The cleanliness of heavy equipment and machinery is a cornerstone of operational integrity, safety, and longevity across numerous industries. Far from being a mere aesthetic concern, a structured approach to cleaning these substantial assets is a critical component of efficient management and regulatory adherence.
This guide provides a comprehensive overview of heavy equipment and machinery cleaning, detailing its importance, the common contaminants encountered, essential cleaning methodologies, industry-specific considerations, and the compelling reasons for engaging professional cleaning services.
Contact us!
Section 1: The Critical Role of Heavy Equipment & Machinery Cleaning
1. Defining Heavy Equipment & Machinery Cleaning: Scope and Purpose
Heavy equipment and machinery cleaning encompasses a range of specialized processes designed to remove accumulated grease, oil, product residue, dirt, and various other contaminants from industrial machinery, production equipment, heavy-duty vehicles (such as forklifts, loaders, and excavators), and other significant assets.
The primary purposes of such cleaning extend beyond superficial appearance; they are fundamentally tied to facilitating maintenance access, enhancing operational efficiency, and ensuring the safety of personnel and the equipment itself (User Query).
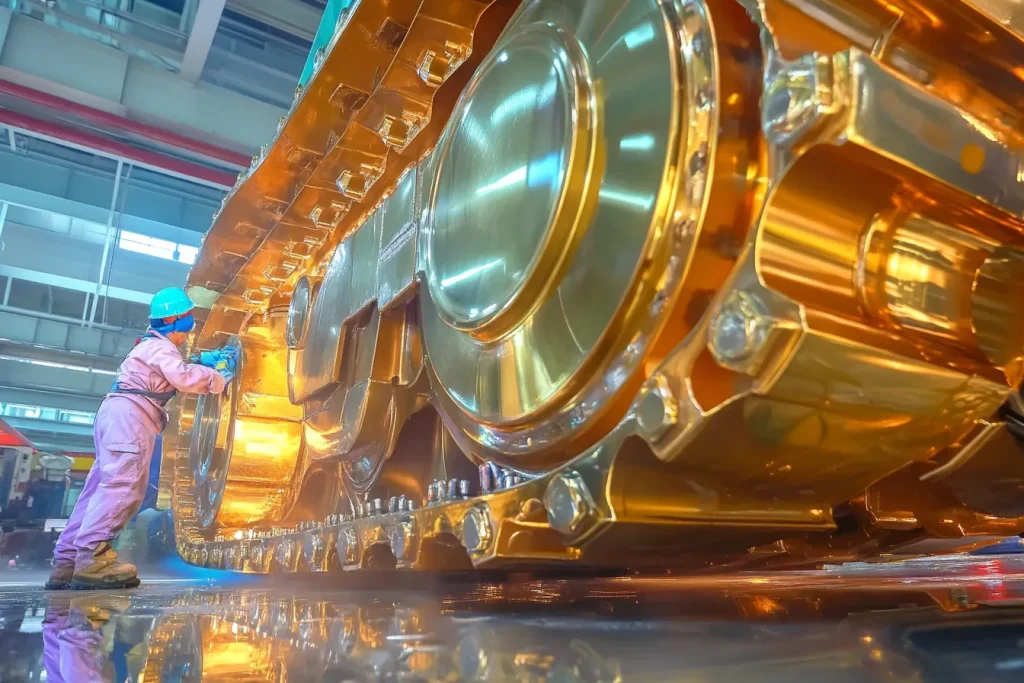
This type of cleaning is far more intricate than a simple rinse or wipe-down with soap and water. It demands specific detergents, specialized cleaning equipment, and a methodical approach to be effective. The strategic importance of this practice cannot be overstated. Rather than being viewed as a routine janitorial task, quality industrial cleaning should be understood as a strategic imperative.
It is an activity that directly contributes to the safety of the workforce, the operational efficiency of the machinery, and compliance with increasingly stringent industry regulations. Indeed, effective industrial cleaning can be an economic powerhouse, directly impacting a company’s bottom line by preserving asset value and optimizing performance. Thus, the decision to implement and maintain a rigorous cleaning regimen is a strategic operational choice that underpins business success and robust risk management.
1. Why Prioritize Cleanliness? The Multifaceted Benefits
The commitment to regular and thorough cleaning of heavy equipment yields a wide array of interconnected benefits that collectively contribute to a more productive, safer, and cost-effective operation.
1.2. Enhancing Operational Efficiency and Performance
Clean machinery inherently operates more smoothly and reliably. The absence of accumulated dirt, dust, or other contaminants minimizes the likelihood of malfunctions, jams, or blockages that can disrupt production schedules. Well-maintained and clean equipment operates with greater efficiency, which directly translates to reduced downtime and heightened productivity.
For example, machines caked in mud and grease tend to retain excessive heat. Regular cleaning ensures that equipment stays cooler, preventing overheating—a common precursor to mid-operation malfunctions and reduced performance. This enhanced thermal regulation is crucial for maintaining optimal operating conditions, especially for machinery subjected to high loads and continuous use.
1.2. Extending Equipment Lifespan and Reducing Downtime
One of the most significant financial advantages of consistent cleaning is the extension of equipment lifespan and the concurrent reduction in unscheduled downtime. Regular cleaning mitigates the risk of damage caused by abrasive contaminants and corrosive substances, thereby prolonging the service life of valuable machinery. Dirty operating conditions are a direct cause of part failures and unexpected breakages, which inevitably lead to lost operational time and expensive repairs.
Furthermore, cleaning prevents the insidious buildup of contaminants around critical systems, such as hydraulic lines and electrical components. This proactive removal of foreign matter safeguards against potential damage, including serious blow-outs of high-pressure oil or dangerous electrical faults. By investing in effective cleaning solutions, businesses can minimize these operational risks, ensuring that their machinery maintains peak performance capabilities for an extended period.
The costs associated with unplanned downtime can be substantial, halting production, delaying project deadlines, and increasing operational expenditures. Regular cleaning is a direct countermeasure to these costly interruptions.
1.2. Ensuring Workplace Safety and Hazard Prevention
Workplace safety is a paramount concern in any industrial setting, and equipment cleanliness plays a vital role in hazard prevention. The process of cleaning dislodges foreign debris—such as rocks, branches, or caked-on mud—that can become slip, trip, and fall hazards for operators and maintenance personnel. Effective washing practices remove objects and accumulations that could lead to injuries from slips, falls, or becoming caught in pinch points that trap kinetic energy.
Well-maintained and clean machinery is inherently safer to operate. Industrial cleaning protocols are designed to prevent common workplace accidents by addressing issues like oil and grease spills, removing potentially hazardous material buildups, and mitigating fire risks associated with combustible dust or residues. For instance, clean steps, grab bars, and handrails on equipment enhance safety by ensuring a solid grip and secure footing for operators entering and exiting cabs. The link between cleanliness and worker well-being is direct and undeniable, contributing to reduced accident rates and lower liability.
1.2. Meeting Regulatory Compliance and Industry Standards
Adherence to regulatory standards is a non-negotiable aspect of modern industrial operations. Industrial cleaning practices are often essential for meeting environmental regulations related to waste disposal and emissions, as well as industry-specific hygiene requirements, particularly in sectors like food processing or pharmaceuticals. Failure to comply with regulations governing heavy machinery cleanliness and maintenance can lead to severe consequences, including substantial fines, damage to a company’s reputation, and, in some cases, operational shutdowns.
Regulatory bodies such as the Occupational Safety and Health Administration (OSHA) and the Environmental Protection Agency (EPA) have established standards that directly or indirectly mandate equipment cleanliness.
For example, OSHA standards may pertain to machine guarding (which is more effective on clean equipment), respirator cleaning procedures for maintenance staff, and the overall maintenance of equipment in hazardous locations. Similarly, EPA regulations strictly govern the handling and disposal of waste generated during cleaning processes, particularly if hazardous materials are involved. Professional cleaning services are typically better equipped to understand and navigate these complex regulatory landscapes, ensuring that cleaning practices meet all legal obligations.
1.2. Improving Inspection Accuracy and Maintenance Access
Cleaning is not merely an ancillary task to maintenance; it is a foundational element of any effective preventative maintenance strategy. A clean machine provides an unobstructed view for inspections, making it significantly easier to identify potential problems such as metal fatigue cracks, signs of oxidization or rusting, and worn or leaking fittings. Once equipment has been thoroughly cleaned, any components that are out of place or require maintenance become much more apparent.
Mechanics and maintenance technicians are considerably more efficient when working on clean machines. The absence of heavy, volatile, or slippery foreign debris makes their work safer and allows for more precise adjustments and repairs. Without a clean surface, inspections are less effective, and underlying issues that could lead to major breakdowns may go undetected. Therefore, regular cleaning facilitates proactive maintenance, allowing for early intervention and the prevention of more serious and costly problems down the line.
1.2. Boosting Company Image and Employee Morale
While often considered ‘softer’ benefits, the impact of a clean operational environment on company image and employee morale is tangible. A clean and well-maintained workspace, including the machinery within it, signals to employees that their health, safety, and well-being are valued by the company. This can lead to a significant boost in morale, reduced absenteeism, and increased overall job satisfaction.
Externally, a fleet of clean and well-maintained heavy equipment contributes positively to a company’s image and reputation. It conveys professionalism, attention to detail, and a commitment to quality and safety, which can be influential factors for clients, partners, and stakeholders.
The diverse benefits of heavy equipment cleaning do not exist in isolation. They are interconnected, creating a synergistic effect where improvements in one area positively influence others. For instance, enhanced operational efficiency due to cleaner machines running cooler can extend the equipment’s lifespan. Similarly, improved workplace safety resulting from fewer slip-and-fall hazards reduces accident-related downtime, which in turn boosts operational efficiency and lowers associated costs.
A safer environment can also contribute to better employee morale, leading to increased productivity. This positive feedback loop means that the cumulative impact of a consistent and proper cleaning regimen is substantially greater than the sum of its individual benefits, reinforcing its strategic importance.
Section 2: Understanding Common Contaminants on Heavy Machinery
Effective cleaning begins with a thorough understanding of the types of contaminants that typically accumulate on heavy equipment and machinery. These substances vary widely in their nature, origin, and the challenges they pose to removal.
2. Identifying the Culprits: A Spectrum of Unwanted Materials
Heavy machinery, by its very nature, operates in environments where it is exposed to a multitude of soiling agents. Common contaminants include:
- Oils, Greases, and Lubricants: These are ubiquitous in mechanical systems and can leak or spill, attracting dirt and forming tenacious films.
- Dust and Dirt: General environmental dust and soil are constant issues, particularly in outdoor settings like construction and agriculture.
- Mud, Rocks, and Branches: Especially prevalent on construction and agricultural equipment, these can cause blockages and abrasion.
- Rust and Scale: Formed by oxidation of metal parts or mineral deposits from water, these can impair function and structural integrity.
- Product Residues: In manufacturing, residues from production processes such as caked-on food products, adhesives, resins, or paint overspray are common.
- Chemical Spills and Residues: Industrial environments may see spills or residues of various chemicals, including acids, alkalis, or solvents.
