only effective but also compliant with legal and safety requirements. CSIA certification, for instance, involves rigorous training, comprehensive examinations on codes and technical standards, and a commitment to ongoing education and a code of ethics.5
Efficiency and Long-Term Savings: Preventing Costly Future Repairs
While professional chimney services involve an upfront cost, they are a prudent investment in the long-term health and safety of the home. Regular professional maintenance, including thorough inspections and timely repairs, prolongs the life of the chimney and appliance, prevents minor issues from developing into major structural problems, and helps avoid the potentially catastrophic costs associated with a house fire or extensive water damage. The early detection and correction of problems by a professional almost always result in lower overall repair costs compared to addressing neglected, advanced-stage deterioration.
Peace of Mind: Ensuring Your Home and Family are Protected
Ultimately, hiring a qualified professional provides homeowners with invaluable peace of mind. Knowing that your chimney and heating appliance have been meticulously inspected, cleaned, and serviced by an expert who understands the complexities and potential hazards involved allows you to enjoy the warmth and comfort of your fireplace or stove with confidence in its safety and reliability.
Professionals bring a holistic system understanding to their work. They don’t just perform isolated tasks like cleaning out soot; they assess the entire chimney and venting system as an integrated unit. This comprehensive perspective, informed by their knowledge of combustion principles, material science, building codes, and the interplay of various components (liner, crown, cap, masonry, appliance), allows them to identify interconnected issues and root causes that a DIYer focusing on a single, apparent problem would likely overlook. For example, a recurring creosote problem might not just be a cleaning issue but could indicate an improperly sized flue, a faulty damper, or the use of unseasoned wood, all of which a professional is trained to diagnose.
Furthermore, a significant, often unstated, benefit of hiring a reputable, insured professional is risk transference. Chimney work, especially repairs or working at heights, carries inherent risks of accidental damage to the property or personal injury. If a homeowner attempts a DIY repair and causes further damage to their chimney or home, or injures themselves, they bear the full financial and personal responsibility.
However, if a licensed and insured professional chimney service provider accidentally causes damage during their work, their business liability insurance should cover the costs of rectification. This protection for the homeowner’s property and against unforeseen accidents is a crucial factor that weighs heavily in favor of professional service.
Conclusion: The Superiority of Professional Chimney Care
The maintenance of a chimney, fireplace, or venting system is a complex undertaking with significant implications for household safety, energy efficiency, and structural integrity. While the allure of DIY solutions for home maintenance is understandable, the specialized knowledge, intricate diagnostic tools, and adherence to stringent safety codes required for proper chimney care place most of these tasks firmly in the realm of professional service.
From conducting multi-level NFPA 211 inspections, potentially involving sophisticated video scanning technology, to the precise methods of sweeping away hazardous creosote and soot, professionals bring a level of expertise that ensures thoroughness and safety. Their ability to diagnose and repair a wide array of issues—ranging from waterproofing masonry and rebuilding crowns, to installing appropriate caps, relining damaged flues, performing intricate masonry repairs like tuckpointing and firebox reconstruction, ensuring functional dampers, repairing critical flashing, humanely removing animal intruders, and servicing the unique needs of various stoves and inserts—is predicated on extensive training and experience.
Professionals operate with a holistic understanding of the chimney as a complex system, recognizing how one component’s failure can impact others. They are equipped not only with specialized tools but also with current knowledge of evolving materials, techniques, and safety regulations, including local building codes and national standards set by bodies like the NFPA and CSIA. This comprehensive approach ensures that problems are not just superficially addressed but that their root causes are identified and rectified.
Ultimately, the decision to engage a professional chimney sweep and maintenance service is an investment in the safety of one’s home and family, the longevity of the chimney structure, and the efficient performance of heating appliances. The peace of mind derived from knowing that these critical systems have been cared for by qualified experts, coupled with the mitigation of risks associated with fire, carbon monoxide poisoning, and costly future damages, underscores the clear and compelling case for entrusting chimney care to those who do it best.