1. The Critical Role of Aircraft Cleaning & Detailing: Beyond Aesthetics
Aircraft cleaning and detailing encompass a range of specialized procedures applied to both the exterior and interior of an aircraft. While enhancing the visual appeal is an obvious outcome, these processes are fundamentally linked to aircraft maintenance, directly impacting safety, operational performance, and the preservation of the aircraft’s significant financial value. This guide covers the essential aspects of cleaning and detailing for General Aviation (GA), Corporate, and Commercial aircraft, highlighting why these are critical maintenance tasks, not merely cosmetic options.
Enhancing Safety and Airworthiness
The primary technical justification for rigorous aircraft cleaning and detailing lies in its contribution to safety and airworthiness, primarily through corrosion prevention and enhanced inspection capabilities.
Contact us!
- Corrosion Prevention: Aircraft operate in diverse environments, constantly exposed to moisture, atmospheric pollutants, de-icing fluids, insect residue, and operational fluids like hydraulic oil or waste system leaks. These contaminants, particularly when combined with moisture (especially in coastal or high-humidity areas), create conditions ripe for corrosion on metal surfaces, including the airframe structure and landing gear components. Regular, thorough cleaning removes these corrosive agents before they can initiate or accelerate damage. Preventing corrosion is vital not only for maintaining structural integrity but also for extending the life of expensive paint systems. It is crucial to recognize that improper cleaning agents themselves can cause damage; even aircraft constructed primarily from composite materials can suffer irreversible harm to substrates, sealants, or finishes if incompatible household or automotive chemicals are used.
- Early Detection of Issues: A clean aircraft is significantly easier to inspect. Dirt, grease, and grime can effectively camouflage developing defects such as cracks in the structure or landing gear, fluid leaks (hydraulic, fuel, oil, water), loose fasteners, or other signs of wear or damage. Regular cleaning ensures surfaces are clear, allowing maintenance personnel and flight crews to perform more effective visual inspections and potentially detect incipient problems before they escalate into serious safety hazards or require costly repairs. This is particularly important in critical areas like landing gear bays, engine nacelles, and the aircraft belly, which are prone to fluid accumulation and stress. The ability to spot a small hydraulic leak or a hairline crack early is a direct safety benefit derived from maintaining a clean aircraft.
Optimizing Performance and Efficiency
Beyond safety, cleanliness directly impacts how efficiently an aircraft operates.
- Drag Reduction: Aerodynamic principles dictate that smoother surfaces generate less resistance, or drag, as the aircraft moves through the air. Accumulations of dirt, grime, insect residue, or even oxidized paint create a rougher surface, increasing parasitic drag. This increased drag requires engines to produce more thrust to maintain a given speed, leading directly to higher fuel consumption. Regular exterior cleaning and polishing maintain a smooth aerodynamic profile, contributing to reduced fuel burn and potentially enhancing performance metrics like speed and range. For commercial and corporate operators, where fuel represents a substantial operating cost, the fuel savings from maintaining a clean exterior can be significant over time.
- Engine Efficiency: While detailed in a later section, clean engine components, particularly within the compressor section, are essential for optimal engine performance and fuel efficiency. Engine washing procedures are a specialized form of technical cleaning aimed at maintaining this efficiency.
Protecting Your Investment and Maximizing Value
An aircraft represents a substantial financial investment, and meticulous cleaning and detailing are integral to protecting that investment.
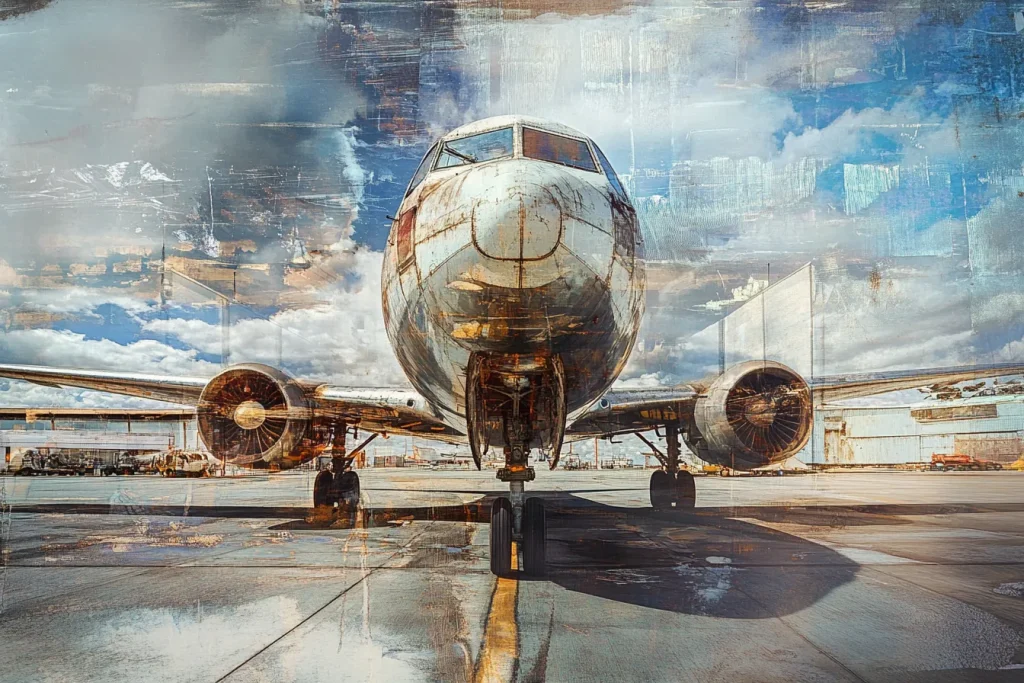
- Asset Preservation: Regular professional cleaning and detailing actively preserve the condition of the aircraft. It protects the expensive paint finish from degradation caused by UV exposure and contaminants, maintains the appearance and integrity of interior furnishings like leather upholstery and wood veneers, and prevents the onset of corrosion that can devalue the airframe. This consistent care helps the aircraft achieve its designed service life, which can exceed 20 years.
