Dry ice blasting is rapidly emerging as a transformative cleaning solution across a multitude of industries. This detailed guide explores the intricacies of this innovative technology, from the scientific principles that govern its effectiveness to its diverse applications and critical safety considerations. Understanding dry ice blasting empowers informed decisions about its suitability for various cleaning challenges, highlighting why professional expertise is often paramount for achieving optimal and safe results.
I. Unveiling Dry Ice Blasting: The Future of Deep Clean
Dry ice blasting represents a significant advancement in cleaning methodologies, offering a powerful yet surprisingly gentle approach to contaminant removal. Its unique characteristics are redefining standards for efficiency, surface preservation, and environmental responsibility in cleaning processes.
Contact us!
A. What is Dry Ice Blasting?
Dry ice blasting is an innovative, non-abrasive, non-conductive, and non-toxic cleaning method that utilizes solid carbon dioxide (CO2) pellets, commonly known as dry ice, accelerated by a stream of compressed air. These pellets, typically the size of a grain of rice, are propelled at high velocities towards a contaminated surface.
The core concept and most significant differentiator of dry ice blasting is the phenomenon of sublimation. Upon impact with the target surface, the dry ice pellets instantly transform from a solid state directly into CO2 gas.
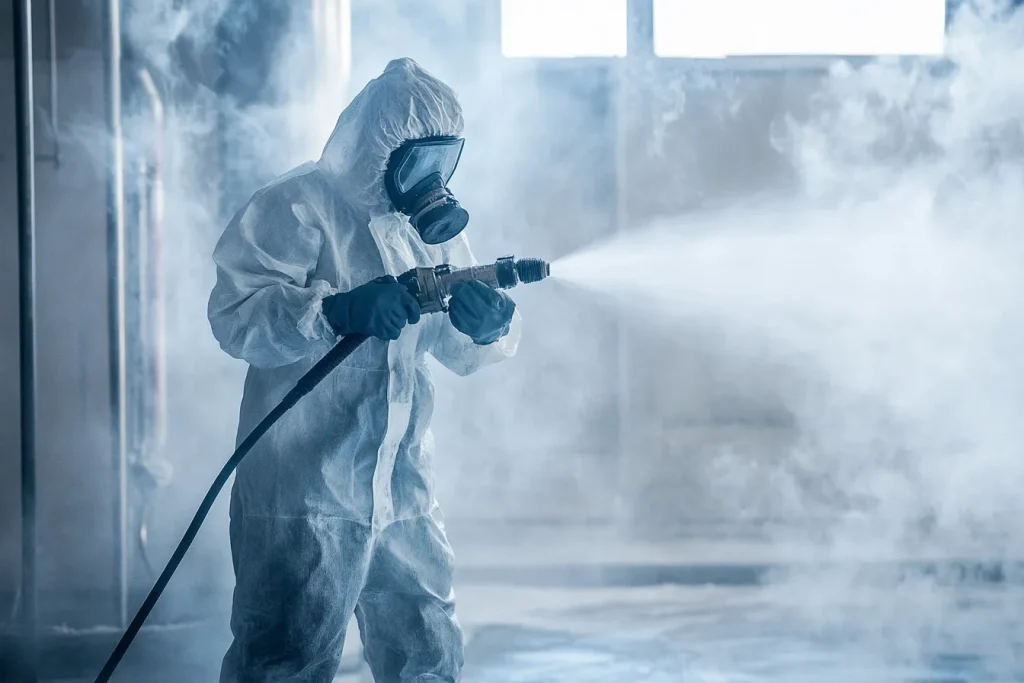
This process lifts contaminants away from the substrate without leaving any secondary waste, such as water, chemical residues, or abrasive media particles. This “no secondary waste” characteristic is fundamental to many of its advantages, streamlining the cleanup process and reducing disposal concerns.
As an expart said: “The innovative process of dry ice blast cleaning is quickly gaining widespread acceptance as an alternative to conventional cleaning methods because it is capable of rapidly removing stubborn deposits from both processing equipment and the production environment”.
Another confirms it is “…a nonabrasive, nontoxic cleaning process that utilizes solid carbon dioxide (CO2) pellets…they sublimate…upon impact, effectively removing contaminants with minimal residue or damage to the surface”.
This cleaning philosophy marks a departure from traditional methods that often involve a compromise between aggressive cleaning power and potential damage to the underlying material, or the use of harsh chemicals with environmental and safety implications.
Dry ice blasting aims to circumvent these trade-offs. The elimination of secondary waste is not merely a convenience; it signifies a fundamental shift in managing cleaning byproducts, thereby diminishing downstream environmental impact and the costs associated with hazardous waste disposal. This evolution points towards more sustainable and less damaging industrial and commercial cleaning practices.
B. The Science Behind the Sparkle: How It Works
The remarkable cleaning efficacy of dry ice blasting is not attributed to a single mechanism but rather to a rapid and synergistic interplay of three distinct physical phenomena that occur almost simultaneously upon impact. This combination allows the process to be both powerful in removing contaminants and gentle on the underlying surface.
- Thermal Shock: The first key action is thermal shock. Dry ice pellets possess an extremely low temperature of $-78.5^{circ}C$ ($-109^{circ}F$). When these super-cooled pellets strike a warmer contaminated surface, they cause a rapid and localized decrease in the temperature of the contaminant layer. This extreme cold induces thermal stress, making the contaminant brittle and causing it to fracture. This embrittlement weakens the adhesion of the contaminant to the substrate.
- Kinetic Energy: Simultaneously, the dry ice pellets are propelled at very high velocities, often approaching the speed of sound, by the compressed air stream. The kinetic energy of these high-speed pellets delivers a physical impact upon the now-brittle contaminant. This impact force helps to dislodge and break up the fractured contaminant particles from the surface.
- Sublimation & Gas Expansion: The most unique aspect of dry ice blasting occurs as the pellets impact the surface: they instantly sublimate, transitioning directly from a solid to CO2 gas. This phase change is accompanied by a rapid and significant volumetric expansion, with the gas occupying 400 to 700 times the volume of the solid pellets. This explosive expansion creates a “micro-explosion” effect at the point of impact, generating a lifting force that flushes the dislodged and fractured contaminants away from the substrate. The CO2 gas then dissipates into the atmosphere, leaving behind only the removed contaminant, which typically becomes a light, dry residue easily swept or vacuumed away.
The “dry” nature of this process, stemming directly from sublimation, is a game-changer for many applications. No water or liquid solvents are introduced, making dry ice blasting exceptionally suitable for cleaning water-sensitive items like electrical components, electronics, and machinery where moisture could cause short circuits, corrosion, or other damage. Furthermore, in environments where moisture can promote mold or bacterial growth, such as food processing facilities or during mold remediation projects, the waterless nature of dry ice blasting is a critical advantage. This avoids introducing conditions that could lead to recontamination or exacerbate existing problems, a significant improvement over wet cleaning methods.
II. The Anatomy of a Dry Ice Blaster: Equipment & Media
Effective dry ice blasting relies on a specialized system of equipment and the appropriate form of dry ice media. The evolution of this technology has led to a diversification of machines and components, each tailored to optimize performance for a widening array of cleaning challenges, from heavy-duty industrial tasks to the delicate cleaning of sensitive artifacts.
A. The Machines: From Pellet Powerhouses to MicroParticle Precision
A typical dry ice blasting setup consists of several key components working in concert. These generally include an air compressor to supply the motive force, a hopper for storing the dry ice media (which is often temperature-regulated), a feeding system to introduce the dry ice into the airflow, a flexible hose to convey the media, a specialized nozzle to accelerate and direct the blast, and a control panel for adjusting parameters like air pressure and media flow rate.
The types of dry ice blasters available reflect the varied demands of different cleaning applications:
- Pellet Blasters: These machines utilize standard dry ice pellets, often about the size of a grain of rice (3 mm diameter is common). They are designed for more general or aggressive cleaning tasks where a higher impact force is beneficial.
- MicroParticle Blasters: For applications requiring a gentler touch, such as cleaning delicate electronics, intricate molds, or historical artifacts, MicroParticle blasters are employed. These systems use finer dry ice particles, which can be produced by shaving larger dry ice blocks or by fragmenting pellets. An example is Cold Jet’s i3 MicroClean® series, which uses finely shaved dry ice, or their SDI Select™ 60, which is capable of shaving any dry ice media input, including blocks or pellets, into the desired particle size. This allows for highly controlled and delicate cleaning.
- Specialty Blasters: Some applications call for unique machine characteristics. For instance, fully pneumatic machines, like Cold Jet’s C100, are available for environments where electrical power sources are restricted or undesirable. Hybrid systems, such as Cold Jet’s E-CO2™ 150, combine dry ice with a minimal amount of abrasive material to tackle tasks like aggressive paint stripping or corrosion removal, offering a compromise when pure dry ice might be too slow or ineffective but traditional abrasive blasting is too harsh or creates too much secondary waste.
Dry ice blasting systems can also be categorized by their hose design:
- Single-Hose Systems: Representing a newer generation of technology, single-hose systems draw the dry ice pellets into the main compressed air stream inside the machine. The mixture is then accelerated through a single hose to the blasting applicator or nozzle. This design generally offers several advantages, including a more consistent and powerful cleaning experience, the ability to use much longer hose lengths without significant pressure drops or loss of pellet velocity (beneficial for large-scale operations or accessing remote areas), greater efficiency in terms of compressed air consumption (potentially leading to energy savings), and a reduced risk of dry ice clogging within the hose.
