I. Industrial Chemical Cleaning
Industrial chemical cleaning is a specialized field dedicated to the maintenance, operational efficiency, and safety of equipment and systems across a multitude of industrial sectors. It represents a cornerstone of modern industrial maintenance, addressing the ubiquitous challenge of contamination that can otherwise impede performance, compromise safety, and shorten the lifespan of critical assets.
A. Defining Industrial Chemical Cleaning
Contact us!
At its core, industrial chemical cleaning is a process that utilizes specifically formulated chemical solutions to remove unwanted contaminants from various industrial components. These contaminants can range from inorganic scales, rust, and corrosion by-products to organic deposits such as oils, greases, and process-specific residues. The chemicals employed are diverse and include acids, alkalis, solvents, and chelating agents, each selected for its efficacy against particular types of foulants and its compatibility with the equipment material.
The scope of industrial chemical cleaning extends far beyond simple surface wiping. It encompasses the comprehensive treatment of internal surfaces of pipelines, vessels, heat exchangers, boilers, tanks, and intricate processing systems. The primary objective is to restore or maintain the operational integrity and efficiency of these systems by eliminating impurities that accumulate during industrial operations. This process is crucial for ensuring that equipment performs according to its design specifications and that production processes run smoothly and without interruption.
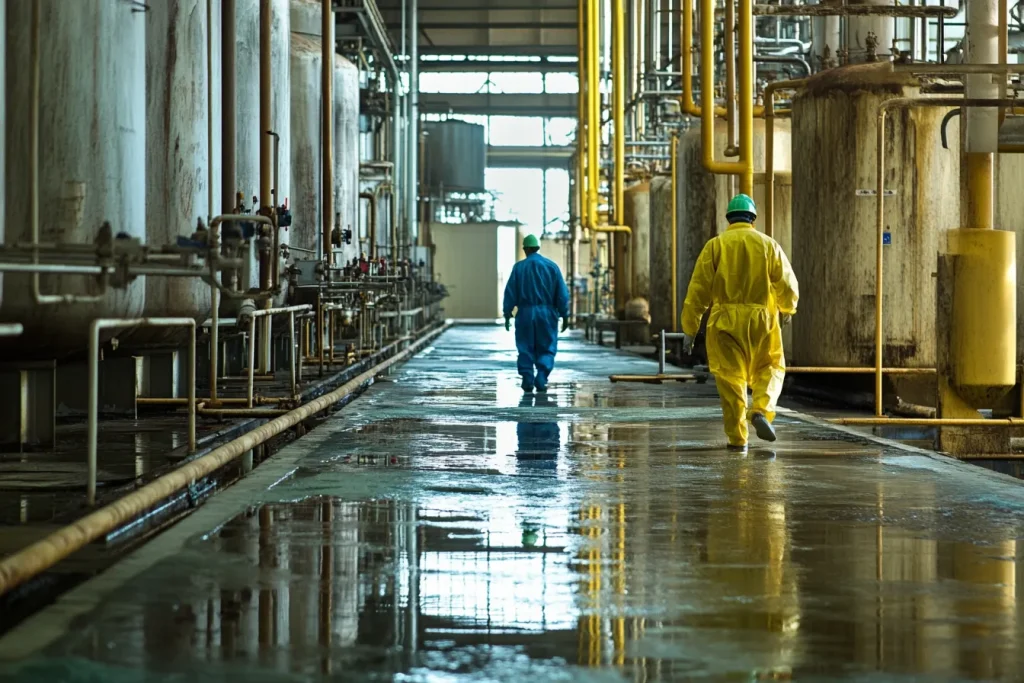
B. The Critical Role of Chemical Cleaning in Modern Industries
The importance of industrial chemical cleaning in contemporary industrial operations cannot be overstated. Its benefits are multifaceted, directly impacting plant efficiency, asset longevity, operational safety, and regulatory compliance.
Firstly, maintaining efficiency and performance is a primary driver.
Over time, industrial systems inevitably accumulate deposits. In pipelines and flow systems, these buildups, such as mineral scale or organic fouling, reduce the internal diameter, thereby restricting flow and increasing the energy required to transport fluids. This leads to decreased system efficiency, higher operational costs, and increased energy consumption. In heat transfer equipment like boilers and heat exchangers, deposits act as an insulating layer, significantly impairing heat transfer rates. This reduction in thermal efficiency means more energy is needed to achieve desired process temperatures, again translating to higher operational expenditures. Chemical cleaning effectively dissolves and removes these deposits, restoring flow capacities and heat transfer coefficients to their original design specifications, thereby optimizing overall efficiency and reducing energy consumption.
Secondly, chemical cleaning is vital for preventing damage and ensuring the longevity of industrial assets.
The accumulation of deposits can lead to severe problems beyond mere inefficiency. Corrosion is a significant threat, as certain deposits can create localized corrosive environments or mask underlying corrosion processes. If left unaddressed, this can lead to leaks, ruptures, or even catastrophic failures of equipment, resulting in costly shutdowns and premature replacement of critical infrastructure. Regular and properly executed chemical cleaning removes these corrosive agents and harmful deposits, mitigating the risk of damage and significantly extending the operational lifespan of the equipment. This proactive approach to maintenance is far more cost-effective than dealing with the consequences of equipment failure.
Thirdly, chemical cleaning plays a crucial role in ensuring safety and compliance.
The removal of hazardous deposits, such as flammable organic materials or residues that could react dangerously, contributes directly to a safer working environment. Moreover, maintaining the structural integrity of pressure vessels, pipelines, and other critical systems through regular cleaning prevents failures that could lead to accidents, injuries, or environmental damage. Many industries are also subject to stringent regulatory standards regarding cleanliness, hygiene, and environmental emissions. Chemical cleaning helps companies meet these compliance obligations by effectively removing contaminants and ensuring that systems operate within permissible limits.
- Manufacturing: General manufacturing facilities utilize chemical cleaning for machinery, tools, conveyor systems, and factory floors to remove dirt, grease, oil, and other contaminants that can impair equipment performance and product quality. For chemical manufacturers, it is even more critical, addressing equipment contamination control between batches, managing hazardous material residues, maintaining stringent cleanroom standards, and removing process byproducts to ensure product purity and process efficiency.
- Food Processing: In the food and beverage industry, chemical cleaning is paramount for maintaining hygiene and sanitation. Equipment, food contact surfaces, and processing lines must be meticulously cleaned and disinfected to prevent microbial contamination, ensure food safety, extend product shelf life, and comply with rigorous health regulations. As noted, without effective chemical cleaning, maintaining high production standards in food manufacturing would be impossible.
- Petrochemical: The petrochemical industry heavily relies on chemical cleaning to manage the severe fouling, scaling, and corrosion issues common in its process equipment and piping systems. Removal of substances like hydrocarbon deposits, iron sulfides, and mineral scales is essential for maintaining flow rates, heat exchanger efficiency, and reactor performance, thereby ensuring operational efficiency, preventing blockages, enhancing safety, and adhering to environmental regulations.
- Power Generation: Power plants, whether thermal, nuclear, or combined-cycle, depend on chemical cleaning to maintain the efficiency and reliability of critical systems. Feedwater systems, Heat Recovery Steam Generators (HRSGs), boilers, condensers, and steam lines are prone to scaling (e.g., calcium carbonate, magnesium silicate) and corrosion product deposition (e.g., iron oxides). These deposits reduce heat transfer efficiency, leading to increased fuel consumption and reduced power output. Unchecked deposits can also cause severe under-deposit corrosion, leading to tube failures and forced outages.
The benefits of chemical cleaning—enhanced efficiency, extended asset life, and improved safety—are not isolated advantages but are deeply interconnected. For instance, the removal of scale from a heat exchanger not only improves thermal efficiency but also reduces the thermal stresses on the equipment components. This, in turn, lessens the likelihood of mechanical failure due to overheating or uneven temperature distribution, contributing to both the longevity of the asset and safer operation.
Similarly, preventing blockages in pipelines through regular cleaning not only maintains flow efficiency but also averts overpressure situations that could lead to ruptures, thus enhancing safety and preventing costly repairs. This synergy means that a comprehensive chemical cleaning program yields benefits that compound across the operational spectrum of an industrial facility.
Furthermore, while chemical cleaning can be employed reactively to address an existing problem, such as a blocked pipeline or a severely fouled heat exchanger, its true strategic value is realized when it is integrated into a proactive maintenance philosophy. Regular, scheduled chemical cleaning, based on an understanding of fouling rates and operational parameters, prevents the severe buildup of deposits.
This preventative approach minimizes the risk of unscheduled shutdowns, reduces the likelihood of extensive damage that might occur if fouling is left unchecked, and often results in lower overall cleaning costs compared to emergency interventions. Adopting such a proactive stance reflects a mature operational strategy focused on long-term reliability, risk mitigation, and optimized lifecycle asset management.
A significant challenge in industrial maintenance is that many of the problems chemical cleaning aims to solve originate in areas hidden from direct view. As highlighted, “the problems that cause the greatest losses often begin where no one can see them. Inside heat exchangers, HRSG boilers, boiler tubes, condensers, and long stretches of pipeline, deposits slowly build up”.
This “unseen” nature of internal fouling means that relying solely on visual inspections or waiting for overt signs of trouble (like pressure drops or efficiency losses) is often too late and can lead to more significant issues.
