I. Understanding Abatement Services: Protecting Health and Environment
Hazardous materials lurking within residential, commercial, and industrial structures pose significant risks to human health and the environment. Abatement services are specialized processes designed to address these dangers by safely removing, containing, or neutralizing these harmful substances.
This guide provides an in-depth look at abatement services for common regulated materials like lead, asbestos, Polychlorinated Biphenyls (PCBs), and regulated gypsum products, emphasizing the critical procedures and the necessity of professional intervention.
Contact us!
A. What are Hazardous Material Abatement Services?
Abatement, in the context of hazardous materials, refers to the procedures implemented to permanently remove or encapsulate known hazardous substances found in building materials or equipment, thereby making the area safe for occupants and the environment. The Occupational Safety and Health Administration (OSHA) defines a “clean-up operation” as any activity where hazardous substances are removed, contained, incinerated, neutralized, stabilized, cleared-up, or otherwise processed or handled with the ultimate goal of making the site safer for people or the environment.
This definition underscores that abatement is far more than simple cleaning; it is a systematic, goal-oriented process focused on long-term risk mitigation and hazard reduction, dictated by the specific hazardous material and stringent regulatory requirements.
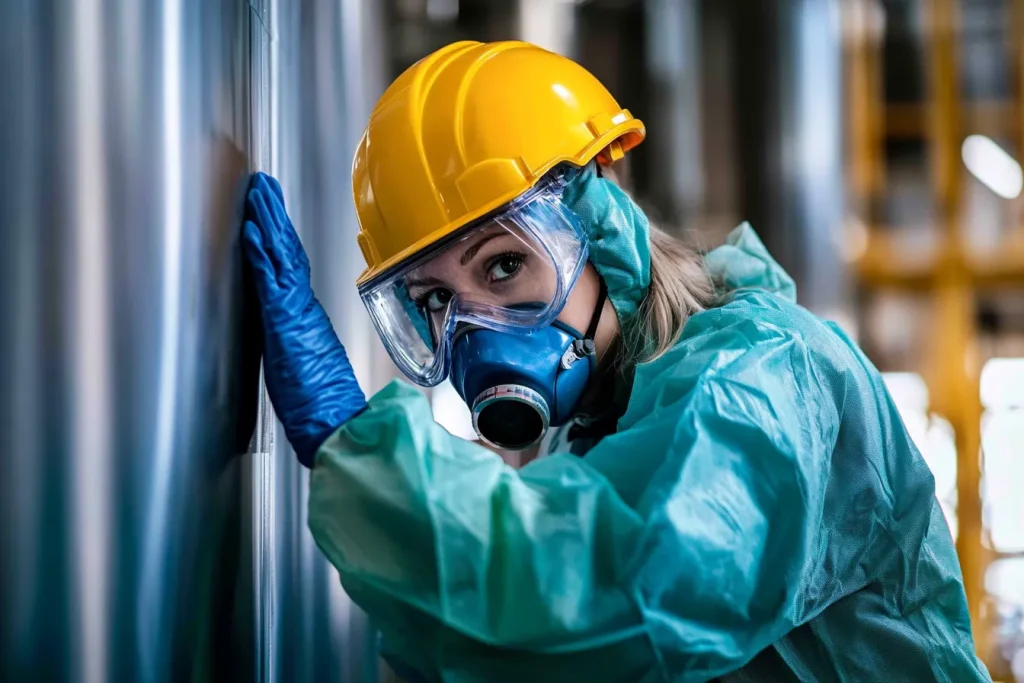
It is important to distinguish “abatement” from “remediation,” terms that are often, yet incorrectly, used interchangeably. Abatement specifically targets the removal or sealing of existing hazardous materials that were typically intentionally incorporated into a structure, such as asbestos insulation or lead-based paint. Remediation, conversely, is a broader process that encompasses abatement but also aims to reverse, stop, or eliminate environmental damage and prevent its recurrence by addressing the source of the problem.
For instance, mold growth due to a persistent moisture issue would require remediation, which includes not only removing the mold (an abatement activity) but also fixing the underlying moisture problem. Understanding this distinction is crucial for property owners to determine the appropriate scope of work necessary to address their specific situation effectively.
Abatement services cover a wide array of hazardous materials, including but not limited to asbestos, lead, PCBs, mold, and biohazards. This guide will specifically focus on the abatement of lead, asbestos, PCBs, and regulated gypsum products, which are commonly encountered in older structures and industrial settings.
B. Why Abatement is Crucial: Health, Safety, and Regulatory Imperatives
The necessity for professional abatement services stems from a confluence of critical factors: the protection of human health, the preservation of environmental safety, and the adherence to legal and regulatory mandates.
Protecting Human Health:
Exposure to hazardous materials such as asbestos, lead, and PCBs can lead to severe and often irreversible health conditions. These include various forms of cancer, debilitating respiratory diseases like asbestosis, significant neurological damage, and adverse developmental effects, particularly in vulnerable populations such as children. Abatement services directly address these grave health risks by methodically removing or containing the hazardous sources. The severity of these health consequences is the primary impetus behind the stringent regulations and meticulous procedures governing abatement work.
Ensuring Environmental Safety:
Beyond the immediate confines of a building or worksite, improper handling of hazardous materials can lead to widespread environmental contamination. Professional abatement practices include the safe containment, removal, and, crucially, the proper disposal of hazardous wastes. This prevents the contamination of soil, water sources, and the air, thereby safeguarding the broader ecosystem. This highlights that the responsibility of abatement extends to ensuring the long-term health of the environment.
Regulatory Compliance:
A complex web of federal, state, and local regulations, primarily enforced by agencies like the Environmental Protection Agency (EPA) and OSHA, governs every aspect of hazardous material management. These regulations dictate how hazardous materials must be identified, handled, removed, and disposed of. Failure to comply with these mandates can result in substantial fines, severe legal liabilities, and mandated work stoppages. The intricate and non-negotiable nature of this legal framework makes professional expertise an indispensable component of any abatement project.
Property Value and Marketability:
From a property owner’s perspective, the presence of known hazardous materials can significantly diminish property value and hinder marketability. Proactively identifying and professionally abating these substances can preserve or even enhance property value, making the property more attractive and safer for potential buyers or tenants. This provides a tangible financial incentive that complements the core health and safety drivers.
The regulatory framework surrounding hazardous materials often pushes for proactive identification, such as pre-renovation inspections for asbestos and lead. This indicates a societal and governmental understanding that preventing exposure through foresight is preferable to merely reacting to contamination after it has occurred.
The detailed regulations from OSHA and the EPA are a testament to the recognized severity of these hazards, necessitating such proactive measures. Furthermore, the imperatives for abatement are deeply interconnected: a failure in proper handling (a health risk) frequently leads to environmental contamination (an environmental risk), which, in turn, can trigger legal and financial penalties (a legal risk). This triangulation of risks underscores the critical importance of executing abatement correctly from the outset, as a failure in one domain often cascades into others.
The following table provides a concise overview of common regulated hazardous materials found in buildings, their typical locations, primary health risks, and key regulatory agencies involved. This serves as a quick reference to help identify potential hazards and understand the concerns associated with them.
Table 1: Overview of Common Regulated Hazardous Materials in Buildings
Hazardous Material | Common Locations in Buildings/Equipment | Primary Health Risks | Key Regulatory Agencies |
---|---|---|---|
Lead | Paint in pre-1978 structures (windows, doors, stairs), dust, soil near older buildings, older plumbing | Neurological damage (especially in children), developmental issues, kidney damage, cardiovascular effects | EPA, OSHA |
Asbestos | Insulation (pipes, boilers), floor tiles, roofing shingles, textured ceilings, cement products | Asbestosis, lung cancer, mesothelioma | EPA, OSHA |
PCBs | Caulk, electrical ballasts (fluorescent lights), paints, sealants in pre-1980 buildings | Probable human carcinogen, immune/reproductive/nervous/endocrine system effects, skin conditions (chloracne) | EPA |
Regulated Gypsum | Drywall/plasterboard (dust may contain crystalline silica; older joint compounds may contain asbestos) | Silicosis (from crystalline silica), lung damage; H₂S gas from improper landfilling | EPA, OSHA (for silica) |
II. In-Depth Focus: Lead Abatement
Lead, a highly toxic metal, was widely used in various building materials for decades before its significant health risks were fully understood and regulated. Lead abatement involves specialized procedures to control and eliminate lead hazards, particularly from lead-based paint, which is a primary source of exposure in older structures.
