1: Decommissioning and Demolition Cleaning
The lifecycle of industrial facilities inevitably includes an end-of-life phase, necessitating either decommissioning for dormancy, repurposing, or complete demolition. Central to these complex processes is a specialized set of activities collectively known as decommissioning and demolition cleaning. This guide provides an in-depth examination of these cleaning operations, detailing their scope, objectives, critical sub-tasks, and the overarching importance of professional execution.
1.1. Defining Decommissioning and Demolition in the Industrial Context
Understanding the distinction and interplay between decommissioning and demolition is fundamental to appreciating the role of cleaning within these operations.
Contact us!
Decommissioning:
In the industrial sphere, decommissioning refers to the formal, systematic process of taking an operational facility or structure out of service. This is not merely shutting down power but involves a comprehensive series of actions including the deactivation of all equipment and systems, the meticulous removal of hazardous materials and residual products, and ensuring full compliance with all pertinent environmental and safety regulations.
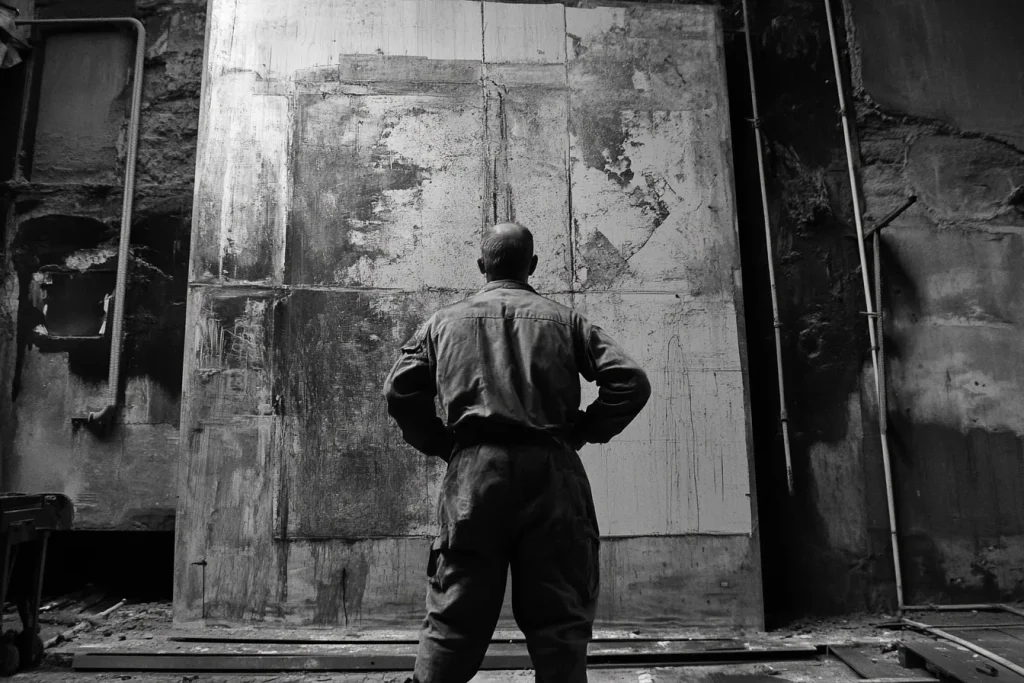
The primary objective of decommissioning is to achieve a safe and orderly shutdown of the facility, effectively mitigating any potential environmental risks and safeguarding public safety. For specialized facilities, such as nuclear plants, decommissioning encompasses an even more rigorous scope, including the complete clean-up of all radioactive contamination and the progressive, carefully planned dismantling of the plant infrastructure. Ultimately, decommissioning prepares a property for various future scenarios, whether it be long-term safe dormancy, repurposing for a new industrial or commercial use, or complete demolition and site redevelopment.
Demolition:
Demolition, in contrast, is the physical act of dismantling, razing, destroying, or wrecking a building, structure, or any part thereof. This process typically involves the use of heavy machinery—such as excavators, cranes, and wrecking balls—and a variety of techniques, including controlled implosions for larger structures. The main goal of demolition is to clear the site, often to make way for new construction, redevelopment, or to remove unsafe or obsolete structures. While speed and cost-effectiveness can be significant drivers in demolition projects, safety and environmental management, particularly concerning dust and debris, remain critical considerations.
Interrelation:
Decommissioning and demolition are often sequential, particularly in complex industrial environments like chemical plants, refineries, or manufacturing facilities. Decommissioning logically precedes demolition because it addresses the inherent hazards associated with operational residues and integrated systems. Specialized cleaning and decontamination activities are frequently the initial phase of the decommissioning process; only once areas are certified as clean and safe can the subsequent strip-out, removal of equipment, and eventual structural demolition commence.
This phased approach ensures that hazardous materials are managed in a controlled manner before large-scale, potentially disruptive demolition activities begin. The thoroughness of this initial decommissioning cleaning phase has a profound and direct impact on the safety, environmental risk profile, and overall cost-effectiveness of the demolition that follows, as well as any subsequent site redevelopment. If cleaning is inadequate, unforeseen hazards can emerge during demolition, contaminants may be spread, and the complexity and cost of site remediation can escalate significantly. This cascading effect underscores the importance of meticulous planning and execution from the very outset of the decommissioning process.
1.2. The Critical Role, Scope, and Objectives of Specialized Cleaning in These Processes
Specialized cleaning is not an ancillary task but a cornerstone of successful decommissioning and demolition projects.
Definition of Decommissioning & Demolition Cleaning:
This encompasses a wide range of cleaning and decontamination activities performed on industrial facilities, structures, internal and external surfaces, and equipment. These activities occur prior to or concurrently with facility closure, dismantling, or demolition. It is an essential preparatory and ongoing element designed to manage risks and facilitate subsequent project phases.
Critical Role:
Industrial cleaning is universally recognized as a fundamental and indispensable part of the facility decommissioning process. Its primary function is to render the facility safe for any future use, whether that be demolition, redevelopment, or repurposing. This is achieved through the systematic removal of hazardous materials, accumulated pollutants, process residues, and other contaminants.
The importance of such cleaning extends across several critical domains: it is vital for the protection of the environment by preventing the release of harmful substances; it safeguards public health by eliminating exposure pathways; it ensures legal compliance with a myriad of regulations; and it is a key enabler for the safe and productive reuse of industrial land. Beyond these operational and regulatory imperatives, the diligence with which decommissioning and demolition cleaning is conducted serves as a critical component of corporate social responsibility and environmental stewardship.
A company’s commitment to thorough cleaning and decontamination significantly influences its public reputation and its standing with regulatory agencies and the local community. Failure to perform these tasks responsibly can lead to environmental damage, health crises, and severe penalties, all of which can irreparably harm public trust. Conversely, a well-executed, transparent decommissioning project showcases a commitment to sustainability and responsible corporate citizenship.
Scope: The scope of decommissioning and demolition cleaning is comprehensive and multifaceted. It typically includes:
- Initial Site Assessment and Planning: Detailed evaluations to identify all potential hazards, define the extent of contamination, and determine the most appropriate decontamination strategies and cleaning needs.
- Removal of Hazardous Materials and Residual Products: This involves the careful extraction of substances such as asbestos, industrial chemicals, lead-based paint, PCBs, mercury, and any remaining process materials.
- Cleaning and Decontamination: Thorough cleaning of all affected structures, machinery, equipment, storage tanks, sumps, and piping systems to remove contaminants and residues.
- Waste Management: The systematic management, segregation, packaging, transportation, and disposal of all generated wastes, both hazardous and non-hazardous, in strict accordance with regulatory standards.
- Dust Control: Implementation of measures to control and suppress dust generated during demolition activities, protecting air quality and worker health.
- Site Remediation Support: Cleaning activities often prepare the site for, or integrate with, broader site remediation efforts aimed at addressing soil and groundwater contamination.
Objectives: The primary objectives of specialized cleaning in decommissioning and demolition are:
- Safety: To protect the health and safety of all workers involved in the decommissioning and demolition processes, as well as to ensure the safety of the public and surrounding communities.
- Environmental Protection: To prevent the contamination of soil, groundwater, surface water, and air by ensuring the controlled removal and management of pollutants and hazardous substances.
- Regulatory Compliance: To achieve and maintain full adherence to all applicable local, state, and federal environmental, health, and safety laws and regulations, thereby avoiding penalties and legal liabilities.
- Asset Recovery and Salvage: To clean and prepare surfaces, machinery, and equipment for potential salvage, recycling, or sale as scrap, thereby maximizing the recovery of value from decommissioned assets.
- Site Reusability: To render the site safe and environmentally sound, making it suitable for future redevelopment, repurposing, or return to a natural state.
2: Core Sub-Task: Removal and Disposal of Residual Products and Hazardous Materials
The effective management of residual products and hazardous materials is arguably the most critical sub-task within decommissioning and demolition cleaning. It directly addresses the primary sources of risk to human health and the environment.
2.1. Identification of Common Residual Products and Hazardous Materials in Industrial Settings
Industrial facilities, by their nature, utilize and generate a wide array of substances. Upon decommissioning, these can remain as residual products or constitute hazardous materials requiring careful management.
Residual Products: These are substances left over from previous industrial processes, storage, or maintenance activities. Common examples include:
- Chemicals and Solvents: A broad category encompassing substances like acetone, toluene, methyl ethyl ketone (MEK), N-methyl-2-pyrrolidone (NMP), propylene glycol methyl ether acetate (PM Acetate), and various press wash solvents used in printing or manufacturing.
- Oils: Various types of oils are frequently encountered, including used motor oils, industrial lubricants, cutting oils, hydraulic fluids, and, in older facilities, oils contaminated with PCBs.
- Sludges: These are semi-solid residues that accumulate in tanks, sumps, and wastewater treatment units. Examples include petroleum sludge, often referred to as tank bottom sludge (TBS), which is a complex emulsion of hydrocarbons, water, sediments, and often contains heavy metals like lead, copper, nickel, vanadium, zinc, and chromium, as well as inorganic minerals. Process-specific sludges from chemical manufacturing or metal finishing are also common.
- Other Process Materials: This can include leftover adhesives, paints, coatings, and plating wastes from finishing operations. Residual wastewater and various industrial process waters may also be present in piping and vessels.
Hazardous Materials: These are substances specifically identified as posing a significant risk to human health or the environment if improperly managed. During industrial decommissioning, several key hazardous materials are frequently encountered:
- Asbestos: Widely used in the past for its insulation and fire-resistant properties, asbestos can be found in pipe insulation, boiler lagging, roofing materials, floor tiles, gaskets, and various older building components. Its removal is stringently regulated due to the risk of releasing airborne fibers, which can cause serious lung diseases.
- Lead: Commonly found in lead-based paints applied to structures and equipment in older facilities (pre-1978), as well as in lead piping, solder, and some industrial components. Lead exposure can cause severe neurological and developmental problems.
- Polychlorinated Biphenyls (PCBs): Primarily found in older electrical equipment such as transformers, capacitors, and fluorescent light ballasts. PCBs were also used in some caulking compounds, paints, and hydraulic fluids. They are persistent environmental pollutants and suspected carcinogens, with their cleanup and disposal heavily regulated by the EPA.
- Mercury: Can be present in various devices such as thermostats, pressure gauges, switches, fluorescent lamps, and some older industrial process equipment. Mercury is a potent neurotoxin.
- Radioactive Materials: In specific industries like nuclear power generation, research laboratories, or certain manufacturing processes using radioactive sources, these materials require highly specialized handling and disposal protocols.
- Chemical Residues: Various hazardous chemical residues from past manufacturing processes may remain in tanks, pipes, and equipment, requiring careful identification and neutralization or removal.
