1. The Foundation of Cleanliness: Understanding Janitorial & Cleaning Accessories
The pursuit of cleanliness and hygiene, whether in bustling commercial centers, healthcare facilities, educational institutions, or residential complexes, relies heavily on a well-orchestrated system of tools and supplies. Among these, janitorial and cleaning accessories play a pivotal, often underestimated, role. These items are not merely peripheral but form the very bedrock upon which effective and efficient cleaning protocols are built.
Defining Janitorial & Cleaning Accessories: More Than Just Tools
Janitorial and cleaning accessories encompass a broad and diverse range of items specifically designed to support and facilitate cleaning operations. These are the implements used for organizing, transporting, applying, or managing cleaning tasks, as well as those dedicated to ensuring the safety of personnel and occupants during these processes.
Contact us!
This category includes, but is not limited to, cleaning carts and caddies, spray bottles, buckets, warning signs, protective gloves, trash bags, measuring devices, tool holders, and dispensers.
While cleaning chemicals and powered equipment like vacuums or floor scrubbers are vital, accessories are the essential enablers that allow these primary agents and machines to be used effectively, safely, and economically.
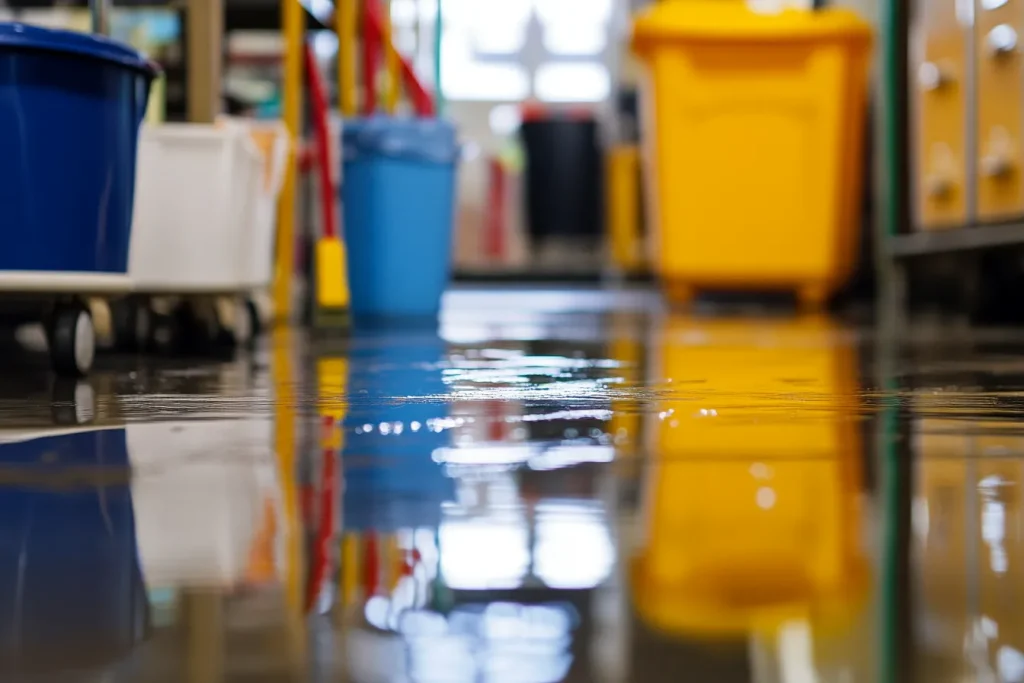
These accessories form an interconnected ecosystem where the performance of one component often influences the utility of another. For instance, high-quality cleaning solutions achieve optimal results only when applied with appropriate tools such as correctly chosen spray bottles or microfiber cloths, and handled with suitable safety gear like chemical-resistant gloves. A poorly designed cleaning cart can hinder the organization of these tools, leading to inefficiencies and compromised workflows.
This systemic interplay means that the selection and management of janitorial accessories should be approached holistically. Viewing these items not as isolated purchases but as integrated parts of a larger cleaning strategy allows for the realization of greater overall value, improved performance, and enhanced safety standards. Procurement decisions, therefore, benefit from considering how different accessories interact and collectively contribute to achieving the overarching goals of cleanliness and hygiene.
The Critical Role of Quality Accessories in Efficiency, Safety, and Hygiene
The selection of janitorial and sanitation supplies, particularly the accessories that support their use, holds the power to transform a mundane cleaning routine into a highly efficient, effective, and impactful endeavor. Investing in high-quality accessories is not merely an operational expense but a strategic decision that yields significant returns in multiple areas.
Quality accessories are fundamental to achieving high standards of hygiene. They aid in the effective application of disinfectants and cleaning agents that target and eliminate germs, bacteria, and viruses, thereby creating safer environments, especially in high-traffic or sensitive locations like offices and healthcare facilities. This proactive approach to germ control is crucial in preventing the spread of illnesses and ensuring the well-being of all occupants.
Furthermore, these supplies play a pivotal role in workplace safety. For example, appropriate warning signs and well-maintained mopping equipment can significantly reduce slip-and-fall incidents, which are common accidents in commercial settings.
Specialized cleaning agents and equipment effectively address spills and slippery surfaces, minimizing potential hazards. The use of proper personal protective equipment (PPE) like gloves and, when needed, masks, minimizes direct exposure to cleaning chemicals and contaminants, safeguarding the health of cleaning staff.
Efficiency is another key benefit derived from quality accessories. Tools that are well-designed, durable, and fit for purpose allow cleaning tasks to be completed more quickly and with less effort. For example, ergonomic janitorial carts reduce physical strain and the need for frequent trips to supply closets, saving valuable time.
This increased efficiency allows cleaning personnel to cover more area or perform more detailed tasks within their allotted time, leading to higher productivity. A clean and organized workspace, maintained with quality supplies, also contributes to the productivity of all occupants by creating a more conducive atmosphere for concentration and task completion.
The return on investment from quality janitorial accessories becomes evident when considering the total cost of ownership. While high-quality, durable items may have a higher initial purchase price, they often result in long-term savings. Commercial-grade accessories are designed for frequent and robust use, meaning they last longer and require replacement less often than cheaper, lower-quality alternatives.
This durability reduces material costs over time and minimizes disruptions caused by equipment failure. Enhanced worker productivity, stemming from better tools and ergonomic designs, translates to more efficient labor utilization. Improved safety outcomes lead to fewer workplace accidents and associated costs, such as medical expenses, lost workdays, and potential liability claims. Ultimately, superior cleaning results contribute to a positive perception of the facility, enhancing its value and appeal to occupants, visitors, and clients.
Facility managers and cleaning business owners who adopt a value-generation perspective, rather than focusing solely on initial cost minimization, will find that quality accessories are a sound investment.
Distinguishing Commercial-Grade vs. Household Supplies
A critical distinction must be made between janitorial supplies designed for commercial or industrial use and those intended for typical household cleaning. Commercial-strength janitorial supplies are fundamentally different from their domestic counterparts; they are formulated to be more potent and constructed to be more durable to meet the demands of heavy-duty, rigorous daily use in commercial spaces.
Consumer brands, even those with a reputation for good quality in a home setting, often do not possess the resilience or efficacy required for consistent performance in demanding commercial environments.
The imperative for choosing commercial-grade supplies stems from their “fitness for purpose.” Household cleaning products and accessories are engineered for occasional, lighter-duty tasks, different soil loads, and varying user expectations. In contrast, commercial supplies are specifically designed and manufactured to withstand sustained, high-demand performance within specific operational contexts, such as hospitals, schools, large office buildings, or industrial facilities. These environments typically feature higher foot traffic, a greater diversity of challenging soils, more stringent hygiene requirements, and the need for cleaning operations to be conducted with maximum efficiency and minimal disruption.
This “fitness for purpose” is reflected in the design, materials, and construction of commercial-grade accessories. For example, an industrial mop and bucket system will be far more hard-wearing and long-lasting than a household equivalent, even if made by the same brand.
Commercial cleaning carts are built with more robust plastics or metal components, stronger frames, and heavy-duty casters to carry significant loads and endure constant movement. Spray bottles designed for commercial use often feature chemical-resistant seals and more durable trigger mechanisms. Gloves will offer specific levels of chemical protection and durability suited to professional cleaning agents.
Attempting to utilize household supplies in a commercial setting typically leads to rapid product failure, increased replacement frequency (and thus higher long-term costs), potential safety hazards (e.g., a flimsy bucket tipping over, a weak trash bag tearing), and ultimately, substandard cleaning results.
This approach proves to be more expensive and less effective in the long run. Therefore, the selection process for janitorial accessories in any professional cleaning context must prioritize the specific demands of the environment and opt for commercial-grade products designed to meet those challenges.
2. Organizing and Transporting Cleaning Essentials
Effective cleaning operations depend not only on the right chemicals and tools but also on the systems used to organize and transport these essentials. Well-designed accessories for organization and transportation streamline workflows, enhance worker efficiency, improve safety, and contribute to a more professional appearance.
Cleaning Carts & Trolleys: Mobile Command Centers
Cleaning carts and janitorial trolleys serve as mobile command centers for cleaning staff, designed to consolidate all necessary cleaning supplies, tools, and waste disposal options into a single, organized, and easily transportable unit. These indispensable accessories typically feature a combination of shelves, compartments, hooks for mops and brooms, holders for various tools, and integrated bags for collecting waste or soiled linens.
