1. High-Pressure Water Jetting: Principles and Power
High-pressure water jetting, encompassing both high-pressure washing and the more intensive hydroblasting, represents a significant advancement in cleaning, surface preparation, and material removal technologies. This section defines these methods, explores the fundamental mechanics of how pressurized water achieves its effects, and delineates the critical pressure ranges that dictate their applications and capabilities.
Defining High-Pressure Washing and Hydroblasting
Hydroblasting, also recognized by terms such as water blasting or hydro-demolition, is an industrial technique that employs highly pressurized water to cleanse, cut through materials, or restore surfaces by dislodging and removing unwanted substances. A defining characteristic of hydroblasting is its reliance solely on the kinetic energy of water impacting a surface to achieve the desired effect. Typically, abrasives are not incorporated into the primary water stream, which offers the advantage of eliminating dust pollution and the challenges associated with the disposal of spent abrasive materials.
Contact us!
It is crucial to distinguish hydroblasting from conventional “power washing.” The primary differentiator is the significantly higher operating pressures involved; hydroblasting systems can generate water pressures up to 30 times greater than those used in power washing. While power washing is often suitable for domestic or light commercial cleaning tasks, industrial hydroblasting operates at an intensity level that allows it to tackle heavy-duty industrial applications.
The terminology in the field can sometimes overlap, with “water jetting” being another commonly used term. For clarity, this guide will use “high-pressure washing” to refer to operations typically up to 5,000 pounds per square inch (psi), as specified in the user query, and “hydroblasting” to encompass the broader spectrum, including both high-pressure and ultra-high-pressure applications. This distinction is vital because the pressure level directly correlates with the method’s capabilities, the types of materials it can remove, and the inherent safety precautions required.
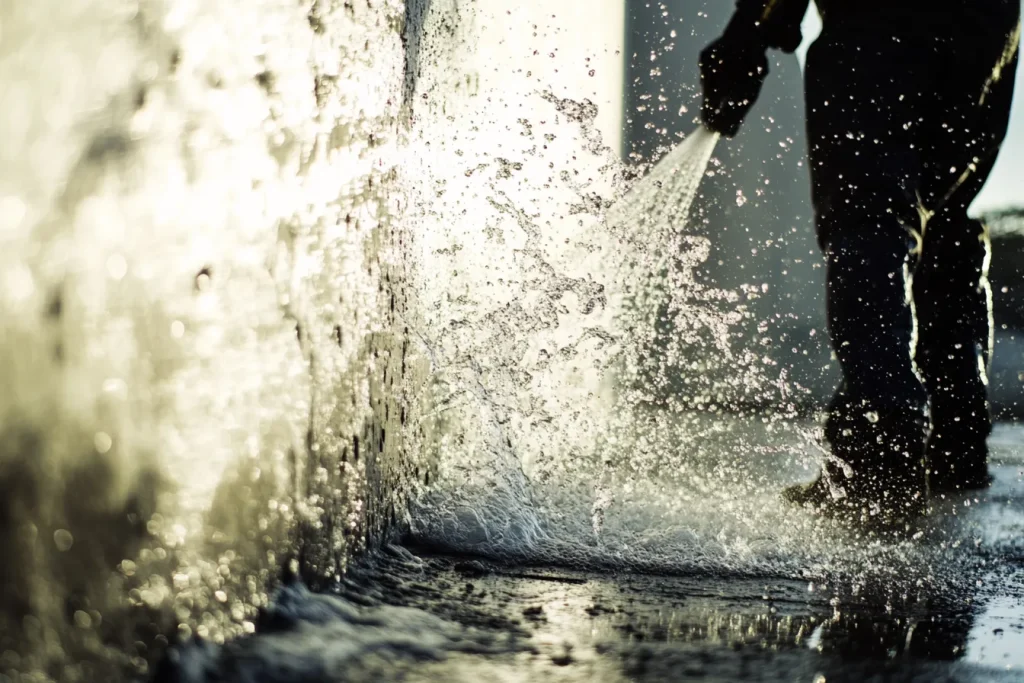
The technological progression from basic power washing to ultra-high-pressure (UHP) hydroblasting signifies a remarkable leap in harnessing water’s intrinsic energy. This evolution has enabled the application of water jetting to tasks that previously depended on methods with greater environmental footprints or higher direct risks, such as extensive chemical usage or abrasive blasting processes that generate significant airborne particulate matter.
The Mechanics of Material Removal: How Water Jets Work
The efficacy of hydroblasting stems from a carefully engineered process. Specialized high-pressure pumps are the core of the system, designed to compress water to extremely high pressures. This highly pressurized water is then channeled through meticulously designed nozzles, which constrict and direct the flow, transforming it into powerful, focused jets.
The capacity of these water jets to clean, cut, or strip materials is a result of several combined physical principles:
- High Pressure: This is the primary source of the impact force. The immense pressure behind the water jet delivers a concentrated blow to the target surface, capable of overcoming the adhesion forces of contaminants or the structural integrity of certain materials.
- High Velocity: As the pressurized water is forced through the narrow orifice of the nozzle, its velocity increases dramatically. This high velocity contributes significantly to the jet’s ability to dislodge stubborn deposits and effectively carry away the removed debris.
- Incompressibility of Water: Water is virtually incompressible. This physical property allows it to transfer the energy imparted by the pump to the target surface with minimal loss, making the process highly efficient in terms of energy transfer.
When this high-pressure, high-velocity water stream impacts a surface, its kinetic energy is unleashed. This energy can be sufficient to cut through robust materials, blast away layers of contaminants, or peel off coatings such as paint or rust. The precise effect achieved—be it gentle cleaning, aggressive stripping, or material cutting—is a function of several controllable variables, including the operating pressure, the specific design of the nozzle (which shapes the jet and its impact pattern), and the standoff distance between the nozzle and the workpiece.
Understanding these mechanics is crucial, as it explains why hydroblasting is so effective across a diverse range of applications. It is not merely “strong water”; rather, it is a sophisticated application of fluid dynamics and energy transfer principles. This foundational knowledge underpins critical operational decisions, such as equipment selection, the adjustment of operating parameters for different tasks, and the implementation of safety protocols.
Understanding Pressure Ranges: High-Pressure vs. Ultra-High Pressure (UHP)
The industrial application of water jetting is broadly categorized by operating pressure. While specific thresholds can vary slightly between different standards or manufacturers, a general consensus exists regarding distinct pressure tiers. These ranges are fundamental to matching the technology to the task at hand.
Pressure Category | Pressure Range (PSI) | Pressure Range (Bar/MPa) | Primary Applications/Characteristics |
---|---|---|---|
Low-Pressure Water Cleaning (LPWC) | < 5,000 | < 340 / < 34 | General industrial and domestic cleaning, light-duty tasks. (User query aligns “high-pressure washing” with this tier) |
High-Pressure Water Cleaning (HPWC) | 5,000 – 10,000 | 340-690 / 34-70 | Removal of marine growth, more demanding cleaning tasks. |
High-Pressure Hydroblasting (HPWJ) | 10,000 – 25,000 (or up to 30,000) | 690-1,700 / 70-170 (or up to 210) | Removal of coatings, rust, scale; heavy-duty cleaning. |
Ultra-High Pressure Hydroblasting (UHPWJ) | > 25,000 (or > 30,000) to > 40,000+ | > 1,700 (or > 210) to > 2,758+ | Complete removal of tenacious coatings and rust, concrete demolition, cutting tough materials. |
Note: Pressure conversions are approximate. Some sources may present slightly varied delineations for these categories.
The WaterJet Technology Association (WJTA), a key industry body, has established a practical color-coding scheme for high-pressure hoses, which aids in visually identifying the maximum working pressure rating of a hose. This scheme ranges from Yellow for 10,000 psi hoses up to Red for 55,000 psi hoses, providing an immediate visual cue for operators regarding equipment capabilities and safety limits.
It is important to recognize that while pressure is a primary classification metric, the optimal execution of a task—be it cleaning, stripping, or cutting—is more subtly dictated by a nuanced interplay of pressure, water flow rate, and nozzle technology. Achieving the desired outcome without damaging the substrate, wasting energy, or compromising safety necessitates a higher level of operator skill and system understanding than is required for simpler cleaning methods.
The choice between high-pressure and ultra-high-pressure systems is contingent upon the specific job requirements; simply increasing pressure is not always the optimal solution. The objective is to find the correct balance of pressure and flow rate tailored to each unique task.
While the pressure range definitions are generally consistent across industry sources, minor variations do exist. This underscores the importance of specifying actual operating pressures for a given task rather than relying solely on descriptive terms like “high pressure” or “ultra-high pressure.” The WJTA hose color codes, for instance, are an important safety standard for hoses but do not strictly define the operational process categories themselves.