A. Identifying Lead Hazards: Common Sources and Risks
The most significant source of lead exposure in buildings is lead-based paint. Structures built before 1978 are highly likely to contain lead-based paint, often hidden under multiple layers of newer, non-lead paint. Common locations include windows and window sills, doors and door frames, stairs, railings, banisters, and porches. The 1978 prohibition on the use of lead-based paint in housing is a critical date for identifying potential hazards.
While intact lead-based paint generally does not pose an immediate threat, its deterioration through peeling, chipping, chalking, or cracking creates hazardous lead dust and flakes. These particles can contaminate surfaces, become airborne, and be easily ingested or inhaled. Renovation, repair, or demolition activities in older buildings are major contributors to the generation of lead dust, even if the paint appears to be in good condition prior to disturbance.
Beyond paint, lead can also contaminate soil around older buildings due to flaking exterior paint. Older plumbing systems may contain lead pipes, solder, or fixtures, which can leach lead into drinking water. Certain older consumer products may also contain lead.
Lead exposure poses severe health risks, especially to children, whose developing bodies absorb lead more readily and are more susceptible to its toxic effects. In children, lead can cause irreversible neurological damage, learning disabilities, behavioral problems, and slowed growth. In adults, lead can damage the central nervous system, cardiovascular system, reproductive system, and kidneys.
Acute (short-term) overexposure, though rare in occupational settings, can lead to acute encephalopathy, a severe brain condition resulting in seizures, coma, and potentially death. Chronic (long-term) overexposure can cause cumulative damage to multiple organ systems. OSHA emphasizes that even low blood lead levels (BLLs), previously considered safe, are now known to be associated with adverse health effects in adults, including impaired kidney function and cognitive dysfunction later in life.
B. The Lead Abatement Process: Step-by-Step
A systematic approach is essential for safe and effective lead abatement. The process generally involves the following key steps:
- Identification and Assessment: The first step is to confirm the presence of lead-based paint. This can be done using EPA-recognized lead test kits for initial screening or, more definitively, through an inspection conducted by a certified lead inspector or risk assessor who may use X-ray fluorescence (XRF) analyzers or collect paint chip samples for laboratory analysis.
- Containment Setup: Critical to preventing the spread of lead dust, the work area must be meticulously contained. This involves sealing off the area from the rest of the building using polyethylene sheeting. Doors, windows, and HVAC vents are sealed. Heavy-duty plastic sheeting is used to cover floors and any furniture or objects that cannot be removed. For extensive projects, full enclosures with negative air pressure systems equipped with High-Efficiency Particulate Air (HEPA) filters may be employed to ensure that air flows into the work area, preventing contaminated air from escaping.
- Personal Protective Equipment (PPE): All workers involved in lead abatement must wear appropriate PPE to prevent exposure. This includes NIOSH-approved respirators with HEPA filters, disposable coveralls (often with hoods and booties), gloves, and eye protection.
- Removal and Waste Collection: Lead-based paint can be removed using various methods, including wet scraping or sanding (to minimize dust), chemical stripping, or using specialized tools like vacuum-shrouded power tools or dustless needle guns connected to HEPA vacuums. All lead-contaminated waste, including paint chips, dust, debris, used PPE, and cleaning materials, must be immediately collected and placed into heavy-duty, 6-mil thick plastic bags or leak-proof containers. These containers must be clearly labeled as “Lead-Contaminated Waste”.
- Waste Testing (TCLP): Depending on regulations and the nature of the waste, a Toxicity Characteristic Leaching Procedure (TCLP) test may be required. This test determines if the lead in the waste leaches out at concentrations that would classify it as hazardous waste under RCRA (typically a lead content of 5 mg/L or higher in the leachate). This testing is a critical decision point, as it dictates the disposal pathway and associated costs.
- Transportation and Disposal: If the waste is determined to be hazardous, it must be transported by a licensed hazardous waste hauler to a permitted RCRA treatment, storage, and disposal facility (TSDF). Non-hazardous lead waste may typically be disposed of in an approved construction and demolition (C&D) landfill, though local regulations must always be confirmed. This aligns with the EPA’s “cradle-to-grave” management system for hazardous wastes.
- Thorough Cleanup: After all lead-based paint and debris have been removed, the contained area must be meticulously cleaned. This involves HEPA vacuuming all surfaces, followed by wet washing with a lead-specific detergent or cleaning agent, and another round of HEPA vacuuming (the “HEPA sandwich”). All tools and equipment used in the abatement process must also be decontaminated.
- Documentation: Comprehensive record-keeping is mandatory throughout the lead abatement process. This includes documentation of inspections, testing results, containment procedures, worker training and certification, air monitoring data (if conducted), waste manifests, and disposal receipts.
C. Regulatory Landscape: EPA’s RRP Rule and OSHA Standards
Two primary federal regulations govern lead abatement activities in the United States: EPA’s Renovation, Repair, and Painting (RRP) Rule and OSHA’s Lead Standards.
EPA Renovation, Repair, and Painting (RRP) Rule: This rule, codified at 40 CFR Part 745, Subpart E, is designed to protect the public, particularly children, from lead-based paint hazards created during renovation, repair, or painting activities in target housing (most pre-1978 homes) and child-occupied facilities (e.g., daycares, preschools built before 1978). Key provisions include:
- Certification: Individuals (renovators) performing or directing such work must be trained by an EPA-accredited training provider and become certified. Firms employing these individuals must also be certified by the EPA or an authorized state program.
- Lead-Safe Work Practices: The rule mandates specific work practices to minimize dust generation and contamination. These include proper containment of the work area (covering floors, sealing off doors and vents, using vertical containment for exterior work), careful material removal, and thorough post-renovation cleaning.
- Prohibited Practices: Certain unsafe practices are banned, such as open-flame burning or torching of lead-based paint, using heat guns that operate above 1100∘F, and power sanding, grinding, or planing without HEPA vacuum attachments.
- Cleaning Verification: After cleaning, renovators must perform a cleaning verification procedure to ensure the area is adequately clean, or conduct dust clearance testing by a certified professional. The RRP rule’s applicability extends to homeowners who rent out any portion of their home or engage in “house flipping” (buying, renovating, and selling homes for profit), meaning many individuals who might not consider themselves professional renovators could unknowingly be subject to these stringent requirements. This broadens the rule’s impact and highlights the potential for unintentional non-compliance, underscoring the need for widespread education.
OSHA Lead Standards (29 CFR 1926.62 for Construction): This standard is focused on protecting workers from occupational exposure to lead. Its requirements apply to all construction work where an employee may be exposed to lead, including abatement, renovation, and demolition. Key provisions include:
- Permissible Exposure Limit (PEL): Sets the maximum allowable worker exposure to lead at 50 micrograms per cubic meter of air (50 µg/m3) as an 8-hour time-weighted average (TWA).
- Action Level (AL): An airborne concentration of 30 µg/m3 (8-hour TWA) triggers requirements for exposure monitoring, medical surveillance, and training, even if exposures are below the PEL.
- Exposure Assessment: Employers must determine employee exposure levels.
- Methods of Compliance: Requires implementation of engineering controls (e.g., ventilation, HEPA vacuums) and work practice controls to reduce exposures.
- Respiratory Protection and PPE: Must be provided and used when engineering and work practice controls cannot reduce exposures to below the PEL.
- Hygiene Facilities and Practices: Requires clean change areas, handwashing facilities, and prohibitions on eating, drinking, or smoking in lead-contaminated areas to prevent ingestion.
- Medical Surveillance: A medical surveillance program must be provided for workers exposed at or above the AL for more than 30 days per year.
- Training: Workers must be trained on lead hazards, safe work practices, and OSHA standards. These overlapping jurisdictions of the EPA (protecting public and environment) and OSHA (protecting workers) create a multi-layered regulatory framework. Professionals must navigate both sets of rules, ensuring comprehensive protection.
D. Required Certifications for Lead Professionals
Working with lead-based paint safely and legally requires specific certifications for both individuals and firms.
- EPA RRP Certification: As mandated by the RRP Rule, individual renovators must successfully complete an 8-hour training course from an EPA-accredited training provider. This certification is typically valid for five years and requires an accredited refresher course for renewal before expiration. The firm employing these renovators must also apply to the EPA (or an authorized state) to become an EPA Lead-Safe Certified Firm.