- Microbial Growth: In certain industries or damp conditions, biofilms and other microbial growth can develop on surfaces.
More specialized industrial pollutants can also settle on machinery, including aerosols, mists (e.g., from halogenated acids, sulfur trioxide), chromic acid from plating operations, entrained liquid droplets from processing tanks (e.g., sulfuric acid, nitric acid), heavy metals (e.g., arsenic, lead, zinc from waste incineration), and various inorganic acid gases (e.g., HCl, SO2, H2S). This wide spectrum of potential contaminants underscores the need for diverse and adaptable cleaning strategies.
2. Challenges Posed by Different Types of Contaminants
The nature of the contaminant dictates the difficulty of its removal and the potential risks it poses. Stubborn contaminants like caked-on grease, dried oil, and compacted dirt can be particularly tough to dislodge and may significantly hinder equipment performance if not addressed. These materials often require specialized cleaning agents and significant mechanical action to break down their adhesion to surfaces.
A recurring challenge is accessing and effectively cleaning intricate machinery components and hard-to-reach areas. Tight spaces, complex geometries, and internal mechanisms often become collection points for dirt and grime, where they can accumulate unnoticed. Contaminants in these inaccessible areas can harbor bacteria, promote corrosion, or impede the smooth operation of moving parts.
Furthermore, certain contaminants present specific hazards. For instance, accumulations of oil or grease can pose significant fire risks, especially in proximity to heat sources or electrical components. Other residues may be corrosive, leading to the degradation of equipment materials over time if not promptly and thoroughly removed.
It is also important to recognize that contaminants rarely exist in isolation on heavy equipment. Dust particles can absorb spilled oil and ambient moisture, forming a tenacious and potentially corrosive sludge that is far more challenging to remove than dry dust alone. Similarly, caked-on materials are often a complex amalgam of various substances—dirt, grease, product spillage, and moisture—that have bonded together and hardened over time.
Cleaning strategies must therefore be capable of addressing these mixtures of contaminants, where the combined properties of the mixture present a more formidable cleaning challenge than any single component would. A simple degreaser, for example, might be insufficient if the grease is heavily mixed with abrasive solids or has chemically reacted with other residues. This complexity in contaminant profiles often necessitates professional assessment to determine the most effective multi-step cleaning approach.
To better understand the diverse challenges, the following table outlines common contaminants, their likely sources, and the primary difficulties they present in cleaning:
Table 1: Common Contaminants, Their Sources, and Primary Cleaning Challenges
Contaminant Type | Likely Sources/Industries | Primary Cleaning Challenges |
---|---|---|
Grease/Oil/Lubricants | All industries with mechanical equipment; engines, hydraulic systems, bearings, gears | Strong adhesion, can attract and bind other dirt, potential flammability, can be difficult to emulsify or dissolve |
Dirt/Mud/Soil | Construction, agriculture, mining, outdoor operations | Abrasive (causing wear), can cake when dry, heavy accumulation, can trap moisture leading to corrosion |
Dust (General & Industrial) | Manufacturing (wood, metal, food), construction, mining, general environment | Fine particles can penetrate small crevices, can be abrasive, combustible dust explosion risk in some industries |
Caked-on Product Residue | Manufacturing (food, chemical, plastics, pharmaceuticals), agriculture (e.g., dried sap) | Can be very hard and adherent, may require specific solvents or mechanical action, potential for chemical reactions |
Rust/Scale (Oxidation/Mineral Deposits) | Equipment exposed to moisture, water systems, boilers, cooling towers, older machinery | Hard, adherent, can weaken underlying material, requires acidic cleaners or strong mechanical action |
Chemical Spills/Residues | Chemical manufacturing, petroleum industry, agriculture (pesticides, fertilizers) | Can be corrosive, toxic, reactive; requires specific neutralization or cleaning agents; safety hazards |
Paint Overspray/Adhesives/Resins | Manufacturing, construction, maintenance activities | Highly adherent, often requires strong solvents or specialized removers, can damage underlying surfaces if improperly removed |
Biofilms/Microbial Growth | Food processing, agriculture (damp areas), water systems, equipment with standing water | Can be difficult to penetrate, sanitization required after removal, potential health hazards |
Soot/Carbon Deposits | Engine exhausts, combustion processes, foundries | Adherent, can be oily, may require strong alkaline cleaners or solvents |
Understanding this spectrum of contaminants and their associated challenges is the first step toward selecting appropriate and effective cleaning methods, which are detailed in the subsequent section.
Section 3: Essential Cleaning Methods for Heavy Equipment & Machinery
A variety of cleaning methods are employed for heavy equipment, each with its own procedures, equipment, suitable applications, and safety and environmental implications. The choice of method depends on the type and extent of contamination, the nature of the equipment and its surfaces, and operational requirements.
3. Degreasing: Tackling Oil and Grease Build-up
Degreasing is a fundamental cleaning process aimed at removing accumulated oils, greases, and similar hydrophobic contaminants from equipment surfaces.
Procedures and Best Practices:
Effective degreasing typically follows a systematic approach:
- Initial Inspection: Before applying any degreaser, inspect the machinery for leaks, damage, or loose connections. Addressing these issues beforehand can prevent complications and ensure the degreasing process is smooth.
- Removal of Loose Debris: Use compressed air, brushes, or manual methods like prying with a spade and steel bar to remove any large, dry chunks of material or loose dirt from the chassis, undercarriage, and other surfaces. This creates a better surface area for the degreaser to act upon the targeted grease and grime.
- Equipment Preparation: Ensure the equipment is cool and any electrical power is turned off. Cover or remove sensitive components that should not come into contact with the degreaser to prevent damage or contamination.
- Degreaser Selection and Dilution: Choose the appropriate type of degreaser based on the contaminant, the surface material, and environmental considerations. If the degreaser is concentrated, dilute it according to the manufacturer’s instructions. For example, a 10:1 dilution ratio means mixing 10 parts water with 1 part degreaser.
- Application: Apply the degreaser solution evenly over the surface using a sprayer or brush, focusing on areas with heavy grease buildup. Ensure all targeted areas, including hard-to-reach places, are covered. Some industrial procedures may involve placing machinery in a contained wash rack with a closed-loop system before detergent application.
- Dwell Time (Soaking): Allow the degreaser to penetrate and work on the contaminants for the recommended time, which can range from a few minutes to half an hour or more for stubborn grease. This dwell time is crucial for the chemicals to break down the bonds of grease and dirt.
- Agitation: For heavily soiled areas or stubborn contaminants, manual agitation with brushes or rags may be necessary to help lift and remove the grime.
- Rinsing: Thoroughly rinse the equipment with water, using a pressure washer or hose, to remove the degreaser and all loosened contaminants. Start from the top and work downwards.
- Drying: Allow the equipment to air dry completely. Compressed air can be used to expedite the drying process, especially for intricate parts.
Types of Degreasers:
A range of degreasing agents is available, each with specific properties:
- Solvent-based Degreasers: These are highly effective at dissolving heavy oils, greases, tars, waxes, adhesives, resins, and paint overspray. They often work quickly and may not require rinsing. However, many traditional solvents can be flammable, emit Volatile Organic Compounds (VOCs), and pose health and environmental hazards if not handled correctly. Examples include petroleum distillates, perchloroethylene, and n-propyl bromide.
- Water-based (Aqueous) Degreasers: These formulations typically contain detergents, surfactants, and alkaline builders (like sodium hydroxide or potassium hydroxide) or chelating agents. They are generally non-flammable, often biodegradable, and safer for workers and the environment than many solvents. They are effective for a wide range of soils but may require more mechanical action or heat. Thorough rinsing and drying are important to prevent residue or potential corrosion on susceptible metals. Many eco-friendly options like Oil Eater® and EnviroGreen fall into this category.
- Enzyme-based Degreasers: These utilize specific enzymes to break down organic soils like fats, oils, and starches. They are typically pH neutral, biodegradable, and very safe for users and surfaces, though they may work more slowly than chemical alternatives.
- Semi-Aqueous Degreasers: These products contain solvents but are dilutable in water, offering a balance between the cleaning power of solvents and the safety profile of water-based solutions.
- Aerosol Degreasers: Packaged in aerosol cans for convenient application, these can be solvent or water-based and are useful for spot cleaning or hard-to-reach areas. Some may have strong chemical compositions requiring careful handling.
- Natural/Citrus-based Degreasers: Utilizing d-Limonene (from citrus rinds) or other plant-derived solvents, these offer strong cleaning power with a more pleasant odor and often better environmental profiles than petroleum-based solvents.
Equipment and Tools for Degreasing:
The equipment for degreasing can range from simple manual tools to more sophisticated systems:
- Manual applicators: Sprayers, brushes, rags, mops.
- Personal Protective Equipment (PPE): Chemical-resistant gloves (nitrile, neoprene), safety goggles or face shields, and potentially respirators for volatile fumes.
- Rinsing equipment: Hoses, pressure washers.
- Containment: For industrial-scale operations, a dedicated wash rack with a closed-loop water recycling system is often used to manage wastewater.
Suitability (Contaminants & Surfaces):
Degreasers are primarily suited for removing organic soils such as oils, greases, lubricants, tar, grime, adhesives, resins, and some types of paint. Alkaline cleaners, often categorized with degreasers, are also effective against rust, scale, and mineral deposits.
Crucially, the chosen degreaser must be compatible with the surface material being cleaned. Some aggressive solvents can damage or dissolve plastics, rubber seals, and certain paint finishes. Water-based alkaline degreasers can be corrosive to aluminum or other soft metals if contact time is prolonged or rinsing is inadequate. Always check manufacturer recommendations and test on an inconspicuous area first.22
Safety and Environmental Notes:
- Safety: Always wear appropriate PPE as specified by the product’s Safety Data Sheet (SDS). Ensure adequate ventilation, especially when using solvent-based or volatile degreasers, to prevent inhalation of harmful fumes. Read product labels and SDS thoroughly before use. Store degreasers in cool, dry, well-ventilated areas, in clearly labeled original containers, and away from incompatible materials or ignition sources.
- Environmental: Opt for biodegradable, low-VOC, and eco-friendly degreasers whenever possible. Never dispose of used degreasers or contaminated rinse water down storm drains or into waterways. Follow local regulations for hazardous waste disposal, which may involve collection by a licensed waste management service. Implement spill prevention and control measures.
The misapplication of degreasers presents a significant, often underestimated, risk. While these agents are powerful cleaning tools, their incorrect use—whether choosing the wrong type for a specific surface material, using an overly concentrated solution, allowing excessive contact time, or failing to rinse thoroughly—can lead to substantial equipment damage.
For instance, aggressive solvents can degrade plastic components, compromise seals and hoses, or strip protective coatings. Similarly, aqueous degreasers, if not properly rinsed and dried, can initiate or accelerate corrosion on vulnerable metal surfaces. This damage might not be immediately apparent but can manifest later as premature component failure, unexpected safety hazards, or the need for costly repairs. This “hidden cost” of improper DIY degreasing underscores the value of professional expertise in selecting and applying these chemical agents correctly.