The market offers a variety of designs, including compact single-mop trolleys for smaller tasks, larger double-mop trolleys with wringers for extensive floor cleaning, specialized linen trolleys for hospitality or healthcare, and robust models constructed from materials like high-density plastic or stainless steel for enhanced durability and hygiene.
The primary function of these carts is to improve organization and efficiency. By keeping all necessary items readily accessible, they significantly reduce the time and effort cleaning staff spend walking back and forth to storage rooms or searching for supplies. This streamlined approach not only saves time but also reduces physical strain, as staff can move smoothly across large facilities without manually carrying heavy buckets or multiple tools. Many trolleys are equipped with ergonomic handles and smooth-rolling casters designed for maneuverability across various floor surfaces.
Modern janitorial carts are more than passive carriers; they are active tools for process optimization. Their design directly influences workflow efficiency, staff ergonomics, and even the management of consumable supplies. A cart with customizable compartments, perhaps incorporating removable caddies, allows staff to tailor the setup to specific tasks or zones within a facility, reducing search time and improving focus. Integrated collection systems for waste and soiled linen minimize the need for separate trips, further enhancing productivity.
Strategically placed hooks and holders ensure that tools like mops, brooms, and warning signs are always at hand and securely stowed during transit, preventing misplacement or damage. Selecting the right cart and training staff on its optimal configuration and use can lead to measurable improvements in cleaning times per area, reduced staff fatigue, and better control over supply usage. This elevates the cart from a mere container to a strategic asset in service delivery.
Beyond efficiency, the physical design of janitorial carts, particularly features like segregated compartments for clean and dirty items and the choice of construction materials, plays a crucial, often underestimated, role in upholding hygiene standards and preventing cross-contamination. This is especially critical in sensitive environments such as healthcare facilities, but it is also important in offices and public buildings to prevent the general spread of illnesses.
Many trolleys feature separate sections for soiled linen or waste, distinct from areas intended for clean supplies or freshly laundered cloths. Some advanced models, particularly those designed for healthcare, incorporate multi-bucket systems specifically to prevent the transfer of contaminants from dirty water back to clean solutions or surfaces. The materials used in cart construction are also significant; high-density plastics or stainless steel are often preferred because they are non-porous, resistant to chemicals and rust, and easy to clean and disinfect, thus preventing the cart itself from becoming a reservoir for bacteria or mold.
If a cart lacks clear separation for soiled and clean items, or is made of materials that are difficult to sanitize, it can inadvertently become a vector for spreading pathogens from one area to another. Thus, the design choice of a janitorial cart is not just about operational convenience but is a fundamental component of an institution’s infection control strategy. Procurement decisions must weigh these hygiene-related design features heavily.
When selecting a cleaning cart or trolley, several key considerations come into play. Durability is paramount, as these units must withstand daily wear and tear; materials like high-density structural foam plastic, aluminum, or stainless steel offer longevity. Capacity should be matched to the size of the area being cleaned and the volume of supplies needed, avoiding carts that are too small (requiring frequent restocking) or too cumbersome for the space.
Maneuverability is critical, so look for carts with high-quality, smooth-rolling, non-marking casters and an ergonomic design that is easy to push and navigate, even in tight spaces. For added security and safety, some carts offer lockable cabinets or hoods, which are essential for storing cleaning chemicals securely or keeping valuable amenities safe, especially in public-access areas or healthcare settings where access control is vital.
Cleaning Caddies: Portable & Practical Solutions
Cleaning caddies are compact, portable containers designed to hold a curated selection of essential cleaning supplies and tools. Their primary purpose is to keep these items organized and within immediate arm’s reach, thereby eliminating the inefficiency of repeatedly returning to a central supply closet or a larger cleaning cart for individual items.
These accessories are particularly useful for targeted cleaning tasks, quick response to spills, or for cleaning smaller, confined spaces where navigating a full-sized janitorial cart would be impractical or disruptive. By ensuring that all necessary small tools and chemical solutions are readily available, caddies significantly boost productivity and allow cleaning staff to focus on the task at hand.
Cleaning caddies come in several designs to suit various operational needs:
- Handheld Caddies: These are typically open-topped containers, often made of durable plastic, with a central handle for easy carrying. They offer maximum portability and are ideal for moving quickly between rooms or workstations. Many feature multiple compartments to keep supplies organized and upright.
- Cart-Mounted Caddies: Some caddies are specifically designed to nest securely within the openings of janitorial carts, often in the space allocated for a trash bag or on dedicated shelving. This integration allows for better organization on the main cart and enables the caddy to be easily removed for focused tasks.
- Bucket-Mounted Caddies: These innovative designs, such as the Rubbermaid BRUTE Rim Caddy, attach to the rim of standard cleaning buckets. They provide convenient storage for spray bottles, cloths, brushes, and other small items, effectively adding utility to an existing bucket without requiring extra carrying.
The essential contents of a well-stocked cleaning caddy can be tailored to specific cleaning zones or tasks, but typically include items such as an all-purpose cleaner, glass cleaner, disinfectant spray or wipes, a set of microfiber cloths for different surfaces, a scrub brush or scouring pad, protective rubber gloves, and a few spare trash bags.
For example, a restroom cleaning caddy would prioritize toilet bowl cleaner, disinfectant, and specific brushes, while a caddy for general office dusting and surface wiping might focus on microfiber cloths, a neutral cleaner, and glass cleaner.
Cleaning caddies are instrumental in effectively implementing “zone cleaning” or “task-based cleaning” methodologies. These approaches involve assigning cleaners to specific areas (zones) or specific types of tasks (e.g., all dusting, all vacuuming) within a facility.
A well-organized caddy, stocked with the precise tools and chemicals needed for that zone or task, allows the cleaner to work with maximum efficiency and focus. For instance, if a cleaner is assigned to sanitize all high-touch surfaces in an office wing, a caddy containing disinfectant, microfiber cloths, and gloves ensures they have everything required without needing to pick through a general-purpose cart or return to a supply closet.
This not only improves speed but also helps ensure the correct products are used for each application and reduces the risk of cross-contamination by dedicating specific tools (or caddy contents) to particular zones, such as restrooms versus food preparation areas. The strategic use of multiple, specialized caddies can significantly enhance the operational efficiency and hygiene standards of cleaning teams, particularly in larger facilities with diverse cleaning requirements. It standardizes toolsets for common tasks and supports more rigorous hygiene protocols.
Tool Holders & Hooks: Enhancing Organization and Tool Longevity
Tool holders and hooks are simple yet highly effective accessories designed to provide organized storage for long-handled cleaning implements such as mops, brooms, dusters, and squeegees. These can be wall-mounted units, ideal for janitorial closets and storage rooms, or integrated directly into the design of cleaning carts and trolleys. Available options range from individual clips and hooks to multi-tool racks and sophisticated shadow boards, constructed from materials like durable plastic, stainless steel for hygiene and longevity, or lightweight aluminum.
These accessories play a vital role in maintaining an orderly cleaning environment, which directly contributes to efficiency and safety.
- Wall-Mounted Systems: Typically installed in janitorial closets or dedicated storage areas, these systems keep tools neatly arranged, off the floor, and readily accessible. This prevents clutter, makes it easier to find the right tool quickly, and utilizes vertical space efficiently.
- Cart-Integrated Systems: Hooks, clips, and brackets built into janitorial carts ensure that essential long-handled tools are secure during transit and always within reach when performing mobile cleaning tasks. This prevents tools from falling off the cart or being leaned precariously, which can cause damage or create hazards.
The advantages of using dedicated tool holders and hooks are multifaceted:
- Tool Care and Longevity: Proper storage protects tools from damage. For instance, mop heads and broom bristles are less likely to be crushed or misshapen if hung correctly, extending their effective lifespan. Storing equipment with the head down can also prevent contamination from running down handles and cross-contaminating hands or other surfaces.
- Safety: Keeping tools off the floor and securely stowed significantly reduces trip-and-fall hazards for cleaning staff and other facility occupants. This is a critical aspect of maintaining a safe working environment.
- Efficiency and Workflow: An organized system where every tool has a designated place saves time previously wasted searching for misplaced items. Shadow boards, which feature outlines of tools on a backing board, provide an immediate visual cue for where each tool belongs and quickly indicate if something is missing. This visual management improves workflow and accountability.
- Hygiene and Cross-Contamination Prevention: Some tool holding systems are color-coded or can be used in conjunction with color-coded tools to support hygiene protocols, ensuring that tools designated for specific areas (e.g., restrooms vs. kitchens) are kept separate and not inadvertently used elsewhere, thus minimizing the risk of cross-contamination.
Best practices for implementing tool holders include selecting holders appropriate for the weight and size of the tools being stored. Tools should ideally be stored with their heads down to allow for proper drying and to prevent contaminants from dripping onto handles. When arranging tools on a rack or board, consideration should be given to spacing to prevent equipment from dripping onto the critical surfaces of tools stored below.
The systematic use of tool holders and hooks aligns directly with the principles of 5S lean management (Sort, Set in Order, Shine, Standardize, Sustain), which are aimed at eliminating waste and improving efficiency through workplace organization. In a janitorial context:
- Sort: Tool holders encourage keeping only necessary and functional tools, prompting the disposal of broken or redundant items.
