1. The Critical Role of Cleanliness in Industrial HVAC and Duct Systems
Industrial Heating, Ventilation, and Air Conditioning (HVAC) systems are far more extensive and complex than their residential or commercial counterparts. These systems are engineered to manage climate control, ensure air filtration, provide necessary ventilation for specialized industrial processes, and maintain a safe and comfortable environment for workers.
An industrial HVAC system is an intricate network comprising extensive ductwork, powerful air handling units (AHUs), fans, sophisticated filtration systems, heating and cooling coils, and often specialized components such as industrial dust collectors and dedicated exhaust systems. The scope of such a system, particularly when considering cleaning, encompasses every component from the point where air enters to where it is discharged, including return air grilles, all duct segments, the interior surfaces of AHUs, mixing boxes, coil compartments, condensate drain pans, humidifiers, dehumidifiers, and fan assemblies. Given this complexity and the critical functions these systems perform, their cleanliness is not merely an aesthetic concern but a fundamental aspect of operational integrity and safety.
Contact us!
Regular and thorough cleaning of these systems is non-negotiable in industrial environments. Unlike office buildings, industrial facilities often generate a wide array of unique and potentially hazardous contaminants, including various types of dust, chemical vapors, and process-specific byproducts, which are inevitably drawn into and circulated by the HVAC systems.
The accumulation of these substances within ductwork and on HVAC components directly and significantly impacts operational efficiency, poses serious safety risks (including fire and health hazards), and can lead to non-compliance with increasingly stringent regulatory standards. The adage “out of sight, out of mind” can have perilous consequences when applied to these vital, yet often concealed, systems. It is a dangerous misconception to assume that if a problem isn’t immediately visible, it doesn’t exist or doesn’t warrant attention. The reality is that contaminants build up progressively, and their effects, though initially subtle, can escalate into major operational and safety crises.
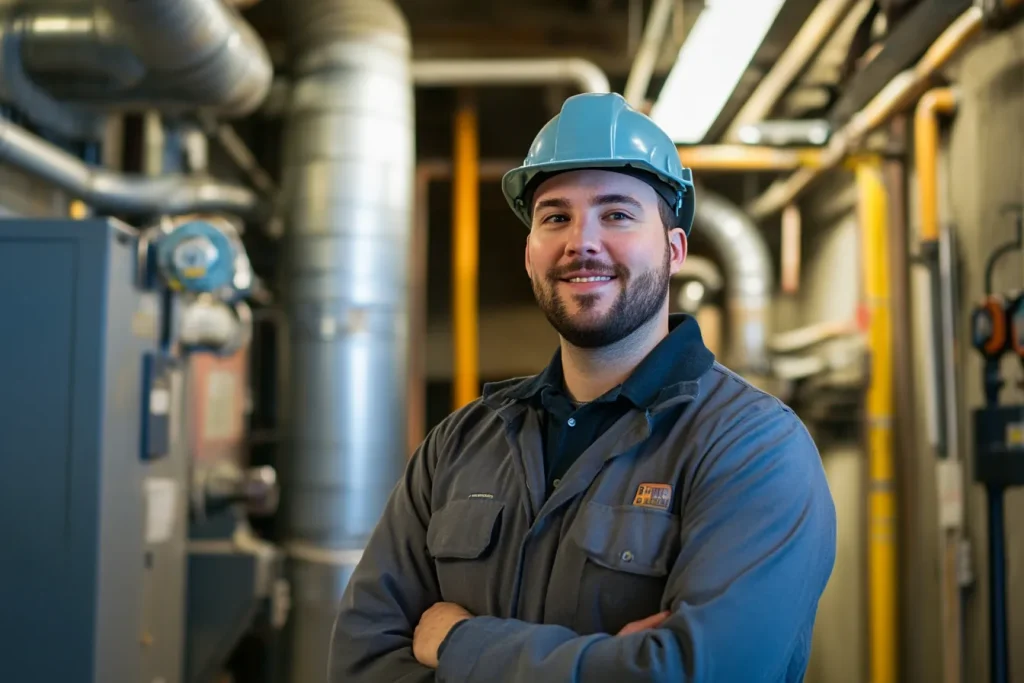
The very definition of an “HVAC system” for cleaning purposes, especially within industrial contexts and as guided by organizations like the National Air Duct Cleaners Association (NADCA), is comprehensive. It covers every component from air intake to discharge. This holistic perspective is frequently overlooked by those unfamiliar with professional cleaning standards.
A piecemeal approach, such as cleaning only the easily accessible duct runs, is fundamentally insufficient. Such limited efforts often lead to rapid recontamination of the cleaned sections by contaminants drawn from the uncleaned portions of the system. This systemic understanding underscores that effective HVAC hygiene demands a comprehensive strategy. Consequently, the maintenance of these complex and critical systems, including their regular professional cleaning, should be recognized as an essential operational expenditure and integrated as a key element within the overarching facility management strategy, rather than being treated as an optional or deferrable task.
2. Understanding the Unseen Threats: Contaminants in Industrial Ductwork
Industrial HVAC systems are constantly challenged by a diverse array of airborne materials. Understanding the specific nature of these contaminants is the first step toward effective management and remediation.
Common Types of Industrial Dust, Debris, and Contaminants:
The contaminants found within industrial HVAC systems are varied and often specific to the processes occurring within the facility. These can be broadly categorized:
- General Particulates: This includes common dust and dirt that infiltrates from outdoors or is generated by general building wear, as well as soot from combustion processes or external sources.
- Process-Specific Dusts: Many industrial operations generate unique dusts. Examples include fine wood dust from milling or sanding, flour and sugar dust in food processing plants, metallic fines from grinding or fabrication, chemical powders in pharmaceutical or chemical manufacturing, and pulverized minerals. A critical characteristic of many of these dusts is their potential combustibility.
- Biological Contaminants: While HVAC systems are designed to condition air, they can inadvertently become breeding grounds for biological contaminants if moisture is present or if filtration is inadequate. These include mold spores, bacteria, and, in some specialized industrial settings like agricultural processing, animal dander.
- Chemicals, Vapors, and Aerosols: Manufacturing processes can release a variety of chemical vapors, mists, and aerosols into the air, which are then drawn into the HVAC system. Oils used in machinery can also become airborne and deposit within ductwork.
- Other Debris: In facilities that have undergone recent construction or renovation, construction debris can find its way into the ductwork. Less commonly, but still possible, are infestations by insects or rodents, leaving behind nests, droppings, and carcasses. In older buildings, deteriorating materials like asbestos-containing insulation can also become a serious airborne hazard within the system.
