The Indispensable Role of Cleanliness in Modern Warehouse & Logistics Operations
The Strategic Imperative of a Clean Facility
In the fast-paced world of logistics and supply chain management, the cleanliness of a warehouse or distribution center is far more than a matter of appearance; it is a cornerstone of operational excellence. A meticulously maintained facility directly contributes to enhanced efficiency by ensuring unobstructed workflows, quicker access to inventory, and smoother operation of material handling equipment. Equally important is the profound impact on safety.
A clean environment significantly reduces the incidence of slips, trips, and falls—common hazards in industrial settings—and minimizes risks associated with clutter or poorly maintained areas.
Contact us!
Furthermore, cleanliness is integral to preserving the integrity of stored goods. Protecting inventory from damage caused by dust, pests, or cross-contamination is a primary function of a robust cleaning program, particularly for sensitive products.
Beyond these operational benefits, adherence to stringent cleanliness standards is frequently mandated by regulatory bodies such as the Occupational Safety and Health Administration (OSHA). This makes a comprehensive cleaning strategy not just a best practice, but a critical compliance requirement. The failure to maintain a clean and safe working environment can lead to costly fines, operational disruptions, and damage to a company’s reputation.
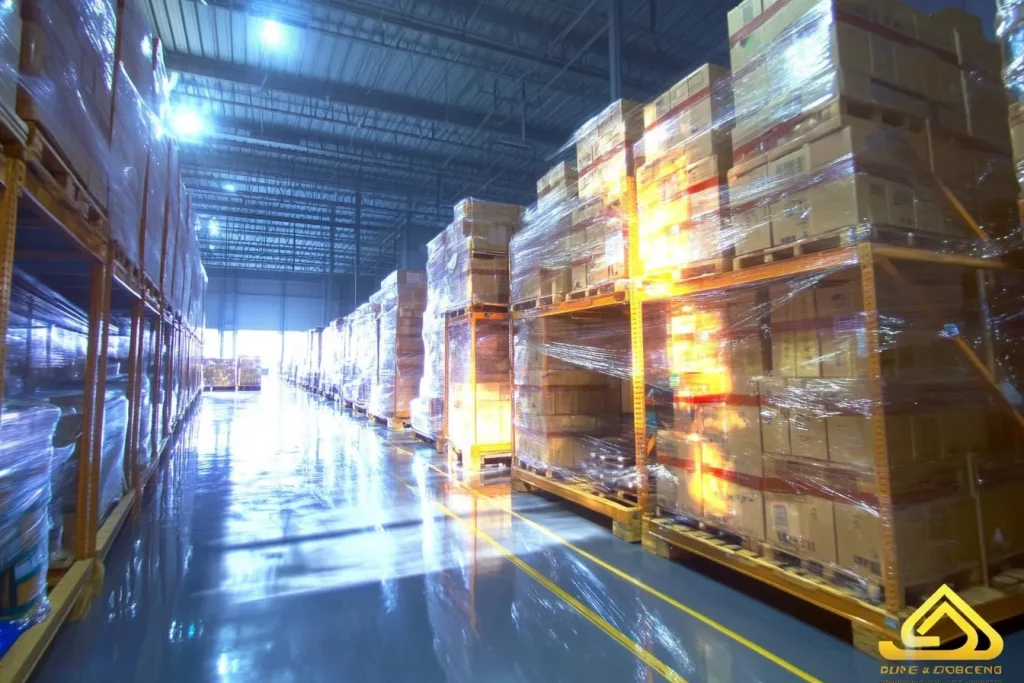
The benefits extend to equipment longevity as well. Debris on warehouse floors, for example, can cause significant damage to the wheels and undercarriages of forklifts and other material handling equipment, leading to expensive repairs and replacements over time. Regular cleaning helps to mitigate these issues, extending the life of valuable assets and reducing maintenance costs.
It is also increasingly recognized that a clean and well-organized warehouse serves as more than just an operational site; it acts as a signal of professionalism and reliability to external stakeholders. Clients and partners visiting a facility that is visibly clean and orderly are more likely to perceive the operation as well-managed and dependable. This positive impression can translate into stronger business relationships and a competitive edge in the marketplace. Thus, investing in high standards of cleanliness is not merely an operational expenditure but a strategic commitment to brand image and market positioning.
Overview of a Holistic Cleaning Approach
This guide provides a detailed framework for establishing and maintaining a comprehensive cleaning program within large storage and distribution centers. It will delve into routine maintenance practices, specialized cleaning protocols for distinct zones within the facility, and essential emergency preparedness measures. The objective is to equip warehouse managers, facility managers, and operations directors with the knowledge to implement effective cleaning strategies that address the “what, why, and how” of achieving and sustaining optimal facility condition. The scope includes detailed procedures for floor maintenance, high-level dust control, spill remediation, and the cleaning of critical areas such as loading docks, battery charging stations, and integrated office and restroom facilities, all while emphasizing safety and regulatory adherence.
Chapter 1: Mastering Large-Scale Floor Maintenance
The floor is arguably the most critical surface in a warehouse, subject to constant traffic, heavy loads, and the accumulation of various types of debris. Effective floor maintenance is fundamental to safety, efficiency, and the longevity of both the floor itself and the equipment that traverses it.
1.1. Concrete Floor Care: Sweeping and Scrubbing with Ride-On Machinery
For large warehouse and logistics facilities, ride-on sweeping and scrubbing machines are indispensable tools for maintaining vast concrete floor areas efficiently and effectively.
Pre-Cleaning Preparation
Before any mechanical cleaning begins, thorough preparation of the area is essential:
- Clear Obstructions: Remove all pallets, movable equipment, products, and any other objects from the path of the cleaning machine. This prevents damage to both the items and the machine, and ensures an unimpeded cleaning path.
- Preliminary Sweeping/Vacuuming: Always sweep or vacuum the floor to remove loose dirt, dust, wood chips, plastic wrap, and other larger debris before using a floor scrubber. Floor scrubbers are designed to wash away grime and soil, not to pick up substantial debris, which can damage scrubber brushes, squeegees, or internal components.
- Safety Signage: Prominently display “wet floor” signs to alert personnel to potential slip hazards during and after scrubbing operations.
Operating Ride-On Sweepers and Scrubbers: Techniques and Best Practices
- Machine Selection:
- Sweepers: Used for dry debris removal. For warehouses with significant dust, vacuum sweepers are preferred as they incorporate dust control systems, typically a roller brush to agitate dust, a fan to vacuum it, and a filter system to separate it.
- Scrubbers: Used for wet cleaning to remove adhered dirt, grime, and spills. They apply a cleaning solution, scrub the floor with brushes or pads, and then vacuum up the dirty solution with a squeegee assembly.
- Combination Sweeper-Scrubbers: These machines perform both sweeping and scrubbing functions in a single pass, offering maximum efficiency for large areas with mixed soiling.
- Ride-On Models: For large warehouse spaces (e.g., over 50,000 sq ft), ride-on machines are significantly more efficient than walk-behind or manual options.
- Brush/Pad Types: The choice between disc and cylindrical (roller) brushes depends on the floor type and debris. Cylindrical/roller brushes are generally better for floors with some texture or for picking up small debris due to their pre-sweeping function, making them well-suited for many warehouse environments. Disc brushes/pads are effective on smoother surfaces. Pad abrasiveness should be chosen carefully based on the floor type (e.g., painted, sealed, or polished concrete) and the type of cleaning (general cleaning vs. stripping).
- Operational Path: A systematic approach enhances efficiency. A common technique is to start cleaning along the perimeter of the area and work inwards, making overlapping passes to ensure complete coverage and avoid missed spots or streaks. This method helps push dirt towards a central area for easier final collection if needed.
- Speed and Maneuvering: Operate the machine at a slow and consistent speed. Avoid fast acceleration or sharp, tight turns, as this allows the squeegee and vacuum system sufficient time to effectively pick up all the dirty water and cleaning solution, preventing streaks and ensuring the floor dries quickly.
- Double Scrubbing for Heavy Soiling: For particularly dirty or greasy floors, a “double scrub” method can be highly effective. On the first pass, apply the cleaning solution and scrub the floor without engaging the squeegee and vacuum. This allows the cleaning solution more dwell time to break down heavy soils. On the second pass, engage the squeegee and vacuum to remove the loosened grime and solution.
- Machine Settings: Consult the operator’s manual for your specific machine. Adjust settings such as water flow rate, detergent dispensing rate (if applicable), brush pressure, and vacuum power according to the type of floor, the level of soiling, and the cleaning agent being used. Using the correct settings optimizes cleaning performance and prevents damage to the floor or machine.
Machine Maintenance Basics
Proper maintenance is crucial for the longevity and performance of ride-on cleaning equipment:
- Post-Use Cleaning: After each use, empty and thoroughly rinse both the solution tank (clean water/detergent) and the recovery tank (dirty water). This prevents the buildup of residue, bacteria, and odors.
- Inspect and Clean Components: Regularly inspect brushes, pads, and squeegee blades for wear and tear. Clean them after use and replace them when they are worn out or damaged to ensure optimal cleaning results. Clogged or dirty filters should also be cleaned or replaced as per manufacturer recommendations.
- Battery Care: For battery-powered machines, ensure batteries are fully charged before use and follow manufacturer guidelines for battery maintenance and charging cycles.