- Set in Order: They provide a clearly defined, designated location for every tool, making them easy to find and return. Shadow boards are an exemplary application of this principle.
- Shine: A tidy and organized tool storage area is inherently easier to keep clean and inspect.
- Standardize: Consistent use of holders and a defined layout establishes a standard for tool storage across the cleaning operation.
- Sustain: Well-designed, easy-to-use, and visually intuitive storage systems, like clearly labeled holders or shadow boards, help maintain the organized state over the long term. Implementing proper tool storage is, therefore, not merely about tidiness; it is a strategic lean management practice for janitorial services. This approach can lead to quantifiable benefits such as reduced time spent searching for tools, less frequent tool replacement due to damage or loss, fewer workplace accidents, and an overall more professional and disciplined approach to cleaning tasks. For cleaning companies, such operational excellence can serve as a competitive differentiator.
3. Applying Cleaning Agents and Managing Solutions
The effective application of cleaning agents and the careful management of chemical solutions are central to achieving desired cleanliness and hygiene standards. A range of accessories is dedicated to these tasks, from precision sprayers to versatile buckets and accurate measuring tools, each playing a role in safety, efficacy, and resource optimization.
Spray Bottles & Sprayers: Precision Application
Spray bottles are indispensable tools in janitorial work, used for applying a wide variety of cleaning solutions, disinfectants, sanitizers, and other liquid chemical products. They allow for controlled application, helping to ensure that surfaces are adequately covered without excessive use of chemicals. These accessories range from simple, manually operated trigger sprayers to more sophisticated pump-up sprayers designed for larger tasks or specific application needs.
The types of spray bottles and sprayers commonly used include:
- Standard Trigger Spray Bottles: These are the most common type, typically made of plastic, and are suitable for general-purpose cleaning tasks where small to moderate amounts of liquid need to be applied directly to surfaces or onto cleaning cloths. The nozzle on these sprayers is often adjustable, allowing for a stream or a spray pattern.
- Pump-Up Sprayers (Compression Sprayers): These sprayers feature a reservoir that is pressurized by manual pumping. Once pressurized, they can deliver a continuous spray without constant trigger action, making them ideal for covering larger areas such as walls, partitions, or equipment, or for tasks like pest control or disinfection of broader surfaces. They come in various capacities, from handheld models to larger tank sprayers (e.g., 1-3 gallons). Many industrial pump sprayers are designed for durability, with reinforced hoses, robust seals, and adjustable nozzles that can produce anything from a fine mist to a coarse stream.
- Specialized Sprayers (Continuous, Mist, Fine Mist): Some sprayers are engineered to produce specific types of spray. Continuous spray bottles, often utilizing advanced trigger mechanisms or bag-in-bottle technology, deliver a sustained mist with a single pull or prolonged press, reducing hand fatigue during extended use. Mist spray bottles are designed to deliver a fine, even mist over a broad area, which is beneficial for applications requiring uniform coverage with minimal product waste, such as air fresheners or some disinfectants. Fine mist sprayers produce an even finer particle size, often preferred for delicate applications or when a very light coating is desired.
The material of the spray bottle itself is a crucial consideration, primarily due to chemical compatibility:
- Plastic (e.g., HDPE, PET): The most common material due to its light weight, impact resistance, and cost-effectiveness. However, not all plastics are compatible with all chemicals; some solvents or highly acidic/alkaline solutions can degrade certain types of plastic over time. It’s essential to choose a plastic bottle rated for the chemicals being used.
- Glass: Offers excellent chemical resistance and is non-reactive, making it suitable for storing and spraying sensitive chemicals, essential oils, or when a premium feel is desired. However, glass is fragile and heavier than plastic.
- Metal (e.g., Aluminum): Provides durability and a high-end appearance but, like plastic, may have limitations regarding chemical compatibility, as some chemicals can react with metal.
The choice of sprayer technology—encompassing nozzle design, the ability to generate specific mist particle sizes, and the consistency of pressure—directly influences both the efficacy of the cleaning chemicals used and the overall consumption of those chemicals. A sprayer that produces an overly coarse or uneven spray pattern can lead to over-application in some areas and under-application in others.
This not only wastes product but can also result in ineffective cleaning or disinfection where coverage is insufficient, or potential surface damage where chemicals are over-applied. Conversely, a sprayer that delivers a fine, consistent, and even mist can provide better surface coverage with less chemical volume, thereby enhancing the effectiveness of the product and reducing operational costs.
This is particularly relevant for large-scale disinfection or application tasks where pump sprayers are employed. Investing in higher-quality sprayers with appropriate nozzle technology tailored to specific chemicals and tasks can therefore lead to significant savings in chemical expenditure over time, ensure more consistent and reliable cleaning outcomes, and even contribute to better air quality by minimizing overspray and the release of volatile organic compounds (VOCs).
Best practices for using and maintaining spray bottles and sprayers are vital for safety and longevity. Always hold the sprayer at the recommended distance from the surface and avoid over-spraying to the point of dripping or running, which wastes product and can damage sensitive materials. It is critical to properly label all spray bottles, especially those containing diluted solutions, clearly indicating their contents and any relevant hazard information, in accordance with workplace safety regulations (e.g., Right to Know rules).
After use, particularly with pump sprayers, they should be depressurized. All sprayers should be rinsed and cleaned regularly, especially when changing chemicals, to prevent clogging of nozzles, cross-contamination, and degradation of sprayer components. For pump sprayers, maintenance may also include checking and cleaning filters, inspecting hoses and seals for wear, and lubricating moving parts as per manufacturer recommendations to ensure optimal performance and extend their service life.
Buckets: Versatile Containment for Cleaning Tasks
Buckets are among the most fundamental and versatile accessories in any janitorial toolkit, serving as essential containers for water, cleaning solutions, and sometimes for carrying tools or collecting waste during specific tasks. They are available in a variety of types, materials, and sizes, each suited to different cleaning applications.
General-Purpose Utility Pails:
These are typically simpler in design, often lightweight, and feature a single sturdy handle for easy transportation of water or cleaning solutions. They are indispensable for a multitude of hands-on cleaning jobs, such as wiping down surfaces, sanitizing equipment, spot-cleaning floors, or preparing small batches of diluted chemicals.
Materials commonly include durable plastics (polypropylene or polyethylene), which are lightweight and resistant to many chemicals, or metals like galvanized steel or stainless steel, which offer greater rigidity and longevity, particularly for heavy-duty tasks not involving corrosive substances. Some utility pails are designed with features like molded pour spouts for easier, spill-free emptying, or internal compartments for holding sponges, cloths, or small tools, enhancing their convenience for specific tasks.
Mop Buckets:
These are specialized buckets designed primarily for floor mopping and almost invariably incorporate a wringer mechanism to control the wetness of the mop head. The type of wringer is a key differentiator:
- Down-Press Wringers: These require the user to push the mop handle downwards into the wringer mechanism. They are generally considered efficient at expelling water and often require less physical effort to operate compared to side-press models, with the handle located above the bucket.
- Side-Press Wringers: These have a lever on the side of the wringer that is pressed to squeeze water from the mop head. While they may require more pressure, they are a common and effective design.
- Funnel-Type Wringers: These are simpler, often more economical wringers without moving parts. The mop head is pushed into a funnel-shaped cone to squeeze out water. They offer good control over mop wetness and are sometimes preferred in environments with safety concerns about moving parts, such as correctional facilities.
Modern mop buckets often incorporate additional features to enhance cleaning effectiveness and user convenience:
- Wave-Breaking Designs: Internal baffles or specific shaping of the bucket can reduce splashing and spillage when the bucket is moved or when the mop is agitated, helping to keep surrounding areas dry and safe.
- Separate Dirty Water Compartments (Dual-Bucket Systems): This is a significant hygiene-enhancing feature. One compartment holds the clean cleaning solution, and the other collects the dirty water wrung from the mop. This prevents the cleaning solution from becoming quickly contaminated with the dirt and debris being removed from the floor, leading to a more hygienic clean.
- Casters: Most commercial mop buckets are equipped with durable, smooth-rolling casters (wheels) for easy mobility across floors, reducing the need to lift and carry heavy buckets.
- Foot Pedal Drains: Some models feature a drain plug at the bottom that can be opened with a foot pedal, allowing for easy emptying of the bucket into a floor drain or mop sink without heavy lifting.
- Integrated Caddies or Holders: Some mop buckets may include small caddies or hooks for carrying spray bottles, scrapers, or extra cleaning cloths.
The evolution of mop bucket design, particularly the widespread adoption of features like dual compartments for separating clean and dirty water and technologies like “wave-breaking” baffles, directly reflects a growing industry emphasis on not just cleaning for appearance, but cleaning for health and hygiene. The traditional single-bucket mopping method inherently involves re-dipping a soiled mop into an increasingly contaminated solution, which can lead to the redistribution of dirt and microorganisms rather than their effective removal.
The innovation of dual-compartment systems directly addresses this fundamental flaw. By keeping the cleaning solution relatively cleaner for a longer period, these systems improve the actual removal of soil and pathogens. Similarly, wave-breaking designs reduce splashes of dirty water, further containing contaminants and enhancing safety.