- State-Specific Lead Abatement Licenses: Beyond the EPA’s RRP certification (which focuses on renovation, repair, and painting that disturbs lead paint), many states have more stringent licensing requirements for individuals and firms conducting lead abatement (activities specifically designed to permanently eliminate lead-based paint hazards). For example, the Michigan Lead Abatement Act of 1998 requires state certification for individuals engaged in lead-based paint activities. This often involves:
- Longer initial training courses (e.g., 24 hours for a Lead Abatement Worker, 32 hours for a Lead Abatement Supervisor in Michigan).
- Passing a state-administered third-party certification examination.
- Meeting minimum education and/or experience qualifications.
- Annual maintenance fees and refresher training (e.g., every three years in Michigan) to maintain certification. This dual system means that federal EPA RRP certification is often a baseline, and professionals performing full-scale abatement may need additional, more comprehensive state-level licenses. This adds layers of complexity and underscores the importance of verifying that professionals hold all necessary credentials for the specific type of work being performed in a given locality.
III. In-Depth Focus: Asbestos Abatement
Asbestos, once lauded for its heat resistance, strength, and insulating properties, is now recognized as a potent human carcinogen. Its widespread use in building materials for much of the 20th century means it remains a significant hazard in many older structures. Asbestos abatement is a highly regulated process aimed at controlling exposure to asbestos fibers during removal, encapsulation, or enclosure activities.
A. Understanding Asbestos: Types, Dangers, and Common Materials
Asbestos is a collective term for a group of six naturally occurring fibrous silicate minerals. The three most common types historically used in commercial products are chrysotile (white asbestos), amosite (brown asbestos), and crocidolite (blue asbestos). Chrysotile was the most widely used.
The primary danger of asbestos lies in the inhalation of its microscopic fibers. These fibers, when airborne and breathed in, can become lodged in the lungs and lead to serious, often fatal, diseases that may not manifest for many years (10-40 years or more) after exposure. These diseases include:
- Asbestosis: A chronic, progressive lung disease characterized by scarring of the lung tissue, leading to breathing difficulties and reduced lung function.
- Lung Cancer: Exposure to asbestos fibers significantly increases the risk of developing lung cancer, and this risk is compounded by smoking.
- Mesothelioma: A rare but aggressive cancer that affects the lining of the lungs (pleura) or abdomen (peritoneum), and is almost exclusively linked to asbestos exposure. Critically, there is no known safe level of asbestos exposure; even brief or low-level exposures can contribute to the risk of developing asbestos-related diseases.
Asbestos-Containing Materials (ACMs) were incorporated into thousands of building products, particularly before the 1980s. Common ACMs include :
- Thermal System Insulation (TSI): Insulation on pipes, boilers, tanks, and HVAC ducts.
- Surfacing Materials: Sprayed-on or troweled-on materials like acoustical plaster, decorative textures (e.g., “popcorn” ceilings), and fireproofing.
- Flooring: Vinyl asbestos floor tiles (VAT), vinyl sheet flooring backing, and flooring adhesives (mastic).
- Roofing and Siding: Cement asbestos shingles, siding, and roofing felt.
- Other Products: Cement pipes, wallboard joint compounds (pre-1980s), gaskets, fire doors, and laboratory benchtops. A comprehensive list can be found in sources like the California Department of Public Health factsheet.
A crucial distinction in assessing asbestos risk is whether the ACM is “friable” or “non-friable.”
Friable ACM is material that, when dry, can be crumbled, pulverized, or reduced to powder by hand pressure, allowing asbestos fibers to be easily released into the air. Examples include damaged TSI or loose sprayed-on fireproofing.
Non-friable ACM is more durable and less likely to release fibers unless it is subjected to cutting, sanding, drilling, grinding, or significant damage. Examples include intact vinyl asbestos floor tiles or cement asbestos siding. However, non-friable ACM can become friable if it is disturbed or deteriorates over time. Friability is a key factor in risk assessment and determines the stringency of control measures required during abatement. The EPA’s NESHAP regulation primarily targets friable asbestos.
B. The Asbestos Abatement Process: From Inspection to Disposal
The asbestos abatement process is meticulously planned and executed to prevent fiber release and ensure worker and public safety.
- Inspection and Assessment: Before any disturbance, a thorough inspection by a certified asbestos inspector is required to identify all suspect ACMs. Samples of these materials are taken and analyzed by an accredited laboratory (typically using Polarized Light Microscopy – PLM) to confirm the presence and type of asbestos. The OSHA standard often relies on the concept of “Presumed Asbestos-Containing Material” (PACM) for certain thermal system insulation and surfacing materials installed before 1981, meaning these materials must be treated as asbestos-containing unless proven otherwise through testing. This proactive approach shifts the burden of proof, compelling assessment rather than assumption.
- Classification of Work: OSHA categorizes asbestos-related work into four classes, each with specific requirements based on the potential for fiber release :
- Class I: Activities involving the removal of TSI or surfacing ACM and PACM. This is considered the highest risk work and requires the most stringent controls.
- Class II: Activities involving the removal of other ACMs that are not TSI or surfacing material, such as wallboard, floor tiles, roofing shingles, and mastics.
- Class III: Repair and maintenance operations where ACM (including TSI or surfacing ACM/PACM) is likely to be disturbed.
- Class IV: Maintenance and custodial activities during which employees contact but do not disturb ACM or PACM, and activities to clean up dust, waste, and debris from Class I, II, and III activities.
- Containment and Regulated Areas: For Class I and often Class II work, a regulated area must be established and clearly demarcated with warning signs. Critical barriers (e.g., polyethylene sheeting) are used to seal all openings (doorways, windows, vents) to the work area. A Negative Pressure Enclosure (NPE) is typically required, especially for Class I work. This involves using HEPA-filtered air-moving equipment to create a lower air pressure inside the containment than outside, ensuring that air flows into the work area and preventing asbestos fibers from escaping. For Class I jobs, a multi-chamber decontamination unit (consisting of an equipment room, shower area, and clean change room) must be established adjacent to the regulated area for workers to safely enter and exit. The on-site “competent person,” as mandated by OSHA , plays a vital role in overseeing the setup and maintenance of these critical controls.
- Removal Techniques:
- Wet Methods: Wetting ACM with an amended water solution (water with a surfactant) before and during removal is a primary control measure to minimize fiber release.
- HEPA Vacuums: Specially designed vacuums with HEPA filters are used for cleaning up asbestos dust and debris. Standard vacuums are not suitable as they can re-disperse fine fibers.
- Manual Removal: Tools used for removal should be hand tools where possible to minimize dust generation. Power tools, if used, must be equipped with HEPA-filtered local exhaust ventilation.
- Glove Bag Removal: For removing asbestos insulation from pipes or other small-scale removals, glove bags (sealed enclosures with built-in gloves) can be used to contain fibers at the point of removal.
- Encapsulation or Enclosure: As alternatives to removal, ACMs can sometimes be encapsulated (treated with a sealant that binds fibers together or covers the surface) or enclosed (isolated behind an airtight, permanent barrier). Encapsulation involves using a material that surrounds or embeds asbestos fibers in an adhesive matrix, while an enclosure creates an impermeable barrier around the ACM.
- Waste Disposal: All asbestos-containing waste (including removed ACM, contaminated PPE, sheeting, and filters) must be wetted, placed in double 6-mil thick, leak-tight plastic bags or other approved containers, and clearly labeled with asbestos warning labels. Disposal must comply with EPA NESHAP regulations and typically occurs at specially designated landfills permitted to accept asbestos waste. Transportation of asbestos waste is also regulated by the Department of Transportation (DOT).
- Air Monitoring: Air sampling is conducted before abatement (baseline), during abatement (area and personal monitoring), and after abatement (clearance monitoring) to ensure containment effectiveness, verify compliance with exposure limits, and confirm the area is safe for re-occupancy.
C. Regulatory Landscape: EPA (AHERA, NESHAP) and OSHA Standards
Asbestos abatement is governed by a comprehensive set of federal regulations, primarily from the EPA and OSHA. These regulations often work in concert, creating a multi-layered safety net.
- EPA Asbestos Hazard Emergency Response Act (AHERA) (40 CFR Part 763, Subpart E): Enacted in 1986, AHERA primarily applies to public and private non-profit elementary and secondary schools. It mandates inspections for asbestos, development of asbestos management plans, and the use of accredited professionals for asbestos-related activities. While legally binding for schools, AHERA’s protocols for inspection and management are often used as guidance for other building types.
