1. Understanding Degreasers
What is a Degreaser?
Degreasers are specialized cleaning agents meticulously formulated to tackle and remove challenging accumulations of grease, oils, fats, waxes, and similar stubborn residues from various surfaces. Unlike general-purpose cleaners, degreasers possess unique chemical properties designed to break down these non-water-soluble substances.
Grease and oil, by their chemical nature, repel water, making them notoriously difficult to lift using standard soap and water alone. Degreasers overcome this challenge through specific chemical actions, ultimately serving the purpose of rendering surfaces clean, hygienically sound, and safe by effectively eliminating these tenacious soils. They are indispensable tools in maintaining cleanliness and functionality in diverse settings, from home kitchens to heavy industrial environments.
Contact us!
Why are Degreasers Necessary?
The need for degreasers arises from the common occurrence of grease buildup in numerous environments. In kitchens, cooking processes inevitably lead to deposits of cooking oils and animal fats on stovetops, ovens, range hoods, and backsplashes. Automotive maintenance generates residues of engine oil, lubricants, and grime on engines, tools, and garage floors. Industrial settings frequently encounter heavy grease and oil contamination on machinery, factory floors, and parts from manufacturing processes.
Failing to address this buildup can have significant consequences. Accumulated grease can impair the efficiency and smooth operation of machinery. Greasy floors and surfaces create serious safety hazards, increasing the risk of slips and falls, particularly in busy kitchens or workplaces.
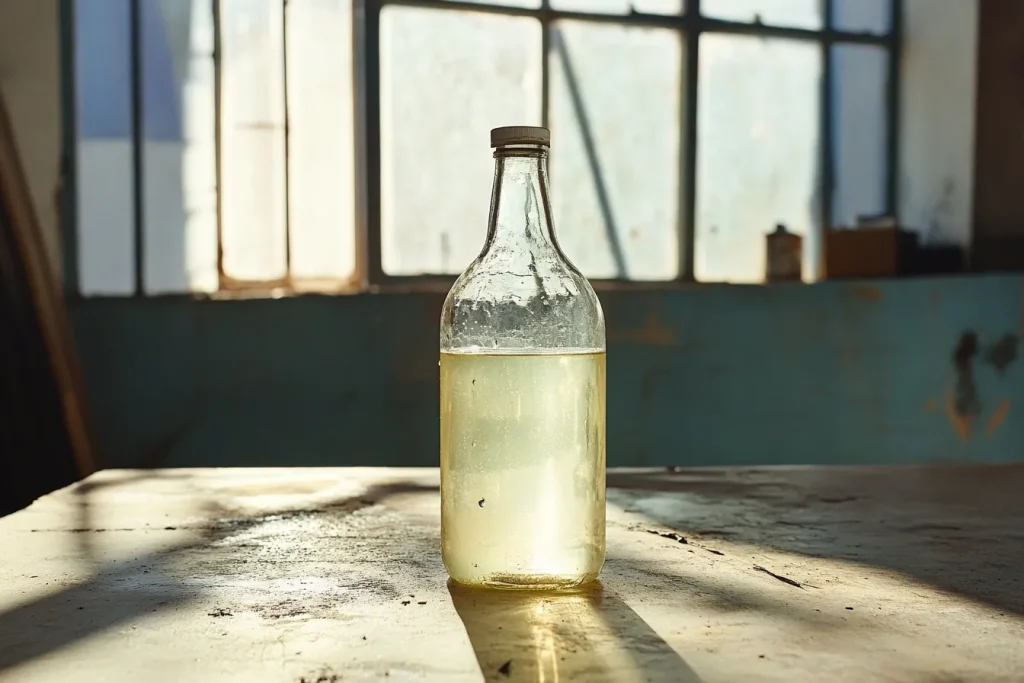
Furthermore, grease acts as a trap for dirt and bacteria, compromising hygiene standards, which is especially critical in food preparation areas. Over time, persistent grease can also damage surfaces or equipment, leading to costly repairs or replacements, and negatively impact the overall appearance of a space.
The fundamental reason degreasers are essential lies in the chemical incompatibility between grease (which is hydrophobic or ‘water-fearing’) and water. Standard cleaners may struggle to overcome the strong adhesion of heavy or baked-on grease to surfaces.
Degreasers employ specific chemical mechanisms – utilizing solvents or alkaline agents – to break this barrier, either dissolving the grease, chemically converting it, or suspending it in a way that allows it to be washed away. The prevalence of activities that generate grease across domestic, commercial, and industrial sectors means that degreasers are not merely cleaning products; they are vital tools for maintenance, safety, and hygiene management.
2: The Science Behind Degreasing – How They Work
The Chemistry of Grease Removal
The core challenge in removing grease is twofold: first, breaking the physical and chemical bonds holding the grease to the surface, and second, making the grease compatible with water or easily wiped away. Degreasers achieve this through several key chemical mechanisms, often employed in combination within a single formulation.