- Universal Wastes: This category includes items like batteries, recalled pesticides, and mercury-containing lamps, which have specific, somewhat relaxed, management requirements under RCRA to encourage proper recycling or disposal.
The accuracy of the initial identification and characterization of these residual products and hazardous materials is paramount. It directly dictates the selection of appropriate safety protocols, handling procedures, disposal pathways, and ultimately, the overall cost and success of the decommissioning project.
Misclassification can lead to severe safety incidents if hazards are underestimated, environmental releases if materials are improperly handled, regulatory violations with attendant fines and legal actions, and unexpected financial burdens if, for example, a waste stream is later found to be more hazardous (and thus more expensive to dispose of) than initially assessed. Conversely, over-classifying a non-hazardous waste as hazardous can lead to unnecessarily high disposal costs. This critical first step of meticulous identification forms the foundation for a safe and compliant project.
2.2. Best Practices for Safe Identification, Characterization, Containment, and Segregation
A systematic approach is essential for managing the diverse array of materials found in industrial decommissioning.
Identification & Characterization:
The process begins with comprehensive site assessments and pre-demolition surveys conducted by competent and qualified persons, such as industrial hygienists or environmental scientists. These assessments should include a thorough review of historical site operations, process flow diagrams, past spill records, visual inspections of all accessible areas, and a robust sampling and analysis plan. Safety Data Sheets (SDS) for chemicals used on-site, combined with process knowledge from former employees and analytical testing of unknown residues, are crucial for determining if materials are hazardous.
Each distinct waste stream must be precisely identified and characterized to determine its properties and regulatory status. For complex mixtures like petroleum sludge, characterization involves detailed analysis of parameters such as pH, electrical conductivity, chemical oxygen demand (COD), total organic carbon (TOC), hydrocarbon fractions (often determined by SARA testing – Saturates, Aromatics, Resins, Asphaltenes), elemental composition, and the concentration of heavy metals.
Containment:
Once hazardous materials are identified, immediate steps must be taken to contain them and prevent their spread. This involves establishing regulated work zones, using physical barriers (e.g., berms, drapes), implementing drainage controls to manage contaminated liquids, and covering equipment or tools with strippable coatings or heavy-duty plastic sheeting to prevent contamination. Hazardous waste must be stored in appropriate containers that are compatible with the waste material, in good condition, properly sealed, and clearly labeled. These containers must meet Department of Transportation (DOT) and United Nations (UN) specifications for structural integrity and hazard communication. Designated hazardous waste storage areas should be established, ensuring they have clear signage, adequate ventilation, secondary containment for liquids, and are regularly inspected.
Segregation:
Proper segregation of different waste streams is critical to prevent dangerous chemical reactions, to ensure compliance with disposal regulations, and to optimize recycling and treatment options. Incompatible materials, such as acids and bases, or flammable substances and oxidizers, must be kept physically separated to avoid violent reactions, fires, or explosions. Hazardous wastes must be segregated from non-hazardous wastes to prevent cross-contamination, which could increase the volume of hazardous waste requiring costly disposal. Furthermore, different categories of hazardous waste (e.g., flammable liquids, corrosive solids, PCB-containing materials) may require different disposal pathways and should be segregated accordingly.7
2.3. Protocols for Safe Removal, Packaging, and Transportation of Hazardous Materials
The physical handling of hazardous materials demands strict adherence to established protocols to protect workers and the environment.
Removal:
The removal of identified hazardous materials should ideally occur before any significant dismantling or demolition activities begin, as this minimizes the risk of uncontrolled releases. This work must be performed by specialized, trained, and often certified teams equipped with the appropriate tools and equipment. Strict adherence to Occupational Safety and Health Administration (OSHA) safety protocols is mandatory. Specific guidelines exist for high-risk materials like asbestos (e.g., wet removal methods, negative pressure enclosures) 18, lead (e.g., dust control, HEPA vacuuming) 18, and PCBs (e.g., specific handling and decontamination procedures for equipment and contaminated building materials). All personnel involved in removal activities must use appropriate Personal Protective Equipment (PPE) selected based on the specific hazards present, including respiratory protection, chemical-resistant suits, gloves, and eye protection.
Packaging:
Once removed, hazardous waste must be packaged in DOT/UN-specified containers that are chemically compatible with the waste they are to contain. Containers must be in good condition, properly sealed to prevent leaks, and correctly labeled with all required information, including hazard class labels, UN identification numbers, shipping names, and handling instructions. It is crucial not to overfill containers or exceed their designated weight limits, as this can compromise container integrity during handling and transport. Secondary containment, such as overpacks or spill pallets, should be used where necessary, particularly for liquid wastes, to provide an additional layer of protection against releases.
Transportation:
The transportation of hazardous materials from the site to a treatment or disposal facility is a highly regulated activity. Only licensed and trained hazardous waste transporters, who are knowledgeable about DOT and EPA regulations, should be used. During loading, containers must be properly secured within the transport vehicle using bracing, strapping, or blocking to prevent shifting, tipping, or puncturing during transit. All shipments of hazardous waste must be accompanied by proper shipping papers, most notably the Uniform Hazardous Waste Manifest, which tracks the waste from its point of generation to its final destination. Transporters must also carry emergency response information, such as the Emergency Response Guidebook (ERG), and drivers must possess appropriate training certifications. Transportation routes should be planned to follow designated hazmat routes and avoid sensitive areas or restricted zones where possible.
The complexity inherent in managing such a diverse array of hazardous materials, each with its unique risks and regulatory requirements, often means that a multi-disciplinary team of experts is essential. This team may include industrial hygienists for exposure assessment, environmental engineers for waste characterization and disposal planning, certified abatement contractors for materials like asbestos and lead, and specialized hazardous waste transportation companies. Relying solely on general contractors who lack this deep, specialized expertise significantly elevates the risk of safety incidents, environmental releases, regulatory non-compliance, and project delays.
2.4. Regulatory Framework (e.g., EPA, RCRA) and Environmentally Sound Practices for Disposal or Treatment
A complex web of regulations governs the management and disposal of hazardous waste, underscoring a societal trend towards increasingly stringent controls and a heightened emphasis on “cradle-to-grave” responsibility. This necessitates meticulous documentation and verifiable compliance at every stage.
Regulatory Framework:
- Resource Conservation and Recovery Act (RCRA): Enacted by the U.S. Congress, RCRA is the cornerstone federal law governing the management of hazardous and non-hazardous solid waste. It establishes a “cradle-to-grave” system, meaning that hazardous waste is tracked and regulated from the moment it is generated until its ultimate disposal. RCRA defines what constitutes a hazardous waste (based on lists or characteristics like ignitability, corrosivity, reactivity, or toxicity), establishes categories for generators based on the quantity of waste produced (Large Quantity Generators – LQGs, Small Quantity Generators – SQGs, and Very Small Quantity Generators – VSQGs), and sets rigorous standards for Treatment, Storage, and Disposal Facilities (TSDFs).
- Environmental Protection Agency (EPA) Regulations: The EPA is responsible for developing and enforcing regulations under RCRA and other environmental statutes. This includes setting specific standards for the management of particular hazardous substances, such as PCBs under 40 CFR Part 761 , asbestos under the National Emission Standards for Hazardous Air Pollutants (NESHAPS, part of the Clean Air Act) , and lead under the Toxic Substances Control Act (TSCA). The EPA also provides detailed guidance on corrective action requirements for facilities that have had releases of hazardous waste or constituents into the environment.
- Occupational Safety and Health Administration (OSHA) Standards: OSHA regulations are focused on protecting worker safety and health. Key standards relevant to decommissioning cleaning include the Hazardous Waste Operations and Emergency Response (HAZWOPER) standard (29 CFR 1910.120 for general industry and 1926.65 for construction), which applies to cleanup operations at hazardous waste sites and emergency responses to hazardous substance releases. OSHA also has specific standards for worker exposure to substances like asbestos (29 CFR 1926.1101) , lead (29 CFR 1926.62) , and respirable crystalline silica.
- Department of Transportation (DOT) Regulations: The DOT, through 49 CFR, regulates the safe transportation of hazardous materials, including requirements for packaging, labeling, placarding, shipping papers (manifests), and driver training.
- State and Local Regulations: Many states are authorized by the EPA to implement their own hazardous waste management programs in lieu of the federal RCRA program. These state programs must be at least as stringent as the federal requirements but can be more stringent or broader in scope. Local ordinances may also apply, particularly regarding demolition permits and noise control.
Environmentally Sound Practices for Disposal or Treatment:
Adherence to the waste management hierarchy is a guiding principle for environmentally sound practices. This hierarchy prioritizes:
- Waste Prevention: Reducing waste generation at the source.
- Reuse: Using materials again for their original purpose.
- Recycling/Recovery: Processing waste materials to recover valuable resources or energy.
- Treatment: Methods to reduce the volume, toxicity, or mobility of hazardous waste.
- Disposal: Safe and permanent containment of residual wastes that cannot be managed by other means.
Specific practices include:
- Recycling/Reuse: Actively explore opportunities to recycle materials like solvents (through filtration or distillation), used oils (through re-refining or fuel-blending), metals, and concrete. Salvageable equipment and components should be decontaminated and prepared for reuse or resale, which can also offset project costs.
- Treatment: A variety of treatment technologies can be employed to alter the character or composition of hazardous wastes. These include thermal treatment (e.g., incineration, pyrolysis), chemical treatment (e.g., neutralization, oxidation, reduction), and biological treatment (e.g., bioremediation for certain organic wastes). The goal of treatment is typically to render the waste less hazardous, reduce its volume, or make it suitable for safe disposal.
- Secure Disposal: For hazardous wastes that cannot be feasibly recycled or treated to non-hazardous levels, disposal in a permitted TSDF is required. The most common type of disposal facility is an engineered hazardous waste landfill, which is designed with multiple layers of protection, including double liners, leachate collection and removal systems, and leak detection systems, to prevent the migration of contaminants into groundwater and surface water.
- Documentation: Meticulous record-keeping is essential for demonstrating regulatory compliance. This includes maintaining copies of waste characterization data, hazardous waste manifests, TSDF receipts, inspection logs, and any required reports to regulatory agencies. This documentation provides a verifiable audit trail for all hazardous waste managed during the project.