- Increased Resale Value: The condition of an aircraft significantly influences its market value. A visibly clean and well-maintained aircraft invariably commands a higher resale or lease value compared to one showing signs of neglect. A pristine appearance signals meticulous care and instills confidence in potential buyers or lessees regarding the overall maintenance standard of the aircraft, making it a more attractive asset. Thus, detailing is not merely an expense but an investment in maintaining the aircraft’s capital value.
2. Navigating the Skies of Regulation and Safety
Aircraft cleaning is not an unregulated activity akin to automotive detailing. It is intrinsically linked to aircraft maintenance and is therefore subject to oversight by aviation regulatory authorities such as the Federal Aviation Administration (FAA) in the United States and the European Union Aviation Safety Agency (EASA) in Europe. Adherence to these regulations, along with manufacturer guidelines and material compatibility considerations, is paramount.
Understanding FAA and EASA Requirements
Both the FAA and EASA recognize aircraft cleaning as a maintenance function, integrating it into their regulatory frameworks, albeit with slightly different approaches.
- FAA Perspective: The FAA explicitly categorizes exterior washing, waxing, and polishing as “preventive maintenance” items under Federal Aviation Regulations (FAR) Part 43, Appendix A, Section C. This classification has significant implications, particularly for aircraft operated commercially under FAR Part 121 (Airlines) and FAR Part 135 (Charter/Commuter). For these operations, such preventive maintenance tasks must adhere to specific procedures and require formal sign-off by certified personnel to return the aircraft to service. Furthermore, thorough cleaning is often mandated as part of required inspections, such as the annual inspection detailed in FAR Part 43, Appendix D, to ensure effective examination of the aircraft structure and systems.
- EASA Perspective: EASA emphasizes adherence to the procedures outlined in the specific Aircraft Maintenance Manual (AMM) for all cleaning and disinfection activities. EASA regulations, particularly those updated in response to health concerns like COVID-19, provide specific guidance on disinfection frequency, methods, and the use of approved disinfecting agents, always referencing the need for operator approval and AMM compliance. While both agencies prioritize safety, the FAA’s approach can sometimes be more performance or risk-based, whereas EASA’s tends to be more prescriptive, mandating specific intervals or procedures.
- Aircraft Maintenance Manual (AMM): Regardless of the governing authority, the AMM produced by the aircraft manufacturer is the definitive source for cleaning procedures. It contains model-specific instructions, lists approved cleaning agents and disinfectants, details precautions for sensitive areas, and outlines any required post-cleaning lubrication or checks. Consulting and strictly adhering to the AMM is essential for safe and compliant cleaning.
The regulatory framework surrounding aircraft cleaning underscores its importance as a maintenance task with direct implications for airworthiness. It necessitates a level of procedural rigor, documentation, and qualified oversight distinct from non-aviation cleaning services.
The Crucial Role of Certified Technicians
The classification of cleaning as maintenance directly impacts who is authorized to perform these tasks, especially in commercial contexts.
- FAA Requirement: For aircraft operating under FAR Parts 121 and 135, the FAA mandates that preventive maintenance, including cleaning, washing, and polishing, must be performed or directly supervised by a certified Airframe & Powerplant (A&P) mechanic. Crucially, an A&P mechanic must approve the aircraft for return to service by making an entry in the aircraft’s maintenance records. Utilizing unqualified personnel, such as automotive detailers lacking A&P certification, for these tasks on Part 121 or 135 aircraft constitutes a violation of regulations and can result in the aircraft being grounded.
- Part 91 Exception: Operations under FAR Part 91 (typically General Aviation) offer more flexibility. The aircraft owner or pilot holding at least a private pilot certificate is permitted to perform preventive maintenance tasks listed in FAR 43 Appendix A, including cleaning, on an aircraft they own or operate, provided it is not used in air carrier service. However, if someone other than the owner/operator performs these tasks for compensation, they generally must hold the appropriate mechanic certification.
- Technician Training: Formal A&P mechanic training programs, certified under FAA Part 147 or equivalent EASA standards, include instruction on aircraft materials, approved processes, corrosion control, and regulatory compliance – knowledge directly applicable to performing cleaning tasks safely and correctly. Coursework often includes specific modules on cleaning, corrosion control, and handling of approved chemicals.
The requirement for certified personnel in many cleaning scenarios highlights that the task involves potential risks to the aircraft’s airworthiness if performed improperly. Certification ensures the individual understands material compatibility, correct procedures, and the potential safety consequences of errors.
Material Compatibility: Choosing the Right Products
Aircraft are complex assemblies of diverse materials, including various metal alloys, composites, plastics, specialized coatings, rubbers, and sensitive electronic components. Ensuring that cleaning products are compatible with these materials is absolutely critical to prevent damage.