- Solvent Action: This mechanism relies on the principle of “like dissolves like.” Solvents, which can include various organic compounds such as hydrocarbons (e.g., mineral spirits, kerosene), terpenes (e.g., d-Limonene), alcohols, or glycol ethers (e.g., 2-butoxyethanol, ethylene glycol phenyl ether), work by dissolving grease and oil at a molecular level. They essentially break down the complex structure of the grease into a liquid solution, allowing it to be wiped or rinsed away. This approach is particularly common in heavy-duty degreasers designed for industrial and automotive applications where thick, stubborn grease is prevalent.
- Saponification: This process is characteristic of highly alkaline degreasers (those with a high pH, typically above 12). Strong alkaline chemicals, such as Sodium Hydroxide (NaOH, also known as Caustic Soda) or Potassium Hydroxide (KOH, Caustic Potash), react directly with fats and oils, which are chemically known as triglycerides. This reaction, called saponification, hydrolyzes the fats and oils, converting them into glycerol and fatty acid salts – essentially creating soap directly from the grease itself. Since soap is water-soluble, the originally water-insoluble grease is transformed into a substance that can be easily rinsed away with water. Other alkaline builders like Sodium Metasilicate (Na2SiO3) also contribute to alkalinity and cleaning power.
- Emulsification: Water-based degreasers frequently depend on emulsification, facilitated by surfactants (surface-active agents). Surfactants are unique molecules possessing a dual nature: one end is hydrophilic (water-attracting), and the other end is hydrophobic or lipophilic (oil-attracting). When introduced to a mixture of oil and water, these surfactants arrange themselves at the interface between the two liquids. Their oil-loving tails penetrate the grease droplets, while their water-loving heads remain in contact with the water. This action breaks the grease into microscopic droplets and surrounds them, forming a stable mixture called an emulsion. These suspended droplets are prevented from coalescing or re-depositing onto the surface and can be readily carried away during rinsing. Common surfactant ingredients include ethoxylated alcohols (like Alcohol C9−C11, ethoxylated) and sulfonates (like Sodium xylene sulfonate). This mechanism effectively allows oil and water, which normally repel each other, to mix.
- Detergency/Wetting: Closely related to emulsification, detergency involves surfactants reducing the surface tension of the water-based cleaning solution. Lowering the surface tension allows the cleaner to spread more easily and penetrate underneath the grease and soil, effectively lifting it from the surface. These active wetting agents enhance the cleaner’s ability to make intimate contact with both the soil and the substrate.
- Dispersion/Deflocculation/Anti-Redeposition: To ensure effective cleaning, it’s crucial that once grease and dirt are lifted, they don’t simply settle back onto the surface. Many degreasers contain dispersing agents or anti-redeposition agents. These chemicals keep the removed soil particles finely dispersed and suspended within the cleaning solution (deflocculation), preventing them from re-adhering to the cleaned area during the washing or rinsing process.
- Complexation/Chelation: Some soils contain mineral components or metal ions (like calcium or magnesium from hard water) that can interfere with the cleaning process or form scale. Certain alkaline cleaners incorporate chelating or complexing agents. These agents bind with metal ions, forming stable, water-soluble complexes. This prevents the metal ions from reacting negatively with other cleaning components or precipitating out of solution, ensuring they are rinsed away effectively.
The specific combination of these mechanisms within a degreaser formulation is carefully chosen based on the intended application. Different types of grease – from light kitchen oils to heavy industrial lubricants – respond differently to these chemical actions.
Solvent action offers potent dissolving power but often comes with safety and environmental drawbacks, including flammability and volatile organic compound (VOC) emissions. Saponification is highly effective for animal fats and vegetable oils but requires strong alkalinity, which can be corrosive to certain surfaces and hazardous to skin.
Emulsification provides versatility and is generally safer but might lack the aggressive power of strong solvents for the most challenging industrial grease. Consequently, formulators often blend these approaches – for instance, a water-based degreaser might use surfactants for emulsification alongside moderate alkalinity for some saponification – to achieve a balance of cleaning performance, user safety, surface compatibility, and environmental considerations.
3: Types of Degreasers – Choosing Your Formulation
Selecting the appropriate degreaser depends heavily on the nature of the task, the type of grease involved, the surface being cleaned, and safety and environmental considerations. Degreasers can be broadly categorized based on their primary chemical formulation.
Solvent-Based Degreasers
- Description: These formulations utilize organic chemical solvents as their primary active ingredient to dissolve grease. Common solvents include hydrocarbons (like mineral spirits, kerosene, xylene), chlorinated solvents (like Trichloroethylene – TCE, Perchloroethylene – PCE, Methylene Chloride), terpenes (like d-Limonene, though often categorized as ‘natural’), alcohols, and glycol ethers (such as 2-butoxyethanol or ethylene glycol phenyl ether).
- Mechanism: Their main mode of action is dissolving grease and oil at a molecular level.
- Applications: Due to their high strength, they are typically reserved for demanding tasks in industrial, automotive, and manufacturing settings. Common uses include cleaning engines, automotive parts, tools, heavy machinery, factory floors, and removing thick grease, tar, adhesive residues, and heavy oils.
