A Comprehensive Guide to General Facility Cleaning & Maintenance in Industrial Non-Production Areas
1. Introduction: The Imperative of Specialized Cleaning in Industrial Non-Production Areas
The effective cleaning and maintenance of non-production areas within industrial facilities represent a critical component of overall operational success, safety, and regulatory adherence. While distinct from the direct manufacturing or processing zones, areas such as administrative offices, control rooms, cafeterias, locker rooms, and restrooms play an indispensable role in supporting the facility’s primary functions and ensuring the well-being of its workforce.
Defining the Scope and Criticality
Industrial cleaning, by definition, encompasses the processes required to maintain cleanliness, hygiene, and sanitation standards across diverse industrial environments, including manufacturing plants, power generation facilities, and warehouses. This extends beyond mere aesthetic considerations, forming a cornerstone of a safe and healthy work environment.
Contact us!
Non-production areas, though not directly involved in output, are integral to operational integrity. Their state of cleanliness directly impacts employee health, safety, morale, and can indirectly influence the efficiency and contamination control of adjacent production processes. The maintenance of these zones is not a peripheral task but a vital support function that underpins the entire facility’s performance.
Failure to uphold stringent cleaning standards in these areas can lead to a cascade of negative consequences, ranging from workforce illnesses and reduced productivity to equipment malfunctions and regulatory non-compliance. Thus, the paradigm for cleaning in industrial non-production areas shifts from a focus on visual appeal, common in standard commercial settings , to a fundamental requirement for operational continuity and risk mitigation.
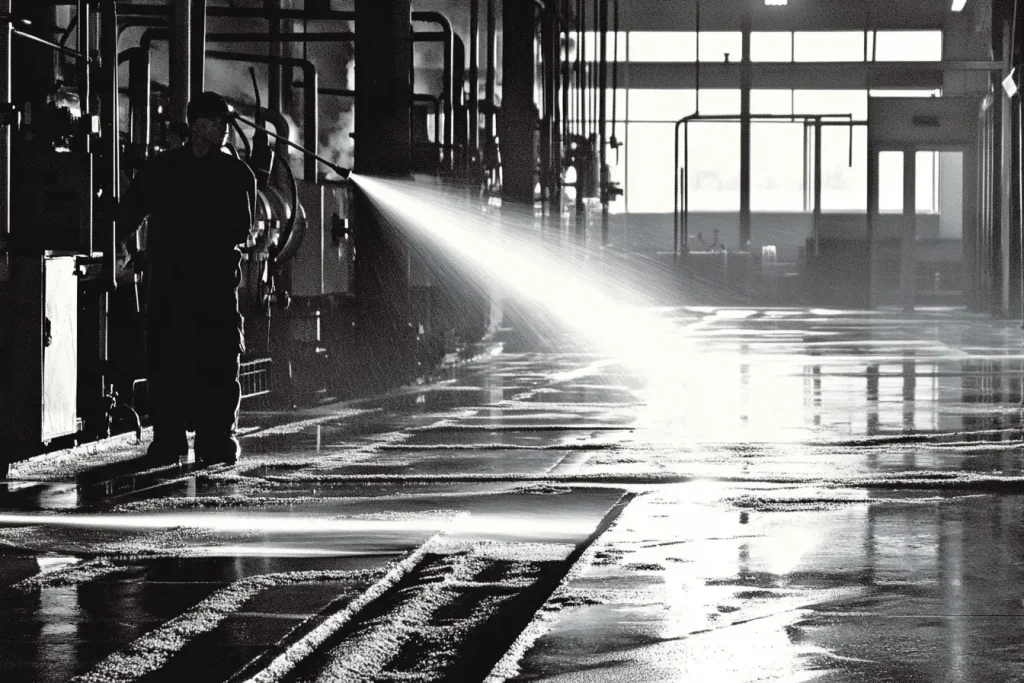
This shift underscores a significant departure from conventional commercial cleaning. The “cost” of inadequate cleaning in an industrial non-production area is not merely a diminished aesthetic or a poor impression; it translates into tangible risks such as accidents, equipment failure, breaches of health and safety regulations, and potential disruptions to production. This elevates the cleaning function from a simple janitorial task to a strategic element of facility management, demanding a proactive and meticulous approach.
Highlighting Unique Challenges
The industrial context inherently presents unique and amplified challenges for cleaning and maintenance, even within its non-production zones. Industrial cleaning is demonstrably more complex than its commercial counterpart, frequently involving the management of, or proximity to, hazardous materials, heavy machinery, and specialized systems that necessitate specific knowledge and handling protocols. The nature of contaminants encountered can be more robust and varied, including residues from heavy equipment, pervasive industrial grime, and potential traces of process chemicals that may migrate from production areas.
For instance, dust in an administrative office located within a manufacturing plant is likely to contain particulates originating from nearby industrial processes, differing significantly in composition and potential hazard from typical office dust found in a standalone commercial building. Furthermore, many industrial facilities operate on a continuous 24/7 basis, posing considerable challenges for scheduling cleaning activities. This operational tempo demands flexible, carefully planned cleaning schedules designed to minimize disruption, particularly in critical areas such as control rooms where uninterrupted operation is paramount.
The cleanliness standards of non-production areas are also intrinsically linked to the hygiene and contamination control requirements of adjacent production zones. These support areas can inadvertently act as reservoirs or vectors for contaminants if not managed with appropriate diligence. For example, dust, microorganisms, or chemical residues from a poorly maintained locker room or cafeteria can be readily transferred into a sensitive manufacturing environment via footwear, clothing, or even through air circulation systems.
Consequently, rigorous cleaning protocols in non-production zones are not merely for the benefit of those specific areas but form a crucial component of a holistic contamination control strategy for the entire facility. This interconnectedness implies that cleaning standards and procedures for an office or restroom within an industrial complex must often be more stringent and specialized than those for similar areas in non-industrial settings, due to these heightened risks of cross-contamination and the potentially severe consequences thereof.
2. Adapting Standard Janitorial Practices for the Industrial Environment
While the fundamental principles of janitorial work provide a baseline, their application within industrial non-production areas necessitates a significant adaptation and elevation of standards, methods, and safety consciousness. The transition is not merely quantitative (more cleaning) but qualitative, demanding a shift in focus from primarily aesthetic outcomes to ensuring operational integrity, safety, and compliance with stringent industry-specific regulations.
Elevated Standards: Moving Beyond Aesthetics to Operational Necessity
Industrial cleaning targets environments such as factories, warehouses, and manufacturing plants, which are inherently more complex and present a wider array of potential hazards than typical commercial office spaces. In this context, cleanliness transcends visual appeal; it becomes a critical factor in ensuring workplace safety, preventing equipment malfunctions, and maintaining overall operational efficiency. Standard janitorial duties, therefore, must be re-engineered to address these heightened requirements, focusing on the mitigation of specific industrial hazards that can manifest even in non-production zones.
Specialized Cleaning Agents and Their Applications
The nature of contaminants in industrial settings often requires cleaning agents with greater potency and specificity than those used in standard commercial cleaning. Industrial non-production areas may be subject to soils, greases, or chemical residues tracked in from production zones, or may have unique hygiene demands, as in cafeterias and restrooms that serve a large workforce potentially exposed to industrial materials. The arsenal of industrial cleaning agents includes:
- Degreasers: Powerful solutions for removing oils, grease, and stubborn grime. These can be solvent-based for heavy-duty applications or water-based, offering a more environmentally friendly option for frequent use.