Identifying these specific contaminants is of paramount importance because the appropriate cleaning methodologies, the necessary safety precautions for cleaning personnel, and the potential risks associated with the contaminants themselves (such as toxicity, corrosivity, or combustibility) vary significantly.
Sources of Contamination in Industrial HVAC Systems:
Contaminants can enter and accumulate in industrial HVAC systems from both external and internal sources:
- External Sources: The primary external source is the outdoor air drawn into the system for ventilation. This air can carry pollen, common dirt, industrial emissions from neighboring facilities, and other pollutants. If the system’s air intake filtration is inadequate or poorly maintained, these external contaminants can easily enter and distribute throughout the facility.
- Internal Sources:
- Manufacturing Processes: Many industrial activities are significant generators of airborne contaminants. Operations like grinding, cutting, sanding, mixing, and combustion processes release fine particles, dust, and fumes directly into the facility’s air.
- Building Materials and Maintenance: Deteriorating building components, such as insulation (especially older asbestos-containing materials), paint, or sealants, can release particles into the air. Maintenance and repair activities can also generate dust and debris.
- Water Intrusion: Leaks from roofing, plumbing, or condensation within the HVAC system itself can introduce moisture, creating favorable conditions for mold and bacterial growth on duct surfaces, coils, and in drain pans.
- Inadequate Filtration: One of the most critical internal sources of system-wide contamination is poorly performing air filters. Filters that are damaged, improperly installed, ill-fitting, or of an incorrect type for the application can allow significant amounts of particulate to bypass the filtration stage. When this occurs, the HVAC system, which is intended to improve air quality, paradoxically becomes a distribution network for these pollutants, actively spreading them throughout the facility. “Dirt trails” observed on or around filters are a clear indication of such bypass.
The diversity of contaminants present in industrial settings means that a standardized, “one-size-fits-all” cleaning approach is not only ineffective but can also be dangerous. For example, the procedures and equipment required for handling potentially combustible dusts, such as fine wood flour or metal dust, are vastly different from those used for general nuisance dust. Combustible dusts necessitate specialized equipment like explosion-proof vacuums and stringent anti-static precautions to prevent ignition. This inherent variability underscores the critical need for an expert assessment of the HVAC system and its specific contaminant load before any cleaning work commences. Such an assessment will inform the selection of appropriate cleaning methods, safety protocols, and personal protective equipment (PPE).
The following table provides an overview of common industrial HVAC contaminants, their typical sources, and associated risks:
Table 1: Common Industrial HVAC Contaminants, Sources, and Risks
Contaminant Type | Common Industrial Sources | Potential Risks |
---|---|---|
Combustible Dusts | Woodworking (wood dust), Food Processing (flour, sugar, spice dust), Metal Fabrication (metal dust/fines), Plastics Manufacturing, Agriculture (grain dust) | Fire, Flash Fire, Dust Explosion (primary & secondary), Respiratory Issues |
Chemical Particulates & Vapors | Chemical Plants, Pharmaceutical Manufacturing, Paint Shops, Printing, Metal Finishing | Toxic Exposure (acute/chronic), Respiratory Irritation/Disease, Carcinogenic Effects, System Corrosion |
Biological Contaminants | Facilities with moisture issues (leaks, condensation), Food Processing, Healthcare (less industrial but relevant for some AHUs) | Mold/Bacterial Growth, Allergies, Asthma Triggers, Respiratory Infections, Odors, Mycotoxin Exposure |
General Industrial Debris | General Manufacturing, Construction/Renovation, Warehousing, Foundries (soot, general dirt) | Reduced System Efficiency, IAQ Degradation, Nuisance Dust, Potential for harboring other contaminants |
Oils & Greases | Machining Operations, Commercial Kitchens (exhaust), Food Processing | Fire Hazard (especially in kitchen exhaust), Reduced Heat Transfer on Coils, Odors, Microbial Growth Substrate |
Fibers (e.g., Asbestos, Fiberglass) | Older Buildings (asbestos insulation), Facilities with exposed/deteriorating fiberglass insulation or duct liner | Serious Respiratory Diseases (Asbestosis, Mesothelioma, Lung Cancer for asbestos), Skin/Eye Irritation |
Understanding these contaminants and their origins is crucial not only for effective cleaning but also for developing long-term preventative strategies. These may include upgrading air filtration systems, implementing better source capture ventilation for dust-generating processes, or promptly addressing water leaks to prevent microbial growth.
3. The High Stakes of Neglect: Risks Associated with Dirty Industrial HVAC Systems
Failure to maintain cleanliness within industrial HVAC systems is not a trivial oversight; it carries significant and multifaceted risks that can impact occupant health, operational efficiency, energy consumption, and overall facility safety. The consequences of neglect can range from decreased productivity and increased utility bills to catastrophic incidents like fires and explosions.
Impact on Indoor Air Quality (IAQ) and Occupant Health:
The primary function of an HVAC system is to provide a comfortable and healthy indoor environment. However, when ductwork and components become laden with contaminants, the system can paradoxically become a source of indoor air pollution. The continuous recirculation of dust, allergens, mold spores, chemical vapors, and other particulates can lead to a host of adverse health effects for building occupants. These may include:
- Respiratory Problems: Short-term exposure can cause irritation of the eyes, nose, and throat, leading to coughing, sneezing, and shortness of breath. Long-term exposure to high levels of certain dusts can result in serious chronic conditions such as chronic obstructive pulmonary disease (COPD), asthma, and various forms of pneumoconiosis, like silicosis (from silica dust) or asbestosis (from asbestos fibers).
- Cardiovascular Issues: Studies have indicated that fine particulate matter can penetrate deep into the lungs and enter the bloodstream, potentially contributing to cardiovascular problems such as heart attacks and strokes.
- Cancer: Certain industrial dusts, notably silica and asbestos, are known human carcinogens. Prolonged exposure significantly elevates the risk of developing lung cancer and other forms of cancer.
- Neurological Effects: Exposure to certain metals present in industrial dust, such as lead and manganese, can cause neurological damage, with symptoms ranging from cognitive deficits to severe neurodegenerative diseases.
- Skin and Eye Irritation: Direct contact with certain types of dust can cause skin irritation, dermatitis, conjunctivitis, and other eye conditions.
- General Symptoms & “Sick Building Syndrome”: Even in the absence of specific diagnosed illnesses, poor IAQ can lead to general malaise among occupants, including headaches, fatigue, difficulty concentrating, and the perception of stale or musty odors, often associated with “Sick Building Syndrome”. Research indicates that cleaning air ducts can lead to a significant reduction in airborne dust and allergens, often by as much as 60%.
