Combustible Dust Cleaning: Ensuring Safety and Compliance in Industrial Environments
Combustible dust represents a severe and often underestimated hazard in numerous industrial settings. The accumulation of finely powdered materials, even those not typically flammable in larger forms, can lead to devastating explosions and fires if not managed with rigorous cleaning protocols and safety measures.
1. The Hidden Menace: Understanding Combustible Dust
The term “dust” often evokes images of harmless, inert particles. However, in an industrial context, certain types of dust can be anything but harmless. Understanding what combustible dust is, where it comes from, and which industries are most vulnerable is the first step toward mitigating its significant risks.
Contact us!
Defining Combustible Dust: More Than Just Dirt
Combustible dust is defined by the National Fire Protection Association (NFPA) in Standard 652 as “a finely divided combustible particulate solid that presents a flash-fire hazard or explosion hazard when suspended in air or the process-specific oxidizing medium over a range of concentrations”. This definition is crucial because it highlights that the hazard is not just about the material itself, but its physical state (finely divided) and its interaction with the environment (suspension in air).
A critical aspect often overlooked is that many materials not considered flammable in their larger, solid forms can become highly explosive when reduced to fine dust. This transformation occurs because the fine particulate form dramatically increases the surface area of the material exposed to oxygen, allowing for rapid combustion if an ignition source is present.
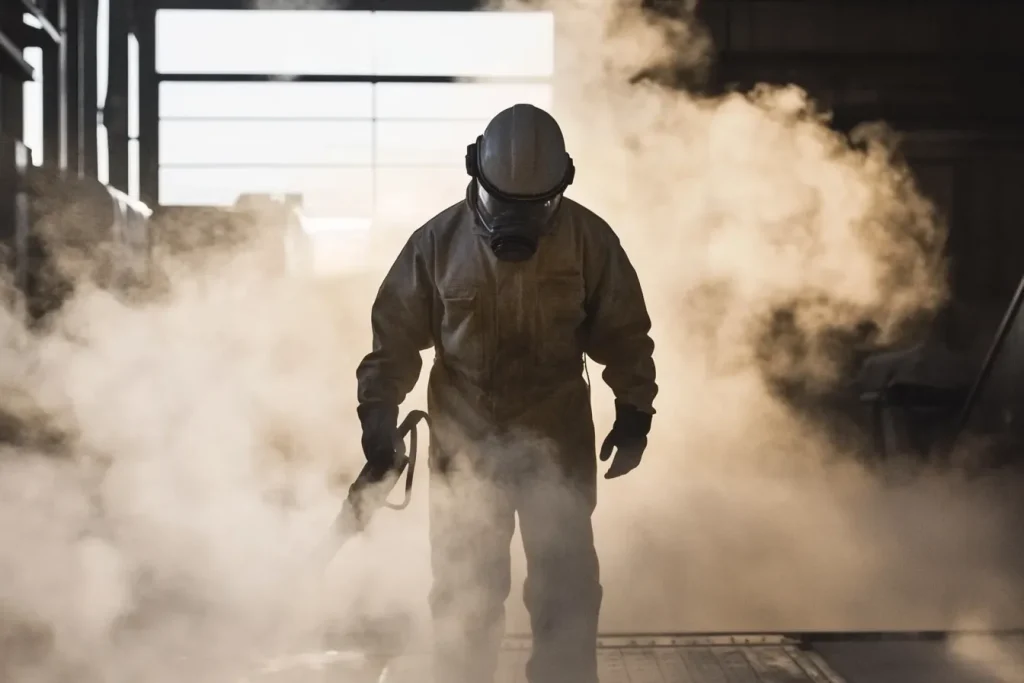
Examples include common industrial materials like aluminum or iron, which are not typically thought of as fire hazards in bulk but can be extremely dangerous as dust. This fundamental misunderstanding of how material properties change at the particulate level means many facilities may not even recognize they harbor a combustible dust problem.
The term “particulate solid” encompasses a variety of forms, including not only fine powders but also fibers, fines, chips, chunks, or flakes. This broad definition ensures that various types of industrial byproducts are considered in hazard assessments.
Common Materials That Form Combustible Dust
The range of materials that can form combustible dust is extensive, spanning numerous categories. Awareness of these materials is vital for facilities to identify potential hazards:
- Food Products: This category is surprisingly vast and includes items like sugar, candy, spices, starch (corn, rice, wheat, potato), flour (various types including soy), powdered milk, egg whites, whey, cocoa powder, and coffee dust. The prevalence of these materials in food processing makes this sector particularly vulnerable.
- Agricultural Products: Beyond processed foods, raw agricultural products like grain, tobacco, alfalfa, cotton, and wood flour are also significant sources of combustible dust.
- Metals: Many metals, when finely divided, are highly combustible. These include aluminum, chromium, iron, magnesium, zinc, and bronze. Metal dusts often have specific, more stringent handling requirements, such as those outlined in NFPA 484, Standard for Combustible Metals.
- Wood and Paper: Sawdust, wood flour, paper dust, and cellulose pulp are well-known combustible dusts commonly found in woodworking and paper manufacturing industries.
- Plastics and Rubber: A wide array of synthetic materials, including various polymers (e.g., polyethylene, (poly)acrylamide), epoxy resins, and rubber, can produce combustible dust during processing.
- Chemicals and Pharmaceuticals: This group includes dyes, pesticides, various pharmaceutical powders (including active pharmaceutical ingredients and excipients), and sulfur.
- Carbonaceous Dusts: Materials rich in carbon, such as coal, charcoal, petroleum coke, and soot, are inherently combustible as dust.
The following table provides a quick reference for common combustible dusts and the industries most frequently at risk:
Table 1: Common Combustible Dusts and High-Risk Industries
Material Category | Specific Examples of Dust | Commonly Affected Industries |
---|---|---|
Food Products | Flour, Sugar, Starch, Powdered Milk, Cocoa, Spice | Bakeries, Grain Elevators, Confectionery, Food Processing, Feed Mills |
Agricultural Products | Grain Dust, Wood Flour, Cotton Fibers, Tobacco Dust | Farming, Silos, Textile Mills, Animal Feed Production |
Metals | Aluminum, Magnesium, Iron, Zinc, Bronze | Metal Fabrication, Foundries, 3D Printing, Automotive, Aerospace |
Wood and Paper | Sawdust, Sanding Dust, Paper Dust, Cellulose | Woodworking, Furniture Manufacturing, Sawmills, Paper Mills, Recycling |
Plastics and Rubber | Polyethylene, Polypropylene, Epoxy Resins, Rubber Dust | Plastics Manufacturing, Rubber Processing, Tire Manufacturing, Recycling |
Chemicals | Dyes, Pesticides, Sulfur, Various Organic Powders | Chemical Manufacturing, Pharmaceutical Production, Agrochemicals, Paint Production |
Pharmaceuticals | APIs, Excipients, Bulk Powders | Pharmaceutical Manufacturing, Nutraceuticals |
Carbonaceous Materials | Coal Dust, Charcoal Powder, Coke Dust, Lignite | Power Generation (coal-fired), Mining, Cement Manufacturing, Foundries (using carbon additives) |
Industries at High Risk for Combustible Dust Incidents
Given the wide array of materials that can form combustible dust, numerous industries face significant risks. Key sectors include:
- Food Manufacturing and Processing: High incidence due to organic dusts like flour, sugar, and spices. Statistics indicate that the food industry accounts for a substantial percentage of dust explosions, with one report noting 24% of workplace explosions in Europe occur in this sector, and another citing 31% of cases in a different dataset.