- Pros: They offer powerful and often rapid cleaning action, effectively breaking down heavy, viscous, or baked-on grease and oil deposits. Some formulations are designed to evaporate quickly (fast-drying), which minimizes downtime for equipment or processes.
- Cons: Solvent-based degreasers present significant safety and environmental challenges. Many are flammable or combustible, requiring strict precautions against ignition sources. They often release Volatile Organic Compounds (VOCs), contributing to air pollution and posing inhalation risks. Direct contact can cause skin irritation, dryness, or chemical burns, and inhalation of vapors can lead to respiratory issues, drowsiness, neurological effects, and potentially long-term health problems including certain cancers. They can damage sensitive materials like certain plastics, rubbers, and painted surfaces. Use requires adequate ventilation, appropriate Personal Protective Equipment (PPE), and careful handling and disposal procedures.
Water-Based (Often Alkaline) Degreasers
- Description: These degreasers use water as the primary solvent carrier, incorporating a blend of other ingredients to achieve cleaning action. Key components typically include surfactants (for emulsification and wetting), builders (often alkaline substances like NaOH, KOH, or silicates to boost cleaning power and potentially saponify fats), and sometimes chelating agents or corrosion inhibitors. While some are neutral, many are alkaline (pH > 7), with heavy-duty versions being highly alkaline (pH 12-14).
- Mechanism: They primarily work through emulsification (suspending grease in water via surfactants) and, if sufficiently alkaline, saponification (chemically converting fats/oils into soap).
- Applications: Their versatility makes them suitable for a broad range of applications. This includes household cleaning (especially kitchens), commercial kitchens, food processing facilities (when certified as food-grade), general institutional and light-to-moderate industrial cleaning, floor maintenance, and cleaning equipment where harsh solvents are undesirable or prohibited.
- Pros: Compared to solvent-based options, water-based degreasers are generally safer for the user and the environment. They are typically non-flammable, have lower VOC content, and many formulations are biodegradable (though verification is needed). They are often gentler on a wider variety of surfaces, including many metals and plastics.
- Cons: They may not possess the same aggressive cleaning power as potent solvents, especially on extremely heavy, aged, or carbonized grease deposits. Performance can sometimes be enhanced by increasing contact time, using agitation, or applying heat. Highly alkaline formulations, while effective, can still be corrosive or irritating to skin and eyes and may attack sensitive metals like aluminum if not properly formulated or rinsed.
Biodegradable / Natural Degreasers
- Description: This category emphasizes environmental responsibility and user safety, utilizing ingredients derived from renewable resources. Common active ingredients include plant-based solvents, most notably d-Limonene, which is extracted from citrus fruit peels. Some formulations may also incorporate microbial agents (bacteria or enzymes) that biologically consume or break down grease. These are often combined with biodegradable surfactants derived from plant sources.
- Mechanism: Citrus-based solvents like d-Limonene act similarly to conventional solvents by dissolving grease. Enzyme-based products use specific enzymes as catalysts to break down targeted organic soils like fats and proteins. Microbial cleaners work over time as microorganisms consume the grease as a food source.
- Applications: Suitable for general-purpose cleaning in homes and businesses, light industrial tasks, removing adhesives and gum, cleaning food spills, and situations where low toxicity, biodegradability, and minimal environmental impact are paramount. d-Limonene is also found in personal care products and natural pesticides.
- Pros: Their primary advantage is their favorable environmental and safety profile. They are typically biodegradable, non-toxic or low-toxicity, non-corrosive, derived from renewable resources, and safer for user handling compared to harsh solvents or caustics. Citrus-based cleaners often have a pleasant natural fragrance. d-Limonene specifically has shown good efficacy against various greases and is non-reactive with metal surfaces.
- Cons: While effective for many tasks, they may lack the sheer power of aggressive solvent-based or highly alkaline degreasers for tackling the most severe industrial grease challenges. Performance can vary significantly based on the specific formulation and concentration of active ingredients. The cost of some natural or enzyme-based products might be higher than traditional chemical cleaners.
