1. Tank & Vessel Cleaning: Scope and Significance
Defining Tank and Vessel Cleaning
Tank and vessel cleaning is a specialized industrial service that encompasses the comprehensive internal and external cleaning of a wide array of storage and processing units. These include, but are not limited to, storage tanks, silos, process vessels, reactors, and various types of containers. Such units are designed to hold a diverse range of materials, including liquids, powders, and bulk solids [User Query]. The scope of this cleaning activity extends beyond mere surface wiping; it involves systematic procedures to remove contaminants, residues, and unwanted materials to ensure operational integrity, safety, and compliance with industry standards.
Why Regular Cleaning is Crucial (Operational Efficiency, Safety, Compliance, Product Integrity)
The imperative for regular and correct tank maintenance and cleaning is multi-faceted, directly impacting operational efficiency, safety, regulatory compliance, and product integrity. Over time, tanks and vessels are prone to several detrimental issues if not properly maintained. Internal moisture build-up can lead to corrosion from the inside out, potentially causing tank damage and seepage, while also adversely affecting the quality of the stored contents.
Contact us!
Sludge accumulation is another common problem. Solids that enter the tank eventually break down, settle at the bottom, and form sludge. If not removed regularly, this sludge can significantly impact the quality of the tank’s contents and lead to clogged pipes and filters. Such blockages can, in turn, affect the smooth operation of plants, vehicles, and boilers. Furthermore, microbial contamination, primarily bacteria, can proliferate in the presence of moisture within the tank. These organisms thrive in such conditions, causing product contamination, further blockages, and damage to filters. Consequently, businesses operating storage tanks must implement adequate maintenance plans that include regular cleaning to mitigate these risks.
Beyond operational concerns, tank cleaning is fundamental for maintaining safety and integrity within industrial environments. Neglected tanks, with significant sediment or sludge buildup, can transform into safety hazards, potentially leading to system malfunctions or even fires. Therefore, regular cleaning is not merely a maintenance task but a critical component of a facility’s overall safety and risk management strategy.
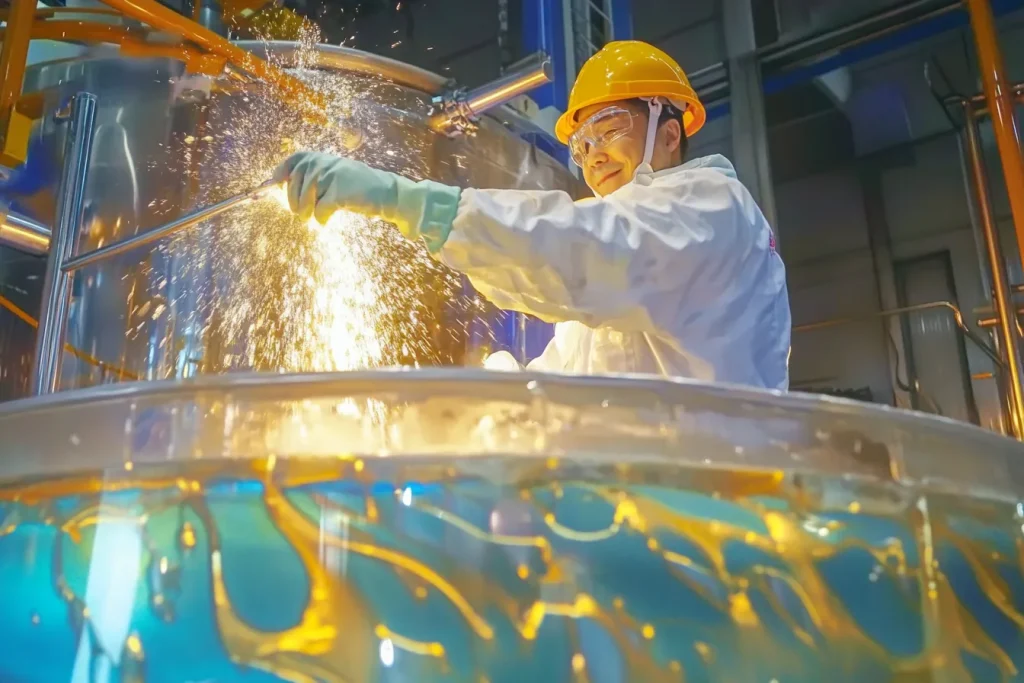
Overview of Materials Stored and Their Impact on Cleaning (Liquids, Powders, Bulk Solids)
Industrial tanks, silos, and bins are engineered to store a vast spectrum of materials. Common powders and dry bulk solids include items such as cement, flour, grains, lime, sand, plastic pellets, and various aggregates. The range of liquids and other bulk materials is equally diverse, encompassing oil, grain, coal, concrete, steel pellets, biomass ash, gravel, and clay. Some tanks are designed for highly specialized contents, such as maple syrup, which may require integrated heating systems to maintain the product’s viscosity and flow.
The nature of the stored material profoundly influences the cleaning approach. For instance, tanks holding food-grade products like flour, grains, or syrup demand stringent cleaning and sanitation protocols that differ significantly from those required for industrial chemicals, petroleum products, or aggregates. The physical and chemical properties of the stored substance—whether it is abrasive like sand, viscous like molasses, prone to creating hardened scale, or hazardous like certain petrochemicals—directly dictate the selection of cleaning methods, the types of chemical agents employed, and the necessary safety precautions.
This inherent diversity in stored materials means that a standardized, “one-size-fits-all” cleaning methodology is impractical and often unsafe. Each substance presents unique challenges related to the type of residue it leaves, its potential reactivity with cleaning agents, and the hazards it may pose during the cleaning operation.
For example, cleaning a tank that held flammable liquids requires different atmospheric monitoring and ignition control measures than cleaning a silo that stored inert powders. Similarly, residues from corrosive chemicals necessitate careful selection of cleaning agents to avoid damaging the tank itself, while food-grade tanks require cleaning agents that leave no harmful residues. This inherent complexity underscores the need for a high degree of specialized knowledge and experience to conduct effective and safe cleaning operations. The assessment of the previously stored material and the resulting residues is a critical first step in planning any tank cleaning project.
Furthermore, the field of industrial materials is not static. As industries innovate, new products, chemicals, and formulations are constantly being developed and subsequently stored in tanks and vessels. These advancements bring forth new types of residues and potential contaminants that may require novel cleaning approaches or adaptations of existing techniques.
Consequently, professionals in the tank cleaning sector cannot rely solely on historical knowledge. They must engage in continuous learning, research, and development to stay abreast of these industrial advancements and effectively address emerging cleaning challenges. This dynamic nature of industrial materials further reinforces the value of specialized, up-to-date expertise in tank and vessel cleaning.
2. Understanding the Landscape: Types of Tanks, Vessels, and Their Cleaning Challenges
Common Industrial Tanks and Vessels (Storage tanks, Silos, Process Vessels, Reactors, Containers)
The industrial landscape features a wide variety of tanks and vessels, each designed for specific purposes and presenting unique cleaning challenges. Storage tanks, for instance, are available in numerous configurations: vertical or horizontal cylindrical designs, open top or closed top, and with various bottom styles such as flat, cone, slope, or dish bottoms. Specific common types include:
- Atmospheric Tanks: These are designed to hold liquids at atmospheric pressure and are frequently used for substances with high flash points like fuel oil and bitumen. They are often vertical, cylindrical, and may have fixed or floating roofs.
- High-Pressure Tanks: Built to withstand significant internal pressures, these tanks store liquefied gases (e.g., hydrogen, chlorine, LPG) or compressed gases (e.g., CNG, MAPP gas). They are often classified as pressure vessels and require robust construction.
- Thermal Storage Tanks: Used for storing thermal energy, these can include large, insulated surface water tanks for seasonal heat storage or ice/slush tanks for short-term cold storage.
- Milk Tanks (Bulk Tanks): Found on dairy farms, these stainless steel tanks are used for cooling and holding fluid milk, requiring rapid cooling and cleaning after each collection to maintain sanitary standards.
- Septic Tanks: Part of small-scale sewage treatment systems, these tanks allow solids to settle and undergo anaerobic digestion.
- Mobile Tanks: While not strictly for storage, these tanks (e.g., oil tankers, railroad tank cars, road tankers) share many features and must be designed to handle sloshing loads and collision risks.
- Refinery Tanks: In refineries, common tank classifications include Crude Oil Tanks (COT), Product and Intermediate Storage Tanks (PIT), and Dispatch Area Tanks (DISPATCH).
- Silos and Bins: These structures are typically used for the storage of powders and dry bulk solid materials.
The physical configuration of the tank or vessel—its shape, size, internal structures (like baffles or agitators), and access points (manways, nozzles)—significantly impacts the cleaning strategy. For example, cleaning a tall, narrow silo will necessitate different equipment and techniques compared to a wide, horizontal cylindrical tank. The presence of internal components can create hard-to-reach areas, complicating the cleaning process.
Specialized tank designs, such as high-pressure tanks or floating roof tanks, introduce further unique cleaning challenges and safety considerations. Floating roof tanks, for example, are employed for storing liquids with lower flash points (e.g., jet fuel, petrol, crude oil) to minimize vapor space and reduce emissions. These roofs, which can be external (FR tanks) or internal (IFR tanks), have seals, legs, and pontoons that require specific attention during cleaning and inspection to ensure their integrity and functionality. The pontoons themselves can be confined spaces that may trap vapors and require separate cleaning and ventilation.
The design of a tank is intrinsically linked to the safety and environmental considerations of both its storage function and its subsequent cleaning. Floating roofs, engineered to control emissions during storage, create specific confined spaces (the pontoons) that must be carefully managed during cleaning operations. Similarly, the robust construction of high-pressure vessels, necessary to contain their contents safely, also dictates specialized procedures for depressurization, isolation, and entry during cleaning. Therefore, a thorough understanding of the tank’s design and its operational purpose is fundamental for anticipating cleaning challenges and implementing appropriate safety measures.
Materials of Construction and Their Implications for Cleaning (Carbon Steel, Stainless Steel, Aluminum, Liners)
The materials used to construct tanks and vessels play a critical role in determining appropriate cleaning methods and agents. Common construction materials include steel (carbon and stainless), concrete, glass-reinforced plastic, various thermoplastics, and polyethylene. The selection of a specific material is typically based on factors such as cost, its chemical resistance to the stored substance, and the required durability.
In custom bulk storage applications, the most frequently utilized metals are carbon steel, stainless steel, and aluminum. A primary consideration in material choice is the reactivity of the stored product. If the material to be stored is known to react with carbon steel, then stainless steel or aluminum may be specified for the tank or silo construction. Furthermore, tanks designed to hold abrasive materials, such as sand or ash, may require an internal bonded layer with an abrasive-resistant finish, commonly known as an AR plate or AR liner, to protect the underlying tank structure.