These health impacts are not only detrimental to individual well-being but also carry substantial costs for businesses in the form of decreased productivity, increased employee absenteeism, higher healthcare expenses, and potential worker compensation claims or legal liabilities.
Reduced System Efficiency and Increased Energy Consumption:
The accumulation of dirt and debris within an HVAC system acts as an impediment to its efficient operation. Clogged air filters, fouled heating and cooling coils, and dust-laden ductwork all contribute to restricted airflow. This forces the system’s fans and motors to work considerably harder to circulate the required volume of air, leading to several negative consequences:
- Increased Energy Consumption: Systems struggling against increased resistance consume significantly more energy. This translates directly into higher utility bills, a major operational expense for most industrial facilities. Studies have shown that professional HVAC cleaning can reduce fan and blower energy consumption by as much as 41% to 60%. The U.S. Environmental Protection Agency (EPA) has also found that cleaning various HVAC components can improve overall system efficiency by up to 20%.
- Reduced Performance: A compromised system may struggle to achieve desired heating or cooling capacities, leading to inconsistent temperatures and occupant discomfort.
- Premature Equipment Failure: The increased strain on motors, bearings, and other components due to restricted airflow and excessive workload can lead to premature wear and tear, more frequent breakdowns, and a shortened operational lifespan for expensive HVAC equipment. Facilities with well-maintained systems, including clean ductwork, can see their HVAC equipment last 30-50% longer than neglected systems.
The financial implications of such inefficiencies are substantial, impacting not only direct energy costs but also capital expenditure due to earlier-than-expected equipment replacement.
Fire Hazards: The Dangers of Combustible Dust Accumulation:
One of the most acute and potentially devastating risks associated with dirty industrial HVAC systems is the hazard of fire and explosion due to combustible dust accumulation. Many dusts generated in industrial processes – including those from wood, flour, sugar, starch, plastics, textiles, metals, and certain chemicals – are highly combustible when suspended in air in the right concentrations. HVAC systems can inadvertently create all the necessary conditions for a dust explosion, often referred to as the “Dust Explosion Pentagon”:
- Fuel: The accumulated combustible dust.
- Oxygen: Present in the air circulated by the system.
- Ignition Source: Could be a spark from electrical equipment, static discharge, friction, or an external fire.
- Dispersion: Dust particles suspended in the air, which can occur if settled dust is disturbed.
- Confinement: The enclosed spaces of ductwork, AHUs, or dust collectors can allow pressure to build rapidly during a deflagration, leading to an explosion.
Industry standards and regulatory bodies like OSHA recognize that even a seemingly small accumulation of dust, such as a layer 1/32 of an inch thick covering just 5% of a room’s surface area (including overhead structures and ductwork), can pose a significant explosion hazard. A primary dust explosion, perhaps within a piece of equipment or a section of ductwork, can be violent enough to dislodge larger quantities of accumulated dust elsewhere in the facility. This newly airborne dust can then ignite, leading to one or more secondary explosions that are often far more destructive and widespread than the initial event. HVAC ductwork, if laden with combustible dust, can act as a direct conduit, propagating fire and explosions rapidly from one area of a facility to another. Both OSHA and the National Fire Protection Association (NFPA) have established stringent regulations and standards for the assessment and control of combustible dust hazards in industrial workplaces.
The chain of consequences stemming from neglected HVAC cleaning is clear and impactful. Initial contaminant buildup directly degrades indoor air quality and poses health risks to occupants. This same buildup impedes system performance, leading to decreased energy efficiency and higher operational costs. The increased operational strain accelerates wear and tear, resulting in more frequent breakdowns and a shorter lifespan for the HVAC equipment. In industries dealing with combustible materials, this neglect culminates in a significantly elevated risk of catastrophic fire or explosion. This interconnected cascade of negative outcomes elevates industrial HVAC cleaning from a simple maintenance task to a critical strategic imperative for comprehensive risk management, operational excellence, and financial prudence. The availability of quantifiable data on benefits, such as the significant energy savings documented in studies , coupled with the severe potential consequences of inaction, provides a compelling business case for investing in regular, professional HVAC system cleaning.
4. The Comprehensive Guide to Industrial HVAC System Cleaning
Effective cleaning of industrial HVAC systems is a meticulous process that requires specialized knowledge, adherence to industry standards, and the use of appropriate tools and techniques. It begins with a thorough assessment and follows a structured approach to ensure all components are addressed safely and effectively.
Pre-Cleaning Assessment and Inspection: The NADCA Approach
Before any cleaning work commences, a comprehensive inspection and assessment phase is crucial. This initial step, strongly advocated by the National Air Duct Cleaners Association (NADCA), sets the stage for a successful cleaning project.
- Visual Inspections and Determining Cleaning Needs:
Qualified HVAC system cleaning contractors will perform detailed visual inspections of all readily accessible components of the HVAC system. This includes air handling units (AHUs), ductwork (supply, return, and exhaust), coils, drain pans, fans, and filtration systems. The purpose of this inspection is to determine the type and extent of contamination, identify any pre-existing damage to system components, and assess any specific challenges or hazards associated with the project. Documentation of any damaged components found during this inspection is essential and should be reported to the facility owner or manager.
The NADCA ACR (Assessment, Cleaning, and Restoration) Standard provides comprehensive guidelines on when HVAC system cleaning is warranted in industrial facilities. Cleaning is generally recommended if an inspection or the building’s operational history indicates one or more of the following conditions: significant accumulation of particulate contamination, compromised system performance due to contaminant buildup, unacceptable odors originating from the system, visible discharge of dirt or debris into the conditioned space, contamination resulting from fire, smoke, or water damage, infestation by birds, rodents, or insects, an increased risk of fire hazard (e.g., from combustible dust), contamination with construction particulate or debris, evidence of mold growth, deterioration of fibrous glass components, or as part of a proactive energy management or indoor air quality program.17 - Understanding NADCA Standards (ACR, The NADCA Standard):
ACR, The NADCA Standard for Assessment, Cleaning & Restoration of HVAC Systems, is the internationally recognized industry benchmark for HVAC hygiene. This comprehensive standard is widely specified for commercial and industrial projects and provides practical, industry-backed information for assessing new and existing HVAC systems, evaluating and verifying the cleanliness of components, preventing job-related hazards, and guiding the cleaning and restoration of HVAC systems to a specific level of cleanliness.