- Two-Hose Systems (or Double Hose Systems): This is an older design where the dry ice pellets and the high-velocity compressed air are transported through separate hoses until they converge at the blasting nozzle or applicator. While these systems may have a simpler mechanical design, potentially leading to increased robustness and easier maintenance in some respects, they are generally considered less efficient. They often require more compressed air, are more prone to pellet jams or blockages, especially if hoses kink or moisture is present, and typically cannot support the same extended hose lengths as single-hose systems without significant performance degradation. However, they can be less expensive initially.
The diversification in machine types clearly indicates that dry ice blasting technology has matured and adapted to meet a broad spectrum of cleaning requirements. This evolution from general-purpose pellet blasters to sophisticated MicroParticle and specialized systems underscores the technology’s versatility and its responsiveness to market demands for both power and precision.
B. Essential Gear: Nozzles, Air Compressors, and Dry Ice Supply
Beyond the blasting unit itself, several other components are critical to a successful dry ice blasting operation. The selection and proper functioning of these elements are integral to the overall system’s performance.
Nozzles: The nozzle is a crucial component, as it is the terminal point where the mixture of compressed air and dry ice particles is shaped, directed, and accelerated onto the target surface. Nozzles are typically manufactured from highly durable materials like hardened aluminum, stainless steel, or specialized plastics to withstand the abrasive impact of high-speed dry ice particles and the extreme cold temperatures involved. They come in various shapes and sizes, each designed for specific applications:
- Flat Nozzles: Offer a wide spray pattern, suitable for cleaning broad, flat surface areas efficiently.
- Round Nozzles: Provide a more concentrated, targeted stream for precise cleaning of smaller areas or stubborn spots.
- Angled or Extended Nozzles: Designed to allow access to hard-to-reach areas, corners, or intricate geometries.
- Fragmenter Nozzles: These specialized nozzles are equipped with internal mechanisms (like a fine mesh of blades) that break down standard dry ice pellets into much finer, ultra-fine particles just before they exit the nozzle. This makes them ideal for cleaning very sensitive or delicate surfaces where a gentler approach is necessary to avoid damage. The internal design and orifice size of a nozzle also determine its flow dynamics, influencing the volume of dry ice and air delivered, and thus the forcefulness or precision of the cleaning action. Manufacturers like Cold Jet offer an extensive range of nozzles, including high-flow, medium-flow, and low-flow options, variable fragmenting MERN (Maximum Entrainment Ratio Nozzle) technology nozzles, and specialized i³ MicroClean nozzles with various air consumption rates (CFM) and blast swath sizes, including angled versions for specific tasks.
Air Compressors: The air compressor is the heart of the propellant system, supplying the volume and pressure of air needed to accelerate the dry ice particles. The requirements for air pressure and volume (typically measured in cubic feet per minute, or CFM, and pounds per square inch, or PSI) vary significantly depending on the type of dry ice blasting system and the specific cleaning application:
- Pellet Systems: Generally require higher air volumes, typically around 100 text{ cfm} (2.8 text{ m}^3/text{min}) at 80 text{ psi} (5.5 text{ bar}).
- MicroParticle Systems: Operate with lower air volumes, often around 30 text{ cfm} (0.9 text{ m}^3/text{min}) at 80 text{ psi} (5.5 text{ bar}).
- Low-Flow Nozzle Systems: Some MicroParticle systems equipped with low-flow nozzles can operate with as little as 12 text{ cfm} (0.3 text{ m}^3/text{min}) at 80 text{ psi} (5.5 text{ bar}). Air quality is also a critical factor. Portable diesel compressors, often used on job sites, tend to produce heated and humid compressed air. This moisture and heat can compromise the quality of the dry ice (causing premature sublimation) and reduce the overall effectiveness of the blasting system. Therefore, an aftercooler is highly recommended when using diesel compressors. An aftercooler effectively reduces the compressed air temperature to within approximately 15^{circ}F (-9.4^{circ}C) of the ambient conditions while simultaneously removing excess moisture from the air stream. For some very precise applications, particularly with CO2 spray cleaning (a related but distinct technology), Clean Dry Air (CDA) meeting specific ISO class standards may be required.
Dry Ice Supply:
The blasting media itself, dry ice, can be sourced in various forms, primarily pellets, blocks, or shavings. Rice-sized pellets (~3 text{ mm}) are common for many blasters. Dry ice can be purchased as needed from local industrial gas suppliers or specialized dry ice manufacturers. It is typically delivered in heavily insulated containers or totes to minimize sublimation during transport and storage, with minimum order quantities often around 500 text{ lbs}. However, it’s important to be aware that dry ice shortages can occasionally occur due to disruptions in the CO2 supply chain.
For high-volume users, on-site dry ice production can be a viable alternative:
- Pelletizers: These machines convert liquid CO2 (LCO2) stored in a bulk tank into solid dry ice pellets of a consistent size. While representing a significant capital investment, pelletizers can offer long-term cost savings, ensure a consistent supply, and eliminate logistical challenges associated with frequent deliveries. Companies like Cold Jet offer a range of pelletizers with varying production capacities, from 80 text{ kg/hr} (~176 text{ lbs/hr}) up to 750 text{ kg/hr} (~1653 text{ lbs/hr}).
- Block Shavers: While less explicitly detailed for blasting in the provided materials, some advanced dry ice blasting machines, like Cold Jet’s SDI Select™ 60, are designed to “shave any dry ice media input”. This implies they can take dry ice blocks or larger pieces and process them into finer particles suitable for MicroParticle blasting. This capability adds flexibility if only block ice is readily available.
The effective operation of a dry ice blasting system hinges on the careful selection and integration of all these components. The blaster unit, air compressor (with appropriate air treatment), dry ice (in the correct form and quality), and the specific nozzle chosen must all be matched to the demands of the cleaning application. A mismatch in any part of this system can lead to suboptimal cleaning results, inefficiency, increased operational costs, or even potential damage to the substrate being cleaned. This interconnectedness underscores the value of professional expertise in configuring and operating dry ice blasting systems.
C. Leading Equipment Manufacturers
The dry ice blasting market is served by several established and specialized manufacturers, indicating a mature technology with ongoing research, development, and a competitive landscape. Among the key players are:
- Cold Jet: Widely recognized as a pioneer and global leader in both dry ice blasting and dry ice production technology. Established in 1986 and headquartered in Loveland, Ohio, USA, Cold Jet holds numerous patents (over 250 worldwide) and offers an extensive range of dry ice blasting systems, pelletizers, and nozzles, catering to a vast array of industries and applications.
- Alfred Kärcher SE & Co. KG: A well-known German manufacturer of cleaning technology solutions, Kärcher also produces dry ice blasters as part of its comprehensive product portfolio.
- Other notable manufacturers mentioned include Nu-Ice Age, Inc., ARTIMPEX nv, and IceTech.
The presence of these global companies, alongside more specialized firms, provides users with a range of equipment options. However, it also highlights the complexity involved in selecting the most appropriate system for a given need, further emphasizing the benefit of consulting with professionals who have experience across different makes and models.
III. A Spectrum of Clean: Diverse Applications of Dry Ice Blasting
The unique combination of potent cleaning power, non-abrasive action, and residue-free results has propelled dry ice blasting into a remarkably diverse range of applications. Its ability to clean effectively without water, chemicals, or damaging the substrate makes it an invaluable tool in industries where traditional methods fall short or pose unacceptable risks.
A. Powering Up Safely: Cleaning Electrical Equipment & Motors
Dry ice blasting is exceptionally well-suited for cleaning electrical equipment and motors due to its fundamental properties: it is non-conductive, non-abrasive, and entirely moisture-free. This allows for the cleaning of sensitive electrical components, often in-place and without the need for extensive disassembly or prolonged cooldown periods, thereby significantly reducing operational downtime.
The benefits of using dry ice blasting for electrical apparatus are numerous. It effectively removes common contaminants such as dust, dirt, grease, oil, carbon deposits, and even light oxidation or rust that can impair performance and lead to failures. Regular cleaning with dry ice can improve critical electrical parameters like megohm readings and polarization indices, enhance thermal dissipation by removing insulating layers of grime, extend the overall lifespan of the equipment, and reduce the risk of malfunctions, flashovers, or catastrophic failures.
Specific use cases are widespread and include:
- Power Generation & Distribution: Substations, switchgears, insulators, surge arresters, transformers, circuit breakers, disconnect switches, bushings, and control panels.
- Industrial Motors & Generators: Electric motors of all sizes, generators, alternators, and associated control circuitry.
- Manufacturing Equipment: Compressors, gas turbines (including starting motors and alternators), and various electronic control systems.
The capability to clean electrical equipment while it is energized (online cleaning) is a significant advantage in certain situations, though this requires highly specialized training and strict adherence to safety protocols. More commonly, equipment is de-energized but cleaned in-situ, saving considerable time compared to methods requiring removal and transport to a dedicated cleaning facility. This proactive maintenance approach, facilitated by the efficiency and safety of dry ice blasting, transforms electrical upkeep from a potentially disruptive and reactive task into a strategic, performance-enhancing activity. Regular cleaning prevents the gradual accumulation of contaminants that can lead to overheating, reduced efficiency, and premature failure, thus safeguarding critical assets and ensuring operational reliability.