The tank’s material of construction directly dictates the types of cleaning chemicals and mechanical actions that can be safely employed. For instance, highly acidic or alkaline cleaning agents that might be effective on stainless steel could severely corrode carbon steel or damage certain types of liners.
Similarly, aggressive mechanical cleaning methods like high-pressure water jetting at extreme pressures or abrasive blasting might be unsuitable for tanks with delicate internal coatings or those made from softer materials. Using incompatible cleaning methods can lead to thinning of the tank wall, damage to protective liners, or even catastrophic tank failure, resulting in costly repairs, environmental contamination, and safety hazards.
Ideally, the lifecycle management of a tank should incorporate considerations for future cleaning requirements right from the design and material selection phase. Choosing a material that is not only resistant to the stored product but also compatible with effective and common cleaning agents for that product’s residues can significantly reduce long-term maintenance costs, minimize cleaning times, and enhance overall safety.
If a tank material is selected without due consideration for the types of cleaning agents that will be needed to remove the anticipated residues, facility operators might face a dilemma where effective cleaning is difficult or impossible without risking damage to the tank itself. This highlights the importance of a holistic approach to tank design, where ease and safety of cleaning are considered alongside storage capacity and product compatibility, ultimately leading to more durable, economically maintained, and safer assets.
Common Contaminants and Residues (Sludge, Scale, Rust, Biofilms, Product Residues)
Over operational periods, all tanks and vessels tend to accumulate a variety of contaminants and residues. These can include sludge, general debris, various chemical contaminants, and water. Sludge is often a complex mixture formed from broken-down solids that have entered the tank and settled at the bottom. In tanks storing crude oil or petroleum products, sludge can also contain water, sand, dirt, salts, scale, waxes, asphaltenes, and other inorganic substances.
Microbial contamination, particularly the growth of bacteria, is common when moisture is present within a tank. These microorganisms can form biofilms on tank surfaces, leading to product contamination, blockages, and damage to associated equipment like filters. Scale (such as beerstone in brewery tanks or water stains), rust, and other hard deposits are also frequently encountered. Additionally, residual amounts of the previously stored product will almost always be present.
Accurate identification of the specific type(s) of contaminant is a crucial first step in selecting the most appropriate and effective cleaning methodology. For example:
- Sludge often requires physical removal methods, which can range from manual shoveling (in appropriate circumstances and with extreme caution) to the use of vacuum trucks or advanced robotic systems. In oil tanks, sludge may also contain recoverable hydrocarbons, making specialized recovery techniques part of the cleaning process.
- Scale and rust typically necessitate chemical cleaning, often with acidic solutions, to dissolve and remove these tenacious deposits.
- Biofilms and other microbial contamination require not only physical removal but also disinfection steps using appropriate biocides or sanitizing agents to ensure the tank is safe for future use, especially in food-grade or pharmaceutical applications.
- Product residues will vary widely based on the product itself, from easily soluble materials to those that are sticky, hardened, or highly viscous, each requiring a tailored cleaning strategy.
The following table provides a quick overview of common tank/vessel types and their associated cleaning considerations:
Table 1: Common Tank/Vessel Types and Cleaning Considerations
Tank/Vessel Type | Common Contents | Typical Contaminants | Key Cleaning Challenges |
---|---|---|---|
Atmospheric Crude Oil Tank (COT) | Crude Oil | Heavy sludge (asphaltenes, waxes, sand, water), H₂S, pyrophoric iron sulfides | Large volume, heavy/viscous sludge, flammable atmosphere, H₂S toxicity, potential for pyrophoric ignition, confined space complexity (e.g., floating roofs) |
Stainless Steel Food Silo | Flour, Sugar, Grains | Product dust, caked material, potential for insect infestation, microbial growth | Maintaining food-grade hygiene, preventing cross-contamination, dry cleaning methods often preferred, access to tall structures |
Lined Chemical Reactor | Various reactive chemicals, polymers | Product build-up, unreacted materials, catalyst residues, scale | Chemical compatibility of cleaning agents with liner and previous contents, potential for hazardous reactions, thorough rinsing required |
High-Pressure Gas Storage | Compressed Natural Gas (CNG), Liquefied Petroleum Gas (LPG) | Minimal physical residue, potential for oil carryover from compressors, trace contaminants | Ensuring complete depressurization, safe handling of residual gas, specific purging requirements, inspection for internal integrity |
Process Vessel (e.g., Mixer) | Pharmaceutical ingredients, paints, adhesives | Viscous product residues, dried material, colorants, binders | Complete removal of all previous product to avoid batch contamination, cleaning of complex internal geometries (agitators, baffles) |
Septic Tank | Domestic wastewater | Sludge (settled solids), scum (floating fats/oils), grit | Removal of biologically active sludge, odor control, potential for pathogenic organisms |
Mobile Road Tanker | Petrol, Diesel, Chemicals, Food Products | Product residues, water, sediment | Frequent product changes requiring thorough cleaning to prevent cross-contamination, internal baffles, ensuring complete drainage |
This table illustrates the direct link between the type of tank, its typical use, the nature of the resulting contamination, and the inherent complexities and hazards associated with its cleaning. This understanding is foundational to planning safe and effective tank cleaning operations.
3. Core Tank Cleaning Methodologies and Sub-Tasks
The Sinner’s Circle: Balancing Chemistry, Time, Temperature, and Mechanical Action
A fundamental principle underpinning all effective industrial cleaning, including tank and vessel cleaning, is the concept often referred to as the “Sinner’s Circle.” This model posits that four primary factors interact to achieve cleanliness: Chemistry, Time, Temperature, and Mechanical Action. The successful and efficient cleaning of any tank or vessel relies on achieving an optimal balance among these four elements. Utilizing the correct equipment and procedures helps to strike this perfect balance, leading to outcomes characterized by efficiency, precision, and reliability.
These four factors are interdependent:
- Chemistry refers to the cleaning agents used (e.g., detergents, solvents, acids, alkalis). The right chemical can dissolve or react with contaminants, making them easier to remove.
- Time is the duration for which the cleaning agent is in contact with the soiled surface, or the duration of the mechanical action.
- Temperature of the cleaning solution or the tank environment can significantly influence the rate of chemical reactions and the viscosity of residues.
- Mechanical Action involves the physical force applied to dislodge and remove contaminants, such as scrubbing, jetting, or agitation.
Altering one factor can often compensate for a reduction in another. For example, increasing the temperature of a cleaning solution might reduce the required contact time or the concentration of the chemical needed. Similarly, employing stronger mechanical action, such as high-impact spray nozzles, can lessen the reliance on aggressive chemicals or elevated temperatures, potentially reducing chemical consumption by as much as 30% and shortening cleaning cycles by up to 40%.
This interplay is not merely a theoretical concept but a practical framework that professionals use to optimize cleaning processes. By understanding these interdependencies, it becomes possible to develop more sustainable and cost-effective cleaning strategies. For instance, if a tank’s material of construction is sensitive to harsh chemicals or high temperatures, cleaning professionals can strategically intensify the mechanical action or extend the contact time with milder chemicals to achieve the desired level of cleanliness.
This ability to strategically balance these four factors is a key differentiator of professional tank cleaning services, allowing them to tailor the cleaning process to the specific requirements of the tank, its previous contents, and any operational constraints, while also minimizing costs, environmental impact, and safety risks.
Sludge, Slops, and Sediment Removal
The removal of accumulated sludge, slops, and sediment is a primary objective in many tank cleaning operations. Each of these materials presents distinct characteristics and requires specific removal techniques and equipment.
Sludge Removal:
Sludge, commonly found at the bottom of tanks, is often a complex and viscous mixture of product residues, water, solid particles (like sand and dirt), scale, waxes, and other inorganic or organic substances. In crude oil storage tanks, sludge is a significant concern, and its removal is necessary to maximize storage capacity, prevent blockages, and mitigate corrosion.8
- Techniques and Equipment:
- Manual and Basic Mechanical Methods: Traditional methods include manual shoveling (with extreme caution and adherence to confined space safety protocols), the use of vacuum trucks to suck out liquefied sludge, and front-end loaders for accessible, de-energized tanks. Power spray nozzles can also be used to break down and mobilize sludge.
- Advanced Mechanical and Robotic Systems (Non-Man Entry): To enhance safety and efficiency, various remote and robotic systems have been developed. These include Camera Manway Cannons that blast water or diluent through existing manways to liquefy sludge while the tank remains sealed. Tank Sweeps, inserted through manways, provide liquid pressure for effective cleaning and offer more coverage. Remotely Operated Vehicles (ROVs) and Remote Operated Crawlers (ROCs) are submersible or mobile units that can agitate, liquefy, and pump sludge from within the tank. The S.R.S.® (Sludge Recovery System) by Nuova Saimar is a notable non-man entry technology that uses high-pressure jet washers installed on the tank roof to crush sludge and fluidize hydrocarbons in a closed-loop system, recovering up to 98% of the contained hydrocarbon. Other robotic tank cleaning systems utilize positioning booms and high-pressure jetting cannons with cameras, controlled remotely.
- Hydrocarbon Recovery from Oil Sludge: For tanks that have contained crude oil or other valuable hydrocarbons, sludge removal often incorporates hydrocarbon recovery techniques. This may involve diluting the remaining crude above the sludge with a compatible hydrocarbon (like diesel or kerosene) and pumping it off. The sludge itself can then be washed with water and specialized chemical agents (e.g., JPX products from Jayne Products) to disperse the oil, which is then floated to the surface for recovery via decanting. Agitation using side-entry mixers, Butterworth-type mixers, or rotary nozzles facilitates this process. Chemical sludge breakers can also be used to reduce tackiness and transfer hydrocarbons to a diluent medium.
- Centrifuges and Filter Presses: Two-phase or three-phase centrifuges can be used to separate oil, water, and solids from sludge or wastewater, allowing for oil recovery and efficient solids removal. Filter presses allow wastewater to drip through a filtering device, separating sludge from water and reducing disposal costs.
The choice of sludge removal technique depends on factors such as the volume and nature of the sludge, tank design and accessibility, the hazards present (flammability, toxicity), and whether hydrocarbon recovery is economically viable or environmentally desirable. The strong industry trend is towards non-man entry systems due to the significant safety benefits they offer by eliminating or minimizing human presence in hazardous confined spaces.
Slops Removal:
“Slops” typically refer to the residual mixture generated from tank cleaning operations, particularly on oil tankers or similar vessels, but the term can apply to mixed liquid waste from various tank cleaning scenarios. Slops usually comprise water, residual oil, sludge, and various cleaning chemicals.16
- Process: The removal and treatment of slops is a multi-step operation.
- Separation: A three-phase separator is often used to break down the slops into its core components: oil, water, and solids. Heat and specific chemicals may be applied to facilitate this separation, along with mechanical separation techniques.