Comparison Table: Degreaser Types
Feature | Solvent-Based Degreasers | Water-Based (Often Alkaline) Degreasers | Biodegradable / Natural Degreasers |
---|---|---|---|
Key Ingredient Examples | Hydrocarbons (Mineral Spirits, Kerosene), Chlorinated Solvents (TCE, PCE), Glycol Ethers (2-Butoxyethanol), Acetone | Water, Surfactants (Ethoxylated Alcohols), Alkaline Builders (NaOH, KOH, Silicates), Chelating Agents | d-Limonene (Citrus Terpene), Plant-Based Surfactants, Enzymes, Microbes |
Primary Mechanism(s) | Dissolving (Solvent Action) | Emulsification, Saponification (if alkaline), Wetting | Dissolving (d-Limonene), Catalytic Breakdown (Enzymes), Biodegradation (Microbes) |
Typical Applications | Heavy Industrial, Automotive (Engines, Parts), Machinery, Tools, Tar/Adhesive Removal | Kitchens, Food Processing (if certified), General Household, Light/Medium Industrial, Floors, Versatile Use | Household Cleaning, Light Industrial, Sensitive Environments, Adhesive Removal, Eco-Conscious Cleaning |
Effectiveness Profile | Very High on Heavy Grease/Oil; Fast-Acting | Good to High, Versatile; May Need More Time/Effort on Heaviest Grease | Good on Light to Moderate Grease; Effectiveness Varies by Formulation |
Key Safety Concerns | Flammability, High VOCs, Inhalation Hazard, Skin/Eye Irritation/Burns, Potential Long-Term Health Effects, Damage to Plastics/Rubber | Can be Irritating/Corrosive (if highly alkaline), Eye/Skin Contact Hazard; Generally Lower Risk than Solvents | Generally Low Toxicity, Low Irritation Potential; Check Specific Product Labels |
Environmental Profile | Often Poor: VOCs, Hazardous Waste Potential, Non-Biodegradable Components | Generally Better: Lower VOCs, Often Biodegradable (check label), Less Hazardous Waste | Generally Good: Biodegradable, Renewable Resources, Lower Environmental Impact |
This table provides a comparative overview, assisting users in aligning degreaser characteristics with their specific requirements, balancing cleaning power against safety and environmental priorities.
The choice often involves trade-offs: maximum strength might necessitate stricter safety measures (solvent-based), while enhanced safety might mean slightly less aggressive action (water-based or natural).
4: Degreasers for Specific Jobs – Matching Product to Task
The effectiveness of a degreaser is maximized when its formulation is matched to the specific type of grease and the environment in which it’s being used.
Kitchen Degreasers
- Target Surfaces: Commonly used on cooktops, inside ovens, range hoods, filters, backsplashes, grills, pots and pans, countertops, sinks, and kitchen floors.
- Grease Type: Primarily designed to tackle food-based soils such as cooking oils (vegetable, olive), animal fats, greasy films from cooking vapors, and baked-on food residues.
- Formulation: Kitchen degreasers are predominantly water-based, often alkaline to help break down fats via saponification and emulsification. They typically contain effective surfactants to lift and suspend grease. Many are available as convenient trigger sprays or foaming formulas, which help the product cling to vertical surfaces like backsplashes or oven walls, increasing contact time. Some formulations also incorporate disinfectants to kill common kitchen bacteria like Salmonella and E. coli, providing cleaning and sanitizing action in one step. An example is Formula 409® Cleaner Degreaser Disinfectant, designed for grease and grime on various kitchen surfaces.
- Considerations: Safety is paramount in kitchen environments, especially near food preparation zones. Products should be explicitly labeled for kitchen use. While effective, overly harsh solvents are generally avoided. Thorough rinsing of surfaces, particularly those that may come into contact with food, is essential to remove any chemical residue. For surfaces directly contacting food, a certified food-grade degreaser (see section 4.4) is required.
Engine & Automotive Degreasers
- Target Surfaces: Formulated for cleaning vehicle engines, engine components, tools, garage floors, and other automotive parts prone to heavy grease accumulation.
- Grease Type: These products must contend with tough, petroleum-based soils including motor oil, transmission fluid, lubricants, hydraulic fluids, road grime, tar, and brake dust.
- Formulation: Due to the heavy and stubborn nature of automotive grease, solvent-based degreasers are frequently used in this category. They are often supplied as aerosol sprays for easy application or as concentrated liquids. Foaming formulations are also available, designed to cling to engine surfaces and penetrate hard-to-reach areas. Water-based alternatives are becoming more common, offering a safer profile; these may be used in conjunction with high-pressure washing or specialized cleaning equipment like ultrasonic tanks for enhanced effectiveness. Products like DST-DEGREEZ are examples of water-based options for engine cleaning.
- Considerations: High cleaning power is a primary requirement. Flammability is a significant hazard when working around potentially hot engine components or ignition sources; non-flammable options should be preferred where possible. Compatibility with materials is crucial, as strong solvents can potentially damage rubber hoses, plastic components, or painted surfaces – checking manufacturer recommendations or performing a spot test is advised. Environmental responsibility dictates proper collection and disposal of the runoff, which will contain oil and other contaminants.
Industrial Degreasers
- Target Surfaces: Used for heavy-duty cleaning tasks across a wide array of industries including manufacturing, aerospace, transportation, logistics, construction, and maintenance services. Applications include cleaning industrial machinery, manufacturing equipment, parts washing (immersion or spray), factory floors, tools, and preparing metal surfaces prior to painting or coating.
- Grease Type: Industrial environments present diverse and challenging soils, including heavy lubricating oils, greases, cutting fluids, hydraulic fluids, metal shavings, inks, waxes, protective coatings (like cosmoline), and general industrial grime.