2. Key Applications of Hydroblasting Technology
Hydroblasting technology’s versatility and power lend it to a wide array of demanding applications across numerous industries. Its capabilities span from meticulous surface preparation to aggressive material removal and comprehensive industrial cleaning.
Surface Preparation Excellence
The quality of surface preparation is paramount for the adhesion and long-term performance of protective coatings. Hydroblasting has emerged as a highly effective method for achieving various industry-recognized cleanliness standards.
- Achieving Industry Standards: Hydroblasting can prepare surfaces to standards comparable to those established by organizations like ISO (International Organization for Standardization) and SSPC (The Society for Protective Coatings). For instance, hydroblasted surfaces can achieve cleanliness levels equivalent to ISO 8501-1:1988 Sa2 (Thorough Blast Cleaning) and Sa2.5 (Very Thorough Blast Cleaning), or SSPC-SP6 (Commercial Blast Cleaning) and SSPC-SP10 (Near-White Blast Cleaning). Specific to hydroblasting, standards such as HB2 (Thorough Hydroblast Cleaning) and HB2.5 (Very Thorough Hydroblast Cleaning) are defined. The NACE No. 5 / SSPC-SP12 standard specifically addresses waterjetting, with WJ-1 designating a “white metal” finish, indicating a surface free of all visible contaminants. It is important to note that ISO and SSPC-NACE use distinct nomenclature for visual cleanliness levels achieved by water jetting to emphasize that these methods differ fundamentally from abrasive blasting techniques.
- HB2 Thorough Hydroblast Cleaning: When viewed without magnification, the surface must be free from visible oil, grease, dirt, most loosely adhering mill scale, rust, paint coatings, and other foreign matter. Any residual contamination should be firmly adherent. A brown-black discoloration of ferric oxide may remain as a tightly adherent thin film on previously corroded or pitted steel.
- HB2. Very Thorough Hydroblast Cleaning: When viewed without magnification, the surface must be free from all visible oil, grease, dirt, dust, mill scale, rust, paint coatings, oxides, corrosion products, and other foreign matter, except for light shadows, slight streaks, or minor discolorations caused by rust stains, mill scale stains, or previous paint coatings. A brown-black discoloration of ferric oxide may remain as a tightly adherent thin film on previously corroded or pitted steel. A significant advantage of water jetting is its unique ability to meet the SC-2 standard for the removal of soluble salts, such as chlorides, sulfates, and nitrates. These invisible contaminants, if left on the surface, can draw moisture through a coating, leading to osmotic blistering and premature coating failure. Traditional dry abrasive blasting can sometimes trap or embed these salts into the surface profile, making their removal difficult. Hydroblasting, by contrast, effectively flushes these salts from the surface. This capability is particularly critical in marine environments or industrial settings where salt contamination is prevalent, directly impacting the longevity of protective coatings and the underlying structural integrity.
- Managing Flash Rusting: Following hydroblasting on steel surfaces, a phenomenon known as “flash rust” can occur as the surface dries. This is a thin layer of rust that forms rapidly. It is typically graded into three levels :
- L: Light Flash Rusting: Characterized by small quantities of light tan-brown rust that partially discolor the original metallic surface. This discoloration may be evenly distributed or appear in patches but is tightly adherent and not heavy enough to easily mark objects brushed against it. This type of flash rust is often referred to as “good rust” and is generally considered acceptable for the application of many industrial coatings by paint manufacturers.
- M: Moderate Flash Rusting: Small quantities of light tan-brown rust will obscure the original metallic surface. This layer may be evenly distributed or patchy and will be heavy enough to mark objects brushed against it.
- H: Heavy Flash Rusting: A heavy layer of dark tan-brown rust will completely obscure the original metallic surface. This layer of rust is loosely adherent and will easily mark objects brushed against it. The formation of “bad rust,” identifiable by a blackish, spotty appearance, is not acceptable for coating. To prevent or control flash rusting, inhibitors can be introduced into the final rinse water, or a passivating agent like sodium nitrite can be added to the hydroblasting water itself.
- Impact on Existing Surface Profiles: A crucial aspect of hydroblasting (HPWJ/UHPWJ) is its effect on the substrate’s surface profile. Unlike abrasive blasting, water jetting does not typically create a new roughness profile on a metallic surface. Instead, it cleans and reveals the existing profile, potentially causing a slight rounding of sharp peaks. Consequently, hydroblasting is predominantly used for maintenance and refurbishment projects where a suitable surface profile, often created by original abrasive blasting during new construction, is already present. The high-velocity water jets penetrate into the pores and crevices of the existing profile, effectively flushing out contaminants such as oil, grease, and entrapped solids, thereby restoring the original cleanliness and texture of the profile.
The following table summarizes common hydroblasting surface cleanliness and flash rust standards:
Table 2: Hydroblasting Surface Cleanliness and Flash Rust Standards
Standard | Description of Achieved Cleanliness / Rust Grade | Key Characteristics | Comparable Abrasive Blasting Standard (if applicable) |
---|---|---|---|
HB2 | Surface free from visible oil, grease, dirt, paint, foreign matter, and most rust. Remaining contamination firmly adherent. Brown-black ferric oxide discoloration may remain. | Thorough cleaning, suitable for many industrial coating applications. | SSPC-SP6 / NACE No. 3 / Sa2 |
HB2.5 | Surface free from visible oil, grease, dirt, loose rust, paint, foreign matter, except for staining. Brown-black ferric oxide discoloration may remain. | Very thorough cleaning, for high-performance coating systems or critical service environments. | SSPC-SP10 / NACE No. 2 / Sa2.5 |
WJ-1 | Surface shall be free of all previously existing visible rust, coatings, mill scale, and foreign matter and have a matte metal finish. | Highest level of waterjet cleaning, “white metal” finish. | SSPC-SP5 / NACE No. 1 / Sa3 (conceptually) |
L | Light Flash Rusting: Small quantities of light tan-brown rust partially discoloring the surface. | Tightly adherent, does not easily mark objects. Often acceptable for recoating (“good rust”). | N/A |
M | Moderate Flash Rusting: Light tan-brown rust obscuring the surface. | Heavy enough to mark objects brushed against it. May require consultation with coating manufacturer. | N/A |
H | Heavy Flash Rusting: Heavy layer of dark tan-brown rust completely obscuring the surface. | Loosely adherent, easily marks objects. Generally not acceptable for recoating without further treatment. | N/A |
Material Removal: Tackling Tough Deposits
Hydroblasting is exceptionally proficient at removing a wide variety of stubborn materials and deposits from numerous surfaces.
- Paint and Coating Stripping: This is a cornerstone application. UHP water blasting, typically operating at pressures between 20,000 and 40,000 psi, is highly effective for removing diverse coatings, including resilient industrial paints (such as lead-based paints), epoxies, polyurea, and other protective layers. It can be applied to surfaces like metal, concrete, asphalt, plastic, and ship hulls. Depending on the pressure applied and nozzle configuration, hydroblasting can achieve selective layer-by-layer removal or complete stripping down to the bare substrate. The removal mechanism can be characterized as erosion, where smaller pressurized streams chip away at high-performance coatings, or delamination, where the water jet gets beneath the coating and lifts it off.
- Rust and Scale Abatement: Hydroblasting efficiently removes rust, mill scale, and other corrosion products from metal surfaces, restoring them to a clean condition. UHPWJ, generally at pressures above 30,000 psi, is particularly suited for thorough rust removal.
- Concrete Demolition and Removal (Hydrodemolition): High-pressure water, in a process known as hydrodemolition (or hydrodem), offers a sophisticated method for selectively removing concrete. This technique can precisely remove damaged or unwanted concrete sections without causing harm to embedded steel reinforcement (rebar) or the underlying sound structure. Hydrodemolition is significantly faster than traditional methods like jackhammering (reportedly up to 25 times faster) and provides numerous advantages, including the reduction of microfracturing in the remaining concrete, diminished noise levels, and the elimination of hazardous silica dust. Furthermore, the process creates a highly textured surface that offers an excellent bond for new concrete overlays. Nominal pressures for hydrodemolition are often around 20,000 psi, though this can be adjusted based on the concrete strength and desired removal depth. This method is also effective for removing road markings, such as white lines, from asphalt or concrete pavements without damaging the road surface itself. The evolution of hydrodemolition reflects a broader trend towards more precise, less damaging, and safer techniques for infrastructure repair and maintenance. It directly addresses the significant drawbacks of conventional mechanical methods, such as inducing micro-cracks, damaging rebar, and generating excessive dust, noise, and vibration. By offering a more “surgical” approach to concrete removal, hydrodemolition contributes to higher quality, more durable repairs and significantly improves worker safety, which is particularly crucial for extending the lifespan of aging infrastructure.