- Disinfectants: Essential for hygiene control, common industrial disinfectants include quaternary ammonium compounds (quats), hydrogen peroxide-based solutions, and bleach-based products, chosen for their efficacy against a broad spectrum of pathogens.
- Alkaline Cleaners: Effective in breaking down organic soils such as fats, proteins, and heavy oils, making them suitable for cafeteria floors or areas prone to such contamination.
- Solvent Cleaners: Used to dissolve materials like adhesives, waxes, or certain types of ink, which might be found in maintenance offices or areas adjacent to specific industrial processes.
- Enzymatic and Foam Cleaners: Offer targeted action for specific soils or application needs, such as breaking down organic waste in drains or providing extended contact time on vertical surfaces.
The selection of these agents must carefully consider not only their cleaning efficacy but also their compatibility with the surfaces being cleaned (especially critical in control rooms with sensitive electronics), potential health impacts on cleaning staff and facility occupants, and environmental considerations.
Advanced Cleaning Equipment and Technology
Standard janitorial equipment often falls short in terms of durability, capacity, and specialized functionality required for industrial environments. Industrial cleaning leverages more robust and advanced technology:
- Industrial Vacuum Cleaners: These are designed for heavy-duty use, featuring powerful motors, larger capacities, and often equipped with High-Efficiency Particulate Air (HEPA) filters. HEPA filtration is crucial for capturing fine particulate matter, which is prevalent in many industrial settings and can pose respiratory risks or damage sensitive equipment.
- Heavy-Duty Floor Scrubbers: Automatic floor scrubbers (walk-behind or ride-on models) are essential for efficiently cleaning large floor areas common in industrial facilities. These machines can scrub, rinse, and dry floors in a single pass, significantly improving productivity and ensuring a higher standard of cleanliness.
- High-Pressure Washers: Used for deep cleaning durable surfaces, removing ingrained dirt, grease, or other tenacious contaminants, particularly in outdoor common areas or robust indoor surfaces.
- Specialized Tools: Equipment for cleaning ventilation systems, tanks (if applicable to waste handling in common areas), or other specific industrial fixtures may also be required.
Enhanced Safety Protocols and PPE Requirements
This is arguably the most critical adaptation. Industrial environments present a higher risk profile due to the potential presence of hazardous materials, proximity to heavy machinery, and the use of more potent cleaning chemicals. Consequently, safety protocols are significantly enhanced:
- Training: Cleaning personnel must receive comprehensive training on Hazard Communication Standards (HazCom), including the interpretation of Safety Data Sheets (SDS), proper chemical handling and dilution procedures, emergency response for spills or exposures, and the correct use of Personal Protective Equipment (PPE).
- PPE: Standard PPE (e.g., basic gloves) is often insufficient. Depending on the task and chemicals used, PPE may include chemical-resistant gloves, safety goggles or face shields, respirators (if airborne contaminants or hazardous vapors are a concern), and protective clothing.
- Risk Assessment: Each cleaning task should be assessed for potential hazards, and appropriate control measures implemented. This includes preventing dangerous chemical interactions, such as the mixing of bleach and ammonia, which can produce toxic gases.
- Regulatory Compliance: Adherence to Occupational Safety and Health Administration (OSHA) regulations and Environmental Protection Agency (EPA) guidelines is paramount.
Increased Intensity and Frequency Considerations
The type and volume of soil, the presence of specific industrial contaminants, foot traffic, and the imperative to maintain stringent safety and hygiene standards often dictate more intensive and frequent cleaning cycles in industrial non-production areas compared to typical commercial settings. Cleaning schedules must be tailored to the specific needs and risks of each area, often requiring daily or even multiple-times-daily attention for high-traffic or critical zones.
The confluence of requirements for specialized agents, advanced equipment, and rigorous safety protocols creates a substantial competency threshold. Standard janitorial staff, lacking specific industrial training and experience, are generally ill-equipped to meet these demands safely and effectively.
Attempting to adapt standard janitorial duties by merely increasing effort, without addressing this fundamental competency gap, can lead to a host of negative outcomes. These include ineffective cleaning due to the misapplication of chemicals or improper use of equipment, damage to facility assets (e.g., using corrosive chemicals on sensitive control room surfaces), serious safety incidents involving personnel (such as chemical burns or respiratory distress from improper chemical mixing or inadequate ventilation), and significant breaches of regulatory compliance. Industrial cleaning, even in non-production areas, demands a qualitative shift in skills, knowledge, and safety consciousness that is typically found in professional industrial cleaning services or meticulously trained and supervised in-house teams.
Furthermore, when adapting janitorial duties for industrial settings, the concept of the “total cost of cleaning” must be comprehensively re-evaluated. This extends far beyond direct labor and basic supply costs, which might suffice for budgeting standard janitorial work. In the industrial context, the true investment must account for specialized and ongoing training programs, higher-cost and more robust PPE, the procurement and maintenance of expensive specialized equipment, potentially higher insurance and liability coverage due to increased risks, and the significant potential costs associated with non-compliance or accidents. A superficial cost analysis that overlooks these amplified factors will lead to under-budgeting, which in turn can pressure teams to compromise on safety, training, or the quality of cleaning, ultimately undermining the very objectives of the cleaning program.
The following table provides a comparative overview:
Table 1: Comparison of Industrial vs. Standard Janitorial Cleaning in Non-Production Areas
Aspect | Standard Janitorial (Non-Production) | Industrial Janitorial (Non-Production) |
---|---|---|
Primary Goal | Aesthetics, general hygiene, occupant comfort | Safety, operational integrity, regulatory compliance, hygiene, preventing cross-contamination |
Typical Contaminants | General dust, light soil, food crumbs, common office spills | Industrial dust/particulates, heavier grime, grease/oil traces, potential chemical residues, higher microbial loads in common areas |
Cleaning Agents | General-purpose cleaners, mild disinfectants | Specialized degreasers, industrial-strength disinfectants, pH-specific cleaners, potential use of solvents or enzymatic cleaners |
Equipment Used | Standard mops, commercial vacuums, basic cleaning tools | Heavy-duty floor scrubbers, industrial HEPA vacuums, pressure washers (where applicable), specialized ventilation cleaning tools |
PPE Requirements | Basic gloves, occasionally masks | Chemical-resistant gloves, safety goggles/face shields, respirators (as needed), potentially specialized protective clothing |
Staff Training | General cleaning techniques, basic chemical safety | HazCom, SDS, advanced equipment operation, specific industrial hazard awareness, emergency response, PPE protocols |
Safety Risks | Low; minor slips, occasional mild chemical exposure | Moderate to High; chemical burns, respiratory issues, slips/trips from industrial soils, equipment-related injuries |
Regulatory Focus | Basic hygiene standards | OSHA (HazCom, PPE, sanitation), EPA (waste disposal, chemical use), industry-specific standards (e.g., food safety in cafeterias) |
Intensity/Frequency | As needed for appearance and basic hygiene; often less frequent | Higher frequency based on risk assessment, soil load, and operational needs; more intensive cleaning methods |
Waste Disposal | Primarily municipal solid waste, standard recycling | Mixed waste streams including potentially hazardous cleaning residues, specific industrial recyclables, stricter segregation rules |
This comparison underscores why a simple escalation of commercial cleaning practices is inadequate for the complexities and risks inherent in industrial non-production environments. A dedicated, specialized approach is essential.