The ACR Standard emphasizes a performance-based approach, meaning the goal is to achieve a defined level of cleanliness, while also providing specific procedural guidelines for various cleaning tasks. It underscores the importance of having trained and qualified personnel perform the work. Ideally, projects should be overseen by an individual holding an Air Systems Cleaning Specialist (ASCS) certification, and inspections should be conducted by those with ASCS or Certified Ventilation Inspector (CVI) credentials, or equivalent qualifications demonstrating a working knowledge of HVAC systems, cleaning techniques, and industry standards. A thorough pre-cleaning assessment based on these standards ensures that the subsequent cleaning plan is tailored, effective, and addresses all pertinent issues, while also establishing a baseline against which post-cleaning cleanliness can be verified.
Core Components and Their Cleaning Methodologies:
Industrial HVAC systems consist of several key components, each requiring specific cleaning approaches to ensure the entire system is brought to a state of cleanliness.
- Ductwork Cleaning: Techniques for Removing Industrial Dust and Debris
The primary principle of duct cleaning, as emphasized by NADCA, is “source removal,” which involves physically dislodging and then capturing contaminants.7- Mechanical Agitation: Various tools are employed to loosen contaminants from the interior surfaces of the ductwork. These include manual brushes, power-driven rotary brushes, compressed air nozzles (often called “skipper balls”), and air whips, which are flexible rods with multiple tentacles that thrash against duct surfaces to dislodge debris. The choice of agitation tool depends on the duct type, size, and the nature of the contamination. Special care must be taken when cleaning internally lined ductwork (e.g., fiberglass lined) or flexible ducts to prevent damage to these materials.
- Negative Pressure and Particulate Collection: During the cleaning process, the section of ductwork being cleaned is placed under continuous negative pressure. This is achieved by attaching a powerful vacuum collection device, which can be truck-mounted for maximum power or a portable unit for accessibility, to the duct system. This negative pressure ensures that all dislodged dust, debris, and contaminants are drawn into the collection device and are not released into the building environment.
- HEPA Filtration: When the particulate collection equipment is exhausting air inside the building, it is mandatory to use High-Efficiency Particulate Air (HEPA) filtration. HEPA filters are rated to capture 99.97% of particles that are 0.3 microns in diameter or larger. If the equipment exhausts outside the building, adequate filtration must still be used to contain the debris removed from the HVAC system.
- Access Points: To facilitate cleaning, technicians may need to create service openings in the ductwork. These access points must be appropriately sized for the tools being used and must be securely and professionally sealed after the cleaning is completed. The goal is to render the ductwork “Visibly Clean” as defined by NADCA standards.
- Air Handling Unit (AHU) Deep Cleaning
AHUs are the operational core of most HVAC systems and can become heavily contaminated if neglected. Comprehensive AHU cleaning involves several components:- Cleaning Coils (Heating and Cooling): Coils are critical for heat exchange and airflow; accumulated dirt and grime severely reduce their efficiency. Cleaning methods include Type 1 (Dry Cleaning) for loose dust and debris, using HEPA-filtered vacuuming, brushing, or compressed air, and Type 2 (Wet Cleaning) for more adherent contaminants, which involves applying specialized, non-corrosive coil cleaning solutions followed by a low-pressure water rinse or steam cleaning. It is crucial to use cleaners appropriate for the coil material (e.g., copper, aluminum) to prevent corrosion. Any bent coil fins should be carefully straightened using a fin comb to restore proper airflow.
- Fan and Blower Assemblies: The fan housing, blades or vanes, scrolls, shafts, and drive assemblies must be thoroughly cleaned to remove all visible surface contamination in accordance with NADCA standards. After cleaning, lubrication of bearings may be necessary as per the manufacturer’s specifications.
- Condensate Drain Pans and Lines: These components collect moisture condensed out of the air and are prone to slime, mold, and bacterial growth if not regularly cleaned. They must be cleaned and flushed thoroughly to ensure proper drainage and prevent water damage or microbial amplification.
- Filter Racks and Filter Replacement: Filter racks should be cleaned each time filters are changed. Filters themselves are not typically cleaned but are replaced with new ones of the appropriate type and MERV (Minimum Efficiency Reporting Value) rating suitable for the specific industrial environment. The frequency of filter replacement depends on the operational environment and filter specifications.
- AHU Interior Surfaces & Disinfection: All interior surfaces of the AHU, including plenums, mixing boxes, and access doors, should be cleaned. If microbial contamination (e.g., mold) is confirmed through inspection or testing, disinfection using an EPA-registered antimicrobial agent may be considered after mechanical surface cleaning has been performed and if the need for such treatment is deemed necessary.
- Exhaust Duct Cleaning: Specialized Approaches
Industrial exhaust systems are designed to remove specific contaminants generated by processes, and their cleaning requires tailored approaches.- Grease Exhaust (e.g., Commercial Kitchens, Food Processing): These systems accumulate highly flammable grease deposits. Cleaning involves scraping, applying specialized chemical degreasers, and often using high-pressure hot water or steam to clean hoods, filters, fans, and ductwork down to the bare metal. NFPA 96, Standard for Ventilation Control and Fire Protection of Commercial Cooking Operations, is a key standard governing these systems.
- Chemical Fume and Particulate Exhaust: The cleaning methods for systems handling chemical fumes, vapors, or hazardous particulates depend heavily on the nature of the substances being exhausted. This may involve wet scrubbing techniques, the use of specialized vacuums designed for hazardous materials, or specific dry cleaning methods. Safety precautions are paramount due to the potential toxicity, reactivity, or corrosivity of the residues. Proper containment and disposal of cleaning waste are critical. Access points must be utilized or created, and all cleaning byproducts (e.g., wash water, dislodged debris) must be carefully contained and disposed of in accordance with environmental regulations. Failure to clean exhaust systems properly can lead to severe fire hazards (especially with grease), exposure of workers to harmful substances, violation of environmental permits, and inefficient ventilation of critical processes.
- Dust Collector Maintenance and Cleaning
Dust collectors are essential for capturing process-generated dust, including potentially combustible dusts. Their proper maintenance and cleaning are vital for safety and operational efficiency.- Filter Inspection and Replacement: Filters (bags, cartridges) are the heart of the dust collector. They require regular inspection for tears, holes, proper seals, and signs of blinding (clogging). Replacement should be based on differential pressure readings across the filters (a high reading indicates clogging), visual inspection, or the manufacturer’s recommended service intervals. Using the correct type and quality of filter media is crucial for performance and safety.
- Hopper Emptying: The hopper at the bottom of the dust collector is intended for the temporary collection of dust, not long-term storage. Hoppers must be emptied regularly and before they become overfilled. Dust backing up from an overfull hopper can damage filters, reduce collection efficiency, and significantly increase the risk of fire or explosion, especially if the dust is combustible.