This underscores the necessity for scheduled cleaning programs, often guided by diagnostic analyses (such as deposit analysis or performance monitoring), and frequently necessitates the specialized expertise and equipment that professional cleaning services provide to assess and treat these hidden threats effectively.
C. Overview of Common Contaminants
To effectively implement chemical cleaning, a thorough understanding of the types of contaminants commonly encountered in industrial settings is essential. The nature of the contaminant dictates the choice of cleaning chemical, the cleaning method, and the overall strategy.
Table 1: Common Industrial Contaminants and Their Characteristics
Contaminant Type | Typical Composition/Examples | Common Formation Mechanisms | Problems Caused in Industrial Systems |
---|---|---|---|
Scale | Mineral build-ups: Calcium carbonate (CaCO3), iron oxides (Fe2O3, Fe3O4), magnesium silicate, sulphide-based compounds. | Precipitation of dissolved minerals from fluids due to changes in temperature, pressure, or pH; exceeding solubility limits. | Reduces flow capacity in pipelines, impairs heat transfer in exchangers/boilers, increases operational costs and energy consumption, can lead to blockages. |
Rust & Corrosion By-products | Iron oxides (e.g., hematite (Fe2O3), magnetite (Fe3O4)), other metal oxides or salts. | Electrochemical reactions between metal surfaces and their environment (e.g., oxygen, moisture, corrosive fluids like H2S, CO2). | Degrades metal integrity, leads to leaks, ruptures, costly shutdowns, structural weakening; various corrosion forms (pitting, crevice) can occur. |
Organic Contaminants/ Deposits | Oils, greases, fats, waxes, hydrocarbon residues, polymers, tars, process-derived organic matter. | Accumulation from process fluids, lubricant leaks, incomplete reactions, or biological activity. | Hinder system performance, reduce heat transfer, can be flammable, cause blockages, interfere with product quality, support microbial growth. |
Particulate Contaminants | Sand, dust, silt, metal fines, catalyst particles, process-generated solids. | Entry from external environment (e.g., desert conditions), wear and tear of equipment, carry-over from process streams. | Cause blockages, abrasion and erosion of surfaces, impede fluid flow, settle in low-flow areas, contaminate products. |
Biofouling (Biological Deposits) | Accumulations of microorganisms (bacteria, fungi, algae) forming biofilms (slime), often trapping silt, corrosion products, and debris. | Adhesion of planktonic microorganisms to surfaces, growth, and production of Extracellular Polymeric Substances (EPS). | Reduces heat transfer efficiency (insulating layer), increases frictional resistance to flow (higher pumping costs), causes blockages, leads to Microbiologically Influenced Corrosion (MIC). |
The types of contaminants detailed above often do not exist in isolation. The presence of one type of deposit can significantly influence the formation, adhesion, or removal difficulty of another. For instance, biofilms, which are biological deposits, can create a sticky matrix that traps particulate matter, silt, or even corrosion products. This composite fouling layer can be much more tenacious and difficult to remove than any single component on its own. Similarly, certain metallic deposits, such as copper plating out from corrosion of upstream components, can mask underlying scales like calcium carbonate or iron oxides.
If this copper layer is not addressed first, subsequent acid cleaning attempts aimed at the underlying scale may be ineffective because the acid cannot reach its target. This phenomenon necessitates a careful diagnostic approach, often involving deposit analysis, to fully understand the composition of the fouling. Consequently, cleaning strategies may need to be multi-staged, for example, incorporating a specialized de-coppering step before the main acid cleaning stage to ensure comprehensive removal of all unwanted materials.
Furthermore, a deep understanding of how these contaminants form is crucial not only for effective cleaning but, more importantly, for developing and implementing preventative measures. Scale formation, for example, is often linked to water chemistry and changes in temperature or pressure. This knowledge allows for interventions such as water softening, pH adjustment, or the use of scale inhibitors to minimize scale deposition in the first place.
Biofouling results from the growth of microorganisms ; therefore, a well-designed biocide treatment program can prevent or significantly reduce its occurrence. Corrosion is an electrochemical process influenced by factors like pH, oxygen levels, and the presence of corrosive species. Thus, corrosion inhibitors, material selection, and control of process conditions can mitigate corrosion. Chemical cleaning, while essential for removing existing deposits, should ideally be part of a broader asset integrity management program that includes these preventative strategies. By addressing the root causes of fouling, the frequency and intensity of chemical cleaning can be reduced, leading to lower maintenance costs, extended equipment life, and more sustainable operations.
II. Core Chemical Cleaning Techniques and Processes
Industrial chemical cleaning encompasses a variety of techniques, each suited to different types of equipment, contaminants, and operational contexts. The selection of the most appropriate technique is critical for achieving desired cleanliness levels efficiently and safely. The primary methods include circulation cleaning, immersion cleaning, and foam cleaning.
Table 3: Comparison of Major Industrial Chemical Cleaning Techniques
Technique | Brief Description | Typical Applications (Equipment/System Types) | Advantages | Limitations/Key Considerations |
---|---|---|---|---|
Circulation Cleaning (CIP/Loop Cleaning) | Chemical solutions are circulated through enclosed systems like pipelines, vessels, and heat exchangers. | Pipelines, heat exchangers, boilers, towers, reactors, food & beverage processing lines, pharmaceutical systems. | Effective for large or complex internal systems not easily disassembled; can be automated (CIP); good for dissolving and flushing deposits. | Requires system to be taken offline; potential for large volumes of chemical and wastewater; effectiveness depends on flow distribution and contact time; may require temporary piping. |
Immersion Cleaning (Soak Cleaning) | Parts or components are submerged in a tank containing a cleaning solution, often with agitation or ultrasonics. | Small to medium-sized removable parts, disassembled machine components, items with complex geometries, batch cleaning. | Thorough cleaning of all surfaces due to full submersion; good for heavy or stubborn deposits requiring long soak times; can incorporate mechanical action (agitation, ultrasonics). | Limited by tank size; requires parts to be removed from service; handling of parts can be labor-intensive; solution bath maintenance is necessary. |
Foam Cleaning | A dense foam carrying cleaning agents is applied to surfaces, adhering for extended contact time. | Large surface areas (internal/external of tanks, walls, floors), food processing equipment, vertical surfaces, areas where liquid runoff is a concern. | Excellent adhesion to vertical/overhead surfaces; prolonged contact time enhances cleaning; reduced chemical consumption; visual confirmation of coverage; lower application pressure. | Requires specialized foaming equipment and foam-compatible chemicals; foam consistency needs control for effectiveness; may not be suitable for heavily occluded internal systems. |
A. Circulation Cleaning: Pipelines and Vessels
Circulation cleaning, often referred to as Clean-In-Place (CIP) when automated, is a widely used method for cleaning the internal surfaces of pipelines, heat exchangers, towers, vessels, and other enclosed or semi-enclosed industrial systems. The fundamental principle involves pumping chemical solutions through the system in a closed or open loop, allowing the chemicals to dissolve, react with, and dislodge contaminants.
The process typically begins with an initial inspection and system isolation. This may involve flushing the system with water, diesel, or Light Cycle Oil (LCO) to remove loose debris and residual process fluids, followed by steam-out to remove oils and degas equipment. The main chemical cleaning stage then commences, where one or more chemical solutions are circulated.
The equipment required includes pumps to provide adequate flow and pressure, hoses, temporary piping to create the circulation loop, and sometimes sophisticated chemical injection systems with dosing pumps and mixers to maintain desired chemical concentrations. Flow rate and velocity are critical parameters, as they ensure sufficient turbulence for effective cleaning and transport of dislodged materials.
Circulation cleaning finds extensive application in industries such as petrochemicals and power generation. For example, in refineries, crude/vacuum units, coking units, fractionating towers, and their associated piping and heat exchanger circuits are routinely cleaned using circulation methods. Similarly, in power plants, feedwater systems, Heat Recovery Steam Generators (HRSGs), boilers, and steam lines are cleaned by circulating appropriate chemical solutions to remove scale and corrosion products. Gas compressor pipelines also benefit from circulation cleaning to remove oil residues, particulates, and rust.
The selection of chemicals is tailored to the specific deposits and system metallurgy. Acidic solutions like hydrochloric acid or citric acid are common for dissolving mineral scales such as calcium carbonate and iron oxides. Alkaline cleaners and detergents/degreasers are used to remove organic deposits like oils and greases. In some cases, oxidizing agents like potassium permanganate are circulated to convert hazardous iron sulfide deposits into more stable iron oxides, reducing the risk of pyrophoric (self-ignition) incidents when equipment is opened to the atmosphere.
The cleaning process can be multi-stage, involving, for example, an alkaline degreasing stage, followed by an acid stage, neutralization, and final rinsing. An advancement in this area is vapor-phase cleaning, where chemical agents are injected with steam. This method can offer advantages such as faster clean-out times, reduced waste generation, and more effective contact with all internal surfaces, especially in complex geometries.
B. Immersion Cleaning: Parts and Components
Immersion cleaning involves the complete submersion of parts or components in a tank or bath filled with a suitable cleaning solution. This technique is particularly effective for items that can be removed from their operational setting and for cleaning parts with complex geometries, blind holes, or where prolonged soaking is necessary to loosen or dissolve tenacious contaminants.