This shift in design signifies a move towards more scientifically-backed cleaning practices. For facilities where hygiene is paramount, such as healthcare settings, food service establishments, and schools, mop buckets with these advanced features are no longer a luxury but a necessity for effective infection control and maintaining high public health standards. This also impacts overall cleaning efficacy, as cleaner water and solution inherently clean more effectively.
Color-Coding for Safety and Cross-Contamination Prevention:
A crucial practice in professional janitorial services is the use of color-coded cleaning equipment, including buckets (and mops, cloths, etc.). This system involves assigning specific colors to tools used in different areas or for different tasks to prevent cross-contamination. For example:
- Red might be designated for high-risk areas like restrooms (toilets and urinals).
- Yellow for other restroom surfaces (sinks, counters).
- Blue for general cleaning in lower-risk areas (offices, classrooms – dusting, window cleaning).
- Green for food preparation and service areas. This visual system helps ensure that a bucket used to clean a restroom is never inadvertently used in a kitchen, thereby minimizing the spread of bacteria and other pathogens. Some red buckets are specifically labeled for sanitizer, aiding in two-step clean-then-sanitize processes. Adherence to a color-coding scheme is vital for meeting Hazard Analysis Critical Control Point (HACCP) guidelines in food service and for general infection control in all environments.
Materials for buckets are typically robust plastics like polypropylene for general utility and many mop buckets, prized for their chemical resistance, durability, and lighter weight. Stainless steel is sometimes used for pails or components of high-end mop buckets due to its exceptional durability and corrosion resistance, though it adds to weight and cost.
Measuring Cups & Spoons: Accuracy in Chemical Dilution
The accurate dilution of concentrated cleaning chemicals is a fundamental aspect of professional cleaning, directly impacting safety, effectiveness, and cost-control. Measuring cups and spoons are essential accessories for achieving this precision. Many professional cleaning products are supplied in concentrated form to reduce packaging, transportation costs, and storage space. However, these concentrates must be diluted with water to the correct ratio before use.
The importance of precise measurement cannot be overstated:
- Safety: Concentrated chemicals can be corrosive, irritant, or otherwise hazardous if handled improperly or used at full strength. Diluting them to the manufacturer’s recommended levels makes them significantly safer for cleaning staff to handle and for use on surfaces without causing harm to occupants or the surfaces themselves. Incorrectly high concentrations can lead to skin irritation, respiratory issues, or damage to materials.
- Effectiveness: Cleaning chemicals are formulated to work optimally at specific concentrations. If a solution is too weak (over-diluted), it may not effectively clean, disinfect, or sanitize as intended, leaving behind dirt, germs, or failing to remove stains. If it’s too strong (under-diluted), it can damage surfaces (e.g., etch stone, discolor fabrics, craze plastics), leave residues, or even be less effective if the chemical action is impeded by excessive concentration.
- Cost-Control: Concentrated chemicals are economical only when diluted correctly. Overuse of concentrate by making solutions too strong leads to rapid depletion of stock and significantly increased chemical costs. Accurate dilution ensures that the product yields the number of usable gallons specified by the manufacturer, maximizing value.
When selecting measuring cups and spoons for janitorial use, certain features are recommended:
- Chemical Resistance: The measuring tools should be made from materials that are resistant to the chemicals being handled. Plastics like polypropylene or polyethylene are common, but for very aggressive chemicals, glass or specialized chemical-resistant plastics might be necessary.
- Clear and Durable Markings: Graduations should be clearly marked, easy to read, and durable enough to withstand repeated use and exposure to chemicals without fading or wearing off. Markings in both metric (milliliters) and imperial (ounces, cups) units can be beneficial.
- Appropriate Sizes: A range of sizes for both cups and spoons allows for accurate measurement of various volumes, from small amounts for spray bottles to larger quantities for mop buckets.
Safe dilution practices are paramount:
- Always Read the Label: The product label and Safety Data Sheet (SDS) provide specific instructions for dilution ratios, necessary PPE, and handling precautions.
- Wear Appropriate PPE: This typically includes chemical-resistant gloves and eye protection (goggles or face shield) to prevent skin and eye contact.
- Add Water First, Then Chemical: When diluting, it is generally recommended to add the water to the mixing container first, followed by the concentrated chemical. This helps prevent splashing of the concentrate and can avoid potentially violent reactions with some chemicals.
- Measure Accurately: Use the designated measuring cups or spoons to measure both the water (if not using a pre-filled container) and the chemical concentrate precisely.
- Mix Gently: Stir the solution gently to ensure thorough mixing without creating excessive fumes or splashes.
- Never Mix Different Chemicals: Unless specifically instructed by manufacturers, never mix different cleaning chemicals together, as this can produce hazardous gases or negate their effectiveness.
- Properly Label Diluted Solutions: All containers holding diluted solutions must be clearly and accurately labeled with the product name, dilution ratio, and any relevant hazard warnings.
The accuracy of chemical dilution, facilitated by appropriate measuring tools and adherence to correct procedures, should be regarded as a key performance indicator (KPI) for janitorial operations.
This is because it directly influences cleaning outcomes, chemical expenditure, staff safety, and environmental responsibility. Inconsistent dilution practices can lead to variable cleaning quality, potential damage to facility assets (requiring costly repairs or replacements), wasted chemical resources (thereby increasing operational costs), and an elevated risk of chemical exposure incidents for staff. Furthermore, improper dilution can result in the discharge of overly concentrated or improperly neutralized chemicals into wastewater systems, posing environmental concerns.
By implementing standardized dilution procedures, providing the correct measuring tools, thoroughly training staff on their use, and potentially conducting periodic audits of dilution accuracy, cleaning departments or service providers can achieve significant improvements in operational consistency, cost management, safety records, and sustainability metrics. This elevates a seemingly minor preparatory task to a strategic operational control point, with far-reaching benefits. Chemical dispensing systems, which automatically dilute concentrates, are also an option for ensuring accuracy and safety, particularly in high-volume usage scenarios.
Dispensers: Hygienic and Efficient Resource Management
Dispensers for consumable janitorial supplies, primarily paper towels and soap in washrooms and other hygiene-critical areas, are far more than mere conveniences. They are integral components of a facility’s hygiene infrastructure, playing a crucial role in promoting health, managing resources efficiently, and contributing to the overall cleanliness and professional appearance of the environment.
Paper Towel Dispensers:
These devices are designed to provide users with a hygienic means of drying their hands. Effective hand drying is a critical step in the hand hygiene process, as wet hands can spread bacteria much more effectively than dry hands—reportedly up to 1,000 times more. Paper towel dispensers come in several types:
- Lever/Crank Dispensers: These require manual operation of a lever or crank to dispense a towel.
- Pull-Down Dispensers: These typically dispense pre-cut towels or allow the user to pull a length of towel from a roll, which is then torn off.
- Automatic (Touch-Free) Dispensers: These are sensor-activated and dispense a towel without any physical contact from the user. They are considered the most hygienic option as they significantly minimize the risk of cross-contamination between users.
The benefits of using paper towel dispensers extend beyond hygiene:
- Waste Reduction and Cost Control: Many dispensers, particularly automatic or controlled-pull models, are designed to dispense a set amount or length of towel per use. This controlled dispensing helps to reduce excessive consumption and waste, ultimately leading to cost savings on paper towel supplies. While the initial investment in an automatic dispenser might be higher, the long-term savings in paper costs and reduced janitorial labor for refilling and waste removal can offset this.
- Environmental Considerations: Environmentally conscious organizations can opt for dispensers that accommodate recycled paper towels. Pairing such dispensers with biodegradable or recyclable towels can significantly reduce the ecological footprint of a facility’s washroom operations.
- Aesthetics and User Perception: Modern paper towel dispensers are available in sleek, compact designs and various finishes to complement interior aesthetics, demonstrating that practicality and style can coexist. A well-maintained, functional dispenser contributes to a positive user experience and reflects well on the facility’s attention to detail and care for its occupants.
- Health and Safety Compliance: In many jurisdictions, providing a means for hand drying in washrooms is a requirement under health and safety regulations, making paper towel dispensers essential for compliance in workplaces and public facilities.
Soap Dispensers:
Soap dispensers are equally critical for promoting effective handwashing, which is the single most important measure for preventing the spread of infections.
- Types: Like paper towel dispensers, soap dispensers are available in manual (push-button or lever) and automatic (touch-free, sensor-operated) versions. Touch-free models are particularly effective in enhancing hygiene by minimizing direct contact with the dispenser surface, thereby reducing the potential for germ transmission from one user to another. This is especially important in public and high-traffic washrooms.
- Advantages:
- Enhanced Hygiene: By eliminating shared, potentially contaminated bar soaps or messy refillable bottles, dispensers reduce the spread of germs.
- Controlled Dispensing: Dispensers deliver a precise, measured amount of soap with each use. This ensures that users apply an adequate quantity for thorough hand cleaning while simultaneously preventing wastage from overuse. This controlled dispensing helps standardize the handwashing process and manage soap consumption efficiently.
- Reduced Waste and Cost Savings: By controlling the amount of soap dispensed, overall soap consumption is lowered, reducing the frequency of refills and contributing to cost savings on supplies. Many commercial soap dispensers are designed for bulk soap refills, which are generally more cost-effective per use and generate less packaging waste compared to individual, single-use soap bottles. This reduction in plastic waste also supports environmental sustainability goals.