- Woodworking: Sawmills, furniture manufacturing, and any facility processing wood generate large quantities of fine wood dust, a well-known explosion hazard. Woodworking accounts for around 24% to 42% of explosions in various statistical reports.
- Chemical Manufacturing: Handling powdered chemicals, plastics, and pharmaceuticals creates inherent risks.
- Metal Processing: Grinding, polishing, and other fabrication processes involving metals like aluminum and magnesium produce highly reactive dusts.
- Pharmaceuticals: The handling of fine powders during various stages, from bulk material handling to packaging, generates dust.
- Agriculture: Grain elevators, feed mills, and facilities handling agricultural commodities are prone to dust explosions.
- Plastics and Rubber Manufacturing: Processing these materials often creates fine particulate matter.
- Textile Industry: Cotton and other fiber dusts can be combustible.
- Fossil Fuel Power Generation: Coal dust is a primary hazard in coal-fired power plants.
- Recycling Operations: Processing paper, plastics, and metals can generate combustible dusts.
Many routine industrial processes inherently create combustible dust, such as grinding, cutting, sanding, conveying, mixing, sifting, and packaging. This means the risk is often integral to a facility’s core operations, not an anomaly, necessitating continuous and vigilant management. Furthermore, the insidious nature of dust means it often accumulates in unseen or hard-to-reach areas like rafters, on top of ductwork, behind equipment, and above suspended ceilings. This “hidden” fuel load can become a significant factor in secondary explosions, making even facilities with otherwise good surface-level housekeeping vulnerable if these areas are neglected.
2. The Science of Disaster: The Dust Explosion Pentagon
For a combustible dust explosion to occur, five specific conditions must be met simultaneously. These conditions are often represented as the “Dust Explosion Pentagon”. Understanding each element and their interplay is fundamental to preventing such catastrophic events. If any one of these elements is removed, an explosion cannot occur.
The Five Elements of a Dust Explosion
- Fuel: This is the combustible dust itself. The characteristics of the dust, such as particle size (finer particles are more hazardous), moisture content (drier dust is generally more easily ignited), and concentration in the air, are critical factors.
- Oxygen: An oxidant, typically oxygen from the ambient air, is required to support combustion. In most industrial environments, sufficient oxygen is readily available, making this element the most difficult to eliminate as a control measure.
- Ignition Source: A source of energy sufficient to ignite the dispersed dust cloud is necessary. Potential ignition sources are numerous and varied, including open flames, welding and cutting sparks, electrical sparks from faulty wiring or equipment, static electricity discharge, hot surfaces, and friction from machinery components. The wide range of potential ignition sources makes their complete elimination challenging.
- Dispersion: The combustible dust particles must be suspended in the air at a concentration within the explosible range (between the Lower Explosible Limit (LEL) and Upper Explosible Limit (UEL)). Activities such as sweeping, using compressed air for cleaning, or even the shockwave from a small initial event can disperse accumulated dust into a dangerous cloud.
- Confinement: The dispersed dust cloud must be in an enclosed or semi-enclosed space, such as a vessel, pipeline, room, building, or piece of equipment. Confinement allows pressure to build rapidly as the dust combusts, leading to an explosion. While a flash fire (rapid burning of a dust cloud) can occur without confinement, a true explosion with damaging pressure effects requires it.
The elements of the Dust Explosion Pentagon are not independent; one can influence or trigger another. For instance, a small, localized ignition source might cause a minor combustion event (a primary explosion). The shockwave from this primary event can then disperse accumulated dust layers throughout a larger, confined area, providing the fuel and dispersion needed for a much larger and more destructive secondary explosion if another ignition source is present or if the primary event propagates. This interconnectedness means that control strategies must address multiple elements of the pentagon, not just focus on, for example, ignition sources. Simply managing ignition sources is insufficient if significant fuel (dust) is allowed to accumulate and can be easily dispersed.
Primary vs. Secondary Explosions: A Chain Reaction of Destruction
Combustible dust incidents often involve two distinct phases: a primary explosion and a subsequent, often more devastating, secondary explosion.
- Primary Explosion: This is the initial explosion that occurs when a dispersed dust cloud within a confined space (like a piece of equipment, a duct, or a small room) is ignited. While potentially damaging in its own right, the primary explosion’s most dangerous consequence is often its ability to dislodge and aerosolize larger quantities of dust that have accumulated on surfaces throughout the facility—on rafters, beams, equipment tops, and floors.
- Secondary Explosion: Once the shockwave from the primary explosion lofts these accumulated dust layers into the air, a much larger, more widespread fuel-air mixture is created. If this newly formed dust cloud encounters an ignition source (which could be the flame front from the primary explosion itself or another independent source), a secondary explosion occurs. These secondary explosions are frequently far more destructive than primary ones due to the significantly larger volume of fuel involved and the larger area over which the pressure wave can propagate. The infamous Imperial Sugar Refinery explosion in 2008, which caused multiple fatalities and extensive damage, is a tragic example of how a primary event can trigger catastrophic secondary explosions fueled by accumulated sugar dust.
The phenomenon of secondary explosions underscores the critical importance of meticulous housekeeping. Preventing the accumulation of dust on all surfaces, especially in hidden and overhead areas, is paramount to eliminating the fuel for these more severe secondary events. While primary explosions can be damaging, it is often the secondary explosions that lead to widespread facility destruction and a higher number of casualties. Therefore, controlling widespread dust accumulation is arguably one of the most critical life-safety imperatives in facilities with combustible dust hazards.
It is also important to recognize that routine industrial activities or improper cleaning methods can inadvertently provide the missing elements to complete the Dust Explosion Pentagon. For example, sweeping with brooms or using compressed air for cleaning can cause significant dispersion of dust particles. Many pieces of processing equipment inherently provide confinement. Friction from misaligned machinery parts or static electricity generated during material transfer can serve as an ignition source. This means that the risk of a dust explosion doesn’t just arise from major system failures but can be triggered by normal operations or well-intentioned but misguided cleaning practices if not managed correctly.