The immersion cleaning process is often multi-stage. A typical sequence includes an initial wash stage, where the bulk of the soil and contaminants are removed through contact with the cleaning solution. This is followed by one or more rinse stages to eliminate any residual cleaning agents and loosened contaminants. Depending on the application and material, additional stages such as rust inhibition, blow-off (using air to remove excess liquid), drying (often with heated air), and cool-down may be incorporated. Multi-stage systems can be configured to combine these steps efficiently, for example, wash/rinse/dry or pre-wash/wash/rinse/rinse/rust inhibit/dry sequences.
Equipment for immersion cleaning ranges from simple soak tanks to sophisticated automated systems. Parts are typically placed in baskets or on fixtures for immersion. To enhance cleaning efficacy, mechanical action is often introduced. This can take the form of agitation, where the parts or the solution are moved (e.g., a pneumatically powered reciprocating platform moving parts up and down in the solution), or through the application of ultrasonic energy.
Ultrasonic cleaners transmit high-frequency sound waves through the cleaning bath, creating cavitation bubbles. The implosion of these bubbles generates an intense scrubbing action at the surface of the parts, effectively dislodging even tightly adhering contaminants from intricate surfaces.
Immersion cleaning is versatile and used for a wide array of applications, including degreasing machined components, removing oils and chips, stripping paint or carbon deposits, cleaning buffing and lapping compounds, preparing surfaces prior to welding, brazing, or coating, precision cleaning of components before assembly or packaging, and general maintenance cleaning of disassembled machine parts like pipes, hoses, clamps, gaskets, and fittings. It is also employed for specialized processes such as passivation and phosphating of metal parts.
A variety of chemical agents can be used in immersion cleaning, including traditional solvents, aqueous detergents (which can be heated to improve performance or used at room temperature), acidic cleaners, and alkaline cleaners. For ferrous parts prone to rusting, rust-inhibiting chemicals can be added to the rinse stage solution to provide temporary corrosion protection.
C. Foam Cleaning: Principles and Applications
Foam cleaning is a technique that has gained popularity, particularly in industries with stringent hygiene requirements, such as food processing and healthcare. The core principle involves generating a thick, dense foam by mixing a chemical cleaning agent (detergent or disinfectant) with water and air, and then applying this foam to the surfaces requiring cleaning. Specialized equipment, known as foamers or foam generators, is used for this purpose.
The primary advantage of foam cleaning lies in the foam’s ability to adhere to surfaces, including vertical and overhead ones, for an extended period. This prolonged contact time allows the active chemical ingredients to penetrate, react with, and lift dirt, grime, and microbial contaminants more effectively than liquid sprays, which tend to run off quickly. This enhanced contact often leads to superior cleaning and sanitizing results with less mechanical scrubbing.
Foam cleaning offers several benefits:
- Enhanced Cleaning Efficiency: The clinging foam effectively loosens and removes soils.
- Reduced Chemical Consumption: Due to better coverage and adhesion, less chemical solution is typically required compared to conventional spraying methods, leading to cost savings and reduced environmental impact.
- Time and Labor Savings: The longer contact time often reduces the need for manual scrubbing, saving time and labor.
- Consistent Coverage: Foam provides a visual confirmation of the areas treated, helping to ensure even application and reduce missed spots.
- Versatility: It can be used on a wide range of surfaces and in various industries, from food processing plants and commercial kitchens to vehicle exteriors and building facades.
- Gentle Application: Foam is generally projected at a lower pressure than high-pressure liquid sprays, making it suitable for cleaning more sensitive surfaces.
Foam can be generated in two main ways:
- Airless Foam: This type of foam is created by drawing atmospheric air into the chemical solution as it passes through a specialized wand. Airless foam is typically “wetter” and is good for allowing the chemical solution to thoroughly penetrate soils. A key advantage is that airless foamers do not require a compressed air supply, simplifying installation and use. The quality of airless foam is largely dependent on the chemical’s inherent foaming ability and its concentration.
- Air-Assisted Foam: This method involves injecting compressed air into the chemical solution, creating a richer, more clinging foam that is often described as “drier” due to its higher aeration. The wetness or dryness of air-assisted foam can usually be adjusted by controlling the air pressure, allowing for optimization based on the chemical used and the cleaning task. However, foam that is too dry may break up into clumps and not clean effectively, while foam that is too wet will not cling well. It is generally best practice to use the minimum amount of air necessary to achieve the desired foam consistency.
The effectiveness of foam cleaning also depends on the chemical formulation. Some cleaning agents are specifically designed for foaming applications. For chemicals that are low-foaming or non-foaming, specialized foaming agents can be added to the solution to enhance its foaming properties at the desired use concentration. Benzalkonium chloride (BZK) is an example of a compound used in sanitizers and disinfectants that can contribute to foam generation and stability.
The selection of a particular chemical cleaning technique—be it circulation, immersion, or foam—is rarely a straightforward decision based solely on the type of equipment to be cleaned. It involves a careful consideration of various trade-offs. For instance, circulation cleaning of a large industrial system might be highly effective for reaching inaccessible internal surfaces but could involve significant volumes of chemicals and generate a correspondingly large amount of wastewater. This has implications for chemical procurement costs, waste disposal expenses, and environmental impact. Immersion cleaning, while thorough for individual parts, requires the logistical effort of disassembly, transport, and handling of components, as well as investment in appropriately sized tanks and potentially energy for heating or ultrasonic generation. Foam cleaning, designed to be efficient in chemical usage, necessitates specialized application equipment and chemicals formulated for optimal foaming. Therefore, a comprehensive cost-benefit analysis, encompassing not just the immediate cleaning effectiveness but also factors like chemical costs, energy consumption, labor requirements, equipment capital and maintenance, downtime, and waste management, is essential for making an informed choice, particularly for large-scale or recurring cleaning operations.
While the chemical agents are central to the cleaning process, the role of mechanical action should not be underestimated. There is often a synergistic relationship between chemical effects (dissolution, reaction) and mechanical forces (flow, agitation, impingement). In circulation cleaning, achieving an appropriate flow rate and turbulence is crucial not only for distributing the chemical solution effectively but also for mechanically dislodging loosened deposits and transporting them out of the system. In immersion cleaning, mechanical agitation or the intense scrubbing action of ultrasonics can dramatically accelerate the cleaning process and improve results, especially for stubborn or layered contaminants. Similarly, the application pressure and nozzle design in foam or spray cleaning contribute to the mechanical removal of soils. Optimizing these mechanical parameters can enhance overall cleaning performance, potentially allowing for the use of milder chemical conditions (lower concentrations, shorter contact times, or less aggressive chemicals), which can lead to cost savings, reduced risk of damage to equipment, and a smaller environmental footprint. Thus, the design of any chemical cleaning protocol should carefully consider and integrate both the chemical and mechanical aspects for maximum efficacy and efficiency.
The mention of vapor-phase chemical cleaning within the context of circulation methods signals an important trend towards more specialized and advanced cleaning technologies. This technique, which involves using chemicals in a gaseous or vapor state, often carried by steam, can offer distinct advantages for certain applications. These may include faster cleaning cycles due to higher temperatures and potentially better penetration into complex geometries, reduced liquid waste volumes, and more uniform contact with all surfaces. While vapor-phase cleaning may require more sophisticated equipment and specialized chemical formulations, its potential benefits in terms of efficiency, waste reduction, and effectiveness highlight the ongoing innovation in the industrial chemical cleaning field. The availability of such advanced techniques suggests that a “one-size-fits-all” approach is increasingly being replaced by tailored solutions designed to meet specific challenges and optimize outcomes, encouraging facilities to stay informed about these developments to enhance their maintenance strategies.
III. Selecting Appropriate Chemicals: A Strategic Approach
The success of any industrial chemical cleaning operation hinges critically on the selection of the appropriate chemical cleaning agents. This choice is not arbitrary but a strategic decision based on a thorough understanding of the contaminants, the materials of construction of the equipment, process conditions, and safety and environmental considerations. An incorrect chemical choice can lead to ineffective cleaning, damage to equipment, safety hazards, or environmental non-compliance.