- Formulation: Industrial degreasers are typically high-strength formulations, available as either potent solvent-based products or concentrated, heavy-duty alkaline water-based cleaners. They are often supplied in bulk containers (drums, totes) and designed for use with various application methods, including manual spraying, automated spray washers, immersion tanks, ultrasonic cleaners, pressure washers, and automatic floor scrubbers. Examples include the Zep Formula 50 concentrate and the J-Clean line of industrial cleaners.
- Considerations: Robust cleaning performance and efficiency are critical. Compatibility with the specific metals, plastics, and elastomers used in industrial equipment must be verified to prevent damage. Worker safety is a major concern due to the strength of the chemicals often involved; adherence to strict safety protocols, including proper use of PPE and adequate ventilation, is essential. Compliance with workplace safety regulations (e.g., OSHA in the US) and environmental regulations regarding chemical usage and wastewater disposal must be maintained. Choosing formulations that balance effectiveness with worker safety and environmental sustainability is increasingly important.
Food-Grade Degreasers
- Target Surfaces: Specifically designed for cleaning surfaces in environments where food is processed, prepared, or packaged. This includes commercial kitchens, bakeries, meat and poultry plants, breweries, dairies, and other food manufacturing facilities. They are used on equipment, countertops, conveyors, floors, and walls where incidental contact with food products might occur.
- Grease Type: Primarily targets food-derived fats, oils, greases, proteins, sugars, and other organic residues generated during food processing.
- Formulation: Food-grade degreasers are typically water-based and formulated using ingredients that are deemed safe for potential incidental contact with food. They often utilize specific surfactants and builders approved by regulatory bodies. Crucially, reputable food-grade cleaners will carry certifications from organizations like NSF International. These certifications fall into specific categories that dictate permissible use:
- NSF A1: Compounds for use as general cleaners on all surfaces in and around food processing areas.
- NSF A8: Compounds for use as degreasers or carbon removers for food cooking or smoking equipment, utensils, or other associated surfaces.
- NSF C1: Compounds for use on surfaces in processing areas where there is no possibility of food contact. Products often explicitly state they do not contain certain prohibited substances like petroleum distillates, chlorinated hydrocarbons, or strong caustics like NaOH. Many are formulated to be biodegradable, non-toxic, and non-corrosive. Examples include elba NSF Certified Industrial Degreaser (NSF A8, C1 listed) and WISE All-Purpose Cleaner/Degreaser (NSF A1 listed).
- Considerations: The most critical factor is ensuring the product holds the correct certification (e.g., NSF registration) for the intended application within the food facility. Using a product with an inappropriate certification category could lead to food contamination and regulatory violations. It is essential to understand that “food-grade” is not a generic term but refers to specific standards and approved uses. For instance, an A8 degreaser might be suitable for cleaning an oven rack between batches, while an A1 cleaner might be used for general wall cleaning. Even with certified products, thorough rinsing with potable water is typically required after use on food-contact surfaces to remove any residues. Choosing non-toxic, non-corrosive, and readily biodegradable options helps maintain a safe working environment and meet sustainability goals.
5: Safety First – Handling Degreasers Responsibly
Given the chemical nature of degreasers, particularly solvent-based and highly alkaline types, prioritizing safety during handling and use is non-negotiable. Failure to follow proper procedures can lead to injury, health problems, or environmental damage.
Read the Label and Safety Data Sheet (SDS)
This is the absolute first and most crucial step before using any degreaser.
- Product Label: Provides essential information including directions for use, dilution ratios (if applicable), surfaces the product is suitable for, basic hazard warnings (e.g., flammable, corrosive), precautionary statements, and brief first aid instructions.
- Safety Data Sheet (SDS): Formerly known as the Material Safety Data Sheet (MSDS), the SDS provides comprehensive technical details about the chemical product. It includes sections on hazard identification, composition/ingredients, first-aid measures, fire-fighting measures, accidental release measures, handling and storage, exposure controls/personal protection, physical and chemical properties, stability and reactivity, and toxicological information. Employers using hazardous chemicals are required by regulatory bodies like OSHA to have SDSs readily accessible to employees. Even for household use, obtaining and reviewing the SDS (often available on the manufacturer’s website) provides invaluable safety knowledge.
Personal Protective Equipment (PPE)
Using appropriate PPE creates a barrier between the user and potentially harmful chemicals. The specific PPE required depends on the product’s hazards, as detailed on the label and SDS.
- Gloves: Chemical-resistant gloves are essential when handling most degreasers, especially strong solvents or alkaline solutions, to prevent skin contact, irritation, or burns. The type of glove material matters; general-purpose latex or vinyl gloves may not offer sufficient protection against aggressive solvents. Nitrile or neoprene gloves are common choices, but for highly penetrating solvents like Methylene Chloride, a double-gloving system (e.g., inner laminate like PE/EVOH, outer nitrile/neoprene) might be recommended. Always inspect gloves for holes or degradation before use and replace them frequently or as recommended by the manufacturer.
- Eye Protection: Chemical splash goggles that fit snugly against the face offer the best protection against splashes and airborne droplets entering the eyes. A face shield worn over goggles provides additional protection for the entire face, especially when pouring liquids or using spray applications. Regular eyeglasses do not provide adequate protection.