The condition of the warehouse floor has a direct and significant bearing on the lifespan of not only the cleaning machinery but also all material handling equipment, such as forklifts and pallet jacks. Debris like wood chips, plastic fragments, and metal shavings, commonly found on warehouse floors, can cause abrasive damage to the wheels, tires, and undercarriages of these vehicles. This leads to increased maintenance costs and premature equipment replacement. Furthermore, if improper cleaning techniques are used—such as overly aggressive scrubbing pads or harsh chemical agents not suited for the specific concrete finish—the floor surface itself can be damaged.
This degradation can lead to increased dust generation, a rougher surface that accelerates wear on tires, and can even compromise the structural integrity of floor sealants or hardeners. A well-planned and consistently executed floor maintenance program, utilizing the correct machinery, appropriate cleaning agents, and best-practice techniques, preserves the floor’s surface. A smooth, clean floor reduces friction and stress on the components of all equipment that operates on it, thereby extending their operational life and reducing overall repair expenditures. This creates a beneficial cycle where good floor care contributes directly to lower long-term operational costs for the entire facility.
Table 1: Comparison of Ride-On Floor Cleaning Machines for Warehouses
Machine Type | Primary Function | Ideal Application (Warehouse Context) | Key Features to Consider |
---|---|---|---|
Ride-On Sweeper | Dry debris removal | Large areas with light to moderate dry debris (dust, paper, small pallet chips) | Cleaning path width, hopper capacity, power source (battery, LPG, diesel), effective dust control system (vacuum and filtration), maneuverability, ease of maintenance. |
Ride-On Scrubber | Wet cleaning and soil removal | Areas with adhered dirt, grime, spills, requiring wet cleaning | Cleaning path width, solution/recovery tank capacity, power source (battery typically), brush type (disc or cylindrical), squeegee performance, water/detergent efficiency, drying time. |
Ride-On Sweeper-Scrubber (Combination) | Both sweeping and scrubbing in one pass | Large, mixed-soiling environments for maximum efficiency | Combines features of both; typically larger capacity, robust construction, ability to handle diverse debris and soiling levels simultaneously, advanced control systems. |
Derived from
1.2. Selecting Appropriate Cleaning Agents for Concrete Floors
Choosing the right cleaning agent is as important as selecting the right machine. The agent must be effective against the soil type without damaging the concrete surface or the cleaning equipment.
Types of Cleaners
- Daily Maintenance Cleaners: These are typically pH-neutral or mildly alkaline concentrated detergents designed for routine cleaning of light to moderate soiling. Many are formulated for use in automatic scrubbers and are safe for various concrete finishes, including those hardened and densified with lithium-silicates. Products like Consolideck DailyKlean are examples. Some are available in pre-measured packs for specific auto-scrubber tank sizes.
- Degreasers/Heavy-Duty Cleaners: For more stubborn soil such as oil, grease, tire marks, and heavy industrial grime, stronger alkaline degreasers or heavy-duty cleaning formulas are necessary. Products like PROSOCO Consolideck® Cleaner/Degreaser are designed to emulsify greasy residues. Tennant offers aggressive cleaning formulas for manufacturing environments.
- Concrete Densifier/Cleaners: Some advanced formulations combine cleaning with concrete densification. These products often contain lithium-silicates that penetrate the concrete, helping to maintain surface hardness and improve gloss while cleaning (e.g., PCM Deep Clean, Betco Crete Rx Densiclean).
- Specialized Pre-Cleaners/Restorative Cleaners: For newly installed concrete, pre-cleaners can remove laitance (a weak, cement-rich layer) and surface salts. For heavily soiled or stained older floors, restorative cleaners or even etching agents (used with caution) might be considered, though these are typically for periodic, not routine, use. EZ Etch is mentioned for cleaning excess mortar and opening up the concrete surface.
Considerations for Selection
- Type and Level of Soiling: Light dust and daily dirt can be managed with a neutral daily cleaner. Embedded grime, oil, or tire marks will necessitate a heavy-duty cleaner or degreaser.
- Floor Finish and Condition: Unsealed concrete may tolerate more aggressive cleaners than polished or sealed surfaces. Always test a cleaner in an inconspicuous area first. For floors treated with densifiers (like lithium-silicates), use compatible cleaners to avoid dulling the finish or negating the densifier’s effects.
- Machine Compatibility (Foaming): Crucially, use low-foaming detergents specifically formulated for use in floor scrubbers. High-foaming products can be drawn into the scrubber’s vacuum motor, causing damage and reducing suction performance. Adding water to the solution tank before adding the detergent can also help minimize foaming.
- Safety and Environmental Impact: Opt for cleaning agents that are biodegradable and have low volatile organic compound (VOC) content where possible. Ensure staff are trained on the safe handling, dilution, and disposal of any chemicals used, referencing the Safety Data Sheet (SDS) for each product. Review local regulations regarding the disposal of wastewater containing cleaning chemicals.
- Manufacturer Recommendations: Always consult the floor scrubber manufacturer’s recommendations for suitable detergent types. Some manufacturers, like Tennant, produce their own line of detergents (e.g., TennantTrue®) optimized for their machines.
Chapter 2: Conquering Dust: Strategies for High-Level and Ambient Dust Control
Dust is a pervasive issue in warehouses, originating from packaging materials (cardboard, wood pallets), product breakdown, external sources, and vehicle exhaust. Uncontrolled dust compromises air quality, can damage products and equipment, poses health risks to employees, and in some cases, can create serious fire and explosion hazards (combustible dust). A comprehensive dust control strategy must address both settled dust on surfaces (especially high-level) and airborne ambient dust.
2.1. Techniques for High-Level Dusting: Ceilings, Racking, Ductwork, and Light Fixtures
Dust accumulation on elevated surfaces is often overlooked but can lead to significant problems.
Systematic Top-Down Approach
The cardinal rule for all cleaning, especially dusting, is to work from the top down. Dust and debris dislodged from high surfaces like ceilings, light fixtures, ductwork, and the tops of racking will inevitably fall onto lower surfaces and the floor. Cleaning these higher areas first ensures that this fallen debris is captured during subsequent cleaning of lower areas and floors, preventing re-contamination and wasted effort. This includes cleaning HVAC system ducts before the areas directly beneath them.
Methods for Different Surfaces
- Ceilings, Beams, and Trusses: These expansive surfaces can harbor vast quantities of dust. Effective methods include high-pressure air blow-downs (directing dust downwards for collection), the use of specialized industrial vacuums equipped for combustible dust if applicable, and manual cleaning with long extension poles fitted with microfiber dusters or specialized vacuum attachments.
- Racking Systems: Dust settles not only on the top surfaces of racking but also on stored products, between boxes, on the back of shelves, and within the racking structure itself. Industrial vacuum cleaners with various extension wands and brush tools are essential for reaching these areas. Deep cleaning schedules should account for periods of lower inventory to allow better access.
- Ductwork and Pipework: Exposed ductwork, pipes, and conduits are prime locations for dust buildup. These often require specialized vacuum attachments designed to clean curved or irregular surfaces.
- Light Fixtures: Dust accumulation on light fixtures reduces their efficiency, leading to dimmer working conditions and increased energy consumption. It can also pose a fire hazard by insulating the fixture and causing overheating. Careful cleaning, often with vacuum brushes or microfiber dusters, is necessary.
Frequency
The frequency of high-level dusting depends on the rate of dust accumulation and the nature of the materials stored or handled. A general guideline is to perform high-level dusting at least once every three months. However, facilities storing sensitive products, those generating high levels of dust, or those with known combustible dust risks may require more frequent cleaning. Regular inspections can help determine the appropriate schedule.
The failure to address high-level dust can lead to a series of escalating problems that extend far beyond simple aesthetics or minor product contamination. Initially, it might seem like a low-priority issue, primarily affecting air quality or causing a light coating on stored goods. However, as dust layers thicken over time, particularly in “out of sight, out of mind” areas like high beams, ductwork, and the tops of racking, the risks multiply. If the accumulated dust is combustible—a common scenario in warehouses handling cardboard, wood from pallets, plastics, or certain powdered goods—it transforms into a significant latent fire and explosion hazard, merely awaiting an ignition source. Falling dust can also infiltrate sensitive electronic equipment or machinery components, leading to abrasion, overheating, or electrical short circuits, thereby shortening equipment lifespan and increasing maintenance costs. Furthermore, HVAC systems will inevitably draw in this airborne and falling dust, leading to clogged filters, reduced airflow efficiency, and higher energy consumption for climate control. Ultimately, persistent neglect of high-level dust can result in OSHA citations for poor housekeeping or specific violations related to combustible dust hazards, carrying financial penalties and potential operational disruptions. Therefore, a proactive and specialized approach to high-level dusting is not merely a cleaning task but a critical component of risk management, asset protection, and long-term operational cost control. The investment in such specialized cleaning is often minor when compared to the potential costs associated with an industrial accident, equipment failure, product recall, or regulatory action.
2.2. Specialized Equipment and Safety Protocols for Elevated Dusting
Cleaning high surfaces safely and effectively requires specialized equipment and strict adherence to safety protocols.
Equipment
- High-Reach Vacuum Systems: These are the cornerstone of modern high-level dusting. Systems like those offered by SkyVac feature powerful industrial vacuums coupled with lightweight, interlocking or telescopic poles (often made of carbon fiber) that can reach heights of 30-40 feet or more from the ground. They come with a variety of angled nozzles, brushes, and tool holders to effectively clean different surfaces (flat, curved, creviced). Many of these systems incorporate HEPA (High-Efficiency Particulate Air) filtration, which is crucial for capturing very fine dust particles (including allergens and some hazardous dusts) and preventing them from being recirculated into the air.