- Resin and Polymer Removal: The intense energy of UHP water jets can effectively cut through and remove tenacious deposits such as polystyrene, acrylic resins, hardened coke, vulcanized rubber, tenacious boiling scale, and various copolymers. This is particularly valuable for cleaning the interiors of industrial tanks, vessels, and reactors where such materials accumulate.
- Other Tough Deposits: Hydroblasting’s capabilities extend to the removal of other challenging substances, including flooring mastics, aged epoxies, thin-set mortars , and various other stubborn accumulations that resist conventional cleaning methods.
While hydroblasting is frequently promoted as being “damage-free” to the underlying substrate , this claim requires careful contextualization. It is true that, when correctly applied, hydroblasting can preserve existing surface profiles and can be precisely controlled for cleaning delicate surfaces. However, the potential for damage exists if the process is misapplied. Incorrect parameters—such as excessive pressure for the substrate, an inappropriate nozzle type, or an incorrect standoff distance or dwell time—can lead to undesirable outcomes.
For instance, on softer materials, erosion can occur, or in concrete removal, the depth of cut per pass can become too great if the nozzles move too slowly or are too close to the surface. Similarly, uncontrolled pressure during the cleaning of heat exchanger tubes could potentially weaken them. This underscores that the “damage-free” attribute is contingent upon the skill and expertise of the operator and the correct calibration of the equipment for the specific task and substrate.
Industrial Cleaning: Restoring Efficiency and Integrity
Hydroblasting is a cornerstone of industrial cleaning, employed to maintain operational efficiency, ensure safety, and preserve the structural integrity of critical equipment and infrastructure across a multitude of sectors.
- Heat Exchangers: Cleaning heat exchangers is a vital application, addressing both the tube-side (internal) and shell-side (external) surfaces. Over time, fouling, scaling, and other deposits accumulate on heat transfer surfaces, significantly impairing thermal efficiency and potentially leading to equipment failure. Hydroblasting removes these deposits, restoring heat transfer rates. The process can be manual, but automated systems are increasingly common. These include flexible lances for navigating U-tubes and curved tubes, and rigid lances for straight tubes, often deployed in multi-lance systems for enhanced speed. Pressures for tube cleaning can reach up to 40,000 psi , while shell-side cleaning may utilize pressures up to 20,000 psi.
- Boilers: Hydroblasting is used extensively for cleaning the internal surfaces of boiler tubes, removing scale, soot, and other combustion by-products that reduce efficiency and can lead to tube overheating and failure. For boiler cleaning, sodium nitrite is sometimes added to the hydroblasting water to act as a passivating agent, preventing flash rust on the cleaned steel surfaces. Advanced systems may incorporate wastewater recycling units to conserve water and reduce the amount of sodium nitrite consumed. The technique is applicable for both internal and external tube cleaning in various boiler designs.
- Pipes and Pipelines: This technology is highly effective for clearing blockages and removing accumulated deposits from industrial piping systems. It can tackle grease, oil, sludge, scale, hard deposits like coke and plastic, and viscous substances such as tar. Specialized rotating hose systems, equipped with advanced nozzle designs, can achieve 100% cleaning of the internal diameter of pipes, even navigating multiple bends. Sewer jetting, a specific form of hydroblasting, is used to maintain municipal and industrial sewer lines.
- Tanks and Vessels: Hydroblasting provides a robust solution for cleaning the interior and exterior surfaces of storage tanks, process vessels, reactors, and other containers. It effectively removes a wide range of residues, including polystyrene, acrylic resins, coke, rubber, and scale. A significant advancement in this area is the use of 3-D nozzle systems and other robotic tools. These automated systems allow for thorough cleaning of tank interiors without requiring hazardous confined space entry by personnel.
- Ship Hulls: A critical application in the maritime industry, hydroblasting is used for removing marine biofouling—such as algae, barnacles, and other marine growths—as well as old paint and rust from ship hulls. This cleaning process is essential for maintaining a ship’s hydrodynamic efficiency, reducing fuel consumption, and preparing the hull surface for the application of new anti-fouling coatings. UHP hydroblasting, with pressures reaching up to 3,000 bar (approximately 43,500 psi), is commonly employed for these tasks. The work can be performed both above and below the waterline, and increasingly, automated or robotic systems are utilized to improve efficiency and safety.
- Specialized Equipment and Infrastructure: Beyond these core applications, hydroblasting is used for a variety of specialized cleaning tasks. These include the removal of rubber deposits from airport runways , general cleaning of heavy industrial equipment and machinery , and in architectural restoration projects for cleaning delicate facades or removing unwanted coatings.
3. Hydroblasting Equipment: Tools of the Trade
The effectiveness, efficiency, and safety of hydroblasting operations are intrinsically linked to the specialized equipment employed. This typically comprises high-pressure pumps, a variety of nozzles tailored to specific tasks, delivery systems like lances and hoses, and increasingly, sophisticated automated and robotic tools.
High-Pressure Pumps: The Power Source
The pump is the heart of any hydroblasting system, responsible for generating the immense water pressures required for demanding cleaning and material removal tasks.
- Plunger Pumps (Positive Displacement Pumps): These are the most common type of pumps used in hydroblasting. They operate on a positive displacement principle, utilizing pistons or plungers moving within cylinders to draw in water at low pressure and expel it at very high pressure. Manufacturers like KAMAT are known for their high-pressure plunger pumps. Systems may incorporate pumps with three to five cylinders to achieve consistent high-pressure output.
- Intensifier Pumps: While less common for general hydroblasting, intensifier pumps are used in specialized applications requiring extremely high pressures, such as waterjet cutting of hard materials like rock, where pressures of 37,000 psi and above may be needed. Pump units can be powered by diesel engines or electric motors, offering flexibility for different operational environments. The power output of these pumps varies significantly, with some large units exceeding 2,500 horsepower (hp) and capable of delivering substantial flow rates, sometimes up to 1,200 gallons per minute (GPM) or more. For particularly demanding, high-volume hydroblasting projects, very large, often trailer-mounted pump units, sometimes referred to as “Big Pumps,” are utilized. The selection of pump type and capacity is critical and depends entirely on the pressure and flow rate requirements of the specific application.
Nozzles: Precision and Impact
Nozzles are critical components that convert the high-pressure water flow from the pump into a precisely shaped, high-velocity jet, which performs the work on the target surface. The design and selection of the nozzle profoundly affect the spray pattern, impact force, cleaning efficiency, and water consumption.
The evolution of nozzle technology, from simple straight-bore designs to complex rotating 3D or ultra-durable sapphire UHP nozzles, has been a primary catalyst in expanding the range of applications and improving the efficiency of hydroblasting. These specialized nozzles enable tasks that would be either impossible or highly inefficient with more basic designs, underscoring that the nozzle is not merely an outlet but a critical tool for tailoring the water jet’s energy to specific requirements.
- Types of Nozzles:
- Straight Bore / Pencil Jet Nozzles: These nozzles produce a very tight, concentrated stream of water, delivering maximum impact force over a small area. They are ideal for spot blasting, precision cutting, or removing very stubborn, localized deposits.
- Fan Jet / Flat Fan Nozzles: These create a wider, flat spray pattern, distributing the impact force over a larger area. They are suitable for cleaning broader surfaces where a sweeping action is effective and high impact is still required.
- Venturi Bore Nozzles (e.g., Long Venturi, Double Venturi): These nozzles feature a converging inlet and a diverging outlet. This design accelerates the water jet (or an abrasive slurry, if used), increasing its velocity and creating a wider, more effective blast pattern for cleaning large surfaces, thereby improving productivity.
- Rotating Nozzles (e.g., Warthog®, RHD systems): These nozzles spin rapidly, often driven by the water flow itself or by an external power source like an air drill. The rotating jets provide 360-degree coverage, making them highly effective for cleaning the internal surfaces of pipes, tubes, tanks, and for general surface preparation.
- Multi-Orifice Nozzles / 3-D Nozzles: Commonly used in automated tank cleaning systems, these nozzles have multiple orifices arranged to project water jets in various directions. This allows the cleaning head to reach into corners, behind obstructions, and cover all internal surfaces of a tank or vessel without manual intervention.
- Specialized Nozzles: The industry has developed numerous specialized nozzles for specific challenges. These include erosion-based nozzles that convert the main water stream into multiple smaller, highly pressurized streams for removing tough coatings, and delamination-based nozzles designed to get under and lift coatings. For pipe cleaning, chisel point nozzles are designed to break through hard blockages, while heavy, weighted culvert nozzles are used to stay at the bottom of large diameter pipes and effectively clear thick debris. Due to the extreme pressures and abrasive nature of some contaminants, nozzles for UHP applications are often made from highly durable materials like sapphire or tungsten carbide to resist wear and maintain performance.