3. High-Pressure Power Washing: Effective Surface Cleaning
High-pressure power washing utilizes the kinetic energy of water, often combined with detergents, to dislodge and remove dirt, grime, mud, loose paint, and other surface contaminants.
Step-by-Step Guide:
- Establish a Dedicated Wash Area: To comply with environmental regulations and ensure efficient cleaning, set up a designated wash bay. This area should ideally have suitable catch basins and a drainage system to manage contaminated water runoff. Options include permanent concrete wash pads or mobile wash mats with containment features.
- Equipment Preparation: Before washing, detach all removable parts from the machine. This allows for more thorough cleaning of individual components and prevents the spread of dirt to already-cleaned sections.
- Clean Dirtiest Sections First: Begin washing the most heavily soiled areas, typically the undercarriage for heavy equipment, to prevent dislodged dirt from contaminating cleaner sections.
- Systematic Washing: Work methodically, often from top to bottom, to allow gravity to assist in carrying contaminants downwards.
- Detergent Application (if used): Apply appropriate detergents, allowing for necessary dwell time as per manufacturer instructions.
- Rinsing: Thoroughly rinse all surfaces to remove detergent residues and loosened contaminants.
- Drying: Allow all components to air dry completely before reassembling the equipment. Compressed air can be used to speed up this process.
- Consistent Routine: Establish a regular cleaning schedule based on equipment usage and operating conditions to prevent excessive buildup.
Choosing the Right Pressure Washer and Nozzles:
Pressure washers vary widely in power source (electric or gasoline engine), portability (portable or stationary units), water temperature capability (cold water, hot water, or steam), and pressure/flow rates (measured in PSI – pounds per square inch, and GPM – gallons per minute). Hot water pressure washers are generally more effective for breaking down and dissolving grease, oil, and stubborn grime, potentially saving time and water compared to cold water units.
Nozzles are critical as they control the spray pattern and effective pressure. Common types include:
- 0-degree (Red) nozzle: Delivers a concentrated, powerful jet for very tough stains on hard surfaces but can easily cause damage.
- 15-degree (Yellow) nozzle: Used for surface preparation like stripping paint or heavy cleaning.
- 25-degree (Green) nozzle: A common general cleaning nozzle for many surfaces.
- 40-degree (White) nozzle: Provides a wider spray for more delicate surfaces or rinsing.
- Soap (Black) nozzle: A low-pressure nozzle used for applying detergents. It is advisable to start with a wider spray pattern and lower pressure, gradually moving closer or switching to a more focused nozzle if needed, especially on unfamiliar or potentially delicate surfaces.
Detergents and Cleaning Agents for Power Washing:
While water pressure alone can be effective, detergents significantly enhance the cleaning power, especially for specific contaminants:
- General Equipment Cleaning Soaps: Formulated to break down common grease, oils, and grime.
- Acidic Pre-soaks/Aluminum Brighteners: Used for removing oxidation, mineral residues, and brightening aluminum surfaces.
- High pH (Alkaline) Detergents: Often used to neutralize acidic pre-soaks and clean general buildup.
- Degreasers: For heavy accumulations of grease, fuel spills, and oils.
- Concrete and Cement Cleaners: Specialized for removing paving materials, lime, fly ash, rust, and water scale from equipment used in construction.
- Multipurpose Cleaners and Rust Removers: Available for various applications. Many suppliers offer a wide range of specialized detergents, such as tar removers, vinyl restoration detergents, and heavy-duty degreasers.
Surface Suitability and Potential Risks:
High-pressure power washing is highly effective for durable surfaces like concrete, brick, and robust steel components. However, extreme caution is necessary with other materials:
- Wood (e.g., decks, some equipment parts): Can splinter, etch, or have paint/stain stripped if pressure is too high or the nozzle is too close.
- Stucco: Can be pressure washed but requires a gentle approach to avoid chipping or etching; soft washing is often preferred.
- Asphalt Shingles: Pressure washing is generally not recommended as it can dislodge granules and damage the roofing material.
- Painted Surfaces: High pressure can strip paint. Test in an inconspicuous area first.
- Vehicles/Equipment Cabs: Can be safe if done correctly with a wide spray pattern and maintaining a safe distance to avoid damaging paint, seals, or causing dents. Avoid spraying directly at windows or sensitive electronics.
- Delicate Components: Bearings, seals, electrical connections, and sensitive sensors can be damaged by direct high-pressure water ingress.
The force generated by pressure washers, particularly heavy-duty models, should not be underestimated. Such units have the power to strip paint from metal and even break concrete. Water pressure exceeding 2,000 PSI requires careful handling, and at levels around 4,000 PSI, the jet can cause severe physical injury, including eye damage.
This underscores that the kinetic energy involved is far greater than what many non-professionals might perceive from a “stronger hose.” Consequently, the risk of both personal injury (from direct impact, ricocheting debris, or slips on wet surfaces) and equipment damage (to sensitive components, seals, wiring, or paint if not properly shielded or if incorrect techniques are used) is significantly higher than with manual cleaning methods. This highlights the necessity for proper training, appropriate PPE, and a thorough understanding of the equipment’s capabilities and limitations.
Safety Gear and Operational Precautions:
Operating a pressure washer requires strict adherence to safety protocols:
- Read the Manual: Familiarize yourself with the specific machine’s operation and safety features.
- Wear Appropriate PPE: This includes ear protection (due to noise), safety goggles or a full face shield (especially at higher PSIs), waterproof safety boots with good traction, full-length coveralls or heavy-duty raincoat (to protect from splashes and debris), and chemical-resistant gloves if detergents are used.
- Safe Handling: Brace for the initial recoil when starting. Never point the spray wand at any person or animal. Keep hands and feet away from the nozzle.
- Operational Awareness: Never operate a pressure washer while standing on a ladder or unstable surface. Be aware of your surroundings, including other personnel, vehicles, and potential hazards like electrical lines or fragile objects.
- Equipment Safety Features: Use the safety latch on the trigger gun when not actively spraying. Relieve any residual pressure from the system after use.
- Electrical Safety (for electric models): Ensure the unit is plugged into a Ground Fault Circuit Interrupter (GFCI) outlet. Do not operate in excessively wet conditions or standing water. Avoid spraying water directly onto electrical components or connections.
Environmental Compliance: Water Runoff and Containment:
Environmental regulations are a critical consideration for pressure washing operations:
- Dedicated Wash Bays: As mentioned, using a designated wash bay with proper drainage and catch basins is often a legal requirement to prevent contaminated water from entering storm drains or natural water bodies.
- Contaminant Control: Wash water can contain fuels, oils, grease, heavy metals, solvents, and other pollutants. Discharging such contaminated water is typically prohibited.
- Water Treatment Systems: Contained wash water may need to be processed through a water treatment system to remove harmful substances before reuse or compliant disposal.
- Eco-Friendly Detergents: When detergents are necessary, opt for biodegradable and environmentally friendly formulations where possible to minimize the impact of the cleaning solution itself.
3. Ultra-High-Pressure (UHP) Water Blasting: For the Toughest Contaminants
Ultra-High-Pressure (UHP) water blasting is an advanced cleaning and surface preparation technique that employs water propelled at extremely high velocities, typically ranging from 20,000 PSI up to 40,000 PSI (approximately 1380 to 2760 bar) or even higher in some specialized applications. The immense energy generated by these water jets exceeds the bonding energy of even the most adherent scales, coatings, or process contamination, effectively stripping them from the substrate.
Principles and Applications of UHP Water Blasting:
UHP water blasting is utilized for a variety of demanding industrial tasks where conventional cleaning methods are insufficient. Key applications include:
- Surface Preparation: Removing old paint, rust, mill scale, and other surface contaminants from steel and concrete surfaces to prepare them for new coatings. It can achieve various NACE/SSPC waterjetting standards (e.g., WJ-1 to WJ-4), leaving a clean, profiled surface ideal for coating adhesion.
- Industrial Equipment Cleaning: Cleaning heat exchangers, tanks, vessels, reactors, pipes, and other process equipment to remove fouling, product buildup, and stubborn deposits.
- Concrete Demolition/Removal: Precisely removing deteriorated concrete without damaging underlying rebar or sound concrete.
- Marine Applications: Cleaning ship hulls, offshore platforms, and heliports to remove marine growth, corrosion, and old coatings.
- Specialized Removal: Eradicating road markings, runway rubber deposits, and graffiti.
Equipment and Technology:
The equipment used for UHP water blasting is highly specialized and robust:
- Pumps: Powerful triplex or quinplex (five-piston) positive displacement pumps are used to generate the ultra-high pressures.
- Hoses and Lances: Specially designed high-pressure hoses, rated to withstand pressures significantly exceeding operational levels (e.g., bursting strength 2.5 times maximum operating capacity), are used to convey the water. Lances or guns, often with various nozzle configurations, direct the water jet.
- Nozzles: Precision-engineered nozzles (e.g., fan jet, rotating, straight jet) are critical for controlling the water stream and maximizing cleaning efficiency for specific applications.
- Automated and Robotic Systems: To enhance safety and efficiency, automated or robotic tools are increasingly employed. These can include robotic crawlers for vertical or overhead surfaces, remotely operated lances, and systems with vacuum recovery to collect spent water and debris.
Suitability: Removing Stubborn Coatings, Rust, and Scale:
UHP water blasting excels at removing extremely tenacious materials:
- Coatings: Effectively strips thick, durable, and abrasion-resistant coatings such as coal-tar epoxies, polyurethanes, chlorinated rubber, and glass flake coatings.
- Rust and Corrosion: Removes heavy rust and corrosion products, even from deep within the pits of a surface profile, without using abrasives that could cause further corrosion.
- Scale and Deposits: Clears hard scale, chemical residues, resins, and other industrial buildups from various surfaces, including steel, concrete, polymers, wood, copper, and aluminum (pressure must be adjusted according to material sensitivity).
- Contaminants: It is effective for removing a wide range of industrial contaminants, leaving surfaces exceptionally clean.
Despite the “blasting” terminology which might suggest a crude application of force, UHP water blasting, when executed by trained professionals with appropriate equipment, can be a remarkably precise method. The ability to adjust pressure, flow rate, nozzle type, and standoff distance allows for targeted cleaning, removing unwanted materials without causing collateral damage to the underlying substrate or surrounding materials. This precision is a key differentiator from less controlled or more abrasive cleaning techniques, making it a “surgical tool” for surface restoration rather than a blunt instrument.
Extreme Safety Measures and Operator Training:
The immense power of UHP water jets (up to 40,000 PSI or more) makes this method inherently hazardous if not managed with extreme caution. Safety is the paramount concern:
- Operator Training: Extensive training and certification for operators are mandatory. They must understand the equipment, hazards, emergency procedures, and safe operating practices.
- Personal Protective Equipment (PPE): Specialized PPE is required, often including water-resistant suits, metatarsal guards, face shields, helmets, and hearing protection. The specific PPE depends on the pressure and application.
- Restricted Access Zones: Clearly demarcated work zones with restricted access are essential to protect other personnel from direct spray or flying debris.
- Equipment Safeguards: Use of dead-man switches, lance safety shrouds, and regular equipment inspection and maintenance are critical.