- Collection and Transfer: On vessels, slops are often collected in dedicated slop tanks before being transferred to specialized collection vessels or directly to shore-based reception facilities.
- Treatment at Reception Facilities: These facilities, operated by licensed waste management companies, further process the slops through methods like additional separation and filtration to remove contaminants.
- Disposal/Recovery: The separated oil is generally reclaimed for reuse, providing an economic benefit. The treated water is discharged under strict regulatory guidelines, while the remaining solids are disposed of in an environmentally compliant and safe manner, which could include recycling, incineration, or landfilling.
Improper disposal of slops can have severe environmental consequences, particularly for marine ecosystems. Therefore, slops management is heavily regulated.
Sediment Removal:
Sediment in tanks can range from fine particles to larger debris and can originate from the stored product, corrosion, or external sources. In ballast water tanks on ships, sediment poses a unique environmental risk as it can harbor nonindigenous aquatic species.18
- Techniques and Equipment:
- Ballast Tank Sediment: Specific options include saltwater flushing in designated open sea exchange areas (mixing open sea water with residual ballast water and sediment, then discharging the mixed water), upland disposal under controlled arrangements in port or drydock, or the use of department-approved sediment reception facilities that ensure the elimination of nonindigenous species.
- General Industrial Sediment: For other types of tanks, sediment can be removed using various methods. Centrifugal separators, like the American Wheatley SRS Series, use tangential flow and vortex action to force suspended sediment to the bottom sump for easy removal. Mechanical methods such as manual or mechanized scraping and brushing are used to dislodge solid deposits and stubborn residues. High-pressure water jetting is effective for removing solid residues, dirt, and scale. Steam cleaning can help dissolve and loosen residues, including some types of sediment. In some cases, abrasive blasting might be used for very hard or tenacious deposits, though care must be taken to avoid damaging the tank surface. Industrial vacuuming is also commonly employed to remove loosened sediment and residual liquids.
The evolution of techniques for removing sludge, slops, and sediment clearly reflects a significant industry-wide movement. This trend is driven by a dual imperative: firstly, to minimize or entirely eliminate human entry into tanks due to the inherent and often severe safety risks associated with confined spaces, such as hazardous atmospheres, engulfment, and physical dangers. Secondly, there is an increasing focus on maximizing the recovery of valuable resources from what was previously considered waste. The recovery of hydrocarbons from oily sludge and slops, for example, not only reduces the volume of waste requiring disposal but also offers an economic return. This shift is propelled by stricter safety regulations, growing environmental consciousness, and economic incentives, moving the industry away from purely disposal-oriented approaches towards more sophisticated and sustainable waste management practices.
Chemical Cleaning
Chemical cleaning plays a vital role in removing contaminants that are not easily dislodged by mechanical means alone, such as scale, rust, certain product residues, and biofilms. The selection and application of chemical agents are critical steps governed by the Sinner’s Circle principles.
- Types of Chemical Agents:
Tank cleaning chemicals can be broadly categorized based on their properties and targets 9:- Alkaline Detergents/Cleaners: These are effective for removing proteinaceous and organic soils, greases, and some mineral deposits. They are commonly used in food processing tanks and wastewater treatment plants. Alkaline substances like sodium hydroxide or potassium hydroxide help neutralize acids and dissolve residues.
- Acidic Cleaners/Descalers: These are formulated to remove inorganic soils such as mineral scale (e.g., calcium carbonate, beerstone), rust, and water stains. Common acids used in descaling formulations include hydrochloric acid, phosphoric acid, sulfamic acid, citric acid, acetic acid, glycolic acid, formic, and lactic acid. The choice of acid depends on the type of scale and the tank material’s compatibility.
- Solvent-Based Cleaners: These are effective for dissolving oil, grease, hydrocarbon residues, adhesives, resins, and paint overspray. However, many solvents pose health and environmental risks and require careful handling, proper ventilation, and appropriate PPE.
- Disinfectants/Sanitizers: Used to kill microorganisms like bacteria and deactivate viruses, these are crucial in tanks requiring hygienic conditions, such as those in the food and beverage, pharmaceutical, or water storage industries. Chlorine-based solutions or products like HuwaSan TR50 (a hydrogen peroxide and silver-based disinfectant) are examples.
- Specialized and Eco-Friendly Cleaners: Products like Scale Remover STSR are marketed as non-corrosive, biodegradable alternatives for removing struvite, vivianite, limescale, calcium carbonate, and rust. Custom-formulated chemicals, including those with thickeners or foaming agents, can be designed for specific descaling requirements. Jayne Products offers specialized chemicals like JPX for hydrocarbon decontamination and H₂S removal.
The selection process must consider the nature of the contaminant, the tank’s material of construction (to avoid corrosion or damage), safety (toxicity, flammability of the chemical), environmental impact, and cost. Often, a sequence of chemicals is used; for example, an alkaline wash to remove organic soils followed by an acidic wash to remove mineral scale.
- Application Methods:
Effective chemical cleaning relies on ensuring adequate contact between the cleaning agent and the contaminated surface for a sufficient duration (exposure time) at the optimal temperature. Common application methods include:- Circulation/Agitation: Chemicals are circulated through the tank using pumps and spray nozzles (e.g., rotary jet heads like Alfa Laval GJ series ) or agitated within the tank to ensure all surfaces are wetted and to provide some mechanical assistance. Clean-In-Place (CIP) systems automate this process, helping to control chemical concentrations, temperature, and time consistently.
- Soaking (Standstill Soaks): The tank or specific parts are filled with the chemical solution and allowed to soak for a predetermined time. This is suitable for removing stubborn deposits from tanks, containers, and even pumps.
- Spraying: Low-pressure spray application can be used to apply chemicals to specific areas, especially those that are hard to reach. This method is also used for cleaning walls and surfaces.
- Foaming: Some cleaning agents can be applied as a foam, which increases contact time on vertical and overhead surfaces, improving cleaning efficiency and reducing chemical consumption.
- Manual Application: For pesticide spray tanks, methods include rinsing, filling the tank partially with water and a 1-2% cleaning solution (e.g., household ammonia or bleach, with cautions against mixing), spraying out the solution, and then performing final rinses.
- Neutralization of Cleaning Chemicals:
After the chemical cleaning process, the spent cleaning solutions, especially strong acids or alkalis, and contaminated rinse water must be managed responsibly. This often involves neutralization to adjust the pH to acceptable levels for discharge or disposal.- Neutralization Tanks: Facilities may have dedicated neutralization tanks that alter the pH of corrosive waste drainage through dilution or by adding neutralizing chemicals before discharge to a sewer system. These tanks themselves require periodic maintenance to remove accumulated sediment or spent neutralizing agents (like limestone rock).
- Chemical Neutralization Procedures: For acidic waste, a base such as sodium carbonate, calcium hydroxide, or sodium hydroxide is slowly added to an ice water solution of the acid while stirring until a pH of at least 5.5 to 9.0 is achieved. The neutralized solution can then, if compliant with local regulations, be disposed of down the drain, typically followed by a large volume of rinse water. Similarly, alkaline wastes would be neutralized with an acid.
- Containment and Characterization: All rinse water generated from cleaning processes must be contained and characterized to determine its properties and appropriate disposal method. It cannot be assumed to be non-hazardous.
High-Pressure Water Washing (Hydroblasting)
High-pressure water washing, also known as hydroblasting or water jetting, is a powerful mechanical cleaning method that utilizes the kinetic energy of water projected at high velocity to dislodge and remove residues, scale, rust, paint, and other contaminants from tank surfaces. This technique is widely used across many industries due to its effectiveness and ability to reduce or eliminate the need for chemical cleaning agents.
Pressures used in hydroblasting can vary significantly depending on the application, ranging from lower pressures for general cleaning to ultra-high pressures (UHP), sometimes exceeding 1000 bar (approximately 14,500 psi), for removing very tenacious deposits or surface preparation. The effectiveness of hydroblasting is a function of both water pressure and flow rate. Options include using low pressure with high water volume or high pressure with lower water volume. High-pressure, low-volume systems can be particularly advantageous as they reduce overall water consumption and the volume of wastewater generated, which in turn lowers disposal costs, especially if heated water is used.
A key advantage of modern high-pressure tank cleaning systems is the integration of specialized 360° rotating nozzles (such as those from Flowplant or the Alfa Laval GJ series). These nozzles are inserted into the tank and rotate in multiple planes, delivering high-impact water jets that systematically cover every internal surface of the vessel. This automated or semi-automated approach significantly enhances safety by minimizing or eliminating the need for personnel to enter the confined space of the tank, thereby avoiding associated risks. The cleaning process becomes quicker and more consistent compared to manual methods.
The choice of specific nozzles, water pressure, and flow rate depends on the type and tenacity of the deposits, the tank’s internal configuration and material, and the desired level of cleanliness. While hydroblasting is primarily a mechanical cleaning method, it can sometimes be used in conjunction with detergents or other cleaning agents for enhanced effectiveness on certain types of contaminants.
Industrial Vacuuming
Industrial vacuuming is an essential sub-task in many tank cleaning operations, employed for the removal of liquids, sludges, slurries, and solid particulate matter from tanks and vessels. Powerful vacuum trucks (wet and dry capabilities) or portable industrial vacuum systems are used to efficiently extract materials, significantly reducing the need for manual labor and minimizing worker exposure to potentially hazardous substances.
Vacuuming is utilized at various stages of the cleaning process:
- Initial Product Removal: After the bulk product has been drained via normal means, vacuum systems are often used to remove the remaining “heel” or puddles of product from the tank floor, below the low suction line.
- Sludge and Sediment Removal: Liquefied or mobilized sludge and sediment can be effectively vacuumed out of the tank.
- During Cleaning Operations: Vacuum systems are used concurrently with methods like high-pressure water washing to continuously remove dislodged debris and wastewater.
- Final Clean-up: After washing and rinsing, vacuums with squeegee attachments can be used to remove final residual liquids, ensuring the tank is as dry as possible.
A critical consideration, especially when dealing with tanks that have contained flammable materials or where combustible dusts may be present, is the risk of ignition. In such potentially explosive atmospheres, standard industrial vacuums can be a source of ignition due to static electricity buildup or electrical components. Therefore, the use of ATEX-certified (Atmosphères Explosibles) industrial vacuum cleaners is mandatory in these environments. These specialized vacuums are designed and constructed to prevent spark generation and safely collect flammable liquids and combustible dusts. They comply with stringent safety standards (e.g., UNI EN 17348:2022) and are certified for use in specific hazardous zones (e.g., ATEX Zone 0, 1, or 2 for gases, and Zone 20, 21, or 22 for dusts). Features of ATEX vacuums often include antistatic filters (e.g., M-class), HEPA filters for fine dust, grounding, and construction from non-sparking materials. Some are powered by compressed air to eliminate electrical ignition sources entirely.