Table 2: Overview of Key Chemical Cleaning Agents
Chemical Category | Specific Examples | Primary Target Contaminants | Mode of Action | Key Considerations (Material Compatibility, Safety, Environmental) |
---|---|---|---|---|
Acids | Hydrochloric acid (HCl), Citric acid (C6H8O7), Phosphoric acid (H3PO4), Sulfamic acid (H3NSO3) | Mineral scales (e.g., calcium carbonate, iron oxides), rust, water hardness deposits, some metal oxides. | Dissolve inorganic deposits by chemical reaction, often releasing gases (e.g., CO2 from carbonates). Lower pH. | Highly corrosive to many metals; requires careful material compatibility assessment (e.g., HCl aggressive to stainless steel if not inhibited); use of corrosion inhibitors often necessary; significant safety (burns, fumes) and PPE requirements; neutralization of spent acid is crucial. |
Alkalis (Bases) | Sodium hydroxide (NaOH, caustic soda), Potassium hydroxide (KOH, caustic potash), Sodium carbonate (Na2CO3, soda ash), Sodium metasilicate. | Organic contaminants (oils, fats, greases, waxes, proteins), some biological films, heavy-duty soils, acidic residues. | Saponify fats (convert to soluble soaps), hydrolyze proteins, emulsify oils, dissolve certain organic and inorganic materials. Raise pH. | Can be corrosive to some metals (e.g., aluminum, zinc); high concentrations can be hazardous to skin and eyes; good for many surfaces including metals, ceramics, plastics; often biodegradable. Neutralization of spent alkali may be needed. |
Solvents & Degreasers | Petroleum distillates (e.g., mineral spirits), chlorinated solvents (less common due to EHS concerns), terpenes, glycol ethers (e.g., 2-Butoxyethanol), alcohols. | Oils, greases, tars, adhesives, resins, paint overspray, inks, waxes, other organic residues not easily removed by aqueous cleaners. | Dissolve organic contaminants without necessarily reacting chemically; some emulsify soils for rinsing. | Flammability varies; toxicity and VOC emissions are major concerns for many solvents; require good ventilation and appropriate PPE; compatibility with plastics and elastomers must be checked; some designed to evaporate without residue. |
Chelants (Sequestering Agents) | EDTA (Ethylenediaminetetraacetic acid), GLDA (L-glutamic acid N,N-diacetic acid), NTA (Nitrilotriacetic acid), Citric acid (also acts as an acid), Phosphonates. | Metallic scales (including some acid-insoluble ones like barium sulfate, calcium oxalate), metal ions in solution (iron control), hard water ions. | Form stable, water-soluble complexes (chelates) with polyvalent metal ions, effectively “sequestering” them and preventing precipitation or facilitating their removal. | Generally less corrosive than strong acids; effective at various pH ranges (some specific to alkaline or acidic pH); biodegradability varies (EDTA is poorly biodegradable); can mobilize heavy metals in waste streams; high stability of chelates can have environmental implications. |
Surfactants (Detergents, Wetting Agents) | Anionic, non-ionic, cationic, amphoteric surfactants. Often components of formulated cleaners rather than standalone agents. | General dirt, particulate soils, assist in removal of oily/greasy films by other active ingredients. | Reduce surface tension of water, allowing better wetting of surfaces and penetration into soils; emulsify oils, disperse particles, suspend soils to prevent redeposition. | Generally low toxicity but some can cause foaming in wastewater; biodegradability varies; effectiveness can be reduced by water hardness (chelants can help). |
Oxidizing Agents | Potassium permanganate (KMnO4), Hydrogen peroxide (H2O2), Sodium hypochlorite (bleach) | Iron sulfides (pyrophoric risk reduction), organic matter, biofilms, dyes, odor-causing compounds. | Chemically alter contaminants by oxidation, breaking them down into simpler, more soluble, or less hazardous substances. Used for disinfection. | Strong oxidizers can be highly reactive and corrosive; require careful handling and material compatibility checks; can generate hazardous byproducts; specific safety precautions needed. |
Reducing Agents | Sodium bisulfite, Sodium hydrosulfite | Oxygen scavenging, some metal oxide removal (e.g., rust under specific conditions), chlorine removal. | Chemically alter contaminants by reduction. | Handling precautions vary; can release sulfur dioxide. |
A. Understanding Chemical Cleaning Agents
A diverse array of chemical agents is employed in industrial cleaning, each with specific properties and applications.
- 1. Acids (e.g., Hydrochloric, Citric, Phosphoric):
Acidic cleaners are primarily used for dissolving inorganic deposits such as mineral scales (e.g., calcium carbonate, calcium sulfate), rust (iron oxides), and other metal oxides. Common examples include hydrochloric acid (HCl), citric acid (C6H8O7), phosphoric acid (H3PO4), and sulfamic acid. Their mode of action involves a chemical reaction with the deposit, typically converting it into a soluble salt that can be flushed away. For instance, hydrochloric acid reacts with calcium carbonate to form calcium chloride, water, and carbon dioxide gas. The corrosivity of acids is a major consideration; they can aggressively attack many metals. Therefore, careful selection based on substrate material is crucial. For example, metals above hydrogen in the electrochemical series will generally corrode in acid, while more noble metals like copper and its alloys tend to be stable in common mineral acids. Corrosion inhibitors are often incorporated into acidic cleaning formulations to protect the base metal of the equipment during the cleaning process. - 2. Alkalis (e.g., Sodium Hydroxide, Potassium Hydroxide, Sodium Carbonate):
Alkaline cleaners are effective for removing organic contaminants such as oils, fats, greases, waxes, and proteinaceous soils, as well as some heavy-duty inorganic soils. Common alkaline substances include sodium hydroxide (NaOH, or caustic soda), potassium hydroxide (KOH), and sodium carbonate (Na2CO3, or soda ash). Their cleaning action often involves saponification (the chemical conversion of fats and oils into soluble soaps) and hydrolysis (the breakdown of proteins). Alkalis can also neutralize acidic residues and help dissolve certain mineral-based deposits. They are generally versatile and can be used on a variety of surfaces, including many metals, ceramics, plastics, and glass. While some strong alkalis can be corrosive, particularly to amphoteric metals like aluminum and zinc, many alkaline cleaners are formulated to be biodegradable.11 - 3. Solvents and Degreasers:
This category includes a broad range of chemicals designed to dissolve or emulsify organic soils. Degreasers specifically target oils and greases, typically working by breaking down these hydrophobic compounds and emulsifying them so they can be rinsed away with water. Solvents are used to dissolve contaminants that are not readily water-soluble or are resistant to aqueous cleaners, such as stubborn or dried-on adhesives, resins, tars, and paint overspray. Examples include petroleum distillates, terpenes, glycol ethers, and alcohols. Some solvents are designed to evaporate quickly without leaving a residue, which is advantageous in certain applications. However, many organic solvents pose health and environmental risks, including flammability, toxicity, and the emission of Volatile Organic Compounds (VOCs). Therefore, their use requires careful attention to safety precautions, including proper ventilation and Personal Protective Equipment (PPE).11 - 4. Chelants (e.g., EDTA, GLDA, NTA):
Chelating agents, also known as sequestrants, are compounds that can form stable, water-soluble complexes with polyvalent metal ions. This action, called chelation, effectively “captures” or “sequesters” the metal ions, preventing them from precipitating or reacting undesirably, and facilitating their removal. Chelants are particularly effective for removing metallic scales, including those that are difficult to dissolve with acids, such as barium sulfate (BaSO4) and calcium oxalate. They are also used for iron control in various industrial processes (e.g., to prevent iron precipitation in oil and gas stimulation treatments) and to remove hard water ions that can interfere with cleaning processes. Common chelating agents include ethylenediaminetetraacetic acid (EDTA), L-glutamic acid N,N-diacetic acid (GLDA), nitrilotriacetic acid (NTA), and citric acid (which also functions as an acid). The strength of the bond between the chelating agent and the metal ion, known as the stability constant, is a key factor in their effectiveness. While chelants are often less corrosive than strong acids and can be effective at high temperatures, some, like EDTA, have poor biodegradability and can raise environmental concerns due to their persistence and potential to mobilize heavy metals in ecosystems.20 - 5. Surfactants (Detergents):
Surfactants (surface-active agents) are essential components in many cleaning formulations. Their primary function is to lower the surface tension of the cleaning solution (usually water-based), allowing it to wet surfaces more effectively, penetrate into soils, and lift contaminants away. Surfactants have molecules with both a hydrophilic (water-loving) part and a lipophilic (oil-loving) part. This structure enables them to emulsify oils and greases (disperse them as fine droplets in water), suspend particulate soils, and prevent redeposition of loosened contaminants. While surfactants are not typically the primary dissolving agent for heavy scale or corrosion, they play a crucial role in enhancing the overall performance of acidic, alkaline, and neutral cleaners. The effectiveness of some surfactants can be diminished by hard water ions (calcium and magnesium); in such cases, sequestering agents (chelants) are often included in the formulation to bind these ions and maintain surfactant performance.19
B. Factors Influencing Chemical Selection
The selection of an appropriate chemical cleaning agent or formulation is a multi-factorial decision process. Key considerations include:
- 1. Nature of Contaminant: This is the foremost factor. The chemical properties of the deposit—whether it is organic (oil, grease, biofilm), inorganic (scale, rust), or a complex mixture—will determine which type of chemical agent will be most effective. For instance, acidic cleaners are chosen for mineral scales, while alkaline cleaners are preferred for organic fouling. A thorough identification of the deposit, sometimes involving laboratory analysis, is often the first step in designing a cleaning protocol.
- 2. Substrate Material Compatibility: The chosen chemical must be compatible with all materials of construction it will contact within the system being cleaned. Aggressive chemicals can cause corrosion, etching, discoloration, or degradation of metals, plastics, elastomers (seals, gaskets), and other materials. For example, acidic cleaners should only be used on surfaces known to be resistant to acid attack, or with appropriate corrosion inhibitors, to prevent damage. Assessing the material composition of the equipment is a critical prerequisite.
- 3. Process Parameters:
- Temperature: The temperature of the cleaning solution significantly influences cleaning effectiveness. Generally, increasing the temperature accelerates chemical reaction rates, increases the solubility of deposits, and reduces the viscosity of the cleaning solution, all of which can enhance cleaning. However, excessively high temperatures can also increase corrosion rates for certain chemical-substrate combinations or degrade the cleaning chemicals themselves. For example, some sanitizers become more corrosive above 55°C (131°F). There is usually an optimal temperature range for each cleaning application.