3. Navigating Compliance: Key NFPA Standards and OSHA Guidance
Managing combustible dust hazards effectively requires adherence to a framework of standards and regulations. The National Fire Protection Association (NFPA) develops consensus standards that provide detailed guidance, while the Occupational Safety and Health Administration (OSHA) enforces workplace safety, often referencing NFPA standards. Understanding these key documents is crucial for compliance.
Overview of NFPA 652: Standard on the Fundamentals of Combustible Dust
NFPA 652 serves as the foundational or “gateway” standard for combustible dust safety. Its primary purpose is to establish the basic principles and minimum requirements for managing the fire and explosion hazards of combustible dusts and particulate solids.
Key mandates of NFPA 652 include:
- Dust Combustibility Testing: Facilities must determine if the dusts they handle are combustible or explosible, often through laboratory testing. This is a fundamental first step, as a facility cannot manage a hazard it hasn’t identified.
- Dust Hazard Analysis (DHA): NFPA 652 requires that a DHA be conducted for all facilities and processes where combustible dust is present. This requirement is retroactive, meaning it applies to existing facilities and processes, as well as all new ones. The initial deadline for completing DHAs for existing processes was September 7, 2020.
- Hazard Management: Identified fire, flash fire, and explosion hazards must be managed through documented prevention and protection measures.
NFPA 652 also directs users to other, more specific NFPA standards for detailed requirements related to particular industries or commodities, such as NFPA 61 for agricultural and food processing facilities, NFPA 484 for combustible metals, NFPA 664 for wood processing, and NFPA 655 for sulfur.
NFPA 654: Standard for the Prevention of Fire and Dust Explosions from the Manufacturing, Processing, and Handling of Combustible Particulate Solids
NFPA 654 applies to industries and commodities not covered by a specific industry or commodity standard (e.g., chemicals, pharmaceuticals, plastics, textiles, and general manufacturing). It provides comprehensive requirements for preventing dust fires and explosions.
A significant focus of NFPA 654 is on housekeeping. Chapter 8 of this standard provides detailed guidance on:
- Cleaning Frequency: Establishing schedules to prevent hazardous accumulations of dust.
- Cleaning Methods: Specifying approved methods, with a strong preference for vacuuming.
- Dust Accumulation Limits: Emphasizing the critical threshold that dust accumulations should not exceed 1/32 of an inch (approximately the thickness of a paper clip) over a surface area of at least 5% of the floor area, or any accumulation that could create a hazardous dust cloud.
- Documentation: Requiring written housekeeping programs and records of cleaning activities.
- Restrictions on Compressed Air: The use of compressed air for cleaning surfaces is generally prohibited or severely restricted due to its tendency to create dust clouds. It may only be permitted under specific conditions, such as for inaccessible areas after other methods have been used and all ignition sources are controlled.
The New NFPA 660: Consolidating Combustible Dust Safety (Effective December 2024)
Recognizing the complexity and potential for inconsistencies across multiple dust-related standards, the NFPA has developed NFPA 660, Standard for Combustible Dusts. This new standard, effective December 6, 2024, consolidates several key NFPA dust standards, including NFPA 652, NFPA 654, NFPA 61 (Agricultural and Food Processing), NFPA 484 (Combustible Metals), NFPA 655 (Sulfur), and NFPA 664 (Wood Processing and Woodworking Facilities) into a single, comprehensive document.
The primary goal of NFPA 660 is to simplify compliance by providing a unified reference that resolves inconsistencies and offers a more structured approach to managing combustible dust hazards. The standard is generally structured with core requirements applicable to all facilities (Chapters 1-10) and industry-specific chapters that retain essential guidance for particular dust types or processes (Chapters 21-25).
Key areas emphasized or updated in NFPA 660 include:
- Reinforcement of the Dust Hazard Analysis (DHA) process.
- Clear guidelines for housekeeping and dust management, including dust buildup limits.
- Protocols for ignition source control.
- New requirements for evaluating hazards such as self-heating, thermal instability, and water reactivity.
The move to consolidate multiple standards into NFPA 660 is intended to bring clarity. However, the very need for such a comprehensive document, which still includes both core and industry-specific requirements, underscores the inherent complexity and nuanced approaches required to manage the diverse range of combustible dust hazards effectively.
OSHA’s Role and Housekeeping Requirements
The Occupational Safety and Health Administration (OSHA) plays a critical role in ensuring worker safety in the United States. While OSHA does not have a single comprehensive standard specifically for combustible dust, it addresses the hazard through several mechanisms:
- OSHA’s General Duty Clause (Section 5(a)(1) of the OSH Act): This clause requires employers to furnish to each worker “employment and a place of employment, which are free from recognized hazards that are causing or are likely to cause death or serious physical harm”. Combustible dust is a well-recognized hazard, and OSHA can cite employers under this clause for failing to adequately address it.
- OSHA’s Combustible Dust National Emphasis Program (NEP) (CPL 03-00-008): This program targets industries known to have combustible dust hazards and outlines OSHA’s inspection and enforcement protocols. The NEP signals a heightened focus by OSHA on these hazards.
- Reliance on NFPA Standards: OSHA frequently uses NFPA standards as references for identifying combustible dust hazards and determining feasible abatement methods. While NFPA standards are not laws in themselves, OSHA’s use of them in enforcement actions gives them significant regulatory weight. Non-compliance with relevant NFPA standards can, and often does, lead to OSHA citations.
- Specific OSHA Standards: Certain existing OSHA standards are also applicable, such as 29 CFR 1910.22, which addresses walking-working surfaces and requires that workplaces be kept clean, orderly, and sanitary. OSHA also provides guidance that aligns with NFPA recommendations, such as cleaning dust residues at regular intervals, using cleaning methods that do not generate dust clouds if ignition sources are present, using only vacuum cleaners approved for dust collection, and keeping dust accumulation below the 1/32-inch threshold.
The evolution of NFPA standards, particularly the mandates within NFPA 652 and the comprehensive nature of the new NFPA 660, reflects a significant shift in regulatory philosophy. The emphasis is now firmly on a proactive, systematic, and documented approach to safety management. This involves thoroughly testing dusts to understand their properties, conducting comprehensive Dust Hazard Analyses to identify facility-specific risks, implementing robust engineering and administrative controls, meticulously documenting all procedures and actions, and ensuring that all employees are adequately trained. This is a departure from a more reactive approach that might have focused primarily on cleaning up after dust has accumulated, towards a holistic strategy of preventing hazardous conditions from developing in the first place.