- The Cardinal Rule: Only cleaning agents, solvents, polishes, and disinfectants specifically formulated, tested, and approved for aviation use should ever be applied to an aircraft. Using household products (like window cleaners containing ammonia, or detergents high in salt) or automotive/industrial cleaners (like caustic truck washes) is strictly prohibited and highly dangerous.
- Risks of Improper Products: Incompatible chemicals can cause a range of damage:
- Corrosion: Salts (sodium chloride) in household detergents or caustic agents (like caustic soda in truck wash) can severely corrode aluminum and other metals.
- Paint Damage: Harsh solvents or abrasive cleaners can strip or dull paint finishes.
- Plastic Damage: Acrylic windows (Plexiglass) and polycarbonate components are highly susceptible to crazing (networks of fine cracks), clouding, or softening when exposed to ammonia, alcohols, ketones, or other solvents found in many non-aviation cleaners. Rigid plastics like ABS can also be sensitive.
- Composite Degradation: Certain chemicals can irreversibly damage composite matrix resins or fibers.
- Seal Damage: Solvents can degrade rubber and synthetic seal materials, potentially leading to leaks.
- Electrical Issues: Some chemicals can damage wiring insulation or cause issues with electrical terminations.
- Approved Chemicals & Specifications: Aviation-approved products are typically tested against stringent industry specifications, such as Boeing D6-17487 (covering various cleaner types), MIL-PRF-85570 (Exterior Cleaner), MIL-PRF-87937 (Aerospace Equipment Cleaner/Degreaser), MIL-PRF-85704 (Turbine Engine Cleaner), or Aerospace Material Specifications (AMS). Approved products include:
- pH-neutral or mildly alkaline exterior washes.
- Specialized degreasers (solvent-based or aqueous, low-VOC options available).
- Polishes and sealants free of harmful silicones.
- Specific disinfectants verified for material compatibility (e.g., 70% Isopropyl Alcohol with caveats, certain QACs). It’s important to differentiate between degreasers, designed to remove oils and grease, and sanitizers/disinfectants, intended to kill microorganisms. While some products like 70% IPA might do both, one cannot assume a degreaser also disinfects.
- Consulting Documentation: Always verify product suitability by checking the aircraft AMM and the product manufacturer’s technical data sheet (TDS) and safety data sheet (SDS) for approved applications and compatibility information.
The selection of cleaning products in aviation is governed by material science. The goal is not just cleanliness but ensuring the chosen chemical will not cause immediate or latent damage that could compromise the aircraft’s structural integrity, system function, or overall safety.
Environmental Compliance
Aircraft cleaning operations are also subject to environmental regulations concerning chemical usage and waste disposal.
- Waste Streams: The Resource Conservation and Recovery Act (RCRA) regulates the handling and disposal of solid and hazardous wastes. Cleaning operations can generate waste streams, including used cleaning solutions, rinse water containing detergents and contaminants (oils, grease, heavy metals), and used wipes or absorbents. If these wastes exhibit hazardous characteristics (ignitability, corrosivity, reactivity, toxicity), they must be managed according to strict RCRA protocols.
- Wastewater Management: There is increasing regulatory scrutiny under the Clean Water Act (CWA) regarding the discharge of wastewater from aircraft washing activities. Runoff containing detergents, degreasers, or removed contaminants can pollute stormwater systems or groundwater if not properly contained and treated. This often necessitates the use of designated wash racks with drainage collection and treatment systems, or water reclamation technology, especially at larger airports.
- Pollution Prevention: The Pollution Prevention Act (PPA) encourages reducing the generation of hazardous substances at the source. This aligns with the aviation industry’s move towards more environmentally friendly cleaning practices, such as using biodegradable, low-VOC (Volatile Organic Compound) cleaners, or adopting waterless cleaning methods (dry washing) to minimize wastewater generation.
Environmental responsibility is an increasingly integral part of aircraft maintenance, influencing the choice of cleaning products, methodologies, and required infrastructure to ensure compliance and minimize ecological impact.
3. Mastering Exterior Aircraft Detailing
Exterior aircraft detailing involves a systematic process to clean, restore, and protect the aircraft’s outer surfaces. It requires careful preparation, appropriate techniques for different soil levels and surface types, and the use of specialized, approved products.
Preparation is Key
Thorough preparation is arguably the most critical phase of exterior cleaning, as errors here can lead to significant damage or system malfunctions.
- Pre-Cleaning Inspection & Safety: Before starting any cleaning, perform a walk-around inspection. Ensure all access panels, doors, and covers are securely fastened to prevent accidental opening or water ingress. Identify areas of heavy contamination that may require pre-treatment.
- Protecting Sensitive Areas: This step is non-negotiable. Use aviation-approved, low-adhesion masking tape (brightly colored tape is recommended for visibility) or specialized plugs to cover and seal all sensitive openings and probes. This includes:
- Pitot tubes and static ports (critical for airspeed and altitude measurement)
- Angle of Attack (AOA) sensors
- Engine inlets and exhausts
- APU inlets and exhausts
- Environmental control system (ECS) vents and outlets
- Any other openings, seams, or vents where water or cleaning solutions could enter and cause damage. Carefully cover windows and windscreens to protect them from abrasive cleaners or polishes used on adjacent surfaces. It is good practice to create a checklist of all items covered to ensure every piece of tape and all plugs are removed before flight.
- Environmental Conditions: Whenever possible, wash the aircraft out of direct sunlight and ensure the surfaces are cool to the touch. Many cleaning compounds, polishes, and coatings perform best under these conditions and can dry too quickly or streak on hot surfaces.