- Contact Time: The duration for which the cleaning chemical is in contact with the contaminant is another critical parameter. Longer contact times generally lead to more thorough cleaning, but this must be balanced against potential damage to the substrate, process downtime, and overall efficiency. Techniques like foam cleaning are specifically designed to maximize contact time on vertical or complex surfaces.
- Concentration: The concentration of the active chemical in the cleaning solution also affects performance. While higher concentrations can increase cleaning activity, there is often a point of diminishing returns, beyond which further increases in concentration provide little additional benefit and may significantly increase corrosivity, safety risks, cost, and waste disposal challenges. Manufacturer recommendations should be followed, and it’s noted that adjusting concentration is often the least effective way to improve cleaning compared to optimizing temperature, time, and mechanical action (turbulence).
- 4. Safety and Environmental Impact: The safety of personnel and the protection of the environment are paramount. The selected chemicals should be evaluated for their toxicity, flammability, reactivity, and the nature of any by-products generated during cleaning or neutralization. The biodegradability of the chemicals and their potential to cause harm if released into the environment are increasingly important considerations. There is a growing emphasis on the development and use of sustainable and ecologically friendly cleaning solutions.
- 5. pH of the Cleaning Solution: The pH of the cleaning solution is a critical property that dictates the activity of many cleaning agents and affects material compatibility. For instance, the effectiveness of chlorine-based sanitizers can be dramatically reduced at pH values above 7.5. The pH must be controlled within the optimal range for the specific chemical and application.
- 6. Water Properties: The quality of the water used to prepare cleaning solutions can also influence performance. Impurities in the water, such as dissolved minerals (hardness ions like calcium and magnesium), can react with some cleaning agents (e.g., reducing surfactant effectiveness) or contribute to new deposit formation. Water treatment or the inclusion of chelating agents in the formulation may be necessary to counteract these effects.
Effective chemical selection often transcends the choice of a single active ingredient. In many industrial scenarios, particularly for complex fouling or sensitive equipment, the optimal approach involves formulating a “solution system.” This system comprises multiple components working synergistically: a primary cleaning agent (acid, alkali, or solvent) to attack the bulk contaminant; surfactants to enhance wetting, penetration, and soil suspension ; chelating agents to manage metal ions and water hardness ; corrosion inhibitors to protect the underlying substrate material, especially when using aggressive chemicals like acids ; and potentially pH buffers to maintain the solution within its optimal working range. The precise balance and interaction between these components are crucial for achieving effective cleaning without causing undue damage or excessive waste. This level of formulation complexity often necessitates specialized chemical knowledge and experience, underscoring the value that professional cleaning services or expert chemical consultants bring to the process. A simplistic approach of merely selecting “an acid” or “an alkali” may prove inefficient, damaging, or more costly in the long run.
Furthermore, the interaction between the cleaning chemical and the contaminant is not static; it is a dynamic process that evolves over the course of the cleaning operation. As an acid dissolves scale, for example, the acid is consumed, and its concentration decreases, while the pH of the solution rises. Soluble by-products are formed, and their concentration in the solution increases. If the solubility limit of these by-products is exceeded, they could precipitate out, potentially forming new deposits or interfering with the cleaning process. This dynamic nature means that a “set and forget” approach is often inadequate, especially for large-scale or prolonged cleaning tasks. Effective chemical cleaning may require in-process monitoring of key parameters such as chemical concentration, pH, temperature, and the level of dissolved solids. Based on this monitoring, adjustments to the cleaning solution (e.g., addition of more chemical, pH adjustment) or process parameters may be necessary to maintain optimal cleaning conditions and ensure the desired outcome.
When evaluating chemical cleaning options, it is also important to adopt a holistic cost perspective. While the direct cost of the cleaning chemicals and the process itself are evident, these must be weighed against the often much higher “cost of not cleaning” or the “cost of improper cleaning.” These indirect costs can include lost production due to reduced efficiency or unplanned shutdowns, accelerated equipment degradation leading to premature replacement, compromised product quality, and the potential for safety incidents or environmental non-compliance. Therefore, the decision-making process for chemical selection should not be driven solely by the pursuit of the cheapest available chemical. A value-based assessment, considering the total impact on operational reliability, asset integrity, safety, and environmental responsibility, is essential. This often justifies investment in more sophisticated, targeted, and sometimes initially more expensive chemical solutions and processes that deliver superior long-term results and minimize overall lifecycle costs.
IV. Post-Cleaning Procedures: Neutralization and Waste Management
Once the chemical cleaning process has effectively removed the target contaminants, the subsequent procedures of neutralization and waste management become critically important. These steps are essential for ensuring the safety of personnel, protecting the environment, and complying with regulatory requirements. The user query specifically highlighted the need for information on these post-cleaning activities.
A. Neutralization of Cleaning Solutions
Neutralization is the process of adjusting the pH of spent acidic or alkaline cleaning solutions to a more neutral level, typically around pH 7, before they are discharged or sent for further treatment. This is a crucial step because unneutralized acidic or alkaline wastes are corrosive and can be harmful to personnel, equipment (including wastewater treatment systems), and the environment.
The fundamental principle involves adding a basic substance to a spent acidic solution or an acidic substance to a spent alkaline solution. This chemical reaction generally produces a salt and water, rendering the solution less hazardous.
- Neutralizing Acids:
Commonly used neutralizing agents for acidic solutions include:- Sodium bicarbonate (baking soda): Often used for smaller volumes or in situations requiring a milder reaction.
- Sodium carbonate (soda ash): Another effective option.
- Calcium hydroxide (lime or slaked lime): A cost-effective alkali for larger volumes.
- Magnesium oxide or magnesium hydroxide: Also used for acid neutralization.
- Ammonia solution: Produces ammonium salts upon reaction. The choice of agent can depend on factors like the type and concentration of the acid, the volume of waste, cost, and the nature of the resulting salt (its solubility and environmental impact).
- Neutralizing Alkalis:
For spent alkaline cleaning solutions, mild acidic agents are typically used for neutralization. Examples include:- Phosphoric acid: Commonly used in automated alkaline neutralization systems.
- Citric acid: A weaker organic acid that can be effective.
- Acetic acid (vinegar): Suitable for small-scale or less industrial applications, and can be effective for neutralizing residues of alkaline degreasers.
- Procedure and pH Monitoring:
A systematic and cautious approach is essential during neutralization:- Personal Protective Equipment (PPE): Appropriate PPE, including acid/alkali resistant gloves, aprons, eye protection (goggles and face shield), and respiratory protection if fumes are expected, must be worn.
- Dilution (if applicable): For highly concentrated solutions, initial dilution with water (if safe and appropriate for the specific chemical) can help to moderate the neutralization reaction and make it safer to handle.
- Slow Addition and Agitation: The neutralizing agent should be added slowly and in small increments to the spent cleaning solution, preferably with continuous stirring or agitation. This helps to control the reaction rate, dissipate any heat generated (neutralization reactions are often exothermic), and prevent localized over-reactions or excessive foaming/gas evolution.
- pH Monitoring: The pH of the solution must be monitored regularly throughout the process using pH indicator strips (litmus paper) or a calibrated pH meter. The goal is typically to bring the pH into a neutral range, often specified by local discharge regulations (e.g., pH 6-9 is a common target range).
- Observation of Reaction: The reaction between the acid and base often produces gases, such as carbon dioxide if carbonates are used to neutralize acids. The cessation of bubbling can be an indicator that the reaction is nearing completion, but pH measurement is the definitive check.
- Safety Check: Once neutralization appears complete and the pH is within the target range, a final safety check should be performed. This includes confirming the pH and ensuring the mixture has cooled if the reaction was significantly exothermic.
Table 4: Common Neutralizing Agents for Spent Cleaning Solutions
Type of Spent Solution (Example Cleaning Chemical) | Common Neutralizing Agent(s) | Typical Reaction Products (Simplified) | Important Safety/Handling Notes |
---|---|---|---|
Acidic (e.g., Hydrochloric Acid – HCl, Sulfuric Acid – H2SO4) | Sodium Hydroxide (NaOH) | Sodium Chloride (NaCl) + Water (H2O); Sodium Sulfate (Na2SO4) + Water (H2O) | Highly exothermic reaction; add NaOH slowly with stirring; monitor temperature. |
Sodium Carbonate (Na2CO3) / Sodium Bicarbonate (NaHCO3) | Sodium Chloride (NaCl) + Water (H2O) + Carbon Dioxide (CO2); Sodium Sulfate (Na2SO4) + Water (H2O) + Carbon Dioxide (CO2) | Foaming/gas evolution (CO2); add slowly to prevent overflow; ensure adequate ventilation. | |
Calcium Hydroxide (Ca(OH)2 – Lime) | Calcium Chloride (CaCl2) + Water (H2O); Calcium Sulfate (CaSO4 – Gypsum) + Water (H2O) | Lime is a powder, can create dust; CaSO4 has low solubility, may precipitate. | |
Alkaline (e.g., Sodium Hydroxide – NaOH) | Hydrochloric Acid (HCl) | Sodium Chloride (NaCl) + Water (H2O) | Exothermic reaction; add acid slowly to alkali with stirring. |
Sulfuric Acid (H2SO4) | Sodium Sulfate (Na2SO4) + Water (H2O) | Highly exothermic; add acid slowly to alkali with stirring. | |
Phosphoric Acid (H3PO4) | Sodium Phosphates + Water (H2O) | Generally less vigorous reaction than strong mineral acids. | |
Acetic Acid (CH3COOH – Vinegar) | Sodium Acetate (CH3COONa) + Water (H2O) | Milder reaction; good for less concentrated alkalis or residues. |
B. Disposal of Cleaning Solutions and Waste
The disposal of spent cleaning solutions, neutralized or otherwise, and any solid waste generated (e.g., removed scale, sludge, contaminated PPE) is subject to stringent environmental regulations and requires careful management.