3. Comprehensive Cleaning Protocols for Industrial Non-Production Zones
Effective cleaning in industrial non-production areas hinges on a systematic approach that begins with thorough assessment and meticulous planning, followed by the implementation of area-specific protocols. While the overarching goal is to maintain a safe, hygienic, and efficient environment, the specific tasks, frequencies, equipment, and critical considerations vary significantly across different zones.
General Approach: Assessment and Planning
Prior to initiating any cleaning regimen, a comprehensive site assessment is paramount. This involves identifying all areas requiring cleaning, determining the types and levels of contamination present, and understanding any specific challenges, such as operational constraints or unique safety considerations.
This assessment forms the basis for developing a detailed cleaning strategy that outlines clear objectives, establishes realistic timelines, and allocates necessary resources, including personnel, equipment, and supplies. Regular reviews and audits of these cleaning procedures are also crucial to ensure ongoing effectiveness and adaptation to any changes in facility operations or regulatory requirements. This proactive planning and review cycle ensures that cleaning efforts are targeted, efficient, and consistently meet the required standards.
3. Administrative Offices
Administrative offices within an industrial facility, while seemingly similar to standard commercial offices, require cleaning protocols that account for their proximity to industrial operations and the potential for unique contaminants.
- Key Tasks:
- Daily dusting of all surfaces, including desks, shelves, and office equipment.
- Vacuuming of carpets and hard floors, preferably with HEPA-filter vacuums to capture fine industrial particulates.
- Regular emptying of trash and recycling receptacles.
- Wiping and disinfecting high-touch surfaces such as doorknobs, light switches, telephones, keyboards, and shared equipment.
- Cleaning of interior windows, glass partitions, and mirrors.
- Periodic deep cleaning, including high dusting (vents, light fixtures) and detailed floor care.
- Frequency:
- Daily: High-touch surface disinfection, trash removal, spot cleaning, and basic floor vacuuming/sweeping.
- Weekly/Bi-weekly: Thorough dusting of all surfaces, comprehensive vacuuming, window cleaning, and more detailed floor cleaning.
- Specific Equipment/Agents:
- Microfiber cloths and mops for effective particle removal.
- HEPA-filter vacuum cleaners.
- EPA-approved disinfectants suitable for office surfaces.
- Neutral pH general-purpose cleaners.
- Glass cleaner.
- Critical Considerations:
- Air Quality: Maintaining good indoor air quality is crucial. This includes regular cleaning and maintenance of HVAC systems and filters to prevent the buildup and circulation of dust and airborne contaminants.
- Contaminant Transfer: Implementing measures to prevent the transfer of contaminants from production areas, such as entryway matting systems and policies regarding work footwear in office areas.
- Industrial Dust: Recognizing that dust in these offices may contain particulates from nearby manufacturing or processing activities, requiring more thorough and frequent cleaning than in a standalone commercial office.
3. Control Rooms
Control rooms are nerve centers of industrial operations, housing sensitive and critical electronic equipment. Cleaning protocols must prioritize equipment integrity and operator safety.
- Key Tasks:
- Meticulous cleaning of sensitive electronic equipment, including monitors, keyboards, control panels, consoles, and related peripherals, using manufacturer-approved methods and materials.
- Thorough dusting of all surfaces, including workstations, shelving, and ancillary equipment.
- Cleaning of internal console cavities, wiring, and cable management systems to prevent dust accumulation.
- Disinfection of high-touch surfaces, such as keyboards, mice, touchscreens, and communication devices.
- Ensuring floors are free of dust and debris.
- Frequency:
- Daily: Cleaning and disinfection of critical operator interfaces (keyboards, mice, primary control surfaces) and high-touch points.
- Regularly (e.g., Weekly/Monthly): Deep cleaning of consoles (often taking approximately two hours per console ), including internal components, cable pathways, and less accessible areas. The frequency depends on the environment and dust levels.
- Specific Equipment/Agents:
- Specialized electronic equipment cleaners and monitor wipes.
- Low-lint or microfiber cloths.
- Anti-static wipes and solutions.
- Compressed air (filtered, oil-free) for removing dust from CPUs, fans, and internal components.
- Vacuums with HEPA filters and non-metallic, soft brush attachments.
- Avoidance of liquid cleaners directly on or near sensitive electronic components; use of specialized, non-harsh solvents where necessary.
- Critical Considerations:
- Equipment Protection: The primary goal is to prevent dust accumulation that can lead to equipment overheating, malfunction, or premature failure.
- Operational Continuity: Cleaning activities must be scheduled and performed to avoid any disruption to 24/7 operations. This often involves cleaning consoles one or two at a time or during planned maintenance windows.
- Air Quality: Maintaining optimal air quality is vital for both operator health and the longevity of electronic equipment.
- Safety Protocols: Strict adherence to all site-specific safety protocols, including electrical safety and any security requirements for accessing control room areas. Cleaning staff may require specialized training and certifications (e.g., CJIS-certified for secure environments ).
3. Cafeterias and Break Rooms
These areas are critical for employee well-being and require stringent hygiene standards to prevent foodborne illnesses and maintain a pleasant environment.
- Key Tasks:
- Frequent wiping and disinfection of tables, chairs, and benches.
- Cleaning and sanitizing countertops, food preparation surfaces (if any), and serving lines.
- Cleaning the interior and exterior of appliances such as microwaves, refrigerators, and vending machines.
- Sanitizing food contact surfaces, condiment stations, and beverage dispensers.
- Daily sweeping and mopping of floors, often requiring degreasing agents, particularly in cooking or heavy-use areas.
- Regular emptying of trash and recycling bins, with particular attention to food waste.
- Maintenance of drains and grease traps to prevent blockages and odors.
- Frequency:
- Multiple times daily/After each meal service: Wiping and sanitizing tables, countertops, and food contact surfaces.
- Daily: Floor cleaning, appliance exteriors, trash removal, spot cleaning.
- Weekly: Deep cleaning of appliances (interiors), display cases, drains, grease traps, and less frequently touched surfaces.
- Specific Equipment/Agents:
- Food-grade sanitizers (e.g., USDA D-2 approved) for food contact surfaces.
- Foaming degreasers (e.g., USDA A-1 approved) for heavy grease and oil.
- Neutral pH floor cleaners or specialized cleaners for greasy floors.
- Disinfectants for non-food contact surfaces.
- Appropriate PPE, including gloves and potentially aprons.
- Critical Considerations:
- Food Safety: Strict adherence to food safety regulations and hygiene practices to prevent cross-contamination and foodborne illnesses.
- Grease Management: Effective removal of grease from floors and surfaces to prevent slips, falls, and fire hazards.
- Pest Control: Maintaining cleanliness to deter pests is crucial.
- Waste Segregation: Proper separation of food waste for composting (if a program is in place), recyclables, and general trash.
- Odor Control: Regular cleaning and proper ventilation to manage food odors.
3. Locker Rooms
Locker rooms are high-traffic, high-humidity environments prone to microbial growth, requiring diligent cleaning and disinfection.
- Key Tasks:
- Cleaning and disinfecting all toilets, urinals, sinks, and shower stalls (if present).
- Wiping down and disinfecting countertops, benches, and other flat surfaces.
- Cleaning and disinfecting locker exteriors and handles.
- Cleaning and disinfecting door knobs and light switches.
- Daily cleaning and disinfection of floors, which are often wet.
- Regular emptying of trash receptacles.
- Ensuring adequate ventilation and implementing odor control measures.
- Frequency:
- Daily: Comprehensive cleaning and disinfection of all high-touch surfaces, sanitary fixtures, and floors.