The following table provides a summary of common hazardous materials encountered during industrial decommissioning, their associated risks, primary regulatory oversight, and typical management considerations:
Table 1: Common Hazardous Materials in Industrial Decommissioning: Risks, Regulatory Oversight, and Typical Management
Material | Primary Risks (Health & Environmental) | Key Regulatory Agencies/Statutes | Typical Removal & Disposal Considerations |
---|---|---|---|
Asbestos | Lung diseases (asbestosis, lung cancer, mesothelioma) from inhalation of fibers. | EPA (NESHAPS under Clean Air Act), OSHA (29 CFR 1926.1101). | Wet removal methods, containment, HEPA vacuuming, specialized worker training/certification, disposal in designated landfills as asbestos waste. |
Lead | Neurological damage, developmental problems, kidney damage, cardiovascular effects. | EPA (TSCA, RCRA), OSHA (29 CFR 1926.62). | Dust control, HEPA vacuuming, chemical stripping, encapsulation, worker protection (PPE, hygiene), proper disposal of lead-contaminated debris (may be hazardous waste depending on leachability). |
PCBs (Polychlorinated Biphenyls) | Probable human carcinogen, immune system effects, reproductive/developmental problems. | EPA (TSCA – 40 CFR Part 761), RCRA. | Specialized handling of PCB-containing equipment (transformers, capacitors) and bulk product waste (caulk, paint). Specific decontamination procedures. Disposal typically via high-temperature incineration or specialized landfills. |
Mercury | Neurotoxin, kidney damage, developmental effects. | EPA (RCRA – often managed as Universal Waste), Clean Air Act (for emissions). | Careful removal of mercury-containing devices (switches, thermostats, lamps) to prevent breakage and spills. Recycling options preferred. If disposed, managed as hazardous waste. |
Solvents (various) | Organ damage (liver, kidney, nervous system), respiratory irritation, flammability, carcinogenicity (some types). | EPA (RCRA), OSHA (HazCom, specific substance PELs). | Identification (SDS), segregation, use of PPE. Options include recycling (distillation), fuel blending, or incineration as hazardous waste. Proper ventilation during handling. |
Oils (industrial, waste) | Environmental contamination (soil, water), some may contain hazardous constituents (e.g., PCBs, heavy metals). | EPA (RCRA, Spill Prevention, Control, and Countermeasure – SPCC rule), state oil regulations. | Characterization to determine if hazardous. Options include recycling (re-refining, fuel blending), incineration, or disposal in permitted facilities. Absorbents for spills. |
Sludges (petroleum, process) | Can contain toxic hydrocarbons, heavy metals, corrosive agents; environmental contamination. | EPA (RCRA), state regulations. | Characterization is critical. Treatment options include dewatering, stabilization, bioremediation, thermal desorption, or incineration. Disposal in hazardous waste landfills if characteristics warrant. |
Radioactive Materials | Cancer, genetic damage from radiation exposure. | Nuclear Regulatory Commission (NRC) or Agreement State agencies, DOE (for government sites). | Highly specialized handling, shielding, decontamination, packaging, and disposal at licensed low-level or high-level radioactive waste facilities. Extensive worker training and monitoring. |
This rigorous regulatory environment and the inherent dangers of these materials mean that a proactive, knowledgeable, and systematic approach is not just recommended, but essential for any industrial decommissioning project.
3: Core Sub-Task: Cleaning Surfaces for Salvage or Scrap
A significant objective of decommissioning and demolition cleaning is the preparation of equipment, structures, and materials for salvage, reuse, or recycling. Effective surface cleaning is paramount to achieving this, as it not only enhances the economic viability of asset recovery but also plays a crucial role in environmental protection and worker safety.
3.1. The Importance of Surface Cleaning for Asset Recovery, Recycling, and Waste Minimization
Thorough cleaning of surfaces offers multiple benefits within the decommissioning lifecycle:
- Asset Recovery and Value Maximization: Cleaned equipment, machinery, and components are significantly more attractive for resale in secondary markets. Decontamination removes residues that could deter buyers or diminish the operational integrity of the salvaged items. For instance, a food processing plant successfully sold 60% of its decommissioned equipment after cleaning, recouping substantial project costs. This recovered value can directly offset the overall expenses of the decommissioning project.
- Enhanced Recycling and Material Quality: For materials destined for recycling, such as metals (ferrous and non-ferrous) and concrete, cleanliness is key. Contaminants like oils, chemicals, paints, and dirt can degrade the quality of recycled feedstock, reduce its market value, or even render it unsuitable for certain recycling processes. Clean scrap metal, for example, commands higher prices and is more readily accepted by recyclers. Cleaning ensures that these materials can be reintegrated into the manufacturing cycle more efficiently, conserving natural resources and reducing the energy demand associated with virgin material production.
- Waste Minimization and Cost Reduction: Effective surface cleaning and decontamination can significantly reduce the volume of materials classified as hazardous waste. By removing surface contaminants, items that might otherwise have to be disposed of as hazardous (due to adhered residues) can potentially be managed as non-hazardous scrap, salvage, or recyclable material. This is a critical cost-saving measure, as the disposal of hazardous waste is substantially more expensive and highly regulated than non-hazardous waste.
- Improved Worker Safety: Handling materials during dismantling, segregation, transportation, and subsequent processing for salvage or recycling poses inherent risks. Cleaned surfaces reduce worker exposure to potentially harmful residual chemicals, dust, or biological agents, creating a safer working environment throughout the downstream handling chain.
- Environmental Stewardship: By facilitating greater reuse and recycling, surface cleaning contributes directly to a more circular economy within the industrial sector. It transforms potential liabilities (contaminated equipment and materials destined for landfill) into assets (recoverable resources), thereby reducing the overall environmental footprint of facility closure. This proactive approach to resource management extends beyond mere regulatory compliance, demonstrating a commitment to sustainable practices.
The economic viability of salvaging or recycling materials is directly correlated with the level of decontamination achieved. Insufficient cleaning can render potentially valuable materials worthless or, worse, classify them as hazardous waste, thereby negating potential revenue streams and substantially increasing disposal costs. This underscores the financial, as well as environmental, importance of investing in thorough surface cleaning.
3.2. Advanced Decontamination Techniques for Various Surfaces and Materials (Metals, Concrete, Equipment)
The selection of an appropriate decontamination technique depends on several factors, including the type and tenacity of the contaminant, the nature of the surface material (e.g., metal, concrete, plastic), the desired level of cleanliness, cost, safety considerations, and waste generation. A pre-cleaning assessment is crucial to determine these factors and choose the most effective and non-damaging method.
- Physical Removal (Gross Decontamination): This is often the first step, involving the removal of loose or bulk contaminants by methods such as dislodging, displacement, rinsing, wiping off, or scraping. Simple scrubbing with brushes, scrapers, or sponges, often aided by water or compatible solvents, can remove significant amounts of surface debris.
- Aqueous Cleaning: This widely used method employs water-based chemical solutions, often enhanced by heat and mechanical energy (such as agitation or high-pressure spraying), to remove contaminants.
- Techniques: Common aqueous cleaning systems include immersion tanks (where parts are submerged), cabinet or spray washers (which use directed sprays within an enclosure), ultrasonic units (which use high-frequency sound waves to create cavitation bubbles that scrub surfaces), and flush stations (for cleaning internal passages).
- Effectiveness: Highly effective for removing oils, greases, dirt, grime, and some chemical residues from a variety of surfaces. Aqueous systems are generally considered safer for workers and the environment than solvent-based cleaning due to reduced Volatile Organic Compound (VOC) emissions.
- Key Considerations: The effectiveness of aqueous cleaning depends on the interplay of detergent type (alkaline, neutral, or acidic), solution temperature, the degree of mechanical energy applied (e.g., spray pressure, agitation intensity), and contact time. Many systems incorporate filtration units to remove dislodged contaminants from the cleaning solution, extending its life and improving efficiency.
- Mechanical Cleaning / Abrasive Blasting: These methods rely on mechanical force, often in conjunction with an abrasive medium, to strip contaminants from surfaces.
- Techniques: A variety of techniques fall under this category, including dry blasting (propelling dry abrasive particles), slurry blasting (abrasives mixed with water), high-pressure water blasting (hydroblasting, which can range from 10,000 to over 25,000 psi), traditional sandblasting, wheel blasting (where a spinning wheel centrifugally propels abrasives), and vibratory finishing in bowls.
- Abrasive Media: Common abrasives include sand (though its use is increasingly restricted due to silicosis risks), steel shot or grit, glass beads, crushed glass, aluminum oxide, silicon carbide, and organic media like walnut shells or coconut shells. The choice of abrasive depends on the substrate material, the type of contaminant, and the desired surface finish.
- Effectiveness: Highly effective for removing stubborn contaminants such as rust, paint, scale, mill scale, and other tightly adhered coatings from metals and concrete. Abrasive blasting can also be used to create a specific surface profile (roughness) to promote adhesion for subsequent coatings.
- Advantages: The abrasive media are generally inert, meaning they do not chemically react with the underlying material being cleaned. This method can be very efficient for large surfaces.
- Key Considerations: Worker safety is paramount due to dust generation (especially with silica-containing abrasives) and high pressures; appropriate PPE, including respiratory protection and blast suits, is essential. Containment may be needed to control dust and recover spent abrasive.
- Thermal Decontamination: This approach utilizes heat to remove or destroy organic contaminants from surfaces, particularly metals.
- Techniques: Methods include placing parts in convection ovens, salt baths (molten salt), fluidized beds (heated particulate media), or pyrolysis units (heating in an oxygen-deficient atmosphere). A secondary cleaning process, such as aqueous or abrasive cleaning, is often required after thermal treatment to remove ash or residues.
- Effectiveness: Effective for removing organic materials like oils, greases, paints, plastics, and other coatings from robust metallic parts and components.
- Key Considerations: Requires precise control of temperature and residence time to ensure complete contaminant destruction without damaging the part itself. Potential for thermal deformation of parts must be evaluated. Integrated air pollution control systems are necessary to manage emissions (VOCs, HAPs) generated during the heating process.
- Chemical Cleaning: This involves the use of chemical solutions to dissolve, react with, or lift contaminants from surfaces.
- Techniques: Common methods include immersion or dip tanks, spraying the chemical solution onto the surface, or flushing (particularly for internal pipe surfaces). Solvents used can range from water-based solutions containing acids, alkalis, or chelating agents to organic solvents (alcohols, ketones, petroleum distillates).
- Effectiveness: Can be highly effective for removing specific chemical residues, rust, scale, mineral deposits, and even radioactive contaminants.
- Key Considerations: Chemical compatibility with the material being cleaned is crucial to avoid damage or degradation. Worker safety requires appropriate PPE (chemical-resistant gloves, suits, respirators) and adequate ventilation, especially when using volatile or toxic chemicals. The generation and disposal of spent chemical solutions and rinse waters pose significant environmental and cost considerations; these wastes may be hazardous themselves. Heating the chemical solutions is often necessary to accelerate the cleaning process.
- Specialized Techniques for Regulated Contaminants:
- PCBs: The removal of PCB-containing caulk and adjacent contaminated building materials is highly regulated. Surfaces from which PCBs have been removed may require cleaning with specific solvents. All PCB remediation waste must be disposed of according to strict EPA regulations (40 CFR sections 761.61 and 761.62).
- Asbestos: For non-friable Asbestos Containing Material (ACM), wet methods are employed during removal to minimize the release of airborne fibers. Friable ACM requires removal by accredited professionals using specialized containment and negative air pressure techniques. Surfaces are typically cleaned using HEPA vacuuming and wet wiping.
- Lead: Lead-based paint removal often involves wet methods, chemical stripping, or abrasive blasting within containment, followed by HEPA vacuuming to capture lead dust. Surfaces may require cleaning with specialized detergents or encapsulation.
- Laser Cleaning: An emerging, non-contact cleaning method that uses a high-energy laser beam to irradiate and ablate (vaporize or dislodge) surface contaminants such as rust, paint, oxides, and organic residues.
- Advantages: Precise, minimal to no damage to the underlying substrate, no use of solvents or abrasives (hence no secondary waste stream from cleaning media), and can be automated.
- Key Considerations: Higher initial equipment cost, suitability for specific contaminants and substrates, and safety precautions related to laser use.
The choice of cleaning technology is increasingly influenced by a careful balance of cleaning effectiveness, operational cost, worker safety, and environmental impact, particularly concerning the type and volume of waste generated. There is a discernible trend towards adopting safer, more sustainable options like advanced aqueous cleaning systems and exploring innovative, low-waste technologies such as laser cleaning, moving away from methods that pose high EHS risks or create significant hazardous waste byproducts.
3.3. Criteria and Verification for Achieving Cleanliness Levels Suitable for Salvage, Reuse, or Scrap
Simply cleaning a surface is not enough; the level of cleanliness must meet specific criteria depending on the material’s intended fate and applicable regulations.
Defining Cleanliness Standards:
The required cleanliness standards are not universal and vary significantly based on several factors:
- Intended End-Use:
- Salvage for Reuse: Equipment or components intended for reuse in another operational capacity must be cleaned to a level that ensures their functional integrity and poses no risk to new users. This might involve removing all process residues and ensuring no cross-contamination.