Failure to meticulously protect sensitive components can lead to blocked sensors providing false flight instrument readings, water ingestion into engines, corrosion in electrical connectors, or damage to avionics – all with potentially severe safety consequences.
Washing Techniques: Wet Wash vs. Dry Wash
Two primary methods are used for washing aircraft exteriors, each with its advantages and disadvantages.
- Wet Wash:
- Procedure: This traditional method involves applying water, often mixed with an approved aircraft washing detergent, to the exterior surfaces using low-pressure sprayers, specialized mops, or brushes. Heavy contamination like grease or exhaust soot may require pre-treatment with approved solvents (applied carefully with non-abrasive tools like soft plastic or wooden scrapers) or stronger alkaline/emulsion cleaners. Agitation with soft brushes or mops may be necessary. The process concludes with a thorough rinse using clean water to remove all residues. Careful control of water pressure is essential; high-pressure washers should generally be avoided or used with extreme caution at very low settings to prevent damage to paint, sealants, or forcing water past seals.
- Pros: Highly effective for removing heavy, widespread contamination such as oil, grease, carbon deposits, mud, and salt accumulations. Thorough rinsing helps remove all loosened contaminants.
- Cons: Consumes large volumes of water (e.g., over 9,500 liters for a Boeing 777). Creates wastewater runoff that may require containment and treatment due to environmental regulations. Carries a higher risk of water intrusion into sensitive areas if preparation is inadequate. May not be permitted at all airports or FBOs due to water restrictions or environmental policies. Can strip existing wax or sealant layers. Less effective at removing oxidation films.
- Dry Wash (Waterless):
- Procedure: This technique utilizes specialized chemical formulations sprayed directly onto the aircraft surface in manageable sections. The chemicals lift and encapsulate dirt particles. Clean, dry microfiber towels are then used to wipe away the chemical and entrapped dirt. A second clean towel is often used to buff the surface, leaving a clean, often glossy and protective, finish.
- Pros: Conserves significant amounts of water, making it environmentally friendly and suitable for locations with water restrictions. Can be performed virtually anywhere (hangar, ramp) without needing dedicated wash facilities. Minimizes the risk of water intrusion into sensitive components. Often faster for routine cleaning of light to moderate soil. Leaves a protective film that can enhance gloss and make subsequent cleaning easier. Allows other maintenance tasks to be performed concurrently on the aircraft.
- Cons: Generally less effective than wet washing for removing heavy deposits of grease, oil, mud, or thick, caked-on dirt, especially in areas like landing gear or engine exhausts. Requires a careful technique and a generous supply of clean microfiber towels to avoid scratching the paint surface with abrasive dirt particles being wiped away. Can be more labor-intensive than wet washing for heavily soiled aircraft.
The choice between wet and dry washing depends on several factors: the degree and type of contamination, local environmental regulations and water availability, the aircraft owner’s preference, and the condition of the aircraft’s paint and protective coatings. Due to increasing environmental pressures and operational convenience, dry washing techniques and products are becoming increasingly popular and sophisticated.
Feature | Wet Wash | Dry Wash (Waterless) |
---|---|---|
Procedure | Water + Detergent Application, Scrubbing, Thorough Rinsing | Specialized Chemical Spray, Wipe-off with Microfiber Cloths |
Effectiveness | Excellent for heavy grease, oil, mud, salt | Good for dust, light dirt, airport film; Less effective on heavy grime |
Water Consumption | High | Minimal to None |
Environmental Impact | Potential runoff concerns, requires water management | Low impact, minimal waste |
Location Flexibility | Often requires dedicated wash rack/area | High flexibility (hangar, ramp) |
Risk of Water Ingress | Higher risk if preparation is inadequate | Very low risk |
Speed (Light Soil) | Can be slower due to setup/rinsing/drying | Often faster |
Finish | Clean surface, may strip wax/sealants | Often leaves a glossy, protective film |
Best Use Cases | Heavily soiled aircraft, post-maintenance cleaning, corrosive environments | Routine cleaning, water-restricted areas, maintaining polished finish |
Achieving a Flawless Finish: Paint Polishing, Sealants, and Coatings
Maintaining the aircraft’s paint system involves more than just washing. Polishing, sealing, or coating the paint provides aesthetic enhancement, protection, and performance benefits.
- Purpose: These processes aim to restore and maintain the paint’s gloss, remove surface imperfections like oxidation, light scratches, or stains (especially around exhaust areas), protect the paint from environmental degradation (UV radiation, contaminants, acid rain), and contribute to drag reduction by creating a smoother surface.
- Process:
- Surface Preparation: A prerequisite for any polishing or coating application is an immaculately clean and dry surface. For paint that is oxidized, faded, or has minor imperfections, a compounding step may be necessary. This involves using rotary or orbital polishers with appropriate pads (e.g., wool for cutting, foam for finishing) and aircraft-approved abrasive compounds. It is crucial to use the least aggressive compound necessary and employ careful technique to avoid burning or damaging the paint.
- Application: Following preparation (and compounding, if needed), aircraft-approved polishes, paint sealants (typically synthetic polymers offering longer durability than traditional waxes), or advanced ceramic coatings are applied. Application methods vary (hand or machine) and manufacturer instructions regarding application thickness, removal, and curing time must be strictly followed. It is critical to avoid automotive waxes, especially those containing silicone or carnauba wax, as they may not withstand flight conditions, can interfere with paint repairs, or potentially cause static buildup.