- Pulse-Jet Cleaning System Checks (if applicable): Many dust collectors use a pulse-jet system (bursts of compressed air) to clean filters. The diaphragm valves and solenoid valves that control these pulses must be inspected regularly to ensure they are functioning correctly. Leaking or malfunctioning valves will result in ineffective filter cleaning and wasted compressed air. The compressed air pressure should also be maintained at the level specified by the manufacturer.
- Airlock Inspection: Rotary airlocks are often installed at the hopper discharge to maintain a seal and, in combustible dust applications, to act as an isolation device to prevent explosion propagation (as per NFPA standards). The flexible wipers or seals within the airlock wear over time and require regular inspection and replacement to maintain their effectiveness.
- Ductwork to and from the Collector: The ductwork leading to the dust collector must be kept clear to ensure that particulates are efficiently transported to the collector. Any accumulation in these ducts can reduce system performance and create hazards.
- Explosion Safety Systems: For collectors handling combustible dust, explosion protection systems (e.g., explosion vents, suppression systems, isolation devices) are often required by NFPA standards (such as NFPA 68 and NFPA 69). These critical safety systems must be regularly inspected and maintained according to their design specifications and relevant NFPA codes. A malfunctioning dust collector can lead to the release of hazardous dusts into the workplace or the environment, increased risk of dust explosions, and non-compliance with environmental and occupational safety regulations.
Specialized Tools and Equipment for Industrial HVAC Cleaning
Professional industrial HVAC cleaning relies on a range of specialized tools and equipment designed for effectiveness, safety, and efficiency.
- Access Tools: These include drills with various bit sizes, pneumatic cutters, and electric shears, used to create necessary service openings in ductwork or equipment housings where existing access is insufficient.
- Inspection Tools: To visually assess conditions inside ductwork and equipment, technicians use tools such as hand-held mirrors, direct-view periscopes (often with attached light sources), high-resolution CCTV camera systems that can navigate through ducts, and flexible borescopes.
- Agitation/Cleaning Tools:
- Brushes: A variety of brushes are used, from simple hand brushes for accessible areas to long-reach brushes and power-driven rotary brushes attached to flexible shafts. These can be driven by electric drills or pneumatic motors.
- Air-Based Tools: High-volume, high-pressure compressed air is used to power tools like air guns for general surface cleaning, air whips (flexible rods with multiple flailing tentacles equipped with air nozzles), and “skipper balls” or directional air nozzles that propel themselves through ductwork while dislodging debris.
- Vacuum Collection Devices: These are critical for source removal. Options include extremely powerful truck-mounted vacuum systems for large-scale projects and more maneuverable portable vacuums equipped with HEPA filters for use within facilities. For environments with combustible dust, specially designed explosion-proof vacuums are mandatory. These vacuums are constructed to prevent ignition sources and often feature grounding and bonding to dissipate static electricity, along with anti-static hoses and non-sparking cleaning tool attachments.
- Compressed Air Sources: Robust air compressors are needed to supply the large volumes of compressed air required by pneumatic cleaning tools.
- Coil Cleaning Tools: These include soft-bristled brushes that won’t damage delicate fins, fin combs for straightening bent fins, low-pressure sprayers for applying cleaning solutions and rinsing, and specifically formulated chemical coil cleaners.
- Safety Equipment: A comprehensive array of Personal Protective Equipment (PPE) is essential, including respirators (ranging from N95 masks to half-face or full-face respirators with appropriate cartridges, depending on the hazard), chemical-resistant gloves, disposable coveralls, eye protection (goggles or face shields), hard hats, safety harnesses for working at heights, and steel-toe boots. Lock-out/tag-out (LOTO) kits are vital for ensuring equipment is de-energized during servicing. Fall protection equipment is also necessary for elevated work. The availability and correct use of this specialized, often expensive, equipment is a key differentiator between professional services and DIY attempts, directly impacting the quality, safety, and efficiency of the cleaning project.
The following table summarizes key cleaning procedures for different HVAC components:
Table 2: Overview of Key Cleaning Procedures by HVAC Component
HVAC Component | Primary Cleaning Objectives | Key Methods/Tools | Relevant Standards (Examples) |
---|---|---|---|
Ductwork (General) | Remove accumulated dust, debris, microbial growth (if present); ensure clear airflow. | Mechanical agitation (brushes, air whips), negative air with HEPA filtration, contact vacuuming. | NADCA ACR |
AHUs – Coils | Restore heat transfer efficiency, remove insulating debris/biofilm, ensure proper airflow. | Dry cleaning (vacuum, brush), Wet cleaning (approved coil cleaners, low-pressure rinse/steam), fin straightening. | NADCA ACR |
AHUs – Fans/Blowers | Remove dust/debris from blades, housing, motor; ensure balanced operation. | Manual cleaning, vacuuming, compressed air. | NADCA ACR |
AHUs – Condensate Drain Pans | Remove slime, mold, blockages; ensure free drainage. | Scraping, cleaning with disinfectant cleaners, flushing lines. | NADCA ACR |
AHUs – Filters | Remove particulates from airstream (Note: Filters are typically replaced, not cleaned). | Removal of old filters, cleaning of filter racks/housings, installation of new, appropriately rated filters. | ASHRAE 52.2 (MERV) |
Exhaust Ducts (Grease) | Remove flammable grease deposits to bare metal; prevent fire hazards. | Scraping, chemical degreasers, high-pressure hot water/steam. | NFPA 96, NADCA ACR |
Exhaust Ducts (Chemical/Process) | Remove specific hazardous materials; ensure effective contaminant removal; prevent re-entry. | Method dependent on contaminant (wet scrubbing, specialized vacuuming, chemical neutralization). | NADCA ACR, OSHA Regs |
Dust Collectors | Maintain collection efficiency, prevent dust escape, mitigate fire/explosion risks. | Filter inspection/replacement, hopper emptying, pulse-jet system checks, airlock maintenance, cleaning of collector housing and associated ducting. | NFPA 652/660, NADCA ACR |
Safety First: Adhering to OSHA and NFPA Guidelines
Safety is paramount in any industrial HVAC cleaning operation. Professionals must adhere to a stringent set of safety protocols and regulations established by bodies like the Occupational Safety and Health Administration (OSHA) and the National Fire Protection Association (NFPA).
- Hazard Assessment: Before any work begins, a thorough hazard assessment must be conducted to identify all potential risks associated with the specific job site and the contaminants present. This includes chemical hazards (toxicity, corrosivity), physical hazards (falls, confined spaces, electrical), biological hazards (mold, bacteria), and the critical risk of combustible dust.