- More Frequent (shift-based or as needed): Spot cleaning and checks in high-use facilities.
- Specific Equipment/Agents:
- Hospital-grade or broad-spectrum disinfectants effective against common pathogens.
- Deodorizing cleaners or separate deodorizers.
- Commercial floor cleaners suitable for wet environments and various flooring materials.
- Scrub brushes for grout and corners.
- Critical Considerations:
- Pathogen Control: Locker rooms can be breeding grounds for bacteria, fungi (e.g., athlete’s foot), and viruses (e.g., Staph, MRSA, influenza). Thorough disinfection is paramount.
- Ventilation: Proper ventilation is essential to control humidity, prevent mold and mildew growth, and manage odors.
- Slip Prevention: Ensuring floors are properly cleaned and dried to minimize slip hazards.
- Deep Cleaning: Periodic deep cleaning to address buildup in grout lines, shower drains, and other hard-to-reach areas.
3. Restrooms
Industrial restrooms demand rigorous cleaning and disinfection to maintain hygiene, comply with regulations, and ensure user comfort.
- Key Tasks:
- Pre-cleaning toilets and urinals to remove gross soil.
- Applying toilet bowl cleaner and allowing appropriate dwell time.
- Thoroughly cleaning and disinfecting all surfaces of toilets and urinals, including seats, handles, and exteriors.
- Cleaning and disinfecting sinks, faucets, countertops, and dispensers.
- Cleaning and disinfecting partitions, door handles, and light switches.
- Dusting of vents, ledges, and other horizontal surfaces.
- Sweeping and mopping floors with a disinfectant solution.
- Emptying trash receptacles and sanitary napkin disposals.
- Restocking essential supplies: toilet paper, paper towels, hand soap.
- Frequency:
- Daily (often 1-2 times or more): Dependent on facility size, number of employees, and shift patterns. All fixtures and high-touch surfaces should be cleaned and disinfected daily.
- Weekly: Deep cleaning, including walls, stall partitions, vents, and detailed grout cleaning.
- Specific Equipment/Agents:
- EPA-registered disinfectants with proven efficacy against common pathogens.
- Non-acid bowl cleaners for daily use; acid-based bowl cleaners for periodic removal of stubborn stains or mineral buildup.
- Glass cleaner for mirrors.
- Appropriate PPE, including gloves and eye protection (goggles) when using spray disinfectants or bowl cleaners.
- Color-coded microfiber cloths and mops to prevent cross-contamination between restroom areas and other facility zones.
- Critical Considerations:
- Regulatory Compliance: Adherence to OSHA standards for sanitation (29 CFR 1910.141) and provision of an adequate number of toilet facilities.
- Dwell Times: Ensuring disinfectants remain on surfaces for the manufacturer-recommended dwell time to achieve effective pathogen kill.
- Cross-Contamination Prevention: Implementing strict procedures, such as using separate cleaning tools for toilets versus sinks, and cleaning from cleanest to dirtiest areas.
- Slip Prevention: Ensuring floors are left as dry as possible after mopping and using “wet floor” signs.
- Odor Control: Achieved through regular cleaning, disinfection, proper ventilation, and use of appropriate cleaning products rather than just masking agents.
The intensity and specificity of cleaning protocols are directly influenced by the unique risk profile of each non-production area. For example, the primary risk in a control room is equipment damage or operational disruption due to dust or improper chemical use , dictating meticulous, non-damaging cleaning methods. In contrast, cafeterias and restrooms present significant health and hygiene risks, prioritizing thorough sanitation and pathogen control. A generic, one-size-fits-all cleaning plan is therefore not only ineffective but potentially hazardous.
Misapplying a protocol, such as using a harsh degreaser suitable for a cafeteria floor in a control room with sensitive electronics, could lead to severe damage and costly downtime. This necessitates that the initial assessment and planning phase includes a detailed, area-specific risk evaluation to tailor cleaning procedures appropriately.
Particularly in high-stakes areas like control rooms, the cleaning function transcends routine hygiene and evolves into a critical preventative maintenance activity. The meticulous, specialized cleaning protocols for these zones directly contribute to equipment reliability, operational uptime, and risk mitigation. Investing in such specialized cleaning should be viewed not as a mere operational expense, but as an investment in the stability and longevity of critical assets.
The potential cost of not performing this specialized cleaning—manifesting as equipment failure, production halts, or safety incidents—far outweighs the cost of the cleaning service itself. The tasks described for control rooms, such as cleaning inside cabinets, blowing out CPUs, and managing cable cleanliness , are less about aesthetics and more about ensuring the continued, reliable functioning of essential operational technology. This elevates the role of the cleaning personnel in these specific zones to that of quasi-maintenance technicians, whose work is integral to the facility’s core operations.
The following table summarizes key aspects of cleaning protocols for these diverse non-production areas:
Table 2: Summary of Cleaning Protocols for Industrial Non-Production Areas
Area | Key Cleaning Tasks | Recommended Minimum Frequency (Examples) | Key Equipment/Agents | Critical Safety/Hygiene Considerations |
---|---|---|---|---|
Administrative Offices | High-touch surface disinfection, HEPA vacuuming (floors/upholstery), trash/recycling removal, general dusting, window cleaning. | Daily (high-touch, trash), Weekly (thorough vacuuming, dusting, windows). | HEPA-filter vacuums, EPA-approved disinfectants, microfiber cloths, neutral cleaners, glass cleaner. | Maintaining good air quality, preventing cross-contamination from production areas, managing industrial dust. |
Control Rooms | Cleaning sensitive electronic equipment (consoles, monitors, keyboards), detailed dust removal from all surfaces and internal components, cable management cleaning, high-touch disinfection. | Daily (operator interfaces, high-touch), Regular Deep Clean (e.g., weekly/monthly per console based on dust levels). | Specialized electronic cleaners, anti-static wipes, compressed air, HEPA vacuums, microfiber cloths. | Protecting equipment sensitivity, ensuring no disruption to 24/7 operations, maintaining optimal air quality for operators and equipment. |
Cafeterias/Break Rooms | Sanitizing tables & food contact surfaces, cleaning appliances, degreasing floors, trash/recycling/compost removal, drain maintenance. | Multiple times daily (tables, food surfaces), Daily (floors, appliances, trash), Weekly (deep clean, grease traps). | Food-grade sanitizers, foaming degreasers, neutral floor cleaners, disinfectants, appropriate PPE. | Strict adherence to food safety regulations, preventing cross-contamination, grease management (slips/fire), pest control. |
Locker Rooms | Cleaning/disinfecting toilets, sinks, showers, benches, locker handles; floor cleaning/disinfection; odor control; trash removal. | Daily (all high-touch surfaces, fixtures, floors), More frequent checks in high-traffic facilities. | Hospital-grade disinfectants, deodorizing cleaners, commercial floor cleaners for wet areas. | High potential for pathogen spread (Staph, MRSA, fungi), humidity/odor control via ventilation, slip prevention. |
Restrooms | Cleaning/disinfecting toilets, urinals, sinks, partitions, high-touch points; floor mopping with disinfectant; trash removal; supply restocking. | 1-2 times daily or more based on occupancy; Weekly (deep cleaning walls, vents, grout). | EPA-approved disinfectants, bowl cleaners (acidic for periodic use), glass cleaner, color-coded microfiber. | Adherence to OSHA sanitation standards, proper disinfectant dwell times, cross-contamination prevention, slip prevention. |
This structured overview provides a practical framework for facility managers to develop, implement, and audit comprehensive cleaning programs tailored to the specific demands of each non-production zone within an industrial setting.