The following table provides a comparative overview of the primary tank cleaning methodologies:
Table 2: Overview of Tank Cleaning Methods
Method | Brief Description | Typical Applications (Contaminant & Tank Type) | Key Equipment | Advantages | Disadvantages/Limitations | Safety Considerations |
---|---|---|---|---|---|---|
Sludge Removal – Manual | Physical removal of sludge by personnel entering the tank, using tools like shovels, scrapers. | Accessible tanks with non-highly hazardous sludge; smaller tanks. | Shovels, buckets, scrapers, squeegees, PPE. | Can be thorough for specific areas if done correctly. | Extremely labor-intensive, high safety risks (confined space, chemical exposure, physical hazards), slow, generates contaminated PPE. | Highest risk; requires full confined space entry protocols, atmospheric monitoring, extensive PPE, rescue plan. Not suitable for many hazardous sludges. |
Sludge Removal – Non-Entry Robotic/Remote | Use of robotic crawlers, cannons, sweeps, or systems like S.R.S.® to dislodge, liquefy, and pump sludge. | Large tanks, hazardous sludge (e.g., crude oil, chemicals), tanks with limited access, situations where man-entry is undesirable. | ROVs, ROCs, Manway Cannons, Tank Sweeps, S.R.S.® (Jet Washers), high-pressure pumps, vacuum systems, control units, cameras. | Significantly reduces/eliminates confined space entry risks, faster, can recover hydrocarbons, often more efficient for large volumes. | High capital cost for equipment, may require skilled operators, effectiveness can depend on sludge characteristics and tank internals. | Lower direct risk to personnel as entry is avoided. Risks associated with equipment operation, high pressures, potential for unexpected reactions if sludge composition is unknown. Requires careful planning and skilled operation. |
Chemical Cleaning – Acidic | Circulation or soaking with acidic solutions to dissolve scale, rust, and inorganic deposits. | Tanks with mineral scale (e.g., calcium carbonate, sulfates), rust, beerstone, water stains. Metal tanks (stainless steel, some carbon steel). | Pumps, hoses, spray nozzles (CIP systems), chemical storage tanks, PPE. | Effective for dissolving tenacious inorganic deposits, can reach inaccessible areas. | Corrosive to some materials, hazardous chemicals require careful handling and disposal, potential for harmful fumes, neutralization required. | Chemical exposure (skin, inhalation), corrosive hazards, potential for reaction with tank material or residual product. Requires appropriate PPE, ventilation, and careful chemical selection and handling. Neutralization of spent chemicals is critical. |
Chemical Cleaning – Alkaline | Circulation or soaking with alkaline solutions to remove organic soils, fats, greases, some protein residues. | Food processing tanks, some chemical tanks, tanks with organic or biological fouling. | Pumps, hoses, spray nozzles (CIP systems), chemical storage tanks, PPE. | Effective for saponifying fats and breaking down organic matter. | Can be corrosive to some materials (e.g., aluminum), hazardous chemicals require careful handling and disposal, potential for harmful fumes. | Chemical exposure, corrosive hazards (especially strong alkalis). Requires appropriate PPE, ventilation, and careful chemical selection. |
Chemical Cleaning – Solvent | Use of solvents to dissolve oils, greases, hydrocarbons, resins, paints. | Tanks contaminated with petroleum products, paints, adhesives, polymers. | Pumps, spray systems, ventilation equipment, specialized PPE. | Highly effective for specific organic contaminants. | Many solvents are flammable, toxic, and/or VOCs, requiring strict safety and environmental controls; disposal can be costly. | High flammability risk, toxicity (inhalation, skin absorption), often requires specialized respiratory protection and ventilation. ATEX-rated equipment may be needed. |
High-Pressure Water Washing (Hydroblasting) | Using high-velocity water jets to physically dislodge contaminants from tank surfaces. | Removal of hard scale, rust, paint, product buildup, general cleaning. Suitable for most tank materials if pressure is controlled. | High-pressure pumps (up to 1000+ bar), lances, automated 360° nozzles, vacuum systems for water/debris removal. | Reduces/eliminates chemical use, fast, effective for many deposit types, non-entry options available. | Can generate large volumes of wastewater, potential for surface damage if pressure is too high or material is soft, high energy consumption. | High-pressure jet injuries, slip hazards from water, noise. If entry is required, confined space rules apply. Automated systems reduce direct personnel risk. |
Industrial Vacuuming | Removal of liquids, sludges, powders, and solids using powerful vacuum systems. | Removing residual product, sludge, sediment, cleaning solutions, dusts. | Vacuum trucks (wet/dry), industrial vacuum cleaners (including ATEX-certified models), hoses, nozzles. | Efficient removal of various materials, reduces manual handling and exposure, can handle hazardous materials with right equipment. | Can be slow for very viscous or large volumes of solids if not pre-liquefied, potential for static buildup if not grounded. | If handling flammable/combustible materials, ATEX-certified and properly grounded equipment is essential to prevent ignition. Confined space entry rules apply if personnel enter for vacuuming. |
Steam Cleaning | Using high-temperature steam to sanitize and loosen residues. | Sanitizing food-grade tanks, removing grease, oils, some organic matter. | Steam generators, hoses, nozzles, PPE. | Good for sanitization, can loosen some residues effectively. | Can generate hot, humid conditions, may not be effective for all deposit types, potential for burns. | Burn hazards from steam and hot surfaces, heat stress in confined spaces. Requires appropriate PPE and ventilation. |
Abrasive Blasting | Propelling abrasive media (sand, grit, beads) at high velocity to remove tough deposits and coatings. | Heavy rust, thick scale, old paint/coatings. Typically for surface preparation prior to re-coating. | Blasting pots, compressors, hoses, nozzles, specialized abrasives, containment systems, PPE. | Very effective for tenacious coatings and corrosion. | Can damage tank surface if not controlled, generates significant dust (often hazardous), requires containment and waste disposal. | High dust levels (respiratory hazard, visibility), abrasive material rebound, noise. Requires specialized PPE including respiratory protection, and often full containment. |
This table provides a comparative look at the various methods, highlighting their applications, equipment, and crucial considerations, thereby underscoring the complexity involved in selecting the optimal approach for any given tank cleaning scenario.
4. Safety First: Navigating the Risks of Tank Cleaning
Tank and vessel cleaning is an inherently hazardous operation, demanding meticulous planning, stringent adherence to safety protocols, and a well-trained workforce. The potential for serious injury, illness, or even fatality is significant if risks are not properly identified and controlled.
Identifying Common Hazards
A multitude of hazards can be encountered during tank cleaning operations. These include :
- Fire and Explosion: Many tanks store or have stored flammable liquids or materials that can produce flammable vapors. When these vapors mix with air (oxygen) in the right proportions, any ignition source can lead to a fire or catastrophic explosion. Ignition sources are varied and can include static electricity generated during cleaning, sparks from electrical or non-intrinsically safe mechanical equipment, hot surfaces (e.g., from welding or cutting nearby), or exothermic chemical reactions, such as the oxidation of pyrophoric iron sulfide deposits found in tanks that have held sour crude oil.
- Chemical Hazards: Tanks often contain residual toxic chemicals. Exposure can occur through skin contact (leading to burns or absorption), inhalation of vapors or mists (causing respiratory problems or systemic poisoning), or accidental ingestion. The health effects can be acute (immediate) or chronic (long-term), depending on the chemical’s toxicity, concentration, and duration of exposure.
- Oxygen Deficiency: An oxygen-deficient atmosphere, defined by OSHA as below 19.5% oxygen by volume , can cause asphyxiation. Oxygen can be displaced by other gases (e.g., nitrogen used for purging, carbon dioxide from reactions), consumed by combustion or rusting processes, or depleted by microbial activity within the tank.
- Oxygen Enrichment: Conversely, an oxygen-enriched atmosphere (above 23.5% oxygen by volume ) significantly increases the flammability of materials and the risk of fire or explosion.
- Physical Hazards: These are numerous and include slips, trips, and falls on wet, oily, or uneven surfaces, especially in poorly lit conditions. Falling objects, striking against or being struck by equipment, and head injuries are also common. The confined nature of tanks often means awkward postures and restricted movement, increasing ergonomic risks. These physical hazards can be exacerbated when fire risks necessitate minimal artificial lighting.
- Microbiological Hazards: The presence of water, sludge, or organic residues at the bottom of a tank can foster the growth of harmful bacteria, fungi, and other microorganisms. Contact with or inhalation of aerosols containing these microbes can lead to allergic reactions, infections, or diseases.
- Emissions: The cleaning process itself can release toxic gases, flammable vapors, or hazardous liquids into the air, or lead to spills that contaminate water or soil. Such emissions pose a significant environmental concern and can also affect worker health if not properly controlled.
The dangers in tank cleaning are often interconnected. For instance, the risk of a flammable atmosphere might necessitate the use of non-sparking tools and limit the type of lighting that can be used, which in turn could increase the risk of slips, trips, and falls due to poorer visibility. An oxygen-deficient atmosphere might simultaneously be a flammable or toxic one. This interplay means that safety management cannot address each hazard in isolation. A comprehensive, integrated safety management system is essential, encompassing all stages from initial risk assessment through to emergency response and post-cleaning review. Such a system must consider how different hazards can combine or exacerbate one another, demanding a holistic safety plan rather than a piecemeal approach.
Confined Space Entry: A Critical Concern
Many, if not most, tank and vessel cleaning operations involve entry into a confined space, which is one of the most hazardous activities in industrial settings. Regulatory bodies like the U.S. Occupational Safety and Health Administration (OSHA) and the UK’s Health and Safety Executive (HSE) have established stringent definitions and requirements for working in such environments.
- Defining Confined Spaces:
- OSHA Definition: A space is considered a “confined space” if it meets all three of the following criteria: 1) It is large enough and so configured that an employee can bodily enter and perform assigned work; 2) It has limited or restricted means for entry or exit (examples include tanks, vessels, silos, storage bins, hoppers, vaults, and pits); and 3) It is not designed for continuous employee occupancy.
- HSE (UK) Definition: A confined space is defined as one which is both enclosed (or largely enclosed) and has a reasonably foreseeable “specified risk” to workers. These specified risks include fire, explosion, loss of consciousness, asphyxiation, or drowning. Understanding these legal definitions is the crucial first step in recognizing when the comprehensive protocols for confined space work must be implemented.
- Potential Hazards in Confined Spaces:
Confined spaces can harbor a multitude of hazards, often concentrated or exacerbated by the enclosed nature of the space, which limits natural ventilation and restricts escape or rescue efforts. These hazards include 1:- Atmospheric Hazards: Oxygen deficiency or enrichment; flammable or explosive atmospheres (gases, vapors, combustible dusts); toxic gases, vapors, or fumes (e.g., hydrogen sulfide, carbon monoxide, volatile organic compounds (VOCs), solvent vapors, welding fumes).