- Benefits of Coatings/Sealants: Modern sealants and ceramic coatings create a hard, durable, sacrificial layer over the paint. For example, Permagard adds approximately 4 microns of flexible protection. These products significantly enhance gloss levels, create a hydrophobic (water-repelling) surface, make future cleaning much easier (dirt and contaminants adhere less readily), and provide robust protection against environmental hazards like UV rays, bird droppings, insect impacts, and de-icing fluids. Durability varies, with some spray-on SiO2 products lasting around 6 months , while professionally applied ceramic coatings can offer protection for several years, sometimes with warranties up to 10 years. Applying high-quality sealants or coatings represents proactive maintenance for the aircraft’s paint system. It extends the paint’s life, reduces the need for more aggressive cleaning or future paint repairs, maintains the aircraft’s appearance, and contributes tangibly to aerodynamic efficiency.
Brightwork Polishing: Restoring the Shine
Many aircraft feature unpainted, polished metal components known as brightwork. Maintaining their distinctive mirror-like finish requires specialized techniques.
- Target Areas: Common brightwork includes wing and empennage leading edges, engine inlets (nacelle lips), propeller spinners, and sometimes thrust reverser components, typically made of aluminum or stainless steel.
- Purpose: The goal is to remove oxidation, tarnish, minor scratches, and surface imperfections to restore and maintain a highly reflective, mirror finish.
- Process: Brightwork polishing is typically a multi-step process using progressively finer grades of specialized metal polishes. Products like Nuvite NuShine II (with grades ranging from aggressive F9 or G6 for initial cutting/oxidation removal, to medium A, to fine F7, and final finish S) or the BrightWork 3-step system are commonly used. The process usually involves:
- Masking off adjacent painted surfaces to prevent damage.
- Applying a small amount of the appropriate cutting polish.
- Using a rotary buffer, often with a wool compounding pad, at controlled speeds (e.g., 1500-2000 rpm) to work the polish and remove oxidation/defects.
- Cleaning the surface and repeating with progressively finer grades of polish and softer pads (e.g., foam pads often used with cotton flannel wraps for final finishing with orbital buffers).
- Hand polishing may be necessary for tight areas inaccessible to buffers. Achieving a flawless, swirl-free mirror finish on brightwork is labor-intensive and demands considerable skill and patience. Using the wrong grade of polish, incorrect buffer speed or pressure, or contaminated pads can easily scratch or burn the metal, requiring significant effort to correct.
Specialized Exterior Care
Beyond general washing and polishing, certain exterior components require specific cleaning and maintenance procedures.
- De-icing Boot Cleaning and Treatment:
- Importance: Pneumatic de-icing boots, typically found on the leading edges of wings and stabilizers of many turboprop and piston aircraft, are critical safety components for flight in icing conditions. Proper maintenance ensures their flexibility, surface condition for effective ice shedding, and overall longevity. Boots can deteriorate from environmental exposure (UV, ozone) even when the aircraft is parked.
- Procedure: Routine cleaning after flight with mild soap and warm water is recommended to remove insect debris and contaminants before they dry. Periodic, more thorough maintenance involves a multi-step process using manufacturer-approved product systems, such as the widely used Collins Aerospace Goodrich line (available from distributors like Aero-Sense). This typically includes:
- Preparation: Cleaning and stripping old protectants using a prep cleaner (e.g., ShineMaster® Prep).
- Conditioning (Neoprene Boots): Applying a rubber conditioner (e.g., AgeMaster® No. 1) to protect against aging and environmental degradation. This requires specific application and drying times.
- Polishing/Sealing: Applying a protective polish (e.g., ShineMaster®) to restore shine, create a smooth surface, and resist dirt buildup. Multiple coats may be needed.
- Performance Enhancement: Applying an ice adhesion-reducing fluid (e.g., ICEX-II®) during icing season to enhance the boot’s ability to shed ice. This is typically the last step. Strict adherence to the product manufacturer’s instructions regarding application methods, number of coats, drying times, and reapplication intervals (often based on flight hours or calendar time) is essential for both effectiveness and boot longevity. Boot care is a specific maintenance task directly related to flight safety.
- Landing Gear and Wheel Well Cleaning:
- Importance: The landing gear operates under extreme stress and is constantly bombarded with runway contaminants: grease, hydraulic fluid, brake dust, dirt, mud, salt (in winter or coastal areas), and foreign object debris (FOD). This accumulation makes the gear assembly highly prone to corrosion and can hide critical defects. Cleanliness is paramount for effective inspection of struts, actuators, linkages, wheels, brakes, and hydraulic lines.
- Procedure: Cleaning landing gear typically requires heavy-duty degreasers specifically approved for aircraft use and compatible with the various materials present (metals, seals, wiring). Products meeting military specifications like MIL-PRF-87937 or commercially available aircraft-specific degreasers are often used. Application methods involve spraying or brushing the degreaser onto the components, allowing sufficient dwell time to penetrate the grime, scrubbing with appropriate brushes (avoiding wire brushes on sensitive parts), and then thoroughly rinsing with water if using a wet wash method. Post-cleaning lubrication of certain components may be required as specified in the AMM. Given the critical nature of the landing gear, its cleaning is primarily a maintenance function enabling thorough inspection, rather than just for cosmetic appearance.