- Respiratory Protection: Necessary when working with volatile solvents or when applying degreasers as aerosols or mists, particularly in enclosed or poorly ventilated spaces. The type of respirator depends on the specific chemical and its concentration in the air. This could range from an air-purifying respirator with appropriate cartridges (for specific vapors/mists) to a supplied-air respirator in highly hazardous situations. It’s critical to note that the odor threshold for some solvents is much higher than the permissible exposure limit, meaning hazardous concentrations can be present without a noticeable smell. Proper fit testing and training are required for effective respirator use.
- Protective Clothing: For tasks involving significant splashing potential or handling highly corrosive/absorbent chemicals, additional protection like chemical-resistant aprons, coveralls, or boots may be necessary to prevent skin contact and contamination of personal clothing.
- Hazard Levels: In industrial or emergency response scenarios, standardized PPE levels (Level A, B, C, D) dictate specific ensembles based on the degree of hazard, ranging from fully encapsulated suits with supplied air (Level A) to standard work uniforms with basic eye and hand protection (Level D). Most routine degreasing tasks fall under requirements closer to Level C or D, but the SDS should always guide selection.
Ventilation is Key
Adequate ventilation is critical to prevent the buildup of potentially harmful vapors or mists, especially when using solvent-based degreasers.
- Work outdoors or in areas with good natural airflow (e.g., an open garage) whenever possible.
- If working indoors, ensure robust mechanical ventilation, such as a strong exhaust fan system that vents directly outside. Simply opening a window may not be sufficient for chemicals with high vapor pressure or toxicity.
- Avoid working in confined spaces (like tanks or pits) unless strict confined space entry procedures are followed, including atmospheric testing and potentially supplied-air respiration.
- Position work so that any airflow draws vapors away from the breathing zone, not towards it. Do not lean directly over open containers or tanks. Turn on ventilation systems well before starting work.
5. Safe Storage, Handling, and Disposal
- Storage: Keep degreaser containers tightly sealed when not in use to prevent spills and evaporation. Store them in a cool, dry, well-ventilated area designated for chemicals. Keep them away from heat sources, flames, sparks, and direct sunlight, especially flammable solvents. Store away from incompatible materials – for example, keep alkaline degreasers separate from acids, and oxidizing agents separate from flammable materials. Follow specific storage guidance from the SDS.
- Handling: Avoid breathing vapors, mists, or spray. Prevent contact with skin and eyes. Use appropriate tools (funnels, pumps) when transferring liquids to minimize spills. Wash hands thoroughly with soap and water after handling, even if gloves were worn. Do not eat, drink, or smoke in areas where degreasers are being used or stored. Ensure empty containers are handled with the same precautions as full ones, as residues may remain.
- Disposal: Never dispose of degreasers, especially solvent-based or highly alkaline/acidic types, by pouring them down drains, into storm sewers, or onto the ground. This can contaminate water supplies and harm the environment. Follow the disposal instructions on the product label and SDS. Contact local environmental health or hazardous waste authorities for guidance on proper disposal procedures in your area. Small amounts of some readily biodegradable, water-based household degreasers might be acceptable for drain disposal if explicitly permitted by the label and local regulations, but hazardous industrial chemicals require specialized waste management. Responsible disposal is crucial.
Critical First Aid Measures
Immediate and appropriate first aid can significantly reduce the severity of injury from chemical exposure. Always follow the specific first aid instructions provided on the product label and SDS. General guidelines include :
- Eyes: If contact occurs, immediately flush the eyes with large amounts of clean, lukewarm water for at least 15-20 minutes. Hold the eyelids open to ensure thorough rinsing under the lids. Remove contact lenses if present and easy to do, continuing to rinse. Seek immediate medical attention.
- Skin: Remove any contaminated clothing immediately. Wash the affected skin area thoroughly with plenty of soap and water for at least 15 minutes. If irritation, redness, pain, or burns develop or persist, seek medical attention. Never use solvents to try and clean chemicals off the skin, as this can increase absorption.
- Inhalation: If vapors or mists are inhaled, move the affected person to an area with fresh air immediately. If breathing is difficult, administer oxygen if trained to do so. If breathing has stopped, begin artificial respiration if trained. Seek prompt medical attention, especially if symptoms like dizziness, headache, nausea, or respiratory irritation occur.
- Ingestion: If swallowed, rinse the mouth thoroughly with water. DO NOT induce vomiting unless specifically instructed to do so by a poison control center or medical professional, as this can cause further damage, especially with corrosive substances. Drink a glassful (cupful) of water or milk, as recommended by the SDS. Seek immediate medical attention or call a poison control center (e.g., 1-800-222-1222 in the US). Have the product container or label available when calling.
DANGER: Never Mix Degreasers with Other Chemicals
This warning cannot be overstressed. Mixing cleaning chemicals, including degreasers, with other products can lead to dangerous, even fatal, chemical reactions.