- Selection Criteria for Nozzles:
- Application: The primary task (cleaning, cutting, stripping) and the geometry of the workpiece (e.g., flat surface, internal pipe diameter) are key determinants.
- Pressure and Flow Rate (GPM): Each nozzle is designed to operate optimally and safely within specific pressure and flow rate ranges. Exceeding these can damage the nozzle or lead to inefficient operation. The pressure drop (ΔP) across the nozzle directly influences the flow rate.
- Material: The nozzle material (e.g., stainless steel, hardened steel, tungsten carbide, sapphire, ceramic) is selected based on the operating pressure, potential for chemical corrosion or abrasion from contaminants, operating temperature, and cost.
- Desired Blast Pattern and Coverage: The shape of the nozzle’s bore and its exit angle determine the spray pattern (e.g., solid stream, flat fan, conical) and the coverage area at a given standoff distance.
- Droplet Size: While less critical for most hydroblasting, in some specialized applications like gas cooling or scrubbing, the size of the water droplets generated by the nozzle can be an important factor.
The following table provides an overview of key hydroblasting nozzle types and their common applications:
Table 3: Key Hydroblasting Nozzle Types and Applications
Nozzle Type | Typical Blast Pattern | Primary Applications | Key Characteristics/Advantages | Typical Pressure Range Suitability |
---|---|---|---|---|
Straight / Pencil Jet | Tight, concentrated solid stream | Spot cleaning, cutting, removing very hard deposits, weld seam preparation | Maximum impact force, longest throw. | High to UHP |
Fan Jet / Flat Fan | Flat, fan-shaped spray | Cleaning large flat surfaces, paint stripping, general washing | Good surface coverage, moderate to high impact. | Low to UHP |
Rotating Nozzles | 360-degree spinning jets (single or multiple orifices) | Pipe and tube cleaning (ID), tank cleaning, surface preparation, concrete demolition | Excellent coverage in enclosed spaces, effective for removing varied deposits. | High to UHP |
3-D / Multi-Orifice | Multiple jets in various directions, often on a rotating head | Automated tank and vessel cleaning (ID) | Comprehensive internal coverage without manual entry, reaches difficult areas. | High to UHP |
Venturi Bore | Wide, accelerated blast pattern | Large surface area cleaning and preparation, abrasive blasting (if media is added) | Increased productivity, wider pattern, can increase abrasive/water velocity. | High to UHP |
Specialized (e.g., Chisel, Culvert) | Varied, task-specific (e.g., forward-focused, weighted) | Clearing hard blockages in pipes (chisel), cleaning large diameter culverts (culvert) | Designed for specific challenging conditions and debris types. | Medium to High |
Lances, Guns, and Hoses: Delivery and Control
These components are responsible for safely and effectively conveying the high-pressure water from the pump to the nozzle and allowing the operator to direct the jet.
- Hoses: High-pressure hoses are specially constructed to withstand the extreme pressures of hydroblasting. They must be rated for the maximum allowable working pressure (MAWP) of the system. The WJTA recommends a color-coding system for hoses to visually indicate their pressure rating, enhancing safety on site. Hoses are considered consumable items and have a finite service life; industry recommendations suggest a life limit (e.g., four years or a certain number of pressure cycles) to prevent failures. Protective abrasive covers are often used to shield hoses from external damage and wear.
- Lances: Lances are rigid or flexible tubes that extend from the control gun or automated tool to the nozzle, allowing the operator to direct the water jet. Rigid lances are used for cleaning straight pipes or easily accessible surfaces. Flexible lances are essential for cleaning the inside of curved tubes, such as those found in U-tube heat exchangers, or for navigating complex pipework. The length of the lance is also a safety consideration; a minimum length (e.g., 36 inches) is often recommended for manual operations to prevent the operator from inadvertently pointing the nozzle at themselves.
- Guns: For manual hydroblasting, operators use high-pressure guns, often referred to as “shotgun” tools. These devices have a trigger mechanism that allows the operator to start and stop the flow of high-pressure water to the nozzle. It is a critical safety requirement that these guns be equipped with “dead-man” switches or other automatic shut-off devices that immediately stop the water flow if the operator loses control or releases the trigger.
- Fittings and Adapters: A variety of specialized fittings and adapters are used to connect hoses to pumps, lances to guns, and nozzles to lances. These components must be made from high-strength materials, designed for UHP service, and ensure leak-free connections to maintain system pressure and prevent hazardous spray.
- Accessories: Various accessories enhance the functionality and safety of hydroblasting operations. These include “tiger tails” (flexible hose protectors that guide hoses around sharp bends), venturi jet pumps (for dewatering), and skids or centralizers that position nozzles correctly within pipes for optimal cleaning.
The integrity and correct selection of these delivery components are paramount for both operator safety and the overall performance of the hydroblasting system. There is an implicit “system” approach to hydroblasting equipment; the pump, hose, lance, and nozzle must be correctly matched not only for pressure rating but also for flow dynamics to achieve optimal performance and safety. A mismatch, such as using an undersized hose with a high-capacity pump or an incorrectly sized nozzle, can lead to significant inefficiencies, premature wear of components, pressure losses, or even dangerous failures like hose bursts or uncontrolled jetting. Regular inspection and maintenance of hoses and connections are key safety practices.
Automated and Robotic Systems: Enhancing Safety and Efficiency
A significant trend in the hydroblasting industry is the increasing adoption of automated and robotic systems. These technologies are driven by the dual imperatives of enhancing operator safety—by removing personnel from potentially hazardous zones—and improving productivity and the consistency of cleaning quality.
- Applications for Automation:
- Tube Cleaning (Heat Exchangers): Automated Tube Cleaning (ATC) systems are widely used. These often feature multiple flexible or rigid lances mounted on a positioning device, which are remotely operated to clean the internal surfaces of heat exchanger tubes.
- Shell-Side Cleaning (Heat Exchangers): Systems like the ATL-5000 allow operators to clean the exterior of tube bundles from a safe, remote location, often a climate-controlled cabin.
- Tank and Vessel Cleaning: Robotic arms equipped with 3-D rotating nozzle systems can be inserted into tanks and vessels, eliminating the need for dangerous confined space entry by humans.
- Pipe Cleaning: Automated rotating hose systems (e.g., RHD systems) can be fed into long pipelines to provide thorough internal cleaning, navigating bends and complex geometries.
- Surface Preparation and Ship Hull Cleaning: Robotic crawlers or articulated arms fitted with hydroblasting heads can traverse large vertical, horizontal, or overhead surfaces for paint stripping and cleaning.
- Concrete Removal (Hydrodemolition): Specialized hydrodemolition robots are used for precise and efficient concrete removal on bridges, parking garages, and other structures.
- Features of Automated Systems: These systems often incorporate advanced features such as remote operation consoles, computerized control of movement and jetting parameters, integrated sensors and cameras for navigation and real-time inspection, and sometimes vacuum systems for simultaneous collection of removed debris and wastewater.
The push towards automation is not solely about improving efficiency; it is fundamentally linked to mitigating the extreme safety hazards inherent in manual high-pressure and ultra-high-pressure operations. As operating pressures continue to rise and the demand for cleaning in hazardous environments (like confined spaces) persists, automation transitions from being a beneficial option to a near necessity.
These systems can operate continuously for extended periods, often performing tasks that would be physically impossible or unacceptably dangerous for human operators. Consequently, future growth in UHP hydroblasting applications will likely be heavily reliant on continued advancements in robotic and automated tool technology.
4. Safety in High-Pressure Operations: A Non-Negotiable Priority
The immense power harnessed in high-pressure washing and hydroblasting operations necessitates an unwavering commitment to safety. The potential for severe injury or fatality is significant if proper procedures are not meticulously followed. This section details the primary hazards, essential personal protective equipment (PPE), industry best practices (with a focus on WJTA guidelines), work area setup, and emergency protocols.
Identifying Key Hazards
A thorough understanding of the potential dangers is the first step toward mitigating them. The high-energy nature of hydroblasting means that even momentary lapses in concentration or procedure can have catastrophic consequences.
- High-Pressure Water Injection/Lacerations: This is the most significant and characteristic hazard of hydroblasting. The water jet, propelled at extreme velocities, can easily puncture skin, standard work boots, gloves, and even specialized protective clothing in a fraction of a second. Such an injection can drive water and contaminants (debris, bacteria, chemicals from the cleaned surface) deep into body tissues, leading to severe internal damage, aggressive infections that can be difficult to treat, compartment syndrome, and potentially requiring amputation or causing fatality. Even an injury that appears minor on the surface, like a small puncture, can mask extensive subcutaneous damage. The extreme potential for severe injury from high-pressure water injection is the single most defining hazard of hydroblasting, fundamentally shaping all other safety protocols, PPE requirements, and the significant industry shift towards automation.