4. Mastering Specialized Cleaning Sub-Tasks in Common Industrial Areas
Beyond routine cleaning of designated zones, certain sub-tasks require specialized knowledge, techniques, and equipment to effectively manage the unique challenges presented in industrial common areas. These include heavy-duty floor care, advanced dust control, and comprehensive waste management, each critical to maintaining a safe, compliant, and efficient operational environment.
4. Heavy-Duty Floor Care
Floors in industrial facilities, even in non-production common areas like corridors, lobbies, or cafeterias, are subjected to significant stresses, including heavy foot traffic, potential spills of various substances, and the tracking of industrial soils. A robust floor care program is therefore essential, not only for aesthetics but more importantly for safety and longevity of the flooring material. The condition of floors has a disproportionately large impact on overall facility safety, particularly concerning slip, trip, and fall hazards , which are a leading cause of workplace injuries. OSHA regulations, such as §1910.22(a)(2), mandate that floors be kept clean and, so far as practicable, dry. Investing in appropriate heavy-duty floor care—encompassing the correct machinery, solutions, and cleaning frequencies—is thus a critical risk management strategy and an indirect contributor to operational efficiency by reducing accidents and facilitating easier movement.
- Techniques for Various Industrial Floor Types:
- Concrete Floors: These are common in industrial settings due to their durability. Effective cleaning involves regular sweeping or vacuuming to remove loose debris. Wet mopping with a neutral pH cleaner is suitable for routine cleaning, while periodic deep cleaning often requires industrial floor scrubbers equipped with appropriate brushes (abrasive for unsealed, tough concrete; softer for sealed surfaces) and concrete-specific detergents. Pre-treating stains, especially oil and grease, is crucial. Applying a quality sealant can significantly aid in stain prevention and ease of cleaning. For instance, daily cleaning might involve sweeping and washing with a floor scrubber and a neutral cleanser with a degreasing agent for oily spills, while deep cleaning involves heavy-duty detergents and more intensive scrubbing.
- Epoxy Coated Floors: Valued for their seamless and chemical-resistant surface, epoxy floors require specific care. Daily sweeping is recommended. Cleaning is best done with warm or hot water, or properly diluted ammonia-based cleaners. Specialized epoxy floor cleaners are also available. It is critical to avoid soap-based cleaners, as they can leave a dulling residue and make the floor slippery when wet. Harsh chemical cleaners can also deteriorate the epoxy coating. While floor scrubbers are ideal for large epoxy surfaces, pressure washing is generally discouraged or should only be used on a very low setting with extreme caution, as it can damage the surface over time.
- Vinyl Floors (VCT, LVT): Often found in offices, break rooms, and corridors, vinyl flooring requires daily sweeping to remove surface dirt and debris. Damp mopping is the preferred method for cleaning, using the mildest possible cleaning solutions; a mixture of apple cider vinegar and hot water is often recommended for its effectiveness and gentle action. Excessive water should be avoided as it can seep into seams and damage the adhesive or the planks themselves. Harsh cleaning methods and abrasive tools are detrimental. Vinyl floors should not be waxed, as their inherent sheen comes from a polyurethane coating; polishes or sealants designed for vinyl can be used if the shine diminishes. For stains, a soft nylon brush with rubbing alcohol (for ink) or mineral spirits (for paint/marker) can be effective. WD-40 or jojoba oil can help remove stubborn scuffs.
- Selection and Use of Industrial Floor Cleaning Machinery:
- Floor Scrubbers: These are indispensable for maintaining large floor areas. They combine scrubbing action with solution dispensing and vacuuming up dirty water, leaving floors clean and nearly dry in one pass. Walk-behind models suit smaller or more congested areas, while ride-on scrubbers offer high productivity for expansive spaces. The choice of brushes (e.g., soft nylon for delicate surfaces, polypropylene for general scrubbing, or more aggressive grit brushes for heavily soiled concrete) and pads (ranging from soft polishing pads to aggressive stripping pads) is critical and depends on the floor type and the nature of the soil.
- Industrial Sweepers: Used for the initial removal of dry, loose dirt, dust, and larger debris before wet cleaning processes like scrubbing or mopping. They are available in manual, walk-behind, and ride-on versions.
- Industrial Vacuum Cleaners: Heavy-duty vacuums with robust construction and large capacities are essential. Models equipped with HEPA filters are highly recommended, especially in industrial environments, to capture fine dust particles and prevent their recirculation into the air.
- Pressure Washers: Effective for deep cleaning very durable surfaces, such as exterior concrete pathways or heavily soiled loading dock areas. Hot water pressure washers are particularly effective against grease and oil. However, caution is advised when using pressure washers on tiled floors (can damage grout ) and epoxy floors (can damage the coating ).
- Appropriate Cleaning Solutions and Degreasers:
- The choice of cleaning solution must be compatible with the floor type and effective against the specific soils present. Neutral pH cleaners are generally safe for most floor types, including vinyl, sealed concrete, and epoxy, for routine cleaning.
- Degreasers are necessary for areas prone to oil and grease accumulation, such as floors in or near maintenance workshops, some industrial corridors, or cafeteria kitchens. These can range from alkaline degreasers to specialized solvent-based or enzymatic products.
- Specialized concrete cleaners, such as those designed to remove laitance (a weak, cement-rich layer on new concrete) or formulated for daily maintenance of densified/polished concrete, should be used where appropriate.
- It is crucial to avoid using the wrong type of chemical for a given floor (e.g., acidic cleaners on polished concrete unless specifically for etching or heavy mineral scale removal, as they can damage the surface ). Proper dilution of concentrated cleaners according to manufacturer instructions is also vital to prevent residue buildup, which can attract more dirt and make floors harder to clean over time. Thorough rinsing after using detergents is often recommended, especially on resilient flooring.
4. Advanced Dust Control Strategies
Dust in industrial common areas is a pervasive challenge that is often underestimated. It is not merely “dirt”; it can be a complex mixture of organic and inorganic particles, including fibers, soil, metal fragments, and chemical residues originating from various processes within the facility or tracked in from outside. This dust poses risks to employee health (causing respiratory issues, allergies, or exacerbating existing conditions ), can damage sensitive electronic equipment (particularly in administrative offices or control rooms ), and may even compromise product quality if it migrates into production zones.
Therefore, effective dust control requires a multi-faceted approach that goes beyond simple surface cleaning and is crucial for long-term operational health, safety, and efficiency.
- Identifying Common Dust Sources in Non-Production Areas: Dust in common areas can originate from numerous sources:
- External Sources: Windblown soil and pollutants from outdoors entering through open doors, windows, and loading docks.
- Tracked-in Material: Dirt, debris, and industrial particulates carried in on footwear and vehicle tires.
- Building Materials: Abrasion of concrete floors, degradation of paint, or fibers from ceiling tiles or insulation.
- Operational Byproducts: Particulates from nearby manufacturing, processing, or packaging operations (e.g., cutting, grinding, material handling) that become airborne and migrate. Cardboard packaging and wooden pallets are significant contributors of fiber dust.
- Human Activity: Skin cells, clothing fibers, and general disturbance of settled dust.
- Mitigation Techniques: A comprehensive dust control strategy typically involves a hierarchy of controls:
- Source Control & Reduction: This is the most effective approach.