- Robotics: The increasing use of robotic and automated UHP systems significantly enhances safety by removing the operator from direct proximity to the high-pressure jet. This is particularly beneficial for hazardous environments or difficult-to-access locations.
Environmental Benefits: Chemical-Free Cleaning:
One of the significant advantages of UHP water blasting is its environmental profile:
- Chemical-Free: In most applications, UHP water blasting uses only pure water, eliminating the need for harsh chemical cleaners, solvents, or detergents. This reduces the risk of chemical exposure for workers and environmental contamination.
- No Abrasives: Unlike abrasive blasting (e.g., sandblasting), UHP water blasting does not introduce grit or other abrasive media into the environment, thus avoiding the creation of dust clouds and the need to dispose of contaminated abrasives.
- Reduced Waste Volume: The primary waste stream is water and the removed contaminants. With vacuum recovery systems, this waste can be contained, and in some cases, the water can be filtered and reused, further minimizing environmental impact. This results in significantly less waste to be disposed of compared to methods like abrasive blasting.
- No Dust or Emissions: The process itself produces no dust or harmful airborne emissions, making it safer for air quality and approved for use in some explosion-proof environments (when appropriate precautions are taken regarding the equipment itself).
Due to its power, specialization, and inherent hazards, UHP water blasting is exclusively a professional service requiring highly trained personnel and sophisticated equipment.
3. Steam Cleaning: Sanitization and Degreasing with Heat
Steam cleaning is a versatile method that utilizes the thermal energy of high-temperature steam, typically at lower pressures than power washing, to clean, degrease, and sanitize surfaces.
How Steam Cleaning Works for Industrial Equipment:
Commercial steam cleaners generate steam at temperatures often ranging from 300°F to 350°F (approximately 149°C to 177°C) or even higher, with operating pressures typically between 100 and 400 PSI. The process works on several principles:
- Thermal Action: The high temperature of the steam effectively melts and loosens grease, oil, grime, and other heat-sensitive soils.
- Moisture and Agitation: The moisture in the steam helps to lift and carry away contaminants. When combined with attachments like brushes, it provides mechanical agitation.
- Sanitization: The high temperatures are lethal to most bacteria, viruses, mold spores, allergens, and even insects and their larvae, providing a significant sanitizing effect without the need for chemical disinfectants. “Dry vapor” steam, which has very low moisture content, is particularly effective as it dissolves oils and sanitizes without leaving excessive wetness.
Procedures for Effective Steam Cleaning:
- Preparation: Clear the work area of obstacles and fragile items. For the surface to be cleaned, remove loose dirt and debris by sweeping or vacuuming.
- Water Fill: Fill the steam cleaner’s boiler or water tank, preferably with distilled or demineralized water to prevent scale buildup within the machine and ensure optimal performance.
- Attachment Selection: Choose the appropriate accessory (e.g., nozzles, detail brushes, floor brushes, upholstery tools) for the surface and type of cleaning required.
- Pressure Adjustment (if applicable): If the steam cleaner allows, start with a lower steam pressure setting, especially for delicate surfaces. Always test the steam on a small, inconspicuous area first.
- Steaming Technique: Hold the nozzle or attachment close to the surface, but generally without direct contact unless using a brush. Move it slowly and steadily across the area, allowing the steam to penetrate and act on the contaminants. For stubborn stains, gentle scrubbing with an attached brush while steaming can be effective. Avoid lingering too long in one spot to prevent potential heat or moisture damage.
- Wiping/Extraction: Depending on the surface and soil load, loosened dirt may need to be wiped away with a microfiber cloth or extracted using a steam vacuum attachment.
- Drying and Ventilation: After steaming, allow surfaces to dry thoroughly. Proper ventilation (e.g., open windows, fans) can expedite drying.
- Post-Cleaning Care: After use, empty and clean the steam cleaner’s water tank, descale if necessary, clean attachments, and store the unit properly.
Types of Steam Cleaners and Attachments:
- Commercial Steam Cleaners: These are more robust and powerful than residential units, designed for frequent, heavy-duty use. They typically achieve higher temperatures and pressures for more effective cleaning and sanitization.
- Steam Vacuums: These units combine steam cleaning with a vacuum function to extract loosened dirt and excess moisture simultaneously, leaving surfaces cleaner and drier.
- Power Source: Steam cleaners can be electrically heated, or heated by oil, natural gas, or LP gas for larger industrial units.
- Portability: Both portable and stationary models are available.
- Dry Steam Generators: Produce steam with very low moisture content, ideal for sensitive electronics or areas where minimal moisture is desired.
- Attachments: A wide array of attachments enhances versatility, including various nozzles for concentrated steam, brushes of different sizes and stiffness for scrubbing, extensions for reach, floor tools, and upholstery tools.
Suitability for Sensitive Surfaces and Contaminants (Grease, Biofilms):
Steam cleaning is highly effective for a broad range of contaminants and surfaces:
- Contaminants: Excellent for removing grease, oil, grime, food waste, wax, biofilms, and for killing bacteria, viruses, mold, mildew, dust mites, and insects/larvae.
- Surfaces: Suitable for many hard, non-porous surfaces like stainless steel, sealed tile and grout, glass, and some plastics (e.g., polypropylene). It can be used on industrial equipment, machinery, engine compartments, transmissions, vats, barrels, tanks, air vents, and even some upholstery and carpets with the correct attachments and techniques.
- Sensitive Areas: The lower pressure and controlled moisture (especially with dry vapor steam) make it suitable for cleaning sensitive areas that might be damaged by high-pressure water or harsh chemicals, such as around electrical components (with extreme caution and proper procedures), engine compartments, and delicate machinery parts.
- Caution: Care must be taken with heat-sensitive surfaces like some plastics, unsealed wood, and delicate fabrics. Always test on an inconspicuous area first.
A key strength of steam cleaning lies in its dual capability: it not only physically removes visible dirt, grease, and grime but also provides significant sanitization due to the high temperatures involved, effectively killing a broad spectrum of microorganisms like bacteria, viruses, and allergens. Studies have shown substantial microbial reduction with even brief exposure to superheated steam. This dual power makes steam cleaning particularly valuable in industries with stringent hygiene requirements, such as food processing or agriculture where preventing biosecurity issues is crucial. This combined cleaning and microbial control can reduce or even eliminate the need for separate chemical disinfection steps, thereby saving time, reducing chemical usage, and minimizing potential chemical residues.
Safety Protocols for High-Temperature Operations:
The primary hazard associated with steam cleaning is the risk of burns from the high-temperature steam or hot surfaces of the equipment.44
- PPE: Wear appropriate personal protective equipment, which typically includes heat-resistant gloves and eye protection. Depending on the application, other PPE might be necessary.
- Awareness and Safe Distance: Ensure all personnel in the vicinity are aware of the cleaning operation and maintain a safe distance.
- Proper Handling: Never direct steam towards people or animals. Handle attachments carefully as they can become very hot.
- Ventilation: Ensure good ventilation in enclosed spaces to dissipate steam and prevent excessive humidity buildup.
- Equipment Knowledge: Thoroughly read and understand the user manual before operating any steam cleaner.
Environmental Advantages:
Steam cleaning offers several environmental benefits:
- Reduced Chemical Use: It cleans and sanitizes effectively using primarily water (steam), significantly reducing or eliminating the need for harsh chemical cleaners, detergents, or disinfectants. This minimizes chemical runoff and worker exposure.
- Water Conservation: Steam cleaners generally use less water than traditional high-volume washing methods like pressure washing, making them a more water-efficient option.
- No Harmful Residues: Since chemicals are often not used, there are no harmful chemical residues left on cleaned surfaces, which is important for food contact surfaces or sensitive environments.
3. Chemical Cleaning: Targeted Solutions for Specific Residues
Chemical cleaning involves the use of specialized chemical agents to dissolve, react with, or dislodge specific types of contaminants that are difficult to remove by mechanical or thermal means alone.
Overview of Chemical Cleaning Processes:
Chemical cleaning is a broad category encompassing various techniques tailored to the contaminant and the equipment being cleaned. The general process involves:
- Initial Inspection and Assessment: Identifying the type of residue, the substrate material, and the extent of contamination to select the appropriate chemical and method.
- Pre-cleaning: Removing loose debris mechanically or with a water rinse, if appropriate.
- Chemical Application: Applying the chosen chemical agent using methods such as immersion, spraying, foaming, flushing, or circulation.
- Dwell Time/Reaction Time: Allowing sufficient contact time for the chemical to work on the contaminant. Agitation or temperature control may be used to enhance the process.
- Rinsing/Neutralization: Thoroughly rinsing the surface to remove the chemical agent and loosened contaminants. In some cases, a neutralizing agent may be required after using strong acids or alkalis.
- Waste Management: Proper collection, treatment, and disposal of spent chemical solutions and contaminated rinse water.
Types of Chemical Cleaning Agents:
A wide array of chemical agents is used, categorized by their chemical nature and primary action:
- Degreasers/Solvent Cleaners: As detailed in Section 3.1, these are used for oils, greases, fats, waxes, adhesives, and some paints. Solvents (e.g., petroleum distillates, alcohols, ketones, chlorinated solvents) dissolve organic contaminants.
- Alkaline Cleaners: Formulations containing alkaline substances like sodium hydroxide (caustic soda), potassium hydroxide, or sodium carbonate. They are effective for removing heavy organic soils (fats, oils, proteins), carbon deposits, some paints, and can saponify fats. Often used in heavy-duty degreasing and for cleaning food processing equipment. Many are biodegradable.
- Acidic Cleaners: Contain acids such as phosphoric acid, hydrochloric acid, citric acid, or sulfamic acid. They are used to remove inorganic deposits like mineral scale (calcium carbonate, lime), rust (iron oxide), hard water stains, and cement residues. Highly corrosive and require careful handling and material compatibility checks.
- Detergents (Surfactants): These are surface-active agents that reduce surface tension, allowing water to wet surfaces more effectively. They help lift, emulsify (for oils/greases), and suspend dirt particles, preventing redeposition. Often incorporated into alkaline or neutral cleaning formulations.
- Disinfectants and Sanitizers: Chemicals like quaternary ammonium compounds, chlorine-releasing agents (e.g., bleach), peracetic acid, or alcohol-based solutions used to kill or inhibit the growth of microorganisms on surfaces. Essential in food processing, healthcare, and other hygiene-sensitive industries.
- Descalers: Typically acidic formulations specifically designed to remove scale buildup from boilers, heat exchangers, pipes, and other water-handling equipment.
- Chelating Agents: Chemicals that bind metal ions, preventing them from interfering with cleaning agents or forming scale. Often added to detergents to improve performance in hard water.
- Specialty Cleaners: Formulated for very specific applications or contaminants, such as NORM (Naturally Occurring Radioactive Material) decontamination chemicals in the petroleum industry , or specialized mold cleaners for manufacturing.
Matching Chemicals to Contaminants and Machinery Surfaces:
This is one of the most critical aspects of chemical cleaning. Incorrect selection can lead to ineffective cleaning or, worse, damage to the equipment.
- Contaminant Type: Organic soils (grease, oil) generally require alkaline cleaners or solvents. Inorganic soils (scale, rust) typically need acidic cleaners.