- Regulatory Framework:
In the United States, the primary federal law governing hazardous waste is the Resource Conservation and Recovery Act (RCRA), administered by the Environmental Protection Agency (EPA). RCRA establishes a “cradle-to-grave” system for managing hazardous waste, from its generation through transportation, treatment, storage, and disposal. Worker safety during these operations is covered by the Occupational Safety and Health Administration (OSHA) standards, particularly the Hazardous Waste Operations and Emergency Response (HAZWOPER) standard (29 CFR 1910.120) and the Hazard Communication Standard (HCS) (29 CFR 1910.1200). Many states have their own hazardous waste regulations that may be stricter than federal requirements. - Hazardous Waste Identification:
The first critical step is to determine whether the waste generated from the chemical cleaning process qualifies as hazardous waste under RCRA criteria. These criteria include characteristics such as ignitability, corrosivity (e.g., pH ≤ 2 or ≥ 12.5), reactivity, and toxicity (determined by the Toxicity Characteristic Leaching Procedure – TCLP). The Safety Data Sheets (SDS) for the original cleaning chemicals provide vital information on their hazards, which helps in this determination. The nature of the contaminants removed can also render the waste hazardous (e.g., if heavy metals are leached into the solution). - Labeling, Storage, and Transportation:
If waste is identified as hazardous, specific RCRA requirements for labeling, storage, and transportation apply:- Labeling: Containers must be clearly and durably labeled with the words “Hazardous Waste,” a description of the contents, the relevant EPA waste codes, and hazard warnings (e.g., “Corrosive,” “Toxic”). Specific labels like “NITRIC ACID WASTE ONLY – NO ORGANICS” may be required for certain waste streams.
- Storage: Hazardous waste must be stored in containers that are suitable for the type of waste (e.g., corrosion-resistant for acidic or alkaline wastes), kept closed except when adding or removing waste, and maintained in good condition to prevent leaks. Storage areas should be secure, well-ventilated, and equipped with secondary containment systems to catch spills or leaks. Different types of hazardous wastes should be kept separate if they are incompatible and could react dangerously if mixed.
- Transportation: The transportation of hazardous waste off-site must be done by transporters who are certified or permitted under RCRA. A hazardous waste manifest system is used to track the waste from the generator to its final disposal facility.
- Best Practices for Minimizing Environmental Impact:
Beyond regulatory compliance, several best practices can help minimize the environmental footprint of chemical cleaning waste:- Source Reduction: Select cleaning chemicals and processes that generate the least amount of hazardous waste. Consider using biodegradable or less hazardous cleaning agents where technically feasible.
- Neutralization: As discussed, neutralize corrosive wastes to reduce their hazardous characteristics before disposal.
- Volume Minimization: Optimize cleaning processes to use the minimum effective volume of cleaning chemicals.
- Wastewater Treatment: Ensure that any liquid effluents, including neutralized solutions and rinse waters, are managed appropriately. If discharged to a sanitary sewer, they must meet the local publicly owned treatment works (POTW) pre-treatment requirements. If processed through an on-site industrial wastewater treatment plant (WWTP), it must be done in a controlled manner, staying within the WWTP’s design and operational load capabilities to avoid upsetting the treatment process or causing permit violations.
- Recycling/Recovery: In some specific cases, it may be possible to recover and reuse certain cleaning chemicals or recover valuable materials from the waste stream, although this is often complex and industry-specific.
Table 5: Key Regulatory Standards for Chemical Cleaning Waste
Regulatory Body/Act | Key Provisions | Relevance to Chemical Cleaning Waste |
---|---|---|
EPA / Resource Conservation and Recovery Act (RCRA) | Defines hazardous waste; “cradle-to-grave” management system; requirements for generation, transportation, treatment, storage, and disposal (TSD) of hazardous waste. | Governs identification of cleaning waste as hazardous (corrosivity, toxicity etc.); mandates proper labeling, accumulation time limits, container management, manifesting for off-site shipment, and use of permitted TSD facilities. |
OSHA / Hazardous Waste Operations and Emergency Response (HAZWOPER – 29 CFR 1910.120) | Worker safety requirements for hazardous waste handling, emergency response, and cleanup operations. | Applies to workers involved in cleaning up spills of hazardous cleaning chemicals, handling hazardous cleaning waste, and emergency response to releases. Mandates training, site safety plans, PPE, medical surveillance. |
OSHA / Hazard Communication Standard (HCS – 29 CFR 1910.1200) | Requires employers to inform workers about hazardous chemicals on-site through labels, Safety Data Sheets (SDS), and training. | Ensures workers handling cleaning chemicals and resultant wastes understand their hazards, safe handling procedures, and emergency measures. SDS for cleaning agents are crucial. |
OSHA / Personal Protective Equipment (PPE) Standards (e.g., 29 CFR 1910.132-138) | Mandates hazard assessment and provision of appropriate PPE (gloves, respirators, eye/face protection etc.) to protect workers. | Requires employers to provide and ensure use of correct PPE when workers are handling cleaning chemicals, performing neutralization, or managing waste. |
Clean Water Act (CWA) / National Pollutant Discharge Elimination System (NPDES) | Regulates discharge of pollutants into waters of the United States. Sets effluent limitations for industrial dischargers. | Governs the discharge of spent cleaning solutions and rinse waters to surface waters (requires NPDES permit) or to Publicly Owned Treatment Works (POTWs) (subject to pre-treatment standards). |
The process of neutralization serves as more than just a pH adjustment step prior to disposal. It is, in itself, a critical safety procedure that demands careful execution to manage potential hazards like exothermic reactions and gas evolution, as highlighted by the detailed steps for nitric acid neutralization. Moreover, the outcome of neutralization can significantly alter the hazardous characteristics of the waste. A successfully neutralized corrosive waste might no longer meet the RCRA definition of corrosive hazardous waste (e.g., if its pH is brought within the 2-12.5 range). This change in classification can have substantial implications for subsequent disposal options, potentially allowing for less stringent (and less costly) disposal methods compared to unneutralized corrosive waste. Therefore, neutralization should be viewed as an integral component of a proactive waste management strategy, aiming to reduce hazards at the source and optimize the entire disposal pathway.
The regulatory framework, particularly RCRA, establishes a “cradle-to-grave” responsibility for generators of hazardous waste. This means that a company’s legal responsibility for its hazardous cleaning waste does not cease when the waste is picked up by a disposal contractor. The generator remains liable for ensuring that the waste is ultimately treated and disposed of in an environmentally sound and legally compliant manner. This underscores the critical importance of selecting reputable, certified, and adequately insured hazardous waste management services. Thorough due diligence on potential waste contractors, including review of their permits, compliance history, and disposal facility audits, is essential for mitigating this long-term liability. Comprehensive record-keeping, including manifests and certificates of disposal, is also vital for demonstrating compliance.
Finally, the capacity and capabilities of on-site or off-site wastewater treatment plants (WWTPs) can act as a significant operational constraint on chemical cleaning activities. As noted, chemical cleaning condensates and rinse waters must often be processed through such facilities, and it is imperative that this is done in a controlled manner, respecting the WWTP’s hydraulic and organic/inorganic load limits. Overloading a WWTP or introducing incompatible chemicals can disrupt its biological or chemical treatment processes, leading to permit violations, environmental damage, and costly remediation efforts. This constraint may influence the selection of cleaning chemicals, favoring those that are more readily biodegradable or less problematic for the specific WWTP. It can also affect the scheduling and scale of cleaning operations, sometimes requiring large cleaning campaigns to be phased over time to allow the WWTP to adequately process the resulting effluents. This highlights the need for integrated planning, where chemical cleaning strategies are developed in close coordination with wastewater management personnel and capabilities.
V. Safety and Operational Best Practices in Chemical Cleaning
The use of potent chemicals in industrial cleaning inherently involves risks. Therefore, adherence to stringent safety protocols and operational best practices is not merely advisable but mandatory to protect workers, equipment, and the environment. A systematic approach to safety, incorporating hazard identification, robust control measures, comprehensive training, and emergency preparedness, is fundamental.
A. Hazard Identification and Risk Assessment
The cornerstone of any safe chemical cleaning operation is a thorough hazard identification and risk assessment conducted before work commences. This process involves systematically identifying all potential hazards associated with the chemicals, the equipment being cleaned, the cleaning method, and the work environment. Hazards can be categorized as:
- Physical Hazards: These include slips, trips, and falls (due to wet surfaces or hoses), temperature extremes (from hot solutions or steam), high pressures (in circulation or hydro-jetting systems), electrical hazards (if equipment is not properly isolated), and moving machinery parts.