- Recycling: Materials destined for recycling (e.g., scrap metal, crushed concrete) must meet the specifications of the recycler. These specifications often limit the types and amounts of allowable contaminants (e.g., oils, paints, plastics on metal).
- Scrap Metal: Scrap dealers have specific criteria for different grades of metal, and contamination can downgrade the material or lead to rejection.
- Regulatory Requirements:
- Hazardous Constituents: If surfaces were contaminated with regulated hazardous substances like PCBs or radioactive materials, specific cleanup levels must be achieved as mandated by regulatory agencies (e.g., EPA, NRC). For PCBs, EPA’s self-implementing cleanup option links cleanup levels to the expected occupancy rates of the area where the contaminated materials are present or were used.
- Free-Release Criteria: For materials potentially contaminated with radioactivity, they must be decontaminated to levels below established “free-release” or “unrestricted use” criteria before they can leave regulatory control. This is often quantified by a Decontamination Factor (DF), which is the ratio of contamination before to after decontamination. For example, a DF of 100 indicates that 99% of the contamination has been removed.
Verification Methods:
A combination of methods is typically used to verify that the desired cleanliness levels have been achieved:
- Visual Inspection: This is the most basic method and is often used for assessing gross contamination, visible dirt, discoloration, stains, or residues. Both natural and ultraviolet (UV) light can be employed; certain organic contaminants fluoresce under UV light, aiding detection. However, visual inspection alone is often insufficient for chemical or radiological contaminants that may not be visible.
- Wipe Sampling: A standard method for assessing surface cleanliness, especially for chemical or radiological contaminants. A sterile wipe (dry or wetted with an appropriate solvent) is systematically wiped over a defined surface area. The wipe is then sent to an accredited laboratory for analysis to quantify the amount of residual contaminant.
- Rinse Water Analysis: For equipment cleaned using liquid methods, analyzing the final rinse water for the presence of contaminants can indicate the effectiveness of the cleaning process. If contaminant levels in the final rinse are above a predetermined threshold, further cleaning may be required.
- Direct Measurement (for radiation): For surfaces potentially contaminated with radioactive materials, radiation survey meters (e.g., Geiger-Mueller counters, scintillation detectors) are used to directly measure radiation levels or surface activity to ensure they are below the applicable release criteria.
- Dimensional Evaluations and Cleanliness Audits: For parts cleaned using mechanical processes, particularly those being remanufactured, dimensional checks and specific cleanliness audits (e.g., particle count analysis) may be required to ensure they meet stringent specifications.
Documentation:
Thorough documentation of all decontamination activities is critical. This includes records of the cleaning methods used, chemicals applied, safety precautions taken, results of verification sampling and analysis, and certification that the materials meet the required cleanliness standards for their intended disposition. For equipment being removed from a radiation-permitted area, a formal decommissioning report signed by a Radiation Safety Officer (RSO) may be required before it can be moved or disposed of. This documentation is vital for demonstrating regulatory compliance, protecting against future liability, and satisfying the requirements of recyclers or buyers of salvaged equipment.
The following table offers a comparative overview of common surface cleaning and decontamination techniques:
Table 2: Comparison of Surface Cleaning & Decontamination Techniques for Salvage/Scrap
Technique | Description | Typical Applications (Materials/Contaminants) | Advantages | Disadvantages/Limitations | Key Considerations (Safety, Waste, Cost) |
---|---|---|---|---|---|
Aqueous Cleaning | Water-based solutions with detergents/chemicals, heat, and mechanical energy (spray, immersion, ultrasonic). | Metals, plastics, ceramics; oils, greases, coolants, particulates, some chemical films. | Safer than solvents (low VOCs), effective for many common contaminants, can be automated. | May require significant water/energy; wastewater treatment needed; may not remove all contaminant types. | Worker exposure to mists/chemicals; wastewater disposal; moderate operating costs. |
Mechanical/ Abrasive Blasting | Propelling abrasive media (sand, grit, shot, beads) at high velocity against a surface. | Metals, concrete; rust, paint, scale, coatings, surface profiling. | Fast, effective for tenacious coatings, creates surface profile for recoating, media often inert. | Dust generation (health hazard, e.g., silicosis with sand), can damage delicate surfaces, noisy. | PPE essential (respiratory, body, hearing); abrasive media disposal/recycling; variable costs depending on media and scale. |
Thermal Decontamination | Using high heat (ovens, pyrolysis, salt baths) to burn off or vaporize organic contaminants. | Primarily metals; paints, oils, greases, plastics, organic resins. | Effective for complete removal of organics, can handle complex shapes. | Energy intensive, potential for part distortion, often requires secondary cleaning for ash, air emissions need control. | High temperatures, air pollution control; ash disposal; can be high cost. |
Chemical Cleaning | Using solvents, acids, alkalis, or chelants to dissolve or react with contaminants. | Metals, some plastics; specific chemical residues, oxides, scale, radioactive isotopes. | Highly selective for certain contaminants, can clean internal surfaces/complex geometries. | Chemical hazards to workers, material compatibility issues, generates liquid hazardous waste. | PPE (chemical resistant), ventilation; hazardous waste disposal of spent chemicals; potentially high chemical and disposal costs. |
Laser Cleaning | Using a focused laser beam to ablate or vaporize surface contaminants. | Metals, stone, composites; rust, paint, oxides, oils, coatings. | Precise, non-contact, no media/solvents (minimal secondary waste), can be automated, gentle on substrate. | Higher initial equipment cost, slower for large areas compared to blasting, effectiveness varies with contaminant/substrate. | Laser safety protocols; minimal waste; high capital cost, lower operating cost. |
This comparative analysis assists in selecting the most appropriate method by balancing cleaning efficacy with operational, safety, environmental, and economic factors.
4: Core Sub-Task: Dust Control During Demolition
Demolition activities, particularly in industrial settings, invariably generate significant quantities of dust. Effective dust control is not merely a matter of site tidiness but a critical component of worker safety, environmental protection, and regulatory compliance. The failure to implement proactive and adequate dust control measures directly leads to increased health risks for workers and the surrounding community, potential environmental contamination, and higher operational costs due to equipment damage, cleanup necessities, and regulatory penalties.
4.1. Understanding the Health Hazards of Demolition Dust and Environmental Impacts
Demolition dust is a complex mixture that can include fine particles from building materials, as well as hazardous substances that were part of the structure or its historical operations.
Health Hazards:
The inhalation of demolition dust can lead to a range of serious, often irreversible, health problems. Key hazardous components and their effects include:
- Respirable Crystalline Silica (RCS): This is a primary concern when demolishing structures containing concrete, brick, stone, mortar, or tiles. Activities like cutting, sawing, grinding, and crushing these materials create very small RCS particles (at least 100 times smaller than ordinary sand) that can be inhaled deep into the lungs. Prolonged exposure to RCS can cause silicosis, an incurable and progressive lung disease characterized by scarring of lung tissue, leading to shortness of breath, disability, and potentially death. RCS exposure also increases the risk of lung cancer, chronic obstructive pulmonary disease (COPD), and kidney disease.
- Asbestos Fibers: If older building materials containing asbestos (e.g., insulation, roofing, siding, tiles) are disturbed during demolition without proper controls, asbestos fibers can become airborne. Inhalation of these fibers can cause asbestosis (a scarring of the lungs), lung cancer, and mesothelioma (a rare cancer of the lining of the chest or abdomen). These diseases often have long latency periods, appearing decades after exposure.
- Lead Dust: Demolition of structures with lead-based paint (common in buildings pre-dating 1978) or other lead-containing materials can release lead dust into the air. Inhalation or ingestion of lead dust can cause lead poisoning, which affects multiple organ systems, including the nervous system, kidneys, and reproductive system. Children are particularly vulnerable to the effects of lead exposure.
- Wood Dust: Generated from the demolition of wooden structures, wood dust can trigger allergic respiratory reactions, asthma-like symptoms, and skin irritation in sensitized individuals. Some types of wood dust are also classified as carcinogens.
- General Particulate Matter (PM10 and PM2.5): Even without specific hazardous components, the fine particulate matter generated during demolition can irritate the respiratory system, trigger asthma attacks, cause bronchitis, and contribute to cardiovascular problems. PM2.5 (particles smaller than 2.5 micrometers) are of particular concern as they can penetrate deep into the lungs and even enter the bloodstream.
- Other Hazards: Demolition dust may also contain mold spores (if the building had water damage), heavy metals (from paints, coatings, or industrial processes), and other chemical residues.
Environmental Impacts:
Uncontrolled demolition dust can have significant adverse effects on the surrounding environment:
- Air Pollution: Dust particles directly contribute to increased levels of particulate matter (PM10 and PM2.5) in the ambient air, potentially exceeding air quality standards.
- Contamination of Soil and Water: Wind can carry dust particles off-site, leading to their deposition on nearby land and water bodies. If the dust contains hazardous substances like lead or asbestos, this can result in the contamination of soil, surface water (through direct deposition or stormwater runoff), and potentially groundwater. This contamination can harm local ecosystems, affect aquatic life, and contaminate drinking water sources.
- Nuisance and Community Impact: Visible dust plumes can be a significant nuisance to neighboring properties, businesses, and the general public, leading to complaints, strained community relations, and potential regulatory action. Effective dust control is therefore not just an EHS requirement but a critical factor in maintaining public trust and ensuring project permissibility. Visible dust can quickly erode community support and lead to project opposition or even shutdowns.
Operational Impacts:
Beyond health and environmental concerns, uncontrolled dust can also negatively affect demolition operations:
- Increased Operating Costs: Excessive dust can accelerate the wear and tear on machinery and equipment, particularly engines and moving parts, leading to more frequent maintenance, repairs, and premature replacement.
- Reduced Visibility and Safety: High levels of airborne dust can reduce visibility on the worksite, increasing the risk of accidents involving workers, equipment, and vehicle traffic.
- Regulatory Non-Compliance: Failure to implement adequate dust control measures can result in violations of OSHA and EPA regulations, leading to fines, stop-work orders, and project delays.
The increasing scrutiny from regulatory bodies like OSHA and the EPA on dust generation, especially concerning hazardous dusts like respirable crystalline silica, is driving a clear trend towards more sophisticated dust monitoring, comprehensive management plans, and the adoption of technologically advanced suppression methods. This shift reflects a growing understanding of the severe risks posed by uncontrolled demolition dust.
4.2. Effective Dust Control Methodologies and Technologies
A variety of methods and technologies can be employed to effectively control dust during demolition activities. The choice of method often depends on the scale of demolition, the type of materials being demolished, site conditions, and regulatory requirements. A combination of approaches is often most effective.
- Wetting Methods (“Wet Wet Wet”): This is one of the most common and fundamental dust suppression techniques. It involves the application of water to surfaces before, during, and after demolition to keep materials damp and prevent dust from becoming airborne.
- Water can be applied using hoses, sprinklers, or water cannons. Demolition equipment, such as excavators, can be fitted with spray nozzles that direct water onto the area of impact.
- The strategy often involves thoroughly soaking the structure or area to be demolished beforehand, continuing to spray water at the point of demolition (e.g., where a wrecking ball strikes or shears cut), and wetting debris as it is being handled, loaded, or moved.
- This method is particularly effective for controlling dust on haul roads, stockpiles, and during general demolition activities.
- Misting Systems / Fog Cannons: These systems generate a fine mist of water droplets (atomized fog) that effectively capture and suppress airborne dust particles by causing them to agglomerate and settle out of the air.
- Misting systems can be more targeted than general wetting and are often more water-efficient. Fog cannons can project mist over large areas or be directed at specific dust-generating operations.