- Surface Material:
- Metals: Ferrous metals (steel, iron) can be attacked by strong acids if not properly inhibited. Aluminum, zinc, and other soft metals are susceptible to damage from strong alkalis and some acids. Stainless steel is generally resistant but can be pitted by chlorides.
- Plastics and Rubbers: Many organic solvents can swell, soften, or dissolve certain plastics and rubbers. Compatibility must be verified.
- Painted Surfaces: Harsh solvents or strong alkalis/acids can strip or dull paint.
- Manufacturer Recommendations: Always consult the equipment manufacturer’s guidelines for cleaning recommendations and approved chemicals.
- Testing: Test the chosen chemical on a small, inconspicuous area of the surface first to ensure compatibility and effectiveness.
Application Methods:
The method of application depends on the chemical, the equipment, and the scale of the operation:
- Immersion (Soaking): Suitable for smaller parts or components that can be submerged in a tank containing the cleaning solution.
- Spraying: Applying the chemical solution using manual spray bottles, pump sprayers, or automated spray systems. Common for larger surfaces.
- Foaming: Applying the chemical as a foam, which clings to vertical surfaces, increasing contact time and reducing runoff.
- Wiping/Brushing: Manual application for targeted areas or when mechanical action is needed.
- Circulation (Clean-In-Place – CIP): For internal cleaning of pipes, tanks, and enclosed systems, where the cleaning solution is circulated through the equipment. Common in food, beverage, and pharmaceutical industries.
- Chemical Injection: Used for pipelines, where chemicals are injected into the product flow or a dedicated cleaning stream.
Critical Safety: Handling, PPE, and Ventilation:
Chemical cleaning inherently involves risks due to the nature of the agents used. Strict safety protocols are non-negotiable:
- Hazard Identification: Understand the specific hazards of each chemical by thoroughly reading the Safety Data Sheet (SDS) provided by the manufacturer. The SDS details health effects, flammability, reactivity, PPE requirements, and emergency procedures.
- Personal Protective Equipment (PPE): This is mandatory and varies with the chemical. Typically includes chemical-resistant gloves (e.g., nitrile, neoprene, butyl rubber, viton – chosen based on the specific chemical), safety goggles and/or face shields, chemical-resistant aprons or coveralls, and respiratory protection (e.g., respirators with appropriate cartridges for vapors/gases, or supplied-air respirators) if ventilation is insufficient or highly toxic substances are used.
- Ventilation: Ensure adequate ventilation (e.g., open doors/windows, local exhaust ventilation, fume hoods) to prevent the buildup of hazardous vapors or fumes, especially when using volatile solvents or chemicals that off-gas.
- Chemical Handling:
- No Mixing: Never mix different cleaning chemicals unless specifically instructed by the manufacturer and fully understanding the reaction. Mixing incompatible chemicals (e.g., bleach and ammonia, or bleach and acids) can produce highly toxic gases or even cause explosions.
- Dilution: Always add concentrated chemicals (especially acids) to water, not water to chemicals, to prevent splashing and uncontrolled reactions. Follow exact dilution ratios.
- Storage: Store chemicals in their original, clearly labeled containers in a cool, dry, well-ventilated area, segregated from incompatible materials, and secured against unauthorized access.
- Emergency Preparedness: Have emergency eyewash stations and safety showers readily accessible. Ensure personnel are trained in first aid procedures for chemical exposure and spill response.
- Training: All personnel handling or working near industrial cleaning chemicals must receive comprehensive training on their hazards, safe handling procedures, PPE use, and emergency response.
Waste Disposal and Environmental Regulations:
The disposal of spent chemical cleaning solutions and contaminated rinse water is heavily regulated:
- Hazardous Waste: Many cleaning chemicals and the contaminants they remove may classify the resulting waste as hazardous under EPA’s Resource Conservation and Recovery Act (RCRA) or local regulations. This requires specific labeling, storage, transportation by licensed haulers, and disposal at permitted facilities.
- Neutralization: Strongly acidic or alkaline solutions often require neutralization to a safe pH range before discharge or disposal.
- Wastewater Treatment: Contaminated rinse water may need on-site treatment or collection for off-site treatment to remove pollutants before discharge.
- Local Regulations: Always follow local, state, and federal guidelines for waste disposal. Never pour chemical waste down drains or into the environment.
- VOC Emissions: Use of solvents can contribute to air pollution through VOC emissions; select low-VOC or VOC-free options where feasible.
While other methods like power washing and steam cleaning often highlight their “chemical-free” nature as a benefit , chemical cleaning retains a crucial role for specific, challenging scenarios.
The significant safety and environmental complexities associated with chemical agents mean they are generally not a primary, all-purpose cleaning method. Instead, chemical cleaning is best viewed as a specialized technique, a “targeted attack,” employed when other methods are insufficient or when a particular chemical reaction is necessary to break down or remove a highly stubborn or unique contaminant (e.g., complex product residues, certain types of scale, or for NORM decontamination). Its effective and safe use demands a high degree of expertise in chemical selection, application procedures, risk assessment, and compliant waste management.
3. Manual Scrubbing and Wiping: Detail-Oriented Cleaning
Despite advancements in automated and high-power cleaning technologies, manual scrubbing and wiping remain indispensable for achieving thorough cleanliness, especially for detailed work and areas inaccessible to machines.
When Manual Methods Are Necessary or Complementary:
Manual cleaning is often required or preferred in several situations:
- Inaccessible Areas: For cleaning tight places, seams, joints, and intricate components where machines cannot effectively reach.
- Detailing: After primary cleaning with methods like pressure washing or water cannons, manual scrubbing can be used for fine-tuning and ensuring all residues are removed.
- Sensitive Equipment/Surfaces: When a gentler touch is needed to avoid damaging delicate components, painted surfaces, or sensitive electronics (e.g., inside operator cabs).
- Cab Interiors: Operator cabs require manual cleaning, including vacuuming, wiping down controls, consoles, seats, and cleaning windows, as high-pressure methods are unsuitable.
- Pre-cleaning: To remove gross soils or prepare surfaces before automated cleaning or disinfection.
- Small Equipment/Parts: For smaller items that can be collected and cleaned centrally using a multi-tank system.
- Specific Requirements: When equipment needs to be exceptionally clean, for instance, for demonstrations, photoshoots, or critical inspections.
Tools and Equipment:
The tools for manual cleaning are generally straightforward but must be appropriate for the task:
- Brushes: Stiff-bristled (non-wire) brushes of various shapes and sizes for dislodging adhered soil.
- Cloths and Rags: Microfiber cloths are often preferred for their absorbency and ability to trap dirt. Shop rags are also common.
- Sponges and Pads: For wiping and light scrubbing.
- Scrapers: Plastic or metal scrapers (used with caution to avoid surface damage) for removing hardened deposits.
- Buckets: Single, double, or three-bucket systems are used to manage cleaning solutions and rinse water, minimizing cross-contamination.
- Mops: For floor cleaning in and around equipment areas.
- Vacuums: Wet/dry vacuums are useful for removing loose debris and liquids, especially from cab interiors or after upholstery cleaning.
- Heavy-Duty Tools: Spades and steel bars may be used for prying off large, dry, caked-on materials from undercarriages before washing.
- Cleaning Trolleys: To organize and transport supplies efficiently.
Suitable Cleaning Agents for Manual Application:
Cleaning agents for manual application are typically milder than those used in high-intensity automated systems, but compatibility with surfaces and effectiveness against the target soil remain crucial:
- Mild Detergents/Soaps: Neutral pH detergents mixed with water are common for general surface cleaning.
- Specialized Interior Cleaners: Automotive interior cleaners for vinyl, plastic, and leather surfaces in cabs; glass cleaners for windows and screens; upholstery cleaners for seats.
- Degreasers: Mild degreasers or butyl-based cleaners can be applied manually for localized grease and grime, especially on painted surfaces.
- Disinfectants: For sanitizing frequently touched surfaces or in hygiene-critical areas, applied after cleaning.
Techniques for Effective Manual Cleaning:
Systematic techniques enhance the effectiveness of manual cleaning and prevent cross-contamination:
- Directional Cleaning: Proceed from cleaner to dirtier areas, and from high to low surfaces, to prevent spreading contaminants onto already cleaned zones.
- Mechanical Action: Effective cleaning relies on physical scrubbing and friction to dislodge soil.
- Cloth Management: Regularly rotate and unfold cleaning cloths to utilize all clean sides. Change cloths frequently, especially when they become soiled or are no longer saturated with cleaning solution. For higher-risk areas, use a new cloth for each distinct zone (e.g., per patient bed in healthcare, or per distinct machine control panel).
- Avoid Cross-Contamination: Never “double-dip” a soiled cloth back into a clean solution container. Avoid shaking soiled cloths or mops, as this can disperse dust and microorganisms.
- Multi-Tank/Pail Systems (for structured cleaning) :
- 3-Tank System (for small parts):
- Tank 1: Scrape gross soil, then soak in water/detergent to loosen remaining soil.
- Tank 2: Transfer parts and scrub clean in a fresh water/detergent solution.
- Tank 3: Rinse with clean water, then optionally disinfect with hot water (e.g., 77°C for 30 seconds).
- 3-Pail System (for large equipment/surfaces where running water is limited):
- Pail 1: Water for initial pre-rinse/loosening of soil.
- Pail 2: Clean water/detergent solution for active cleaning (apply to surface, then scrub).
- Pail 3: Clean water for final rinsing.
- 3-Tank System (for small parts):
Safety and Ergonomics for Manual Labor:
Manual cleaning, while seemingly low-tech, carries its own set of safety and ergonomic considerations:
- PPE: Always wear appropriate PPE, such as gloves (to protect from chemicals and sharp edges), eye protection (from splashes), and masks if dust or aerosols are generated. Insulated coveralls may be needed if hot water is involved.
- Chemical Safety: If using any cleaning chemicals, even mild ones, understand their hazards (via SDS) and use them correctly.
- Physical Hazards: Be aware of sharp edges, pinch points, and unstable footing when working around machinery.
- Ergonomics: Repetitive motions, awkward postures, and forceful exertions during scrubbing can lead to musculoskeletal injuries. Employ good body mechanics, take breaks, and use tools with ergonomic designs where possible.
- Training: Ensure personnel are trained in the correct cleaning procedures, safe use of any chemicals, and recognition of hazards.
Even in an era of advanced automated cleaning systems, manual methods play an enduring and critical role, particularly in quality control. While pressure washers and UHP blasters are efficient for large-scale soil removal, manual cleaning is often essential for “detailing,” “fine-tuning,” and achieving an “extra clean” standard, especially for inspections or client-facing equipment.
Manual application allows for close visual inspection and tactile feedback that automated systems cannot replicate. This is crucial for identifying missed spots, ensuring thoroughness in critical or complex areas (like control panels or sensitive sensor arrays), and achieving a higher overall standard of cleanliness. Thus, manual cleaning is not just a fallback for areas machines cannot reach; it often serves as a vital final step to ensure a level of precision and completeness that automation alone might not achieve.