B. Perfecting Production: Molds in Manufacturing (Plastics, Rubber, Die Casting, Foundry)
In manufacturing sectors that rely heavily on molds – such as plastics injection molding, rubber molding, die casting, and foundry operations – maintaining mold cleanliness is paramount for product quality and production efficiency. Dry ice blasting has proven to be a highly effective and advantageous method for cleaning these critical tools.
The primary benefit is its non-abrasive nature. Dry ice pellets effectively remove built-up residues of release agents, uncured product material, oils, grease, and other contaminants without abrading, eroding, or otherwise damaging the delicate surfaces of the molds. This is crucial for preserving the precise critical tolerances, intricate details, and surface finish of the mold, which directly impacts the quality of the parts produced and extends the operational lifespan of the expensive molds themselves.
Further advantages include the ability to clean molds while they are still hot and in-place within the production machinery. This eliminates the significant downtime associated with traditional cleaning methods that often require molds to be cooled, removed from the press, manually scrubbed (often with solvents or abrasives), and then reheated before production can resume. By cleaning online, dry ice blasting dramatically reduces these non-productive periods, leading to increased throughput. Consequently, manufacturers experience improved product quality with fewer rejects or defects caused by contaminated mold surfaces, reduced scrap rates, and substantial decreases in cleaning time and associated labor costs.
Specific applications include cleaning:
- Plastics Industry: Injection molds, compression molds, blow molds, extrusion dies, and molds for composite materials.
- Rubber Industry: Molds for tires, seals, gaskets, and other rubber components.
- Foundry & Die Casting: Core boxes (removing sand, resin, and other residues), die-cast tooling (for semi-solid casting, squeeze casting, low-pressure permanent molding (LPPM), and permanent molding), effectively removing scale, oxides, and lubricants from die cavities.
In industries where even minor mold imperfections or residues can result in costly product defects and production losses, dry ice blasting’s ability to maintain pristine mold integrity while minimizing downtime positions it not just as a cleaning method, but as a valuable process optimization tool that directly contributes to higher quality outputs and improved profitability.
C. Pressing Matters: Revitalizing Printing Presses
The printing industry demands high levels of precision and consistency, where the cleanliness of printing machinery is directly linked to output quality and operational efficiency. Dry ice blasting offers a superior solution for maintaining printing presses, effectively removing the stubborn and varied contaminants that plague this equipment. It efficiently cleans away dried and burnished ink, heavy grease, caked-on paper dust and lint, spray powders, and adhesive residues from various components of the printing machinery.
A key advantage is its non-abrasive action, which is critical for protecting the sensitive and expensive components of modern printing presses. Unlike manual scrubbing with solvents or abrasive cleaning techniques, dry ice blasting will not damage delicate rollers (anilox, gravure, offset), printing plates, drums, gears, guides, or sensor arrays. This preserves the precise engineering of these parts, ensuring accurate registration and consistent print quality.
Furthermore, dry ice blasting allows for cleaning in-place with minimal to no disassembly of the press and often without requiring a full cooldown. This dramatically reduces maintenance downtime, allowing for more frequent cleaning cycles and quicker return to production. The process is also dry and chemical-free, eliminating issues related to solvent handling, hazardous waste disposal, and potential damage from moisture. Benefits include reduced scrap rates due to cleaner machinery, consistently higher print quality, prolonged equipment life, and lower labor costs associated with cleaning.
Specific components and press types that benefit from dry ice blasting include:
- Press Types: Web-fed presses, sheet-fed offset presses, flexographic presses, and gravure presses.
- Components: Printing rollers, plates, drums, ink trays and fountains, feeder units, delivery units, gear trains, deck guides, grippers, and even clogged ink nozzles.
In an industry where consistent quality, high throughput, and minimal downtime are paramount, dry ice blasting provides a rapid, effective, and safe cleaning method. By addressing the contaminant buildup that directly degrades print quality and can lead to equipment malfunctions, it helps maintain machinery at peak operational performance.
D. The Gold Standard in Hygiene: Food Processing Equipment
The food and beverage processing industry operates under stringent hygiene and sanitation standards mandated by regulatory bodies such as the FDA (Food and Drug Administration), USDA (United States Department of Agriculture), and EPA (Environmental Protection Agency). Dry ice blasting has gained approval from these agencies as a safe and effective method for cleaning and sanitizing food processing equipment. It is highly effective at removing a wide array of common food industry contaminants, including protein buildup, grease and oils, tenacious baked-on residues (like caked-on flour or sugars), bacterial biofilms, mold, and mildew.
The advantages of dry ice blasting in this sector are manifold and directly address critical food safety and operational concerns:
- Waterless Cleaning: This is a paramount benefit, as the absence of water prevents the growth and proliferation of harmful microorganisms like mold and bacteria, which thrive in moist environments. This also eliminates lengthy drying times associated with wet cleaning.
- No Chemical Residues: Dry ice blasting cleans without the use of chemical sanitizers or detergents, ensuring that no harmful residues are left behind to contaminate food products. This protects food safety, quality, and taste. The dry ice itself is food-grade, being made from beverage-grade CO2.
- In-Place Cleaning: Equipment can often be cleaned in-situ, without the need for extensive disassembly, and frequently while still warm or hot from production. This drastically reduces cleaning downtime and allows for more frequent sanitation cycles.
- Non-Abrasive: The process does not abrade or damage food processing equipment surfaces, preserving their integrity and preventing the creation of scratches or crevices where bacteria could harbor.
- Effective Sanitization: The extremely low temperature of the dry ice ($-78.5^{circ}C$) has a sanitizing effect, killing bacteria, mold spores, and other microorganisms on contact. Studies have shown its effectiveness in decontaminating surfaces from pathogens like Salmonella, E. coli, and Listeria.
Dry ice blasting is used to clean a wide variety of food processing equipment, including conveyor systems, mixers, blenders, ovens, proofers, slicers, depositors, packaging machinery, refrigeration units, freezers, storage tanks, heat exchangers, and electrical motors and control panels. It is suitable for diverse sectors within the food industry, such as bakeries, confectioneries, meat and poultry processing, dairy production, snack food manufacturing, and beverage production.
By addressing the dual critical needs of stringent hygiene and minimal production interruption, dry ice blasting offers a significant operational advantage. Its regulatory approvals, coupled with its inherent dry, residue-free, and sanitizing properties, directly support compliance and enhance food safety. Quantifiable benefits such as significantly faster cleaning times (e.g., 65% faster) and reduced labor costs (e.g., 80% reduction) further underscore its efficiency.
E. Preserving the Past: Gentle Historical Restoration
The field of historical restoration demands cleaning methods that are not only effective in removing accumulated grime and detrimental contaminants but are also exceptionally gentle to avoid damaging irreplaceable heritage materials. Dry ice blasting has emerged as a highly valued technique in this sensitive domain due to its non-abrasive, precise, and adjustable nature.
It is adept at removing decades or even centuries of accumulated dirt, soot (from pollution or past fires), mold, mildew, biological growth, efflorescence, graffiti, and multiple layers of old paint or coatings without harming the underlying original surfaces or disturbing delicate patinas that contribute to an object’s historical character. This is a critical distinction from many traditional restoration cleaning methods that might involve harsh chemicals, abrasive scrubbing, or high-pressure water, all of which can cause irreversible damage, etching, or discoloration to aged and often fragile materials.
The benefits of dry ice blasting in historical preservation are compelling:
- Non-Abrasive & Controllable: The intensity of the blast can be finely tuned, allowing conservators to remove unwanted surface layers while leaving the substrate untouched.
- Environmentally Friendly & Safe: It uses no harsh chemicals, produces no secondary waste media (the CO2 sublimates), and does not introduce large quantities of water, which can be detrimental to many historic materials. This makes it safer for the artifacts, the operators, and the surrounding environment.
- Deep Cleaning Capability: The pressurized stream can penetrate cracks, crevices, and intricate details (like carvings and moldings) that are difficult to clean effectively with manual methods.
- Versatility: It can be safely and effectively used on a wide array of common historical materials, including stone (marble, granite, limestone, sandstone), brick, terracotta, wood, plaster, bronze, and other metals.
Dry ice blasting has been successfully employed in the conservation of numerous significant historical assets, including historic buildings and facades, monuments, statues, sculptures, architectural features, and various artifacts. Notable examples include its use in the conservation of the Civil War ironclad USS Monitor and at the Philadelphia Museum of Art.
The unique challenge in heritage conservation lies in balancing cleaning efficacy with the absolute need to preserve irreplaceable historical fabric. Dry ice blasting’s precision and non-damaging qualities offer a sophisticated solution where other methods might be too crude or destructive, allowing for the careful revelation and preservation of historical integrity for future generations.
F. After the Flames: Effective Fire Damage Remediation (Soot, Smoke, and Odor Removal)
Fire incidents leave behind a complex array of damage, including charred materials, pervasive soot, oily smoke residues, and stubborn, unpleasant odors. Dry ice blasting has become a preferred method for fire damage remediation due to its speed, effectiveness, and ability to address multiple aspects of the damage simultaneously. It excels at removing charred wood, soot, vaporized synthetic resins from burnt plastics and textiles, and the deeply embedded smoke particles that cause lingering odors.