- Streamlined Process: Dispensers simplify and expedite the handwashing process, especially in busy environments, by providing an easy and efficient means of accessing soap without fumbling with caps or pumps on individual bottles, which can also lead to spills and messes.
Well-designed and properly functioning dispensers, particularly touch-free soap and paper towel dispensers, act as subtle but effective behavioral nudges. They encourage better hand hygiene practices among facility users by making the process easier, more convenient, and more appealing. If a soap dispenser is empty, broken, difficult to use, or appears unhygienic, individuals are less likely to wash their hands properly, or perhaps at all.
Conversely, an easily accessible, reliably functioning, touch-free dispenser that provides an adequate amount of soap and is followed by a similar paper towel dispenser makes the desired behavior (thorough handwashing and drying) simpler and more likely to be performed correctly.
This can contribute significantly to a reduction in the spread of illnesses within that environment, leading to tangible benefits such as reduced absenteeism due to illness in workplaces or schools, and a generally healthier environment for everyone. Investing in reliable, user-friendly dispensers is, therefore, an investment in the collective health and well-being of a building’s occupants and demonstrates a facility’s commitment to high hygiene standards. The aesthetic appeal of clean, modern dispensers also plays a role, enhancing user confidence in the overall cleanliness and care provided by the facility.
When selecting dispensers for different environments, factors to consider include the expected volume of traffic, available space, the type of users (e.g., adults, children, individuals with disabilities), the existing decor of the room, and both the initial and ongoing costs (including refills and maintenance). For instance, high-traffic public washrooms benefit most from durable, high-capacity, automatic dispensers to minimize refill frequency and maximize hygiene.
4. Ensuring Safety and Managing Waste
A cornerstone of any professional cleaning regimen is the diligent management of safety and waste. This involves not only protecting cleaning staff and facility occupants from potential hazards created during cleaning operations but also ensuring the efficient and hygienic containment and disposal of waste. Key accessories in this domain include warning signs, protective gloves, and appropriate trash bags or can liners.
Warning Signs: Preventing Accidents in Cleaning Zones
Janitorial warning signs are indispensable safety accessories used to alert individuals to potential temporary hazards associated with cleaning activities. Their primary purpose is to prevent accidents, particularly slips, trips, and falls, which are common occurrences in commercial settings, often resulting from wet floors during or after mopping, or from equipment left in walkways. Beyond immediate hazard alerts, these signs also serve to inform building occupants that cleaning is in progress, encouraging them to avoid freshly cleaned areas, which helps prevent re-soiling and allows cleaning solutions or floor finishes to dry undisturbed.
Common types of janitorial warning signs include:
- “Wet Floor” Signs: These are perhaps the most ubiquitous, typically A-frame or cone-shaped signs placed prominently where floors have been recently mopped, waxed, or where spills have occurred.
- “Cleaning in Progress” Signs: These provide a general alert that cleaning activities are underway in a specific area, cautioning individuals to be aware of potential obstructions, noise, or temporary access restrictions.
- “Restricted Area” or “Closed for Cleaning” Signs: Used to temporarily block off access to an area while intensive cleaning, disinfection, or maintenance is performed, ensuring the safety of occupants and the integrity of the cleaning process.
- “Trip Hazard” Signs: These warn of potential tripping dangers such as cables, hoses, uneven surfaces, or equipment temporarily placed in a pathway.
- Color-Coding Guideline Signs: While not hazard warnings in the same sense, these signs can be posted in janitorial closets to guide staff on the correct use of color-coded cleaning equipment for different areas, thereby supporting cross-contamination prevention protocols.
The consistent and correct use of warning signs is crucial for liability management and demonstrating a commitment to safety compliance. By providing clear visual warnings, facilities can significantly reduce the likelihood of accidents and associated costs, including injuries, lost work time, and potential legal claims.
For warning signs to be effective, their design and placement are critical:
- Visibility: Signs should feature high color contrast (e.g., bright yellow background with black text/symbols) and be made of reflective material if used in low-light conditions.
- Legibility: The text and any accompanying pictograms should be large, clear, and easily understandable from a distance. Universally recognized symbols are often preferred.
- Placement: Signs must be placed strategically at eye level (for standing signs) or directly on the floor (for floor-standing signs), in well-lit areas, and ensuring a clear line of sight from all approach directions. Crucially, they should be positioned near the actual hazard they are addressing, effectively warning individuals before they encounter the dangerous condition. For example, wet floor signs should be placed at all entrances to a wet area.
Janitorial warning signs function as more than just immediate alerts to physical hazards. They act as broader communication tools that manage expectations, guide behavior, and reinforce a culture of safety and respect for the cleaning process within a facility.
A “Cleaning in Progress” sign, for instance, does more than just warn of a potential slip; it communicates that an area is temporarily out of normal use and implicitly requests cooperation from occupants. This can reduce frustration and allow cleaning staff to work more efficiently and safely. Instructional signs related to hygiene protocols, such as those for hand-washing techniques or waste disposal, also educate and encourage desired behaviors throughout the facility.
A comprehensive signage strategy, encompassing both acute hazard warnings and more general instructional or informational signs, contributes to a smoother, safer, and more respected cleaning operation. It fosters a sense of partnership between cleaning staff and facility occupants, where occupants understand and support the cleaning efforts, leading to a cleaner and safer environment for everyone. This elevates signage from a mere compliance item to an active tool for operational management, safety promotion, and cultural reinforcement.
Gloves: Essential Personal Protective Equipment (PPE)
Gloves are a fundamental piece of personal protective equipment (PPE) for janitorial staff, offering crucial protection for the hands against a variety of hazards encountered during cleaning tasks. These hazards include exposure to harsh cleaning chemicals and detergents, contact with dirt, grime, and potentially infectious microorganisms (germs and bacteria), and physical abrasion. Proper glove use helps prevent skin irritation, dermatitis, chemical burns, and the transmission of pathogens, safeguarding the health of the cleaning professional and preventing cross-contamination to other surfaces or individuals.
A variety of glove materials are available, each with distinct properties, advantages, and disadvantages, making material selection critical based on the specific tasks and chemicals involved:
Material | Key Properties (Durability, Puncture Resistance, Flexibility/Fit, Dexterity) | Chemical Resistance (General, Acids, Bases, Solvents, Oils) | Allergy Risk | Common Janitorial Applications | Pros | Cons |
---|---|---|---|---|---|---|
Nitrile | Good to excellent durability, high puncture resistance, good flexibility and snug fit, good dexterity. | Good to excellent resistance to many chemicals, including oils, greases, solvents, some acids, and bases. Preferred for broad chemical resistance. | Low | Heavy-duty cleaning, handling disinfectants, solvents, degreasers, waste handling, tasks requiring good tactile sensitivity and protection against punctures or tears. Often a default choice for general janitorial work. | Durable, highly puncture-resistant, good chemical barrier, latex-free (prevents latex allergies), tends to rip visibly when punctured (alerting user). | Can be more costly than latex or vinyl, may offer less elasticity or tactile sensitivity than latex for some users. |
Latex (Natural Rubber) | Good durability, good puncture resistance (but less than nitrile), excellent flexibility and snug fit, excellent dexterity. | Good for biological hazards and water-based solutions. Good resistance to acids, bases, alcohols. Poor for organic solvents, oils, and greases. | High | General cleaning with water-based detergents, handling biological waste (if no allergy), tasks requiring high dexterity and tactile sensitivity. | Very flexible, comfortable, excellent fit and dexterity, good barrier against bacteria and viruses. | Significant risk of latex allergies for user or those they contact, can degrade with exposure to oils and certain chemicals, punctures may not be easily visible. |
Vinyl (PVC) | Fair durability, lower puncture resistance (tears easily), looser fit, fair dexterity. | Limited chemical resistance; suitable for some common acids and alcohols. Not recommended for strong solvents or prolonged chemical exposure. | Low | Light-duty cleaning tasks, food handling (some types), situations requiring frequent glove changes and where chemical exposure is minimal or brief (e.g., quick wipe-downs with mild detergents). | Economical, latex-free, soft and comfortable for short-term wear. | Less durable, more susceptible to punctures and tears, offers limited chemical protection, looser fit can reduce dexterity. Releases phthalates with some chemicals. |
Rubber (General Purpose/Reusable, e.g., Neoprene, Butyl) | Varies by specific rubber type; generally thicker and more durable than disposable gloves. Neoprene offers good abrasion resistance. Butyl is less physically robust. | Neoprene: Good for acids, bases, alcohols, fuels, peroxides, oils, greases. Butyl: Good for ketones, esters; poor for gasoline, hydrocarbons. | Low to Moderate (depending on specific rubber) | Heavy-duty scrubbing, handling concentrated chemicals (select material based on specific chemical), tasks requiring robust physical protection or extended immersion. Neoprene is good for oily/dirty situations and uneven surfaces. | Often thicker providing better physical protection, can be reusable (cost-effective if properly maintained), specific types offer excellent resistance to aggressive chemicals. Neoprene is durable and flexible. | Can be less dexterous due to thickness, requires thorough cleaning and drying to prevent contamination if reused. Some janitorial teams find reusable gloves get “dingy” and prefer disposable for sanitation. Specific rubbers can be expensive. |
The choice between disposable and reusable gloves depends on the specific application, hygiene requirements, and cost considerations:
- Disposable Gloves (Nitrile, Latex, Vinyl): These are designed for single use and are discarded after each task or when compromised. Their primary advantage is in preventing cross-contamination, as a fresh pair can be used for different areas or tasks, ensuring that germs are not transferred. They are convenient, require no cleaning or maintenance, and can be cost-effective when purchased in bulk, especially when factoring in the labor saved from not having to wash reusable gloves. Disposable gloves are generally preferred for tasks requiring high levels of hygiene or involving contact with potentially infectious materials.