- Health Hazards: These primarily relate to chemical exposures. Acute effects can include skin or eye burns, respiratory irritation, or systemic poisoning. Chronic effects can result from long-term exposure to certain chemicals, leading to conditions like dermatitis, respiratory sensitization, or organ damage. The generation of dusts, fumes, mists, or vapors during cleaning also poses significant health risks.
Key information sources for hazard identification include:
- Safety Data Sheets (SDS): Provided by chemical manufacturers, SDSs contain detailed information on chemical properties, health and physical hazards, safe handling and storage procedures, PPE recommendations, and emergency measures. Access to and understanding of SDSs for all chemicals used is a requirement under OSHA’s Hazard Communication Standard.
- Occupational Exposure Limits (OELs): These are regulatory or recommended airborne concentrations of substances to which workers can be exposed without adverse health effects. Sources include OSHA’s Permissible Exposure Limits (PELs) (often found in the Z-Tables), NIOSH Recommended Exposure Limits (RELs), and ACGIH® Threshold Limit Values (TLVs®).
Once hazards are identified, the associated risks (the likelihood and severity of harm) must be assessed to prioritize and select appropriate control measures.
B. Hierarchy of Controls
OSHA and other safety authorities advocate for a “hierarchy of controls” to manage workplace hazards. This hierarchy prioritizes control measures from most effective to least effective, with the primary goal being to eliminate or reduce hazards at their source.
- Elimination/Substitution: The most effective approach is to eliminate the hazard altogether or substitute a hazardous chemical or process with a safer alternative. For example, replacing a highly toxic solvent with a less hazardous, water-based cleaner, or redesigning a process to prevent fouling in the first place.
- Engineering Controls: If elimination or substitution is not feasible, engineering controls are implemented to make physical changes to the workplace or equipment to reduce exposure. Examples relevant to chemical cleaning include :
- Isolating or enclosing the cleaning process (e.g., using closed-loop circulation systems).
- Implementing wet methods to reduce the generation of dusts or airborne particulates.
- Providing general dilution ventilation to reduce the concentration of airborne contaminants in the work area.
- Using local exhaust ventilation (LEV), such as fume hoods or snorkel extractors, at the point of chemical mixing or application to capture contaminants at their source.
- Administrative and Work Practice Controls: These involve establishing specific procedures and policies to minimize exposure. Examples include :
- Developing and implementing safe work procedures for chemical handling, mixing, and application.
- Rotating job assignments or adjusting work schedules to limit individual worker exposure times.
- Providing comprehensive worker training on chemical hazards and safe work practices.
- Ensuring good housekeeping to prevent spills and accumulation of residues.
- Personal Protective Equipment (PPE): PPE is considered the last line of defense and is used when engineering and administrative controls are not feasible or do not provide sufficient protection, or while such controls are being implemented.
C. Personal Protective Equipment (PPE)
When a hazard assessment indicates that PPE is necessary, employers are responsible for selecting, providing (often at no cost to the employee), and ensuring the proper use of appropriate PPE. Employees, in turn, are responsible for wearing the PPE correctly, attending training on its use and care, maintaining it properly, and reporting any damage or need for replacement.
Types of PPE commonly required for industrial chemical cleaning include :
- Eye and Face Protection: Safety glasses with side shields, chemical splash goggles, and face shields to protect against chemical splashes, fumes, and flying particles.
- Hand Protection: Chemical-resistant gloves appropriate for the specific chemicals being handled. The SDS for each chemical will often specify suitable glove materials (e.g., nitrile, neoprene, butyl rubber).
- Body Protection: Chemical-resistant aprons, coveralls, or full-body suits to protect skin from contact with hazardous chemicals. NIOSH provides guidance on selecting chemical protective clothing.
- Respiratory Protection: Respirators (e.g., air-purifying respirators with appropriate cartridges/filters, or supplied-air respirators) are required when workers may be exposed to harmful airborne concentrations of chemical vapors, mists, or dusts that cannot be controlled by ventilation alone. A comprehensive respiratory protection program, including medical evaluations, fit testing, and training, is mandated by OSHA (29 CFR 1910.134) when respirators are required.
- Foot Protection: Chemical-resistant boots, possibly with steel toes if impact hazards are present.
- Head Protection: Hard hats may be required if there is a risk of falling objects or head impact.
The specific PPE selected must be based on the hazards identified in the risk assessment for each particular cleaning task. OSHA provides specific standards for various types of PPE (e.g., 29 CFR 1910.133 for eye and face protection, 29 CFR 1910.135 for head protection).
D. Chemical Handling, Storage, and Ventilation
Safe handling and storage of cleaning chemicals are critical to prevent accidents, exposures, and environmental releases.
- Handling: Always follow the procedures outlined in the SDS. Ensure workers are thoroughly trained on the specific hazards of the chemicals they are using and the correct procedures for mixing, transferring, and applying them. Use appropriate tools and equipment (e.g., designated pumps, funnels) to minimize spills and splashes.
- Storage: Chemicals must be stored in containers that are compatible with their contents, properly labeled, and kept closed when not in use. Incompatible chemicals (e.g., strong acids and strong bases, or oxidizers and flammable materials) must be segregated to prevent accidental mixing, which could lead to violent reactions, fires, or toxic gas release. Storage areas should be cool, dry, well-ventilated, secure from unauthorized access, and equipped with spill containment measures (e.g., secondary containment pallets or berms) and appropriate spill response materials.
- Ventilation: Adequate ventilation is a key engineering control for minimizing exposure to airborne chemical contaminants. General dilution ventilation increases the exchange of air in a work area, reducing overall contaminant concentrations. Local exhaust ventilation (LEV), such as fume hoods or extraction arms, is more effective as it captures contaminants at or near their source of generation, preventing them from spreading into the worker’s breathing zone. Proper ventilation is particularly important when working with volatile solvents, strong acids or alkalis that can produce fumes, or during any operation that generates mists or vapors.
E. Emergency Response Procedures
Despite all precautions, accidental spills or exposures can occur. Therefore, robust emergency response procedures must be in place.
- Regulatory Requirements: OSHA’s HAZWOPER standard (29 CFR 1910.120) sets out requirements for emergency response operations involving releases of hazardous substances. This standard covers aspects like emergency response plans, training for responders, PPE for emergency situations, and decontamination procedures.
- Spill Control: Spill response kits containing appropriate absorbents (e.g., vermiculite, sand, specialized absorbent pads), neutralizing agents (if applicable and safe to use), and containment materials (e.g., booms, dikes) should be readily available in areas where chemicals are handled or stored. Workers must be trained on how to safely contain and clean up spills according to established procedures, including proper disposal of contaminated materials.
- First Aid and Decontamination: Immediate access to safety showers and eyewash stations is essential in areas where corrosive or irritating chemicals are used. Workers must be trained on their location and proper use. First aid procedures for chemical exposures (e.g., flushing affected skin or eyes with copious amounts of water for a specified duration, typically at least 15-30 minutes for corrosive materials ) should be clearly understood. Decontamination procedures for personnel and equipment after a spill or exposure are also critical.
- Emergency Communication and Evacuation: Clear procedures for reporting emergencies, alerting personnel, and evacuating the area if necessary must be established and practiced. Contact information for emergency services and on-site emergency responders should be readily accessible.
- Training: All personnel involved in chemical cleaning operations must receive comprehensive training on emergency procedures, including the use of emergency equipment, spill response actions, first aid, and evacuation routes. Regular drills and refresher training help ensure preparedness.
Achieving a high level of safety in chemical cleaning operations is not simply a matter of adhering to a checklist of rules or providing PPE. It requires the development and maintenance of a comprehensive safety system and, more importantly, a pervasive safety culture. This system integrates proactive hazard identification and risk assessment, the diligent application of the hierarchy of controls with a strong emphasis on engineering solutions first, rigorous and ongoing training programs, and well-rehearsed emergency preparedness plans.
Each component of this system supports and reinforces the others. For example, the selection of appropriate PPE is directly informed by the initial hazard assessment and the effectiveness of the engineering and administrative controls already in place. A strong safety culture, fostered by management commitment and active employee participation, transforms safety from a set of imposed rules into a shared value, where all personnel are vigilant in identifying and mitigating risks.
Safety Data Sheets (SDS) play a dynamic and central role throughout the entire lifecycle of a chemical cleaning operation. They are not static documents to be filed away after initial receipt but are active informational tools that should be consulted repeatedly by various personnel.
The information contained within an SDS is critical for: initial chemical selection (considering hazards and compatibility), conducting thorough risk assessments, determining appropriate engineering controls and safe handling procedures, selecting the correct PPE for specific exposure scenarios, planning emergency response measures (including first aid and spill control), and making informed decisions about neutralization and waste disposal. The effective and consistent use of SDS by planners, operators, safety officers, and waste handlers is a cornerstone of chemical safety and regulatory compliance.
While engineering controls and PPE are tangible and visible safety measures, their effectiveness is profoundly influenced by the quality, consistency, and relevance of employee training. Untrained or inadequately trained personnel may not understand the hazards they face, may inadvertently bypass engineered safeguards, or may use PPE incorrectly, rendering it ineffective. Comprehensive training ensures that workers understand not only the “what” and “how” of safety procedures but also the “why” behind them. This understanding fosters a more proactive and responsible approach to safety, transforming passive compliance into active participation in risk mitigation. Training should cover chemical-specific hazards, safe work practices, proper use and limitations of PPE, emergency procedures, and waste handling protocols. It should be viewed as an ongoing investment, with regular refreshers and updates, especially when new chemicals, processes, or regulations are introduced. Competency assessments can also help verify the effectiveness of training programs.