- Window Polishing and Scratch Removal:
- Materials: Aircraft transparencies (windshields, cabin windows) are most commonly made from acrylic (Polymethyl Methacrylate, PMMA, trade names like Plexiglas) or sometimes polycarbonate (trade name Lexan), not glass. These plastics offer impact resistance and weight savings but are much softer than glass, scratching easily, and are highly sensitive to certain chemicals. Maintaining optical clarity is essential for pilot visibility and safety.
- Procedure: Routine cleaning should only be done using aviation-approved plastic cleaners/polishes (e.g., Prist, or mild soap and water) applied with soft, clean microfiber or cotton cloths. Never use abrasive cleaners, paper towels, or dry cloths on dirty windows, as this will cause scratches. Avoid household window cleaners (especially those containing ammonia), gasoline, acetone, or other harsh solvents, which can cause immediate damage or long-term crazing. For existing fine scratches, hazing, or cloudiness, specialized restoration kits are available (e.g., Clearfix, Scratch Off, Micro-Mesh). These kits typically involve a multi-step process using specific liquid polishing compounds of varying abrasiveness applied with dedicated foam or microfiber pads, often using an orbital buffer, to carefully polish out imperfections and restore optical clarity. Following the kit instructions precisely is crucial. Protecting window clarity requires meticulous care using only compatible, approved products and techniques.
4. Immaculate Interiors: Cabin and Cockpit Detailing
Aircraft interior detailing focuses on cleaning, sanitizing, and restoring the cabin and cockpit environment. This is vital for passenger and crew comfort, health, and safety (particularly instrument visibility in the cockpit), as well as preserving the significant value invested in high-quality interior materials and furnishings. The diverse range of materials requires careful product selection and appropriate techniques.
Cockpit Care: Cleaning Instruments and Sensitive Electronics Safely
The flight deck contains highly sensitive and expensive instrumentation and avionics critical for safe flight operations. Cleaning this area demands extreme caution.
- High Sensitivity: Instrument panels, Multi-Function Displays (MFDs), Primary Flight Displays (PFDs) often featuring glass screens with anti-reflective coatings, switches, control yokes, throttles, and communication/navigation equipment are extremely vulnerable to damage from liquids and inappropriate cleaning chemicals. Liquid ingress can cause short circuits or corrosion, while incompatible chemicals can damage screen coatings, plastics, or lettering. Such damage can be exceptionally costly to repair and, more importantly, could compromise the reliability of essential flight systems.
- Recommended Technique: The cardinal rule is never spray cleaning liquids directly onto the instrument panel or controls. Doing so risks forcing liquid into sensitive areas or applying excessive amounts. The widely accepted best practice is:
- Fold a clean, soft, lint-free microfiber towel into quarters.
- Lightly spray an approved cleaner onto a section of the towel while holding the towel outside the cockpit.
- Gently wipe the intended surfaces (instrument faces, bezels, panels, switches) with the dampened portion of the towel.
- Follow immediately with a separate clean, dry microfiber towel to remove any residue.
- Approved Cleaners: Use only cleaners specifically approved for aviation electronics or cockpit displays, or as recommended in the AMM. Electronic contact cleaners may be suitable for some switches (power off), while specialized anti-static screen cleaners are best for displays. Mild solutions like highly diluted isopropyl alcohol (IPA) are sometimes used cautiously on certain surfaces, but compatibility must always be verified first, as IPA can damage some plastics or coatings. Avoid ammonia-based cleaners, abrasive substances, or general-purpose interior sprays unless explicitly approved for cockpit use.
The potential consequences of damaging cockpit avionics through improper cleaning far outweigh any perceived convenience of quicker methods. Meticulous technique and verified product compatibility are non-negotiable safety requirements.
Cabin Deep Clean: Carpets, Upholstery, and Headliners
Aircraft cabins feature a variety of materials requiring specific cleaning approaches.
- Material Variety: Flooring is typically high-quality carpet (often wool or wool blends in corporate/GA, durable synthetics in commercial). Seats are upholstered in leather, synthetic leather (coated fabrics), or various woven fabrics. Sidewalls and headliners may be covered in fabric, vinyl, or composite panels.
- Carpet Cleaning Methods: The choice between methods depends largely on the carpet material and the level of soiling:
- Hot Water Extraction (often called Steam Cleaning): This method uses specialized machines that spray a heated cleaning solution into the carpet pile and immediately extract the solution along with loosened dirt and grime using powerful suction. It provides a deep clean effective for heavily soiled areas and high-traffic zones. However, it introduces significant moisture, requiring adequate drying time to prevent mold or mildew. It may not be suitable for moisture-sensitive materials like wool, which can shrink or be damaged.
- Dry Cleaning: This encompasses several low-moisture techniques. Some use absorbent compounds sprinkled onto the carpet, agitated, and then vacuumed up. Others utilize specialized solvents applied with machines or cloths to dissolve dirt, which is then removed. Dry cleaning methods are generally preferred for wool and other moisture-sensitive carpets as they minimize drying time and reduce the risk of shrinkage or water staining. If solvents are used, adequate ventilation is essential.
- Upholstery/Fabric Cleaning: Thorough vacuuming with appropriate attachments (including HEPA filters) is the first step. For spills and stains, prompt treatment is key. Use specialized spot removers compatible with the specific fabric type and stain (e.g., different agents for protein, oil, or tannin-based stains). Always test any cleaning agent on an inconspicuous area first to check for colorfastness or damage. Blot stains gently; never rub, which can spread the stain and damage fibers. Some delicate fabrics may require professional dry cleaning methods only. Always consult the AMM or material manufacturer’s guidelines if available.