- Flying Debris: Material dislodged from the surface being cleaned (e.g., paint chips, rust scale, concrete fragments) can be ejected at high velocity, becoming dangerous projectiles that can cause impact injuries or eye damage.
- Slips, Trips, and Falls: The work environment in hydroblasting is often wet, and hoses can create tripping hazards. Water and removed debris can make surfaces slippery, increasing the risk of falls, especially when working at heights or on uneven surfaces.
- Noise Exposure: Hydroblasting equipment, particularly the pumps and nozzles, can generate extremely high noise levels, often exceeding 100 decibels (dBA). Prolonged exposure to such noise without adequate hearing protection can lead to temporary or permanent hearing loss.
- Hose Failure/Whipping Hoses: High-pressure hoses are subjected to immense stress. If a hose fails (bursts) or a connection becomes loose or separates under pressure, the hose can whip around violently with tremendous force, capable of causing severe impact injuries to anyone nearby.
- Electric Shock: If electrically powered hydroblasting units are used, there is a risk of electric shock, particularly in wet environments, if equipment is not properly grounded or if electrical components are damaged.
- Confined Space Hazards: Many hydroblasting tasks, such as cleaning tanks, vessels, or large pipes, involve working in confined spaces. These environments present multiple hazards, including the potential for oxygen-deficient or toxic atmospheres (from contaminants being cleaned or from equipment exhaust if not properly ventilated), limited means of entry and egress, and difficulties in rescue operations.
- Operator Fatigue: Manually operating hydroblasting equipment, especially high-pressure lances or “shotguns,” can be physically demanding due to the reactive back thrust from the nozzle and the need to maintain control. Prolonged operation can lead to fatigue, which can impair judgment and increase the risk of accidents.
- Chemical Hazards: Although hydroblasting primarily uses water, chemical hazards can arise if the surfaces being cleaned are contaminated with hazardous chemicals, or in rare instances where chemical additives are used in the water stream. Exposure can occur through skin contact, inhalation of vapors, or injection.
- Back Thrust: The nozzle emits water at high velocity, creating a reactive force known as back thrust, which the operator must counteract. This force can be substantial, particularly at higher pressures and flow rates, stressing the operator and potentially leading to loss of control if not properly managed. Operators should typically not be required to withstand a back thrust exceeding one-third of their body weight.
Personal Protective Equipment (PPE): Essential Gear for Operators
Given the severe hazards, appropriate and specialized PPE is non-negotiable for all personnel involved in hydroblasting operations. The specific PPE required will vary depending on the operating pressure, the nature of the application, and the findings of a job-specific risk assessment. Standard work clothing offers virtually no protection against high-pressure water jets.
Table 4: Recommended Personal Protective Equipment (PPE) for Hydroblasting Operations
Body Part Protected | Type of PPE | Key Specifications/Materials | Rationale/Hazards Addressed |
---|---|---|---|
Full Body | Waterproof, impact-resistant suit/apron | Neoprene-coated nylon, multi-layer waterjetting-approved fabric. Kevlar® or equivalent ballistic material suits often required for pressures >5,000 psi. | Protection against high-pressure water jet injection, lacerations, flying debris, chemical splash (if applicable), and wet conditions. |
Head | Hard Hat | ANSI-compliant industrial safety helmet. | Protection from falling objects and impact hazards. |
Eyes/Face | Full Face Shield (worn over primary eye protection) | Impact-resistant polycarbonate or similar material, ANSI Z87.1 compliant. | Protection for the entire face from direct jet impact, splash, and high-velocity debris. |
Eyes | Safety Glasses or Goggles (worn under face shield) | ANSI Z87.1 compliant, impact-resistant, with side shields (for glasses) or fully sealed (for goggles). | Primary eye protection from particles and splash that may get under a face shield. |
Hands | Waterproof, heavy-duty, impact/cut-resistant gloves | Neoprene, rubber, PVC, or specialized waterjet-resistant materials. Reinforced palms and fingers. | Protection against water injection (limited), cuts, abrasions, chemical contact, and maintaining grip in wet conditions. |
Feet | Steel-toed, metatarsal-guard, waterproof, non-slip safety boots | ANSI Z41 compliant, often made of rubber or specialized waterjet-resistant materials. Kevlar® or similar puncture-resistant layers. | Protection against water injection, impact from dropped objects, crushing hazards, punctures, and slips on wet surfaces. |
Hearing | Earplugs or Earmuffs | Appropriate Noise Reduction Rating (NRR) for noise levels exceeding 85 dBA. | Prevention of noise-induced hearing loss from loud equipment operation. |
Respiratory | Respirator (type dependent on contaminants) | NIOSH-approved, selected based on risk assessment (e.g., for dusts, mists, vapors, oxygen deficiency in confined spaces). | Protection from inhalation of airborne contaminants, hazardous dusts (e.g., lead, silica), or chemical vapors. |
Hose Protection | Hose Shroud | Durable, flexible material covering hose-to-tool connections frequently handled by the operator. | Provides an additional barrier of protection in case of a leak or failure at the connection point closest to the operator. |
All PPE must be maintained in good condition, fit the operator correctly, and operators must receive comprehensive training on its proper use, care, limitations, and inspection procedures.
WJTA (WaterJet Technology Association) Safety Guidelines and Best Practices
The WaterJet Technology Association (WJTA) is a leading authority in promoting safety within the waterjetting industry. The WJTA publishes “Recommended Practices for the Use of High Pressure Waterjetting Equipment,” which serves as a crucial safety manual, and offers training and certification programs for hydroblaster operators. Adherence to these guidelines is considered industry best practice and is vital for minimizing the inherent risks of hydroblasting. WJTA certification is often regarded as the gold standard for professional hydroblaster training.
Key recommendations synthesized from WJTA principles and related safety documents include :
- Operator Training and Certification: Only personnel who have received thorough training and, where applicable, certification should be permitted to operate, maintain, or repair hydroblasting equipment. Training must cover equipment operation, recognition and control of hazards, correct PPE use, emergency procedures, and lockout/tagout protocols. Regular refresher training is essential to keep skills current and reinforce safety awareness.
- Job-Specific Risk Assessment: Before any hydroblasting work commences, a comprehensive risk assessment specific to the job, location, materials being cleaned, and equipment being used must be conducted. This assessment should be documented and reviewed if conditions change.
- Equipment Inspection and Maintenance: All components of the hydroblasting system—including pumps, hoses, nozzles, lances, guns, fittings, and safety devices—must be regularly inspected for wear, damage, or improper assembly before each use. Damaged or suspect equipment must be immediately removed from service and repaired or replaced by qualified personnel. The Maximum Allowable Working Pressure (MAWP) specified for any component in the system must never be exceeded.
- Safe Operating Procedures:
- The high-pressure water jet must never be directed at any person, and no part of the body should ever be placed in front of the nozzle, even if protective gear is worn.
- Control guns must be equipped with “dead-man” switches or similar automatic shut-off devices that stop the water flow if the operator loses control or releases the trigger. These safety devices must never be bypassed, tied down, or otherwise defeated.
- All high-pressure connections must be securely tightened and confirmed to be leak-free before pressurizing the system and during operation.
- The system must be completely de-energized (pump shut off, pressure bled from the lines) and appropriate lockout/tagout procedures implemented before performing any maintenance, changing nozzles, or attempting to tighten or open any part of the high-pressure system.
- Whip checks (safety cables or straps) must be used on all high-pressure hose connections to restrain a hose in the event of a coupling failure.
- Hoses should be handled carefully, protected from sharp edges or kinking, and routed to minimize tripping hazards. Pressurized hoses should not be handled within one foot of connections.
- For manual operations, teams should rotate duties to minimize operator fatigue, especially when dealing with significant back thrust.
- Sufficient trained personnel must be assigned to safely execute the work.
- Hygiene: Operators are advised to wash thoroughly after all waterjetting operations to remove any residue which may contain traces of harmful substances.
Effective hydroblasting safety is not solely dependent on equipment or PPE; it relies heavily on a robust safety culture within the organization, continuous and effective training, and unwavering operator vigilance. Fatigue and complacency, particularly during repetitive or long-duration manual operations, represent significant hidden risks that must be actively managed.
Work Area Setup and Control
Properly establishing and controlling the work area is essential to protect both operators and other personnel in the vicinity.
- The immediate work area must be clearly demarcated and barricaded to prevent entry by untrained or unauthorized individuals. A minimum distance of 15 feet is often recommended for barricades.