- Extension Poles with Duster Heads: For some light dusting applications or as a supplementary tool, microfiber dusters attached to telescopic poles can be used. Microfiber is effective at trapping dust rather than just displacing it.
- Aerial Lifts / Elevated Work Platforms (EWPs): For areas that are inaccessible from the ground even with extension tools, or where more direct access and maneuverability are needed (e.g., for heavy cleaning or maintenance alongside dusting), scissor lifts or boom lifts may be necessary. Operation of such equipment requires specific training and certification.
- Explosion-Proof Vacuums: If combustible dust is present, only vacuums specifically designed and certified as explosion-proof (or intrinsically safe) must be used. These vacuums are constructed to prevent any internal sparks or heat that could ignite the dust.
Safety Protocols
- Personal Protective Equipment (PPE): This is non-negotiable.
- Eye Protection: Dust-proof safety glasses or goggles are essential to prevent particles from entering the eyes.
- Respiratory Protection: A good quality respirator or mask is vital. For general nuisance dust, an N95-rated disposable respirator may suffice. For finer particles, hazardous dusts, or prolonged exposure, a higher level of protection (e.g., P100 filters on a reusable half-mask or full-face respirator) may be required, based on a risk assessment.
- Gloves: Protect hands from dust, grime, and cleaning solutions, and can improve grip.
- Head Protection: A hard hat might be necessary if there is a risk of falling objects from above, or when working around racking or in areas where personnel are on lifts.
- Ladder Safety: While the use of ladders for high dusting should be minimized in favor of extension tools , if a ladder must be used, it must be the correct type for the job, inspected before use, set up on a stable and level surface, and used according to safe ladder practices (e.g., maintaining three points of contact). Workers should be trained in safe ladder use, and such use should be approved by a manager.
- Aerial Lift/EWP Safety: Only trained and certified operators are permitted to use aerial lifts. Pre-use inspections, adherence to manufacturer’s operating instructions, use of fall protection (harness and lanyard), and awareness of surroundings are critical.
- Area Securement: The area directly beneath where high-level dusting is being performed should be cordoned off using caution tape or barriers to protect other workers or pedestrians from falling debris, tools, or dust.
- Training: All personnel involved in high-level dusting must receive comprehensive training on the safe use of equipment (vacuums, lifts), hazard identification (e.g., recognizing potentially combustible dust, unstable racking), proper PPE selection and use, and emergency procedures.
- Equipment Inspection: All equipment, especially high-reach poles, vacuum hoses, connections, and any lifting devices, must be inspected before each use to ensure they are in good working order and free from damage.
2.3. Managing Combustible Dust: Risks and Mitigation
Combustible dust is a fine, solid particulate material that, when suspended in the air in the right concentration and exposed to an ignition source, can cause a fire or a violent explosion. Many materials commonly found or processed in warehouses can generate combustible dust, including wood (from pallets, crating), paper and cardboard, plastics, textiles, food products (flour, sugar, spices), and some metals.
Identification and Hazards
Combustible dust often accumulates in hidden and hard-to-reach areas such as on top of beams, trusses, ductwork, conduit, machinery, and high shelving. The danger lies in its potential for both primary and secondary explosions. A smaller, initial (primary) explosion can dislodge larger quantities of accumulated dust from these surfaces, creating a much larger dust cloud. This cloud can then be ignited by the primary event or another ignition source, leading to a devastating secondary explosion that can destroy structures and cause severe injuries or fatalities. Even seemingly minor ignition sources, such as static electricity discharge, sparks from faulty equipment, or hot surfaces, can trigger a combustible dust event.
OSHA Concerns
OSHA is increasingly focused on combustible dust hazards. While there isn’t a single comprehensive OSHA standard for combustible dust across all industries, the agency enforces safety through the General Duty Clause (requiring employers to provide a workplace free from recognized hazards) and by referencing consensus standards from organizations like the National Fire Protection Association (NFPA), such as NFPA 652 (Standard on the Fundamentals of Combustible Dust) and NFPA 61 (Standard for the Prevention of Fires and Dust Explosions in Agricultural and Food Processing Facilities). OSHA mandates the control of dust accumulation, particularly in areas with friction or restricted ventilation, and citations for inadequate combustible dust management are common.
Specialized Cleaning Procedures and Equipment
- Adherence to Guidelines: All cleaning activities in areas with potential combustible dust must strictly adhere to OSHA guidelines and relevant NFPA standards.
- Explosion-Proof (Intrinsically Safe) Vacuums: This is the most critical piece of equipment. Only vacuum cleaners specifically designed and certified as explosion-proof for the class of dust present should be used. These vacuums are constructed with non-sparking motors and components and are grounded to prevent static discharge, eliminating potential ignition sources during the cleaning process. They must also be equipped with HEPA filters to capture fine dust particles effectively.
- No Compressed Air for Blow-Down (Generally): Using compressed air to blow dust off surfaces is generally discouraged in areas with combustible dust, as it can create a dust cloud within the explosive range and spread the hazard. If blow-down is absolutely necessary (e.g., for inaccessible areas), it must be done under very controlled conditions, with all ignition sources eliminated, and often only when other methods are not feasible, following strict NFPA guidelines. Vacuuming is the preferred method.
- Regular and Thorough Cleaning: The key to managing combustible dust is to prevent its accumulation. This requires frequent, scheduled, and thorough cleaning of all surfaces where dust can settle, including overhead structures, equipment, and hidden areas. The cleaning frequency will depend on the rate of dust generation.
- Proper Dust Disposal: Collected combustible dust must be handled and disposed of carefully according to regulations to prevent it from becoming a hazard elsewhere.
2.4. Ambient Dust Control Measures
In addition to cleaning settled dust, controlling airborne (ambient) dust is crucial for maintaining air quality and reducing overall dust levels in a warehouse.
- Ventilation Systems: Well-designed and maintained industrial ventilation systems, including local exhaust ventilation (LEV) at dust-generating sources and general dilution ventilation, can significantly reduce airborne dust concentrations. Extractor fans can create airflow patterns that pull dust particles towards collection points or filters. Regular inspection and cleaning of ventilation components, including ductwork and filter replacement, are essential for optimal performance.
- Air Filtration Units: Strategically placed industrial air filtration units, often equipped with multi-stage filters including HEPA filters, can continuously circulate and clean the air in specific zones or throughout the warehouse. These are particularly useful in areas with high dust generation or for targeting specific contaminants.
- Water Dust Suppression (Fogging/Misting): For certain types of dust and in specific environments, water-based dust suppression systems can be effective. These systems release a fine mist or fog of water droplets into the air. The droplets collide with airborne dust particles, causing them to agglomerate and become heavy enough to settle out of the air. Automated systems can be programmed to operate at intervals or when dust levels exceed a certain threshold. This method is often used in large open areas or for controlling dust from bulk material handling.
- Dust Control Curtains and Barriers: Physical barriers, such as industrial curtains or temporary walls, can be used to isolate dust-generating activities or areas from the rest of the warehouse. This helps contain dust at its source and prevents it from migrating to cleaner zones or sensitive products.
- Operational Practices:
- Minimize Material Movement: Reducing unnecessary traffic of vehicles and personnel can lessen the amount of dust stirred up from floor surfaces.
- Control Vehicle Speed: Enforcing speed limits for forklifts and other vehicles can minimize the creation of airborne dust from tire friction and air displacement.
- Proper Material Storage: Storing dusty materials in sealed containers, bags, or on pallets covered with plastic sheeting can prevent them from releasing dust into the environment.
- Entrance Matting: Using high-quality industrial matting systems at entrances and exits can help trap dirt and dust from footwear and vehicle wheels, preventing it from being tracked further into the facility.
By implementing a combination of these high-level and ambient dust control measures, warehouses can significantly improve air quality, enhance safety, protect products and equipment, and maintain a cleaner, more efficient working environment.
Chapter 3: Effective Spill Management and Remediation Protocols
Spills are an unfortunate but common occurrence in busy warehouse and logistics environments. Whether it’s a minor product leak or a significant chemical release, a swift, safe, and effective response is crucial to protect personnel, prevent environmental contamination, minimize operational disruption, and ensure regulatory compliance.
3.1. Rapid Response: Cleaning Chemical, Oil, and General Product Spills
The initial actions taken in the first few minutes of a spill are often the most critical.
Initial Assessment and Containment
- Safety First – Assess the Situation: The immediate priority is the safety of personnel. If a spill occurs, workers should quickly assess the situation from a safe distance. Identify the spilled material if possible (e.g., by looking at container labels or referring to manifests). Determine if there are immediate dangers such as fire, toxic fumes, or corrosive properties. If the spill is large, highly hazardous, or beyond the capabilities of on-site personnel, evacuate the immediate area and call for emergency services.
- Notify Personnel: Alert nearby workers and the designated supervisor or spill response team immediately.
- Don Appropriate PPE: Before approaching the spill, personnel involved in the cleanup must don the correct Personal Protective Equipment (PPE) based on the nature of the spilled material. This is determined by the Safety Data Sheet (SDS) for chemicals.
- Stop the Source (If Safe): If the source of the spill can be safely stopped (e.g., turning off a valve, uprighting a fallen container), this should be done to prevent further release. Do not attempt this if it puts personnel at risk.
- Contain the Spill: The next critical step is to prevent the spill from spreading. Use absorbent materials like socks, booms, or dikes to create a perimeter around the spill. This is especially important for liquid spills to keep them from reaching drains, waterways, or larger areas of the warehouse floor.