The advantages over traditional fire cleanup methods (such as manual sanding, scraping, wire brushing, or even soda blasting) are significant:
- Speed and Efficiency: Dry ice blasting is considerably faster, often reducing project timelines by 50% or more compared to manual methods. This allows for quicker re-occupancy and mitigation of further damage.
- Superior Cleaning: It provides a more thorough clean, reaching into tight angles, around structural elements like trusses and nails, and behind wiring and plumbing without causing damage to these components.
- Odor Elimination: A key benefit is its remarkable effectiveness in removing smoke odors. The process physically removes the odor-causing carbon particles and residues. Odors are often undetectable within 24 hours of blasting, significantly reducing or even eliminating the need for chemical deodorizers or encapsulating sealants.
- No Secondary Waste: Unlike sand or soda blasting, dry ice sublimates, leaving only the dislodged soot and char for cleanup. This simplifies the disposal process and reduces overall project costs.
- No Water Damage: Being a dry process, it avoids introducing moisture, which can exacerbate problems by causing swelling of materials, promoting mold growth, or leading to corrosion, especially critical when dealing with water damage from firefighting efforts.
- Safe for Electrical Components: Its non-conductive nature allows for cleaning around electrical systems without risk, provided they are de-energized.
Dry ice blasting is effective on a variety of surfaces commonly found in fire-damaged structures, including wood (framing, sheathing, decorative elements), concrete, brick, and metal surfaces. Its ability to address not just the visible soot but also the invisible, pervasive odors and harmful residues makes it a comprehensive restoration tool. This effectiveness, combined with speed and reduced secondary issues, has led to its increasing recommendation by insurance industry professionals and restoration contractors.
G. Banishing Bio-Contaminants: Thorough Mold Remediation
Mold contamination in buildings poses significant health risks and can compromise structural integrity if left unaddressed. Dry ice blasting has proven to be a highly effective and efficient method for mold remediation, capable of removing mold growth, mildew, and tenacious mold spores from a wide range of surfaces, including porous materials like wood.
The benefits of using dry ice blasting for mold remediation are substantial, often outperforming traditional methods like manual scraping, sanding, wire brushing, or chemical treatments:
- Speed and Reduced Labor: Dry ice blasting can reduce mold remediation project time by as much as 60-80%. This translates to lower labor costs and minimized displacement time for occupants.
- High Spore Removal Rate: The process physically dislodges and removes mold spores with a very high efficacy, reportedly close to 100% in some cases. The extreme cold ($-78.5^{circ}C$) of the dry ice also kills mold spores and bacteria on contact, providing a sanitizing effect.
- Inhibits Regrowth: Because it is a completely dry cleaning method, no moisture is reintroduced into the treated environment. This is crucial, as moisture is a primary factor for mold growth. By leaving surfaces dry and clean, dry ice blasting helps to inhibit mold regrowth.
- Accessibility: The pressurized blast stream can effectively clean hard-to-reach areas, such as tight corners, crevices, between joists and studs, around nails, wiring, and plumbing fixtures, where manual methods often fail to achieve complete removal.
- No Chemicals or Secondary Waste: It eliminates the need for harsh biocides or chemical cleaners, enhancing worker and occupant safety and avoiding chemical residues. Since the dry ice sublimates, there is no secondary blasting media to clean up, reducing disposal costs and efforts.
- Safe on Various Surfaces: It can be used safely in domestic, commercial, and industrial buildings on materials like wood framing, sheathing, joists, trusses, concrete, and masonry without causing structural damage when applied correctly. Its moisture-free nature also makes it safe for use around electrical systems and plumbing.
Effective mold remediation requires not only the removal of visible mold growth but also the elimination of microscopic spores and the addressing of conditions that foster regrowth. Dry ice blasting uniquely achieves these objectives by physically stripping away the growth, neutralizing spores through thermal shock, and leaving the treated area dry and less conducive to future mold proliferation. This comprehensive approach makes it a superior choice for ensuring a healthier indoor environment.
IV. The Clear Advantages: Why Choose Dry Ice Blasting?
Dry ice blasting offers a compelling suite of benefits that distinguish it from many conventional cleaning methods. These advantages stem from its unique scientific principles and contribute to its growing adoption across diverse and demanding applications.
- Non-Abrasive Action: Perhaps the most significant advantage is its non-abrasive nature. Unlike methods that rely on grit or harsh scrubbing, dry ice pellets are relatively soft and sublimate on impact, meaning they do not scratch, etch, or erode the underlying surface material. This is critical for cleaning delicate machinery, preserving historical artifacts, maintaining critical tolerances on molds, and protecting sensitive electronic components.
- Non-Conductive Properties: Dry ice is an electrical insulator. This makes dry ice blasting exceptionally safe and effective for cleaning electrical equipment, motors, control panels, and other energized or potentially energized components without the risk of short circuits or electrical shock, provided proper safety protocols are followed.
- No Secondary Waste Generation: This is a hallmark of dry ice blasting. Because the CO2 pellets convert directly to gas upon impact, there is no residual blasting media (like sand, soda, beads, or water) left behind. The only material requiring cleanup and disposal is the actual contaminant that was removed from the surface. This dramatically reduces cleanup time, labor costs, and the expense and environmental burden associated with disposing of contaminated secondary waste streams, which can often be hazardous.
- Waterless Process: The entire process is dry, introducing no moisture to the cleaned surface or environment. This is invaluable for applications where water is detrimental, such as in bakeries (to prevent dough spoilage), on electrical equipment (to prevent shorts or corrosion), in mold remediation (to inhibit regrowth), and in fire restoration (to avoid compounding water damage).
- Speed and Efficiency: Dry ice blasting is often significantly faster than traditional manual cleaning methods or even some other blasting techniques, especially when factoring in the elimination of secondary waste cleanup. This speed translates directly into reduced downtime for equipment and facilities, leading to increased productivity.
- In-Situ Cleaning Capability: In many instances, equipment and machinery can be cleaned in place (“in-situ”) without the need for extensive disassembly, cooling down, or removal to a dedicated cleaning area. This further minimizes downtime and labor associated with preparation and reassembly.
- Environmentally Responsible: The CO2 used to make dry ice is often a recycled byproduct from other industrial processes, meaning its use in blasting does not typically add new CO2 to the atmosphere. The process avoids the use of harsh chemical solvents, detergents, or ozone-depleting substances, reducing harm to the environment and worker exposure to hazardous materials.
- Enhanced Operator Safety (with proper protocols): When compared to methods involving hazardous chemical exposure (e.g., solvents) or the generation of harmful airborne particulates (e.g., silica dust from sandblasting), dry ice blasting can offer a safer working environment, provided that all necessary safety precautions for handling dry ice and CO2 gas are strictly adhered to.
- Deep Cleaning and Accessibility: The pressurized stream of dry ice particles can effectively penetrate and clean complex geometries, tight crevices, nooks, and crannies that are often inaccessible or very difficult to clean thoroughly using manual methods or other cleaning techniques.
- Quantifiable Benefits and Cost Savings: The cumulative effect of these advantages often results in significant and quantifiable economic benefits. These include drastically reduced equipment downtime, leading to more production uptime; lower labor costs due to faster cleaning and no secondary waste cleanup; elimination of costs associated with purchasing, handling, and disposing of chemical solvents or contaminated abrasive media; extended lifespan of cleaned equipment due to the non-abrasive process; improved product quality and reduced scrap rates in manufacturing due to cleaner molds and machinery; and faster project completion in remediation scenarios. For example, one automotive weld line case study reported that implementing dry ice blasting reduced the required labor from four workers to one, decreased labor time by up to 69%, cut cleaning costs by up to 60%, and resulted in annual savings of $153,712. In a fire restoration project, an estimated 70% labor cost saving was achieved, translating to a $20,000 saving on a single job. The food industry has seen benefits such as 65% faster cleaning times, an 80% reduction in labor costs, and the elimination of chemical expenses through the adoption of dry ice blasting. The cost-effectiveness of dry ice blasting, therefore, extends far beyond a simple comparison of hourly service rates or media costs. It encompasses a holistic view of savings derived from enhanced operational efficiency, reduced waste, prolonged asset life, and improved output quality. This broader financial impact is crucial when evaluating the true return on investment for this advanced cleaning technology.
V. Considerations and Caveats: Understanding the Limitations
While dry ice blasting offers a remarkable array of advantages, it is not a universal panacea for all cleaning challenges. Understanding its limitations and potential drawbacks is essential for making informed decisions about its applicability.
- Cost Factors:
- Equipment Investment: The initial capital outlay for purchasing dry ice blasting machines can be substantial, with basic units starting around $10,000 and more advanced or larger systems costing upwards of $50,000 or more. Ancillary equipment, such as high-capacity air compressors and on-site dry ice pelletizers, also represents significant investments.
- Operational Costs: The cost of dry ice media itself can be considerable, with prices typically ranging from $1 to $3 per pound. A pellet dry ice machine can consume up to 2.5 text{ lbs} of dry ice per minute, potentially leading to media costs of $450 per hour or more during intensive operations. Furthermore, the air compressors required are energy-intensive, contributing to high recurring energy expenses.