- Good Housekeeping: Regular and thorough cleaning to prevent accumulation.
- Material Management: Covering material stockpiles (if they are a nearby source), using dust-suppressing packaging, or modifying processes to generate less dust.
- Surface Treatment: Paving unpaved roads and parking lots near facility entrances to reduce tracked-in dust. Applying gravel or landscaping rock to unpaved, low-traffic areas.
- Entryway Control: Installing effective matting systems at all entrances to capture dirt and moisture from footwear. Implementing wheel wash stations for vehicles entering from dusty areas can minimize tracked material.
- Dust Suppression:
- Watering: Applying water to unpaved roads or outdoor areas to weigh down dust particles. Regular, light watering is generally more effective than infrequent, heavy applications.
- Chemical Suppressants: Using hygroscopic salts (e.g., calcium chloride, magnesium chloride) or lignosulfonates on unpaved surfaces or material stockpiles to bind dust particles and retain moisture. Care must be taken to select environmentally appropriate suppressants, especially near water sources.
- Containment and Barriers:
- Enclosures & Curtains: Enclosing dust-generating processes or using dust curtains at material transfer points if these are impacting common areas.
- Windbreaks: Constructing natural (e.g., vegetation) or artificial windbreaks (e.g., fences, walls) to reduce wind speed at ground level and limit the dispersion of dust from outdoor sources.
- Ventilation and Air Filtration:
- HVAC Systems: Ensuring HVAC systems are properly designed, maintained, and equipped with high-efficiency filters (e.g., MERV 13 or higher) to capture airborne particulates. Regular filter replacement is critical.
- Local Exhaust Ventilation (LEV): If specific, identifiable dust sources within or near common areas exist, LEV systems can capture dust at its point of generation.
- Industrial Air Purifiers: Deploying standalone industrial air purification units equipped with HEPA filters in critical common areas (e.g., offices, control rooms, cafeterias) can significantly reduce airborne dust concentrations. HEPA filters are rated to capture at least 99.97% of airborne particles 0.3 micrometers (μm) in diameter.
- Cleaning Practices:
- Vacuuming: Regular vacuuming of all surfaces (floors, upholstery, ledges) using industrial vacuums equipped with HEPA filters is essential to remove settled dust without re-dispersing it into the air.
- Wet Cleaning: Wet mopping of hard floors and damp wiping of surfaces are more effective than dry dusting for capturing and removing fine dust particles. Microfiber cleaning tools are particularly efficient.
- High-Level Cleaning: Periodically cleaning high and hard-to-reach areas (e.g., tops of cabinets, light fixtures, ductwork) where dust can accumulate unnoticed and later become dislodged.
- Source Control & Reduction: This is the most effective approach.
- Dust Control Equipment:
- Industrial Vacuum Cleaners with HEPA Filters: As mentioned, these are fundamental for effective dust removal. Explosion-proof models may be necessary if combustible dusts are a concern, though less common for general non-production areas unless specific risks are identified.
- Air Scrubbers/Purifiers: Portable or stationary units that draw air through a series of filters, including HEPA filters, to remove airborne contaminants. These are particularly useful during cleaning activities that might disturb settled dust or in areas with ongoing dust issues.
- Dust Collection Systems: While more common in production areas, smaller or localized dust collectors (e.g., downdraft tables if minor benchwork occurs in a common maintenance office, or ambient air cleaners) might be applicable in some non-production settings with specific dust sources. These systems typically include a blower, dust filter (baghouse or cartridge type), filter cleaning mechanism, and dust receptacle.
4. Industrial Waste Management in Non-Production Areas
Effective waste management in the non-production areas of an industrial facility is crucial for maintaining hygiene, ensuring regulatory compliance, promoting sustainability, and controlling costs. These areas generate a diverse array of waste streams that require careful handling, segregation, and disposal. A particular challenge arises from cleaning activities themselves, as used cleaning agents, soiled wipes, and empty containers can sometimes constitute hazardous waste, adding a layer of complexity not typically encountered in standard commercial office waste management.
- Waste Stream Identification and Segregation:
The first step is to accurately identify the different types of waste generated. Common waste streams in industrial non-production areas include:- Municipal Solid Waste (MSW)-like materials:
- Offices: Paper, cardboard, plastic bottles, food wrappers, general office trash.
- Cafeterias/Break Rooms: Food scraps, food packaging (plastic, paper, foil), beverage containers, used napkins, disposable cutlery and plates.
- Restrooms/Locker Rooms: Paper towels, toilet paper cores, soap packaging, sanitary waste.
- Commercial & Industrial (C&I) Waste: Larger volumes of packaging materials (cardboard, plastic shrink wrap) from supplies, potentially discarded office equipment or furniture.
- Cleaning-Related Waste:
- Empty containers of cleaning chemicals (some may be hazardous depending on residues ).
- Used wipes, rags, and absorbents (may be contaminated with cleaning chemicals, oils, or other substances, potentially rendering them hazardous).
- Used Personal Protective Equipment (PPE) (gloves, masks – may be contaminated).
- Potentially Hazardous Waste: Beyond cleaning residues, this could include spent batteries, fluorescent lamps (containing mercury), or electronic waste (e-waste) from offices or control rooms.
- Municipal Solid Waste (MSW)-like materials:
Effective segregation at the point of generation is paramount. This typically involves providing clearly labeled bins for different categories:
-
- Recyclables (paper, plastics, glass, metal)
- Compostables (food scraps, certain paper products – if a composting program is in place )
- General Non-Hazardous Waste (for landfill)
- Hazardous Waste (requiring specialized handling and disposal )
- Collection, Storage, and Labeling Protocols:
- Receptacles: Waste receptacles must be appropriate for the type of waste they contain. Those used for putrescible solid or liquid waste (e.g., food waste in cafeterias) must be constructed to prevent leaks, be easily cleanable, and maintained in a sanitary condition. Such receptacles should ideally have solid, tight-fitting covers unless they can be kept sanitary without them.
- Storage Areas: Designated areas for temporary storage of accumulated waste should be maintained in a clean and orderly manner, preventing pest harborage and odor issues. Hazardous waste storage areas have specific regulatory requirements regarding containment, security, and signage.
- Labeling: All waste containers, especially those for hazardous waste, must be clearly and accurately labeled according to applicable regulations (e.g., EPA, DOT). Labels should identify the contents and any associated hazards. All documentation related to special or hazardous waste handling and disposal must be meticulously maintained.
- Recycling Programs for Offices and Cafeterias:
Implementing robust recycling programs is a key component of sustainable waste management.- Materials: Common recyclables include office paper, cardboard, plastic bottles and containers (e.g., PET, HDPE), glass bottles and jars, and aluminum and steel cans.
- Collection: Provide clearly marked recycling bins in convenient locations throughout offices, cafeterias, and break rooms. Employee education and clear signage are crucial for minimizing contamination of recyclables.
- Processing: Collected recyclables are typically sent to a Materials Recovery Facility (MRF) for sorting and processing before being sent to manufacturers to be made into new products.
- Food Waste Composting: In cafeterias, implementing a food waste composting program can significantly reduce landfill volume. This requires separate collection of food scraps and compostable paper products, and coordination with a composting facility. The EPA provides various tools and resources to help communities and businesses improve their recycling programs, emphasizing the environmental benefits of reducing landfill waste, conserving natural resources, and preventing pollution.