Specific Procedures for Different Spill Types
- Oil and Fuel Spills (e.g., diesel, hydraulic fluid):
- Hazards: Flammability, slip hazard, environmental contamination.
- Action: Eliminate all ignition sources in the vicinity (no smoking, welding, or equipment that could spark). Use oil-specific (oleophilic and hydrophobic) absorbents such as white pads, pillows, or loose granular absorbents. These will absorb the oil but repel water, which is useful if water is also present.
- Chemical Spills (General – Acids, Bases, Solvents):
- Hazards: Corrosivity, toxicity, reactivity, flammability (varies greatly by chemical).
- Action: Always consult the Safety Data Sheet (SDS) first. The SDS provides specific information on hazards, required PPE, and appropriate cleanup procedures for that particular chemical.
- For acids or bases, neutralization may be required before absorption. Use appropriate neutralizing agents (e.g., soda ash or baking soda for acids; a mild acid like citric acid for bases). Apply neutralizers slowly to avoid excessive heat or splattering.
- Use universal (typically gray or black) absorbent pads, socks, or loose absorbents for most general chemical spills once neutralized or if direct absorption is indicated by the SDS. For aggressive or highly reactive chemicals, specialized hazmat absorbents (often yellow) may be necessary.
- Non-Hazardous Product Spills (e.g., food items, beverages, water-based non-toxic liquids):
- Hazards: Primarily slip hazards, potential for pest attraction if not cleaned promptly, possible staining.
- Action: While less critical from a hazardous material perspective, these spills still require immediate attention. Contain the spread if liquid. Use general-purpose absorbents (pads, granular) to soak up liquids. Sweep or scoop up solid or absorbed materials. Clean the affected area with an appropriate detergent and ensure it is thoroughly dried to eliminate slip risks.
Cleanup and Disposal
- Once the spill is contained and absorbed (and neutralized if necessary), use tools like non-sparking shovels, scoops, or brooms to carefully collect the contaminated absorbent materials.
- Place all contaminated waste, including used PPE, into appropriate, clearly labeled disposal bags or containers (e.g., heavy-duty plastic bags, drums). The labeling should indicate the nature of the waste.
- Dispose of the waste in strict accordance with all local, state, and federal environmental regulations. If the spilled material was hazardous, the resulting waste is also considered hazardous and typically requires handling and disposal by a licensed hazardous waste transporter and disposal facility. Maintain records of hazardous waste disposal.
The true impact of a spill extends far beyond the immediate cost of cleanup materials. A lack of adequate preparedness—such as missing or incomplete spill response plans, insufficient or incorrect spill kit supplies, or inadequately trained personnel—can dramatically escalate the consequences and overall costs. When responses are slow or improper, safety risks to employees are magnified due to prolonged exposure or incorrect handling of hazardous substances. The spill itself can spread over a much wider area, seeping into porous concrete, contaminating soil if outdoors, or entering drainage systems. This broader contamination footprint necessitates more extensive, time-consuming, and therefore more expensive remediation efforts. Operational downtime also increases as larger sections of the warehouse may need to be cordoned off for longer periods. Furthermore, failures in spill response, reporting, or disposal can lead to substantial fines from regulatory agencies like OSHA and the EPA. In cases of significant environmental contamination, the costs for cleanup can be exorbitant, coupled with severe damage to the company’s reputation and public trust. Thus, proactive investment in comprehensive spill preparedness—including robust plans, regular training, and well-stocked, strategically located spill kits tailored to site-specific hazards—is not merely an expense but a critical cost-avoidance strategy. The upfront costs of such preparedness are often trivial compared to the potential financial and non-financial liabilities of a poorly managed spill.
Table 2: Spill Response Quick Reference: Initial Actions by Spill Type
Spill Type | Immediate Hazard Assessment | Primary PPE (Minimum) | Stop the Source (If Safe) | Containment Method | Protect Drains? | Ventilation Consideration | Notification | Key Reference |
---|---|---|---|---|---|---|---|---|
Oil/Fuel (e.g., diesel, hydraulic fluid) | Flammability, slip hazard, environmental toxicity | Nitrile/oil-resistant gloves, safety goggles/face shield | Yes | Oil-specific absorbent socks/booms, dikes, loose oil absorbent | Yes, critical | Yes, for fumes | Supervisor, Safety Team | SDS |
Industrial Chemicals (Acids/Bases) | Corrosivity, toxicity, reactivity (refer to SDS) | Chemical-resistant gloves (per SDS), chemical splash goggles & face shield, apron/suit | Yes (with caution) | Chemical-resistant/Hazmat (yellow) socks/booms, dikes, compatible loose absorbents; Neutralize first if required | Yes, critical | Yes, critical for vapors (per SDS) | Supervisor, Safety Team, potentially Emergency Services (if large/highly hazardous) | SDS |
Non-Hazardous Product (e.g., food, benign liquids) | Slip hazard, pest attraction | General-purpose gloves, safety glasses (if splash risk) | Yes | General purpose absorbent socks, pads, loose absorbents | Yes (if large) | As needed | Supervisor | N/A |
Derived from
3.2. Hazardous Material Spill Control: Preparedness and Action
Handling hazardous materials (hazmat) requires a higher level of preparedness due to the potential for severe health impacts, environmental damage, and regulatory scrutiny.
Emergency Response Plan
A formal, written Emergency Action Plan (EAP) or Spill Response Plan is a cornerstone of hazmat safety and is often mandated by regulations like OSHA’s HAZWOPER standard or as part of an EPA SPCC plan. This plan should be site-specific and, at a minimum, include:
- Identification of Potential Hazards: A list of hazardous materials on site and their locations.
- Roles and Responsibilities: Clearly defined roles for a spill response team, supervisors, and employees.
- Notification Procedures: Who to contact internally (e.g., supervisor, EHS manager) and externally (e.g., emergency services, regulatory agencies) and when.
- Evacuation Plans: Routes and procedures for evacuating personnel if necessary.
- Spill Control Procedures: Step-by-step actions for containment, cleanup, and decontamination for different types of anticipated spills, referencing SDSs.
- PPE Requirements: Specific PPE to be used for different hazardous materials.
- Decontamination Procedures: How to decontaminate personnel and equipment after a spill.
- Waste Disposal: Procedures for compliant disposal of contaminated materials.
- Training Requirements: Details of initial and refresher training for all relevant personnel.
- The plan should be regularly reviewed, updated, and drilled.
Essential Spill Kit Contents and Usage
Strategically located, clearly marked, and regularly inspected spill kits are vital for an effective initial response. Contents should be tailored to the specific hazards present in the warehouse but generally include:
- Personal Protective Equipment (PPE): A range of gloves (nitrile, chemical-resistant), chemical splash goggles, face shields, impervious aprons or coveralls, and respiratory protection (e.g., cartridge respirators suitable for specific chemical vapors, as indicated by SDSs).
- Absorbents:
- Socks/Booms: For creating barriers and containing the spread of liquids.
- Pads/Pillows: For soaking up pooled liquids.
- Loose Absorbents: Granular materials like vermiculite, clay, or specialized chemical absorbents.
- Types should include oil-only (white), universal (gray/black for general liquids), and hazmat (yellow for aggressive chemicals like strong acids/bases).
- Neutralizers: Packets or containers of neutralizing agents for acid spills (e.g., sodium bicarbonate, sodium carbonate/soda ash) or basic spills (e.g., citric acid). Some commercial neutralizers change color to indicate when neutralization is complete.
- Containment Tools: Non-sparking shovels, scoops, brooms, and squeegees for collecting absorbed material. Temporary drain covers or plugs.
- Disposal Supplies: Heavy-duty, chemical-resistant disposal bags or sealable plastic drums, clearly labeled for hazardous waste.
- Signage: Caution tape or warning signs to secure and demarcate the spill area.
- Instructions/SDS: Laminated quick-reference spill response instructions and access to SDSs for chemicals stored in the area. Spill kits must be restocked immediately after use.
OSHA/EPA Requirements for Hazardous Spill Response
Several key regulations govern hazardous spill response:
- OSHA 29 CFR 1910.120 (HAZWOPER): This standard applies to employers engaged in hazardous waste operations, emergency response to releases of hazardous substances, and cleanup at uncontrolled hazardous waste sites. It mandates specific training levels, site characterization, safety and health programs, PPE, decontamination, and emergency response plans. Warehouses with significant hazmat storage or potential for large releases may fall under aspects of HAZWOPER for their emergency response teams.
- OSHA 29 CFR 1910.38 (Emergency Action Plans): Requires employers to have an EAP, which must include procedures for reporting emergencies (like hazardous spills), evacuation, and rescue/medical duties.
- EPA Regulations (Resource Conservation and Recovery Act – RCRA): Title 40 CFR Parts 260-279 establish “cradle-to-grave” management standards for hazardous waste, including generation, transportation, treatment, storage, and disposal. Spilled hazardous materials and contaminated cleanup debris are often classified as hazardous waste.
- EPA Spill Prevention, Control, and Countermeasure (SPCC) Rule (40 CFR Part 112): Requires facilities that store, handle, use, or consume oil or oil products above certain threshold quantities, and which could reasonably be expected to discharge oil into navigable waters or adjoining shorelines, to develop and implement an SPCC Plan. This plan outlines measures to prevent oil spills and procedures for responding to them.
- Emergency Planning and Community Right-to-Know Act (EPCRA): Requires facilities handling Extremely Hazardous Substances (EHSs) above threshold planning quantities to notify State Emergency Response Commissions (SERCs) and Local Emergency Planning Committees (LEPCs). LEPCs develop community emergency response plans. Facilities may also have reporting requirements under EPCRA for certain chemical releases.