- Rental and Contractor Services: For those not purchasing equipment, hiring contractor services or renting equipment can be more expensive on an hourly or project basis compared to some traditional cleaning methods, especially for smaller or less complex jobs.
- Safety Management and Hazards: The use of dry ice blasting necessitates rigorous adherence to safety protocols due to several inherent hazards:
- CO2 Asphyxiation Risk: As dry ice sublimates, it releases large volumes of CO2 gas. In enclosed or poorly ventilated spaces, this CO2 can displace oxygen, creating an asphyxiation hazard. Symptoms can range from headaches and dizziness to unconsciousness and, in severe cases, death. Robust ventilation and CO2 monitoring are mandatory.
- Frostbite and Cold Burns: Dry ice exists at $-78.5^{circ}C$ ($-109^{circ}F$). Direct skin contact with dry ice pellets, cold equipment surfaces, or the concentrated blast stream can cause severe frostbite almost instantaneously. Specialized Personal Protective Equipment (PPE) is essential.
- Noise Exposure: The blasting process generates extremely high noise levels, often reaching or exceeding 115 text{ dB}. Prolonged exposure without adequate hearing protection can lead to permanent hearing damage.
- Airborne Contaminants and Projectiles: The dislodged contaminants become airborne during the cleaning process. Depending on the nature of these contaminants (e.g., lead paint, mold spores, hazardous dust), they may require containment measures or subsequent re-cleaning of surrounding areas. The high-velocity dry ice particles and debris also pose a projectile risk to eyes and exposed skin.
- Explosion Hazard (Storage): If dry ice is stored in a completely sealed, airtight container, the pressure from sublimating CO2 gas can build up, potentially leading to a violent rupture or explosion of the container.
- Effectiveness Limitations:
- Tenacious or Thick Contaminants: While effective on a wide range of materials, dry ice blasting may not be as efficient or effective as more aggressive abrasive methods for removing extremely thick, dense, or strongly adhered contaminants. Examples include very thick layers of old paint on hard surfaces, heavy rust scale, or some types of tenacious adhesives or robust coatings.
- Surface Profiling: Because dry ice blasting is inherently non-abrasive, it does not typically create a significant surface profile or etch on the substrate. If a textured surface is required to promote adhesion for subsequent painting or coating applications, methods like sandblasting might be more appropriate.
- Thermal Shock on Sensitive or Thin Materials: Although generally non-damaging due to the rapid sublimation, there is a potential for thermal shock to affect very thin or particularly sensitive substrates, especially those with critical dimensional tolerances. If the material’s mass is very low or the contaminant layer is thick (requiring prolonged exposure), the rapid localized cooling could theoretically induce stresses leading to cracking or deformation. While some sources claim minimal thermal effects on most machinery , caution and testing on a small, inconspicuous area are advisable for highly sensitive applications.
- Dry Ice Supply and Logistics: Dry ice cannot be stored for long periods due to continuous sublimation. This necessitates careful logistics for supply and delivery, especially for large projects or in areas with limited local suppliers. As mentioned, CO2 shortages can also impact dry ice availability.
- Environmental Considerations (CO2 Release): While the CO2 used for dry ice production is often captured as a byproduct of other industrial processes (thus being recycled), the blasting process itself releases this CO2 gas into the atmosphere. Some studies suggest, however, that the shorter project durations and reduced fuel consumption associated with dry ice blasting might partially offset its direct CO2 emissions when compared to the overall environmental footprint of other, longer cleaning methods.
- Condensation: If the surface being cleaned is cooled below the dew point of the ambient air, moisture condensation can occur on the surface after blasting. This is generally less of an issue when cleaning hot equipment but can be a concern for certain materials or in humid environments if not properly managed.
- Training and Skill Requirement: Operating dry ice blasting equipment safely and effectively requires adequate training and skill. Operators need to understand how to adjust parameters for different applications and how to manage the associated safety risks.
- Proprietary Parts and Maintenance: Some manufacturers may use proprietary parts in their dry ice blasting machines, which could potentially affect the cost and availability of maintenance and repairs.
- Number of Operators: Due to the nature of the equipment and safety oversight, dry ice blasting operations typically require at least two people.
These limitations indicate that while dry ice blasting is a highly versatile and beneficial technology, it is not the universally optimal solution for every cleaning scenario. Its significant advantages are best leveraged in specific industrial, commercial, and restoration contexts where its unique benefits outweigh these considerations, often through the engagement of professional service providers who can manage the costs, safety, and technical complexities involved.
VI. Safety First: Navigating Dry Ice Blasting with Caution
The powerful cleaning capabilities of dry ice blasting are accompanied by inherent hazards that demand meticulous attention to safety protocols. Understanding these risks and implementing appropriate control measures are paramount for protecting personnel, equipment, and the environment. The complexity of these safety requirements is a primary reason why professional expertise is often indispensable.
A. Identifying the Hazards
Several potential hazards are associated with the dry ice blasting process and the handling of dry ice itself:
- CO2 Displacement and Asphyxiation: This is arguably the most critical hazard. Dry ice is solid carbon dioxide. As it sublimates, it converts into CO2 gas, which is heavier than air and can accumulate in low-lying areas or enclosed, poorly ventilated spaces. Elevated concentrations of CO2 displace oxygen in the air. Exposure to CO2 concentrations of 3-5% can cause headaches, rapid breathing, and discomfort. Higher concentrations (8-10% and above) can lead to more severe symptoms including nausea, cramps, disorientation, loss of consciousness, suffocation, respiratory arrest, and potentially death.
- Frostbite and Cold Burns: Dry ice maintains an extremely cold temperature of $-78.5^{circ}C$ ($-109^{circ}F$). Direct contact between bare skin and dry ice pellets, the cold blast stream, or uninsulated parts of the blasting equipment can cause severe frostbite (a thermal burn due to extreme cold) almost instantly. Flesh can stick to the extremely cold material.
- Noise: The dry ice blasting process generates very high noise levels, often reaching 115 text{ dB} or more. Exposure to such intense noise without adequate hearing protection can lead to temporary or permanent hearing loss.
- Airborne Debris and Projectiles: The high-velocity impact of dry ice pellets dislodges contaminants from the surface. These contaminants, along with fine dry ice particles, become airborne. This debris can pose a significant risk to the eyes and skin of operators and anyone in the vicinity. Depending on the nature of the contaminant being removed (e.g., lead paint, mold spores, silica-containing materials), respiratory protection may also be necessary to prevent inhalation of hazardous dusts.
- Explosion Hazard (Storage and Transport): Dry ice continuously sublimates into CO2 gas. If dry ice is stored in a completely sealed, airtight container, the pressure from the accumulating gas can build up to dangerous levels, potentially causing the container to rupture or explode violently.
- Equipment Handling Risks: Dry ice blasting equipment involves high-pressure air hoses and specialized nozzles. Improper handling, insecure connections, or equipment malfunction can lead to hose whipping or uncontrolled discharge of the blast stream, posing an impact hazard.
The hazards are often interconnected. For example, the need for robust ventilation to manage CO2 levels might influence how noise is controlled or how airborne contaminants are dispersed. Handling dry ice to load the machine (frostbite risk) is a prerequisite for the operation that generates noise and projectiles. This interconnectedness necessitates a comprehensive safety approach that addresses the entire operational system, not just isolated risks. Such a systematic approach to safety is a hallmark of professional operations.
B. Gearing Up: Essential Personal Protective Equipment (PPE)
To mitigate the identified hazards, the use of appropriate Personal Protective Equipment (PPE) is mandatory for all personnel involved in or near dry ice blasting operations. This PPE forms a protective system, and reliance on a single item is insufficient.
- Insulated Gloves: Thermal-insulating gloves specifically designed for handling cryogenic materials are essential to prevent frostbite when touching dry ice, loading the blasting machine, or coming into contact with cold equipment surfaces. Standard work gloves or nitrile exam gloves do not offer adequate protection.
- Eye and Face Protection: Safety glasses with side shields are a minimum requirement. However, due to the high velocity of particles, safety goggles that provide a tighter seal, or a full-face shield worn over safety glasses/goggles, offer superior protection against flying debris and dry ice particles.
- Hearing Protection: Given noise levels often exceeding 115 text{ dB}, high-quality earplugs and/or earmuffs are required to prevent noise-induced hearing loss.
- Respiratory Protection: The need for respiratory protection depends on CO2 levels and the nature of the contaminants being removed.
- For CO2: In confined spaces or areas where CO2 concentrations might exceed permissible exposure limits despite ventilation, a self-contained breathing apparatus (SCBA) or an air-supplied respirator may be necessary. Standard dust masks do not protect against CO2 gas.
- For Contaminants: If blasting hazardous materials (e.g., lead paint, mold, certain coatings), an appropriate particulate respirator (e.g., N95, P100) or a more advanced respirator may be required based on a hazard assessment.
- Protective Clothing: Long-sleeved shirts, trousers, or coveralls should be worn to protect exposed skin from flying debris and accidental contact with cold surfaces or the blast stream.
Proper selection, fit, use, and maintenance of PPE are crucial. Training on these aspects is a vital component of any dry ice blasting safety program.