- EPA National Emission Standards for Hazardous Air Pollutants (NESHAP) (40 CFR Part 61, Subpart M): NESHAP regulates asbestos emissions from asbestos mills, manufacturing and fabricating operations, and, most relevantly for abatement, demolition and renovation activities in facilities. “Facility” includes institutional, commercial, public, industrial, or residential structures with four or more dwelling units (with some exceptions). NESHAP requires a thorough inspection for asbestos before demolition or renovation, notification to the EPA or delegated state agency before starting work (for projects exceeding certain thresholds of Regulated Asbestos-Containing Material – RACM), and specific work practices for removing and disposing of RACM (primarily friable asbestos materials or non-friable ACM that has been or will be subjected to sanding, grinding, cutting, or abrading).
- EPA Model Accreditation Plan (MAP) (40 CFR Part 763, Subpart E, Appendix C): Issued under AHERA and later expanded by the Asbestos School Hazard Abatement Reauthorization Act (ASHARA), the MAP establishes minimum training and accreditation requirements for individuals performing asbestos work in schools and public and commercial buildings. It defines five disciplines: Worker, Contractor/Supervisor, Inspector, Management Planner, and Project Designer.
- OSHA Asbestos Standards (e.g., 29 CFR 1926.1101 for Construction; 29 CFR 1910.1001 for General Industry): These standards are designed to protect workers from the health hazards of asbestos exposure in the workplace. They establish Permissible Exposure Limits (PELs) for airborne asbestos fibers, require initial and periodic exposure monitoring, delineation of regulated areas, specific engineering controls and work practices for different classes of asbestos work, provision and use of appropriate PPE (especially respirators), hygiene facilities, medical surveillance programs for exposed workers, and comprehensive worker training.
Understanding how these regulations interrelate is crucial. For example, an AHERA-style inspection might identify ACM in a commercial building. If renovation is planned that will disturb this ACM, NESHAP requirements for notification and work practices are triggered. The work must then be performed by MAP-accredited personnel following OSHA’s stringent worker protection standards.
D. Required Certifications for Asbestos Professionals
Due to the significant risks involved, individuals and firms performing asbestos abatement work must meet specific training and certification/licensing requirements.
- EPA Model Accreditation Plan (MAP) Accreditation: Individuals seeking to work in asbestos abatement must complete initial training courses from an EPA or state-approved training provider in one of the five MAP disciplines. Course lengths vary by discipline; for example, initial training for an Asbestos Abatement Worker is typically 4 days (32 hours), and for a Contractor/Supervisor is 5 days (40 hours). Annual refresher training is required to maintain accreditation.
- State Licensing: Most states have their own asbestos licensing programs for individuals and contracting firms, often mirroring or exceeding EPA MAP requirements. Obtaining a state license usually requires:
- Proof of successful completion of an accredited MAP training course.
- Passing a state-administered examination.
- For certain disciplines like Worker and Supervisor, documentation of a medical examination confirming fitness to wear a respirator and a respirator fit test.
- Payment of application and renewal fees. Contracting firms must also typically obtain a state license or permit to offer and perform asbestos abatement services. It is essential to verify that any asbestos professional or firm hired holds the appropriate and current accreditations and licenses for the specific state and type of work being performed.
IV. In-Depth Focus: Polychlorinated Biphenyls (PCBs) Abatement
Polychlorinated Biphenyls (PCBs) are a group of persistent man-made organic chemicals that were widely used in various industrial and commercial applications due to their chemical stability, non-flammability, and electrical insulating properties.Their manufacture was banned in the United States in 1979 due to evidence of their persistence in the environment and adverse health effects. However, PCBs can still be found in older buildings and equipment, necessitating specialized abatement procedures.
A. Identifying PCB Hazards: Sources in Buildings and Equipment
PCBs are not naturally occurring and were manufactured from 1929 until the 1979 ban. Buildings constructed or renovated between approximately 1950 and 1980 are at the highest risk of containing PCB-laden materials. Common sources include:
- Caulking, Grout, and Expansion Joint Material: PCBs were added to these materials to enhance flexibility, adhesion, and durability. They are particularly common in commercial, industrial, and multi-story residential buildings with concrete or masonry construction from that era.
- Paints, Sealants, and Coatings: Oil-based paints, varnishes, and specialty coatings sometimes contained PCBs.
- Electrical Equipment: Older fluorescent light ballasts, transformers, and capacitors are well-known sources of PCBs. While many of these have been removed over time, some may remain in older installations.
- Other Building Materials: PCBs have also been found in ceiling tiles, floor tiles and adhesives (mastics), window and door glazing, rubber and felt gaskets, insulation materials, plastic applications (like vinyl and PVC), and spray-on fireproofing.
- Secondary Contamination: A significant concern is that PCBs from primary sources, like caulk, can leach into and contaminate adjacent porous building materials such as wood, masonry, concrete, and even dust. These secondarily contaminated materials also become PCB remediation waste and require proper management.
The identification process for PCBs typically involves :
- Determining Building Age: Buildings constructed or significantly renovated between 1950 and 1980 are prime candidates.
- Visual Inspection and Records Review: Examining building records for construction dates and materials used, and visually inspecting for suspect materials (e.g., deteriorating caulk, old fluorescent light fixtures).
- Sampling and Analytical Testing: The only conclusive way to confirm the presence and concentration of PCBs is by collecting samples of suspect materials and having them analyzed by an accredited laboratory using appropriate EPA methods.
The presence of PCBs alongside other hazardous materials like asbestos or lead-based paint is also a possibility in buildings from this era. This potential for “double” or “triple contamination” can complicate abatement projects, possibly requiring professionals with cross-certifications or coordinated multi-disciplinary teams.
B. The PCB Abatement Process: Safe Handling and Removal
PCB abatement requires careful planning and execution to prevent worker exposure and environmental release.
- Abatement Strategy and Plan: Before starting work, a detailed abatement plan should be developed. This plan typically includes identifying the PCB sources and concentrations, determining cleanup levels, outlining removal procedures, specifying PPE, detailing waste handling and storage protocols, and identifying disposal options. Depending on the nature and extent of contamination and the chosen disposal method, notification to the EPA may be required.
- Removal Activities:
- Tool Selection: Tools should be chosen to minimize the generation of dust and heat, which can volatilize PCBs. Manual tools like utility knives, chisels, and pry bars may be suitable for smaller areas or hardened caulk. For larger projects, electromechanical joint cutters or similar tools may be used, preferably with dust aspiration systems equipped with HEPA filters.
- Surface Cleaning: After removing bulk PCB-containing materials (like caulk), the underlying surfaces (joint faces) may need to be cleaned to remove residual PCBs. For smooth, non-porous surfaces, this might involve cleaning with a solvent (e.g., acetone), which requires additional specific PPE and ventilation.
- Personal Protective Equipment (PPE): The level of PPE depends on the potential for dust generation and solvent use. Standard PPE includes :
- Gloves and Skin Protection: Chemical-resistant gloves (nitrile butadiene rubber is often recommended) and disposable Tyvek® or similar coveralls.
- Eye Protection: Safety glasses with side shields or protective goggles.
- Respiratory Protection: For activities generating dust or when using solvents, an air-purifying respirator (NIOSH-approved) with combination organic vapor and HEPA cartridges should be considered.
- Worker Hygiene: To prevent ingestion or take-home contamination, eating, drinking, and smoking must be prohibited in the work area. If significant dust is generated, providing showers and separate changing facilities for work clothing and street clothes is recommended.
- Waste Handling and Storage: All removed PCB-containing materials and contaminated debris (including used PPE and cleaning materials) must be immediately contained, typically by wrapping in polyethylene sheeting or placing in DOT-approved drums or containers. These containers must be properly labeled and transported to a designated, secure storage area pending disposal.
C. Health and Environmental Impacts of PCBs
PCBs pose significant threats due to their toxicity, persistence, and tendency to bioaccumulate.
- Persistence and Bioaccumulation: PCBs do not readily break down in the environment. They can persist for long periods, cycling between air, water, and soil. They are taken up by plants and small organisms and accumulate in the fatty tissues of animals, leading to increasing concentrations (bioaccumulation and biomagnification) as they move up the food chain. This makes fish consumption a potential route of human exposure. The long-term environmental presence of PCBs makes their proper disposal during abatement activities absolutely critical to prevent further contamination.