- Headliners/Sidewalls: These are typically cleaned using approved interior cleaners applied lightly to microfiber cloths, taking care not to saturate the material, which could lead to sagging or water stains. Technique focuses on gentle wiping.
The diverse and often expensive materials used in aircraft interiors mean that a one-size-fits-all cleaning approach is inappropriate. Selecting the correct method and chemistry based on the specific material is crucial to achieve effective cleaning without causing costly damage.
Leather Care: Cleaning and Conditioning
Leather seating and accents are common in corporate and GA aircraft, requiring specific care to maintain their luxurious appearance and longevity.
- Importance: Proper care preserves the look, supple feel, color, and characteristic smell of leather. It prevents the material from drying out, becoming brittle, and developing cracks, especially in the variable temperature and humidity conditions found in aircraft cabins. Well-maintained leather significantly contributes to the perceived value and comfort of the interior.
- Procedure:
- Regular Dusting/Wiping: Frequent light dusting or wiping with a clean, dry microfiber cloth removes surface debris.
- Cleaning: For more thorough cleaning or addressing spills, use a mild, pH-balanced leather cleaner specifically approved for aviation use. Apply the cleaner to a soft cloth, not directly to the leather. Gently wipe the surface. For spills, blot immediately with a clean cloth. Avoid harsh detergents or solvents.
- Conditioning: This is a vital step often overlooked. After cleaning and allowing the leather to dry, apply a high-quality leather conditioner using a clean, soft cloth. Conditioners replenish natural oils lost over time, keeping the leather flexible and preventing cracking. Many also contain UV inhibitors to protect against sun damage. Conditioning frequency depends on usage and climate but is typically recommended every 3 to 6 months.
- Material Variations: Genuine leather requires cleaners and conditioners that nourish the hide. Synthetic leathers (coated fabrics) are generally cleaned with mild soap/surfactant solutions or approved disinfectants, depending on the top coat (e.g., polycarbonate), and typically do not require conditioning in the same way as natural leather.
- Restoration: For leather that is already faded, scratched, or cracked, professional leather restoration services can often repair damage and redye surfaces. DIY kits are also available but require careful application.
Simply cleaning leather is insufficient for long-term preservation. Regular conditioning is the key proactive step to maintain its suppleness, prevent degradation, and protect the investment in premium interior furnishings.
Polishing Wood Veneer and Trim
High-gloss wood veneer finishes add elegance to many aircraft cabins but require careful handling.
- Delicate Surfaces: Wood veneers are thin layers of real wood bonded to a substrate, often finished with high-gloss coatings. They are susceptible to scratching, water damage, and fading.
- Procedure: Treat wood veneer like fine furniture:
- Dusting: Dust regularly using a soft, dry, lint-free microfiber cloth to prevent abrasive particles from scratching the finish.
- Cleaning: For fingerprints or light soil, use a slightly dampened (never wet) soft cloth, wiping gently with the wood grain. If necessary, use a highly diluted mild soap solution on the damp cloth, followed immediately by wiping with a clean damp cloth and then drying thoroughly with a soft, dry cloth. Excess moisture is the enemy of veneer, potentially causing lifting, warping, or clouding of the finish.
- Polishing: Apply a high-quality furniture polish or wax specifically designed for wood veneers sparingly every few months. Choose products compatible with aircraft cabin environments (potential humidity/pressure changes) and preferably offering UV protection. Apply thinly with a soft cloth, following the grain, and buff gently to a shine. Avoid overuse, which can lead to buildup.
Controlling moisture during cleaning and using appropriate protective polishes are essential for maintaining the beauty and integrity of wood veneer finishes.
Galley and Lavatory Sanitation: Ensuring Hygiene Standards
Galleys and lavatories are critical areas requiring the highest standards of cleaning and sanitation due to their high usage and potential for harboring bacteria and viruses.
- Critical Areas: These confined spaces involve food handling (galley) and waste management (lavatory), making them potential hotspots for cross-contamination and the spread of illness if not meticulously maintained. Rigorous hygiene protocols are essential for the health and safety of passengers and crew.
- Procedure: A systematic approach is crucial:
- Preparation: Remove all loose items, food waste, and trash.
- Cleaning: Thoroughly clean all surfaces before disinfecting, as dirt can inhibit disinfectant effectiveness. Work methodically, typically from top to bottom, and from cleaner areas to dirtier areas (e.g., clean countertops before toilet bowls). Use appropriate cleaners for different surfaces (stainless steel, countertops, mirrors, toilet bowls).
- Disinfection: Apply an EPA-registered, aircraft-approved disinfectant to all surfaces, paying close attention to high-touch points: faucet handles, flush controls, toilet seats, door handles (inside and out), light switches, countertops, cabinet latches, galley appliance controls, and waste bin lids. Follow the disinfectant label instructions precisely regarding dilution (if applicable), application method (wipe, do not spray near electronics), and required contact time (the surface must remain wet for the specified duration).
- Rinsing/Wiping: If required by the disinfectant instructions, rinse or wipe surfaces with a clean damp cloth after the contact time to remove residue.
- Waste Disposal: Dispose of all cleaning cloths (preferably disposable in lavs) and waste properly.
- Prevent Cross-Contamination: Use separate cleaning cloths, sponges, and equipment for the lavatory versus the galley. Color-coding tools can help maintain this separation.