C. The Air We Breathe: Critical Ventilation Requirements
Adequate ventilation is arguably the most critical safety control for dry ice blasting due to the risk of CO2 asphyxiation. CO2 is odorless and colorless at hazardous concentrations, making it an insidious threat if not actively managed.
- General Principle: Always conduct dry ice blasting in well-ventilated areas. For indoor applications, especially in confined spaces, mechanical ventilation systems are usually required.
- Ventilation Strategies:
- Exhaust Ventilation (Local Exhaust): This is generally the most efficient method. It involves placing an exhaust intake near the source of CO2 generation (the blasting operation) to capture and remove the CO2-rich air directly, exhausting it safely outside and away from fresh air intakes. This creates negative pressure in the work area, drawing in fresh air.
- Supply Ventilation (Dilution Ventilation): This involves blowing fresh air into the space to dilute the CO2 concentration and push contaminated air out through openings. Careful setup is needed to ensure effective air exchange and avoid “short-circuiting,” where fresh air exits without adequately mixing with and displacing the contaminated air.
- Air Monitoring: Continuous CO2 monitoring using gas detectors is essential, particularly in enclosed or confined spaces, or areas with potentially poor natural air circulation (e.g., pits, tanks, basements, remote corners). These monitors should be equipped with audible and visual alarms to alert personnel if CO2 levels approach or exceed safe limits.
- Occupational Exposure Limits (OELs): Regulatory bodies like OSHA (Occupational Safety and Health Administration) and NIOSH (National Institute for Occupational Safety and Health) have established exposure limits for CO2:
- OSHA Permissible Exposure Limit (PEL): 5,000 text{ parts per million (ppm)} as an 8-hour time-weighted average (TWA).
- OSHA Short-Term Exposure Limit (STEL): 30,000 text{ ppm} for a maximum of 15 minutes.
- NIOSH Recommended Exposure Limit (REL): 5,000 text{ ppm} as a TWA for up to a 10-hour workday during a 40-hour workweek.
- NIOSH Immediately Dangerous to Life or Health (IDLH) Concentration: 40,000 text{ ppm}. Exposure to IDLH concentrations requires immediate escape and use of SCBA for entry/rescue.
- Warning Signage: Clear warning signs should be posted at all entry points to areas where dry ice blasting is occurring or where CO2 accumulation is possible, alerting personnel to the potential hazard and required precautions (e.g., “Caution: Carbon Dioxide Hazard – Authorized Personnel Only – Ventilation Required”).
Given the invisible nature of CO2 gas and its potential for rapid and severe health effects, robust ventilation coupled with continuous air monitoring is not merely a best practice but a non-negotiable life-safety requirement. The complexity of designing and implementing effective ventilation and monitoring systems for varying environments is a significant factor favoring professional dry ice blasting services.
D. Handling with Care: Dry Ice Storage and Emergency Protocols
Safe practices extend to the storage, transportation, and disposal of dry ice, as well as preparedness for emergencies.
- Dry Ice Storage:
- Always store dry ice in containers specifically designed for it. These containers must be well-insulated but not airtight. They must allow the CO2 gas produced by sublimation to vent safely, preventing pressure buildup. Styrofoam coolers with loose-fitting lids are often suitable for smaller quantities.
- Store containers in well-ventilated areas, away from direct sunlight, heat sources, and occupied or confined spaces (e.g., never in walk-in freezers, cold rooms, unventilated basements, or vehicle passenger compartments).
- Dry Ice Transportation:
- Use insulated, vented containers.
- Transport dry ice in a separate compartment from the driver and passengers (e.g., in the trunk of a car with fresh air circulation, or in the cargo area of a van/truck, ensuring the area is ventilated).
- Secure packages against movement and damage during transit.
- Dry Ice Disposal:
- The safest way to dispose of unused dry ice is to allow it to sublimate completely in a well-ventilated area, outdoors if possible, away from people and animals.
- Never dispose of dry ice in sinks, toilets, drains, garbage disposals, or enclosed trash receptacles, as the extreme cold can damage plumbing, and the rapid gas release can cause pressure buildup or displace oxygen in confined waste systems.
- Emergency Preparedness and First Aid:
- Emergency Response Plan: Develop and clearly communicate a site-specific emergency response plan that covers potential incidents like CO2 overexposure, frostbite injuries, equipment malfunctions, or fires (if flammable contaminants are being removed). All team members must be trained on these procedures.
- Emergency Contacts & First Aid: Keep emergency contact numbers (e.g., local emergency services, company safety officer) and well-stocked first aid kits readily accessible.
- First Aid for CO2 Exposure (Asphyxiation):
- Immediately move the victim to an area with fresh air. Rescuers must not enter an area with suspected high CO2 levels without wearing SCBA.
- If breathing is difficult, trained personnel should administer oxygen, if available.
- If the victim is not breathing, begin artificial respiration (CPR) immediately.
- Call for professional medical assistance urgently.
- First Aid for Frostbite/Cold Burns:
- Remove the source of cold contact immediately. Carefully remove any clothing or jewelry from the affected area, unless it is frozen to the skin.
- Slowly rewarm the frostbitten area. Immerse the affected part in warm water – not hot – with a temperature between 37^{circ}C and 40^{circ}C (99^{circ}F to 104^{circ}F) for 15 to 30 minutes, or until normal skin color and sensation return. Water should be tolerable to normal skin.
- Do not rub or massage the frostbitten area, as this can cause further tissue damage.
- Do not use direct dry heat (like a radiator or fire) to rewarm.
- After rewarming, gently dry the area and apply a sterile, non-stick dressing to protect it. If blisters form, do not break them, as this increases infection risk.
- Over-the-counter pain relievers (e.g., ibuprofen) can be taken for pain.
- Seek prompt medical attention for all but the most minor frostbite, especially if there is blistering, numbness persists, or the skin appears white, waxy, or blackened.
The extensive and detailed nature of these storage, handling, and emergency protocols underscores that dry ice and its application in blasting carry significant inherent risks. These risks are manageable with proper training, equipment, and procedures, but they highlight why dry ice blasting is generally not suited for casual or unprepared DIY use. Professional services are equipped and trained to manage these aspects comprehensively.
VII. Dry Ice Blasting vs. Traditional Methods: A Comparative Overview
Choosing the right cleaning method requires a clear understanding of how dry ice blasting measures up against more conventional industrial and commercial cleaning techniques.
No single method is universally superior; the optimal choice depends on the specific contaminant, the nature of the substrate, environmental regulations, safety requirements, budget constraints, and the desired cleaning outcome. Dry ice blasting offers a unique profile of advantages that make it the ideal solution for many challenging situations, but it also has characteristics that may make other methods more suitable in different contexts.
Key Criteria for Comparison:
- Cleaning Effectiveness: How well does it remove the target contaminants?
- Substrate Impact (Abrasiveness): Does it damage, etch, or alter the surface being cleaned?
- Waste Generation (Secondary Waste): Does the process itself create waste media that requires cleanup and disposal?
- Environmental Impact: What are the effects on the environment (e.g., chemical use, CO2 emissions, water consumption, waste produced)?
- Operator Safety: What are the primary hazards to operators?
- Speed/Efficiency: How quickly can the cleaning task be completed, including setup and cleanup?
- Cost (Initial & Operational): What are the equipment, media, labor, and disposal costs?
- Suitability for Specific Applications: How well does it perform in key areas like electrical cleaning, mold remediation, food processing, etc.?
Dry Ice Blasting vs. Sandblasting:
- Dry Ice Blasting:
- Effectiveness: Excellent for a wide range of contaminants, including grease, oil, paint, mold, soot, and production residues.
- Substrate Impact: Non-abrasive; does not damage or profile most substrates. Ideal for delicate surfaces, precision components, and preserving surface integrity.
- Waste Generation: No secondary waste media; dry ice sublimates. Only the removed contaminant needs disposal.
- Environmental Impact: Uses recycled CO2; no chemical pollutants. Direct CO2 emission during blasting.
- Operator Safety: Risks include CO2 exposure, frostbite, noise, projectiles. No silica dust hazard.
- Speed/Efficiency: Can be very fast, especially when factoring in no media cleanup. Allows in-place cleaning.
- Cost: Higher initial equipment cost; media cost can be significant. Overall project cost can be competitive or lower due to reduced downtime and cleanup.
- Applications: Electrical, molds, printing, food (FDA approved), historical restoration, fire/mold remediation.
- Sandblasting (Abrasive Blasting):
- Effectiveness: Very effective for aggressive stripping of heavy rust, thick paint, and scale.
- Substrate Impact: Highly abrasive; profiles, etches, and can damage the substrate, especially softer materials. Not suitable for delicate items.
- Waste Generation: Creates significant secondary waste (used abrasive media mixed with contaminant), which can be hazardous and costly to dispose of. Generates large amounts of dust.
- Environmental Impact: Dust pollution; disposal of contaminated media. Some abrasives are inert, but removed contaminants can make waste hazardous.
- Operator Safety: Major risk of silicosis or other respiratory diseases from inhaling abrasive dust (especially silica sand); projectile hazards; noise. Requires extensive PPE and containment.
- Speed/Efficiency: Fast for aggressive material removal, but extensive setup (containment) and cleanup are required.
- Cost: Lower hourly media/equipment cost for some setups, but total project cost can be high due to labor for containment, cleanup, and waste disposal.