- Reusable Gloves (Often thicker rubber, neoprene, or butyl): These are designed for multiple uses and are typically more robust, offering better protection against abrasions, cuts, and prolonged exposure to certain chemicals. They can be more economical for specific heavy-duty tasks if properly cared for. However, they require meticulous cleaning, disinfection, and drying after each use to prevent them from becoming a source of contamination. If not maintained properly, they can harbor bacteria and odors. Some find that thicker reusable gloves can reduce dexterity and tactile sensitivity. For many janitorial services, the enhanced sanitation and convenience of disposable gloves often outweigh the potential durability benefits of reusables, especially in environments where hygiene is paramount.
When selecting gloves, key factors to consider include the type of chemicals being handled (refer to Safety Data Sheets for compatibility), the physical hazards present (e.g., risk of punctures from sharps), the required level of dexterity for the task, the duration of wear, and any potential allergies of the wearer. For general janitorial duties involving a range of cleaning agents, nitrile gloves are often a suitable and popular choice due to their balanced profile of chemical resistance, durability, and being a latex-free option.
While various glove materials have their place, there is an observable trend and a growing preference towards nitrile gloves as a default option in many professional janitorial settings. This shift is driven by nitrile’s advantageous combination of good chemical resistance against a variety of common cleaning agents, superior durability and puncture resistance compared to latex or vinyl, and reasonable tactile sensitivity.
Crucially, nitrile is a synthetic material and therefore does not pose the risk of latex allergies, which are a significant occupational health concern in workplaces where latex gloves were historically common. Vinyl gloves, while inexpensive, generally offer a lower level of protection and durability, making them less suitable for many professional cleaning tasks.
Nitrile gloves emerge as a versatile and reliable compromise, offering better overall protection and broader applicability than vinyl, while avoiding the allergy issues associated with latex. This preference reflects a heightened awareness of occupational health and safety standards and a demand for more dependable performance in professional cleaning operations. Although nitrile gloves may sometimes be more costly than vinyl or latex options , the benefits in terms of reduced risk, enhanced worker safety, and suitability for a wider range of tasks often justify the investment for professional organizations.
Trash Bags / Can Liners: Effective Waste Containment
Trash bags, also known as can liners, are fundamental accessories for effective waste management in any facility. Their primary role is to contain waste hygienically, prevent bins from becoming soiled, simplify the emptying process, and minimize odors and the spread of contaminants. Choosing the correct size, strength, and material for can liners is essential for operational efficiency, cost-effectiveness, and preventing issues like spills, tears, and overflows.
Can liners vary significantly in several key aspects:
- Sizes: Liners are available in a wide array of sizes to fit various trash receptacles, from small 4-9 gallon bags suitable for desk-side bins or restroom wastebaskets, to medium 10-13 gallon bags for kitchen cans, large 14-30 gallon bags for office or commercial use, and extra-large 32-60 gallon (or even larger) liners for industrial applications or outdoor containers. Selecting the correct size ensures the bag fits the can properly, preventing it from slipping in or being too small to utilize the can’s full capacity. Formulas exist to calculate the appropriate bag width and height based on the dimensions of round or rectangular cans.
- Strength (Thickness): The strength or thickness of a can liner is a critical factor in its performance and is typically measured in one of two units:
- Mils: A mil is one-thousandth of an inch (0.001 inch). This unit is commonly used to measure the thickness of Low-Density Polyethylene (LDPE) liners. LDPE liners typically range from around 0.30 mils for very light duty to 6.0 mils or more for extremely heavy-duty applications.
- Microns: A micron (micrometer) is one-millionth of a meter. This unit is commonly used for measuring the thickness of High-Density Polyethylene (HDPE) liners. HDPE liners can range from as thin as 6 microns for light waste to 24 microns or more for heavier applications. It’s important to note that regardless of whether the measurement is in mils or microns, a larger number generally indicates a thicker and more durable liner within its respective material type.
- Materials (Resin Types): The two primary types of plastic resin used to manufacture can liners offer different properties:
- Low-Density Polyethylene (LDPE) Liners: These liners are generally thicker, more flexible, and offer superior stretch and puncture/tear resistance compared to HDPE liners of similar application intent. This makes them ideal for containing waste that is sharp, heavy, or irregularly shaped, such as construction debris, food waste containing bones or sharp packaging, yard waste with twigs, or items that might stretch or poke the bag. They are commonly used in kitchens, restaurants, healthcare facilities (for certain waste streams), and for industrial or outdoor applications where toughness is paramount.
- High-Density Polyethylene (HDPE) Liners: These liners are made from a resin that allows them to be thinner yet still possess good strength for their gauge, though they have less stretch and are more susceptible to puncture from sharp objects than LDPE. HDPE liners are a cost-effective option for disposing of lighter, softer, and less rigid waste, such as paper, office trash, or restroom waste (e.g., paper towels). Because they use less plastic material overall for a given capacity (when appropriate for the waste type), they can be a more environmentally friendly and economical choice when puncture resistance is not a primary concern.
The suitability of a can liner for different janitorial tasks and waste types is determined by matching these variations to the specific demands:
- For light, dry waste in offices or restrooms where sharp objects are unlikely, thinner HDPE liners (e.g., 6-12 microns) are often sufficient and cost-effective.
- For medium-duty trash in cafeterias or kitchens with mixed waste like food scraps and paper/plastic containers, a mid-range HDPE liner (e.g., 12-17 microns) or a lighter-duty LDPE liner might be appropriate.
- For heavy-duty trash, construction debris, or waste containing sharp or jagged items (glass, metal, wood), thicker LDPE liners (e.g., 1.0 mil to 3.0+ mil) are necessary to prevent punctures and tears.
- For extra-heavy-duty or bulky waste in manufacturing facilities, warehouses, or outdoor public spaces, the thickest HDPE liners (e.g., 17-25 microns) or robust LDPE liners are recommended.
A common misconception when selecting can liners is that “thicker is always better.” While thickness (gauge) is an indicator of strength, the type of resin (LDPE vs. HDPE) and its inherent properties (flexibility, puncture resistance, stretch) are equally, if not more, critical in determining a liner’s suitability for a specific application.
For example, an HDPE liner might have a lower micron value than an LDPE liner’s mil value, yet still be appropriate for its intended load if that load consists of soft paper waste. Using a very thick and expensive LDPE liner for light office paper waste is an unnecessary expense and an inefficient use of resources. Conversely, opting for a thinner HDPE liner to save costs when dealing with construction debris containing sharp edges will inevitably lead to bag failures, spills, and increased labor for cleanup, thereby negating any initial savings on the liner itself.
Understanding the distinct characteristics of LDPE (thicker, more stretch, better for sharps) versus HDPE (thinner for its strength, less stretch, good for soft/bulky waste) and guiding selection based on the specific nature of the waste stream—rather than solely on a perceived notion of “thickness”—can lead to significant cost optimization and vastly improved waste containment performance. It is about choosing the right combination of material characteristics and strength for the job at hand.
The following table provides a general guide for selecting trash bags/can liners:
Liner Type | Thickness Range | Key Properties | Common Waste Types | Typical Janitorial Applications |
---|---|---|---|---|
LDPE | 0.35 – 6.0+ mils | High puncture resistance, excellent stretch/flexibility, good load capacity. | Sharp objects, rough edges, heavy items, food waste (with bones/packaging), yard waste, construction debris. | Kitchens, restaurants, industrial settings, outdoor bins, healthcare (some applications), construction sites. |
HDPE | 6 – 24+ microns | Good strength for its gauge (less material), less stretch, lower puncture resistance for sharps. | Office paper, soft plastics, restroom waste (paper towels), light food waste (no sharps), bulky light items. | Offices, restrooms, classrooms, retail (non-sharp waste), general light-duty waste collection. |
Other key considerations for selection include ensuring the liner is the correct size for the trash can to prevent slipping or improper fit , and features like drawstring closures, which can improve ease of closing, portability (especially for heavy loads), and reduce spillage.
5. Specialized Tools: Squeegees for Superior Surface Cleaning
Squeegees are specialized cleaning tools designed for the efficient removal of liquids—water, cleaning solutions, or slurry—from flat surfaces such as floors, windows, mirrors, and walls. The effectiveness of a squeegee is largely determined by its blade, particularly the material from which the blade is made. Different blade materials offer varying properties in terms of flexibility, durability, chemical resistance, and abrasion resistance, making the selection of the right squeegee blade crucial for optimal performance on different surfaces and with various types of soil or chemicals.
Understanding Squeegee Blade Materials: A Comparative Analysis
The choice of squeegee blade material directly impacts water recovery, streak prevention, blade longevity, and overall cleaning efficiency, especially for floor scrubbing machines and professional window cleaning. The most common materials include Natural Rubber (Gum Rubber), Linatex® Rubber, Polyurethane (Urethane), Neoprene, and Silicone.