3. Removal of Caked-On Materials: Restoring Surfaces
Caked-on materials—such as dried mud, hardened grease, solidified product residues, or thick layers of corrosion—present some of the most significant cleaning challenges for heavy equipment. Their removal often requires a multi-faceted approach combining mechanical force, chemical action, and appropriate techniques.
Strategies for Loosening and Removing Hardened Deposits:
The initial and most crucial step is to loosen the bond between the caked-on material and the equipment surface. This often involves:
- Pre-soaking: Applying water (warm or hot water is often more effective for many residues) or a suitable chemical solution to the affected area and allowing it to penetrate and soften the hardened deposit.
- Dwell Time: For chemical agents (detergents, solvents, degreasers), allowing a sufficient dwell time (e.g., 15-30 minutes or as recommended by the manufacturer) is critical for the chemical to break down the structure of the caked-on material.
- Specialized Equipment: Removal typically requires more than simple rinsing; specific detergents and specialized cleaning equipment are often necessary.
Mechanical Methods (Scraping, Prying):
For thick, dry, or brittle caked-on materials, manual mechanical removal is often the first line of attack:
- Dry Removal First: It is often recommended to manually pry or scrape off large, dry chunks of material from components like the chassis and undercarriage before wetting the surface. This can be done using tools like spades, steel bars, or heavy-duty scrapers. Performing this step dry prevents the material from liquefying and becoming more difficult to handle and contain.
- Targeted Scraping/Brushing: For more localized or adhesive contaminants, careful scraping (using tools appropriate for the surface to avoid damage), brushing with stiff-bristle brushes, and wiping can be effective.
Use of Specialized Cleaners and Solvents:
Chemical action plays a vital role in breaking down the composition of caked-on materials:
- Alkaline Cleaners: Strong alkaline detergents and powders are effective against caked-on grease, oil, some paints, carbon deposits, and rust.
- Acid Descalers: Formulations containing acids like hydrochloric or citric acid are used to dissolve hardened mineral deposits, limescale, and some types of rust.
- Solvent Cleaners: Powerful solvents can break down caked-on resins, inks, gums, cured polyurethane, and other challenging organic residues. Specialized mold cleaners are used in manufacturing to remove solidified product from molds.
- Heavy-Duty Degreasers: Concentrated alkaline or solvent-based degreasers are designed to tackle baked-on or heavily caked grease and oil.
- Combination Products: Some cleaners combine solvents, surfactants, wetting agents, and detergents to attack the molecular structure of the contamination without harming the underlying surface.
Combining Methods for Optimal Results:
Successfully removing caked-on materials rarely relies on a single technique. A systematic, multi-step approach is usually most effective:
- Manual Dry Removal: Pry/scrape off large, loose, or brittle deposits.
- Air Pressure: Use an air gun to blow away any remaining loose debris after dry scraping.
- Initial Wetting/Softening: Spray the machine with a high-volume hose, often using warm or hot water, to dislodge further chunks and begin softening remaining deposits.
- Manual Grease Removal: If significant grease is present, manually pull off chunks or wipe with cloths after initial softening.
- Chemical Application: Apply a suitable detergent, degreaser, or solvent sparingly, focusing on areas with visible contamination. Allow for adequate soaking/dwell time.
- High-Pressure Rinse/Wash: Use a high-volume hose or pressure washer to rinse away the chemical and dislodged material, working from top to bottom.
- Detailing: Use a pressure washer for finer detailing of tighter places if needed. For extremely stubborn or extensive caked-on materials, more intensive methods like steam cleaning (for its thermal and softening effect) or UHP water blasting (for its sheer dislodging power) may be employed by professionals.
The process of removing caked-on material can be likened to an “archaeological dig.” These deposits are often not homogenous but layered, consisting of different substances (e.g., an outer layer of dry mud, followed by a layer of oil-soaked dirt, then perhaps a layer of hardened product residue, and finally underlying rust) that have accumulated and solidified over time.
Effective removal, therefore, is not just about applying maximum force. It requires a strategic, layer-by-layer approach. One might need to physically dislodge the outermost loose layer, then chemically soften or dissolve a more adherent layer, followed by using pressure or thermal methods to remove the next, and so on. This necessitates patience, the correct selection of tools and chemical agents for each specific “layer,” and an understanding of how these different materials interact and adhere to the equipment surface.
Safety and Environmental Care During Removal:
Given the often aggressive methods and potentially hazardous nature of the materials being removed, safety and environmental protection are critical:
- PPE: Comprehensive PPE is mandatory, including full-length coveralls (insulated if hot water is used), protective footwear, face and eye protection (goggles or face shield), and heavy-duty gloves. This protects against flying debris, chemical splashes, sharp edges, and the force of cleaning equipment.
- Waste Disposal: Properly collect and dispose of all removed solid materials (chunks of mud, grease, etc.) according to local regulations.
- Chemical Handling: If chemical cleaners or solvents are used, all standard chemical safety protocols (SDS review, ventilation, correct application, PPE) and hazardous waste disposal procedures must be strictly followed.
- Containment: If pressure washing or significant water volumes are used, ensure proper containment of wash water to prevent environmental contamination, ideally using a closed-loop wash rack system.
The following table provides a comparative overview of the cleaning methods discussed, highlighting their primary actions, typical applications, and key considerations.
Table 2: Comparative Overview of Heavy Equipment Cleaning Methods
Cleaning Method | Primary Action | Key Equipment | Typical Contaminants Targeted | Common Surfaces | Key Safety Concerns | Key Environmental Concerns | Relative Cost (General) |
---|---|---|---|---|---|---|---|
Degreasing | Chemical dissolution/emulsification | Sprayers, brushes, rags, PPE, wash racks | Oils, greases, lubricants, tar, grime, some adhesives/resins | Metals, plastics, painted surfaces (compatibility check needed) | Chemical exposure (skin, eyes, inhalation), flammability (solvents), ventilation needed | Chemical disposal, VOC emissions (solvents), water contamination if not contained | $ – $$ |
High-Pressure Power Washing | Physical force (water impact), often with detergent | Pressure washer (hot/cold), nozzles, detergents, PPE, wash bay | Dirt, mud, grime, loose paint, light grease/oil, biological growth | Concrete, steel, robust painted surfaces; caution on wood, stucco, soft metals, electronics | High-pressure water injuries, flying debris, slips/falls, electrical hazards (electric units) | Water runoff contamination (oils, chemicals, solids), water consumption | $$ |
Ultra-High-Pressure Water Blasting | Extreme physical force (water impact) | UHP pump, specialized hoses/lances/nozzles, robotic systems, extensive PPE | Stubborn coatings (epoxy, polyurethane), heavy rust, thick scale, concrete, tenacious deposits | Steel, concrete; can be adapted for others with pressure control (professional use only) | Extreme water jet injuries, projectile hazards; requires highly specialized training & PPE | Minimal if only water used; waste is water & removed solids; potential for water reuse | $$$ |
Steam Cleaning | Thermal energy, moisture, light pressure | Steam cleaner (electric/fuel-fired), nozzles, brushes, PPE | Grease, oil, biofilms, bacteria, viruses, allergens, light dirt/grime, food residue | Metals, sealed hard surfaces, some plastics, engine parts; caution on heat-sensitive materials | Burn hazards (hot steam/surfaces), moisture control, ventilation | Low water use, reduced chemical need; generally eco-friendly | $$ |
Chemical Cleaning | Chemical reaction/dissolution | Tanks, sprayers, pumps, PPE, ventilation systems | Specific residues: rust, scale, complex organics, NORM, product buildup | Material-specific; requires careful compatibility assessment | High risk of chemical exposure, burns, toxicity, reactivity; requires expert handling & extensive PPE | Hazardous chemical waste generation & disposal, air/water pollution, VOCs | $ – $$$ |
Manual Scrubbing/Wiping | Manual abrasion, chemical action (mild agents) | Brushes, cloths, scrapers, buckets, mops, vacuums, PPE | Light dirt, localized grime, cab interiors, final detailing | All surfaces, especially delicate or complex areas | Ergonomic strain, slips/falls, minor chemical exposure, sharp edges | Minimal with mild/eco-friendly agents; proper disposal of soiled materials | $ |
Caked-on Material Removal | Combination of mechanical, chemical, thermal methods | Spades, scrapers, pressure washers, specialized chemicals, steam cleaners | Hardened mud, solidified grease, thick product residue, heavy corrosion | Robust surfaces primarily; depends on specific methods used | Varies by method; can involve high force, strong chemicals, heat – requires appropriate PPE | Varies by method; waste disposal and water containment are key concerns | −$ |
Section 4: Industry-Specific Heavy Equipment Cleaning Considerations
While the fundamental cleaning methods discussed in Section 3 are broadly applicable, the specific types of heavy equipment, the nature of contaminants encountered, operational demands, and the regulatory environment vary significantly across different industries. Understanding these nuances is crucial for effective and compliant cleaning.
4. Construction (Excavators, Loaders, Cranes, Dozers, etc.)
Heavy equipment in the construction sector operates in arguably some of the harshest environments, constantly exposed to abrasive materials and demanding conditions.
- Key Contaminants: The primary culprits are mud, dirt, concrete splatter, asphalt residues, heavy grease, oil, fuel spills, dried sludge, rocks, and miscellaneous debris like branches.
- Primary Cleaning Focus & Challenges:
- Undercarriage and Tracks: These areas accumulate vast amounts of mud, rocks, and debris, which can impair mobility, accelerate wear on components like rollers and idlers, and add significant weight to the machine. Thorough cleaning often requires manual prying of large chunks followed by powerful washing with pressure washers or water cannons.
- Booms, Buckets, and Attachments: Caked-on materials such as dried concrete or compacted soil can reduce the operational efficiency of these components, affect their balance, and put undue stress on hydraulic systems.
- Hydraulic Systems & Engine Compartments: The ingress of dust, dirt, and moisture into engine compartments and around hydraulic lines can lead to overheating, component failure, and fire hazards. Regular cleaning is essential to prevent these issues.
- Operator Cabs: Maintaining clean windows, mirrors, and camera lenses is critical for operator visibility and safety. Interior cleanliness also contributes to operator comfort and hygiene.
- Environmental Compliance: Managing wash water runoff is a significant challenge. Contaminated water containing oils, grease, and suspended solids must be prevented from entering waterways. This often necessitates the use of designated wash pads with containment and water recycling or treatment systems, especially at fixed sites or larger projects.
- Safety: The sheer size and complexity of construction equipment pose inherent safety risks during cleaning. Workers must be protected from slips and falls caused by dislodged debris or wet surfaces, as well as potential injuries from high-pressure water or contact with moving parts if lockout/tagout procedures are not followed.
- Inspection and Maintenance: Clean equipment allows for easier and more accurate inspection for wear, damage (like cracks or leaks), and the need for maintenance, ultimately contributing to the longevity and reliability of the machinery.
4. Agriculture (Tractors, Harvesters, Sprayers, Implements, etc.)
Agricultural machinery faces unique cleaning challenges related to biosecurity, chemical residues, and the types of organic matter encountered.