- They are particularly useful for ongoing demolition work in specific areas or for controlling dust from crushing operations.
- Barriers and Enclosures: Physical barriers are used to contain dust within the demolition zone and prevent its migration off-site.
- This can include erecting windscreens, draping structures with tarpaulins or plastic sheeting, using geotextile covers on stockpiles, or installing scaffolding wraps around buildings being demolished.
- For interior demolition, temporary enclosures or containment structures can be built around the work area. Wind breaks can also be strategically placed to reduce wind speed across exposed areas.
- Negative Air Machines: These are portable air filtration units primarily used for interior demolition or within contained areas. They create negative air pressure within the work zone, drawing air from the space through a series of filters, typically including a High-Efficiency Particulate Air (HEPA) filter, which removes dust, asbestos fibers, mold spores, and other airborne particles before exhausting clean air outside the containment.
- Wetting Agents / Chemical Dust Suppressants / Soil Stabilizers: These are chemical products that are added to water or applied directly to surfaces to enhance dust control.
- Wetting agents (surfactants) reduce the surface tension of water, allowing it to penetrate fine materials more effectively.
- Dust suppressants (e.g., hygroscopic salts like calcium chloride or magnesium chloride, lignosulfonates, polymer emulsions) work by binding fine particles together, forming a crust, or keeping surfaces moist.
- Soil stabilizers create a more durable surface on unpaved roads or stockpiles, reducing dust generation from traffic or wind.
- When selecting chemical agents, it is important to consider their biodegradability, suitability for the specific soil or material type, potential environmental impacts (on wildlife, vegetation, water quality), and cost.
- Controlled Demolition Techniques: The method of demolition itself can influence dust generation. Planning demolition sequences to proceed in a controlled manner, such as deconstruction (dismantling piece by piece) versus uncontrolled collapse, can help minimize dust. Using tools that generate less dust (e.g., shears instead of impact hammers for some applications) can also be beneficial.
- Vehicle Movement Control: Traffic on unpaved site roads is a major source of dust. Measures include:
- Enforcing low vehicle speed limits.
- Using designated haul roads that are regularly wetted or treated with suppressants.
- Installing tire washing stations at site exits to remove mud and dust from vehicle tires.
- Paving or applying gravel to frequently used access roads.
- Proper Material Handling and Storage:
- Covering stockpiles of debris or soil with tarps or applying suppressants.
- Using enclosed chutes or conveyors for transferring materials, especially fine or dusty materials.
- Minimizing drop heights when loading debris into trucks.
4.3. Air Quality Monitoring, Occupational Safety Regulations (e.g., OSHA), and EPA Guidelines
A robust dust control strategy must be underpinned by regulatory compliance and verification through air quality monitoring.
Occupational Safety and Health Administration (OSHA):
OSHA is the primary U.S. agency responsible for ensuring worker safety. Key requirements and standards related to demolition dust include:
- General Duty Clause (Section 5(a)(1) of the OSH Act): This clause requires employers to provide a workplace that is “free from recognized hazards that are causing or are likely to cause death or serious physical harm to employees.” This includes hazards from excessive dust exposure.
- Specific Substance Standards:
- Respirable Crystalline Silica (29 CFR 1926.1153 for construction): This comprehensive standard sets a Permissible Exposure Limit (PEL) for RCS of 50 micrograms per cubic meter of air (μg/m3) as an 8-hour time-weighted average (TWA). It also mandates specific requirements such as exposure assessment, use of engineering controls and work practices (outlined in Table 1 of the standard for specific tasks, or alternative exposure control methods), respiratory protection when controls are insufficient, medical surveillance for exposed workers, development of a written exposure control plan, and worker training.
- Asbestos (29 CFR 1926.1101): This standard details requirements for asbestos surveys, notification, worker training, regulated areas, engineering controls (e.g., wet methods, HEPA vacuums, negative pressure enclosures), respiratory protection, and medical surveillance during asbestos abatement and demolition activities.
- Lead (29 CFR 1926.62): This standard sets a PEL for lead, and requires exposure monitoring, engineering controls, respiratory protection, protective clothing, hygiene facilities (showers, change rooms), and medical surveillance for workers exposed to lead.
- Hazard Communication Standard (HazCom) (29 CFR 1910.1200): Requires employers to identify and evaluate chemical hazards (including hazardous dusts) in the workplace, label containers, provide Safety Data Sheets (SDS), and train employees on the hazards and protective measures.
- Respiratory Protection Standard (29 CFR 1910.134): If respirators are required to protect workers from dust exposure (i.e., when engineering and administrative controls cannot reduce exposures to below PELs), employers must implement a comprehensive written respiratory protection program. This program must include procedures for respirator selection, medical evaluations for wearers, fit testing, proper use and maintenance, and worker training.
- Housekeeping Standards: OSHA mandates regular cleaning and good housekeeping practices to prevent the accumulation of dust, which can become an inhalation hazard or, in some cases (combustible dusts), a fire or explosion hazard.
Environmental Protection Agency (EPA):
The EPA regulates dust emissions primarily from an environmental perspective:
- National Ambient Air Quality Standards (NAAQS): The EPA sets NAAQS for several criteria pollutants, including particulate matter (PM10 and PM2.5). While NAAQS apply to ambient air quality in general, demolition sites can be significant sources of PM, and states implement plans to meet and maintain these standards, which may include regulations for controlling dust from construction and demolition activities.
- Fugitive Dust Emissions: The EPA and state environmental agencies require industries, including construction and demolition, to implement measures to control fugitive dust emissions – dust that escapes from identifiable sources like construction sites, unpaved roads, and storage piles – to minimize environmental contamination and public nuisance.
- Asbestos NESHAP (National Emission Standards for Hazardous Air Pollutants): This EPA regulation under the Clean Air Act specifies work practices for asbestos to be followed during the demolition and renovation of most buildings, including notification requirements and procedures for handling and disposing of asbestos-containing materials to prevent asbestos emissions.
National Institute for Occupational Safety and Health (NIOSH):
NIOSH is a research agency that conducts studies and makes recommendations for the prevention of work-related injuries and illnesses. Many OSHA standards are based on NIOSH research and recommendations concerning occupational exposures, including those to hazardous dusts.
Air Quality Monitoring:
Monitoring is essential to assess worker exposures, verify the effectiveness of dust control measures, and ensure compliance with regulatory limits.
- Real-Time Dust Monitoring: Instruments are available that can provide continuous, real-time measurements of particulate matter concentrations (e.g., PM10, PM2.5) at the worksite. These can be used to trigger alerts if dust levels exceed preset thresholds, allowing for immediate corrective action.
- Hyperlocal Data Collection: Deploying a network of sensors across a large demolition site can help identify specific pollution hotspots and enable targeted dust control efforts.
- Personal Exposure Monitoring: This involves placing sampling devices in the breathing zone of workers to measure their individual exposure to specific dusts (e.g., silica, lead, asbestos) over a work shift. Results are compared to OSHA PELs to assess compliance and the adequacy of controls.
- Area Monitoring: Sampling devices placed in fixed locations around the worksite or at the site perimeter can help assess the overall effectiveness of dust control measures and determine potential off-site migration of dust.
Dust Management Plan:
Developing and implementing a site-specific Dust Management Plan is a best practice and often a regulatory requirement. This plan should:
- Identify all potential sources of dust generation.
- Describe the specific dust control measures that will be implemented for each source.
- Outline procedures for air quality monitoring (worker exposure and area monitoring).
- Specify PPE requirements.
- Detail procedures for regular inspection and maintenance of dust control equipment.
- Assign responsibilities for implementing and overseeing the plan.
- Include contingency measures for unexpected events or high dust levels.
The following table summarizes key dust control methods and their typical applications:
Table 3: Key Dust Control Methods in Demolition and Their Applications
Method | Description | Primary Application Area | Advantages | Limitations/Considerations |
---|---|---|---|---|
Wetting (Water Sprays/Hoses) | Applying water directly to materials and active demolition points. | Haul roads, active demolition face, crushing operations, debris handling, stockpiles. | Relatively inexpensive, readily available, effective for many dust types. | Requires water source, can create muddy conditions, may need frequent reapplication, potential for runoff issues, freezing in cold weather. |
Misting Systems/ Fog Cannons | Generating fine water droplets to capture airborne dust. | Large open areas, specific emission points (e.g., crushers, transfer points), active demolition. | More water-efficient than direct spraying for airborne dust, can cover large areas. | Higher initial cost than simple hoses, effectiveness can be wind-dependent, requires power source. |
Physical Barriers/ Enclosures | Using tarps, sheeting, windscreens, or temporary structures to contain dust. | Building perimeters, interior demolition zones, stockpiles, conveyor belts. | Effective at preventing off-site migration, can protect sensitive adjacent areas. | Can be labor-intensive to install/maintain, may restrict access, wind loading on barriers. |
Negative Air Machines | Portable HEPA filtration units creating negative pressure in a contained area. | Interior demolition, asbestos/lead abatement enclosures, areas with highly toxic dusts. | High efficiency in removing fine particulates, controls airborne contaminants within an enclosure. | Limited to enclosed spaces, requires power, filter replacement/disposal. |
Chemical Dust Suppressants/ Wetting Agents | Applying chemical solutions to bind dust particles or improve water penetration. | Unpaved roads, stockpiles, large exposed soil areas, long-term dust control. | Can provide longer-lasting control than water alone, some products are environmentally friendly. | Cost of chemicals, potential environmental impact of some agents, requires proper application, effectiveness varies with product and conditions. |
By integrating these control methods with robust monitoring and adherence to regulatory standards, demolition projects can significantly reduce the risks associated with dust generation.
5: Core Sub-Task: Site Remediation Support
Decommissioning and demolition cleaning activities do not occur in a vacuum; they are often integral precursors to, or components of, broader site remediation efforts. The cleaning and removal of contaminants from structures and equipment directly support and facilitate the subsequent, often more complex, task of addressing contamination in soil and groundwater. The thoroughness and strategic execution of this initial cleaning phase can significantly influence the efficiency, cost, and ultimate success of achieving the site’s remediation objectives.
5.1. Defining Site Remediation and Its Goals for Decommissioned Industrial Sites (Soil, Groundwater Cleanup)
Definition: Site remediation is a multi-faceted process aimed at managing, reducing, or eliminating contamination from soil, sediment, surface water, or groundwater to protect human health and the environment. For decommissioned industrial sites, which often harbor a legacy of contamination from past operations such as spills, leaks, or improper disposal of raw materials, process intermediates, and wastes, remediation is a critical step towards making the land safe and suitable for its intended future use. It is important to recognize that the decommissioning process itself, if not managed with foresight, can inadvertently lead to a spread of existing contamination, further complicating remediation needs.
Goals of Site Remediation for Decommissioned Industrial Sites:
The overarching goals of site remediation are to:
- Protect Human Health and Safety: Prevent current and future human exposure to harmful contaminants through pathways such as direct contact, ingestion of contaminated soil or water, or inhalation of vapors.
- Protect the Environment and Ecosystems: Minimize adverse impacts on local flora and fauna, restore ecological balance, and prevent further degradation of environmental resources.
- Restore Contaminated Media: Clean up contaminated soil and groundwater to levels that are protective of human health and the environment, with a particular focus on restoring current or reasonably expected future sources of drinking water and groundwater closely connected to surface waters, whenever such restoration is practicable and attainable.
- Prevent Contaminant Migration: Implement measures to halt or control the movement of contaminants from source areas to other parts of the site or off-site into surrounding areas.
- Enable Safe Reuse or Redevelopment: Make the site suitable and safe for its intended future purpose, whether that is industrial, commercial, residential, recreational, or a return to a natural state. This often involves meeting specific cleanup standards tied to the planned land use.