- Alkaline Degreasers + Acids: Combining strong alkaline products (like many degreasers) with acidic cleaners (like toilet bowl cleaners or rust removers) causes a violent neutralization reaction. This can generate significant heat, causing the mixture to boil, spatter, and release potentially hazardous fumes or corrosive mist.
- Degreasers + Bleach (Sodium Hypochlorite): Mixing bleach with acidic cleaners releases toxic chlorine gas. Mixing bleach with ammonia-containing cleaners (like some glass cleaners or all-purpose cleaners) releases toxic chloramine gases. Many degreasers, particularly alkaline ones, should also NEVER be mixed with bleach or other chlorinated compounds, as hazardous gases can be released.
- General Rule: Unless the product label specifically instructs otherwise, mix degreasers only with water for dilution, following the recommended ratios precisely. DO NOT mix different degreasers together, and DO NOT mix degreasers with any other cleaning product or chemical.
The inherent chemical reactivity that enables degreasers to break down stubborn grease also makes them hazardous when combined improperly. These chemicals are designed for specific reactions with soils, not with other potent cleaning agents.
Mixing creates uncontrolled chemical reactions with potentially severe consequences, underscoring the need to treat all cleaning products with caution and strictly adhere to label instructions.
6: Surface Compatibility – Avoiding Damage
While the primary goal is grease removal, it’s equally important that the degreaser does not harm the surface being cleaned. Choosing an incompatible product can lead to irreversible damage such as etching, discoloration, softening, cracking, or removal of protective coatings.
Why Compatibility Matters
Degreasers work through chemical action – dissolving, reacting, emulsifying. If the chemical formulation is too aggressive for the substrate material, the degreaser can attack the surface itself, not just the grease sitting on top of it.
This interaction depends on both the degreaser’s chemistry (e.g., solvent type, pH level) and the surface’s chemical resistance. A product that works wonders on a steel engine block might destroy a plastic dashboard or strip paint from a delicate appliance. Therefore, ensuring compatibility is essential for achieving a clean and undamaged result.
General Guidelines by Material
- Metals: Most common metals like steel and iron are resistant to many degreasers. However, reactive metals like aluminum, magnesium, zinc (galvanized surfaces), and copper alloys (brass, bronze) can be susceptible to attack by highly alkaline (high pH) or highly acidic (low pH) solutions, leading to corrosion, etching, or discoloration. Neutral or mildly alkaline water-based degreasers are generally safer for sensitive metals. Some formulations contain corrosion inhibitors to protect metal surfaces. Natural solvents like d-Limonene are noted for being non-reactive with metals. Always check the product label for specific metal compatibility.
- Plastics & Rubber: This is a major area of concern, particularly with solvent-based degreasers. Many solvents can cause plastics and rubbers to swell, soften, become brittle, crack, or even dissolve completely. The effect varies greatly depending on the specific type of plastic or rubber and the specific solvent. Water-based degreasers are typically much safer for most plastics and rubbers, but compatibility should still be verified, especially with sensitive types or concentrated alkaline solutions. Specialized plastic degreasers are available for applications like preparing plastic parts for painting.
- Painted Surfaces: Harsh solvents are very likely to strip, lift, dull, or discolor paint finishes. Even strong alkaline solutions can sometimes affect certain paints. For cleaning painted surfaces, it’s best to use milder, pH-neutral or slightly alkaline water-based degreasers specifically labeled as safe for paint, or highly diluted solutions of stronger products. Degreasers designed specifically for automotive paint or pre-paint preparation exist and are formulated for compatibility.
- Other Surfaces: Compatibility should also be considered for materials like glass (generally resistant, but check for coatings), concrete (can be etched by strong acids), wood (can be damaged by water or strong chemicals), fabrics/upholstery (require specialized cleaners), and sealed surfaces (sealants can be damaged). Some versatile water-based or natural degreasers claim broad surface compatibility , but caution is always advised.
The Golden Rule: Always Spot Test!
Given the variability in both degreaser formulations and surface materials, the single most reliable way to ensure compatibility is to perform a spot test before full application.
- Choose a small, hidden, or inconspicuous area of the surface to be cleaned.
- Apply a small amount of the degreaser (at the intended dilution, if applicable) to that area.
- Allow it to sit for the recommended dwell time, then wipe or rinse as directed.
- Let the area dry completely and inspect carefully for any signs of damage: discoloration, etching, softening, swelling, dulling, or removal of finish.
- If any adverse effects are observed, do not use the product on that surface. If the test area looks unchanged, it is likely safe to proceed with cleaning the entire surface, though continued vigilance is recommended.
This simple step takes only a few extra minutes but can prevent costly and potentially irreparable damage. Manufacturer claims provide guidance, but real-world conditions and material variations mean that spot testing offers the definitive confirmation of compatibility for a specific situation. A degreaser is only truly effective if it cleans without causing harm.
7: When to Call the Professionals
While many degreasing tasks around the home or workshop can be handled safely and effectively with careful product selection and adherence to safety precautions, there are situations where hiring a professional cleaning service is the wiser, safer, and often more efficient choice.