- Controlling Odors and Hazardous Substances: During the cleaning process, measures must be implemented to control the release of odors, dust, and potentially hazardous vapors into the surrounding environment. This often involves careful containment strategies, ensuring adequate ventilation in the work area, and using the negative pressure systems effectively.
- Personal Protective Equipment (PPE): The results of the hazard assessment will dictate the specific PPE required for the cleaning crew. This can range from basic dust masks and gloves to full-face respirators with specialized cartridges, chemical-resistant suits, hard hats, safety harnesses for work at height, and steel-toed boots.
- Lock-out/Tag-out (LOTO): All sources of energy (electrical, mechanical, pneumatic) to the HVAC equipment being cleaned (e.g., AHU motors, fans, electrical resistance heating coils) must be de-energized and locked out/tagged out according to established OSHA procedures before any cleaning or maintenance work begins. This prevents accidental startup and potential injury.
- Confined Space Entry: If cleaning requires personnel to enter confined spaces such as large ducts, plenums, or AHU casings, strict confined space entry procedures must be followed. This includes air monitoring, attendant personnel, rescue plans, and proper ventilation.
- Combustible Dust Safety (NFPA & OSHA Compliance): This is a critical area of concern in many industrial facilities. Key safety measures include:
- Preventing Ignition Sources: Rigorous efforts to eliminate all potential ignition sources, including static electricity, sparks from tools or equipment, open flames, and hot surfaces.
- Proper Grounding and Bonding: All cleaning equipment, especially vacuum systems, must be properly grounded and bonded to prevent the buildup and discharge of static electricity, which can ignite a dust cloud.
- Specialized Equipment: Use of industrial, explosion-proof HEPA-filtered vacuums and non-sparking cleaning tools is mandatory when dealing with combustible dusts.
- Dust Hazard Analysis (DHA): Cleaning contractors should be aware of the facility’s DHA (if one exists) or be able to recognize conditions that suggest a combustible dust hazard. They must operate in compliance with relevant NFPA standards such as NFPA 652 (Standard on the Fundamentals of Combustible Dust), the new consolidated NFPA 660 (Standard for Combustible Dusts and Particulate Solids), and any applicable industry-specific NFPA standards (e.g., NFPA 61 for agricultural/food, NFPA 484 for metals, NFPA 654 for general manufacturing, NFPA 664 for wood).
- Fall Protection: When working on rooftop units, elevated platforms, or near unprotected edges, appropriate fall protection measures (e.g., harnesses, lanyards, guardrails) must be used.
- Chemical Safety: If chemical cleaning agents or EPA-registered antimicrobial products are used, they must be handled according to the manufacturer’s instructions and Safety Data Sheet (SDS) information. Antimicrobial agents should only be applied if a need has been established (e.g., confirmed microbial contamination) and only after thorough mechanical cleaning has been completed. Adherence to these safety standards is not merely a matter of regulatory compliance; it is fundamental to protecting the health and safety of the cleaning crew, facility personnel, and the facility itself. It is also a key indicator of a professional and responsible cleaning service. The stringent safety protocols, particularly for high-risk scenarios like combustible dust or hazardous chemical residues, are interwoven with the effectiveness of the cleaning process. An unsafe cleaning operation can inadvertently create more significant hazards than it aims to resolve, such as triggering a dust explosion by using inappropriate equipment or causing widespread chemical exposure through improper containment.
Post-Cleaning Verification: Ensuring a Job Well Done
Once the cleaning process is complete, verification is essential to ensure that the HVAC system has been cleaned to the agreed-upon standard and is ready to be returned to service. NADCA provides clear guidelines for this crucial step.
- Conformity to NADCA Standards: The primary goal is to verify that the cleaning has rendered the HVAC components clean in accordance with NADCA Standards.
- Method 1: Visual Inspection: The most common method of verification is a thorough visual inspection of all cleaned surfaces within the HVAC system. Components should be “Visibly Clean,” meaning they are free from all non-adhered substances, debris, and contamination. This inspection should cover ductwork interiors, AHU components (coils, fans, drain pans), and any other areas included in the scope of work.
- Method 2: NADCA Vacuum Test (for Non-Porous Surfaces): If visual inspection is inconclusive, or if a more quantitative measure of cleanliness is required, the NADCA Vacuum Test can be performed on non-porous surfaces (like unlined metal ductwork). This scientific test involves vacuuming a defined area (typically 100 cm²) through a pre-weighed filter cassette using a calibrated air sampling pump. The cassette is then reweighed, and the net weight of debris collected must not exceed 0.75 mg/100 cm² for the surface to pass the test.
- Coil Cleaning Verification: Specific verification for cleaned coils includes checking for the removal of visible debris from between the fins and ensuring the fins are not damaged or excessively bent. Measuring the static pressure drop across the coil bank before and after cleaning can also provide a quantitative measure of improved airflow and cleaning effectiveness.
- Restoration of System Components: Any air volume control devices, such as dampers, that had their positions marked prior to cleaning must be restored to their original, marked settings. All access panels and service openings created for cleaning must be securely and properly sealed.
- Post-Project Documentation: Upon completion of the project, the cleaning contractor should provide the facility manager with comprehensive post-project documentation. This typically includes a written report detailing the work performed, the methods used, the results of the cleanliness verification (including visual records and any laboratory results if the NADCA Vacuum Test was conducted), chain of custody documentation if samples were sent to an external laboratory, and any other supporting documents or recommendations. This verification and documentation process provides assurance to the facility manager that the cleaning project was performed to a recognized industry standard and achieved the desired outcomes. It also provides valuable records for facility maintenance logs and compliance purposes. The systematic and scientifically grounded approach provided by the NADCA framework—encompassing thorough assessment, component-specific cleaning methodologies, robust engineering controls like negative pressure and HEPA filtration, and verifiable cleanliness outcomes—distinguishes professional HVAC cleaning from inadequate or superficial attempts. True professionalism in this specialized field is clearly defined by adherence to these established standards (NADCA, NFPA, OSHA), the proficient use of specialized equipment, and an unwavering commitment to thoroughness that spans from the initial assessment to the final verification. This sets a high benchmark that DIY efforts or unqualified contractors simply cannot achieve.
5. The Tangible Benefits of Professional Industrial HVAC Cleaning
Investing in professional cleaning for industrial HVAC systems yields a multitude of tangible benefits that extend beyond mere cleanliness. These advantages positively impact indoor air quality, system performance, energy expenditure, facility safety, and equipment longevity, contributing to a healthier, safer, and more cost-effective operational environment.