- Health Effects: PCBs are classified as probable human carcinogens by the EPA and the International Agency for Research on Cancer (IARC). Beyond cancer, PCBs are linked to a wide range of serious non-cancer health effects, including :
- Immune system suppression.
- Reproductive system problems (e.g., reduced fertility, effects on birth weight and development).
- Nervous system damage (e.g., neurobehavioral and developmental deficits in children exposed in utero).
- Endocrine system disruption (e.g., effects on thyroid hormone levels).
- Dermal effects, such as chloracne (a severe acne-like condition).
- Liver damage and elevated liver enzymes. The breadth and severity of these health impacts underscore the importance of stringent exposure controls during any PCB abatement work.
D. Regulatory Landscape: EPA’s TSCA and RCRA Regulations
The management of PCBs is primarily governed by the Toxic Substances Control Act (TSCA), with the Resource Conservation and Recovery Act (RCRA) playing a role in certain waste management scenarios.
- Toxic Substances Control Act (TSCA): TSCA is the principal federal law regulating PCBs in the United States. It banned the manufacture, processing, and distribution in commerce of PCBs in 1979. EPA regulations under TSCA, found at 40 CFR Part 761, establish detailed requirements for the use, marking, storage, cleanup, and disposal of PCB-containing materials and PCB waste.
- PCB Bulk Product Waste: This category generally includes waste derived from manufactured products containing PCBs in a non-liquid state at any concentration, such as PCB-containing caulk or paint. Disposal options under 40 CFR §761.62 include :
- Performance-based disposal (e.g., in a TSCA-permitted incinerator, TSCA chemical waste landfill, or a RCRA hazardous waste landfill).
- Disposal in state-permitted non-hazardous solid waste landfills (requires landfill approval and notification to the landfill if PCB concentration is >50 ppm).
- A risk-based disposal option, which requires EPA approval.
- PCB Remediation Waste: This includes materials contaminated as a result of a spill or release of PCBs, such as contaminated soil, sediments, and building materials (like concrete or wood) from which PCB bulk product waste has been removed. Disposal and cleanup options under 40 CFR §761.61 include :
- Self-implementing cleanup and disposal (cleanup levels linked to expected occupancy rates; requires EPA notification).
- Performance-based cleanup and disposal (similar disposal facility options as for bulk product waste).
- Risk-based cleanup and disposal (requires EPA approval based on a site-specific risk assessment).
- PCB Bulk Product Waste: This category generally includes waste derived from manufactured products containing PCBs in a non-liquid state at any concentration, such as PCB-containing caulk or paint. Disposal options under 40 CFR §761.62 include :
- Resource Conservation and Recovery Act (RCRA): While TSCA provides the primary regulatory framework for PCBs, RCRA may also apply if PCB waste independently meets the definition of a RCRA hazardous waste (e.g., due to ignitability, corrosivity, reactivity, or toxicity characteristics for other constituents, or if it’s a listed hazardous waste). If PCB waste is also a RCRA hazardous waste, it must be managed according to the stricter of the two sets of regulations. A hazardous waste manifest is required for the transportation of PCB wastes being shipped for disposal, regardless of RCRA status.
The regulatory landscape for PCBs is focused almost entirely on managing the legacy of their past use. This involves identifying existing PCBs in buildings and the environment, and ensuring their safe cleanup and disposal to prevent ongoing exposure and further contamination.
E. Training and Awareness for PCB Handling
Unlike lead and asbestos, there is no universal federal certification program for PCB abatement workers or supervisors. However, due to the complexities of PCB regulations and the hazards involved, specialized knowledge and awareness are crucial.
- EPA Recommendation: The EPA encourages building owners and contractors to consult with environmental professionals experienced in PCB identification, cleanup, and disposal activities.
- PCB Awareness Training: Various organizations offer PCB awareness training courses. These courses are designed for building owners, abatement contractors, and workers who may encounter or handle PCB-containing or PCB-contaminated materials during renovation, repair, or abatement projects. Topics typically covered include :
- Introduction to PCBs (properties, history, uses).
- Applicable laws and regulations (TSCA, RCRA).
- Health effects of PCB exposure.
- Identification of PCBs in caulk and other building materials.
- Methods for preventing and reducing exposure.
- PCB testing and sampling procedures.
- Safe removal, cleanup, and waste disposal practices. Such training helps ensure that work is conducted in compliance with regulations and in a manner that protects human health and the environment. Personnel involved in PCB abatement should also be aware that their activities might disturb other hazardous materials like asbestos or lead-based paint, potentially requiring additional certifications and safety protocols.
V. In-Depth Focus: Regulated Gypsum Product Removal
Gypsum board, commonly known as drywall, sheetrock, or plasterboard, is a ubiquitous building material used for walls and ceilings. While generally considered safe in its intact state, the removal and disposal of gypsum products can be regulated due to potential health hazards from dust and environmental concerns associated with landfilling.
A. Understanding Hazards in Gypsum Products
The primary hazards associated with gypsum products arise during activities that generate dust, such as demolition, cutting, sanding, or improper handling, and from its disposal.
- Crystalline Silica Hazard: Many gypsum products, including drywall and joint compounds, contain crystalline silica (often in the form of quartz) as a component. When gypsum board is cut, sanded, or crushed, respirable crystalline silica particles can become airborne. Inhalation of these fine particles is a significant occupational health hazard, potentially leading to:
- Silicosis: A chronic and irreversible lung disease characterized by inflammation and scarring of the lung tissue, which impairs breathing.
- Lung Cancer: Respirable crystalline silica is classified as a known human carcinogen by the International Agency for Research on Cancer (IARC) and the National Toxicology Program (NTP).
- Other Health Effects: Prolonged or repeated exposure can also damage the kidneys and contribute to autoimmune diseases. The presence of crystalline silica means that even a common material like drywall can pose serious health risks if dust is not properly controlled during removal or renovation.
- Asbestos in Older Gypsum Systems: Prior to the late 1970s / early 1980s, asbestos was sometimes used in joint compounds, taping compounds, and textured finishes applied to gypsum wallboard. Therefore, older drywall systems must be suspected of containing asbestos until tested. If asbestos is present, even at low concentrations (e.g., less than 1% as discussed in some university procedures ), specific asbestos handling and disposal protocols must be followed to prevent fiber release. This “hidden hazard” in what appears to be a benign material underscores the importance of thorough assessment before disturbing older building components.
- Disposal Concerns and Regulation: The chemical composition of gypsum (calcium sulfate dihydrate) leads to specific environmental concerns when it is landfilled, particularly when mixed with organic waste:
- Hydrogen Sulfide Gas (H₂S) Generation: Under anaerobic (oxygen-deficient) conditions in a landfill, sulfates in gypsum can be converted by bacteria into hydrogen sulfide gas. H₂S is a flammable, toxic gas with a characteristic rotten egg odor, posing risks to public health and safety, and creating nuisance odor problems. This is a primary reason why gypsum waste disposal is often regulated.
- Methane Generation: Gypsum decomposition in landfills can also contribute to the generation of methane (CH4), a potent greenhouse gas.
- Landfill Liner Damage: Leachate from gypsum waste can be aggressive towards certain types of landfill liners, potentially compromising their integrity.
- Dedicated Landfill Cells: Due to these environmental risks, many jurisdictions require that gypsum waste, classified as a non-hazardous high-sulfate waste, be disposed of in dedicated landfill cells or monofills that are specifically designed to manage sulfate-rich wastes and prevent the co-disposal with organic materials. This segregation is based on preventing harmful chemical reactions within the landfill environment.
B. Safe Removal and Disposal Practices for Regulated Gypsum
Safe handling during removal and appropriate disposal are key to managing the risks associated with gypsum products.
- Dust Control: The primary strategy during removal is to minimize dust generation. This involves :
- Wet Methods: Wetting down materials before disturbance or wetting dust before cleanup can significantly reduce airborne particles.
- HEPA Vacuums: Using industrial vacuums equipped with HEPA filters for cleanup ensures that fine particles, including respirable crystalline silica, are captured.
- Prohibition of Dry Sweeping: Dry sweeping should be avoided as it re-suspends dust into the air.
- Personal Protective Equipment (PPE): When dust generation is unavoidable, workers should wear appropriate PPE :
- Respiratory Protection: A NIOSH-approved respirator suitable for particulate matter (e.g., N95, R95, P95, or higher, depending on the anticipated exposure levels to crystalline silica as outlined in OSHA/NIOSH guidelines ).