- Engulfment Hazards: The potential for an entrant to be surrounded and overcome by a liquid (drowning) or a flowable solid material like grain, sand, or powder (leading to asphyxiation or crushing).
- Configuration Hazards (Entrapment/Asphyxiation): Internal structures such as inwardly converging walls, or floors that slope downward and taper to a smaller cross-section, can trap or asphyxiate an entrant.
- Physical Hazards: Temperature extremes (heat stress or cold stress); excessive noise levels (amplified by reverberation); vibration; slips, trips, and falls; falling objects; electrical hazards (from equipment or lighting); mechanical hazards (from moving parts like agitators or conveyors if not properly isolated).
- Biological Hazards: Presence of bacteria, viruses, molds, insects, or animals.
- Permit-to-Work Systems: Elements and Importance:
OSHA designates a confined space as a Permit-Required Confined Space (PRCS) or “permit space” if it has one or more of the following characteristics: 1) Contains or has the potential to contain a hazardous atmosphere; 2) Contains a material that has the potential for engulfing an entrant; 3) Has an internal configuration such that an entrant could be trapped or asphyxiated; or 4) Contains any other recognized serious safety or health hazard.
Entry into a PRCS is strictly controlled by a permit-to-work system. This is a formal, written authorization and safety checklist procedure that ensures all potential hazards are identified, assessed, and effectively controlled before entry is allowed and during the work. The entry permit is a cornerstone of confined space safety and typically includes :- Identification of the permit space to be entered.
- Purpose of the entry.
- Date and authorized duration of the entry.
- Names of authorized entrants, attendants, and entry supervisors.
- Identified hazards of the permit space.
- Measures used to isolate the space and to eliminate or control hazards (e.g., lockout/tagout, purging, ventilation).
- Acceptable entry conditions (e.g., atmospheric readings).
- Results of initial and periodic atmospheric tests (oxygen, flammables, toxics), along with the tester’s signature or initials.
- Rescue and emergency services information and how to summon them.
- Communication procedures.
- Required personal protective equipment (PPE).
- Any other relevant permits (e.g., hot work permit). The permit must be signed by the entry supervisor, verifying that all pre-entry preparations have been completed and that the space is safe for entry. It must be posted at the entry point or otherwise made available to entrants.
- Roles and Responsibilities: Entrant, Attendant, Supervisor:
OSHA’s standard (29 CFR 1910.146) clearly defines the duties for each member of the confined space entry team 47:- Authorized Entrant: Knows the hazards they may face, including signs/symptoms of exposure; properly uses all required PPE; maintains communication with the attendant; exits the space immediately if ordered, if an alarm sounds, or if they recognize warning signs of exposure or a prohibited condition.
- Attendant: Remains stationed outside the permit space for the duration of entry operations; knows the hazards and behavioral effects of exposure; maintains an accurate count of entrants; maintains communication with entrants; monitors conditions inside and outside the space; controls access to the space; summons rescue and emergency services as soon as they determine entrants may need assistance; orders evacuation if a prohibited condition arises or if they detect behavioral effects of hazard exposure in entrants; performs no duties that might interfere with their primary duty to monitor and protect entrants; and does not abandon their post unless relieved by another qualified attendant.
- Entry Supervisor: Knows the hazards; verifies that all tests, procedures, and equipment specified on the permit are in place before signing and authorizing entry; oversees entry operations; terminates entry and cancels the permit when work is completed or if a prohibited condition arises; verifies that rescue services are available and that the means for summoning them are operable; removes unauthorized individuals from the area.
- Pre-Entry Checks: Isolation, Lockout/Tagout, Ventilation:
Before any entry, critical physical steps must be taken to render the space safe:- Isolation: The permit space must be removed from service and completely protected against the release of energy and material into the space. This involves :
- Lockout/Tagout (LOTO): De-energizing and securing all energy sources (electrical, mechanical, hydraulic, pneumatic, chemical, thermal, etc.) that could pose a hazard.
- Blanking or Blinding: Installing solid plates in pipelines to prevent material flow.
- Misaligning or Removing Sections of Lines/Pipes: Physically disconnecting pipes.
- Double Block and Bleed: Closing two valves in a line and opening a vent/drain valve between them to safely release any trapped material or pressure.
- Ventilation: If the atmosphere is hazardous or potentially hazardous, mechanical ventilation using fans or blowers is often required to purge contaminants and supply fresh air. Specific procedures include :
- Positioning the fan to draw in clean, fresh air (avoiding re-circulation of contaminated air or intake of exhaust fumes).
- Using flexible ducting to deliver air to all parts of the space, especially remote areas.
- Ventilating for a sufficient period (e.g., a minimum of 5 minutes is mentioned in one source for NCSU policy ) before testing the atmosphere and allowing entry.
- Continuing ventilation throughout the entry operation. It is crucial to understand that ventilation is a means of controlling atmospheric hazards; it is not a substitute for eliminating the source of the hazard where feasible.
- Isolation: The permit space must be removed from service and completely protected against the release of energy and material into the space. This involves :
The highly detailed and stringent nature of requirements for confined space entry—spanning definitions, hazard assessments, permit systems, clearly defined roles, and meticulous pre-entry preparations—collectively highlights a fundamental safety principle: avoiding entry altogether is always the preferred initial strategy. The significant risks inherent in sending personnel into confined spaces, coupled with the extensive regulatory overhead, have been major drivers for innovation in the tank cleaning industry. The development and increasing adoption of non-man entry technologies, such as robotic cleaning systems, remote-controlled cannons, and advanced sludge fluidization techniques , are direct responses to these challenges. These technologies aim to achieve the necessary cleaning standards without exposing human workers to the dangers of confined spaces, thereby bypassing many of the associated risks and complex compliance procedures. This shift represents a significant advancement in both worker safety and operational efficiency for tank cleaning operations.
Atmospheric Monitoring: Ensuring a Breathable Environment
Continuous and accurate atmospheric monitoring is a critical safety measure for any tank cleaning operation involving confined space entry, or where there is a potential for hazardous atmospheres to develop.
- Gases to Monitor:
The specific gases monitored depend on the tank’s previous contents, the cleaning agents used, and the processes occurring within or near the tank. However, standard monitoring typically includes 1:- Oxygen (O2): Monitoring for both oxygen deficiency (less than 19.5% by volume) and oxygen enrichment (greater than 23.5% by volume).
- Flammable/Combustible Gases and Vapors: Measured as a percentage of the Lower Explosive Limit (%LEL). The Upper Explosive Limit (UEL) is also relevant for understanding the flammability range. Common combustible gases include methane, propane, hydrogen, and vapors from solvents or petroleum products.
- Toxic Gases:
- Commonly Monitored: Carbon Monoxide (CO) and Hydrogen Sulfide (H2S) are frequently monitored due to their common occurrence and high toxicity.
- Volatile Organic Compounds (VOCs): A broad category of carbon-containing chemicals that evaporate easily at room temperature. Many VOCs are toxic or carcinogenic (e.g., benzene).
- Other Specific Toxics: Depending on the situation, other toxic gases such as ammonia (NH3), chlorine (Cl2), hydrogen cyanide (HCN), sulfur dioxide (SO2), nitrogen dioxide (NO2), phosgene (COCl2), ozone (O3), and various solvent vapors may need to be monitored.
The order of testing is typically: 1) Oxygen, 2) Flammable gases and vapors, and 3) Potential toxic air contaminants.
- Types of Gas Detection Equipment:
A variety of gas detection instruments are available, tailored to different needs 55:- Multi-Gas Monitors: These are the most common for confined space entry, capable of simultaneously detecting oxygen, LEL, CO, H2S, and often one or two other selectable toxic gases. Examples include the Dräger X-am® series (e.g., X-am® 2500, 5000, 8000), MSA ALTAIR 5X, and WatchGas POLI series. These typically use electrochemical sensors for O2 and toxics, and catalytic bead or infrared sensors for LEL.
- Single-Gas Detectors: Used for monitoring a specific known gas hazard. Examples include the Dräger Pac® series or WatchGas UNI, available for O2, CO, H2S, SO2, NH3, Cl2, etc., primarily using electrochemical sensors.
- Photoionization Detectors (PIDs): These instruments are used for detecting a broad range of VOCs at low concentrations (ppm or ppb levels). PIDs use ultraviolet light to ionize VOC molecules, and the resulting current is measured. Examples include Dräger X-pid® series and WatchGas NEO. Some multi-gas monitors can be equipped with a PID sensor.
- Colorimetric Detector Tubes: These are glass tubes filled with a reagent that changes color when exposed to a specific gas. They provide a spot measurement for a wide variety of gases and vapors, often used for substances for which electronic sensors are not readily available or for quick checks.
- Infrared (IR) Sensors: Used in some multi-gas detectors for detecting combustible gases (especially in low oxygen or inert atmospheres where catalytic sensors may not work) or specific gases like carbon dioxide (CO2).
- Calibration Procedures:
To ensure accuracy and reliability, gas detectors must be regularly calibrated and tested 60:- Full Calibration: This involves adjusting the instrument’s sensor responses to match known concentrations of certified calibration gas. This should be done according to the manufacturer’s instructions, typically at regular intervals (e.g., every 6-12 months, or more frequently depending on use and exposure).
- Bump Test (Functional Check): This is a qualitative check performed before each day’s use. A known concentration of test gas is briefly passed over the sensors to ensure they respond and that all alarms (audible, visual, vibrating) activate correctly. The International Safety Equipment Association (ISEA) strongly recommends this practice. If a monitor fails a bump test, it must undergo a full calibration before being used. OSHA expects employers to follow manufacturer’s instructions for calibration and maintenance.
- Interpreting Results:
Understanding the readings from atmospheric monitors is crucial for making safety decisions 40:- Oxygen: The acceptable range is typically 19.5% to 23.5% by volume. Readings outside this range indicate a hazardous atmosphere.
- Combustible Gases (%LEL): Most monitors will alarm at 10% of the LEL. OSHA regulations for permit-required confined spaces generally prohibit entry if the LEL is 10% or greater. Some procedures, like alternate entry, may require even lower levels, such as 5% LEL. If a reading is above the UEL, the atmosphere is too rich to burn, but ventilation could bring it into the flammable range.
- Toxic Gases: Readings are compared against established occupational exposure limits:
- OSHA Permissible Exposure Limits (PELs): Legally enforceable limits for an 8-hour time-weighted average (TWA) exposure. For example, CO PEL is 50 ppm; H2S PEL is 20 ppm (though this can vary, and lower limits are often recommended).
- NIOSH Recommended Exposure Limits (RELs): Recommendations by the National Institute for Occupational Safety and Health, often more stringent than PELs. For respirable crystalline silica, the NIOSH REL is 50μg/m3.
- ACGIH Threshold Limit Values (TLVs®): Guidelines developed by the American Conference of Governmental Industrial Hygienists, widely respected and often adopted.