- Applications: Heavy rust/paint removal from robust surfaces (steel structures, ship hulls), surface preparation for coatings where profiling is desired. Not for electronics, food contact, or delicate restoration.
Dry Ice Blasting vs. Soda Blasting:
- Dry Ice Blasting: (As above: non-abrasive, no secondary waste, dry, non-conductive).
- Soda Blasting:
- Effectiveness: Good for removing paint, grease, light surface rust, mold, and soot. Has deodorizing properties (due to baking soda).
- Substrate Impact: Considered mildly abrasive. Gentler than sandblasting but can still dull polished surfaces or damage very soft materials if not carefully controlled. One source suggests it is less damaging than dry ice on soft substrates , which contrasts with the general consensus of dry ice being non-abrasive.
- Waste Generation: Creates significant fine dust (sodium bicarbonate) as secondary waste, which can be difficult to clean completely, especially from crevices, and can interfere with repainting if not thoroughly removed.
- Environmental Impact: Sodium bicarbonate itself is relatively benign, but large quantities can alter soil pH if allowed to seep into the ground. Waste disposal of dust/contaminant mixture is required.
- Operator Safety: Dust inhalation (nuisance dust, or hazardous if contaminant is toxic); eye irritation; noise.
- Speed/Efficiency: Can be effective, but dust cleanup adds time.
- Cost: Equipment can be less expensive than dry ice systems. Media cost is generally moderate.
- Applications: Automotive restoration (paint stripping), fire/mold remediation, graffiti removal, parts cleaning where mild abrasion is acceptable.
Dry Ice Blasting vs. High-Pressure Water Jetting (Hydroblasting):
- Dry Ice Blasting: (As above: dry, no water damage, safe for electrical, no secondary waste media).
- High-Pressure Water Jetting:
- Effectiveness: Good for removing dirt, grime, loose paint, marine growth, and some industrial deposits. Effectiveness on grease/oil is limited without detergents.
- Substrate Impact: Can be abrasive at very high pressures, potentially damaging softer surfaces, wood, or concrete. Can force water into seals or joints.
- Waste Generation: Does not add solid media waste, but generates large volumes of contaminated wastewater that requires collection, treatment, and proper disposal, which can be complex and costly.
- Environmental Impact: Water consumption; potential for contaminated runoff if not contained. Treatment/disposal of wastewater.
- Operator Safety: High-pressure water jet can cause severe injection injuries; slip hazards; potential exposure to atomized contaminants; noise.
- Speed/Efficiency: Can be fast for large surface areas, but drying time and wastewater management add to overall project duration.
- Cost: Equipment costs vary. Operational costs include water, energy, and wastewater treatment/disposal.
- Applications: Cleaning building exteriors, concrete, ship hulls, heat exchangers, tank cleaning. Not suitable for water-sensitive equipment (electrical) or where moisture is undesirable.
Dry Ice Blasting vs. Steam Cleaning:
- Dry Ice Blasting: (As above: faster, no drying time, no moisture, safe for electrical, generally louder).
- Steam Cleaning:
- Effectiveness: Good for sanitizing, degreasing, and removing some types of residues, especially organic matter. Effectiveness comparable to dry ice for some specific applications like turbine cleaning.
- Substrate Impact: Generally non-abrasive, but prolonged exposure to heat and moisture can damage some sensitive materials (e.g., some plastics, wood, painted surfaces).
- Waste Generation: No media waste, but can produce some wastewater/condensate, though less than water jetting. Surfaces are left damp and may require wiping/drying.
- Environmental Impact: Water and energy consumption.
- Operator Safety: Risk of steam burns; heat stress in enclosed areas; slip hazards. Quieter than dry ice blasting.
- Speed/Efficiency: Generally slower than dry ice blasting due to heat-up time, application rate, and need for drying.
- Cost: Equipment and operational costs can be comparable for some industrial applications.
- Applications: Sanitization in food/beverage, healthcare; degreasing engines/parts; cleaning upholstery; specific industrial tasks like turbine cleaning in noise-sensitive environments.
Dry Ice Blasting vs. Chemical/Solvent Cleaning:
- Dry Ice Blasting: (As above: no chemical residues, no hazardous solvent waste, often allows in-place cleaning, environmentally safer).
- Chemical/Solvent Cleaning:
- Effectiveness: Can be highly effective for dissolving specific contaminants like heavy grease, oils, adhesives, and certain coatings, for which they are formulated.
- Substrate Impact: Solvents can damage or discolor plastics, rubbers, paints, and other sensitive materials. Some chemicals are corrosive to metals.
- Waste Generation: Leaves chemical residues that often require thorough rinsing (which itself creates wastewater). Generates hazardous waste in the form of spent solvents, contaminated rags, and rinse water, requiring costly and regulated disposal.
- Environmental Impact: Significant concerns due to VOC emissions from solvents, toxicity of chemicals, and challenges of hazardous waste disposal.
- Operator Safety: High risk of exposure to hazardous/toxic chemicals through inhalation, skin contact, or ingestion. Requires specialized PPE (respirators, chemical-resistant gloves/suits), good ventilation, and careful handling procedures. Some solvents are flammable.
- Speed/Efficiency: Application can be quick, but dwell times, manual scrubbing, rinsing, and drying can make the overall process lengthy. Equipment often needs disassembly.
- Cost: Chemical costs can be high, especially for specialized or environmentally safer formulations. Hazardous waste disposal is a major cost factor.
- Applications: Degreasing parts, stripping specific coatings, precision cleaning of electronics (with specialized solvents), where chemical action is essential.
The following table provides a summarized comparison:
Table 1: Comparative Analysis of Industrial Cleaning Methods
Feature | Dry Ice Blasting | Sandblasting | Soda Blasting | Water Jetting | Steam Cleaning | Chemical/Solvent Cleaning |
---|---|---|---|---|---|---|
Abrasiveness | No | Yes (High) | Yes (Mild) | Potential (at high psi) | No | No (but can be corrosive) |
Secondary Waste | No (only contaminant) | Yes (media + contaminant) | Yes (media + contaminant) | Yes (wastewater) | Minimal (condensate) | Yes (spent chemicals, rinse) |
Water Usage | No | No (unless wet blasting) | No | Yes (High) | Yes (Low/Medium as steam) | Often (for rinsing) |
Elec. Conductive | No | No | No | Yes | Yes | Yes (many solvents) |
Environmental Impact | Low-Medium (CO2 emission, recycled CO2 used) | High (dust, waste disposal) | Medium (dust, pH impact, waste) | Medium-High (water use, wastewater) | Low-Medium (energy/water use) | High (VOCs, hazardous waste) |
Operator Safety | CO2, frostbite, noise, projectiles | Silicosis, projectiles, noise | Dust, irritation, noise | Injection injury, slip, noise | Burns, heat stress, slip | Chemical exposure, flammability |
Typical Speed | Fast | Medium-Fast (slow cleanup) | Medium | Medium-Fast (slow drying/treatment) | Medium-Slow | Variable (dwell/manual effort) |
Key Advantages | Non-abrasive, no residue, dry, fast, versatile | Aggressive stripping, profiling | Mild abrasive, deodorizes | No dust, good for large areas | Sanitizes, good for grease/organics | Specific chemical action |
Key Disadvantages | Cost, CO2 safety, noise, not for all tenacious soils | Damages substrate, high waste, dust hazard | Dust, residue, can affect pH | Water damage risk, wastewater | Moisture, slower, surface heat | Hazmat, residue, surface damage |
Common Applications | Electrical, molds, food, printing, historical, fire/mold | Heavy rust/paint, surface prep | Auto, fire/mold, graffiti | Exteriors, concrete, marine | Sanitizing, degreasing, upholstery | Degreasing, specific coatings |
Sources:.
This comparative analysis underscores that while dry ice blasting has a broad range of applicability and many compelling advantages, particularly its non-abrasive nature and lack of secondary waste, the “best” cleaning method is ultimately determined by the specific requirements of the task at hand. The complexity of these trade-offs often necessitates expert consultation to ensure the most effective, safe, and economical solution is chosen.
VIII. Why Professionals Make the Difference: The Case for Expert Dry Ice Blasting Services
While the concept of dry ice blasting might seem straightforward, its practical application involves a level of complexity, cost, and safety management that typically positions it beyond the scope of casual do-it-yourself (DIY) endeavors, especially for significant or industrial-scale projects. Opting for professional dry ice blasting services offers numerous advantages that ensure safety, efficiency, and superior results.
A. The Expertise & Training Edge
Professional dry ice blasting operators bring a depth of specialized knowledge and hands-on experience that is critical for success. This expertise encompasses a thorough understanding of:
- Equipment Operation: Familiarity with various types of blasting machines (pellet, MicroParticle, single-hose, two-hose), their capabilities, and their optimal operating parameters.
- Nozzle Selection: Knowledge of the wide array of available nozzles and their specific applications – choosing the right nozzle type, size, and angle for the contaminant, substrate, and accessibility of the area being cleaned is crucial for effectiveness and preventing damage.
- Parameter Optimization: Skill in adjusting critical parameters such as air pressure, dry ice feed rate, and standoff distance to match the specific cleaning challenge. Incorrect settings can lead to inefficient cleaning, excessive media consumption, or even damage to sensitive substrates.