Significant Improvements in Indoor Air Quality:
One of the most immediate and noticeable benefits of thorough HVAC cleaning is a marked improvement in indoor air quality (IAQ). The process removes accumulated dust, allergens (such as pollen and mold spores), bacteria, volatile organic compounds (VOCs), and other potentially harmful airborne contaminants from the ductwork and HVAC components. This leads to:
- A reduction in unpleasant odors that may have been emanating from or distributed by the HVAC system.
- A healthier breathing environment for all employees and occupants, which can be particularly beneficial for individuals with pre-existing respiratory conditions, asthma, or allergies. Studies have shown that clean air ducts can lead to as much as a 60% reduction in airborne dust and allergens. Improved IAQ directly contributes to enhanced employee well-being, comfort, morale, and can lead to increased productivity and reduced absenteeism due to illness.
Enhanced HVAC System Efficiency and Airflow:
When HVAC components such as coils, fans, filters, and duct interiors are free of dirt, debris, and obstructions, the entire system can operate much closer to its original design specifications and peak efficiency. Key improvements include:
- Increased Supply Airflow: A groundbreaking multi-climate study conducted by NADCA demonstrated that professional HVAC system cleaning resulted in a 10% to 46% increase in supply airflow. This means more conditioned air is delivered where it’s needed, improving the system’s ability to heat, cool, and ventilate effectively.
- Improved Operational Efficiency: The same NADCA study also found that cleaning led to decreased pressure fluctuations within the system, contributing to smoother and more stable operation.
- Consistent Temperature Distribution: With improved airflow and efficiency, the system can better maintain consistent temperatures throughout the facility, enhancing occupant comfort. An efficient HVAC system not only performs its primary functions more effectively but also experiences less strain, contributing to its overall longevity.
Measurable Energy Savings:
The enhanced efficiency achieved through cleaning translates directly into significant energy savings. When fans, blowers, and motors do not have to work as hard to overcome the resistance caused by dirt and blockages, their energy consumption drops considerably.1
- The NADCA energy study documented a remarkable 41% to 60% reduction in the energy consumed by fans and blowers after professional cleaning.
- The U.S. EPA estimates that cleaning dirty coils and other HVAC components can improve the overall efficiency of the system by up to 20%, with homeowners potentially saving up to 15% on their energy bills. While these figures may vary for large industrial systems, the principle of substantial energy savings remains valid. These energy savings directly reduce a facility’s operational costs, offering a strong and often rapid return on the investment made in professional cleaning services.
Reduced Fire Risks and Enhanced Safety:
For many industrial facilities, particularly those handling combustible dusts (such as wood, flour, sugar, plastics, metals) or flammable materials like grease in exhaust systems, HVAC cleaning is a critical fire safety measure.
- The removal of accumulated combustible dust from ductwork, AHUs, and dust collectors drastically reduces the fuel load available for a fire or explosion.
- Clean ductwork prevents the ventilation system from becoming a pathway for the rapid spread of fire and smoke throughout the facility.
- Regular cleaning helps facilities maintain compliance with NFPA standards and OSHA regulations related to combustible dust management and fire prevention. Protecting lives, preventing catastrophic damage to assets, and ensuring business continuity by mitigating these severe fire risks are paramount concerns for any industrial operation.
Extended Equipment Lifespan and Reduced Maintenance Costs:
An HVAC system that operates cleanly and efficiently experiences less strain on its mechanical components, such as motors, fans, bearings, and compressors. This leads to:
- Longer Equipment Life: According to the U.S. Department of Energy, well-maintained HVAC systems, which includes keeping air ducts clean, can last 30% to 50% longer than neglected systems. This defers the significant capital expenditure associated with premature equipment replacement.
- Fewer Breakdowns and Repairs: Reduced wear and tear mean fewer unexpected breakdowns and costly emergency repairs. NADCA estimates that facilities can save up to 25% on annual HVAC maintenance costs by keeping their air ducts clean. Maximizing the operational lifespan of expensive HVAC equipment and minimizing ongoing repair and maintenance costs contribute significantly to long-term financial savings and operational reliability.
The collective impact of these benefits – improved health and safety, enhanced operational performance, and favorable financial outcomes – presents a holistic value proposition for professional industrial HVAC cleaning. It is an investment that pays dividends across multiple critical areas of facility management.
Furthermore, the increasing availability of robust studies and quantifiable data, such as the NADCA energy study and EPA findings , empowers facility managers to make informed, data-driven decisions about HVAC hygiene. This shift from anecdotal evidence to demonstrable ROI allows cleaning professionals to clearly articulate the true value of their services, positioning comprehensive HVAC cleaning as a strategic and prudent business practice.
6. Why Professional HVAC Cleaning is Essential for Industrial Facilities: The DIY vs. Pro Dilemma
When considering the cleaning of industrial HVAC systems, the question of whether to undertake the task in-house (DIY) or to engage professional services inevitably arises. Given the complexity, scale, and potential hazards associated with these systems, the choice carries significant implications for safety, effectiveness, and long-term operational integrity.
The Limitations and Dangers of DIY Attempts in Industrial Settings:
Attempting to clean large-scale industrial HVAC systems using in-house maintenance staff or non-specialized personnel is fraught with limitations and considerable dangers:
- Lack of Specialized Knowledge: Industrial HVAC systems are intricate, often incorporating unique components and controls. Personnel without specific training in HVAC system design, airflow dynamics, contaminant properties (including combustibility, toxicity, and microbial characteristics), and appropriate cleaning methodologies are ill-equipped to perform the task safely and effectively.
- Inadequate Tools and Equipment: Standard maintenance tools or residential-grade cleaning equipment are wholly insufficient for the demands of industrial HVAC cleaning. They cannot achieve the necessary level of agitation within large ductwork, generate the powerful negative pressure required for contaminant capture, or provide the HEPA-level filtration essential for protecting indoor air quality during the cleaning process. Specialized equipment like explosion-proof vacuums for combustible dust environments is typically unavailable to DIYers.
- Risk of System Damage: The use of improper tools or aggressive, uninformed cleaning techniques can easily damage sensitive HVAC components. This includes tearing duct lining, bending delicate coil fins, damaging fan blades, or harming control systems. Such damage can lead to inefficient operation, costly repairs, and may even void equipment warranties.
- Incomplete Cleaning and Worsening Contamination: DIY efforts often only address the most easily accessible parts of the HVAC system, leaving significant portions heavily contaminated. More alarmingly, improper techniques can dislodge dust and debris without effective capture, potentially pushing contaminants further into the system or, worse, releasing them in large quantities into the facility’s occupied spaces, thereby exacerbating IAQ problems.
- Significant Safety Hazards: This is perhaps the most critical concern. Industrial HVAC cleaning can expose workers to numerous safety risks if not managed professionally:
- Exposure to Hazardous Materials: Without proper assessment and PPE, workers can be exposed to harmful dusts (e.g., silica, metals), chemical residues, and biological contaminants like mold spores, leading to acute or chronic health problems.