Table 2: Overview of Key NFPA Standards for Combustible Dust
Standard | Primary Focus/Purpose | Key Requirements Relevant to Cleaning | Relationship to OSHA |
---|---|---|---|
NFPA 652 (Standard on the Fundamentals of Combustible Dust) | Establishes fundamental requirements for managing combustible dust hazards. Acts as a “gateway” standard. | Mandates Dust Hazard Analysis (DHA) for all facilities. Requires dust combustibility testing. Outlines general principles for hazard management, including housekeeping. | Foundational guidance often referenced by OSHA. Compliance with DHA is critical. |
NFPA 654 (Standard for the Prevention of Fire and Dust Explosions from the Manufacturing, Processing, and Handling of Combustible Particulate Solids) | Provides requirements for general industry and materials not covered by specific commodity standards. | Specifies detailed housekeeping methods, frequency, and dust accumulation limits (e.g., 1/32 inch). Prefers vacuuming, restricts compressed air. Requires written housekeeping programs. | Frequently used by OSHA as a benchmark for acceptable practices in general industry. |
NFPA 660 (Standard for Combustible Dusts – New, Consolidating Standard) | Consolidates NFPA 652, 654, and several commodity-specific standards (metals, agriculture, wood, sulfur) into one comprehensive document. | Integrates and refines requirements from previous standards. Emphasizes DHA, written dust management programs, cleaning frequencies, ignition source control, and documentation. | Expected to become the primary reference for OSHA for combustible dust safety, streamlining compliance expectations. |
4. Proactive Prevention: The Critical Role of Dust Hazard Analysis (DHA)
The Dust Hazard Analysis (DHA) is not merely a recommendation but a mandatory requirement under NFPA 652, forming the cornerstone of any effective combustible dust safety program. It is a proactive measure designed to systematically identify, evaluate, and control the fire, flash fire, and explosion hazards associated with combustible dusts within a facility.
What is a DHA and Why is it Mandatory?
A DHA is defined as a systematic review of the processes and areas within a facility where combustible particulate solids are present. Its purpose is to identify potential fire, flash-fire, and explosion hazards, assess their likelihood and severity, and recommend measures to mitigate these risks. The DHA aims to uncover all potential hazards, including those that may not be immediately obvious or were previously unknown, define safe operating parameters, and outline existing and additional hazard management measures. As part of the process, locations within the facility are typically categorized based on their hazard level (e.g., not a hazard, might be a hazard, or a confirmed deflagration/fire hazard).
The mandate for conducting a DHA comes directly from NFPA 652, which requires it for ALL facilities that handle or generate combustible dust. This requirement applies retroactively to existing facilities and processes, as well as to all new installations. The deadline for existing facilities to complete their initial DHA was September 7, 2020 , underscoring the urgency and importance placed on this analysis. A DHA is specifically triggered if dust testing reveals a Kst value greater than zero, indicating that the dust is explosible.
The DHA serves as the foundational assessment upon which all subsequent prevention, protection, and mitigation strategies are built. Without a thorough understanding of the specific dust properties (obtained through combustibility testing) and the unique hazards present within a facility’s operations and layout, any cleaning plan or control measure implemented would be based on assumptions. Such an approach could be dangerously inadequate or, in some cases, even introduce new risks. Therefore, the DHA is the essential first step before any effective and compliant cleaning protocols or safety systems can be designed and implemented.
Key Components of a DHA
A comprehensive DHA involves several critical components and must be conducted with diligence and expertise:
- Qualified Personnel: NFPA 652 stipulates that the DHA “shall be performed or led by a qualified person”. This individual should possess documented experience and education regarding DHA methodologies, as well as the assessment and identification of mitigation options for fire, flash fire, and explosion hazards. While the DHA is often a team effort involving facility personnel familiar with operations, maintenance, and safety systems, the leadership of a qualified person, potentially an external consultant, is crucial. A “fresh set of eyes” from an external expert can often identify hazards that internal staff, despite their process knowledge, might overlook due to familiarity. Consultants also bring valuable cross-industry insights and specialized hazard identification skills.
- Dust Combustibility Testing: An essential precursor to or component of the DHA is laboratory testing of representative dust samples from the facility. This testing determines if the dust is combustible and, if so, its explosibility characteristics (e.g., Kst, Pmax, Minimum Ignition Energy (MIE)). These properties are vital for assessing the severity of potential explosions and designing appropriate protective measures.
- Systematic Review: The DHA involves a methodical examination of all processes and areas where combustible dust is present or may accumulate. This includes evaluating raw material handling, processing equipment (grinders, mixers, conveyors, etc.), dust collection systems, potential ignition sources (electrical, mechanical, static), existing fire protection and explosion mitigation systems, and housekeeping practices.
- Hazard Identification and Risk Assessment: The core of the DHA is identifying specific locations and scenarios where combustible dust could lead to a fire, flash fire, or explosion. For each identified hazard, the analysis should evaluate the risk, considering both the likelihood of an incident and its potential consequences.
- Recommendations for Prevention and Mitigation: Based on the identified hazards and risks, the DHA must provide practical and prioritized recommendations for managing these hazards. This can include engineering controls (e.g., improved dust collection, explosion venting or suppression), administrative controls (e.g., enhanced housekeeping procedures, ignition source control programs), and the use of appropriate PPE.
- Documentation: The findings, analyses, and recommendations of the DHA must be thoroughly documented in a written report. This report serves as a critical record for compliance, a basis for implementing corrective actions, and a reference for future safety audits and DHA updates.
- Regular Review and Revalidation: A DHA is not a one-time event. NFPA standards require that the DHA be reviewed and updated at least every five years, or whenever significant changes occur in processes, materials, equipment, or facility design that could affect combustible dust hazards. This ensures that the safety measures remain relevant and effective in a dynamic industrial environment, making the DHA a living document and a continuous risk management tool.
The mandatory nature of the DHA, its comprehensive scope, and the requirement for qualified leadership underscore its critical importance. It is the definitive starting point for any facility seeking to achieve compliance and ensure a safe environment where combustible dust is present.
5. Specialized Combustible Dust Cleaning Procedures: A Step-by-Step Approach
Once a Dust Hazard Analysis (DHA) has been completed and the specific risks associated with combustible dust in a facility are understood, a tailored cleaning program can be developed. This program must adhere to strict safety protocols and utilize specialized procedures and equipment to prevent igniting the dust or creating hazardous conditions during the cleaning process itself.
Core Principle: Safety First and Foremost
Before any cleaning activities commence, a site-specific risk assessment for the cleaning tasks must be performed, drawing upon the findings of the overall facility DHA. Cleaning combustible dust is inherently hazardous, and the act of cleaning can itself introduce risks if not managed correctly.
Personal Protective Equipment (PPE): The use of appropriate PPE is mandatory for all personnel involved in combustible dust cleaning. The specific PPE required will be determined by the DHA and the nature of the dust, but commonly includes:
- Flame-resistant garments (FRG) or coveralls to protect against flash fires.