- Prominent warning signs, such as “DANGER – HIGH-PRESSURE WATER CLEANING,” must be posted at the perimeter of the work zone and along any high-pressure hoses that extend outside the barricaded area.
- The work area should be kept clear of unnecessary objects, tools, and debris to ensure good footing and visibility for the operators.
- If hydroblasting is performed at an elevated position (e.g., on ladders or scaffolding), appropriate fall protection measures, such as safety harnesses and lanyards tied off to secure anchor points, or guardrails, must be used.
- For operations within confined spaces, a permit-required confined space entry program must be strictly followed. This includes pre-entry atmospheric testing, continuous monitoring, adequate ventilation, a designated attendant stationed outside the space, and established rescue procedures.
While automation significantly enhances safety by removing the operator from the immediate hazard zone of the high-pressure jet , it introduces a different set of safety considerations. These pertain to the operation and maintenance of robotic systems, potential for unexpected movements, software or control system failures, and the complexities of interacting with powerful automated machinery.
As automated hydroblasting systems become more prevalent, specific safety guidelines addressing these unique robotic aspects will become increasingly important, supplementing the existing guidelines that primarily focus on manual operations.
Emergency Procedures and First Aid
Despite all precautions, accidents can happen. Therefore, well-defined emergency response plans and readily available first aid are critical.
- A clear, site-specific emergency response plan must be established and communicated to all personnel involved in the hydroblasting operation. This plan should include procedures for equipment shutdown, medical emergencies, and evacuation routes.
- Operators must be trained on how to immediately stop the flow of high-pressure water in an emergency. This typically involves releasing the dead-man switch on a manual gun or activating an emergency stop on automated equipment.
- Suitable first aid facilities must be readily accessible at the operation site.
- Crucially, any injury caused by a high-pressure water jet, regardless of how minor it may appear externally, must be treated as a serious medical emergency. The operator must seek immediate, specialized medical attention. It is vital to inform medical personnel that the injury is a high-pressure injection injury, not a simple puncture wound. This is because high-pressure jets can inject water, debris, and bacteria deep into tissues, causing extensive damage that may not be immediately visible. Standard wound treatment protocols are often inadequate, and specialized surgical intervention may be required to prevent severe complications, including amputation or life-threatening infections.
5. Environmental Stewardship in Hydroblasting
While hydroblasting offers distinct advantages over some traditional cleaning methods in terms of reduced chemical use and dust generation, responsible environmental stewardship necessitates careful management of its byproducts, primarily wastewater and solid waste.
Benefits: Reduced Chemical Use, Dust Suppression
One of the primary environmental benefits of hydroblasting is its reliance on the physical force of water, rather than chemical action, for most cleaning and stripping applications. This significantly reduces or eliminates the need for harsh, corrosive, or toxic chemical solvents, thereby minimizing the introduction of these substances into the environment and reducing the complexities of chemical waste disposal.
Compared to dry abrasive blasting (e.g., sandblasting), hydroblasting does not generate significant airborne dust. Dry abrasive methods can release large quantities of fine particulate matter, including silica (if sand is used as the abrasive) and particles of the coating being removed (which may contain hazardous substances like lead or chromates).
This dust poses inhalation risks to operators and bystanders and can contaminate the surrounding environment, often requiring extensive and costly containment structures. Hydroblasting, by using water as the medium, inherently suppresses dust at the source, leading to improved air quality on site and simplifying containment requirements.
Wastewater Management: Collection, Containment, and Treatment
Although the input is primarily water, the wastewater (effluent) generated during hydroblasting operations can contain various contaminants removed from the cleaned surfaces. These may include paint chips, rust particles, scale, oil, grease, and, if present in the original coatings or deposits, hazardous substances such as lead, asbestos, or other heavy metals. Therefore, effective wastewater management is a critical environmental consideration.
- Collection and Containment: It is essential to collect and contain all wastewater to prevent its uncontrolled discharge into stormwater drains, surface waters, or onto the land, which is often illegal and can lead to significant environmental penalties. Common collection and containment methods include:
- Blocking site drains and catch basins using temporary plugs, bungs, or inflatable bladders.
- Creating temporary dikes or berms around the work area using sandbags, absorbent booms, or portable containment systems to direct and hold wastewater.
- Utilizing wet vacuum systems or dedicated vacuum trucks that can simultaneously collect wastewater and dislodged solid debris from the work surface.
- For larger projects or fixed facilities, constructing permanent wash slabs with integrated drainage and collection sumps.
- Treatment and Filtration: Depending on the nature and concentration of contaminants, collected wastewater often requires treatment before it can be legally discharged or reused. Treatment processes can range from simple to complex:
- Settling: Allowing wastewater to stand in tanks or basins (settling tanks or frac tanks) permits heavier solid particles to settle out by gravity.
- Filtration: Passing the wastewater through various types of filters (e.g., bag filters, cartridge filters, sand filters) removes suspended solids (TSS) to meet specific discharge limits or reuse quality standards.
- Oil/Water Separation: If oils or greases are present, specialized oil/water separators may be employed.
- Chemical Treatment: In some cases, chemical precipitation or pH adjustment might be necessary to remove dissolved contaminants, though this adds complexity and chemical handling requirements.
- Disposal: The ultimate disposal route for treated wastewater depends on its quality and local regulations. Options include:
- Discharge to a sanitary sewer system, provided it meets the acceptance criteria of the local Publicly Owned Treatment Works (POTW) and any necessary permits are obtained. POTWs are typically not designed to handle high concentrations of certain industrial pollutants.
- Discharge to surface waters, if the treated water meets stringent quality standards stipulated in a National Pollutant Discharge Elimination System (NPDES) permit (in the U.S.) or equivalent local environmental discharge permits.
- Off-site transport by a licensed waste management service for treatment and disposal at a specialized facility, particularly if the wastewater contains hazardous contaminants that cannot be effectively treated on-site.
- Regulations: Wastewater discharges from industrial activities, including hydroblasting, are typically governed by national and local environmental laws, such as the Clean Water Act and NPDES permitting program in the United States, or the Resource Management Act in New Zealand. Operators must be aware of and comply with all applicable regulations.
While hydroblasting is often presented as an “eco-friendly” alternative due to its primary use of water and lack of chemical additives or airborne dust generation , its overall environmental footprint is heavily influenced by the nature of the contaminants being removed and the diligence applied to wastewater and solid waste management.
The principle of “clean water in” does not inherently guarantee “clean water out” if the removed substances are themselves pollutants. Thus, the “eco-friendly” label is conditional upon responsible and comprehensive management of all waste streams, which can become particularly complex and costly if hazardous materials are involved.
Solid Waste Disposal: Handling Paint Chips, Removed Coatings, and Potentially Hazardous Materials
The solid waste generated from hydroblasting consists primarily of the materials dislodged from the cleaned surfaces. This can include old paint chips, rust scale, concrete debris, marine growth, and other residues. The handling and disposal of this solid waste are dictated by its composition.
If the coatings or materials being removed contain hazardous substances—such as lead (common in older paints), asbestos, chromates, cadmium, or other heavy metals—the resulting solid waste (and potentially the entrained wastewater) must be managed as hazardous waste. This involves:
- Hazardous Waste Determination: Testing the waste to confirm its hazardous characteristics according to regulatory criteria.
- Proper Containment: Collecting and storing the hazardous waste in sealed, labeled containers to prevent releases.
- Licensed Transport and Disposal: Arranging for a licensed hazardous waste transporter to take the waste to a permitted hazardous waste treatment, storage, and disposal facility (TSDF).
Non-hazardous solid debris can generally be disposed of more simply, often as general industrial waste, but local regulations should always be consulted. Even non-hazardous paint chips and residues should be diligently collected to prevent them from contaminating the surrounding area. The increasing stringency of environmental regulations concerning dust emissions, chemical exposure, and particularly the disposal of hazardous waste (such as lead-based paint debris) is a significant factor driving the adoption of hydroblasting, especially UHP methods.
These regulations make traditional methods like dry abrasive blasting or chemical stripping more challenging and costly from a compliance perspective. Hydroblasting, with its potential for better containment of solid waste (as a slurry) and reduced hazardous inputs (no abrasives, often no added chemicals), can offer a more compliant and manageable solution in many scenarios, despite potentially higher initial capital costs for the equipment.
Water Recycling and Conservation Opportunities
A key aspect of sustainable hydroblasting practice is the potential for water recycling and reuse. This not only conserves a valuable resource but can also reduce operational costs associated with water purchase and wastewater disposal.
- Systems can be implemented to collect the hydroblasting wastewater, filter out contaminants, and then reuse the treated water for continued blasting operations or other suitable non-potable applications on site.