- Comply with Regulatory Requirements: Satisfy all applicable federal, state, and local environmental regulations, such as the EPA’s RCRA Corrective Action program, which mandates investigation and cleanup of releases from hazardous waste facilities.
5.2. How Initial Cleaning, Decontamination, and Waste Removal Activities Directly Support and Facilitate Subsequent Site Remediation Efforts
The cleaning and decontamination phases of decommissioning play a crucial supportive role in the overall site remediation strategy. These initial actions directly facilitate more effective and efficient cleanup of subsurface contamination by:
- Reducing Contaminant Source and Load: The removal of residual products, sludges, hazardous materials from tanks, pipes, and process equipment, as detailed in Section 2, eliminates primary, often highly concentrated, sources of contamination. This significantly reduces the mass of contaminants that could potentially leach into underlying soil and groundwater, thereby lessening the burden on subsequent remediation technologies. Similarly, the cleaning and decontamination of building structures and surfaces, as discussed in Section 3, removes surface-level contaminants that could otherwise be mobilized during demolition activities and contribute to soil or stormwater contamination.
- Preventing Cross-Contamination: Controlled cleaning and systematic waste removal practices are essential to minimize the spread of contaminants from known hot spots to cleaner areas of the site during the often disruptive activities of decommissioning and demolition. Effective dust control measures (Section 4) are also critical in this regard, as they prevent the airborne dispersal of contaminants onto surrounding soil surfaces.
- Improving Site Characterization Accuracy: A site that has been cleared of above-ground structures, equipment, and surface debris allows for safer, easier, and more effective site investigation. This is crucial for accurately delineating the horizontal and vertical extent of soil and groundwater contamination. Activities such as test pit excavation, soil boring, and monitoring well installation, which are fundamental to understanding subsurface conditions and designing an appropriate remediation strategy, are greatly facilitated by a clean and accessible site.
- Enhancing the Effectiveness of Remediation Technologies: The removal of bulk waste, free product (e.g., pools of oil or solvents), and highly contaminated materials during the initial cleaning phase can significantly improve the performance and cost-effectiveness of subsequent soil and groundwater treatment methods. Many in-situ remediation technologies, such as bioremediation, chemical oxidation, or soil vapor extraction, are more efficient when source concentrations are reduced, as high concentrations can be toxic to microorganisms or consume excessive amounts of chemical reagents.
- Facilitating Safer and Easier Access for Remediation Operations: The removal of buildings, equipment, and debris not only clears the way for site investigation equipment but also provides better physical access for the often large and specialized machinery required for remediation activities, such as excavators, drill rigs, and mobile treatment units. A less cluttered and hazardous site improves operational safety for remediation personnel.
- Reducing Overall Remediation Time and Cost: By proactively addressing significant surficial and structural contamination sources through thorough cleaning and removal, the scope, duration, and consequently the cost of the subsequent, often more technically complex and expensive, soil and groundwater remediation phases can be substantially reduced. This phased approach optimizes resource allocation and project timelines.
- Supporting Regulatory Closure: A well-documented and thorough cleaning and source removal program can be a significant factor in achieving regulatory site closure, often referred to as a No Further Action (NFA) determination or a Certificate of Completion from environmental agencies. Demonstrating that above-ground sources of contamination have been effectively managed strengthens the case for site closure once subsurface remediation goals are met.
Site remediation should not be viewed as an activity isolated from the preceding decommissioning and cleaning stages. Instead, an integrated approach, where cleaning is strategically planned and executed as a preparatory step for subsurface remediation, is crucial for achieving holistic and lasting environmental restoration of industrial sites. This continuum of action ensures that each phase builds upon the success of the previous one.
5.3. Integrating Cleaning Strategies with Broader Remediation Technologies and Objectives
To maximize the benefits of cleaning activities for site remediation, integration must begin at the earliest stages of project planning.
- Early Planning Integration: The anticipated future use of the site and the corresponding remediation goals should be established early in the decommissioning planning process. For example, a site intended for residential use will typically require much more stringent cleanup levels for soil and groundwater than a site that will continue to be used for industrial purposes. This early understanding informs the scope and rigor of cleaning and decontamination required.
- Phased Approach to Remediation: Decommissioning cleaning naturally fits as the initial phase within a larger, phased remediation project. A typical sequence might involve:
- Phase 1: Source Removal and Surface Decontamination. This includes the cleaning of tanks, pipes, equipment, building surfaces, and the removal of all residual products and hazardous materials as described in previous sections.
- Phase 2: Comprehensive Site Investigation. Following initial cleaning and demolition (if applicable), a detailed investigation is conducted to characterize the nature and extent of any remaining soil and groundwater contamination.
- Phase 3: Remedial Action. Based on the investigation findings and cleanup objectives, appropriate soil and groundwater remediation technologies are selected and implemented.
- Selection of Compatible Cleaning Methods: Cleaning methods should be chosen not only for their effectiveness on the target contaminants and surfaces but also with consideration for their potential impact on subsequent remediation efforts. For instance, cleaning methods that could inadvertently mobilize volatile organic compounds (VOCs) into the soil should be avoided if soil vapor extraction is a planned remediation technology. Conversely, certain cleaning residues might enhance bioremediation if compatible with the microorganisms to be used.
- Coordinated Waste Management: Waste streams generated from cleaning activities (e.g., contaminated rinse water, spent cleaning solutions, contaminated PPE, removed residues) must be managed and disposed of in a manner that is consistent with the overall site waste management strategy and does not create new remediation challenges. The costs and logistics of this waste disposal should be factored into both the cleaning and remediation budgets.
- Data Sharing and Iterative Planning: Information gathered during the cleaning phase, such as the types, quantities, and locations of contaminants encountered, is invaluable for refining the site investigation plan and the selection of remediation technologies. This data should be systematically documented and shared with the remediation team.
- Specific Remediation Technologies Supported by Initial Cleaning:
- Excavation: The removal of contaminated soil is a common remediation technique. Prior cleaning of the site by removing surface debris, structures, and hazardous materials makes the excavation process safer, more efficient, and more targeted, ensuring that only contaminated soil is removed and managed.
- In-Situ Treatment Technologies: These include methods like bioremediation (using microorganisms to degrade contaminants), chemical oxidation or reduction (injecting chemicals to destroy or immobilize contaminants), soil vapor extraction (removing VOCs from soil by vacuum), and air sparging (injecting air into groundwater to volatilize contaminants). The effectiveness of these technologies is often significantly enhanced by the prior removal of source materials and highly concentrated “hot spots” through cleaning and targeted excavation. For example, removing a layer of surface oil allows treatment agents to better contact the underlying contaminated soil.
- Ex-Situ Treatment Technologies: These involve excavating contaminated soil or pumping groundwater for treatment above ground (e.g., soil washing, thermal desorption, pump-and-treat systems). Initial cleaning ensures that the volumes of material requiring such often costly treatment are minimized.
- Capping and Containment: If residual contamination is to be managed in place using engineered caps (e.g., impermeable layers) or containment barrier walls, the site surface must first be cleared of all structures, equipment, and debris. Thorough cleaning ensures that no incompatible materials are left beneath the cap that could compromise its integrity.
The effective integration of cleaning with broader remediation strategies can substantially improve a property’s redevelopment potential and its market value. A site that has been demonstrably and verifiably cleaned and remediated to high standards, with clear documentation of all actions taken, is far more attractive for future investment and use because it significantly reduces the perceived environmental liabilities for potential new owners or developers.
6: Overarching Considerations for Effective Decommissioning and Demolition Cleaning
Beyond the specific sub-tasks, several overarching considerations are critical to the safe, compliant, and effective execution of decommissioning and demolition cleaning projects. These include comprehensive safety planning, robust worker training and protection, and diligent navigation of the complex environmental regulatory landscape.
6.1. Comprehensive Safety Planning: Risk Assessment, Hazard Communication, and Emergency Preparedness Protocols (adhering to OSHA, NFPA, ANSI standards)
The inherently hazardous nature of decommissioning and demolition, particularly in industrial settings with a legacy of chemical use and complex infrastructure, demands meticulous safety planning. The presence of unknown factors often makes this work particularly dangerous. A “culture of safety” that permeates all levels of the operation, from initial planning through to final site handover, is more crucial than mere adherence to a checklist of regulations. This proactive safety culture is essential for managing the highly variable and often unpredictable hazards encountered on these projects.
- Risk Assessment:
A cornerstone of safety planning is a thorough, site-specific risk assessment conducted by competent persons before any work commences. This assessment must identify all potential hazards, including:- Chemical hazards: Exposure to residual process chemicals, hazardous materials (asbestos, lead, PCBs, mercury), flammable substances, and toxic gases.
- Physical hazards: Falls from height, being struck by falling objects or equipment, noise, vibration, electrical hazards, confined space entry risks, and structural instability leading to unplanned collapse. An engineering survey is essential to evaluate the condition of the structure and the possibility of such collapses.
- Biological hazards: Mold, bacteria in stagnant water, or animal vectors.
- Radiological hazards: In specific facilities. The risk assessment should also evaluate environmental factors that could increase safety risks, such as weather conditions or site topography.
- Hazard Communication:
Effective communication of identified hazards and control measures is vital. This involves:- Full implementation of OSHA’s Hazard Communication Standard (HazCom), ensuring workers are informed about the hazardous substances they may encounter.
- Clear and conspicuous labeling of hazardous materials, contaminated areas, and safety equipment.
- Ready accessibility of Safety Data Sheets (SDS) for all chemicals on site.
- Regular safety meetings, pre-task briefings (toolbox talks), and ongoing communication to discuss site-specific hazards, safe work procedures, and any changes in site conditions.
- Emergency Preparedness and Response:
A comprehensive, site-specific emergency preparedness and response plan must be developed, communicated to all personnel, and regularly practiced. Key elements include:- Clearly defined evacuation routes, emergency exits, and assembly points.
- Specific procedures for responding to various credible emergencies, such as fires, chemical spills, medical incidents, structural collapses, or natural disasters.
- A reliable system for emergency communication (e.g., alarms, radios, designated personnel) and a list of emergency contact numbers.
- Adequate and readily accessible first aid supplies, emergency medical services (EMS) arrangements, and appropriate fire suppression equipment (e.g., fire extinguishers).
- Procedures for coordinating with local emergency services (fire department, police, ambulance) and informing them of site-specific hazards.
- Regular emergency drills and simulations to ensure all personnel are familiar with procedures and can respond effectively.
- Adherence to Standards:
Compliance with applicable safety standards is mandatory.- OSHA (Occupational Safety and Health Administration): OSHA standards provide the primary regulatory framework for worker safety in the United States. Relevant standards cover general construction safety (29 CFR 1926), specific demolition operations (29 CFR 1926 Subpart T), hazardous waste operations and emergency response (HAZWOPER), personal protective equipment (PPE), respiratory protection, confined space entry, and standards for specific hazardous substances like asbestos, lead, and silica.
- NFPA (National Fire Protection Association): NFPA develops and publishes codes and standards widely used to minimize the risk and effects of fire and other hazards. Relevant standards may include NFPA 70E (Standard for Electrical Safety in the Workplace®), NFPA 241 (Standard for Safeguarding Construction, Alteration, and Demolition Operations), and NFPA 400 (Hazardous Materials Code).
- ANSI (American National Standards Institute): ANSI facilitates the development of voluntary consensus standards. Some ANSI standards, such as ANSI/ASSP A10.6 (Safety and Health Program Requirements for Demolition Operations), provide valuable industry best practices and may be incorporated by reference in contracts or even by some regulatory bodies.