- Respiratory protection (e.g., N95 respirators, powered air-purifying respirators (PAPRs), or self-contained breathing apparatus (SCBA), depending on dust concentration and toxicity) to prevent inhalation of harmful particulates.
- Eye protection (e.g., safety goggles or face shields).
- Gloves appropriate for the materials being handled.
- Safety footwear, often with conductive properties to help dissipate static electricity.
- Hard hats, especially when working around overhead structures or equipment.
It is crucial to remember that PPE is the last line of defense; the primary focus should always be on eliminating or controlling the hazard at its source.
The following table provides a comparison of common cleaning methods, highlighting their suitability and limitations:
Table 3: Comparison of Combustible Dust Cleaning Methods
Method | Pros | Cons | Appropriate Scenarios |
---|---|---|---|
Certified Explosion-Proof Vacuuming | Preferred by NFPA standards. Minimizes dust cloud generation. Efficiently collects dust. | Higher equipment cost. Requires specific certifications for the hazard. Requires trained operators. | Most situations involving dry combustible dusts. The primary and safest method. |
Wet Washing / Wet Sweeping | Can effectively suppress dust clouds. Can cool surfaces. May be suitable for some dusts that are difficult to vacuum. | Not suitable for water-reactive dusts (e.g., aluminum, magnesium). Electrical hazards if equipment is not de-energized. Can be messy and require wastewater management. May damage water-sensitive materials/equipment. | For non-water-reactive dusts where vacuuming is impractical. Areas without significant electrical hazards (or where power is locked out). Surfaces that can tolerate moisture. |
Blow-Down (Compressed Air/Steam) – Highly Restricted Use | Can reach some inaccessible areas. | Creates significant dust clouds. High risk of explosion if ignition sources are present. Generally prohibited or severely restricted by NFPA/OSHA. | Only as a last resort after other methods (vacuuming, washing) have been attempted. For truly inaccessible locations. ALL ignition sources must be rigorously controlled or eliminated. Area must be clear of personnel not directly involved. |
Sub-Task 1: Certified Explosion-Proof Vacuum Systems – The Preferred Method
Vacuuming is universally recognized by NFPA and OSHA as the preferred and safest method for cleaning combustible dust. This preference is due to its ability to capture and contain dust effectively, thereby minimizing the generation of hazardous dust clouds. However, it is absolutely critical that only certified explosion-proof vacuum systems are used. Standard commercial or household vacuum cleaners are not designed for this purpose and can themselves become potent ignition sources due to sparks from their motors, static electricity buildup, or hot surfaces.
Understanding Certifications (ATEX, UL, CSA, NRTL):
The selection of a compliant vacuum cleaner is a complex task, as it must be certified for the specific hazardous environment in which it will be used.
- NRTL Certification (North America): In the United States and Canada, electrical equipment for hazardous locations must be tested and certified by a Nationally Recognized Testing Laboratory (NRTL). Examples of NRTLs include UL (Underwriters Laboratories) and CSA (Canadian Standards Association). It is important to note that NFPA and OSHA do not certify equipment themselves; they set the standards that NRTLs test against.
- NEC Class/Division/Group Ratings: For North American hazardous locations, vacuums are rated according to the National Electrical Code (NEC) classification system:
- Class II: Indicates the presence of combustible dust.
- Division 1: Areas where combustible dust is normally present in the air in ignitable concentrations during regular operations, or where mechanical failure or abnormal operation of equipment might produce such concentrations and also provide an ignition source.
- Division 2: Areas where combustible dust is not normally present in ignitable concentrations but may become so due to infrequent malfunctioning of handling or processing equipment, or where dust accumulations might interfere with heat dissipation from electrical equipment or be ignitable by abnormal operation.
- Groups E, F, G: These groups categorize dusts by their specific properties. Group E includes combustible metal dusts (e.g., aluminum, magnesium), which are often highly conductive and reactive. Group F includes certain carbonaceous dusts (e.g., coal, carbon black). Group G includes other combustible dusts not in E or F (e.g., flour, grain, wood, plastic). A vacuum must be certified for the specific Class, Division, and Group(s) corresponding to the dust(s) present.
- ATEX Directives (Europe): In Europe, equipment for potentially explosive atmospheres must comply with ATEX directives. Vacuums are categorized based on the zone of operation:
- Zone 20: Area where an explosive atmosphere consisting of a cloud of combustible dust in air is present continuously, for long periods, or frequently (inside containers, pipework).
- Zone 21: Area where an explosive atmosphere consisting of a cloud of combustible dust in air is likely to occur in normal operation occasionally.
- Zone 22: Area where an explosive atmosphere consisting of a cloud of combustible dust in air is not likely to occur in normal operation but, if it does occur, will persist for only a short period.
- Equipment is marked with categories like 1D (Zone 20), 2D (Zone 21), 3D (Zone 22).
The complexity of these certification systems means that selecting the correct vacuum is not a simple matter of choosing one labeled “explosion-proof.” It requires a detailed understanding of the specific dust characteristics and the environmental classification of the area where cleaning will occur. An incorrectly specified vacuum can be as dangerous as using a standard vacuum.
Key Features of Compliant Vacuums:
A vacuum cleaner suitable for combustible dust must possess several critical design features:
- NRTL Listing/Certification: The entire vacuum system, not just individual components like motors or switches, must be listed or certified by an NRTL for the specific hazardous location classification (Class, Division, Group) or meet ATEX requirements for the relevant zone.
- Bonding and Grounding: The vacuum must be constructed with all conductive parts bonded together (electrically continuous) and effectively grounded to dissipate static electricity. This includes the chassis, motor housing, collection container, inlet, hoses, wands, and cleaning tools. Look for features like conductive or static-dissipative hoses and accessories, and anti-static casters.
- Motor Placement and Protection: The electric motor should not be in the dust-laden airstream unless it is specifically listed for Class II, Division 1 locations. Typically, motors are located on the “clean side” of the filtration system, or the vacuum may be pneumatically powered (air-operated), which eliminates electrical ignition sources from the motor.
- Non-Sparking Construction: Components that may experience impact or friction, or are in direct contact with the dust, should be made of non-sparking materials (e.g., stainless steel, aluminum for certain parts) to prevent mechanical sparks.
- Appropriate Filtration: The vacuum must have a filtration system capable of safely capturing the specific dust. This often includes:
- Antistatic filters to prevent static buildup on the filter media itself.
- High-Efficiency Particulate Air (HEPA) filters may be required for very fine dusts or hazardous substances to ensure clean exhaust air.
- Paper filter elements should generally not be used, especially for collecting liquids or wet materials, as they can degrade or lose integrity.
- Sealed System: The vacuum should be designed to prevent leakage of dust from the collection container or other parts of the system.
Operational Procedures for Explosion-Proof Vacuums:
Proper operation is as crucial as selecting the right equipment:
- Inspect Before Use: Always inspect the vacuum for damage, ensure all components are correctly assembled, and verify that grounding connections are intact.