- Employee Training: OSHA mandates that employees are trained on the hazards of chemicals in their work area (Hazard Communication Standard), proper use of PPE, and emergency procedures, including spill response relevant to their duties.
3.3. Post-Spill Surface Decontamination and Remediation
After the bulk of a spill has been absorbed and removed, the affected surfaces must be decontaminated to eliminate any remaining hazardous residues.
Techniques for Neutralizing and Cleaning Contaminated Surfaces
The goal of decontamination is to remove or neutralize contaminants to a safe level.
- Physical Removal: Gross contamination (visible material) should be physically removed first by methods such as wiping, scraping, or gentle rinsing.
- Chemical Neutralization: If the spill involved an acid or a base, the surface should be treated with an appropriate neutralizing agent. For example, a solution of baking soda or soda ash can be used for acid spills. The pH of the surface should be tested after neutralization (e.g., with pH paper) to ensure it is within a safe range (typically pH 6-8) before proceeding with further cleaning.
- Cleaning with Solutions/Solvents: After gross removal and neutralization (if applicable), wash the surface with a suitable cleaning solution or detergent. The choice of cleaner depends on the contaminant and the surface material. Surfactants in detergents help to lift and emulsify residues. For some organic contaminants, specific solvents might be needed, but care must be taken as solvents can be flammable, toxic, or damage certain surfaces or PPE. Always check compatibility.
- Rinsing: Thoroughly rinse the cleaned area with fresh water (or an appropriate rinsing solution) to remove any remaining cleaning agents and loosened contaminants. Multiple rinses with smaller volumes of clean solution are generally more effective than a single rinse with a large volume.
- Disinfection/Sterilization: If the spill involved biological hazards (e.g., in a food-grade warehouse or a spill of biohazardous material), the area must be disinfected using an EPA-registered disinfectant appropriate for the pathogens of concern. Ensure the disinfectant is left on the surface for the required contact time (dwell time) specified on its label to be effective.
- Systematic Cleaning: When cleaning the spill area, work from the outer edges of the contaminated zone inward towards the center. This helps prevent spreading the contamination to clean areas.
- Ventilation: Ensure good ventilation during the decontamination process, especially if using volatile cleaning agents or if the spilled material produced vapors.
Proper Disposal of Contaminated Materials
All materials used in the cleanup and decontamination process that have come into contact with the hazardous substance are considered contaminated and must be managed appropriately:
- Collection: Collect all contaminated items, including used absorbents, wipes, PPE (gloves, suits, respirators if disposable), and any tools that cannot be effectively decontaminated, in designated, leak-proof, and clearly labeled hazardous waste containers.
- Segregation: If different types of hazardous wastes are generated that are incompatible, they must be kept separate.
- Regulatory Compliance: Disposal must comply with all RCRA regulations for hazardous waste. This includes proper labeling, storage, manifesting, and transportation by a licensed hazardous waste hauler to a permitted treatment, storage, and disposal facility (TSDF).
- Record Keeping: Maintain detailed records of all hazardous waste generated and disposed of, including manifests, as required by EPA and state regulations.
Documentation
Thorough documentation of the entire spill incident and response is critical for regulatory compliance, insurance purposes, and internal review to improve future preparedness:
- Incident Report: Document the date, time, location, type and quantity of material spilled, cause of the spill (if known), personnel involved, and any injuries or exposures.
- Response Actions: Detail the steps taken for containment, cleanup, decontamination, and waste disposal.
- Notifications Made: Record who was notified (internal and external agencies) and when.
- Waste Disposal Records: Keep copies of hazardous waste manifests.
- This documentation helps demonstrate due diligence and can be invaluable if regulatory questions arise.
Chapter 4: Cleaning Protocols for Specialized Warehouse Zones
Beyond general floor and high-level cleaning, warehouses contain specialized zones that present unique cleaning challenges and require tailored protocols to maintain safety, efficiency, and compliance.
4.1. Loading Dock Cleaning: Maintaining Safety and Efficiency in High-Traffic Areas
Loading docks are critical hubs of activity in any warehouse, constantly exposed to external elements and heavy operational wear. Their cleanliness is directly linked to safety and operational throughput.
Common Issues
Loading docks are prone to a variety of cleanliness and safety issues:
- Debris Accumulation: Dirt, dust, mud, leaves, and gravel are tracked in by trucks and personnel. Packaging materials like broken pallet fragments, shrink wrap, cardboard scraps, and strapping bands accumulate rapidly during loading and unloading operations. This debris creates significant trip hazards.
- Spills: Oil, fuel, hydraulic fluid leaks from trucks, as well as product spills, are common. These create slippery surfaces and can attract pests.
- Weather-Related Hazards: Rainwater, snow, and ice can make dock surfaces extremely slippery and hazardous.
- Grease and Grime: Over time, grease and grime from vehicle exhaust and operational activities can build up on dock surfaces, levelers, and surrounding walls.
Cleaning Procedures
A multi-faceted approach is needed to keep loading docks clean and safe:
- Regular Sweeping and Debris Removal: This should be a frequent, ideally daily, task, or even performed between truck loads if traffic is heavy. All loose debris, including packaging waste and broken pallets, must be promptly removed to prevent trip hazards and maintain an orderly area.
- Immediate Spill Cleanup: All spills, whether oil, chemical, or product, must be addressed immediately using appropriate absorbents and cleaning methods as detailed in Chapter 3. Oil and grease spills should be covered with absorbents before being mopped or scrubbed.
- Pressure Washing: Periodic pressure washing is essential for deep cleaning loading dock surfaces, dock pits, and adjacent walls. This helps remove ingrained dirt, tire marks, grease, and other stubborn residues. The frequency might be every few months, depending on use and exposure. Hot water pressure washers are particularly effective for tackling grease and oil.
- Weather-Related Cleaning: Actively manage weather-related issues. Ensure rainwater drains properly. Remove snow and apply de-icing agents promptly to prevent ice formation and maintain safe footing.
- Degreasing: For concrete dock floors with persistent grease or oil stains, apply industrial degreasers, allow appropriate dwell time, scrub with stiff brushes, and then rinse thoroughly (often with a pressure washer).
- Trash Management: Provide ample, clearly marked trash and recycling bins in the loading dock area and ensure they are emptied regularly before overflowing.
Equipment
- Industrial Sweepers: For large dock areas, ride-on or robust walk-behind sweepers can efficiently collect loose debris. Models like the Kärcher KM 75/40 W Bp are suitable for such tasks.
- Pressure Washers: Commercial or industrial-grade pressure washers are necessary. Hot water units (e.g., Kärcher HDS 3.5/30) offer superior performance for grease and oil.
- Floor Scrubbers: Ride-on or walk-behind scrubbers can be used on sealed or smooth concrete dock surfaces to provide a deeper clean and help minimize slip hazards after sweeping.
- Manual Tools: Heavy-duty brooms, mops, buckets, scrub brushes, and squeegees are also essential for spot cleaning and smaller tasks.
- Absorbents and Spill Kits: Keep spill kits readily accessible on or near the loading dock for quick response to leaks and spills.
Safety and Slip/Trip/Fall Prevention
Loading docks are inherently hazardous; good housekeeping is a primary defense.
- Lighting: Ensure the loading dock area is well-lit, both internally and externally, to enhance visibility and prevent accidents. Regularly check and replace burnt-out bulbs.
- Clear Pathways: Keep walkways and work areas free of clutter, equipment, and stored materials.
- Dock Edge Markings: Use high-visibility paint or reflective tape to clearly mark the edges of the dock and changes in elevation to prevent falls.
- Guardrails/Barriers: OSHA mandates fall protection for open dock edges (e.g., guardrails, chains, or barriers when a truck is not present).
- Dock Plates and Levelers: Ensure dock boards, plates, and levelers are in good condition, properly secured during use, and have their load capacity clearly marked and adhered to. Regular inspection and maintenance are crucial.
- Footwear: Encourage or require workers to wear sturdy, non-slip safety footwear.
- Training: Train all employees who work on or around loading docks on safe work practices, hazard recognition, and emergency procedures. This includes procedures for safely interacting with trucks and trailers.
- Weather Seals: Consider installing weather seals or brush seals on dock doors to help prevent rain, snow, wind, and pests from entering the dock area, keeping it cleaner and drier.
4.2. Battery Charging Area Maintenance: Ensuring Safety and Compliance
Battery charging areas for electric forklifts and other powered industrial trucks (PITs) are zones with specific hazards that demand rigorous cleaning and safety protocols.
Hazards
- Acid Spills and Leaks: Lead-acid batteries contain sulfuric acid, a highly corrosive electrolyte. Spills or leaks during watering, charging, or due to battery damage can cause severe chemical burns to skin and eyes, and damage equipment and concrete floors.
- Hydrogen Gas (Gassing): During the charging process, lead-acid batteries produce hydrogen gas, which is colorless, odorless, and highly flammable. If ventilation is inadequate, hydrogen can accumulate and create an explosive atmosphere if an ignition source (spark, flame, hot surface) is present.
- Electrical Hazards: Batteries store significant electrical energy. Accidental short-circuiting of terminals by metal tools, jewelry, or improper connections can cause sparks, arcing, battery explosions, or electric shock. Charging equipment itself also presents electrical hazards.
- Corrosion: Acidic residue and fumes can cause corrosion on battery terminals, cables, connectors, charging equipment, and storage racks, leading to poor electrical connections, reduced battery life, and equipment failure.