- Key Contaminants: Soil, mud, extensive plant matter (stalks, husks, chaff, leaves), seeds, grain dust, manure, residues from pesticides, herbicides, and fertilizers, as well as standard operational fluids like oils, fuels, and lubricants.
- Primary Cleaning Focus & Challenges:
- Biosecurity: This is a paramount concern. Thorough cleaning is essential to prevent the spread of plant diseases, insect pests, and invasive weed seeds from one field or farm to another. Equipment can act as a vector for these biological contaminants.
- Sprayer Decontamination: Agricultural sprayers require meticulous cleaning to remove all traces of chemical residues (pesticides, herbicides) from tanks, pumps, hoses, filters, screens, and nozzles. Carryover of one chemical can damage sensitive non-target crops in subsequent applications or reduce the efficacy of the next product used. Specific cleaning agents or neutralizers are often required, and label instructions for both the chemical product and the cleaning agent must be strictly followed.
- Harvester (Combine) Cleaning: Harvesters accumulate vast amounts of dry, combustible crop residue (chaff, dust) internally and externally. This buildup poses a significant fire hazard and can also interfere with mechanical operations. Comprehensive cleaning, often involving compressed air and detailed manual work, is vital, especially before storage or moving between different crop types.
- Tractors and Implements: Removing caked-on soil, plant debris, and manure from various components is necessary to prevent corrosion, wear, and interference with moving parts.
- Water Management and Access: Cleaning large agricultural machinery can require substantial volumes of water. Access to an adequate water supply, especially for in-field cleaning, can be a challenge. Hot water pressure washers are often recommended for grease and oil but may inhibit some chemical detergents if temperatures are too high.
- Protection of Sensitive Components: Modern agricultural equipment is increasingly equipped with sophisticated electronic sensors, monitors, and control systems. These components can be vulnerable to damage from direct high-pressure water spray or certain cleaning chemicals, necessitating careful cleaning techniques.
- Time and Labor: Thoroughly cleaning large and complex machinery like combines can be extremely time-consuming, sometimes taking hours or even days.
4. Manufacturing (Production Machinery, Conveyors, CNC Machines, Mixers, etc.)
Cleaning in the manufacturing sector is often directly linked to product quality, operational uptime, and worker safety, with specific challenges depending on the industry (e.g., food, pharmaceutical, automotive, metal fabrication).
- Key Contaminants: These are highly varied and include product residues (e.g., food particles, polymers, pigments, metal fines), lubricants, coolants, cutting fluids, hydraulic oils, dust (from raw materials or processes), and general grease and grime.
- Primary Cleaning Focus & Challenges:
- Maintaining Precision and Preventing Defects: For machinery involved in precision manufacturing (e.g., CNC machines, robotics), even small amounts of contamination on critical components can affect accuracy, leading to product defects or tool wear.
- Preventing Product Contamination: This is absolutely critical in industries like food processing, pharmaceuticals, and electronics manufacturing. Cleaning protocols must ensure the removal of all residues, allergens, and microbial contaminants to meet stringent hygiene standards and prevent cross-contamination.
- Minimizing Downtime: Manufacturing facilities often operate on tight schedules. Cleaning activities must be planned and executed efficiently, often during planned maintenance shutdowns, between production runs, or during off-peak hours, to minimize disruption to production.
- Accessing Complex Machinery: Production machinery can be intricate, with many moving parts, enclosed areas, and hard-to-reach spots where contaminants can accumulate. Partial disassembly may be necessary for thorough cleaning.
- Chemical Compatibility and Residue Management: The residues encountered may require specific detergents, solvents, or sanitizers. Ensuring these cleaning agents are compatible with the machinery’s materials of construction (metals, plastics, elastomers) and that no harmful residues are left behind is crucial.
- Automated vs. Manual Cleaning: The choice of cleaning method often depends on the equipment. Some systems may have Clean-In-Place (CIP) capabilities, while others, like dry mixers, coating pans, or large reactors, may require specific semi-automated or manual procedures involving pre-rinsing, detergent soaking with agitation, and post-rinsing.
- Workforce Skill and Training: Operating advanced cleaning equipment and handling specialized cleaning chemicals safely and effectively requires a skilled and well-trained workforce.
4. Logistics & Warehousing (Forklifts, Loaders, Pallet Jacks, Conveyor Systems, etc.)
In logistics and warehousing, the focus of equipment cleaning is primarily on maintaining operational reliability, ensuring a safe working environment, and protecting the goods being handled.
- Key Contaminants: Common contaminants include dust (from storage areas and packaging), dirt tracked in from outside, oil and grease leaks from equipment, battery acid residues (from electric forklifts), tire marks on floors, and debris from transported goods or damaged packaging.
- Primary Cleaning Focus & Challenges:
- Forklift Cleaning (Electric vs. Internal Combustion – IC): This is a key piece of equipment.
- Electric Forklifts: Require very careful cleaning to avoid water damage to sensitive electrical components, batteries, and control systems. Compressed air, careful wiping with non-toxic, biodegradable solutions, and avoiding direct water spray on electrical parts are recommended.
- IC Forklifts: Can generally withstand pressure washing for exterior cleaning, but care should still be taken around engine components and air intakes.
- Maintaining Operator Safety and Visibility: Clean windows, mirrors, lights, and operator controls on forklifts and other vehicles are essential for safe operation. Removing clutter from the operator console prevents distractions.
- Battery Maintenance Areas: For electric forklifts, battery charging stations can accumulate corrosive acid spills and residues, requiring regular neutralization and cleaning to prevent damage and ensure safety.
- Wheels, Undercarriage, and Moving Parts: Debris, strapping, or plastic wrap can become entangled in wheels and axles, affecting maneuverability and causing premature wear. The undercarriage also collects dirt and grime that needs removal.
- Conveyor Systems: Dust, debris, and spilled materials can accumulate on and around conveyor belts, rollers, and drive mechanisms, leading to jams, increased wear, and potential fire hazards if combustible dust is present.
- Warehouse Floor Safety: Leaks from equipment (oil, hydraulic fluid, battery acid) or spills of transported goods can create slip hazards on warehouse floors. Regular floor cleaning and prompt spill response are critical.
- Preventing Damage to Goods: Dirty equipment (e.g., forklift forks with abrasive grit) can potentially damage the goods being handled.
- Forklift Cleaning (Electric vs. Internal Combustion – IC): This is a key piece of equipment.
4. Petroleum (Oil Rigs, Drilling Equipment, Production Machinery, Tanks, Vessels)
The petroleum industry presents some of the most extreme and hazardous heavy equipment cleaning challenges due to the nature of the products handled, the operating environments, and the stringent safety and environmental regulations.
- Key Contaminants: A complex mix including crude oil and its fractions, drilling muds (containing solids, chemicals, and sometimes oil-based components), hydrocarbons (volatile organic compounds like Benzene, Toluene, Ethylbenzene, Xylene – BTEX; and toxic gases like Hydrogen Sulfide – H2S), Naturally Occurring Radioactive Material (NORM) scale, paraffin waxes, asphaltenes, grease, salt buildup from marine environments, and various process chemicals.
- Primary Cleaning Focus & Challenges:
- Hazardous Materials Handling: Many contaminants are flammable, explosive, toxic, corrosive, or radioactive (NORM scale). Cleaning personnel require specialized training and extensive PPE to handle these materials safely.
- Explosion and Fire Prevention: This is a paramount concern. Cleaning methods must be chosen to minimize ignition risks. This often involves the use of explosion-proof pressure washers, non-sparking tools, and rigorous Lockout/Tagout (LOTO) procedures before any work commences on equipment. Atmospheres must be monitored for flammable gases.
- Confined Space Entry: Cleaning the interiors of tanks, vessels, columns, and mud pits often requires entry into permit-required confined spaces. This involves extensive safety protocols, including atmospheric testing, ventilation, rescue plans, and specialized training.
- NORM Decontamination: NORM scale, which can precipitate in pipes, vessels, and pumps handling production fluids, poses a radiation hazard. Its removal requires specialized chemical treatments (e.g., FQE NORM-Clear, often alkaline solutions circulated at specific temperatures and pH levels) and carefully controlled procedures to minimize worker exposure and manage radioactive waste. The presence of residual free oil can compromise the effectiveness of NORM cleaning chemicals by coating the scale and preventing contact.
- Hydrocarbon Residue Removal: Heavy oils, bitumen, asphaltenes, carbon deposits, and paraffin waxes are often very tenacious and difficult to remove. Methods include strong solvents, steam cleaning, specialized chemical treatments (like IN2ERT™ technology, which uses chemical-enriched nitrogen to purge and clean equipment of H2S, VOCs, and heavy hydrocarbons), or non-abrasive methods like dry ice blasting.
- Drilling Mud and Solids Control Equipment Cleaning: Shale shakers, screens, hydrocyclones (desanders, desilters), centrifuges, and mud tanks require regular and thorough cleaning to remove drilled solids and maintain the properties of the drilling fluid, which is crucial for efficient and safe drilling operations.
- Pipeline Cleaning: Internal cleaning of pipelines to remove scale, paraffin, sludge, corrosion products, or biofilm is achieved through methods like mechanical pigging (using foam, steel, or smart pigs), hydro-jetting, chemical cleaning (with acids or alkalis), ice pigging, or steam blowing, depending on the deposit type and pipeline characteristics.
- Tank and Vessel Cleaning: This is a complex operation often involving multiple steps such as bottom flushing, pre-washing, main washing with various mediums (seawater, freshwater, detergents, chemicals like caustic soda), butterworthing (using rotating high-pressure nozzles), steaming, gas-freeing, and verification of cleanliness (visual inspection, wall wash tests). Automated robotic systems and drones are increasingly being used to improve safety and efficiency.
- Environmental Regulations: The petroleum industry is subject to extremely strict environmental regulations regarding the discharge of wastewater and the disposal of contaminated sludge, solids, and hazardous waste. All cleaning operations must comply with these regulations.
A significant challenge in petroleum equipment cleaning is dealing with “invisible threats.” While visible contaminants like crude oil spills and drilling mud are obvious , the industry also contends with less apparent but highly hazardous substances.
These include toxic gases like H2S, flammable and carcinogenic Volatile Organic Compounds (VOCs) such as BTEX , and NORM scale, which emits ionizing radiation. These invisible threats can pose severe acute and chronic health risks to workers and create significant safety hazards, such as the flammability of VOCs. Therefore, cleaning in the petroleum sector is not merely about removing what is seen; it is critically about decontaminating equipment from these unseen dangers.
This requires specialized detection equipment (as no single instrument can detect all types of NORM radiation ), specific chemical neutralizers or suppressants (e.g., for H2S, VOCs, or NORM dissolution ), and highly trained personnel who are acutely aware of these invisible hazards and the protocols to manage them safely. This elevates the need for professional expertise in the petroleum sector far beyond that of many other industries.
The following table summarizes the key cleaning considerations for each of these industries.