- Eye Protection: Safety glasses or goggles to prevent dust irritation.
- Gloves and Coveralls: May be advisable to minimize skin contact and contamination of clothing.
- Careful Handling: Gypsum board should be handled with care to prevent breakage and dust creation. Workers should avoid standing on unstable piles of demolished material.
- Waste Collection and Disposal:
- Dust and debris should be collected and placed in covered containers to prevent dispersal.
- Gypsum waste must be disposed of in accordance with all applicable federal, state, and local regulations. It should not be washed down drains, as it can cause blockages.
- If landfilling is the chosen route, disposal in dedicated “high sulfate” cells or monofills may be required, segregated from organic wastes.
- Managing Asbestos in Gypsum Products: If older gypsum wallboard systems are suspected or confirmed to contain asbestos (e.g., in joint compound or textured surfaces), even if the asbestos content is below the threshold for NESHAP-regulated RACM, specific asbestos safety protocols should be followed during removal. These include wet methods, HEPA vacuuming, careful handling to minimize dust, proper bagging of waste, and appropriate PPE for asbestos.
- Recycling as a Preferred Alternative: Gypsum is highly recyclable. Recycled gypsum can be used as a raw material in the manufacture of new drywall, as an additive in cement production, or as a soil amendment in agriculture (providing calcium and sulfur). Recycling offers significant environmental benefits by:
- Reducing the volume of waste sent to landfills.
- Conserving natural gypsum resources (reducing the need for mining).
- Lowering energy consumption and greenhouse gas emissions associated with virgin gypsum production.
- Avoiding the environmental problems (H₂S and methane generation, liner damage) associated with landfilling gypsum. The dual benefits of resource conservation and hazard avoidance make recycling a particularly compelling and sustainable management option for gypsum waste.
VI. Core Abatement Procedures and Best Practices (Applicable Across Multiple Material Types)
While each hazardous material presents unique challenges, several core procedures and best practices are fundamental to most abatement projects. These practices form a “system of systems” where each component is vital for overall success and safety. Failure in one area, such as inadequate containment, can compromise other measures like PPE effectiveness or lead to failed clearance air monitoring.
A. Setting Up Containment: Isolating the Hazard
The primary goal of containment is to isolate the work area, preventing the spread of hazardous dust, fibers, or contaminants to adjacent clean areas, thereby protecting occupants and the environment. Effective containment is the first line of defense.
- Key Elements of Work Area Containment:
- Physical Barriers: This involves constructing an enclosure around the work zone. Polyethylene (poly) sheeting, typically 6-mil thick or greater, is commonly used to seal off doorways, windows, HVAC vents, and other openings. Critical barriers are erected to completely isolate the regulated area. Floors and any immovable objects within the work area are covered with impermeable drop cloths or poly sheeting. For lead RRP work, specific procedures include covering floors with taped-down plastic sheeting extending a certain distance, sealing doors and vents with plastic, and potentially using vertical containment for exterior work.
- Regulated Area Demarcation: The work zone must be clearly marked with warning signs indicating the presence of hazardous materials and restricting unauthorized entry.
- Negative Pressure Enclosures (NPEs): For abatement of highly hazardous friable materials like asbestos (Class I work) or during significant lead dust-generating activities, an NPE is often mandatory. An NPE uses HEPA-filtered air exhaust units (negative air machines) to continuously draw air from the containment and exhaust it (often to the outside, after filtration). This creates a lower air pressure inside the containment relative to the surrounding areas, ensuring that any air leakage flows into the work area rather than contaminants escaping out.
- Decontamination Units: For high-risk materials like asbestos, a multi-stage decontamination enclosure system is required for workers to safely enter and exit the regulated area. This typically consists of a clean room (to put on clean PPE), a shower room (for showering after work and before removing respirators), and an equipment room (for decontaminating tools and storing contaminated PPE before showering). For lead work, OSHA requires clean change areas with separate storage for protective work clothing and street clothes to prevent take-home contamination.
- Secondary Containment for Stored Waste and Liquids: Beyond work area containment, regulations also address the storage of hazardous materials and waste generated during abatement. Secondary containment systems are designed to catch leaks or spills from primary containers (e.g., drums, totes). Common types include containment berms, spill pallets, or double-walled tanks. According to EPA regulations (e.g., 40 CFR 264.175), such systems must:
- Underlie the containers and be free of cracks or gaps.
- Be sufficiently impervious to contain leaks, spills, and accumulated precipitation.
- Be sloped or designed to drain and remove liquids.
- Have sufficient capacity to contain 10% of the volume of all containers or the volume of the largest container, whichever is greater.
- Prevent the migration of hazardous substances to soil, groundwater, or surface waters.
B. Air Monitoring: Ensuring Safety Before, During, and After
Air monitoring is a critical component of hazardous material abatement, providing quantitative data on airborne contaminant levels. Its purposes include assessing initial conditions, ensuring control measures are effective, protecting worker and public health, and documenting conditions for final clearance.
- Phases of Air Monitoring (particularly for asbestos ):
- Preliminary/Baseline Monitoring: Conducted before abatement activities begin. This is optional but can establish pre-existing background levels of contaminants or determine if an alternative indoor air standard is needed if background levels are unusually high.
- During Abatement Monitoring:
- Area Monitoring: Samples are collected at various locations around the perimeter of the containment (outside the work area) and near decontamination unit exits to detect any breaches in containment. For asbestos, results must typically be less than or equal to 0.01 fibers per cubic centimeter of air (f/cc) or an established alternative standard.
- Personal Monitoring: Samples are collected from within the breathing zone of workers inside the containment to assess their individual exposures against OSHA Permissible Exposure Limits (PELs). OSHA’s standard for hazardous waste operations (1910.120) also broadly requires initial, periodic, and ongoing air monitoring for all hazardous substances of concern at a site.
- Clearance Monitoring: Performed after all abatement work and cleanup are complete, and the area has passed a thorough visual inspection. For asbestos, this involves aggressive air sampling inside the de-activated containment (using leaf blowers and fans to dislodge any settled fibers) to simulate worst-case re-occupancy conditions. Typically, a set number of samples (e.g., five for asbestos in many jurisdictions) are collected from randomly selected locations. The area is considered safe for re-occupancy only if all samples meet the specified clearance criteria (e.g., for asbestos, ≤0.01 f/cc by PCM analysis, or ≤70 structures per square millimeter (s/mm2) by TEM analysis for schools and some other settings).
- Air Sampling Techniques:
- Phase Contrast Microscopy (PCM): The most common and cost-effective method for analyzing asbestos air samples. PCM counts all fibers meeting certain size criteria (length, width, aspect ratio). It provides quick results and is used by OSHA for comparison to PELs, but it cannot differentiate between asbestos fibers and other fiber types (e.g., fiberglass, cellulose).
- Transmission Electron Microscopy (TEM): A more sophisticated and expensive method for asbestos analysis. TEM can visualize much smaller fibers and can positively identify asbestos fibers by their morphology and elemental composition. It is often required for final clearance in schools (AHERA) and may be used in other situations requiring higher sensitivity or specific fiber identification.
- Other Methods: For other airborne hazardous substances like lead dust or chemical vapors, various NIOSH-approved sampling and analytical methods are used. These can include drawing air through specific filter media for laboratory analysis, or using direct-reading instruments and colorimetric indicator tubes for real-time or screening-level measurements, depending on the contaminant and site conditions.
- Laboratory Analysis: All air samples requiring laboratory analysis must be sent to laboratories accredited for the specific type of analysis being performed (e.g., AIHA-LAP, LLC accredited for PCM asbestos analysis; NIST NVLAP accredited for TEM asbestos analysis).
C. Waste Disposal: Navigating EPA, DOT, and RCRA Regulations
Proper disposal of hazardous waste generated during abatement is crucial to prevent future health risks and environmental contamination. This process is heavily regulated.
- Hazardous Waste Identification: The first critical step is to determine if the waste is legally defined as hazardous. Under the EPA’s Resource Conservation and Recovery Act (RCRA), a waste is hazardous if it is specifically listed as such by EPA or if it exhibits one or more hazardous characteristics: ignitability, corrosivity, reactivity, or toxicity. For some materials, like lead-based paint debris, the Toxicity Characteristic Leaching Procedure (TCLP) is used to determine if it’s a toxic hazardous waste.