- Heavy Lifting: Batteries are heavy; proper material handling equipment (e.g., hoists, conveyors, specialized battery carts) is needed for changing batteries to prevent musculoskeletal injuries.
Cleaning Procedures for Acid Residue and Corrosion
Regular cleaning is essential to neutralize acid, remove corrosion, and maintain a safe environment.
- Routine Cleaning of Batteries:
- Spot Cleaning: Regularly (e.g., weekly) inspect and clean the tops of battery cases to remove any acidic residue, dust, and grime. This prevents conductive pathways from forming between terminals and the case.
- Thorough Washing: Depending on usage and conditions, entire batteries should be thoroughly washed 2 to 4 times per year. This often involves removing the battery from the truck and washing it in a designated area with appropriate containment for wash water.
- Neutralizing Agents: Spilled electrolyte and acid residue must be neutralized before cleaning.
- Common neutralizers include baking soda (sodium bicarbonate) – typically a solution of one pound per gallon of water – or soda ash (sodium carbonate).
- Commercial battery acid neutralizers are also widely available. Many of these products contain a pH indicator that changes color to visually confirm when the acid has been neutralized (e.g., AcidSorb, NAB Battery Acid Cleaner & Neutralizer).
- Application and Rinsing:
- Liberally spray or pour the neutralizing solution onto the spilled acid or affected surfaces (battery cases, terminals, connectors, racks, floor). Allow sufficient dwell time for the neutralization reaction to complete.
- After neutralization is confirmed (e.g., by color change or pH testing), thoroughly rinse the batteries and the area with clean water using a hose or low-pressure washer. Ensure that rinse water is managed appropriately, especially if it may contain lead or other contaminants; check local discharge regulations.
- Floor Cleaning in Charging Areas:
- Absorbent products used on floor spills can soak up liquid acid but may leave active acid residue in the pores and cracks of concrete, often visible as white chalky marks. Liquid neutralizers are more effective at seeping into these areas for complete neutralization.
- Once neutralized, the floor should be cleaned with a suitable industrial floor cleaner (e.g., NAB Citrus Cleaner is mentioned as a neutral pH product safe for industrial flooring after acid neutralization).
- Products to Avoid:
- Using baking soda as a dry powder or thick paste directly on battery terminals can sometimes form a conductive paste that is difficult to rinse free and may impede good electrical contact. A solution is generally preferred.
- Avoid using caustic soda (sodium hydroxide) for neutralization, as it can be overly aggressive, potentially damage plastic battery casings, and create a highly alkaline byproduct if overused.
- Cleaners containing alcohol or petroleum-based solvents should not be used on battery casings as they can warp, crack, or degrade the plastic.
- Corrosion Prevention: Keep battery terminals and connectors clean, dry, and tight. Applying a thin coat of non-conductive terminal protector spray after cleaning can help prevent future corrosion.
Ventilation, PPE, and Eyewash Station Requirements (OSHA)
OSHA has specific requirements for battery charging areas to mitigate the associated hazards:
- Ventilation: Adequate ventilation must be provided to ensure diffusion of gases (primarily hydrogen) from the battery and to prevent the accumulation of an explosive mixture]. This typically involves mechanical ventilation systems designed to keep hydrogen concentrations well below the Lower Explosive Limit (LEL), often recommended to be below 1% hydrogen by volume or 25% of the LEL.
- Personal Protective Equipment (PPE): Employers must provide, and ensure workers use, appropriate PPE when handling acids or batteries. This includes:
- Eye and Face Protection: Face shields worn over chemical splash goggles].
- Hand Protection: Acid-resistant rubber gloves].
- Body Protection: Acid-resistant aprons or coats].
- Eyewash and Safety Shower: Facilities for quick drenching of the eyes and body must be provided within 25 feet (7.62 meters) of areas where employees are handling battery electrolyte or charging batteries]. These stations must be unobstructed, clearly marked, and regularly tested.
- Spill Control and Neutralization: Facilities must be provided for flushing and neutralizing spilled electrolyte]. This includes having neutralizing agents and spill cleanup materials readily available.
- Fire Protection: Appropriate fire extinguishers (typically Class ABC, but verify based on specific site hazards) must be available and maintained. Smoking and other ignition sources are strictly prohibited in charging areas.
- Floor Construction: Floors in battery charging areas should ideally be of acid-resistant construction or otherwise protected from acid accumulations (e.g., with coatings or containment)].
- Maintenance Practices: Vent caps on batteries must be kept in place and functioning during charging to avoid electrolyte spray]. Battery tops should be kept clean, dry, and free of corrosion. Chargers should be turned off when connecting or disconnecting leads. Charging apparatus should be protected from damage by trucks].
4.3. Maintaining Hygiene in Integrated Office Spaces and Restrooms
Office spaces, restrooms, and employee break rooms co-located within a warehouse facility present a unique hygiene challenge. They are susceptible to the transfer of industrial grime, dust, and other contaminants from the operational areas, demanding more rigorous cleaning protocols than standalone commercial offices.
Addressing Industrial Grime and Dust Transfer
The constant movement of personnel and materials between the warehouse floor and these ancillary areas means that dirt, dust, grease, and even chemical residues can be easily tracked in. This necessitates:
- Enhanced Entrance Matting: High-performance, multi-zone matting systems should be installed at all transition points from the warehouse to office, restroom, and break room areas. These mats help scrape, capture, and hold dirt and moisture from footwear.
- Increased Cleaning Frequency: Surfaces in these areas, especially floors, will require more frequent cleaning. Daily vacuuming (with HEPA filter vacuums to capture fine industrial dust) and mopping of hard floors is often essential.
- Targeted Dusting: Regular dusting of all horizontal and vertical surfaces, including desks, shelves, window sills, and electronic equipment, is needed to manage settled dust that migrates from the warehouse.
Cleaning and Disinfection Protocols for Shared Facilities
A two-step process of cleaning (removing visible dirt and impurities) followed by disinfection (killing germs) is recommended for optimal hygiene.
- Restrooms:
- Frequency: Due to the potential for higher soil loads from the industrial environment, restrooms in warehouses should be cleaned and disinfected at least daily, and potentially multiple times per day (e.g., 2x/day is suggested for industrial/warehouse settings) depending on usage.
- Tasks: Thoroughly clean and disinfect all high-touch surfaces (door handles, light switches, faucets, flush handles, stall locks, soap and towel dispensers), toilets (bowls, seats, exterior), urinals, sinks, and countertops. Mop and disinfect floors. Empty and sanitize trash receptacles.
- Products: Use EPA-registered hospital-grade disinfectants effective against a broad spectrum of bacteria and viruses.
- Supplies: Ensure consistent restocking of soap, paper towels, toilet paper, and hand sanitizer.
- Office Spaces and Break Rooms:
- Frequency: Daily cleaning and sanitizing are typically required.
- Tasks: Wipe down and sanitize all frequently touched surfaces such as desks, tables, chairs, keyboards, mice, telephones, light switches, and door handles. Clean and sanitize surfaces in kitchenettes or break areas, including countertops, sinks, microwave ovens (interior and exterior), and refrigerator handles. Vacuum carpets and upholstered furniture; mop hard floors. Empty trash and recycling bins regularly.
- Deep Cleaning: Periodically schedule deep cleaning for these areas, which includes tasks like cleaning light fixtures, inside and on top of cabinets, walls, and windows.
Cross-Contamination Prevention Strategies
Preventing the spread of germs and contaminants from one area to another, particularly from restrooms or the warehouse floor into office spaces, is critical.
- Color-Coded Cleaning System: Implement a color-coded system for cleaning tools (microfiber cloths, mops, buckets, etc.). Assign specific colors to different areas or tasks (e.g., red for restrooms/toilets, yellow for sinks/washroom surfaces, blue for general office areas/desks, green for kitchen/food prep areas). This visually reinforces the separation of tools and prevents a cloth used to clean a toilet from being used on an office desk.
- Procedural Discipline:
- Clean from Cleanest to Dirtiest: Within a room (like a restroom), clean less contaminated surfaces (e.g., mirrors, countertops) before more contaminated ones (e.g., toilets).
- Clean from Top to Bottom: Dust and clean higher surfaces before lower ones to prevent re-soiling cleaned areas.
- Tool Hygiene and Management:
- Change cleaning cloths and mop heads frequently, especially when moving from a dirty area to a cleaner one, or between rooms.
- Use fresh or properly laundered microfiber cloths for each task or area. Microfiber is effective at trapping dirt and pathogens.
- Clean and disinfect cleaning equipment (buckets, mops, carts) regularly.
- Hand Hygiene for Cleaning Staff: Emphasize and enforce strict handwashing protocols for cleaning personnel: before starting work, after cleaning specific areas (especially restrooms), after handling waste, before and after breaks, and after removing gloves. Provide access to hand sanitizers when soap and water are not immediately available.
- Dedicated Equipment: Where feasible, consider using entirely separate sets of cleaning equipment (vacuums, mops, etc.) for the warehouse production areas versus the integrated office and welfare facilities to minimize the transfer of heavy industrial soils and potential chemical residues.
- Air Quality Management: Ensure adequate ventilation in office and restroom areas to help dilute airborne contaminants. If dust infiltration from the warehouse is a significant and persistent issue, consider supplementary air filtration units in these ancillary spaces.
- Employee Education (General Staff): Encourage all employees to practice good personal hygiene, clean up personal spills in break rooms promptly, and report any facility hygiene issues.