- Compliant Disposal Methods:
The disposal method depends on the waste classification:- Non-Hazardous Solid Waste: Typically disposed of in municipal solid waste landfills or waste-to-energy incinerators through contracts with licensed waste hauling services. Recycling and composting should be prioritized to minimize landfilling.
- Hazardous Waste: This waste stream, which can include certain cleaning chemical residues, spent solvents, contaminated wipes or PPE, some paints, batteries, and fluorescent bulbs, requires strict adherence to “cradle-to-grave” management under the Resource Conservation and Recovery Act (RCRA). This involves:
- Proper identification and classification of the waste (often using Safety Data Sheets for chemical products).
- Segregation from non-hazardous waste.
- Storage in appropriate, labeled containers in designated, secure areas.
- Use of licensed hazardous waste transporters.
- Treatment and/or disposal at permitted hazardous waste facilities.
- Maintenance of detailed records, including manifests.
- Crucially, hazardous waste must never be mixed with general trash, poured down drains, or otherwise improperly disposed of, as this can lead to severe environmental contamination and significant legal penalties.
- Special Wastes: Some industrial wastes, while not classified as hazardous under RCRA, may still require special handling, evaluation, or disposal methods due to their characteristics or local/state regulations. Examples could include asbestos-containing materials (if disturbed during maintenance or renovation activities near common areas) or certain types of industrial sludge if they were to be managed through non-production area systems. Generators are responsible for classifying their waste and ensuring proper disposal.
The inadvertent generation of hazardous waste through cleaning activities in non-production areas presents a significant, often overlooked, challenge. Facility managers must ensure that waste segregation programs and staff training explicitly address the handling of cleaning-related wastes.
This includes procedures for identifying which cleaning products or their residues are hazardous (referencing SDS), how to manage empty containers (e.g., triple-rinsing some, managing others as hazardous waste), and the proper disposal of soiled wipes or PPE. This adds a layer of complexity and due diligence to waste management in industrial non-production areas that is not typically present in standard commercial office settings, underscoring the need for specialized knowledge and robust procedures to ensure compliance and environmental protection.
The following table offers a quick guide for segregating common waste items:
Table 3: Industrial Waste Segregation and Disposal Quick Guide (Non-Production Areas)
Common Waste Type | Segregation Category | Key Disposal Considerations/Regulations |
---|---|---|
Office Paper, Cardboard | Recyclable | Keep clean and dry; follow local Material Recovery Facility (MRF) rules; flatten cardboard. |
Plastic Bottles/Containers (e.g., PET, HDPE) | Recyclable | Empty and rinse if necessary; check local recycling guidelines for acceptable plastic types. |
Glass Bottles/Jars | Recyclable | Empty and rinse; check local guidelines for color separation or co-mingled collection. |
Aluminum/Steel Cans | Recyclable | Empty and rinse. |
Food Scraps (Cafeteria) | Compostable (if program exists) | Collect in designated bins; ensure no non-compostable contaminants (e.g., plastic wrappers); follow facility/composter guidelines. |
General Trash (non-recyclable, non-hazardous office/breakroom waste) | General Waste (Landfill) | Standard municipal or commercial waste pickup; ensure no hazardous materials are included. |
Used Cleaning Wipes/Rags (general purpose, water-based cleaner) | General Waste (Landfill) | If not contaminated with hazardous substances, can typically go to general waste. |
Empty General Cleaner Containers (non-hazardous) | Recyclable (if clean) / General Waste | Rinse thoroughly if to be recycled (check plastic type); otherwise, dispose as general waste if truly non-hazardous per SDS. |
Used Cleaning Wipes/Rags (solvent-based or other hazardous cleaner) | Hazardous Waste | Consult SDS for cleaner; if contaminated with hazardous constituents, must be managed as hazardous waste. Do not launder with general items. Store in labeled, closed container. |
Empty Industrial Cleaner Containers (contained hazardous constituents) | Hazardous Waste | Consult SDS; if container held acutely hazardous waste or cannot be effectively emptied/triple-rinsed, it may be hazardous waste. Label and store appropriately. |
Used PPE (e.g., gloves, respirators contaminated with hazardous substances) | Hazardous Waste | If contaminated with hazardous materials (e.g., from cleaning spills or using hazardous chemicals), manage as hazardous waste. Store in labeled, closed container. |
Fluorescent Lamps, Batteries (some types), E-waste | Universal Waste / Hazardous Waste | Often managed as Universal Waste (streamlined hazardous waste rules) or fully regulated hazardous waste depending on type and quantity. Requires specific recycling or disposal routes, not landfill. Check local and federal regulations. |
This guide serves as a starting point; always refer to specific product SDS and local/federal waste regulations for definitive classification and disposal requirements.
5. The Strategic Advantages of Partnering with Professional Industrial Cleaning Services
Engaging specialized professional industrial cleaning services offers numerous strategic advantages that extend beyond mere cleanliness. For facilities grappling with the complexities of maintaining non-production areas in an industrial context, outsourcing these functions can lead to enhanced safety, improved operational efficiency, robust regulatory compliance, and significant long-term cost-effectiveness. These benefits stem from the specialized expertise, advanced technologies, and focused approach that professional providers bring to the table.
Access to Specialized Expertise, Training, and Advanced Technology
Professional industrial cleaning companies possess a depth of knowledge and experience specifically tailored to the unique demands of industrial environments. Their personnel are typically trained to handle specialized equipment, understand the nuances of different industrial contaminants, and develop individualized cleaning plans suited to each facility’s specific needs.
This expertise is crucial for tackling complex cleaning tasks that go beyond the scope of standard janitorial capabilities. Furthermore, these companies often invest in and utilize advanced cleaning equipment and scientifically formulated cleaning solutions designed for optimal performance and safety in industrial settings. Some firms also leverage cutting-edge technologies, such as robotic cleaning systems or IoT-enabled monitoring, to enhance efficiency and effectiveness. This access to specialized human capital and technological resources is a significant differentiator.
The efficiency and effectiveness of industrial cleaning are substantially amplified by this specialization. Professional services, by their very nature, focus on cleaning and maintenance as their core competency. This dedicated focus allows them to invest significantly in specialized training programs for their staff, tailored explicitly to the hazards and requirements of diverse industrial environments.
They are also more likely to procure, maintain, and efficiently deploy advanced and specialized cleaning equipment and technologies due to the economies of scale derived from serving multiple clients. Their accumulated experience across various industrial sectors provides a rich repository of knowledge on best practices for addressing a wide array of cleaning challenges. Consequently, the “value of specialization” translates into professional services often achieving a higher, more consistent standard of cleanliness and safety, and doing so more efficiently, than an in-house team for whom cleaning is an auxiliary, rather than primary, function.
Enhanced Safety, Risk Mitigation, and Regulatory Compliance (OSHA, EPA)
Safety is a paramount concern in industrial settings, and professional cleaning services play a vital role in mitigating risks and ensuring a safer working environment. They are adept at identifying and removing potential hazards, such as spills, accumulated dust, or improperly stored waste, thereby reducing the likelihood of accidents and injuries. Critically, reputable industrial cleaning providers are well-versed in regulatory requirements, including those set forth by OSHA (e.g., Hazard Communication, PPE standards, sanitation requirements) and the EPA (e.g., chemical handling, waste disposal).
Their staff are trained in the safe handling of potentially hazardous materials and employ cleaning methods that adhere to these stringent standards. This expertise helps facilities avoid common OSHA citations and maintain a strong compliance posture. By entrusting cleaning to professionals, facilities can reduce their liability exposure and the risk of costly fines associated with non-compliance. They are equipped to manage the complexities of chemical safety protocols and ensure that waste, including any hazardous byproducts of the cleaning process itself, is disposed of in accordance with all applicable laws.