- No Ignition Sources: Never vacuum smoldering materials, glowing embers, or known ignition sources.
- Approved Accessories: Use only conductive or static-dissipative hoses, wands, and tools that are approved by the vacuum manufacturer and designed for combustible dust service. Ensure they are properly bonded to the vacuum system.
- Filter Maintenance: Regularly inspect and clean/replace filters according to the manufacturer’s recommendations and the specific dust load. Clogged filters reduce efficiency and can create hazards.
- Hose Management: Use appropriate hose lengths and diameters for the application to maintain adequate conveying velocity and prevent blockages. Avoid excessive bends or kinks.
- Metal Dusts: Special precautions are needed for highly reactive metal dusts like aluminum, magnesium, or titanium. These may require vacuums with immersion separation systems, where the dust is collected into a liquid bath (typically oil or water, depending on the metal’s reactivity) to neutralize its explosive potential. Dry vacuuming of some metal dusts is prohibited.
- Emptying Collection Containers: Follow safe procedures for emptying dust collection containers, minimizing dust dispersion. The collected dust itself is still combustible and must be disposed of properly according to hazardous waste regulations if applicable.
The following checklist can aid in the selection of certified explosion-proof vacuum systems:
Table 4: Checklist for Selecting Certified Explosion-Proof Vacuum Systems
Feature/Consideration | Explanation/Why it Matters |
---|---|
NRTL Certification (e.g., UL, CSA) | Third-party validation that the entire vacuum system meets safety standards for use in specific hazardous locations. Essential for North American compliance. |
Appropriate Class/Division/Group Rating (NEC) | Ensures the vacuum is designed for the specific type of combustible dust (Group E, F, G) and the likelihood of its presence in ignitable concentrations (Division 1 or 2). |
ATEX Zone Rating and Category (EU) | Ensures compliance with European directives for equipment used in potentially explosive atmospheres (Zone 20, 21, 22; Category 1D, 2D, 3D). |
Fully Bonded & Grounded Construction | All conductive components are electrically connected and have a path to earth ground to prevent static electricity accumulation and discharge, a common ignition source. |
Non-Sparking Materials of Construction | Parts like inlets, collection bins, and internal deflectors made of materials (e.g., stainless steel) that are less likely to produce mechanical sparks upon impact or friction. |
Motor Placement/Type | Motor should be outside the dust-laden airstream or specifically certified for the hazardous environment (e.g., Class II, Div 1 motor). Pneumatic (air-operated) vacuums eliminate electrical motor ignition risk. |
Filtration System (Antistatic, HEPA) | Filters must be antistatic to prevent charge buildup. HEPA filtration may be needed for fine or hazardous dusts. No paper filters for wet collection. |
Conductive/Static-Dissipative Hoses & Accessories | Ensures that static charges generated by dust movement through hoses and tools are safely conducted to the grounded vacuum unit. |
Immersion Separator (for specific metal dusts) | Required for safely collecting highly reactive metal dusts (e.g., aluminum, magnesium) by neutralizing them in a liquid bath. |
Sub-Task 2: Wet Cleaning Methods – Application and Limitations
While certified vacuuming is the preferred method, wet cleaning techniques such as water wash-down or wet sweeping can be employed in certain situations, particularly when vacuuming is impractical or as a supplementary measure.
When is Wet Cleaning Appropriate?
- Dust Suppression: Wet methods are effective at suppressing dust clouds, preventing fine particles from becoming airborne.
- Impractical Vacuuming: In some large outdoor areas or where the nature of the surface makes vacuuming difficult, wet cleaning might be considered.
- Source Control with Wet Collectors: Wet dust collectors or scrubbers can be integrated into processes to capture dust at the source, neutralizing it in a liquid medium (usually water). These systems are particularly useful for high-temperature or high-humidity air streams and can handle some challenging dusts.
Safe Techniques: Washing Down and Wet Sweeping
- Apply water gently to surfaces to wet the dust and prevent it from becoming airborne. Avoid high-pressure sprays that could aerosolize fine particles or spread contamination.
- For wet sweeping, use brooms or squeegees to gather the wetted dust into piles for collection and disposal.
- Ensure adequate drainage if large volumes of water are used. Contaminated water may need to be collected and treated before disposal, depending on the nature of the dust and local environmental regulations.
- The “top-down” cleaning approach (cleaning higher surfaces before lower ones) is also applicable to wet cleaning methods to prevent re-contamination.
When to Avoid Wet Cleaning:
The decision to use wet cleaning methods is highly context-dependent and must be carefully evaluated due to significant limitations and potential hazards:
- Water-Reactive Dusts: This is a critical prohibition. Many combustible dusts, particularly metal dusts such as aluminum, magnesium, titanium, sodium, and lithium, react exothermically with water. This reaction can produce flammable hydrogen gas and significant heat, creating a severe explosion or fire hazard that is often more dangerous than the dry dust itself. The DHA must identify if any dusts present are water-reactive.
- Electrical Hazards: Using water near energized electrical equipment or wiring poses a serious risk of electrical shock, short circuits, and equipment damage. All electrical power to equipment in the cleaning area must be shut off, locked out, and tagged out (LOTO) before wet cleaning begins, and equipment must be suitably protected from water ingress.
- Material Damage or Product Quality: Water can damage certain products, raw materials, or equipment components. It can also affect product quality in industries like food processing or pharmaceuticals if not carefully controlled.
- Freezing Conditions: In unheated areas or environments prone to freezing temperatures, wet cleaning is impractical as the water can turn to ice, creating slip hazards and potentially damaging structures.
- Hygroscopic Dusts: Some dusts are hygroscopic, meaning they readily absorb moisture from the air or when wetted. This can cause them to become sticky, caked, or corrosive, making them more difficult to remove and potentially creating new hazards or operational problems.
- Biological Growth: If areas remain damp after wet cleaning, it can promote the growth of mold or bacteria, particularly with organic dusts.
The choice of cleaning method must always be informed by the DHA, considering the specific properties of the dust, the nature of the facility and equipment, and potential interactions.
Sub-Task 3: Proper Grounding and Bonding of Equipment – Eliminating Static Ignition
Static electricity is a pervasive and often invisible ignition source in industrial environments handling combustible dusts. The movement of dust particles, whether during processing, conveying, or cleaning, can generate significant electrostatic charges on equipment, hoses, tools, and even personnel. If these charges accumulate to a sufficient level, a spark (electrostatic discharge) can occur, potentially igniting a nearby combustible dust cloud. Therefore, proper grounding and bonding of all cleaning equipment, especially vacuum systems, are fundamental safety requirements. NFPA 77, Recommended Practice on Static Electricity, provides detailed guidance on these measures.