6.2. Essential Worker Training, Certifications, and PPE Requirements
The competence and protection of the workforce are paramount in decommissioning and demolition cleaning. The level and specificity of worker training and certification directly correlate with the ability to safely and compliantly execute complex cleaning and hazardous material handling tasks. Generic training is insufficient for the unique hazards of these projects; inadequate or non-specific training significantly increases the likelihood of accidents, exposures, and regulatory non-compliance.
- Worker Training:
All workers must receive comprehensive training appropriate to their roles and responsibilities. This training should cover:- Hazard recognition for chemical, physical, biological, and radiological hazards specific to the site and tasks.
- Safe work practices and procedures for their assigned tasks, including proper use of tools and equipment.
- Emergency procedures, including evacuation, spill response, and first aid.
- The requirements of applicable OSHA standards (e.g., HazCom, PPE, specific substance standards).
- Proper selection, use, limitations, inspection, and maintenance of PPE. Training must be provided in a language and vocabulary that workers can understand. Site-specific orientation and training should be conducted before any worker begins activities on site. Refresher training should be provided as needed and as required by regulations.
- Certifications:
Depending on the nature of the work and the hazardous materials present, workers and supervisors may require specific certifications:- HAZWOPER (Hazardous Waste Operations and Emergency Response): As mandated by OSHA (29 CFR 1910.120 and 1926.65), workers involved in cleanup operations at sites contaminated with hazardous substances, or those responding to emergencies involving hazardous substance releases, must receive HAZWOPER training. This typically involves a 40-hour initial course for general site workers who will have significant exposure, a 24-hour course for workers with more limited or occasional exposure, and an 8-hour annual refresher course for all levels. HAZWOPER training covers topics such as hazard recognition, toxicology, PPE selection and use, decontamination procedures, spill control, and emergency response.
- Asbestos Abatement Worker/Supervisor Certification: Individuals involved in the removal, encapsulation, or disturbance of asbestos-containing materials (ACM) must be trained and certified according to EPA and state regulations.
- Lead Abatement Worker/Supervisor Certification (or EPA RRP Certification for Renovation, Repair, and Painting): Required for activities involving the disturbance or removal of lead-based paint.
- Confined Space Entry Training: Workers who must enter permit-required confined spaces (such as tanks, vessels, pits, or manholes) need specialized training on hazard recognition, atmospheric testing, entry procedures, attendant duties, and rescue operations, as per OSHA’s confined space standards (29 CFR 1910.146 for general industry or 1926 Subpart AA for construction).
- Equipment Operation Certifications: Operators of specialized equipment like forklifts, aerial lifts, cranes, and excavators must be trained and certified/licensed as required.
- Personal Protective Equipment (PPE):
The employer is responsible for conducting a hazard assessment to determine the appropriate PPE required for each task and for providing this PPE to workers at no cost. Workers must be trained on the correct way to select, don, doff, adjust, wear, inspect, maintain, and store their PPE.
Common PPE for decommissioning and demolition cleaning includes:- Basic 5-part PPE for demolition: Hard hat, safety glasses (or goggles/face shields as needed), high-visibility vest or jacket, appropriate work gloves (e.g., leather, cut-resistant), and steel-toe protective footwear.
- Respiratory Protection: This is critical when airborne contaminants like dust, mists, vapors, or fibers are present. The type of respirator depends on the contaminant and its concentration. Options range from N95 filtering facepiece respirators for nuisance dusts to half-face or full-face air-purifying respirators (APRs) with appropriate cartridges/filters (e.g., P100 for particulates, organic vapor cartridges for solvents), or even supplied-air respirators (SARs) or self-contained breathing apparatus (SCBA) for highly toxic substances or oxygen-deficient atmospheres.
- Chemical-Resistant Clothing: When handling hazardous liquids or sludges, chemical-resistant coveralls (e.g., Tyvek® or similar), aprons, gloves, and boots are necessary to prevent skin contact. The specific material of the protective clothing must be compatible with the chemicals being handled.
- Hearing Protection: Earplugs or earmuffs are required in areas with high noise levels from machinery or demolition activities.
- Fall Protection Systems: Personal Fall Arrest Systems (PFAS), including harnesses, lanyards, and anchor points, are required for workers exposed to fall hazards of 6 feet (in construction) or more.
6.3. Navigating Key Environmental Regulations and Permitting for Industrial Facility Closure and Decommissioning
The closure and decommissioning of an industrial facility are subject to a wide array of environmental regulations designed to protect public health and the environment from the potential release of hazardous substances. Navigating this multifaceted regulatory landscape requires dedicated environmental compliance expertise throughout the project lifecycle. Attempting to manage this without specialized knowledge can lead to significant legal, financial, and reputational repercussions for the facility owner.
- Facility Closure Requirements:
Federal laws, particularly RCRA, mandate proper facility closure procedures for sites that have handled or stored hazardous materials. The primary goal of closure is to ensure the safe management (disposal or containment) of any hazardous wastes remaining on site to prevent contamination of the surrounding environment.80- “Clean closure” is the preferred approach and involves the complete removal of all hazardous wastes and, where necessary, the decontamination or removal of contaminated soil and equipment from the site being closed.
- “Closure with waste in place” may be an option if clean closure is not feasible. This typically involves engineering controls (e.g., caps, liners) to contain the waste and requires long-term post-closure care, monitoring, and maintenance, potentially for up to 30 years or more, to ensure the containment systems remain effective.
- Key Environmental Regulations (beyond waste disposal covered in Section 2.4):
- Clean Air Act (CAA): This federal law regulates air emissions from stationary and mobile sources. During decommissioning and demolition, activities such as equipment cleaning (e.g., solvent use), material handling, demolition itself (dust), and operation of on-site machinery can generate air pollutants. Permits may be required for certain emission sources, and specific work practices or emission controls may be mandated, particularly for hazardous air pollutants (HAPs). The Asbestos NESHAP, which dictates procedures for asbestos removal and disposal to prevent fiber release, is a key CAA regulation relevant to demolition.
- Clean Water Act (CWA): The CWA regulates the discharge of pollutants into waters of the United States. Decommissioning and demolition activities can generate wastewater from cleaning processes (e.g., equipment washing, decontamination rinsate) and contaminated stormwater runoff from the site. National Pollutant Discharge Elimination System (NPDES) permits may be required for direct discharges to surface waters, and pre-treatment standards may apply for discharges to publicly owned treatment works (POTWs). Stormwater Pollution Prevention Plans (SWPPPs) are often required for construction and demolition sites to manage runoff.
- Toxic Substances Control Act (TSCA): TSCA provides EPA with authority to require reporting, record-keeping, and testing requirements, and restrictions relating to chemical substances and/or mixtures. Certain substances that were widely used in older industrial facilities, such as PCBs (in electrical equipment, caulk) and lead-based paint, are regulated under TSCA, which dictates specific procedures for their handling, cleanup, and disposal.
- Comprehensive Environmental Response, Compensation, and Liability Act (CERCLA/Superfund): CERCLA provides a federal framework for the cleanup of abandoned or uncontrolled hazardous waste sites. If significant historical contamination is discovered during decommissioning that poses an imminent and substantial endangerment, CERCLA provisions could be triggered. Understanding past site uses and potential liabilities under CERCLA is important.
- Permitting:
Decommissioning projects often require a variety of permits from federal, state, and local authorities before work can begin. The specific permits needed will vary depending on the location, the nature of the facility, the types of materials being handled, and the scope of work. Examples include:- Demolition permits from local building departments.
- Hazardous waste generator permits or EPA Identification Numbers (if generating regulated quantities of hazardous waste).
- Air permits for potential emissions from demolition or cleaning activities.
- Water discharge permits (NPDES or local POTW permits) for wastewater or stormwater.
- Special permits for handling and disposing of specific wastes like asbestos or PCBs. Permits often come with specific conditions that must be adhered to before, during, and after the closure and decommissioning activities.
- Notification Requirements:
Regulatory agencies typically require formal notification of various decommissioning-related activities. This can include notifying the EPA or state environmental agency of intent to close a hazardous waste management unit, plans for asbestos abatement, demolition of structures, or generation and shipment of hazardous waste. For example, Small Quantity Generators (SQGs) of hazardous waste have periodic re-notification requirements under RCRA. Timely and accurate notifications are crucial for maintaining compliance. - Environmental Justice Considerations:
Increasingly, environmental regulations and permitting processes incorporate considerations for environmental justice. This may involve assessing the potential for disproportionate adverse environmental or health impacts on minority, low-income, or other overburdened communities located near the facility being decommissioned. Meaningful public participation and engagement with these communities may be required as part of the planning and approval process.82 - Site Restoration and Remediation Standards:
If site remediation is required (as discussed in Section 5), the cleanup levels that must be achieved are determined by applicable environmental regulations and are often tied to the intended future land use of the site. State voluntary cleanup programs or brownfield initiatives may offer pathways for addressing contamination and obtaining regulatory closure.
The sheer number and complexity of these regulations underscore the need for specialized environmental compliance expertise. Professionals in this field can help facility owners identify all applicable requirements, secure necessary permits, develop compliant work plans, manage documentation, and interact effectively with regulatory agencies, thereby minimizing the risk of costly violations and ensuring a smoother project execution.
7: The Imperative of Professional Expertise in Decommissioning and Demolition Cleaning
The multifaceted nature of decommissioning and demolition cleaning, laden with significant safety, environmental, and regulatory challenges, underscores a critical reality: engaging specialized professional services is not merely an operational choice but a fundamental strategic imperative. The potential consequences of undertaking such complex work without the requisite expertise—ranging from severe accidents and environmental damage to substantial fines and long-term liabilities—far outweigh the upfront investment in qualified professionals.
7.1. Advantages of Engaging Specialized Professional Services: Expertise, Efficiency, and Risk Mitigation
Professional decommissioning and demolition cleaning contractors bring a host of advantages that are difficult, if not impossible, for a facility owner to replicate internally.
- Specialized Expertise and Experience:
Reputable professional firms possess years, often decades, of hands-on experience in managing the unique challenges of industrial decommissioning and demolition. This experience translates into an in-depth understanding of:- Complex cleaning and decontamination techniques suitable for various contaminants and materials.
- Safe and compliant methods for handling a wide spectrum of hazardous materials, including asbestos, lead, PCBs, mercury, and reactive chemicals.
- The intricacies of local, state, and federal regulatory requirements, including building codes, safety standards (OSHA), and environmental laws (EPA, RCRA). Professionals are adept at conducting thorough site assessments, identifying hidden dangers that might be overlooked by less experienced personnel, and developing customized, site-specific work plans that address all critical aspects of the project.
- Efficiency and Time Savings:
Specialized contractors have established systems, methodologies, and trained crews that enable them to execute projects with significantly greater efficiency than an in-house team or general contractor could typically achieve. They can:- Streamline the entire process, from initial planning, hazard assessment, and inventory management through to the final removal of materials and site handover.
- Complete projects more quickly, minimizing facility downtime (if applicable before full closure) and accelerating the timeline for site redevelopment or sale.
- Free up the client’s management and staff to focus on their core business activities or transition strategies, rather than being bogged down in the complexities of decommissioning and cleanup.
- Risk Mitigation:
This is perhaps the most crucial advantage. Professional services are geared towards systematically identifying, assessing, and mitigating the myriad risks inherent in these projects:- Safety Risks: They prioritize worker and public safety by conducting comprehensive site evaluations, developing detailed safety plans, ensuring the correct use of appropriate PPE, and adhering to strict safety protocols and regulations. This significantly reduces the likelihood of accidents, injuries, and property damage.
- Environmental Risks: Their expertise in hazardous material identification, containment, removal, and disposal minimizes the potential for spills, releases, and environmental contamination.