- Effective water recycling systems can significantly reduce the volume of wastewater generated, with some reports indicating reductions of up to 90% in certain applications, such as boiler cleaning.
- In addition to conserving water, recycling can also reduce the consumption of any additives used in the water, such as flash rust inhibitors like sodium nitrite.
- The use of high-efficiency nozzles, which optimize the cleaning effect for a given flow rate, also contributes to water conservation by minimizing the total volume of water required for a task.
The viability and design of on-site water recycling systems for hydroblasting projects depend on several factors. These include the scale and duration of the project, the types and concentrations of contaminants in the wastewater (which dictate the complexity and cost of the necessary filtration and treatment), the required quality of the recycled water, and the overall cost-benefit analysis comparing the investment in recycling equipment against savings in water and disposal costs.
While systems like the one described for boiler cleaning (costing around $25,000 but offering savings in water and chemical use) demonstrate practicality , the economic and technical feasibility must be assessed on a case-by-case basis.
6. Hydroblasting vs. Alternative Methods: A Comparative Overview
Choosing the most appropriate method for surface preparation or industrial cleaning involves evaluating various factors, including technical requirements, environmental impact, safety, and cost. Hydroblasting offers distinct advantages in many scenarios but also has limitations compared to alternatives like abrasive blasting and chemical cleaning. The “best” method is not absolute but highly contextual, depending on a complex interplay of project-specific constraints and objectives.
Comparison with Abrasive Blasting (Sandblasting)
Abrasive blasting, commonly known as sandblasting (though various abrasive media are used), is a traditional method for surface preparation and cleaning.
- Advantages of Hydroblasting over Abrasive Blasting:
- No Dust Generation: Hydroblasting, using water alone, eliminates the significant airborne dust associated with dry abrasive blasting. This improves visibility, reduces respiratory health risks for workers and nearby personnel, and simplifies or eliminates the need for complex and costly dust containment structures.
- No Abrasive Media Waste: It avoids the generation of large volumes of spent abrasive media, which can be contaminated with the removed material (e.g., lead paint) and may require specialized and expensive disposal as hazardous waste. With hydroblasting, removed paint chips and debris can often be collected as a slurry or via wet vacuuming.
- Effective Removal of Soluble Salts: Hydroblasting is highly effective at removing invisible soluble salts (chlorides, sulfates) from the substrate. These salts, if not removed, can cause premature coating failure through osmosis. Dry abrasive blasting can sometimes embed or trap these salts within the surface profile.
- Preservation of Substrate Profile: When correctly applied, hydroblasting cleans the existing surface profile without significantly eroding or damaging the substrate material itself. This is particularly important for maintaining the integrity of precisely engineered surfaces or when multiple cleaning cycles are anticipated over the life of a structure. In contrast, abrasive blasting inherently removes a layer of the substrate material along with the coating or contaminant.
- Suitability for Sensitive Areas: The absence of dust and, if no abrasives are added to the water stream, the reduced risk of sparks can make hydroblasting a safer option for use in potentially flammable atmospheres or areas sensitive to particulate contamination.
- Limitations of Hydroblasting compared to Abrasive Blasting:
- No Profile Creation: On smooth, new, or previously unprofiled surfaces, hydroblasting cleans but does not etch or create a new surface roughness profile (anchor pattern). Many protective coatings require a specific surface profile for optimal adhesion, which abrasive blasting readily provides.
- Flash Rusting: Steel surfaces cleaned by hydroblasting are susceptible to flash rusting as they dry. This requires management, either through the use of inhibitors, rapid drying, or by ensuring the type of flash rust formed is acceptable to the coating manufacturer.
- Efficiency/Production Rate: The cleaning rate of hydroblasting can sometimes be slower than that of aggressive abrasive blasting, particularly for removing very thick or tenacious coatings from large areas. However, this is highly dependent on the specific coating, substrate, and the hydroblasting equipment parameters (pressure, flow, nozzle). While UHP hydroblasting might have lower square-foot-per-hour rates for some tasks, the significantly reduced time and cost for containment setup and cleanup can make its overall project time competitive or even superior. For certain types of coatings, such as viscous ones, hydroblasting can actually offer a faster removal rate.
- High Capital and Maintenance Costs: Hydroblasting equipment, especially UHP units and automated systems, can have a higher initial purchase cost and potentially higher maintenance expenses compared to some abrasive blasting setups.
- Water Usage and Wastewater Management: Hydroblasting inherently requires a source of water and generates wastewater that must be collected, contained, and often treated before disposal, adding to operational complexity and cost.
- Wet Abrasive Blasting (Slurry Blasting, Vapor Blasting): This method represents a hybrid approach, where a controlled amount of abrasive material is introduced into the high-pressure water stream (or a lower-pressure water stream with compressed air). Wet abrasive blasting significantly reduces airborne dust compared to dry blasting while still providing the cutting and profiling action of abrasives. It combines some advantages of both methods.
Comparison with Chemical Cleaning
Chemical cleaning relies on solvents, acids, alkalis, or detergents to dissolve or loosen contaminants from a surface.
- Advantages of Hydroblasting over Chemical Cleaning:
- No Chemical Residue: Pure water hydroblasting leaves no chemical residues on the cleaned surface that could interfere with subsequent coating adhesion, processes, or pose environmental concerns. Post-rinsing to remove chemical residues is typically not required after water-only blasting. Chemical cleaning processes often necessitate thorough rinsing and sometimes even mechanical cleaning afterward to eliminate any residual chemicals that could contaminate future products or affect coating performance.
- Generally More Environmentally Friendly: Hydroblasting avoids the use of potentially harsh, corrosive, toxic, or volatile organic compound (VOC)-emitting chemicals. This reduces the environmental impact associated with chemical manufacturing, transport, use, and the disposal of spent chemical solutions and contaminated rinse water.
- Improved Worker Safety: It significantly reduces the risk of worker exposure to hazardous chemicals through skin contact, inhalation of vapors, or accidental ingestion.
- Limitations of Hydroblasting compared to Chemical Cleaning:
- Accessibility for Complex Geometries: Chemical solutions, through immersion or circulation, can often reach and clean intricate internal passages or highly complex geometries where direct line-of-sight impact by a water jet is not possible without extensive disassembly.
- Effectiveness on Certain Specific Deposits: For some types of very stubborn, chemically bonded deposits, or where a specific chemical reaction is needed to break down the contaminant (e.g., certain types of scale or polymers), chemical cleaning might be more effective or may be required as a pre-treatment before hydroblasting.
The limitations of one method often highlight the strengths of another, suggesting that in some complex projects, a combination of methods might be the most effective approach. For example, hydroblasting could be used for initial bulk removal of fouling and critical salt decontamination, potentially followed by a light abrasive blast to impart a specific surface profile if required by the coating system.
Similarly, a chemical pre-treatment might be employed to soften very stubborn deposits before final removal by hydroblasting. This integrated approach can leverage the unique advantages of each technology while mitigating their individual drawbacks.
Advantages and Limitations of Hydroblasting (General Summary)
- Advantages:
- Highly effective for removing a diverse range of materials and contaminants from various surfaces.
- Significantly reduces or eliminates airborne dust and associated pollutants compared to dry abrasive methods.
- Often avoids the use of harsh chemicals, reducing environmental impact and worker exposure.
- Can be precisely controlled to clean delicate surfaces or aggressively cut hard materials.
- Preserves the original substrate profile when correctly applied, unlike abrasive methods that erode the substrate.
- Uniquely effective for removing soluble salts (chlorides, sulfates) that can cause premature coating failure.
- The availability of automated and robotic systems enhances safety, efficiency, and consistency.
- Limitations:
- Can have high initial capital costs for equipment, particularly for UHP and automated systems.
- Does not create a new surface profile on smooth metallic surfaces; it cleans the existing profile.
- Steel surfaces are prone to flash rusting after cleaning, which may require management.
- Poses significant safety hazards (e.g., high-pressure injection injuries) if not managed with extreme care and expertise.
- Requires a water source and generates wastewater that needs collection, treatment, and proper disposal.
- Manual hydroblasting can be physically demanding and may have slower production rates than abrasive blasting for certain large-scale applications, though this is offset by reduced setup/cleanup.
- Requires highly skilled and trained operators to ensure safety and effectiveness.
A comprehensive evaluation of cleaning and surface preparation methods must extend beyond initial equipment or labor costs. It should encompass the “total cost of ownership,” including expenses related to containment, waste characterization and disposal (especially if hazardous materials are involved), potential health impacts on workers and the community, and the long-term cost implications related to the quality and longevity of the applied coating or the efficiency of the cleaned equipment.