The presence of office spaces, restrooms, and break rooms directly within or adjacent to the primary operational areas of a warehouse creates a substantially increased hygiene challenge compared to standalone office buildings. These ancillary spaces are under constant threat of contamination from the dust, dirt, grime, and potentially even chemical residues that are inevitably generated by and transported from the industrial activities of the warehouse. This transfer occurs via footwear, clothing, airborne particles, and equipment movement. Consequently, standard office cleaning routines are often insufficient to manage this heightened level of soiling. Cleaning protocols must be more frequent and intensive, and the cleaning agents used may need to be more robust (while remaining safe for occupants and surfaces) to effectively deal with industrial-type grime. Furthermore, there’s a critical need for stringent cross-contamination prevention measures to protect the health of office-based personnel and to prevent these ancillary areas from becoming breeding grounds for pests or secondary sources of contamination that could migrate back into the warehouse, potentially affecting stored products. This amplified hygiene burden underscores the value of professional cleaning services that possess expertise in both industrial-scale cleaning and the specific hygiene requirements of commercial office and welfare facilities, ensuring a holistic and effective approach to cleanliness throughout the entire integrated site.
Chapter 5: Embedding Safety and Compliance in Warehouse Cleaning Programs
A successful warehouse cleaning program is not just about aesthetics or efficiency; it is fundamentally rooted in safety and regulatory compliance. Integrating these elements from the outset is crucial for protecting workers, avoiding penalties, and ensuring sustainable operations.
5.1. Adhering to OSHA Standards for Warehouse Cleanliness and Safety
The Occupational Safety and Health Administration (OSHA) sets forth numerous standards that directly or indirectly pertain to warehouse cleanliness and the safety of cleaning operations.
Key Regulations
- 29 CFR 1910.22 (Walking-Working Surfaces): This is a foundational OSHA standard for all general industry workplaces, including warehouses. It mandates that “All places of employment, passageways, storerooms, service rooms, and walking-working surfaces are kept in a clean, orderly, and sanitary condition”. It further requires that floors in workrooms be “maintained in a clean and, to the extent feasible, in a dry condition” and kept free of hazards like “sharp or protruding objects, loose boards, corrosion, leaks, spills, snow, and ice”. This standard directly impacts floor cleaning, spill response, and general housekeeping.
- 29 CFR 1910.1200 (Hazard Communication Standard – HCS): This standard requires employers to inform employees about the chemical hazards they may be exposed to in the workplace. For cleaning operations, this means ensuring that all cleaning chemicals are properly labeled, Safety Data Sheets (SDSs) for each chemical are readily accessible to employees, and employees are trained on the hazards of these chemicals and the protective measures to take.
- 29 CFR 1910.132 (Personal Protective Equipment – General Requirements): Employers are required to assess workplace hazards and provide appropriate PPE to employees at no cost. They must also ensure employees are trained on the proper selection, use, care, and limitations of their PPE. This is critical for cleaning staff who may be exposed to dust, chemicals, or other hazards.
- Specific Area and Task Standards:
- Battery Charging Areas: OSHA standards like 1926.441 (for construction, but often referenced for general industry principles) and 1917.157 (Marine Terminals, also providing good practice guidance) address requirements for ventilation to prevent hydrogen gas accumulation, provision of PPE (face shields, aprons, rubber gloves), facilities for quick drenching of eyes and body (eyewash stations/showers), and procedures for neutralizing spilled electrolyte.
- Loading Dock Safety: While no single OSHA standard covers all loading dock safety, various regulations address fall protection from open dock edges, safe operation of powered industrial trucks (forklifts), and maintaining clear, unobstructed pathways.
- Combustible Dust: OSHA addresses combustible dust hazards through the General Duty Clause and by referencing NFPA standards. Employers must take steps to prevent hazardous accumulations of combustible dust.
- Sanitation (Restrooms): 29 CFR 1910.141 outlines requirements for toilet facilities, including maintaining them in a sanitary condition, providing hot/cold running water, soap, and hand drying means.
Impact of Non-Compliance
Failure to comply with OSHA standards can lead to serious consequences, including:
- Citations and significant financial penalties.
- Potential for temporary or permanent operational shutdowns until hazards are abated.
- Increased risk of workplace accidents, injuries, and illnesses, leading to higher workers’ compensation costs and lost productivity.
- Damage to company reputation and employee morale.
Proactive Measures for Compliance
- Regular Audits and Inspections: Conduct routine self-inspections to identify and correct potential hazards and ensure cleaning standards are being met.
- Documented Cleaning Procedures: Develop and maintain written cleaning procedures for all tasks and areas, incorporating safety precautions and PPE requirements.
- Comprehensive Training: Provide thorough and ongoing training to all cleaning staff on safe work practices, chemical handling, equipment operation, PPE use, and emergency procedures.
- Record Keeping: Maintain records of training, inspections, maintenance of cleaning equipment, and hazardous waste disposal. Cleaning logs and checklists can provide verifiable documentation during audits.
5.2. Essential Personal Protective Equipment (PPE) for Cleaning Operations
Selecting and correctly using the appropriate PPE is paramount for protecting cleaning personnel from the diverse hazards encountered in a warehouse environment. The specific PPE required will vary based on the task, the cleaning agents used, and the potential contaminants present.
Matching PPE to Task
A risk assessment should guide PPE selection for each cleaning task. Table 4 provides a general matrix for common warehouse cleaning activities.
Table 4: Personal Protective Equipment (PPE) Matrix for Warehouse Cleaning Tasks
Cleaning Task | Eye/Face Protection | Hand Protection | Respiratory Protection | Body Protection | Foot Protection | Fall Protection |
---|---|---|---|---|---|---|
Routine Floor Sweeping/Scrubbing (Ride-On) | Safety Glasses | Work Gloves | Optional/Dust Mask | Standard Workwear | Non-Slip Safety Shoes | N/A |
High-Level Dusting (Non-Combustible, from ground w/ extensions) | Safety Goggles | Dusting Gloves | N95/P100 Respirator | Standard Workwear | Non-Slip Safety Shoes | N/A |
High-Level Dusting (Combustible Dust or using Aerial Lift) | Safety Goggles/Face Shield | Work Gloves | P100 Respirator / Supplied Air (for confined space/high concentration) | Coveralls | Non-Slip Safety Shoes | Full Body Harness & Lanyard (for Aerial Lift) |
Chemical Spill Cleanup (e.g., Mild Detergent) | Safety Goggles | Waterproof/General Purpose Gloves | Not Usually Required | Apron (optional) | Non-Slip Safety Shoes | N/A |
Hazardous Material Spill Cleanup (e.g., Corrosive, Flammable – per SDS) | Chemical Splash Goggles & Face Shield | Chemical-Resistant Gloves (specific to chemical) | Cartridge Respirator (specific to chemical vapor – per SDS) | Chemical-Resistant Apron/Suit | Chemical-Resistant Boots | N/A |
Battery Acid Handling/Spill Cleanup | Face Shield over Goggles | Acid-Resistant Rubber Gloves | Acid Gas Respirator (if high vapor/poor ventilation) | Acid-Resistant Apron | Acid-Resistant Boots | N/A |
Restroom Cleaning (Routine) | Safety Glasses (if splash risk) | Waterproof Cleaning Gloves | Not Usually Required | Apron (optional) | Non-Slip Shoes | N/A |
Loading Dock Pressure Washing | Face Shield/Goggles | Waterproof Gloves | Dust/Mist Respirator (if significant aerosolization or contaminants) | Waterproof Outerwear | Waterproof Non-Slip Boots | N/A |
Derived from
Training and Maintenance of PPE
- Training: Employees must be thoroughly trained on why PPE is necessary, how to properly select, don (put on), doff (take off), adjust, and wear their assigned PPE. They must also understand its limitations, proper care, maintenance, useful life, and disposal.
- Inspection and Maintenance: PPE must be inspected before each use for any damage or defects. Reusable PPE (like respirators or chemical-resistant suits) must be cleaned and stored according to manufacturer instructions. Damaged or worn-out PPE must be replaced immediately.
- Fit Testing: For tight-fitting respirators, OSHA requires initial and periodic fit testing to ensure an effective seal.
5.3. Implementing Effective Cleaning Schedules and Staff Training
A structured cleaning schedule and well-trained staff are the operational backbone of any successful warehouse cleaning program.
Developing Cleaning Schedules
Cleaning schedules should be tailored to the specific needs of the facility, considering factors like size, traffic levels, types of materials handled, and operational hours. They should clearly define what needs to be cleaned, how often, by whom, and with what methods/equipment. Table 3 provides a general guideline for frequencies.