Procedures for Effective Grounding and Bonding:
- Bonding: This is the process of connecting all conductive components within a system (e.g., parts of a vacuum cleaner, sections of ductwork, nozzles, collection drums) together using conductive materials like wires or straps. Bonding ensures that all connected items are at the same electrical potential, preventing sparks from jumping between them. For example, the nozzle, wand, hose, filter assembly, and collection container of a vacuum system should all be electrically continuous.
- Grounding: This is the process of connecting the bonded system (or individual conductive items) to a verified earth ground, such as a driven ground rod or the building’s grounding system. Grounding provides a safe path for any accumulated static charge to dissipate to the earth, preventing it from building up to hazardous levels.
- Application: These principles apply to all equipment used in combustible dust environments:
- Vacuum Cleaners: As previously detailed, certified explosion-proof vacuums are designed with internal bonding and a designated grounding point. Hoses and tools must also be conductive or static-dissipative and properly connected.
- Ductwork and Dust Collectors: Fixed dust collection systems require all sections of ductwork, hoods, collectors, and associated equipment to be bonded and grounded.
- Personnel: In some highly sensitive environments, personnel may need to use conductive footwear, anti-static wrist straps, or work on grounded floor mats to prevent charge accumulation on their bodies.
- Verification: It is crucial to ensure that bonding and grounding connections are made to clean, bare metal surfaces, as paint, rust, or coatings can act as insulators and impede electrical continuity. The integrity of grounding and bonding systems should be periodically inspected and tested (e.g., with an ohmmeter to verify low resistance paths) to ensure they remain effective.
Grounding and bonding are not optional accessories but integral safety features. A single ungrounded component in a cleaning system can accumulate enough static charge to become an ignition source. This meticulous attention to detail in ensuring electrical continuity and a reliable path to ground is vital for preventing static-induced ignitions.
Sub-Task 4: Careful Handling to Avoid Dust Cloud Generation – Keeping Dust Contained
A core principle of safe combustible dust cleaning is to minimize the generation and dispersion of dust clouds. A suspended dust cloud is one of the five essential elements of the Dust Explosion Pentagon. Improper cleaning techniques can inadvertently create these hazardous conditions.
Techniques to Minimize Dust Dispersion During Cleaning:
- Vacuuming: Using certified explosion-proof vacuums with appropriate filtration is the most effective way to capture dust at its point of accumulation without making it airborne.
- Gentle Sweeping (Limited Use): If vacuuming is absolutely not feasible, dust can be gently swept using soft brooms or brushes made of non-sparking materials. The collected dust should then be carefully scooped into conductive or static-dissipative containers that are bonded and grounded. Vigorous sweeping must be avoided.
- Wet Methods (Where Appropriate): Applying water or other suitable liquids (for non-water-reactive dusts) can effectively dampen dust and prevent it from becoming airborne during collection (see Sub-Task 2).
- Strict Limitation of Compressed Air: The use of compressed air or steam for “blow-down” cleaning of surfaces is strongly discouraged and often prohibited by NFPA standards and OSHA guidance. Compressed air readily disperses fine dust into large clouds, significantly increasing the risk of an explosion if an ignition source is present. This practice is a common source of OSHA citations. It should only be considered as a last resort for cleaning inaccessible areas after all other methods (vacuuming, washing) have been attempted, and only if all potential ignition sources in the vicinity have been rigorously controlled or eliminated, and appropriate respiratory protection is used.
- Source Capture and Air Cleaning: During ongoing industrial processes that generate dust, local exhaust ventilation (LEV) or source capture systems (e.g., hoods connected to dust collectors) should be used to capture dust as it is produced, preventing its escape into the wider environment. Portable air cleaners with HEPA filtration can also help reduce ambient dust levels in some enclosed areas.
The “Top-Down” Cleaning Approach:
A practical technique to improve cleaning effectiveness and prevent re-contamination is the “top-down” method. Cleaning should always start from the highest points in a room or area (e.g., ceiling trusses, rafters, tops of machinery, overhead pipes and ductwork) and proceed downwards to lower surfaces and finally the floor. This ensures that any dust dislodged from higher areas falls onto surfaces yet to be cleaned, rather than re-contaminating already cleaned areas. This systematic approach enhances both the thoroughness and efficiency of the cleaning process.
The act of cleaning itself can, paradoxically, create a hazard if performed incorrectly. This underscores the paramount importance of comprehensive training for cleaning personnel and strict adherence to procedures designed to keep dust contained and prevent the formation of explosive clouds.
Sub-Task 5: Documentation of Cleaning Procedures – Ensuring Accountability and Compliance
Thorough documentation is a critical component of any combustible dust safety program, including cleaning procedures. NFPA standards (notably NFPA 652, 654, and the new NFPA 660) emphasize the need for written programs and record-keeping.
What to Document:
Comprehensive documentation should include:
- Written Housekeeping Program: A formal, written program detailing the methods, frequency, and responsibilities for cleaning combustible dust in all areas of the facility. This program should be based on the findings of the DHA.
- Cleaning Activity Logs: Records of when cleaning was performed, which areas were cleaned, the specific methods used (e.g., vacuum model, wet wash), and the personnel who conducted the work.
- Inspection Records: Logs of regular inspections for dust accumulation levels (e.g., depth measurements in various locations), the condition of dust-generating equipment, and the functionality of dust control systems.
- Dust Hazard Analysis (DHA) Reports: The initial DHA report and all subsequent reviews and updates must be maintained.
- Employee Training Records: Documentation of all training provided to employees and contractors regarding combustible dust hazards, safe work practices, cleaning procedures, emergency response, and the use of PPE.
- Equipment Maintenance Records: Records of inspection, maintenance, and repair for all equipment used for combustible dust control and cleaning, especially certified explosion-proof vacuums and dust collection systems.
- Incident Reports and Corrective Actions: Detailed reports of any fires, explosions, flash fires, or near-miss incidents related to combustible dust, along with documentation of investigations and corrective actions taken to prevent recurrence.
Importance for Safety Audits and Continuous Improvement:
Meticulous record-keeping is vital for several reasons:
- Demonstrating Compliance: Documentation provides tangible evidence of a facility’s due diligence and efforts to comply with OSHA regulations, NFPA standards, and requirements from local Authorities Having Jurisdiction (AHJs) and insurance providers. This is crucial during safety audits or inspections.
- Trend Analysis: Analyzing cleaning logs, inspection records, and incident reports over time can help identify trends, such as areas with persistent dust accumulation, recurring equipment issues, or the effectiveness of different cleaning frequencies or methods. This data can inform adjustments to the housekeeping program.
- Preserving Institutional Knowledge: Well-maintained records ensure that critical safety information and procedures are preserved, even with personnel changes. This supports consistency in safety practices over time.