VI. The Advantage of Professional Chemical Cleaning Services
While some industrial facilities may attempt to conduct chemical cleaning operations using in-house staff, engaging specialized professional chemical cleaning services often presents significant advantages in terms of expertise, safety, efficiency, and overall cost-effectiveness. The decision to outsource these critical tasks is frequently a strategic one, allowing companies to focus on their core competencies while ensuring that cleaning is performed to the highest standards.
A. Expertise, Specialized Equipment, and Optimized Chemical Use
Professional chemical cleaning companies bring a depth of knowledge and experience that is typically difficult to replicate with an in-house team whose primary responsibilities lie elsewhere. These specialists have :
- Deep Technical Knowledge: They possess a thorough understanding of various foulants, chemical cleaning agents, material compatibilities, and cleaning methodologies. They are adept at diagnosing complex fouling problems and developing tailored cleaning solutions for diverse types of equipment and industrial systems across different sectors.
- Access to Advanced Technology and Specialized Equipment: Professional services often invest in and maintain a wide range of specialized cleaning equipment that may be too costly or infrequently used for an individual facility to own. This can include high-pressure water jetting units, automated circulation skids, sophisticated foam generators, ultrasonic cleaning tanks, and specialized tools for accessing and cleaning hard-to-reach areas. Access to such equipment can lead to more effective, efficient, and safer cleaning outcomes.
- Optimized Chemical Use and Formulation Skills: With their expertise in chemical properties and interactions, professionals can select the most appropriate chemicals and optimize their concentrations and application methods. This often leads to more effective cleaning with potentially reduced overall chemical consumption, minimized waste generation, and lower risk of damage to equipment. They may also have access to proprietary or advanced chemical formulations not readily available on the general market.
B. Ensuring Safety and Regulatory Compliance
Safety and compliance are paramount in chemical cleaning, and professional services are typically well-equipped to manage these aspects:
- Focus on Safety Protocols: Reputable professional cleaning companies prioritize safety. Their personnel are usually extensively trained in the safe handling of hazardous chemicals, the correct use of appropriate PPE, confined space entry procedures (if applicable), and emergency response protocols. This focus helps minimize the risk of accidents, injuries, and exposures to both their own staff and the client’s personnel and facility.
- Adherence to Regulatory Standards: Professional services are generally well-versed in the complex web of environmental regulations (e.g., EPA’s RCRA for hazardous waste, Clean Water Act for discharges) and worker safety standards (e.g., OSHA’s HAZWOPER, Hazard Communication Standard). They understand the requirements for compliant chemical handling, waste characterization, neutralization, transportation, and disposal, helping the client avoid potentially costly fines, legal issues, and reputational damage associated with non-compliance.
C. Efficiency, Cost-Effectiveness, and Extended Asset Lifespan
While engaging professional services involves an upfront cost, it can often lead to greater overall efficiency and long-term cost savings:
- Time Savings and Reduced Downtime: Outsourcing chemical cleaning tasks allows the client’s own employees and technical staff to remain focused on their core business activities and production responsibilities. Professionals, with their specialized equipment and experienced crews, can often complete cleaning projects more quickly and efficiently, minimizing operational downtime for the cleaned equipment.
- Long-Term Cost Savings and Asset Preservation: Effective and thorough cleaning by professionals can prevent the rapid re-fouling of systems and mitigate the risks of corrosion and other forms of degradation. This helps to extend the operational lifespan of critical assets, deferring the need for expensive repairs or premature replacements. By preventing unexpected failures and ensuring systems operate at optimal efficiency, professional cleaning contributes to avoiding costly unscheduled shutdowns and reducing energy consumption.
- Improved Productivity and Workplace Environment: A clean, well-maintained industrial environment, free from hazardous residues and operating efficiently, can contribute to improved employee morale, health, and productivity. It also presents a more professional image to clients, visitors, and regulatory agencies.
D. Focus on Core Business Operations
Perhaps one of the most significant strategic advantages of using professional chemical cleaning services is that it allows the client company to dedicate its internal resources—personnel, management attention, and capital—to its primary, revenue-generating activities. Chemical cleaning, while critical, is often a non-core function for many industrial enterprises. Outsourcing it to specialists who can perform the task more effectively and safely can be a sound business decision.
Engaging reputable professional chemical cleaning services can also be viewed as a form of risk transfer and liability management. While the ultimate “cradle-to-grave” responsibility for hazardous waste typically remains with the generator, the immediate operational risks associated with the cleaning process itself—such as accidental spills, worker exposure during cleaning, or damage to equipment due to improper chemical application—are largely borne by the professional service provider. Reputable contractors carry appropriate insurance (e.g., general liability, pollution liability) and possess certifications that provide a degree of financial protection and assurance to the client. This transfer of operational risk, contingent upon careful contractor selection and well-defined contractual agreements, can be a significant, albeit sometimes less tangible, benefit.
Furthermore, professional cleaning companies, by virtue of their specialization, are more likely to be at the forefront of technological advancements, new chemical formulations, and evolving regulatory landscapes within the cleaning industry. Cleaning is their core business, incentivizing them to invest in research, development, training, and the adoption of innovative and improved methods, such as more environmentally friendly (“greener”) chemicals or more efficient cleaning techniques like vapor-phase cleaning. Clients who engage such services benefit from this continuous improvement cycle without having to make similar investments themselves. This can lead to access to more effective, safer, and environmentally sound cleaning solutions over time, transforming the relationship from a simple vendor-client transaction to a long-term partnership where the service provider can also act as a knowledgeable consultant.
Finally, when evaluating the option of professional services versus performing chemical cleaning in-house, it is crucial for companies to consider the “true cost” of the in-house alternative. This calculation must extend beyond the direct costs of chemicals and the labor hours of internal staff. Indirect costs, which can be substantial, include: the time and expense of specialized training for personnel in handling hazardous chemicals and waste ; the procurement, maintenance, and certification of PPE ; capital investment and ongoing maintenance for any specialized cleaning equipment; management time for planning, supervision, and ensuring regulatory compliance; increased insurance premiums or potential liabilities associated with handling hazardous materials and waste; and the opportunity cost of diverting skilled technical staff from their primary production or maintenance roles. A comprehensive cost-benefit analysis that accurately accounts for all these direct and indirect costs, as well as the potential risks of less effective or non-compliant in-house cleaning, often reveals that engaging professional services is the more economically sound and strategically prudent option.
VII. Final Thoughts
Industrial chemical cleaning is an indispensable discipline for the modern industrial landscape, playing a pivotal role in maintaining operational efficiency, ensuring the longevity of critical assets, and upholding stringent safety and environmental standards. This guide has delineated the fundamental principles of chemical cleaning, from understanding the diverse nature of contaminants and the chemical agents used to combat them, to the array of techniques employed for their removal.
The selection of an appropriate cleaning strategy is a complex, multi-faceted process. It demands a thorough assessment of the type and extent of contamination, meticulous consideration of the compatibility of cleaning chemicals with equipment materials, and careful optimization of process parameters such as temperature, contact time, and concentration. The synergistic interplay between chemical action and mechanical forces further refines the efficacy of any chosen technique, be it circulation, immersion, or foam cleaning. The advent of advanced methods like vapor-phase cleaning underscores the continuous innovation within this field, offering pathways to enhanced efficiency and reduced environmental impact.
Post-cleaning procedures, particularly the neutralization of spent solutions and the compliant management of all generated waste, are as critical as the cleaning process itself. Adherence to a robust regulatory framework, including RCRA and OSHA standards, is non-negotiable, emphasizing the “cradle-to-grave” responsibility of waste generators and the importance of safe, environmentally sound disposal practices. The capacity of wastewater treatment facilities also emerges as a key consideration, often influencing chemical choices and operational planning.
Underpinning all chemical cleaning activities is an unwavering commitment to safety. A systemic approach, founded on thorough hazard identification and risk assessment, the diligent application of the hierarchy of controls, comprehensive worker training, and robust emergency preparedness, is essential to mitigate the inherent risks associated with handling potent chemicals. The dynamic use of Safety Data Sheets as active informational tools throughout the cleaning lifecycle is a cornerstone of this safety paradigm.
Finally, the engagement of professional chemical cleaning services offers tangible benefits, including access to specialized expertise and equipment, optimized chemical usage, enhanced safety performance, and assured regulatory compliance. By entrusting these critical but often non-core tasks to specialists, industrial facilities can better focus on their primary business operations, manage risks effectively, and benefit from continuous improvements in cleaning technology and practices. A comprehensive evaluation of the “true cost” of in-house versus outsourced cleaning often validates the strategic and economic advantages of professional engagement.
In conclusion, a systematic, informed, and responsible approach to industrial chemical cleaning is vital for sustainable and successful industrial operations. By integrating sound chemical principles, robust engineering practices, and a strong safety culture, industries can effectively manage contamination, optimize performance, and safeguard their personnel, assets, and the environment.