When these broader factors are considered, methods like UHP hydroblasting, which might appear more expensive upfront, can prove to be more economical and sustainable in the long run for specific applications, particularly those with stringent environmental or safety requirements or where coating performance is critical.
The following table provides a comparative overview:
Table 5: Comparative Analysis: Hydroblasting vs. Abrasive Blasting vs. Chemical Cleaning
Feature/Criterion | Hydroblasting (Water Only) | Dry Abrasive Blasting | Wet Abrasive Blasting | Chemical Cleaning |
---|---|---|---|---|
Surface Profile Creation | No (cleans existing profile) | Yes (creates new profile) | Yes (creates profile) | No |
Dust Generation | Minimal to None | High (significant airborne dust) | Significantly Reduced (dust suppressed by water) | None (but potential for vapors/fumes) |
Waste Generated (Volume/Type) | Wastewater (contaminants + water), removed material (slurry) | High volume of spent abrasive + removed material (dry) | Reduced abrasive volume + water + removed material (slurry) | Spent chemicals, rinse water, removed material (often dissolved or suspended) |
Soluble Salt Removal | Excellent | Poor (can embed salts) | Moderate to Good (water helps dissolve) | Variable (depends on chemical formulation) |
Chemical Residue on Surface | None (with pure water) | None (if properly cleaned post-blast) | Minimal (if rinsed) | Potential for residue if not thoroughly rinsed |
Speed/Productivity | Variable; can be slower or faster depending on application | Generally fast for many applications | Often slower than dry blasting but faster than manual methods | Variable; can be fast for immersion, slow for circulation or specific reactions |
Equipment Cost | Moderate to Very High (especially UHP/automated) | Low to Moderate | Moderate to High | Low (for simple methods) to High (for complex systems) |
Operator Skill/Safety Risk | High skill; Very High safety risk (injection) | Moderate skill; High safety risk (dust, projectiles) | Moderate skill; Moderate safety risk (reduced dust, injection) | Variable skill; High safety risk (chemical exposure, burns) |
Environmental Impact – Air | Low | High (dust pollution) | Low to Moderate (reduced dust) | Moderate (potential VOCs, odors) |
Environmental Impact – Waste | Wastewater management critical; solid waste depends on removed material | High volume solid waste, potentially hazardous | Moderate volume slurry, potentially hazardous | Liquid chemical waste, potentially hazardous; rinse water management |
7. The Professional Imperative: Why Expertise Matters in Hydroblasting
While the principles of hydroblasting might seem straightforward—using high-pressure water to clean or remove material—the actual execution is a complex, demanding, and potentially hazardous undertaking. Attempting such tasks without the requisite professional expertise, training, and equipment can lead to inefficient results, costly damage, severe injuries, and environmental non-compliance.
The decision to engage professional hydroblasting services is, therefore, not merely a matter of convenience but a critical investment in safety, quality, efficiency, and regulatory adherence. This is fundamentally a risk management strategy, as the potential costs associated with an accident (including injury, fatality, equipment damage, project delays, and regulatory fines) or a poorly executed job (such as premature coating failure or inefficiently cleaned equipment) can far outweigh the expense of hiring qualified experts.
Complexity of Equipment and Process Control
Hydroblasting relies on sophisticated and powerful equipment, including high-capacity pumps, an array of specialized nozzles, robust hoses and lances, and increasingly, advanced automated and robotic systems. Operating this machinery safely and effectively demands expert knowledge for proper setup, calibration, real-time adjustment, and routine maintenance.
Achieving the desired outcome—whether it’s a specific surface cleanliness standard for coating, complete removal of a tenacious deposit without damaging the underlying substrate, or efficient cutting of materials—depends on the precise control of multiple interrelated variables.
These include operating pressure, water flow rate, nozzle type and orifice size, standoff distance from the surface, and the traverse speed of the jet. This is far from a simple “point and shoot” operation. Incorrect settings or misapplication of the technique can lead to a host of problems: ineffective cleaning, leaving behind contaminants or residues; damage to the substrate, such as erosion, gouging, or, in the case of heat exchanger tubes, potential weakening or perforation ; or excessive consumption of water and energy, leading to unnecessary operational costs and environmental burden.
The increasing sophistication of hydroblasting technology, particularly with UHP systems, automated controls, and highly specialized nozzle designs, inherently widens the knowledge and skill gap between a generalist operator and a dedicated, trained professional. This technological progression further reinforces the necessity for specialized expertise, as hydroblasting is not a technology that can be casually adopted or mastered without significant and ongoing investment in training and experience—domains typically cultivated by professional service providers.
Critical Safety Requirements and Risk Mitigation
As extensively detailed in Section 4, hydroblasting operations are fraught with significant and potentially lethal hazards, with high-pressure water injection injuries being the most prominent and severe risk. Professional hydroblasting personnel undergo rigorous training and often hold certifications (such as those offered by the WJTA) that cover safe operating procedures, comprehensive hazard recognition, emergency response protocols, and the correct selection, inspection, and use of specialized Personal Protective Equipment (PPE).
These professionals are skilled in implementing critical safety measures mandated by industry best practices and regulations. This includes establishing secure work area barricades, adhering to strict lockout/tagout procedures during equipment setup and maintenance, ensuring proper hose management to prevent failures and tripping hazards, and understanding the dynamics of back thrust and operator fatigue. Attempting hydroblasting without this depth of safety knowledge and operational discipline dramatically elevates the risk of severe injury or fatality to operators and bystanders.
Ensuring Effective and Damage-Free Outcomes
Professional hydroblasting contractors possess the experience and technical understanding to select the optimal combination of equipment, operating parameters, and techniques for each unique task and substrate. This tailored approach is crucial for maximizing cleaning or removal effectiveness while minimizing the risk of damage to the surfaces being treated or to adjacent structures.
They are proficient in achieving specific industry surface preparation standards (e.g., NACE/SSPC cleanliness levels, WJ-1 to WJ-4, or hydroblasting-specific grades like HB2/HB2.5) and are knowledgeable about managing associated phenomena such as flash rusting on steel surfaces to ensure compatibility with subsequent coating applications. This expertise extends to adapting techniques for a diverse range of applications, from the delicate cleaning required for sensitive heat exchanger tubes to the controlled aggression needed for concrete demolition or the removal of hardened industrial deposits.
Navigating Environmental Regulations and Disposal
The environmental aspects of hydroblasting, particularly wastewater and solid waste management, are subject to increasingly stringent regulations (as discussed in Section 5). Professional service providers are typically well-versed in these local, regional, and national environmental laws and standards.
They have the knowledge and equipment to implement appropriate containment strategies, collect effluent and debris effectively, and manage the treatment and/or disposal of waste streams in a compliant manner.
This is especially critical when the hydroblasting process involves the removal of hazardous materials, such as lead-based paint, asbestos-containing materials, or other toxic residues, where improper handling can lead to significant environmental contamination and severe legal penalties. Engaging professionals helps ensure that all environmental obligations are met, protecting both the environment and the client from liability.
The Value of Experienced, Certified Professionals
Ultimately, entrusting high-pressure washing and hydroblasting tasks to experienced, certified professionals offers numerous tangible benefits:
- Efficiency and Reduced Downtime: Professionals, equipped with the right tools and expertise, can often complete projects more quickly and achieve first-pass cleaning effectiveness, thereby reducing costly operational downtime for industrial facilities.
- Prevention of Costly Damage: Their understanding of material interactions and process control minimizes the risk of accidental damage to valuable equipment, structures, or surfaces being cleaned.
- Enhanced Safety and Compliance: Professionals operate with a strong safety culture and adhere to established safety protocols and environmental regulations, protecting personnel, the public, and the client’s reputation.
- Access to Advanced Technology: Professional contractors often invest in the latest hydroblasting technologies, including high-efficiency UHP units and sophisticated automated or robotic systems, which may not be economically feasible or practical for individual companies to own and maintain.
- Comprehensive Service: The “professional imperative” extends beyond individual operator skill to encompass the entire organizational capacity to manage hydroblasting operations. This includes robust safety program management, diligent equipment maintenance schedules, established environmental compliance protocols, and ongoing investment in training and advanced technology.
In conclusion, while the allure of performing hydroblasting tasks in-house might seem like a cost-saving measure, the inherent complexities, severe safety risks, potential for ineffective or damaging outcomes, and stringent environmental regulations make a compelling case for engaging specialized professional services.
The expertise, training, equipment, and comprehensive management systems offered by reputable hydroblasting contractors represent an investment in safety, quality, efficiency, and peace of mind that typically far outweighs the initial outlay. For tasks involving the immense power of high-pressure and ultra-high-pressure water jetting, the professional imperative is clear: expertise is not just beneficial, it is essential.