Recognizing Complex or Hazardous Situations
Consider calling professionals when faced with:
- Extremely Heavy or Widespread Contamination: Large areas covered in thick, stubborn industrial grease (e.g., entire factory floors, large machinery) may require specialized equipment and techniques beyond typical DIY capabilities.
- Hazardous Materials: If the grease is mixed with known hazardous substances, or if the required cleaning agent itself is highly toxic, flammable, or reactive, professionals trained in hazardous material handling are better equipped.
- Confined Spaces: Cleaning inside tanks, pits, or other poorly ventilated confined spaces poses significant risks from vapor accumulation and oxygen displacement. OSHA regulations require specific training, procedures, and equipment for confined space entry, which professionals possess.
- Lack of Proper PPE or Ventilation: If the required safety equipment (e.g., specific respirators, chemical suits) or adequate ventilation is unavailable, attempting the job poses unacceptable health risks.
- Uncertainty or Lack of Experience: If unsure about the correct procedures, chemical compatibility, safety protocols, or proper waste disposal methods, it’s safer to defer to experts.
- Regulatory Compliance: Commercial or industrial facilities often face strict regulations regarding workplace safety (OSHA) and environmental protection (EPA) concerning chemical use and waste disposal. Professionals are knowledgeable about these requirements and help ensure compliance.
- Large-Scale or Time-Sensitive Needs: When large areas need to be cleaned quickly to minimize downtime, professionals with efficient equipment and trained crews can accomplish the task much faster than individuals.
Advantages of Professional Cleaning Services
Hiring a reputable commercial or industrial cleaning service offers several benefits, particularly for challenging degreasing jobs:
- Expertise and Training: Professionals possess in-depth knowledge of different types of grease, the most effective cleaning agents for each, and the correct application techniques. They are trained in safety procedures, chemical handling, and identifying potential hazards.
- Specialized Equipment: They have access to industrial-grade equipment such as high-pressure hot water washers, steam cleaners, large floor scrubbers, specialized containment systems, and advanced cleaning tools that provide superior cleaning power and efficiency compared to consumer-level gear.
- Safety and Compliance: Professionals are equipped with the appropriate PPE and are trained in its correct use. They understand and adhere to safety regulations (like OSHA standards) and environmental laws concerning chemical handling and hazardous waste disposal, reducing liability for the client. They often carry proper insurance coverage.
- Efficiency and Time Savings: With experienced crews and powerful equipment, professional services can complete demanding cleaning tasks significantly faster and more thoroughly, freeing up the client’s time and resources to focus on their core activities or business operations.
- Improved Results: Their combination of expertise, appropriate chemicals, and specialized equipment often leads to a higher standard of cleanliness and more effective removal of deeply ingrained or widespread grease than might be achievable through DIY efforts. This can enhance facility appearance, hygiene, and equipment longevity.
- Peace of Mind: Engaging professionals provides assurance that the job will be done correctly, safely, and in compliance with relevant regulations, mitigating risks associated with improper chemical handling or disposal.
While DIY degreasing is suitable for many common situations, the decision to hire professionals involves weighing the cost against the potential risks, the complexity of the task, the need for specialized knowledge or equipment, and the value of ensuring safety and regulatory compliance.
For demanding, large-scale, or hazardous degreasing challenges, professional services offer a valuable solution that prioritizes safety, efficiency, and optimal results.
8: Conclusion – Degreasing with Confidence
Summary of Key Takeaways
Successfully tackling grease requires more than just elbow grease; it demands the right approach and the right product. This guide has highlighted the essential aspects of understanding and using degreasers effectively and safely:
- Know Your Degreaser: Recognize the fundamental differences between solvent-based, water-based/alkaline, and biodegradable/natural degreasers, understanding their respective strengths, weaknesses, mechanisms, and typical applications.
- Match Product to Task: Select a degreaser specifically formulated for the type of grease (kitchen, automotive, industrial) and the surface material you are cleaning. Pay close attention to specialized requirements, such as NSF certifications for food-grade applications.
- Prioritize Safety Above All: Always read the product label and Safety Data Sheet (SDS) before use. Consistently use the recommended Personal Protective Equipment (PPE), ensure adequate ventilation, and store and handle chemicals responsibly.
- Never Mix Chemicals: Heed the critical warning against mixing degreasers with bleach, acids, ammonia, or any other cleaning products unless explicitly instructed, due to the risk of hazardous reactions.
- Test for Compatibility: Protect surfaces from damage by always performing a spot test in an inconspicuous area before applying any degreaser broadly.
Final Encouragement
Armed with this knowledge, users can approach degreasing tasks with greater confidence, choosing the right tools for the job and employing them in a way that maximizes effectiveness while minimizing risks to themselves, others, and the surfaces being cleaned.
Remember that while many tasks are manageable, complex or hazardous situations warrant calling upon the expertise and resources of professional cleaning services. By understanding the science, respecting the chemistry, and prioritizing safety, even the toughest grease challenges can be overcome.