Table 3: Recommended Cleaning Frequencies for Key Warehouse Areas
Area/Task | Recommended Frequency | Key Activities |
---|---|---|
Main Warehouse Floors (High Traffic Aisles, Staging Areas) | Daily | Sweeping/Scrubbing (ride-on machines) |
Main Warehouse Floors (Lower Traffic, Storage Zones) | Weekly / As Needed | Sweeping/Spot Scrubbing |
High Surfaces (Racking, Ceilings, Ductwork, Light Fixtures) | Quarterly to Bi-Annually (or more if very dusty/combustible dust) | Specialized Vacuuming (e.g., high-reach systems), Controlled Blow-Down, Manual Dusting with Extensions |
Loading Docks (Surface & Debris) | Daily / Per Shift | Sweeping, Debris Removal (pallets, wrap), Spill Check & Cleanup |
Loading Docks (Pressure Wash) | Monthly / Quarterly | Deep Cleaning, Degreasing, Grime Removal |
Battery Charging Area (Spot Clean Residue, Terminals) | Weekly | Inspect, Neutralize & Clean Acid Residue on batteries/racks/floor |
Battery Charging Area (Full Battery Wash) | 2-4 times per year (or as needed) | Thorough Neutralization & Washing of entire batteries |
Integrated Office Spaces (General Cleaning) | Daily | Dusting, Wiping Surfaces, Vacuuming/Mopping Floors, Trash Removal |
Restrooms (within Warehouse Facility) | Daily (multiple times if high use, e.g., 2x/day) | Clean & Disinfect All Fixtures (toilets, sinks, urinals), Surfaces, Floors; Restock Supplies; Trash Removal |
Break Rooms/Kitchenettes (within Warehouse Facility) | Daily | Wipe Surfaces (tables, counters), Clean Appliances (microwave, fridge exterior), Mop Floors, Trash Removal |
Spill Cleanup (Any Area) | Immediately | Assess, Contain, Clean/Neutralize, Remediate, Proper Disposal (per spill type and SDS) |
Schedules should be documented, posted where visible, and responsibilities clearly assigned. Regular review and adjustment of the schedule based on observations and feedback are important.
Importance of Staff Training
Comprehensive and ongoing training is arguably the most critical investment in a cleaning program. Warehouse cleaning operations often involve complex tasks, specialized machinery, and interaction with potentially hazardous chemicals and environments.
Without adequate training, staff may inadvertently use equipment incorrectly, leading to damage or inefficient cleaning. They might misuse chemicals, creating safety risks for themselves and others, or damaging the surfaces they are trying to clean. Perhaps most critically, untrained staff may fail to follow essential safety protocols, increasing the likelihood of accidents, injuries, or OSHA violations.
Well-trained staff, on the other hand, understand not only how to perform tasks but also why certain procedures are in place. This deeper understanding fosters better on-the-job decision-making, such as selecting the correct PPE for a given hazard or accurately identifying and responding to a hazardous spill. Efficient and correct use of resources—including time, cleaning agents, and equipment—is a direct outcome of good training, leading to lower operational costs and superior cleaning results. Furthermore, a properly trained team is more likely to proactively identify and report potential hazards they observe during their duties, contributing to a stronger overall safety culture within the facility. Therefore, robust training programs should cover:
- Specific Cleaning Procedures: Detailed methods for each task and area, including the sequence of operations.
- Safe and Effective Equipment Operation: Correct use of all cleaning machinery (sweepers, scrubbers, vacuums, pressure washers, aerial lifts if used), including pre-use checks, operational techniques, and routine maintenance.
- Chemical Handling (HazCom): Understanding Safety Data Sheets (SDSs), proper dilution ratios, application methods, storage requirements, disposal procedures, and the specific hazards associated with each cleaning chemical used.
- Personal Protective Equipment (PPE): As detailed above – selection, use, limitations, and maintenance.
- Safety Protocols: Emergency procedures (fire, medical, spill), ladder safety, electrical safety, lockout/tagout if applicable to equipment maintenance, hazard recognition, and reporting.
- Spill Response: Procedures for containing, cleaning, and disposing of various types of spills, especially hazardous materials. Training should be a continuous process, with initial comprehensive training for new hires and regular refresher sessions for all staff to reinforce knowledge and introduce new techniques or address new hazards.
The Strategic Advantage of Professional Warehouse Cleaning Services
Maintaining a clean, safe, and compliant warehouse or logistics facility is a complex and demanding undertaking. While in-house cleaning efforts can address some basic needs, the scale, specialized requirements, and inherent risks associated with large industrial environments often make partnering with a professional cleaning service a more strategic and ultimately more effective solution. The advantages offered by reputable professional services in terms of expertise, equipment, efficiency, safety assurance, and overall value are compelling.
Unmatched Expertise and Specialization
Professional industrial cleaning companies bring a depth of knowledge and experience that is difficult to replicate with an internal team whose primary focus is not cleaning. These firms specialize in the unique challenges of warehouse environments, understanding the behavior of industrial soils, the intricacies of cleaning around heavy machinery and racking, and the specific requirements for maintaining various surfaces, from concrete floors to high-level ductwork. Their personnel are typically trained and certified in advanced cleaning techniques, the safe handling of industrial-strength cleaning agents and hazardous materials, and current safety protocols, including OSHA regulations. This specialized expertise ensures that cleaning tasks are performed correctly, safely, and to a consistently high standard.
Access to Specialized Equipment and Advanced Techniques
Warehouses require industrial-grade cleaning equipment designed for durability, efficiency, and large-scale applications. Professional services invest in and maintain a fleet of such equipment, including heavy-duty ride-on floor sweepers and scrubbers, high-powered pressure washers, specialized high-reach vacuum systems for elevated dusting, and potentially advanced tools like electrostatic sprayers for disinfection. For an individual warehouse to purchase, maintain, and train staff on such a diverse range of specialized equipment can be prohibitively expensive and logistically burdensome. Professionals also stay abreast of the latest cleaning technologies and methodologies, including the use of eco-friendly, sustainable, and OSHA-compliant cleaning products, ensuring a more effective and responsible clean.
Enhanced Efficiency and Productivity for Core Warehouse Operations
One of the most significant benefits of outsourcing cleaning is the ability for warehouse management and staff to concentrate on their core business functions—logistics, inventory management, order fulfillment, and shipping—rather than diverting time and resources to cleaning. Professional cleaning services can often schedule their work during off-peak hours or shutdowns to minimize disruption to warehouse operations. Moreover, a consistently clean, well-organized, and hazard-free warehouse environment inherently boosts the productivity and efficiency of the warehouse’s own employees. Clear pathways, easily accessible inventory, and reduced risk of equipment malfunction due to dirt and debris all contribute to smoother, faster workflows.
Ensuring Consistent Safety, Regulatory Compliance, and Risk Mitigation
Navigating and adhering to the complex web of OSHA, EPA, and other relevant health and safety regulations is a critical responsibility for warehouse operators. Professional cleaning services are typically well-versed in these standards and can play a vital role in helping facilities maintain compliance, thereby avoiding costly fines, potential legal issues, and operational disruptions. They implement systematic cleaning programs that proactively identify and address potential hazards, such as slippery floors, dust accumulations (including combustible dust), chemical spill risks, and improperly maintained areas.
This significantly reduces the risk of common warehouse accidents like slips, trips, and falls, as well as more serious incidents like fires or chemical exposures. Furthermore, many professional services provide detailed cleaning logs and checklists, offering verifiable documentation of cleaning activities, which can be invaluable during safety audits or inspections.
Engaging professional warehouse cleaning services should be viewed not merely as an operational expense but as a strategic investment in risk management. Warehouse environments are inherently fraught with potential risks stemming from heavy machinery, constant material movement, the possibility of spills, and the pervasive accumulation of dust, which can sometimes be combustible.
Maintaining these facilities to the high standards of cleanliness and safety required by regulations and best practices demands specialized knowledge, appropriate equipment, rigorous training, and consistent, diligent effort—a significant undertaking for in-house resources whose primary responsibilities lie elsewhere. Failure to meet these exacting standards can precipitate a cascade of negative consequences, including OSHA violations carrying hefty fines, workplace accidents leading to injuries and compensation claims, environmental incidents requiring costly remediation, and damage to valuable inventory or equipment.
Professional cleaning companies are specifically structured to manage these cleaning-related risks. They make substantial investments in comprehensive staff training programs, cutting-edge cleaning technologies, and up-to-date knowledge of evolving regulatory landscapes.
By outsourcing these complex and often hazardous cleaning operations—such as working at height for high-level dusting, managing chemical spills, or ensuring the safe cleaning of battery charging areas—a warehouse effectively transfers a significant portion of the associated operational and liability risks to the service provider.
This third party is inherently better equipped and more focused on mitigating these specific risks. This transfer allows warehouse management to dedicate their attention and resources to core business risks and strategic operational objectives, secure in the knowledge that a critical component of facility safety, compliance, and overall hygiene is being expertly and professionally managed. The frequently cited benefit of “peace of mind” is a direct and valuable outcome of this strategic delegation of risk.
Cost-Effectiveness and Overall Value Proposition (ROI)
While engaging a professional cleaning service involves an upfront financial commitment, the long-term return on investment (ROI) often makes it a highly cost-effective decision. This ROI is realized through multiple avenues:
- Reduced Direct Costs: Prevention of accidents minimizes expenses related to medical treatment, workers’ compensation claims, and potential legal fees.
- Equipment and Facility Longevity: Regular, proper cleaning prevents the buildup of corrosive substances and abrasive debris, extending the life of machinery, racking, and the building fabric itself, thus reducing repair and replacement costs.
- Improved Inventory Control: A cleaner, more organized warehouse reduces the risk of product damage, contamination, or misplacement, leading to better inventory accuracy and reduced losses.
- Enhanced Employee Well-being: A clean and healthy work environment demonstrably improves employee morale, reduces absenteeism due to illness, and can even contribute to higher retention rates.
- Business Reputation: A visibly clean and well-maintained facility projects an image of professionalism, quality, and attention to detail, which can positively influence the perceptions of customers, suppliers, auditors, and potential employees.
In conclusion, the decision to hire a professional warehouse cleaning service is a strategic one that aligns with the goals of optimizing operational efficiency, ensuring a safe and healthy workplace, maintaining regulatory compliance, and ultimately enhancing the overall value and resilience of the logistics operation. The expertise, specialized resources, and systematic approach offered by professionals provide benefits that typically far outweigh the costs, allowing businesses to focus on what they do best.