- Immediately Dangerous to Life or Health (IDLH) Values: Represents an exposure concentration that is likely to cause death or immediate or delayed permanent adverse health effects or prevent escape from such an environment. Entry into IDLH atmospheres requires the highest level of respiratory protection (e.g., SCBA) and stringent rescue provisions.
The following tables provide a quick reference for key safety hazards and common gases monitored:
Table 3: Key Safety Hazards and Mitigation Strategies in Tank Cleaning
Hazard Type | Specific Risks | Key Mitigation Measures |
---|---|---|
Flammable Atmosphere | Explosion, Fire | Continuous LEL monitoring, inerting (e.g., with nitrogen), ventilation (forced air), elimination of ignition sources (bonding/grounding, intrinsically safe equipment), hot work permit. |
Oxygen Deficiency | Asphyxiation, Impaired Judgment, Loss of Consciousness | Continuous O2 monitoring (target 19.5%-23.5%), forced air ventilation, supplied-air respirators (e.g., SCBA) if ventilation is insufficient. |
Oxygen Enrichment | Increased Fire/Explosion Risk | Continuous O2 monitoring (target <23.5%), identify and eliminate source of enrichment (e.g., leaking oxygen lines). |
Toxic Gas Exposure (e.g., H2S, CO, VOCs) | Poisoning, Organ Damage, Sensitization, Carcinogenicity | Continuous toxic gas monitoring (specific to anticipated hazards), forced air ventilation, supplied-air respirators (SCBA) or air-purifying respirators with appropriate cartridges, chemical specific PPE. |
Engulfment (Liquid/Solid) | Drowning, Asphyxiation, Crushing | Dewatering/draining tank, isolation of inlet pipes (blinding, double block & bleed), use of retrieval systems, stand-by rescue team. |
Chemical Burns/Contact | Skin/Eye Damage, Systemic Toxicity via Absorption | Appropriate chemical-resistant PPE (gloves, suits, boots, face shields, goggles), emergency eyewash/shower stations, proper chemical handling procedures. |
Physical Hazards (Slips, Trips, Falls, Struck-by, etc.) | Traumatic Injuries | Good housekeeping, adequate lighting (explosion-proof if needed), fall protection (guardrails, harnesses, lanyards), securement of equipment, proper tool use, head protection. |
Electrical Hazards | Shock, Electrocution, Ignition Source | Lockout/Tagout of electrical equipment, use of Ground Fault Circuit Interrupters (GFCIs), use of low-voltage or intrinsically safe equipment in wet/hazardous locations. |
Microbiological Hazards | Infections, Allergic Reactions | PPE (gloves, respirators if aerosolized), disinfection procedures, personal hygiene. |
Table 4: Common Gases Monitored in Confined Spaces and Their Significance
Gas Name | Chemical Formula | Typical Source in Tank Cleaning | Acceptable Level (OSHA PEL TWA unless noted) | LEL (Vol %) | IDLH Level (ppm unless noted) | Primary Health/Safety Danger |
---|---|---|---|---|---|---|
Oxygen | O2 | Ambient air; consumed by reactions (rusting, biological), displaced by other gases | 19.5% – 23.5% (OSHA Safe Range) | N/A | <19.5% or >23.5% | Asphyxiation (<19.5%), Increased flammability (>23.5%) |
Methane (Combustible) | CH4 | Natural gas, decomposition of organic matter, petroleum products | Monitor as %LEL (Alarm at 10% LEL) | 5.0% | 2,500 ppm (10% LEL is 5,000 ppm) | Flammable/Explosive, Asphyxiant (simple) |
Hydrogen Sulfide | H2S | Decomposition of organic matter, crude oil, sour gas, some chemical processes, sewage | 20 ppm (OSHA Ceiling) | 4.0% | 100 ppm | Highly Toxic (respiratory paralysis, olfactory fatigue), Flammable |
Carbon Monoxide | CO | Incomplete combustion (engines, heaters, welding), some chemical processes | 50 ppm | 12.5% | 1,200 ppm | Toxic (chemical asphyxiant – binds to hemoglobin), Flammable |
Benzene (VOC) | C6H6 | Petroleum products, solvents | 1 ppm (OSHA TWA), 5 ppm (STEL) | 1.2% | 500 ppm | Toxic, Carcinogen, Flammable |
Ammonia | NH3 | Refrigerants, cleaning agents, fertilizers, decomposition of organic matter | 50 ppm | 15% | 300 ppm | Toxic (irritant to eyes, skin, respiratory tract), Corrosive, Flammable (at higher conc.) |
Chlorine | Cl2 | Water treatment chemicals, bleaching agents, industrial processes | 1 ppm (OSHA Ceiling) | N/A | 10 ppm | Highly Toxic (severe respiratory irritant, corrosive) |
Volatile Organic Compounds (VOCs) – General | Various | Solvents, fuels, paints, cleaning agents, stored chemicals | Varies by specific VOC (e.g., PELs for individual compounds) | Varies | Varies | Toxicity varies (irritation, organ damage, carcinogenicity), many are flammable |
Note: PEL, LEL, and IDLH values can vary slightly depending on the reference source and specific regulations. Always consult current, authoritative sources for the specific substances and jurisdictions.
Personal Protective Equipment (PPE) Requirements
Personal Protective Equipment is the last line of defense against hazards that cannot be entirely eliminated or controlled by other means (engineering controls, administrative controls). The specific PPE required for tank cleaning depends on a thorough hazard assessment of the tank, its previous contents, the cleaning methods used, and the potential for exposure. Common PPE includes:
- Respiratory Protection: Essential when hazardous atmospheres are present or likely. This can range from:
- Air-Purifying Respirators (APRs): Equipped with cartridges or filters specific to the contaminants (e.g., organic vapor cartridges, HEPA filters for particulates like P95, N95, R95). APRs can only be used if there is sufficient oxygen and the contaminant type and concentration are known and within the respirator’s capacity.
- Supplied-Air Respirators (SARs): Including Self-Contained Breathing Apparatus (SCBA) or airline respirators, which provide clean breathing air from an independent source. These are required in oxygen-deficient atmospheres, IDLH conditions, or when contaminant levels are unknown or exceed APR capabilities. Proper selection, fit-testing (crucial for tight-fitting respirators), training, and maintenance of respirators are mandatory.
- Chemical-Resistant Clothing: Suits, coveralls, aprons, and hoods made from materials resistant to the specific chemicals being handled. This prevents skin contact and absorption.
- Gloves: Heavy-duty, chemical-resistant gloves appropriate for the substances encountered.
- Footwear: Chemical-resistant, slip-resistant safety boots, often with steel toes.
- Eye and Face Protection: Safety goggles, face shields to protect against chemical splashes, flying debris, and impact.
- Head Protection: Hard hats to protect against falling objects or head bumps.
- Fall Protection: For work at heights (e.g., on top of tanks, or entry into deep tanks), safety harnesses and lifelines connected to an anchor point or retrieval system are necessary.
- Retrieval Systems: For confined space entry, entrants often wear a full-body harness with a retrieval line attached, allowing for non-entry rescue by the attendant if needed.
Emergency Preparedness and Rescue Procedures
Despite all precautions, emergencies can occur. A robust emergency preparedness and rescue plan is a non-negotiable component of any tank cleaning operation, especially those involving confined space entry.
Key elements include:
- Written Emergency Rescue Plan: This plan must be developed and communicated to all personnel involved. It should detail procedures for various scenarios (e.g., atmospheric hazard, injury, engulfment).
- Rescue Team: A designated rescue team must be available. This can be an in-house team or an external service (e.g., local fire department). If relying on an external service, their capability to respond in a timely and effective manner to the specific site and confined space hazards must be verified.
- Training: Rescue team members must be extensively trained in rescue techniques, use of rescue equipment, first aid, and CPR. At least one member should typically be certified in CPR and first aid. They must also be trained as authorized entrants and be familiar with the specific hazards of the permit spaces they may need to enter. Regular practice drills (e.g., annually) are essential.
- Retrieval Systems: Non-entry rescue is always the preferred method. This involves using retrieval equipment such as a full-body harness worn by the entrant, a lifeline, and a mechanical winch or hoist operated by the attendant from outside the space. This equipment must be in place and ready for use before entry.
- Communication Systems: Reliable communication between the entrant, attendant, and emergency services is vital. This can include two-way radios, hardwired systems, or visual signals.
- First Aid and Medical Support: Appropriately stocked first-aid kits and eyewash/flushing stations must be readily available on-site. Procedures for obtaining prompt emergency medical services must be established.
- Summoning Rescue: Clear procedures for the attendant to summon the rescue team and other emergency services must be in place.
Attempting a rescue without proper training and equipment is extremely dangerous and is a leading cause of multiple fatalities in confined space incidents, as would-be rescuers often become victims themselves.
5. Managing the Aftermath: Waste Characterization, Disposal, and Documentation
Once the physical cleaning of a tank or vessel is complete, the generated waste materials—including sludge, sediment, spent cleaning chemicals, contaminated rinse water, and discarded PPE—must be managed and disposed of in a manner that complies with all applicable environmental regulations and protects human health. This phase involves careful waste characterization, classification, selection of appropriate treatment and disposal methods, and meticulous record-keeping.
Waste Characterization Procedures
Waste characterization is the process of determining the physical and chemical properties of the waste to ascertain if it is hazardous and to identify suitable management options. Both the U.S. Environmental Protection Agency (EPA) under the Resource Conservation and Recovery Act (RCRA) and the UK’s Environment Agency provide frameworks for this process.
- U.S. EPA RCRA Requirements:
Remediation waste, which includes materials generated from the cleanup of contaminated sites or equipment like tanks, often retains the hazardous characteristics of the contaminants it contains. RCRA provides two primary methods for characterizing waste 31:- Sampling and Analysis: This involves collecting representative samples of the waste and subjecting them to laboratory analysis to identify constituents and their concentrations. This data is then compared against regulatory thresholds for hazardous characteristics (ignitability, corrosivity, reactivity, toxicity).
- Process Knowledge: If the process that generated the waste is well understood, and the constituents of the materials used and produced are known, this knowledge can be used to determine if the resulting waste is likely to be hazardous. This requires thorough documentation of the process and materials. The EPA’s “contained-in” policy is particularly relevant for remediation wastes. It states that environmental media (like soil or water) or debris contaminated by a listed hazardous waste must be managed as hazardous waste until it no longer “contains” the hazardous waste (i.e., concentrations are below health-based levels or it has been treated).
- UK Environment Agency Guidelines (WM3):
In the UK, businesses are legally required to classify their waste before it is sent for recycling or disposal, using the List of Waste (LoW), also known as the European Waste Catalogue (EWC). The technical guidance document WM3 outlines a detailed step-by-step process for waste classification 66:- Check if the waste needs to be classified: Determine if the material is legally defined as waste and if it falls under classification requirements.