Material | Key Properties (Flexibility, Abrasion Resistance, Tear Resistance) | Durability Score (General Indication) | Chemical Resistance (Oils, Solvents, Acids, General) | Typical Cost Indication | Ideal Cleaning Applications/Floor Types |
---|---|---|---|---|---|
Natural Rubber (Gum Rubber) | High flexibility, lower abrasion resistance, good tear resistance. Conforms well to uneven surfaces. | Medium | Poor against oils and many organic solvents (degrades quickly). Good for water-based solutions, organic salts, ammonia, some acids, alkalis. | $ (Lower) | Smooth floors (VCT, terrazzo, sealed concrete), floors with grout lines. General-purpose water collection on even surfaces. |
Linatex® Rubber | Excellent flexibility, high abrasion resistance, exceptional tear resistance. | High to Very High | Better chemical resistance than natural rubber; works well with many chemicals but can still be damaged by oily soils/petroleum over time. Doesn’t swell like gum rubber. | $$ (Moderate) | Versatile for most floor types: VCT, LVT, grouted tile, natural stone, brick, rough concrete, sealed concrete, wood. Heavy-duty applications. |
Polyurethane (Urethane) | Moderate to good flexibility (can be stiffer), excellent abrasion resistance, outstanding cut and tear strength. | Very High | Excellent resistance to a wide range of chemicals, especially oils, solvents, fuels, and hydrocarbons. | $$$ (Higher) | Oily environments (kitchens, automotive shops, machine shops), industrial flooring, rough/uneven concrete, rubber floors, non-slip surfaces. Any floor surface where chemical resistance is key. |
Neoprene | Good flexibility, good abrasion resistance, good tear resistance. Maintains shape well. | High | Highly resistant to chemicals, oils, and greases. Good for weathering. Cloth-inserted (C.I.) neoprene offers enhanced resistance. | −$ (Moderate to Higher) | Oily and dirty situations, uneven concrete with abrasive materials, manufacturing environments. Automotive industry (especially C.I. Neoprene). |
Silicone | Highly flexible, soft. Good abrasion resistance in its applications. | High (for its applications) | Good resistance to heat, many chemicals, and abrasion. | −$ (Moderate to Higher) | Window cleaning, mirrors, shower doors, tiles, car glass. Ideal for streak-free results on smooth, flat surfaces. Also used in paint protection film (PPF) installation and vinyl wrapping. |
Detailed Material Properties:
- Natural Rubber (Gum Rubber): This traditional squeegee material is prized for its softness and flexibility, allowing it to conform exceptionally well to smooth floor surfaces like Vinyl Composite Tile (VCT) and terrazzo, as well as effectively reaching into grout lines to collect solution. It generally offers good tensile strength and elasticity. However, its softness means it tends to wear out more quickly than harder materials, especially on abrasive surfaces. A significant drawback is its poor resistance to oily soils and many organic solvents, which can cause the rubber to degrade, swell, or become wavy, severely hampering performance. It remains a cost-effective choice for general-purpose cleaning with water-based solutions on smooth, even floors.
- Linatex® Rubber: Linatex is a premium grade of natural rubber, specifically processed to exhibit exceptional performance characteristics. It is renowned for its superior tear resistance, high flexibility even at low temperatures, and remarkable abrasion resistance, making it significantly more durable than standard gum rubber. This durability translates to longer-lasting performance and reduced need for frequent replacements, offering good value over time. Linatex is versatile and performs well on a wide variety of floor types, including rougher surfaces like concrete and brick, due to its abrasion resistance. It offers better chemical resistance than standard natural rubber and does not swell as readily when exposed to some chemicals, though it can still be damaged by prolonged exposure to oily soils or petroleum-based products. It is often recommended for heavy-duty applications and is a preferred choice for many automatic floor scrubbers on diverse surfaces like VCT, LVT, grouted tile, and natural stone.
- Polyurethane (Urethane): Urethane squeegee blades are synthetic and known for their outstanding chemical resistance, making them the ideal choice for environments where oils, greases, solvents, fuels, or other aggressive chemicals are present. They exhibit excellent wear resistance and can be used effectively on virtually any floor surface, including rough and uneven industrial floors. Polyurethane blades are very durable, with high cut and tear strength and long-lasting flex fatigue properties. While generally more expensive than natural rubber blades, their longevity and superior performance in harsh chemical environments or on abrasive surfaces often justify the cost. They are highly recommended for applications in kitchens, automotive repair shops, machine shops, and on non-slip or rubber flooring. Some urethane blades feature ridges to create a better seal on very rough surfaces.
- Neoprene: Neoprene is a synthetic rubber that offers a good balance of flexibility, durability, and chemical resistance. It is known for maintaining its shape and performance characteristics over time, even with exposure to moderate chemicals and temperature variations. Neoprene is particularly noted for its durability in oily and dirty conditions and can be used effectively on uneven concrete surfaces, even those with abrasive materials. It is highly resistant to many chemicals, oils, and greases, and also withstands weathering well. For even greater resistance to abrasions and chemicals, especially in demanding environments like the automotive industry, cloth-inserted (C.I.) neoprene is available. Neoprene is a strong choice for manufacturing settings and other industrial applications.
- Silicone: Silicone squeegee blades are valued for their extreme flexibility, softness, and ability to create a tight seal against smooth surfaces like glass, resulting in streak-free and often squeak-free liquid removal. They are durable and offer good resistance to heat, a range of chemicals, and abrasion within their typical applications. Silicone is predominantly used for window cleaning, mirrors, shower doors, tiles, and automotive glass cleaning or detailing (e.g., window tinting, PPF installation, vinyl wrap application). Its ability to conform closely to surfaces without scratching makes it ideal for achieving pristine, clear results on delicate or highly polished surfaces.
Selecting the Right Squeegee Blade for Optimal Performance
Choosing the correct squeegee blade is not a one-size-fits-all decision; it requires careful consideration of several factors to ensure optimal cleaning performance, maximize blade life, and protect floor or window surfaces. The optimal material depends on the specific type of floor or surface being cleaned, the types of soils or contaminants present (especially oils or chemicals), the desired durability, and budgetary constraints. There is no single “best” material for all situations; the goal is to match the blade’s characteristics to the unique challenges of the cleaning task.
For example, for smooth Vinyl Composite Tile (VCT) floors with water-based soiling, Linatex® or commodity gum rubber are often suggested. However, if those same VCT floors are in a kitchen environment with heavy grease and oil, a polyurethane blade would be far more appropriate due to its superior oil resistance. Similarly, for rough concrete or non-slip surfaces embedded with abrasive material, the toughness of Linatex® or polyurethane is generally preferred over softer rubbers.
In the context of automated floor scrubbers, the squeegee blade assembly (typically a front and rear blade) is not merely an accessory but a critical interface that directly determines the machine’s ability to perform its primary function: leaving floors clean, dry, and safe.
The material, condition, and proper adjustment of these blades are paramount to the overall performance and return on investment of what are often expensive pieces of cleaning equipment. An automated scrubber can perfectly dispense and agitate cleaning solution, but if the squeegee blades are worn, damaged, made of an inappropriate material for the floor type or chemicals used, or incorrectly adjusted, the machine will fail to effectively pick up the dirty solution.
This failure negates the cleaning action, leaves floors wet (posing a significant slip-and-fall hazard), and can result in unsightly streaks or the redeposition of soil. The relatively inexpensive squeegee blade, therefore, has a disproportionately large impact on the efficacy and safety outcomes of automated cleaning programs.
Proper selection based on the application, regular inspection for wear or damage (such as nicks, tears, or rounded edges), timely replacement when worn, and correct adjustment are crucial maintenance practices. These steps maximize the efficiency of automated cleaning, ensure safety standards are met, and help achieve the desired levels of cleanliness, underscoring the importance of not overlooking these “consumable” yet critical parts in complex cleaning machinery.
6. Maintaining Your Janitorial Accessories for Longevity and Hygiene
The lifespan and effectiveness of janitorial accessories are not solely dependent on their initial quality but are significantly influenced by how they are cleaned, stored, and maintained. Adopting best practices for the care of these tools is a crucial aspect of any professional cleaning operation, contributing to cost savings, consistent performance, and enhanced safety and hygiene.
Best Practices for Cleaning, Storing, and Inspecting Accessories
A systematic approach to the maintenance of janitorial accessories is essential. Improper storage can lead to safety hazards, inefficiencies, and premature degradation of supplies, while neglecting cleaning can turn tools into sources of cross-contamination.
Cleaning:
- Tools and Equipment: All cleaning tools and equipment, including buckets, caddies, sprayer tanks, and non-disposable parts of mops or brushes, should be thoroughly cleaned after each use to remove dirt, chemical residues, and microorganisms. This prevents build-up that can impair function or harbor bacteria.
- Cloths and Mop Heads: Reusable cleaning cloths, microfiber pads, and mop heads must be laundered regularly and properly according to manufacturer guidelines to maintain their absorbency and cleaning efficacy, and to prevent the spread of germs. They should be allowed to dry completely before storage.
- Carts and Trolleys: Janitorial carts should be wiped down and disinfected regularly to remove accumulated dirt and grime. Pay attention to wheels, handles, and storage compartments. Ensure they are dry before storing to prevent rust on metal components or mold growth.