- Substrate and Contaminant Assessment: Experience in evaluating different types of contaminants and substrates to determine the most effective and safest approach. As one source notes, “Professional training makes the difference between average and exceptional cleaning operations”.
Formal training and certification are increasingly important in this field. Reputable service providers invest in training their personnel, often through programs offered by equipment manufacturers like Cold Jet or industry organizations. Such training covers not only machine operation and effective cleaning techniques but also, crucially, essential safety guidelines. The effectiveness of dry ice blasting is not solely a function of the machine; it is significantly influenced by the skill and judgment of the operator. An untrained individual may struggle to achieve the desired level of cleanliness, waste resources, inadvertently damage the surface being treated, or, most critically, create avoidable safety hazards.
B. Access to Specialized, High-Cost Equipment
Industrial-grade dry ice blasting systems represent a substantial financial investment. This includes:
- Blasting Machines: Costs can range from approximately $10,000 for basic models to $50,000 or more for advanced, high-capacity units. Specialty machines or those with integrated features like IoT capabilities (e.g., Cold Jet Aero$_2$® ULTRA Series ) can be even more expensive.
- Air Compressors: High-volume, high-pressure air compressors capable of meeting the demands of dry ice blasters (e.g., 100 text{ cfm} at 80 text{ psi} for pellet systems ) are also costly pieces of equipment, often requiring dedicated power sources and maintenance.
- Ancillary Equipment: This includes a variety of specialized nozzles for different tasks , aftercoolers for air treatment (especially with diesel compressors ), extended hose lengths, and potentially on-site dry ice production equipment like pelletizers, which themselves are a major capital expense.
- Dry Ice Media Costs: The ongoing cost of purchasing dry ice can be significant, potentially running to several hundred dollars per hour of operation depending on the machine’s consumption rate.
For most individuals or businesses with only occasional or small-scale cleaning needs, the substantial upfront investment and recurring operational costs make purchasing this specialized equipment economically impractical. Professional service providers, on the other hand, can amortize these high capital costs over numerous projects and clients, making the technology accessible on a per-job basis. While equipment rental is an option, it still involves logistical challenges, media sourcing, and lacks the operator expertise provided by a full-service company.
C. Ensuring Rigorous Safety Compliance & Mitigating Risks
As detailed extensively in Section VI, dry ice blasting involves significant safety considerations that professionals are trained and equipped to manage effectively. These include:
- Hazard Management: Professionals understand the risks of CO2 asphyxiation, frostbite, high noise levels, and airborne projectiles. They are trained in implementing control measures such as proper ventilation strategies, CO2 monitoring, safe dry ice handling and storage procedures, and establishing controlled work zones.
- Personal Protective Equipment (PPE): Professional crews are equipped with and trained in the correct use of all necessary PPE, including insulated gloves, eye and face protection, hearing protection, and appropriate respiratory protection.
- Regulatory Compliance: Reputable service providers are knowledgeable about and adhere to relevant occupational safety and health regulations, such as those set by OSHA and NIOSH regarding CO2 exposure limits and other workplace safety standards.
- Emergency Preparedness: Professional teams typically have established emergency response plans and first aid capabilities to deal with any incidents that may occur.
Attempting dry ice blasting without a thorough understanding of these safety requirements and the proper equipment to manage them can lead to serious injury or even fatalities. Hiring professionals transfers the primary responsibility and liability for safe operation and risk mitigation from the client to the experienced service provider. This provides crucial peace of mind, particularly for businesses concerned with maintaining a safe work environment and complying with all applicable regulations.
D. Achieving Maximum Efficiency and Superior Results
Professional dry ice blasting services are geared to complete cleaning projects with maximum efficiency and to a higher standard of quality than typically achievable through DIY efforts. This is due to:
- Experience and Technique: Seasoned operators have encountered a wide variety of cleaning scenarios and have honed their techniques to remove different types of contaminants from diverse substrates quickly and effectively, without causing damage. They know how to optimize blasting parameters for speed and thoroughness.
- Appropriate Equipment Selection: Professionals have access to a range of machines and nozzles, allowing them to select the optimal combination for each specific job, ensuring that the cleaning is neither too aggressive (risking damage) nor too gentle (resulting in incomplete cleaning or excessive time).
- Reduced Downtime: Their efficiency translates directly into reduced downtime for the client’s operations or facilities. Case studies consistently demonstrate significant reductions in cleaning time and associated labor costs when professionals employ dry ice blasting, particularly when compared to traditional manual methods. For instance, one report indicated that a well-equipped dry ice blasting crew could clean up to 500 text{ sq ft} of contaminated surface per hour, often requiring half the labor of traditional methods for the same task.
- Consistent Quality: Professional application ensures a more uniform and thorough clean, leading to better overall results and potentially extending the life of the cleaned assets.
The value of this optimized process – combining skilled labor, the right tools, and efficient workflow – is difficult for an untrained individual to replicate, especially on complex or large-scale projects.
E. Responsible Contaminant Disposal
While a key benefit of dry ice blasting is that the blasting media (dry ice) sublimates and leaves no secondary residue, the contaminants that have been removed from the surface still need to be managed and disposed of correctly. These dislodged materials fall to the ground or are carried by the air stream and typically settle as a dry residue.
Professionals are equipped to handle this aspect of the job:
- Containment and Collection: They can implement measures to contain the spread of dislodged debris (e.g., using drop cloths, plastic sheeting, or localized vacuum systems) and then collect it efficiently, often using industrial vacuum cleaners.
- Proper Disposal: If the removed contaminants are hazardous (e.g., lead-based paint chips, certain types of mold, chemical residues), professional services will have procedures for their proper characterization, handling, and disposal in accordance with local environmental regulations. A DIY operator might be unaware of these requirements or ill-equipped to meet them, potentially leading to improper disposal and environmental contamination.
This “closing the loop” on the cleaning process by responsibly managing the removed waste ensures that the overall environmental benefits of dry ice blasting are fully realized.
F. The Importance of Insurance and Liability Coverage
Reputable professional dry ice blasting companies carry comprehensive insurance coverage to protect both their business and their clients from unforeseen incidents. This typically includes:
- Public Liability Insurance: Covers third-party injury or property damage that might occur as a result of the contractor’s operations.
- Damage to Property Being Worked Upon: Specifically covers accidental damage to the client’s property that is the subject of the cleaning work.
- Employers’ Liability Insurance: Protects their employees in case of work-related injuries.
- Professional Indemnity Insurance (Errors & Omissions): May cover claims arising from professional negligence or failure to perform services adequately.
This insurance provides a crucial financial safety net. While dry ice blasting is generally safe when performed correctly, the use of high-pressure equipment and the inherent hazards of dry ice mean that accidents or unintended damage, though rare with professionals, are not impossible. A DIY approach lacks this formal risk management and financial protection, leaving the property owner potentially liable for any damages or injuries that occur.
In summary, the combination of specialized expertise, high equipment costs, rigorous safety demands, efficiency gains, responsible waste handling, and insurance coverage makes professional dry ice blasting services the most sensible, safe, and ultimately cost-effective choice for the vast majority of applications, particularly in commercial, industrial, and sensitive restoration contexts.
IX. Embracing a Smarter, Drier Clean with Professional Assurance
Dry ice blasting has unequivocally established itself as a transformative cleaning technology, offering a powerful, precise, and environmentally responsible alternative to many conventional methods. Its core advantages – being non-abrasive, non-conductive, generating no secondary waste, and utilizing a waterless process – make it uniquely suited for a vast spectrum of demanding cleaning tasks.
From safely decontaminating sensitive electrical components and food processing equipment to gently restoring priceless historical artifacts and effectively remediating fire and mold damage, its versatility is remarkable.
However, the journey from understanding the impressive capabilities of dry ice blasting to successfully and safely implementing it is one that underscores the critical value of professional expertise.
The technology, while elegant in its scientific principles, involves sophisticated equipment with significant upfront and operational costs. More importantly, it carries inherent safety risks associated with cryogenic temperatures, potential CO2 displacement, high noise levels, and airborne particulates. Managing these risks effectively demands specialized training, rigorous adherence to safety protocols, appropriate personal protective equipment, and often, complex environmental controls like engineered ventilation and air monitoring.
While the allure of a DIY approach might exist for seemingly smaller tasks, the potential for inefficient cleaning, damage to valuable assets, or serious safety incidents often outweighs any perceived cost savings. Professional dry ice blasting services bring not only the correct industrial-grade equipment but also the crucial knowledge to select optimal parameters, the skill to execute the cleaning efficiently and thoroughly, and the commitment to operate within stringent safety and environmental guidelines. Furthermore, professionals provide the assurance of liability coverage and responsible contaminant disposal, completing the cleaning cycle in a truly comprehensive manner.
Ultimately, dry ice blasting is more than just a machine; it is a specialized tool that, like any advanced instrument, yields its best and safest results in the hands of a skilled artisan. For those seeking to leverage the full potential of this advanced cleaning method, engaging with experienced professionals is not merely a recommendation but an investment in quality, safety, efficiency, and peace of mind. As industries continue to seek smarter, drier, and more sustainable cleaning solutions, partnering with qualified dry ice blasting experts ensures that these advanced benefits are realized safely and effectively.