- Identify the code or codes that may apply: Consult the LoW to find potential classification codes based on the waste’s origin and nature.
- Identify the assessment needed: LoW codes are categorized as:
- Absolute Hazardous: The waste is always hazardous if assigned this code.
- Absolute Non-Hazardous: The waste is always non-hazardous if assigned this code.
- Mirror Hazardous / Mirror Non-Hazardous: These entries require further assessment of the waste’s properties to determine if it is hazardous.
- Determine the chemical composition of the waste: This can be achieved through:
- Manufacturer’s Safety Data Sheets (SDS) for unchanged products.
- Knowledge of a well-understood industrial process.
- Sampling and chemical analysis of the waste.
- Identify if substances in the waste are ‘hazardous substances’ or Persistent Organic Pollutants (POPs): Compare the identified chemical constituents against lists of classified hazardous substances and POPs.
- Assess the hazardous properties: Determine if the waste exhibits any of the 15 hazardous properties (HP1 to HP15) defined in regulations, based on concentration thresholds or testing.
- Assign the classification code(s) and describe hazardous properties.
The complexity inherent in waste characterization, particularly for mixed wastes, residues from complex chemical processes, or when relying on potentially incomplete process knowledge, presents a significant compliance challenge and potential liability for the waste generator. For instance, under UK regulations, if the composition of a waste falling under a “mirror” entry cannot be definitively determined to be non-hazardous through assessment, it must be classified as hazardous. This meticulous and often technical assessment process strongly favors the engagement of professional environmental or tank cleaning services that possess specialized expertise in waste sampling, analysis, and regulatory interpretation. Such services can significantly reduce the risk of misclassification and ensure compliance.
Classifying Waste: Hazardous vs. Non-Hazardous
Based on the characterization process, the waste is formally classified as either hazardous or non-hazardous. This classification is critical as it dictates all subsequent handling, storage, transportation, and disposal requirements and associated costs. In the UK, the assigned LoW code will often directly indicate if the waste is “absolute hazardous,” “absolute non-hazardous,” or if it’s a “mirror” entry requiring assessment to determine its hazardous status. Product labels with hazard pictograms (e.g., orange and black danger symbols or red and white hazard pictograms) can also provide an initial indication, but a full assessment is usually necessary for waste streams.
Environmentally Sound Disposal and Treatment Methods
The choice of disposal or treatment method must be environmentally sound and appropriate for the specific waste type and classification. The waste management hierarchy (reduce, reuse, recycle, recover, dispose) should guide these decisions, prioritizing options higher up the hierarchy whenever feasible.
Common methods include 29:
- Dewatering: Used to separate solids from liquids in non-hazardous sludges or slurries, reducing volume for landfill disposal. Water removed typically requires treatment.
- Sedimentation: Similar to dewatering, uses gravity to settle out solids from liquid waste streams.
- Composting: Applicable for organic, non-hazardous waste, transforming it into a soil conditioner.
- Incineration: A common method for hazardous waste, using high temperatures to destroy organic constituents. However, it can release air pollutants if not properly controlled and generates ash requiring disposal.
- Root-Zone Treatment: An eco-friendly method for relatively clean domestic or some industrial wastewaters, using natural processes involving plants and soil.
- Chemical Neutralization: For corrosive wastes (e.g., acidic or alkaline cleaning solutions), pH adjustment is performed to render them less hazardous before discharge or further treatment.
- Recycling and Recovery (e.g., Used Oil): Used oil from tank cleaning can often be processed through filtering, centrifugation, and chemical treatment to remove impurities. The recovered oil can then be recycled as a lubricant or used as a fuel, conserving resources and reducing the need for virgin oil. Hydrocarbon recovery from oily sludge in petroleum tanks is another example of resource recovery.
- Landfilling: Reserved for solid wastes that cannot be reused, recycled, or recovered, or for treated residues. Hazardous waste landfills have stringent design and operating requirements.
The increasing sophistication of tank cleaning and waste processing technologies reflects a broader industry trend towards more sustainable practices. Advanced techniques like on-site hydrocarbon recovery from sludge or the reprocessing of used oils into valuable products move tank cleaning operations away from a simple “dispose-of-everything” mindset. These methods align with global sustainability goals by minimizing waste sent to landfills and maximizing resource utilization. This shift not only benefits the environment but can also offer economic advantages through the sale of recovered products or reduced disposal costs, representing a key value proposition for advanced professional cleaning services.
Regulatory Requirements for Waste Disposal (US EPA, EU/UK regulations)
The disposal of waste generated from tank cleaning is strictly regulated to protect human health and the environment.
- United States (EPA):
- RCRA governs the management of hazardous waste from its point of generation to its final disposal (“cradle-to-grave”). This includes requirements for waste identification, manifests for transportation, and disposal at permitted Treatment, Storage, and Disposal Facilities (TSDFs).
- Land Disposal Restrictions (LDRs) under RCRA prohibit the land disposal of untreated hazardous wastes and set treatment standards that must be met before disposal.
- EPA effluent guidelines, such as those in 40 CFR Part 442 for Transportation Equipment Cleaning, establish standards for wastewater discharged to Publicly Owned Treatment Works (POTWs) or directly to U.S. waters under the National Pollutant Discharge Elimination System (NPDES) program. Prohibitions exist against discharging pollutants that could interfere with POTW operations, cause fires in sewers, or pass through untreated.
- For ship and barge cleaning, the International Convention for the Prevention of Pollution from Ships (MARPOL), implemented in the U.S. by the Act to Prevent Pollution from Ships and enforced by the U.S. Coast Guard, sets rules for the disposal of cargo residues and tank washings, depending on the cargo type (e.g., Annex I for oil, Annex II for noxious liquid substances).
- United Kingdom/European Union:
- The Environment Agency (EA) in England (with equivalent bodies in Scotland, Wales, and Northern Ireland) enforces waste management regulations. The overarching framework often stems from EU directives, which are transposed into national law.
- The List of Waste (LoW) / European Waste Catalogue (EWC) is fundamental for classifying waste.
- Specific regulations apply to activities like the decommissioning of Floating Production Storage and Offloading (FPSO) units, which must often be dismantled at EU-approved sites.
- Permitting requirements, such as Pollution Prevention and Control (PPC) permits or Waste Management Licences (WML), apply to facilities treating or disposing of waste.
Compliance with these complex and jurisdiction-specific regulations is mandatory, with significant penalties for violations.
Record Keeping and Documentation
Comprehensive record-keeping is a legal requirement and an essential component of demonstrating due diligence and compliance in waste management.
- United States (RCRA): Generators of hazardous waste, particularly Large Quantity Generators (LQGs), have extensive record-keeping obligations. These include:
- Waste Classification Records: Documentation of how waste determinations were made (test results, process knowledge used), applicable waste codes, and composition. Must be kept for at least three years after the waste is last sent for TSD.
- Hazardous Waste Manifests: Signed copies from the receiving TSDF must be kept for at least three years from the date the waste was accepted by the initial transporter.
- Contingency Plans and Incident Reports: Written contingency plans must be maintained and updated. Reports of incidents requiring plan activation must be submitted to the EPA and kept.
- Land Disposal Restrictions (LDR) Documentation: Notices, certifications, and waste analysis data demonstrating compliance with LDR treatment standards must be retained for at least three years.
- Tank and Storage Area Inspection Records: Records of regular inspections of hazardous waste storage tanks and areas.
- Biennial Reports: LQGs must submit reports to the EPA every two years detailing the types and quantities of hazardous waste generated and how it was managed. Copies must be kept for at least three years.
- General Requirements: For wastewater discharges, regulations typically require notification to authorities, ongoing monitoring of effluent quality, regular reporting of monitoring results, and maintenance of all related records.
The following table illustrates the connection between waste types from tank cleaning, their characterization, classification, and disposal:
Table 5: Waste Characterization and Disposal Options
Waste Type | Key Characterization Parameters | Typical Classification (Example Codes) | Preferred Disposal/Treatment Method(s) | Key Regulatory Considerations (Examples) |
---|---|---|---|---|
Oily Sludge (from petroleum tank) | Total Petroleum Hydrocarbons (TPH), Benzene, Toluene, Ethylbenzene, Xylenes (BTEX), heavy metals, water content, solids content, ignitability (flash point) | Often Hazardous (e.g., EPA D001 for ignitability, D018 for Benzene; UK LoW codes like 16 07 08* or 13 05 02*) | Hydrocarbon recovery (e.g., via S.R.S.®, chemical washing, centrifugation), stabilization, incineration, secure landfill (if treated to LDR standards). | RCRA hazardous waste regulations (manifests, LDRs, TSDF requirements). UK Hazardous Waste Regulations, Duty of Care. MARPOL Annex I for ship-generated oily sludge. |
Acidic Cleaning Solution (e.g., HCl) | pH, concentration of acid, presence of dissolved metals or other contaminants from tank | Hazardous if pH ≤2 (EPA D002 for corrosivity; UK LoW HP8 Corrosive). May also be toxic depending on dissolved contaminants. | Neutralization to acceptable pH (e.g., 5.5-9.0 ), precipitation of metals, discharge to POTW (if permitted and pretreated), or off-site treatment/disposal. | EPA pretreatment standards for discharge to POTW (40 CFR 403). RCRA for hazardous characteristics. UK consent to discharge, hazardous waste regulations if classified as such. |
Alkaline Cleaning Solution (e.g., NaOH) | pH, concentration of alkali, presence of dissolved organics or other contaminants | Hazardous if pH ≥12.5 (EPA D002 for corrosivity; UK LoW HP8 Corrosive). | Neutralization to acceptable pH, treatment for organic content (if high), discharge to POTW (if permitted and pretreated), or off-site treatment/disposal. | Similar to acidic solutions: EPA pretreatment standards, RCRA, UK consent to discharge, hazardous waste regulations. |
Contaminated Rinse Water | Residual cleaning chemicals, traces of stored product, suspended solids, pH, COD/BOD | May be hazardous or non-hazardous depending on contaminant levels and origin. | On-site treatment (e.g., oil/water separation, filtration, biological treatment), discharge to POTW (if compliant), or off-site disposal. | EPA effluent guidelines (e.g., 40 CFR 442 for transportation equipment cleaning). Local POTW discharge limits. UK environmental permits. |
Solid Sediment with Heavy Metals | Concentration of specific heavy metals (e.g., lead, chromium, cadmium) via TCLP testing | Hazardous if TCLP results exceed EPA regulatory limits (e.g., D008 for Lead). UK LoW codes for wastes containing dangerous substances. | Stabilization/solidification to immobilize metals, disposal in a hazardous waste landfill. | RCRA LDRs require treatment to reduce metal leachability. UK hazardous waste regulations for consignment and disposal. |
Non-Hazardous Inert Solids (e.g., sand, soil from tank bottom) | Visual inspection, process knowledge, basic screening for contaminants | Typically Non-Hazardous (e.g., UK LoW codes like 17 05 04 for soil and stones). | Landfill disposal (municipal or industrial non-hazardous landfill), potential for reuse if clean. | General waste management regulations, Duty of Care (UK). Ensure no commingling with hazardous waste. |
This table highlights that the journey from waste generation to final disposal is a regulated and technically involved process, demanding careful assessment and adherence to a complex web of rules to ensure environmental protection and legal compliance.