Storing:
- Designated Areas: Janitorial supplies should be stored in a designated, clean, dry, and well-organized area, such as a dedicated janitorial closet or storeroom. This area should be separate from food storage or general office supplies.
- Chemical Storage: Cleaning chemicals require particular attention. They should be stored separately from other supplies, ideally in a locked cabinet or closet, especially if hazardous or if unauthorized access is a concern (e.g., in schools). Ensure storage areas are well-ventilated and away from heat sources. Adhere to specific temperature or ventilation requirements indicated on product labels or Safety Data Sheets (SDS).
- Tool Organization: Mops, brooms, and other long-handled tools should be stored using appropriate tool holders or hooks, keeping them off the floor. This allows them to air dry properly (preventing bacterial growth on mop heads) and protects bristles and handles from damage. Storing tools with heads down is often recommended to prevent contaminants from running down handles.
- Accessibility and Labeling: Organize products based on usage, grouping similar items together to streamline cleaning processes. All containers, especially those holding diluted chemicals or transferred products, must be clearly and accurately labeled. Sturdy shelves designed for the weight and size of products should be used to prevent accidents and damage.
Inspecting:
- Regular Checks: Regularly inspect all accessories for wear and tear, damage, or malfunction. This includes checking janitor cart wheels for smooth operation and wear, ensuring locks on cabinets are functional, examining sprayer nozzles for blockages or leaks, and checking buckets for cracks.
- PPE Inspection: Gloves should be inspected for rips or punctures before each use. Reusable gloves require careful inspection for signs of degradation or embedded contaminants.
- Tool Condition: Check mop heads for excessive soiling or wear, broom bristles for being splayed or broken, and squeegee blades for nicks, cuts, or rounded edges.
Extending Lifespan and Ensuring Effectiveness
Investing in well-constructed, durable supplies is the first step towards ensuring longevity, as quality products are designed to withstand the rigors of frequent commercial use and tend to last longer. However, even the best quality accessories require proper care to maximize their service life and maintain their effectiveness.
A proactive maintenance schedule for janitorial accessories should not be viewed as an additional burden but rather as a crucial strategy for minimizing long-term operational costs, ensuring consistent cleaning quality, and mitigating safety and hygiene risks. For example, regular cleaning and lubrication of moving parts on janitor carts or pump sprayers can prevent premature failure and costly replacements. Keeping tools and equipment in good repair not only ensures they perform effectively but also prevents accidents that could arise from faulty equipment.
Neglecting the maintenance of these items—allowing cart wheels to seize, sprayer nozzles to become permanently clogged, or mops to become laden with bacteria—inevitably leads to decreased efficiency, poorer cleaning outcomes, potential safety hazards, and the need for more frequent and often more expensive replacements.
Implementing a simple but consistent maintenance program for all janitorial accessories—from the largest carts to the smallest measuring spoons—can significantly reduce the lifecycle cost of these items, improve worker safety and morale, and ensure that cleaning tasks are performed to the highest possible standard. This shifts the operational perspective from reactive replacement driven by failure to proactive care, yielding better financial, operational, and hygiene outcomes.
7. The Professional Advantage: Why Expertise Matters in Cleaning
While do-it-yourself (DIY) cleaning may seem like a cost-effective solution for some situations, particularly in smaller residential settings, the complexities and demands of maintaining cleanliness and hygiene in commercial, industrial, or large-scale residential environments often necessitate the expertise of professional cleaning services. The advantages offered by professionals in terms of skill, equipment, efficiency, and overall results typically far outweigh the perceived savings of an in-house or DIY approach.
Expertise, Experience, and Specialized Equipment of Professional Cleaners
One of the primary reasons to opt for professional cleaners is the depth of expertise and experience they bring to the task. Professional cleaning personnel are trained in the most effective and efficient cleaning techniques, understanding the appropriate products and methods for a wide variety of surfaces, materials, and soil types. They know how to tackle tough stains, eliminate odors, and disinfect properly without causing damage to valuable furnishings, fixtures, or finishes.
This knowledge extends to understanding chemical properties, dilution rates, dwell times for disinfectants, and safety protocols for handling potentially hazardous materials.
Furthermore, professional cleaning companies invest in specialized, often industrial-grade, equipment and supplies that are typically not available or practical for individual businesses or homeowners to purchase and maintain.
This can include high-powered carpet extractors, commercial floor scrubbers and polishers, steam cleaners, advanced microfiber systems, and a wider range of specialized cleaning agents. This advanced equipment allows them to achieve a deeper, more thorough clean than is generally possible with standard household tools.
Efficiency, Quality, and Consistency Beyond DIY Efforts
Professional cleaners operate with a systematic approach and efficiency honed through training and experience. They can complete cleaning tasks in a significantly shorter timeframe than untrained individuals, while ensuring a higher level of thoroughness. Many professional services follow detailed checklists and quality control procedures to ensure that all specified tasks are completed to a consistent standard during each visit, leaving no corners cut or areas overlooked.
This consistency and reliability are often difficult to achieve with DIY efforts, which can be subject to time constraints, varying levels of motivation, or lack of a structured cleaning plan. The quality of clean delivered by professionals is generally superior, resulting in a visibly cleaner, fresher, and more hygienic environment.
Enhanced Safety, Hygiene, and Cost-Effectiveness in the Long Run
Professional cleaners are trained in proper sanitation techniques designed to effectively remove germs, allergens, and other contaminants from the environment, contributing to a healthier space for employees, customers, or residents. They understand how to prevent cross-contamination and are knowledgeable about handling and disposing of hazardous materials safely. This focus on health and safety is particularly crucial in environments like healthcare facilities, schools, or food service establishments, but is beneficial in any shared space.
While engaging professional cleaning services involves an upfront cost, it can prove to be cost-effective in the long run. Professionals use high-quality products and correct techniques that can prolong the lifespan of carpets, flooring, upholstery, and other expensive assets by preventing premature wear and tear caused by improper cleaning methods or harsh chemicals.
Moreover, a consistently clean and hygienic environment can lead to reduced absenteeism due to illness among employees and a generally more productive workforce. The cost of preventing a widespread illness or addressing a pest infestation averted by professional cleaning practices can far outweigh the service fees.
Focusing on Core Business Operations by Outsourcing Cleaning
For businesses, outsourcing cleaning services to professionals allows management and employees to save valuable time and energy, enabling them to focus on their core competencies and strategic objectives rather than diverting resources to manage in-house cleaning tasks. Cleaning is a specialized function, and attempting to manage it internally without the requisite expertise can be inefficient and detract from the primary mission of the organization.
Engaging professional cleaning services should be viewed not merely as an operational expense but as a strategic investment that directly contributes to a company’s brand image, the well-being of its occupants, and overall productivity. A clean, well-maintained commercial space delivers a strong, positive first impression to clients, visitors, and potential partners, reinforcing the company’s professionalism and attention to detail. For employees, a consistently clean and hygienic workplace can significantly improve morale, reduce stress, and foster a sense of being valued by the organization, which in turn can lead to increased productivity and lower staff turnover.
The expertise that professionals bring in using the correct products and methods also protects a facility’s physical assets, such as expensive flooring, furniture, and specialized equipment, from damage that might occur with less knowledgeable cleaning efforts. Ultimately, the comprehensive value derived from enhanced brand perception, improved employee and customer health and satisfaction, asset preservation, and the ability to concentrate on core business functions often provides a return on investment that transcends the direct cost of the cleaning service.
The specialized equipment, consistent quality, and expert knowledge offered by professional cleaners deliver a level of cleanliness, hygiene, and peace of mind that is typically difficult and inefficient to achieve through DIY or ad-hoc internal efforts.
Final Thoughts
The effective management of cleanliness and hygiene is a multifaceted endeavor, heavily reliant on the appropriate selection, use, and maintenance of a diverse array of janitorial and cleaning accessories. From sophisticated cleaning carts that optimize workflow and hygiene protocols, to precisely engineered sprayers that maximize chemical efficacy, and specialized squeegee blades that ensure floor safety and appearance, each accessory plays a critical role in the broader ecosystem of clean.
The distinction between commercial-grade and household supplies underscores the importance of “fitness for purpose,” ensuring that tools are robust and effective enough for demanding professional environments.
Key considerations such as the organization provided by caddies and tool holders, the precision enabled by measuring devices, the safety ensured by warning signs and appropriate gloves, and the resource management facilitated by dispensers all contribute to operational efficiency, cost-effectiveness, and the overall health and safety of facility occupants and cleaning staff. Furthermore, proactive maintenance of these accessories is not an ancillary task but a core strategy for extending their lifespan, ensuring their continued effectiveness, and mitigating risks.
While understanding and utilizing these accessories effectively can significantly improve in-house cleaning efforts, the comprehensive expertise, specialized industrial-grade equipment, systematic efficiency, and consistent quality offered by professional cleaning services provide a distinct advantage, particularly in commercial and large-scale settings.
Investing in professional cleaning is a strategic decision that contributes to enhanced brand image, occupant well-being, asset preservation, and allows organizations to focus on their core operations, ultimately delivering value that extends far beyond the direct cost of service. The meticulous attention to detail, adherence to safety and hygiene standards, and the ability to tackle complex cleaning challenges make professional cleaners an invaluable partner in maintaining truly clean, healthy, and productive environments.