- RCRA “Cradle-to-Grave” Management: For wastes classified as hazardous under RCRA, generators (including abatement contractors or facility owners) are responsible for the waste from the point of generation until its ultimate safe disposal – the “cradle-to-grave” system. This entails:
- Proper Identification, Labeling, and Storage: Hazardous waste must be correctly identified, characterized, and stored in appropriate containers that are closed, in good condition, compatible with the waste, and clearly labeled with the waste’s identity and associated hazards. Incompatible wastes must be segregated.
- Uniform Hazardous Waste Manifest: A multi-copy manifest document must accompany all shipments of RCRA hazardous waste. This document tracks the waste from the generator, through a licensed hazardous waste transporter, to a permitted Treatment, Storage, and Disposal Facility (TSDF). The generator retains copies to prove proper disposal.
- Transportation: Transporters of hazardous waste must comply with both EPA regulations and U.S. Department of Transportation (DOT) hazardous materials regulations (HMR) regarding placarding, packaging, and shipping papers.
- Treatment, Storage, and Disposal Facilities (TSDFs): RCRA hazardous waste must be sent to a TSDF that is specifically permitted to receive and manage that type of waste. These facilities are stringently regulated to ensure safe management.
- Land Disposal Restrictions (LDRs): Under RCRA, many hazardous wastes are prohibited from land disposal unless they meet specific EPA-established treatment standards designed to reduce their toxicity or mobility.
- Specific Material Disposal Pathways:
- Lead Waste: If TCLP testing shows it’s RCRA hazardous ($ geq 5 text{ mg/L}$ leachable lead), it must go to a licensed TSDF. If non-hazardous, it can typically go to an approved construction and demolition (C&D) landfill, subject to state/local rules.
- Asbestos Waste: Must be wetted, placed in sealed, labeled, leak-tight bags or containers, and disposed of in an EPA-approved landfill that is permitted to accept asbestos waste, in accordance with NESHAP regulations.
- PCB Waste: Primarily regulated under TSCA (40 CFR Part 761). Disposal options vary based on the type of PCB waste (bulk product vs. remediation waste) and concentration, but include TSCA-permitted chemical waste landfills, TSCA incinerators, or RCRA hazardous waste landfills for certain PCB wastes. Some lower-concentration PCB bulk product waste may go to state-permitted solid waste landfills with appropriate approvals and notifications.
- Regulated Gypsum Waste: If not recycled, it should be disposed of in dedicated “high sulfate” landfill cells, segregated from organic waste, to prevent hydrogen sulfide gas generation, per specific Environment Agency or local rules.
D. Documentation and Record-Keeping: The Path to Compliance
Meticulous documentation and record-keeping are not merely administrative tasks; they are fundamental to demonstrating regulatory compliance, managing liability, and providing a complete historical account of abatement activities. In the event of future health claims or regulatory audits, which can occur years after project completion, these records serve as the primary evidence of due diligence.
- Key Records to Maintain :
- Employee Training Records: Documentation of all hazard-specific training (e.g., lead, asbestos, PCB awareness, HAZWOPER), including course content, dates, instructor qualifications, and employee certifications. These must be kept for current personnel until facility closure and for at least three years after a former employee’s last day of work.
- Waste Classification Records: All data and documentation supporting waste determinations, including laboratory analytical results (e.g., TCLP for lead), sampling methods, descriptions of the waste-generating process, waste composition, and all applicable waste codes. These are typically kept for at least three years after the waste was last sent for treatment, storage, or disposal.
- Hazardous Waste Manifests: Signed copies of manifests received from the designated TSDF, confirming receipt and management of the waste. These must be retained for at least three years from the date the waste was accepted by the initial transporter.
- Contingency Plans: For Large Quantity Generators (LQGs) of hazardous waste, a written RCRA contingency plan detailing emergency response procedures.
- Inspection Records: Logs of daily site inspections, containment integrity checks, and equipment functionality.
- Air Monitoring Data: All results from personal, area, and clearance air monitoring, including sampling locations, dates, times, volumes, analytical methods, laboratory reports, and interpretations.
- Abatement Plans and Project Reports: The initial work plan, daily logs of activities, photographic records, and a final report summarizing the project, including any deviations from the plan and corrective actions taken.
- Regulatory Notifications: Copies of all notifications submitted to federal, state, or local agencies (e.g., EPA NESHAP notification for asbestos demolition/renovation, EPA notification for certain PCB cleanups).
- PPE Program Records: Documentation of respirator fit-testing, PPE selection, and maintenance.
- Medical Surveillance Records: For workers covered by OSHA standards (e.g., lead, asbestos), medical records must be maintained for the duration of employment plus 30 years.
- Retention Periods: Vary depending on the specific regulation and type of record, but generally range from 3 to 5 years, with some (like medical records) being much longer. It is crucial to be aware of all applicable federal, state, and local record-keeping requirements.
E. Preventing Cross-Contamination
Cross-contamination is the unintentional transfer of hazardous materials from contaminated areas, surfaces, tools, or personnel to clean areas. Preventing it is paramount in abatement work. While engineering controls like containment and NPEs are vital, the human factor – worker training, diligence, and adherence to protocols – is equally critical.
- Key Practices for Preventing Cross-Contamination :
- Strict Containment: Effective isolation of the work area using barriers and negative air pressure, as detailed previously.
- Decontamination Procedures: Rigorous procedures for personnel exiting the work area (e.g., vacuuming PPE, showering, changing clothes in designated decontamination units) and for decontaminating tools and equipment before they are removed from the containment.
- Segregation: Keeping contaminated tools, equipment, and waste physically separated from clean areas and materials.
- Controlled Entry/Exit Points: Using designated decontamination zones or change areas as the sole points of entry and exit for the regulated area.
- Wet Methods: Using water or wetting agents to suppress dust and fiber generation during removal and cleanup activities.
- HEPA Vacuuming: Thoroughly vacuuming all surfaces within the containment with HEPA-filtered vacuums during and after abatement.
- Disposable PPE: Using disposable coveralls, gloves, head coverings, and foot coverings, and treating them as contaminated waste after use.
- Worker Training and Hygiene: Educating workers on the importance of personal hygiene (e.g., handwashing), proper donning and doffing of PPE, and procedures to prevent tracking contaminants out of the work area. highlights that even seemingly low-risk actions can become high-risk if personnel are not properly trained or conscientious.
- Documented Sanitation Standard Operating Procedures (SSOPs): Having clear, written procedures for all cleaning and decontamination tasks, including responsible personnel, step-by-step instructions, monitoring, and corrective actions.
The following table provides a consolidated overview of the key regulatory frameworks that abatement service professionals must navigate. This illustrates the complexity of the regulatory environment and reinforces the necessity for specialized expertise.
Table 2: Key Regulatory Frameworks for Abatement Services
Regulation/Act | Key Focus Areas for Abatement | Governing Agency(ies) | Primary Materials Covered |
---|---|---|---|
OSHA Standards (e.g., 29 CFR 1926.1101, 1926.62) | Worker safety, Permissible Exposure Limits (PELs), Personal Protective Equipment (PPE), training, medical surveillance | OSHA | Asbestos, Lead, Crystalline Silica, other site-specific hazards |
EPA RRP Rule (40 CFR 745, Subpart E) | Lead-based paint disturbance during renovation/repair/painting, firm & individual certification, lead-safe work practices | EPA, Authorized States | Lead |
EPA NESHAP (40 CFR 61, Subpart M) | Asbestos emissions during demolition/renovation, facility inspections, notifications, work practices, waste disposal | EPA, Authorized States | Asbestos (RACM) |
EPA AHERA / MAP (40 CFR 763) | Asbestos in K-12 schools (inspection, management plans), professional accreditation standards for asbestos work | EPA, Authorized States | Asbestos |
EPA TSCA (40 CFR 761) | PCB use, marking, storage, cleanup, and disposal | EPA | Polychlorinated Biphenyls (PCBs) |
EPA RCRA (40 CFR Parts 260-279) | Hazardous waste identification, generation, transportation, treatment, storage, disposal, manifest system | EPA, Authorized States | General Hazardous Wastes (can include lead, some PCB waste) |
DOT Hazmat Regulations (49 CFR Parts 100-185) | Transportation of hazardous materials, including packaging, labeling, placarding, shipping papers | DOT | All regulated hazardous materials during transport |
VII. The Critical Importance of Professional Abatement Services
When faced with the presence of hazardous materials like lead, asbestos, or PCBs in a home or building, the decision on how to address the situation is paramount. While a do-it-yourself (DIY) approach might seem like a way to save money, it carries profound risks that far outweigh any potential financial benefits.