Table 3: Industry-Specific Cleaning Focus Areas & Key Challenges
Industry | Common Equipment Types | Key Contaminants | Primary Cleaning Focus | Unique Challenges/Risks |
---|---|---|---|---|
Construction | Excavators, loaders, cranes, dozers, pavers, concrete mixers | Mud, dirt, concrete, asphalt, grease, oil, fuel residue, dried sludge | Undercarriage/tracks, attachments, engine/hydraulics, operator cab visibility, preparation for maintenance | Heavy abrasive material buildup, managing large volumes of contaminated wash water, safety around large machinery |
Agriculture | Tractors, harvesters (combines), sprayers, tillers, planters | Soil, plant matter, seeds, manure, pesticides, herbicides, fertilizers, oils | Biosecurity (preventing pest/disease spread), sprayer decontamination (chemical residue removal), harvester fire prevention | Chemical carryover damaging crops, biosecurity breaches, water access in fields, protecting sensitive electronics from water |
Manufacturing | Production lines, CNC machines, mixers, reactors, conveyors, molds | Product residues (food, chemicals, plastics), lubricants, coolants, metal fines, dust, oils | Maintaining precision, preventing product cross-contamination, minimizing downtime, cleaning complex machinery | Diverse machinery types requiring varied protocols, tight cleaning windows, hazardous material handling (specific industries), ensuring sterility (pharma/food) |
Logistics & Warehousing | Forklifts (electric & IC), pallet jacks, loaders, conveyor systems | Dust, dirt, oil/grease leaks, battery acid, tire marks, debris from goods | Forklift operational readiness (esp. electric vs. IC), operator safety/visibility, floor safety, conveyor function | Protecting sensitive electrical components (electric forklifts), battery acid hazards, maintaining clean floors in high-traffic areas |
Petroleum (Oil & Gas) | Drilling rigs, pumps, pipelines, tanks, vessels, separators, heat exchangers | Crude oil, drilling mud, hydrocarbons (H2S, BTEX), NORM scale, paraffin, asphaltenes, salt, process chemicals | Safety (explosion/fire prevention, toxic exposure), NORM decontamination, hydrocarbon removal, confined space entry, solids control | Extreme hazards (flammable, toxic, radioactive materials), high-pressure systems, remote/offshore locations, stringent environmental regulations, specialized waste disposal |
Section 5: The Professional Advantage: Why Expert Heavy Equipment Cleaning is a Smart Investment
While the idea of performing heavy equipment cleaning tasks in-house (Do-It-Yourself – DIY) might initially appear as a way to reduce upfront costs, a more thorough examination reveals a multitude of complexities, inherent hazards, and potential long-term financial burdens. Engaging professional cleaning services specialized in heavy equipment offers substantial advantages in terms of expertise, safety assurance, regulatory compliance, and overall value for money. This section details why entrusting this critical task to experts is often the most prudent and ultimately beneficial approach for any business operating heavy machinery.
5. Navigating the Complexities and Hazards of DIY Cleaning
Attempting to clean heavy equipment without specialized knowledge and equipment can lead to a range of negative outcomes.
Risks of Improper Cleaning:
- Equipment Damage: One of the most significant risks is causing damage to the machinery itself. The use of incorrect cleaning chemicals can lead to corrosion of metal parts, degradation of seals and gaskets, or damage to painted surfaces. Applying excessive pressure during power washing can strip paint, force water into sensitive bearings or electrical components, and damage delicate parts. Improper drying can also lead to moisture retention and subsequent corrosion or electrical faults. Such damage often results in costly repairs, reduced equipment lifespan, and unscheduled downtime.
- Safety Hazards for Staff: Personnel undertaking cleaning tasks without adequate training or PPE are exposed to numerous safety hazards. These include chemical burns or respiratory problems from cleaning agents, injuries from high-pressure water jets, slips and falls on wet or greasy surfaces, ergonomic injuries from strenuous manual scrubbing in awkward positions, and risks associated with operating unfamiliar or improperly maintained cleaning equipment.
- Ineffective Cleaning: Without the right techniques, equipment, or cleaning agents, in-house efforts may fail to remove all contaminants, particularly those in hard-to-reach areas or stubborn, caked-on deposits. This incomplete cleaning means the underlying problems persist, leading to continued operational issues, wear, and potential safety risks.
Challenges of In-House Cleaning:
Beyond the direct risks, managing heavy equipment cleaning in-house presents several operational challenges:
- Lack of Specialized Knowledge & Training: Effectively cleaning diverse types of heavy equipment requires a deep understanding of various contaminants, the chemical properties of different cleaning agents, their compatibility with numerous materials, correct application procedures, and comprehensive safety protocols. This level of specialized knowledge is often lacking in general maintenance staff.
- Investment in Equipment & Supplies: Professional-grade cleaning equipment such as high-PSI pressure washers, industrial steam cleaners, UHP water blasting units, specialized nozzles, foamers, and a full range of appropriate PPE represents a significant capital investment. Additionally, procuring and storing a variety of industrial-strength cleaning chemicals, degreasers, and solvents adds to the ongoing expense. Professionals typically amortize these equipment costs over many jobs, making their per-use cost lower.
- Time Commitment & Operational Disruption: Thorough heavy equipment cleaning is a time-consuming process. Assigning these tasks to in-house staff can divert them from their core operational duties, potentially impacting productivity. Furthermore, if cleaning is not scheduled efficiently or takes longer than anticipated due to lack of expertise, it can lead to extended equipment downtime and operational disruptions.
- Consistency and Thoroughness: Achieving a consistently high standard of cleanliness across all equipment and on every occasion can be difficult with in-house teams who may not be dedicated cleaning professionals or may lack the motivation or detailed training of specialists.
- Waste Disposal Management: The proper and legal disposal of contaminated wash water, chemical residues, and collected solid waste is a complex and often costly responsibility. This includes understanding and complying with EPA and local regulations for hazardous waste, which can be a significant burden for non-specialized businesses.
5. Expertise and Specialized Equipment of Professional Services
Professional industrial cleaning services bring a level of expertise and access to specialized equipment that is typically beyond the reach of most in-house operations. Their personnel are specifically trained in various cleaning methodologies, from chemical cleaning and degreasing to high-pressure washing, UHP water blasting, and steam cleaning. This training includes understanding how to safely and effectively apply these methods to different types of machinery and contaminants.
Professionals utilize industrial-grade, potent cleaning products that are often more effective than consumer-grade alternatives. More importantly, they have the knowledge to select the correct agent for a specific task, minimizing the risk of material damage while maximizing cleaning efficacy. They also possess or have access to advanced cleaning machinery, such as UHP water blasters, large-capacity steam cleaners, automated tank cleaning systems, or robotic cleaning tools, which can perform tasks more efficiently and safely than manual or less powerful methods. This access to high-quality tools and solutions is part of their service, meaning the client benefits without incurring the direct capital expenditure.
5. Ensuring Safety and Regulatory Compliance (OSHA, EPA)
One of the most compelling reasons to hire professional cleaning services is their ability to navigate and ensure compliance with the complex web of safety and environmental regulations. Reputable professional services are well-versed in OSHA standards related to worker safety, such as requirements for machine guarding, respirator use and cleaning, maintenance of equipment in hazardous locations, appropriate PPE, hazard communication (HazCom), and Lockout/Tagout (LOTO) procedures. They implement systematic cleaning protocols that address potential hazards and focus on high-risk areas.
Similarly, professionals understand and adhere to EPA regulations concerning hazardous waste identification, management, transportation, and disposal, following the “cradle-to-grave” responsibility principle. This includes managing universal wastes like certain pesticides or mercury-containing equipment that might be encountered. They are equipped to handle hazardous materials safely and ensure that all waste is disposed of in an environmentally responsible and legally compliant manner, often maintaining the necessary documentation to prove it. This diligence helps businesses avoid potentially severe fines, legal repercussions, and project delays that can arise from non-compliance.
5. Cost-Effectiveness in the Long Run: Beyond the Upfront Price
While the upfront cost of hiring a professional cleaning service might seem higher than performing the task in-house, a long-term cost-benefit analysis often reveals the opposite. Regular, professional cleaning is an investment that contributes to significant long-term cost savings.
The hidden costs of DIY cleaning can accumulate rapidly. These include the ongoing expense of purchasing cleaning supplies and specialized equipment, the cost of equipment maintenance and eventual replacement, the value of employees’ time diverted from their primary roles, and, crucially, the potential costs of repairing equipment damaged by improper cleaning techniques.
Professionals, with their expertise and efficient methods, can often complete cleaning tasks more quickly and thoroughly than in-house staff. This efficiency minimizes equipment downtime. More importantly, by preventing premature wear, corrosion, and component failures through effective contaminant removal, professional cleaning extends the operational lifespan of expensive machinery and reduces the frequency and cost of repairs and replacements. The prevention of costly compliance fines or accident-related expenses further tips the balance in favor of professional services.
5. Achieving Superior Results and Peace of Mind
Ultimately, professional heavy equipment cleaning services deliver a higher standard of cleanliness. Their systematic protocols and expertise ensure that even hidden contaminants and buildup in hard-to-reach areas are effectively removed. This superior level of cleanliness directly contributes to a healthier, safer, and more productive work environment.
Beyond the tangible benefits, engaging experts provides business owners and managers with invaluable peace of mind. Knowing that the cleaning of critical and expensive assets is being handled by trained, insured, and compliant professionals allows management to focus on core business operations. This “risk transfer” is a significant, though often unstated, advantage.
By outsourcing specialized cleaning, a company effectively transfers many of the operational risks associated with the cleaning task itself—safety liabilities, environmental compliance, potential for equipment damage during cleaning—to the service provider. This is particularly valuable in high-hazard industries or when dealing with complex machinery and stringent regulations.
Furthermore, by relieving internal staff of a demanding, non-core task, businesses can better allocate their resources. Management and employee time can be redirected towards primary business functions, strategic goals, and revenue-generating activities, rather than being consumed by the complexities of specialized cleaning, training, and compliance monitoring. In this sense, professional cleaning services act as an enabler, contributing to overall business efficiency and productivity that extends far beyond just the physical cleanliness of the equipment.
Final Thoughts
The comprehensive cleaning of heavy equipment and machinery is an indispensable practice that extends far beyond mere aesthetics. It is a strategic activity that directly impacts operational efficiency, equipment longevity, workplace safety, regulatory compliance, and a company’s overall image and profitability. The array of contaminants encountered is diverse, and the methods required for their effective removal are often complex, demanding specialized knowledge, tools, and adherence to stringent safety and environmental protocols.
While routine, light cleaning by equipment operators plays a role in daily upkeep, the deep, thorough cleaning of these substantial assets presents significant challenges. The potential for equipment damage through incorrect chemical use or excessive force, the safety risks to untrained personnel, the complexities of hazardous waste disposal, and the rigorous demands of OSHA and EPA compliance all underscore the limitations and potential pitfalls of an in-house approach for many organizations.
Entrusting heavy equipment cleaning to dedicated professionals offers a clear advantage. These services bring specialized expertise, industrial-grade equipment, and a commitment to safety and regulatory standards that ensures the job is done correctly and responsibly. By doing so, businesses not only achieve cleaner, more reliable equipment but also safeguard their personnel, protect their financial assets from avoidable damage and fines, and ensure their operations remain efficient and compliant. Ultimately, investing in professional heavy equipment cleaning is an investment in the long-term health and success of the entire operation.