6. The Professional Advantage: Why Expert Tank Cleaning Services are Essential
While some basic tank cleaning tasks might appear manageable in-house, the complexities, inherent hazards, and stringent regulatory requirements associated with most industrial tank and vessel cleaning operations make engaging professional services not just a matter of convenience, but often a necessity for safety, compliance, and efficiency.
Specialized Knowledge and Experience
Professional tank cleaning companies possess a depth of specialized knowledge and a breadth of experience that is difficult for non-specialist, in-house teams to replicate, especially if tank cleaning is an infrequent task. This expertise encompasses:
- Understanding Diverse Systems: Professionals are familiar with a wide variety of tank designs (atmospheric, pressure, floating roof, silos, reactors), materials of construction (carbon steel, stainless steel, lined tanks), and the characteristics of myriad stored products (from crude oil and aggressive chemicals to food-grade substances and pharmaceuticals).
- Tailored Cleaning Methodologies: They can accurately assess the nature of contaminants (sludge, scale, biofilms, product residues) and apply the most effective cleaning methodologies, expertly balancing the “Sinner’s Circle” factors—chemistry, time, temperature, and mechanical action—for optimal results. This includes selecting appropriate chemical agents that are effective against the contaminant yet compatible with the tank material, and determining the correct application techniques.
- Handling Complex Challenges: Experienced firms are equipped to manage challenging scenarios, such as tanks with high sludge volumes, limited access points, severely corroded interiors, or those containing highly hazardous materials like benzene, hydrogen sulfide (H2S), pyrophorics, or even low-level radioactive sludge.
This accumulated knowledge, often built over decades and numerous diverse projects, allows professionals to anticipate potential problems, develop effective solutions, and execute cleaning operations safely and efficiently.
Access to Advanced Equipment and Technology
Professional tank cleaning services invest heavily in a wide range of specialized and advanced equipment, which is often beyond the practical or financial reach of individual facilities. This arsenal typically includes:
- High-Pressure Water Jetting Systems: Capable of generating pressures up to and exceeding 1000 bar (14,500 psi) for effective removal of hard scale, rust, and stubborn residues.
- Industrial Vacuum Trucks and Systems: Powerful units for wet and dry vacuuming of liquids, sludges, and solids, including ATEX-certified models for use in potentially explosive atmospheres.
- Non-Man Entry Robotic and Remote Cleaning Systems: Technologies such as manway cannons, remotely operated vehicles (ROVs), robotic crawlers (ROCs), tank sweeps, and integrated systems like Nuova Saimar’s S.R.S.® or Alfa Laval’s Gamajet (GJ) rotary jet heads significantly enhance safety by eliminating or minimizing human entry into confined spaces. These systems often incorporate cameras and high-pressure nozzles for precise and thorough cleaning.
- Confined Space Entry and Rescue Equipment: Full sets of PPE, atmospheric monitoring devices, ventilation equipment, retrieval systems, and communication gear.
- Waste Processing Equipment: Mobile units like centrifuges, filter presses, and thermal oxidizers for on-site waste volume reduction, hydrocarbon recovery, and VOC emission control.
- Decontamination Units: Trailers and containment systems for personnel and equipment decontamination.
This advanced technology not only enables safer and more thorough cleaning but also often leads to faster project completion and reduced downtime for the client’s facility.
Ensuring Safety and Regulatory Compliance (OSHA, EPA, HSE)
Navigating the complex and ever-evolving landscape of safety and environmental regulations is a core competency of reputable professional tank cleaning services. They invest in comprehensive training for their crews, including specialized certifications like OSHA 40-hour HAZWOPER, confined space entry and rescue, and specific equipment operation.
Professionals are well-versed in and adhere to all applicable local, state, national, and international regulations and standards, such as those from:
- OSHA (e.g., 29 CFR 1910.146 for Confined Spaces, Hazard Communication).
- EPA (e.g., RCRA for hazardous waste, Clean Water Act for effluent discharge).
- Department of Transportation (DOT) for hazardous materials transport.
- National Fire Protection Association (NFPA) and American National Standards Institute (ANSI) safety codes.
- UK Health and Safety Executive (HSE) (e.g., Confined Spaces Regulations 1997) and environmental bodies like SEPA.
They maintain rigorous safety protocols, conduct thorough pre-job hazard assessments, implement permit-to-work systems, and ensure proper atmospheric monitoring and PPE usage. This commitment to safety and compliance minimizes the client’s risk of accidents, injuries, environmental incidents, regulatory fines, and legal liabilities. Professional services can also provide necessary documentation, such as waste manifests and cleaning certificates (e.g., chlorination certificates for water tanks ), for compliance audits.
The sheer volume and intricacy of these regulations (OSHA, EPA, RCRA, DOT, NFPA, ANSI, HSE, SEPA, MARPOL, etc., as indicated by numerous sources) mean that maintaining full compliance demands dedicated resources, continuous training, and vigilant oversight. For a company whose primary business is not tank cleaning, attempting to manage this internally can be a significant operational distraction and a source of unmanaged, potentially costly, risk. Outsourcing to specialized professionals effectively transfers a substantial portion of this regulatory burden and its associated risks.
Efficiency, Cost-Effectiveness, and Reduced Downtime
While engaging professional services involves an upfront cost, it often proves more cost-effective in the long run. Professionals can typically complete cleaning projects more efficiently due to their experience, specialized equipment, and trained crews, leading to reduced tank downtime and quicker return to service.
Regular professional cleaning acts as preventative maintenance, helping to:
- Prevent costly problems such as product contamination, equipment blockages, and premature tank corrosion or failure.
- Extend the operational lifespan of the tank and associated equipment.
- Maintain optimal tank storage capacity and ensure smoother material flow, enhancing overall process efficiency. As one source notes, proactive cleaning is generally much cheaper than dealing with the significant financial and operational consequences of neglect.
Comprehensive Waste Management and Disposal
A significant advantage of hiring professional tank cleaning companies is their ability to provide turnkey waste management solutions. This typically includes:
- On-site waste characterization and profiling.
- Safe removal and segregation of waste materials.
- Proper packaging and labeling for transport.
- Transportation by licensed hazardous waste haulers.
- Compliant treatment and disposal through their network of approved facilities, which some larger service providers own and operate themselves. This comprehensive service relieves the client of the complex and highly regulated burden of waste disposal, ensuring it is handled legally and responsibly.
Liability and Insurance Considerations
Tank cleaning is a high-risk activity, and professional services carry comprehensive insurance coverage to protect both their operations and their clients from financial losses arising from accidents or incidents. This typically includes:
- General Liability Insurance: Covers third-party bodily injury and property damage.
- Workers’ Compensation Insurance: Covers injuries to their own employees.
- Tools & Equipment Insurance: Protects their specialized machinery.
- Commercial Auto Insurance: For their fleet of vehicles, including vacuum trucks.
- Pollution Liability Insurance (Environmental Impairment Liability): Crucial for covering cleanup costs and third-party damages resulting from spills or environmental contamination.
- Errors & Omissions (E&O) Insurance (Professional Liability): Covers claims of negligence or inadequate work.
The extensive insurance portfolio required for professional tank cleaning operations, including specialized coverages like Pollution Liability and E&O, underscores the multifaceted nature of the risks involved. These go beyond the standard risks covered by general liability and workers’ compensation. A facility choosing to use its own personnel for such a specialized, high-risk activity might find its existing insurance policies inadequate, potentially leaving the company financially exposed in the event of a significant incident. Hiring properly insured professional services mitigates this risk for the client.
Peace of Mind: Protecting Assets, Personnel, and the Environment
Ultimately, the decision to hire professional tank cleaning services is an investment in peace of mind. It provides assurance that a critical and potentially hazardous maintenance task is being handled by experts who are equipped with the right knowledge, tools, and safety protocols. This protects valuable assets from damage, safeguards personnel from injury, ensures compliance with environmental regulations, and allows the client company to focus on its core business operations with greater confidence. The early detection of potential tank issues during professional cleaning and inspection can also prevent major failures and unscheduled shutdowns, further contributing to operational stability and financial well-being.
7. Final Thougths
Tank and vessel cleaning is a complex, multifaceted operation critical to maintaining operational efficiency, ensuring product integrity, complying with stringent safety and environmental regulations, and preserving the longevity of valuable industrial assets. The process involves a detailed understanding of various tank types, the materials they store, and the specific contaminants that can accumulate, such as sludge, slops, sediment, scale, rust, and biofilms.
Effective cleaning relies on a balanced application of core methodologies—chemistry, time, temperature, and mechanical action—tailored to the specific situation. Key sub-tasks include sophisticated sludge, slops, and sediment removal techniques (increasingly utilizing non-man entry and robotic systems for safety and hydrocarbon recovery), targeted chemical cleaning for stubborn deposits, high-pressure water washing, and industrial vacuuming (with specialized ATEX-certified equipment for hazardous environments).
Safety is paramount throughout every stage of tank cleaning. Operations often involve navigating the severe risks associated with confined space entry, including hazardous atmospheres (oxygen deficiency/enrichment, flammable gases, toxic vapors), engulfment, and various physical hazards. Rigorous adherence to confined space entry procedures—including permit-to-work systems, clearly defined roles for entrants, attendants, and supervisors, comprehensive pre-entry checks like isolation and lockout/tagout, continuous atmospheric monitoring with calibrated equipment, appropriate PPE, and robust emergency preparedness and rescue plans—is non-negotiable.
The management of waste generated from cleaning operations is another critical component, requiring meticulous waste characterization, classification as hazardous or non-hazardous according to EPA RCRA or UK Environment Agency (WM3) guidelines, selection of environmentally sound treatment and disposal methods, and diligent record-keeping to ensure full regulatory compliance.
Given the inherent dangers, technical complexities, specialized equipment requirements, and extensive regulatory obligations associated with tank and vessel cleaning, the engagement of professional cleaning services is strongly recommended. These expert firms bring specialized knowledge, advanced technology, trained and certified personnel, and comprehensive safety and environmental compliance programs.
They offer efficient and cost-effective solutions, manage waste responsibly, carry appropriate insurance, and ultimately provide facility owners and operators with the peace of mind that this essential maintenance task is being performed safely, effectively, and in full accordance with all legal and industry standards. Investing in professional tank cleaning is an investment in safety, operational reliability, environmental stewardship, and long-term asset protection.