Engaging professional industrial cleaning services should therefore be viewed not merely as an operational expenditure but as a strategic investment in comprehensive risk management. These professional entities effectively assume and manage many of the risks inherently associated with industrial cleaning tasks—such as the handling of potent chemicals, the operation of specialized and potentially dangerous equipment, and the critical adherence to complex regulatory frameworks.
This transfer of risk from the facility to the service provider can yield substantial benefits, including a reduced likelihood of safety incidents and the associated costs of workers’ compensation claims. It also lowers the risk of incurring regulatory fines for non-compliance with OSHA or EPA standards , and provides a safeguard against damage to sensitive equipment or facility assets that could result from the use of improper cleaning methods by untrained personnel. Industrial cleaning inherently involves risks from hazardous materials, complex equipment, and stringent regulations. Managing these risks effectively in-house demands considerable and ongoing investment in specialized training, diligent supervision, and deep domain knowledge.
Professional industrial cleaning companies, conversely, specialize in managing these very risks as a core element of their business operations. They come prepared with appropriately trained personnel, adequate insurance coverage, and established, proven safety protocols. Outsourcing to such professionals, therefore, allows the facility to offload a significant portion of this operational and compliance burden, enabling its own management and staff to concentrate more fully on primary production activities and core business risks.
Improved Operational Efficiency and Equipment Longevity
While this guide focuses on non-production areas, the principles of cleanliness impacting operational efficiency and equipment lifespan remain relevant. Clean and well-maintained environments contribute to smoother overall operations. For example, clean HVAC systems in administrative offices and control rooms operate more efficiently and provide better air quality, which can positively affect employee alertness and health. Well-maintained floors in common areas reduce wear and tear on any material handling equipment that might traverse these zones.
Most critically, meticulous cleaning in areas like control rooms directly prevents dust and contaminant buildup that can lead to the overheating, malfunction, or premature failure of sensitive and expensive electronic equipment. Professional cleaning services, through their regular and thorough maintenance, help prevent costly repairs and extend the life of facility assets.
Cost-Effectiveness: Reduced Downtime, Lower Repair Costs, Optimized Resource Use
Although engaging professional services involves an upfront cost, it often proves to be more cost-effective in the long run compared to managing cleaning operations in-house. This is because the “total cost” of an in-house program includes not only direct labor (salaries, benefits) and supplies, but also the expenses associated with specialized training, purchasing and maintaining advanced cleaning equipment, management oversight, and the potential liabilities from accidents or non-compliance.
Professional services benefit from economies of scale, specialized efficiencies, and optimized resource utilization (chemicals, water, labor), which can translate into better value. Furthermore, by preventing equipment damage, reducing workplace accidents (and associated costs like insurance claims and lost workdays), and minimizing operational downtime, professional cleaning contributes to overall financial savings. Case studies have demonstrated tangible reductions in labor and maintenance costs for facilities that outsource their industrial cleaning needs.
Focus on Core Business Activities and Improved Employee Morale and Productivity
Outsourcing cleaning and maintenance allows the facility’s management and staff to concentrate on their core business activities and strategic objectives, rather than diverting valuable time and resources to managing complex cleaning operations. A professionally cleaned and maintained environment also has a significant positive impact on employee morale, job satisfaction, and productivity. Employees working in a clean, safe, and hygienic workspace are generally more motivated, experience less stress, and are less prone to illness-related absenteeism. This fosters a more positive and efficient workforce, contributing directly to the company’s bottom line.
Commitment to Green Cleaning and Sustainability
Many leading professional industrial cleaning companies are committed to environmentally responsible practices. This includes the use of eco-friendly, biodegradable cleaning products, water-efficient equipment, energy-saving methodologies, and comprehensive waste reduction and recycling programs.
Such providers are often knowledgeable about green cleaning standards and certifications, such as the EPA’s Safer Choice program, which identifies products formulated with safer chemical ingredients. Partnering with a sustainability-conscious cleaning service helps industrial facilities meet their own environmental goals, reduce their ecological footprint, and enhance their corporate social responsibility profile.
Beyond the immediate operational benefits, the decision to engage professional industrial cleaning services, particularly those that visibly incorporate green and sustainable practices, can create a positive ripple effect on the company’s overall business reputation and its long-term sustainability. A demonstrably clean and well-maintained facility makes a strong positive first impression on clients, partners, and potential investors.
A clear commitment to providing a safe and healthy work environment, often achieved and maintained through professional cleaning services, enhances employee morale and can be a significant factor in attracting and retaining skilled talent. Furthermore, professional services are typically better equipped to implement, document, and report on sustainable cleaning practices.
This alignment with growing environmental consciousness is increasingly important for corporate social responsibility reporting, regulatory expectations, and public perception. Thus, the strategic choice to utilize professional industrial cleaning can contribute to the company’s brand image, its standing as a responsible employer, and its commitment to environmental stewardship, all of which underpin long-term business value and resilience.
6. Conclusion: The Indispensable Role of Professional Cleaning in Modern Industrial Facilities
The comprehensive cleaning and maintenance of non-production areas within industrial facilities are far more than ancillary services; they are fundamental to operational integrity, employee well-being, regulatory compliance, and overall business success.
As this guide has detailed, the unique challenges posed by industrial environments—ranging from specialized contaminants and sensitive equipment to stringent safety standards and the need for operational continuity—demand a level of expertise, equipment, and procedural rigor that significantly surpasses standard janitorial practices.
Adapting to these demands requires a paradigm shift, viewing cleaning not just through an aesthetic lens but as a critical preventative maintenance and risk management function. Whether addressing the meticulous dust control required in control rooms, the stringent hygiene standards of cafeterias, the robust floor care needed for high-traffic common areas, or the complexities of industrial waste management, a specialized approach is indispensable.
Partnering with professional industrial cleaning services emerges as a strategically sound decision for many facilities. The advantages are compelling and multifaceted:
- Unmatched Expertise and Technology: Professionals bring highly trained personnel, specialized knowledge of industrial contaminants and cleaning methodologies, and access to advanced cleaning technologies and equipment, ensuring tasks are performed effectively and safely.
- Enhanced Safety and Compliance: Their understanding of OSHA, EPA, and other relevant regulations, coupled with rigorous safety protocols and hazardous material handling capabilities, significantly reduces workplace risks and ensures compliance, thereby mitigating potential liabilities and fines.
- Operational and Cost Efficiencies: By preventing equipment damage, reducing accidents and associated downtime, and optimizing the use of resources, professional services contribute to improved operational efficiency and can offer greater long-term cost-effectiveness than attempting to replicate such specialized services in-house.
- Focus on Core Competencies: Outsourcing allows the facility’s staff to concentrate on their primary business functions, enhancing overall productivity and strategic focus.
- Improved Work Environment: A professionally maintained facility boosts employee morale, health, and productivity, contributing to a more positive and efficient organizational culture.
- Sustainability Commitment: Many professional services are adept at implementing green cleaning practices, helping facilities achieve their environmental stewardship goals.
In conclusion, the decision to invest in professional industrial cleaning services for non-production areas is an investment in the facility’s safety, efficiency, compliance, and long-term viability. It allows industrial operations to leverage specialized expertise to manage an essential but non-core function, ensuring that all areas of the facility support the overarching mission in a safe, clean, and optimally maintained state.