- Electrical and Mechanical Hazards: HVAC systems involve high-voltage electricity, moving parts (fans, motors), and potentially gas lines or refrigerants. Mishandling these can lead to electrical shock, entanglement, gas leaks, or exposure to hazardous substances.
- Combustible Dust Ignition: Attempting to clean areas with combustible dust using non-approved equipment (e.g., standard vacuum cleaners) or without proper grounding and bonding can create sparks, leading to a devastating dust explosion.
- Other Physical Hazards: Risks include falls from height when accessing rooftop units or elevated ductwork, and hazards associated with working in confined spaces within AHUs or large ducts. The scale of industrial systems and the nature of the contaminants involved mean that DIY attempts are not only likely to be ineffective but can also be extremely dangerous, potentially leading to serious injuries, property damage, and significant operational disruptions.
The Value of Expertise: Certified Professionals and Adherence to Standards (NADCA, OSHA, NFPA):
In stark contrast to the limitations of DIY, engaging qualified professional HVAC cleaning services offers numerous advantages rooted in expertise, proper equipment, and adherence to established industry standards:
- Specialized Training and Certification: Professional cleaning technicians, particularly those certified by NADCA as Air Systems Cleaning Specialists (ASCS) or Certified Ventilation Inspectors (CVI), possess in-depth knowledge of HVAC system design and operation, appropriate cleaning techniques for various contaminants and system components, and a thorough understanding of relevant health and safety standards. NADCA actively encourages consumers to seek out such certified professionals.
- Appropriate Industrial-Grade Equipment: Professionals utilize a comprehensive arsenal of specialized tools and equipment designed for industrial applications. This includes powerful vacuum collection units (with HEPA filtration and explosion-proof capabilities where necessary), various agitation tools (mechanical brushes, air whips, high-pressure air nozzles), advanced inspection cameras, and a full range of safety gear.
- Adherence to Industry Best Practices and Standards: Reputable professionals conduct their work in accordance with established industry standards, primarily ACR, The NADCA Standard for Assessment, Cleaning & Restoration of HVAC Systems. This ensures a systematic, effective, and verifiable cleaning process.
- Comprehensive Safety Compliance: Professional firms are well-versed in and adhere to OSHA safety regulations (e.g., Lock-Out/Tag-Out, confined space entry, PPE requirements, hazard communication) and relevant NFPA standards for fire safety, especially concerning combustible dust hazards. This commitment to safety protects their workers, facility personnel, and the client’s property.
- Thoroughness and Verification: Professionals are committed to cleaning the entire HVAC system as defined by the scope of work, not just the easily accessible parts. They also provide verification of cleanliness, often through visual inspection against NADCA criteria or quantitative testing if required, offering documented proof of a job well done.
- Efficiency and Minimized Disruption: Experienced crews can typically complete complex industrial cleaning projects more efficiently and with less disruption to the facility’s ongoing operations compared to in-house attempts.
- Liability and Insurance: Professional HVAC cleaning companies carry appropriate liability insurance and workers’ compensation coverage, which protects the facility from financial responsibility in the event of accidental damage or injury during the cleaning process.
The following table provides a clear comparison between DIY approaches and professional services for industrial HVAC cleaning:
Table 3: Comparison: DIY vs. Professional Industrial HVAC Cleaning
Aspect | DIY Approach | Professional Service |
---|---|---|
Expertise/Training | Typically Low/None | Certified/Highly Trained (e.g., NADCA ASCS/CVI) |
Equipment | Basic/Inadequate for Industrial Scale | Specialized Industrial-Grade (HEPA Vacs, Agitation Tools, Explosion-Proof if needed) |
Safety Protocols | Minimal/Often Overlooked | Comprehensive & Mandatory (OSHA, NFPA compliant) |
Adherence to Standards | Non-existent | Standard Practice (NADCA ACR, etc.) |
Thoroughness/Effectiveness | Low/Superficial, Often Incomplete | High/System-Wide, Source Removal Focus |
Risk of System Damage | High (due to improper methods/tools) | Low (with proper techniques by trained personnel) |
Handling of Hazardous Materials | High Risk of Exposure/Mishandling | Managed Safely & Compliantly (e.g., combustible dust, chemicals, mold) |
Cost-Effectiveness (Long-Term) | Potentially Higher (due to damage, inefficiency, re-cleaning) | Higher Upfront Cost, but Better ROI (energy savings, longevity, safety) |
Warranty Implications | Potential Voiding of HVAC Equipment Warranties | Helps Maintain Warranty Validity (with documented professional service) |
Liability | Facility Bears All Risk | Contractor Liability/Insurance Coverage |
Cleanliness Verification | None/Subjective | Formal Verification (Visual, NADCA Vacuum Test if needed), Documentation |
Invest in Professional Cleaning for a Safer, More Efficient Industrial Environment.
The evidence strongly indicates that for industrial HVAC systems, the decision between DIY and professional cleaning is not merely a choice between saving a perceived upfront cost and paying for a service. Instead, it is a fundamental decision impacting operational safety, regulatory compliance, system efficacy, and overall risk management.
The inherent complexities of these systems, the specialized nature of industrial contaminants (including highly hazardous materials like combustible dusts or toxic residues), the rigorous industry standards governing their cleaning and maintenance (NADCA, OSHA, NFPA), and the severe potential consequences of improper handling (such as fires, explosions, or significant health impacts) all converge to make professional expertise indispensable.
The existence of robust industry standards like NADCA’s ACR, The Standard for Assessment, Cleaning & Restoration of HVAC Systems , serves to elevate the entire HVAC cleaning industry, especially within the commercial and industrial sectors.
These standards provide a clear benchmark for quality and performance, enabling facility managers to identify truly qualified service providers who have invested in comprehensive training, appropriate certifications (such as ASCS and CVI) , and the specialized equipment necessary to tackle complex industrial projects safely and effectively. This framework ultimately benefits the end-users, who can make more informed decisions and expect a higher caliber of service and verifiable outcomes.
Therefore, for any industrial facility aiming to ensure a safe working environment, maintain regulatory compliance, optimize HVAC system performance and energy efficiency, protect valuable equipment assets, and mitigate serious operational risks, the engagement of qualified, certified, and experienced professional HVAC cleaning services is not just recommended—it is an essential investment.
The long-term benefits in terms of safety, operational continuity, cost savings, and asset protection far outweigh the initial expenditure, making professional cleaning the only prudent and responsible choice for the demanding environment of industrial operations.