The complexity of abatement work, the specialized knowledge and equipment required, and the stringent regulatory landscape make hiring certified and experienced professionals the only responsible and safe choice.
A. The Dangers of DIY: Health, Safety, Legal, and Environmental Risks
Attempting to remove or disturb hazardous materials without proper training, equipment, and containment can have devastating consequences:
- Severe Health Risks: The foremost danger of DIY abatement is acute and chronic health effects from exposure. Microscopic asbestos fibers, for instance, can remain airborne for hours when disturbed, easily inhaled, and can lead to fatal lung diseases years later. In the UK alone, asbestos is linked to 5,000 deaths annually. Lead dust generated from improper paint removal can cause irreversible neurological damage in children and systemic health problems in adults. DIYers often lack the understanding of how these materials become airborne and how to protect themselves and their families from exposure, including “take-home” contamination where fibers or dust are carried on clothing to contaminate living spaces.
- Inadequate Containment and Cross-Contamination: Professionals use sophisticated containment methods, including sealed enclosures and negative air pressure systems, to prevent the spread of contaminants. DIY attempts typically lack these measures, resulting in hazardous dust and fibers spreading throughout the property, contaminating clean areas, HVAC systems, and personal belongings.
- Improper Waste Disposal and Environmental Contamination: Hazardous waste disposal is strictly regulated. DIYers are generally unaware of these complex requirements (e.g., for manifesting, transportation by licensed haulers, disposal at permitted facilities) and may illegally dispose of hazardous materials with regular trash or in unapproved locations. This can lead to significant environmental contamination of soil, water, and air, posing risks to the wider community.
- Legal Consequences and Financial Penalties: Numerous federal, state, and local laws govern hazardous material abatement and disposal. Unauthorized or improper removal can lead to substantial civil fines and, in some cases, criminal prosecution. For example, knowingly violating RCRA regulations regarding hazardous waste can result in penalties of up to $50,000 per day of violation and/or imprisonment for up to 5 years, with penalties doubling for subsequent violations. DOT regulations also carry significant penalties for improper transportation of hazardous materials.
- Lack of Specialized Equipment and Knowledge: Professional abatement requires specialized equipment such as HEPA-filter vacuums, negative air machines, air monitoring devices, and specific types of personal protective equipment (PPE) that are not readily available or understood by the general public. Furthermore, the technical knowledge to safely use this equipment and implement complex abatement procedures is acquired through extensive training and experience.
- Insurance Issues: Standard homeowner’s insurance policies may not cover damage, liability, or health issues arising from improper or illegal DIY hazardous material removal.
- Reduced Property Value and Incomplete Removal: An improper DIY job may not fully remove the hazard, or worse, may exacerbate it. This can lead to ongoing health risks, the need for future professional remediation (often at a higher cost to correct mistakes), and a potential decrease in property value.
The risk-reward calculation for DIY abatement is overwhelmingly negative. The potential “savings” are often minor compared to the potentially catastrophic and life-altering downsides.
B. Why Professionals are Essential: Expertise, Equipment, and Compliance
Hiring certified and licensed abatement professionals offers a multitude of benefits that ensure the job is done safely, legally, and effectively.
- Expertise and Training: Certified abatement specialists undergo rigorous training and possess the experience to accurately identify hazardous materials, assess the associated risks, understand the complex web of applicable regulations, and implement the safest and most effective abatement techniques tailored to the specific material and situation.
- Specialized Equipment: Professionals have access to and are proficient in using advanced, industry-standard equipment. This includes HEPA vacuums that capture microscopic particles, negative air machines to maintain containment integrity, appropriate types of respirators and disposable PPE, and air monitoring instruments to verify safety.
- Regulatory Compliance: Licensed abatement contractors are knowledgeable about and adhere to all federal (EPA, OSHA, DOT), state, and local regulations. This includes obtaining necessary permits, providing required notifications to agencies, following mandated work practices, conducting air monitoring, and ensuring proper waste disposal. This adherence protects property owners from significant legal and financial liabilities. The use of tools like EPA asbestos abatement notification forms is standard practice for professionals to ensure compliance.
- Proper Waste Management: Professionals ensure that all hazardous waste is correctly identified, segregated, packaged, labeled, manifested, transported by licensed haulers, and disposed of at government-approved facilities, with complete documentation.
- Comprehensive Cleanup and Verification: After removal, professionals conduct thorough cleaning of the work area. For many types of abatement (especially asbestos), clearance air testing is performed by an independent third party to verify that the area is safe for re-occupancy.
- Liability Protection and Peace of Mind: Hiring qualified, insured, and licensed professionals provides a crucial layer of liability protection for the property owner. Should any issues arise, demonstrating that certified experts performed the work according to all applicable standards is a significant defense. Ultimately, it offers peace of mind, knowing that the hazardous material has been dealt with responsibly, safeguarding the health of current and future occupants and protecting the environment. This professional handling also contributes to a broader public good by preventing wider environmental contamination and reducing the societal burden of occupational and public health issues stemming from uncontrolled hazardous material exposure.
C. The True Cost: Beyond the Initial Quote
While the upfront cost of professional abatement services may seem higher than attempting a DIY solution, it is crucial to consider the true, long-term costs. The perceived savings from DIY can be quickly eclipsed by:
- Medical Expenses: Treatment for asbestos-related diseases, lead poisoning, or other conditions caused by exposure can be extensive and lifelong.
- Legal Fines and Penalties: As discussed, non-compliance can lead to severe financial penalties from regulatory agencies.
- Environmental Cleanup Liabilities: If improper disposal leads to environmental contamination, the property owner may be held responsible for costly cleanup operations.
- Cost of Re-doing Improper Work: If a DIY attempt fails to adequately remove the hazard or spreads contamination, professionals will still need to be hired, often at an increased cost to rectify the situation.
- Diminished Property Value: An improperly managed hazardous material issue can significantly reduce a property’s value and marketability.
Investing in professional abatement is an investment in health, safety, legal compliance, and the long-term value of the property.
Table 3: DIY vs. Professional Abatement: A Critical Risk/Benefit Comparison
Aspect | DIY Approach | Professional Service |
---|---|---|
Health & Safety | High risk of personal and family exposure, cross-contamination, long-term illness | Trained personnel, proper PPE, engineered containment, air monitoring to ensure safety |
Legal Compliance | Very high risk of non-compliance with complex EPA, OSHA, state/local laws; potential for severe fines, legal action | Adherence to all applicable regulations, proper permits, notifications, and documentation |
Equipment & Expertise | Lack of access to and training on specialized equipment (HEPA vacuums, negative air machines, etc.) | Use of industry-standard specialized equipment; certified, licensed, and experienced staff |
Waste Disposal | High likelihood of improper, illegal disposal leading to environmental harm and further liability | Legal, documented transportation and disposal of hazardous waste at approved facilities |
Cost | Seemingly lower upfront cost, but extremely high potential for devastating long-term costs (health, legal, re-work) | Higher upfront cost, but represents a sound investment in mitigating long-term health, financial, and legal risks and liabilities |
Outcome & Peace of Mind | Uncertainty about completeness of removal, ongoing risk of exposure, potential for future problems | Thorough removal, often with third-party clearance verification, assurance of safety, compliance, and peace of mind |
D. Your Responsibility: Call a Professional
The safe management of regulated hazardous materials such as lead, asbestos, PCBs, and even dust from regulated gypsum products is a complex and high-stakes undertaking.
Given the significant health risks, the intricate environmental regulations, the potential for severe legal and financial consequences, and the specialized knowledge and equipment required, attempting DIY abatement is strongly discouraged and, in many cases, illegal.
The only responsible course of action when facing a potential hazardous material issue in a property is to contact qualified, certified, and licensed abatement professionals. These experts are equipped to:
- Accurately identify and assess the hazard.
- Develop a site-specific abatement plan that complies with all regulations.
- Implement appropriate engineering controls and safe work practices.
- Ensure workers are properly protected.
- Manage and dispose of hazardous waste correctly.
- Provide documentation verifying that the abatement was performed safely and effectively.
Protecting the health of occupants, workers, and the environment, while ensuring legal compliance, should always be the top priority. When it comes to hazardous material abatement, there is no substitute for professional expertise.