- Regulatory & Financial Risks: By ensuring compliance with all applicable laws and standards, professionals help clients avoid costly fines, legal actions, and the long-term liabilities associated with improper decommissioning or waste disposal.
The value proposition of professional services extends beyond mere task execution. It encompasses comprehensive project management, adept navigation of the regulatory maze, and a degree of liability transfer (to the extent contractually agreed and supported by the contractor’s insurance and indemnifications). In essence, these professionals act as a crucial shield for the client, safeguarding them against the inherent complexities and potential pitfalls of such demanding undertakings.
7.2. Ensuring Adherence to Stringent Safety and Environmental Regulations (EPA, OSHA Compliance)
Navigating the complex and ever-evolving landscape of environmental and safety regulations is a core competency of specialized decommissioning and demolition cleaning firms.
- Comprehensive Regulatory Compliance: Professionals are responsible for ensuring that all aspects of the project are conducted in full compliance with applicable local, state, and federal laws and regulations. This includes, but is not limited to, standards set by the EPA (e.g., RCRA for hazardous waste, Clean Air Act for emissions, Clean Water Act for discharges, TSCA for PCBs and lead) and OSHA (e.g., general construction safety, demolition specific standards, HAZWOPER, asbestos, lead, silica, confined space entry).
- Avoidance of Penalties: This diligent attention to compliance helps clients avoid the substantial financial penalties, legal challenges, and project shutdowns that can result from regulatory violations.
- Permitting and Documentation: Professional services typically include managing the necessary permitting processes, preparing and submitting required notifications to regulatory agencies, and maintaining meticulous documentation of all activities, including waste manifests, analytical results, and closure reports. This documentation is critical for demonstrating due diligence and protecting against future claims.
- Safe Hazardous Waste Management: A key area of expertise is the compliant management of hazardous waste. This encompasses accurate identification and characterization of waste streams; proper segregation to prevent incompatible reactions and optimize disposal; compliant packaging and labeling; use of licensed transporters; and disposal at permitted treatment, storage, and disposal facilities (TSDFs).
- Data Security: In facilities where data-bearing devices are being decommissioned, professionals can also ensure secure data destruction, protecting businesses from potential data breaches and associated legal liabilities.
7.3. Access to Advanced Technologies, Specialized Equipment, and Highly Trained Personnel
Professional firms invest in and maintain resources that are typically beyond the reach or core competency of an industrial facility owner.
- Specialized Equipment: They possess and operate a wide array of specialized equipment designed for efficient and safe cleaning, decontamination, material handling, and demolition. This may include ultra-high-pressure water blasting units, industrial vacuum trucks (for wet and dry materials), negative air machines with HEPA filtration, robotic demolition tools, specialized excavators with shears or grapples, and various decontamination units. Access to the right equipment for the specific task significantly enhances safety and productivity, which would be prohibitively expensive for a facility owner to acquire and maintain for a one-time project.
- Advanced Technologies and Techniques: Leading contractors stay abreast of and utilize innovative technologies and advanced techniques for cleaning (e.g., automated hydroblasting, foam cleaning, laser cleaning), decontamination, and hazardous material handling, often leading to more effective, safer, and sometimes more cost-efficient outcomes.
- Highly Trained and Certified Personnel: The workforce of a professional decommissioning firm is its greatest asset. These teams are typically:
- Extensively trained in relevant safety procedures and regulatory requirements (OSHA 10/30-hour, HAZWOPER 40/24-hour, etc.).
- Certified for specific high-hazard tasks such as asbestos abatement, lead removal, confined space entry, and the operation of specialized heavy equipment.
- Experienced in working in challenging industrial environments and managing complex logistical operations.
- Often cross-trained to handle multiple aspects of a project, improving efficiency and coordination.
7.4. Cost-Effectiveness Through Strategic Planning, Waste Minimization, and Liability Reduction
While engaging professional services involves an upfront cost, it frequently proves to be more cost-effective in the long run when all factors are considered.
- Strategic and Early Planning: Professionals develop detailed, customized decommissioning and cleaning plans based on thorough site assessments and a clear understanding of the client’s objectives and regulatory obligations. For complex industrial sites, initiating this planning process 12 to 18 months before the intended closure is often recommended to allow for adequate investigation, permitting, and resource allocation. This proactive planning helps to optimize timelines, allocate resources efficiently, and anticipate potential challenges.
- Waste Minimization and Asset Recovery: A key focus of professional services is to minimize the generation of waste, particularly hazardous waste, and to maximize the recovery of value from decommissioned assets.
- They implement strategies for segregating waste streams to ensure that non-hazardous materials are not unnecessarily contaminated.
- They are adept at identifying equipment, machinery, and materials (like scrap metal) that can be salvaged, decontaminated, and sold or recycled, often generating revenue that can help offset project costs.
- Liability Reduction: By ensuring full regulatory compliance, implementing robust safety measures, and maintaining thorough documentation, professional services significantly reduce the client’s exposure to short-term and long-term liabilities. This includes avoiding fines for non-compliance, minimizing the risk of costly accidents or environmental releases, and protecting against future legal claims related to improper waste disposal or site contamination.
- Prevention of Costly Mistakes: Amateur or inadequately planned decommissioning efforts can lead to serious and expensive mistakes, such as damage to adjacent property or utilities, uncontrolled release of hazardous materials requiring emergency response and extensive cleanup, or project delays due to regulatory stop-work orders. Professionals, through their experience and planning, help prevent these costly errors.
- Overall Cost Savings: When the benefits of efficiency, risk mitigation, regulatory compliance, asset recovery, and avoidance of penalties are factored in, the engagement of professional services often results in lower overall project costs compared to attempting the work in-house or with non-specialized contractors.
The increasing specialization within the decommissioning and demolition industry strongly suggests that facility owners should seek service providers with demonstrable, specific experience relevant to their particular industry sector (e.g., chemical, petroleum refining, nuclear, pharmaceutical, manufacturing) and with the specific types of contaminants and structures present on their site. Generic demolition or cleaning expertise is often insufficient for the unique challenges posed by complex industrial facilities, where highly specialized knowledge, such as managing petroleum sludge or navigating nuclear decommissioning protocols, is paramount.
7.5. Illustrative Examples or Brief Case Study Insights Demonstrating Successful Outcomes
Real-world examples highlight the value and necessity of professional expertise in complex decommissioning and demolition cleaning projects:
- Chemical Plant Decommissioning (EWMI) : A project involving the complete internal demolition of a 400,000-square-foot chemical manufacturing plant required meticulous cleaning, decommissioning, and demolition of numerous pipes, vessels, tanks, and other equipment. A critical challenge was the diversity of chemical wastes present, which necessitated pre-sampling, detailed characterization, and compliant transportation and disposal. All 42 tanks and vessels were thoroughly cleaned of liquids, sludges, and solids, along with associated process piping, before demolition and scrap preparation. The project’s success, marked by adherence to a strict timeline and zero loss-time safety incidents, was attributed to a detailed work plan emphasizing schedule, sequence, and safety.
- Above Ground Storage Tank (AST) Decommissioning (EWMI) : In a massive project in California, over 220 ASTs, ranging in size from 5,000 to 1,000,000 gallons, were decommissioned and demolished. This involved identifying and properly removing all asbestos-containing material (ACM) from each tank according to state and federal guidelines. Following tank demolition, contaminated soils beneath the tank floors were excavated, stockpiled, analyzed, and then transported and disposed of at a permitted facility. This case demonstrates the integration of hazardous material abatement, demolition, and remediation support.
- Hydrochloric Acid Plant Demolition (EWMI) : This project involved surgical and structural demolition of a former acid plant, including buildings, pipe racks, vessels, and process equipment. A key goal was to maximize the reclamation of building materials (scrap metal, concrete for fill) and minimize landfill waste. Scrap metal sales helped offset project costs. The project was completed safely and on time, with additional scope items successfully incorporated.
- Asbestos Removal for Proactive Risk Reduction (Asbestos Safety and Eradication Agency Report) : Several organizations have made proactive decisions to remove asbestos, even if not immediately failing, to reduce future risks, eliminate ongoing management costs (audits, maintenance), and increase property value and reuse options. Examples include the City of Adelaide removing significant friable asbestos from a former bakery to protect public and staff safety, and BOC Australia stripping 6,500m² of asbestos roof and wall sheeting to mitigate risks from future storm damage. These cases underscore the long-term benefits of addressing hazardous materials comprehensively.
- Comprehensive Industrial Services (O6 Environmental, Republic Services) : Companies like O6 Environmental and Republic Services offer “turnkey” demolition, dismantling, and decontamination services across various industrial sectors, including specialty chemical, petroleum refining, pharmaceutical, and manufacturing. Their services explicitly include handling hazardous materials, bulk excavation, industrial cleaning (power washing, chemical cleaning), abatement of regulated materials (lead, PCBs), waste characterization, transportation, disposal, and asset recovery. Their emphasis on highly trained teams, specialized equipment, and regulatory compliance highlights the professional standards expected in the industry.
These examples consistently demonstrate that successful industrial decommissioning and demolition cleaning projects are characterized by meticulous planning, expert execution by trained professionals, strict adherence to safety and environmental regulations, and a strategic approach to waste management and asset recovery. The complexity and high-stakes nature of these undertakings make professional expertise indispensable for achieving desired outcomes while minimizing risks.
8: Final Thoughts
Decommissioning and demolition cleaning in industrial facilities represents a critical and highly complex phase in the lifecycle of these assets. It is far more than a simple cleanup operation; it is a meticulously planned and executed series of tasks essential for ensuring worker safety, protecting public health and the environment, complying with a stringent and multifaceted regulatory framework, and preparing sites for future productive use.
The core sub-tasks—removal and disposal of residual products and hazardous materials, cleaning surfaces for salvage or scrap, dust control during demolition, and site remediation support—are interconnected and demand specialized knowledge, equipment, and methodologies.
The successful management of hazardous substances like asbestos, lead, PCBs, mercury, petroleum sludges, and various chemical residues requires rigorous identification, characterization, containment, segregation, removal, and compliant disposal, all while adhering to “cradle-to-grave” responsibilities under regulations such as RCRA. Similarly, preparing equipment and structures for salvage or recycling through advanced decontamination techniques not only offers economic benefits through asset recovery but also promotes sustainability and waste minimization.
Controlling the significant health and environmental hazards posed by demolition dust, particularly silica and other toxics, necessitates proactive strategies including wetting, misting, barriers, and robust air monitoring. Furthermore, initial cleaning and decontamination activities are fundamental to supporting and streamlining subsequent site remediation efforts aimed at addressing legacy soil and groundwater contamination.
Overarching all these activities is the absolute necessity for comprehensive safety planning, including detailed risk assessments, effective hazard communication, emergency preparedness, and stringent adherence to OSHA, EPA, NFPA, and ANSI standards. A highly trained and appropriately certified workforce, equipped with the correct Personal Protective Equipment, is indispensable for navigating the hazardous environments typical of these projects.
Given the inherent complexities, the potential for severe consequences from errors, and the extensive regulatory obligations, the engagement of specialized professional decommissioning and demolition cleaning services is not just advisable but imperative for most industrial facility closures. Professionals bring unparalleled expertise, access to advanced technologies and specialized equipment, highly trained personnel, and a systematic approach to project management.
Their engagement translates into enhanced safety, greater efficiency, robust regulatory compliance, effective risk mitigation, and often, long-term cost-effectiveness through strategic planning, waste minimization, asset recovery, and the avoidance of significant liabilities.
Ultimately, responsible decommissioning and demolition cleaning is a testament to a company’s commitment to safety, environmental stewardship, and corporate responsibility. It is a critical investment in protecting human health, preserving environmental quality, and enabling the sustainable redevelopment and reuse of industrial land for future generations.