- Facilitating Continuous Improvement: Documentation forms the basis for reviewing the effectiveness of the combustible dust safety program and identifying opportunities for continuous improvement in procedures, equipment, and training.
In essence, documentation transforms combustible dust cleaning from a series of isolated tasks into a manageable, verifiable, and improvable system that contributes to overall workplace safety.
6. The Professional Advantage: Why Expert Combustible Dust Cleaning is Essential
While the preceding sections outline the critical procedures for combustible dust cleaning, the complexity, inherent dangers, and stringent regulatory requirements associated with this task often make it unsuitable for in-house teams lacking specialized training and equipment. Engaging professional combustible dust cleaning services offers significant advantages in terms of expertise, safety, compliance, and overall risk management.
Specialized Knowledge and Experience
Professional cleaning companies specializing in combustible dust remediation possess a deep understanding of the multifaceted challenges involved:
- Regulatory Expertise: They are well-versed in the nuances of NFPA standards (652, 654, 660, and commodity-specific standards) and OSHA requirements, and how these apply to diverse industrial environments and dust types. This knowledge is crucial for ensuring that cleaning is performed in a compliant manner.
- Hazard Recognition and Assessment: Experienced professionals can effectively identify potential combustible dust hazards, contribute to or interpret Dust Hazard Analyses (DHAs), and understand the specific characteristics and risks associated with different types of dust (e.g., metal dusts vs. organic dusts).
- Methodology for Diverse Environments: They have experience cleaning a wide range of industrial settings, including complex process areas, confined spaces, and hard-to-reach overhead structures (e.g., rafters, ductwork, tops of machinery) where dust accumulation is common and particularly dangerous.
The sum of all requirements—conducting a DHA, understanding specific NFPA codes, selecting and operating certified equipment, implementing detailed procedures for vacuuming, wet cleaning, grounding and bonding, avoiding dust cloud generation, and maintaining comprehensive documentation—creates a level of complexity that is typically beyond the capacity and core competency of non-specialized in-house staff.
Access to Proper Equipment and Technology
Effective and safe combustible dust cleaning requires specialized equipment that many facilities do not own due to cost and specificity:
- Certified Explosion-Proof Vacuums: Professionals invest in and maintain a range of industrial-grade, NRTL-certified explosion-proof and dust-ignition-proof vacuum systems appropriate for different hazardous location classifications and dust types.
- Specialized Tools and Accessories: This includes conductive and non-sparking hoses, wands, nozzles, and brushes designed for combustible dust applications, as well as tools for cleaning intricate or delicate equipment.
- Access Equipment: Professionals are equipped with and trained to use appropriate access equipment, such as aerial lifts, scaffolding, and specialized high-reach vacuum systems (e.g., SpaceVac technology mentioned in ), to safely clean elevated and inaccessible areas.
- Advanced Filtration and Containment: They utilize vacuums with advanced filtration (HEPA, ULPA) to capture even the finest particulates and ensure proper containment and disposal of collected combustible dust, which may be classified as hazardous waste.
Ensuring Safety and Regulatory Compliance
Hiring professionals significantly enhances a facility’s ability to meet safety and compliance obligations:
- Adherence to Safety Protocols: Reputable professional services operate under strict safety protocols, employing trained technicians who understand how to perform hazardous cleaning tasks while minimizing risks to themselves, facility personnel, and the property.
- Meeting Regulatory Mandates: Professionals help facilities comply with OSHA regulations and NFPA standards, thereby reducing the likelihood of citations, fines, operational shutdowns, and potential legal liabilities.
- Documentation Support: Professional cleaning services typically provide documentation of the services performed, which can be incorporated into the facility’s overall compliance records and assist during safety audits.
Risk Mitigation and Liability Reduction
Ultimately, engaging expert combustible dust cleaning services is a crucial risk management strategy:
- Preventing Catastrophic Incidents: The primary benefit is a significant reduction in the likelihood of devastating dust explosions and fires, which can result in fatalities, severe injuries, extensive property damage, and long-term business interruption.
- Transfer of Risk: By outsourcing this highly hazardous task to qualified, insured professionals, a facility transfers a portion of the associated risks and liabilities.
- Identification of Unseen Hazards: Professionals, with their specialized focus, may identify potential dust-related hazards or inadequate control measures that in-house staff, occupied with routine operations, might overlook.
While professional combustible dust cleaning services involve a cost, this should be viewed as an investment in safety, compliance, and business continuity. The potential financial, human, and reputational costs of a combustible dust explosion—as evidenced by numerous industrial incidents —far outweigh the expense of proactive, expert cleaning. The benefits of improved safety, enhanced productivity from a cleaner environment, assurance of compliance, and prolonged equipment life further position professional cleaning as a value-adding service, not merely an operational expense.
Final Thoughts
Combustible dust poses a pervasive and severe threat across a multitude of industries. The potential for catastrophic explosions and fires necessitates a comprehensive and meticulous approach to its management and removal.
This guide has detailed the nature of combustible dust, the scientific principles governing its explosive behavior via the Dust Explosion Pentagon, the critical framework of NFPA standards and OSHA regulations, the foundational importance of a Dust Hazard Analysis (DHA), and the specialized procedures required for safe cleaning.
Key takeaways from this analysis include:
- The Ubiquitous and Deceptive Nature of the Hazard: Many common industrial materials transform into potent explosion hazards when in finely divided dust form. Accumulations often occur in hidden, hard-to-reach areas, creating unacknowledged fuel loads for devastating secondary explosions.
- The Indispensability of a Dust Hazard Analysis (DHA): A facility-specific DHA, conducted by qualified personnel, is not just a regulatory mandate but the essential first step in understanding and mitigating combustible dust risks. Without it, cleaning and control efforts are uninformed and potentially unsafe.
- The Complexity of Safe Cleaning Procedures: Effective combustible dust cleaning demands specialized knowledge and strict adherence to protocols. This includes the correct selection and use of certified explosion-proof vacuum systems, careful consideration of when and how to use wet cleaning methods (and when to avoid them entirely, especially with water-reactive dusts), meticulous grounding and bonding of all equipment to prevent static ignition, and techniques to avoid generating hazardous dust clouds.
- The Criticality of Documentation and Training: Written housekeeping programs, detailed records of cleaning and inspection activities, and comprehensive employee training are integral to a sustainable and compliant dust safety program.
Given the significant risks, the technical complexity of compliant cleaning methods, the specialized equipment required, and the depth of regulatory knowledge needed, it is strongly recommended that facilities engage professional, experienced combustible dust cleaning services.
Such services offer the specialized expertise, certified equipment, and adherence to safety protocols necessary to effectively and safely manage this critical hazard. Investing in professional cleaning is an investment in worker safety, regulatory compliance, asset protection, and overall business continuity. Attempting to manage combustible dust without the requisite expertise and resources is a gamble with potentially catastrophic consequences.