Adhering to structured cleaning and disinfection protocols in galleys and lavatories is vital for preventing the spread of pathogens and ensuring a hygienic environment onboard.
Disinfection Services: Modern Protocols for Health and Safety
Routine disinfection of the entire aircraft cabin has gained significant importance, particularly in the wake of global health events.
- Increased Importance: Operators are now more focused than ever on implementing robust disinfection protocols to protect passengers and crew from infectious diseases transmitted via surfaces or airborne particles.
- Protocols: Effective disinfection should always follow thorough cleaning. The frequency of disinfection depends on the type of operation (commercial vs. private), flight duration, passenger load, and specific regulatory mandates or company policies. Protocols typically target high-touch surfaces throughout the cabin, including seat belts and buckles, armrests, tray tables, window shades, passenger service units (lights, air vents), overhead bin handles, lavatory and galley surfaces, and crew communication equipment.
- Approved Disinfectants: This is a critical consideration. Disinfectants must be proven effective against relevant pathogens (e.g., meet EPA List N criteria for efficacy against SARS-CoV-2) AND be explicitly approved by the aircraft manufacturer (OEM) or listed as compatible in the AMM. Many effective disinfectants can be harmful to sensitive aircraft materials if not approved.
- Isopropyl Alcohol (IPA): A 70% aqueous solution is frequently recommended by OEMs like Boeing and Airbus for disinfecting high-touch surfaces. However, care must be taken on leather and porous materials, and IPA is flammable, so it should be applied via wipes or wetted cloths, never sprayed directly in the cabin.
- Other Chemicals: Quaternary Ammonium Compounds (QACs) and hydrogen peroxide-based disinfectants are also used, but only if specifically tested and approved for aviation use on the relevant surfaces. Bleach-based products are generally unsuitable due to corrosivity.
- Application Methods: Disinfectants are typically applied using pre-moistened wipes or by wetting single-use cloths, ensuring the surface remains wet for the manufacturer’s specified contact time. Pooling or dripping, especially near electronic components, must be avoided. Adequate ventilation during and after application is important. Some processes may require wiping away residue after the contact time.
- *Emerging Technologies: Ultraviolet (UV-C) light disinfection systems are sometimes used as a supplement to manual cleaning and disinfection. However, UV light only disinfects surfaces in its direct line of sight, can potentially degrade or discolor materials over long-term exposure, and its use requires consultation and approval from the aircraft OEM.
- Documentation: As with other maintenance tasks, cleaning and disinfection activities should be documented according to the operator’s procedures.
The need for effective disinfection adds a layer of complexity, requiring careful balancing of pathogen efficacy with the absolute necessity of ensuring chemical compatibility with all aircraft interior materials, guided by OEM recommendations.
Surface Type | Common Materials | Recommended Cleaning Method | Recommended Disinfection (If Approved) | Precautions | |
---|---|---|---|---|---|
Cockpit Displays/Instruments | Glass (coated), Plastic | Damp Microfiber (cleaner on cloth, not sprayed) | Approved Electronic/Screen Cleaner or Wipe | NO direct spraying; Verify chemical compatibility; Avoid abrasives | |
Carpets (Wool) | Wool, Wool Blend | Dry Cleaning (low moisture) or Hot Water Extraction (use caution) | Approved fabric-safe disinfectant mist (test first) | Avoid over-wetting; Potential shrinkage with water | |
Carpets (Synthetic) | Nylon, Polyester | Hot Water Extraction or Dry Cleaning | Approved fabric-safe disinfectant mist | Follow AMM/manufacturer guidance | |
Upholstery (Fabric) | Various Woven Textiles | Vacuuming, Spot Cleaning (test first), potentially Dry Cleaning | Approved fabric-safe disinfectant mist (test first) | Blot stains, don’t rub; Check colorfastness | |
Upholstery (Genuine Leather) | Natural Hide | Mild Aviation Leather Cleaner, Conditioning | 70% IPA Wipe (use caution) or other approved leather-safe disinfectant | Condition regularly; Avoid excess moisture/solvents | |
Upholstery (Synthetic Leather) | Coated Fabrics (Vinyl, Polycarbonate top coat) | Mild Soap/Surfactant Solution or Approved Cleaner | Approved disinfectant wipe (check compatibility) | Follow AMM; May not need conditioning | |
Sidewalls/Headliners | Fabric, Vinyl, Composite Panels | Damp Microfiber with Approved Interior Cleaner | Approved disinfectant wipe (check material) | Avoid saturation; Gentle wiping | |
Wood Veneer | Wood Layer with Finish | Dry Dusting; Damp Cloth (mild soap if needed, dry immediately) | Check AMM – Disinfectants may damage finish | AVOID excess moisture; Wipe with grain | |
Galley Surfaces | Stainless Steel, Laminate | Approved Cleaner/Degreaser | Approved Food-Safe Disinfectant (follow contact time/rinse req.) | Clean before disinfecting; Prevent cross-contamination | |
Lavatory Surfaces | Plastic, Metal, Composites | Approved Cleaner/Disinfectant | Approved Disinfectant (ensure full contact time) | Clean top-down, clean-to-dirty; Use separate tools |
5. Advanced Technical Cleaning Procedures
Certain aircraft cleaning tasks go beyond standard detailing and fall into the realm of specialized technical cleaning, often focused on maintaining the performance and integrity of critical systems like engines or addressing particularly stubborn contamination.
Engine Washing: Methods and Benefits
Regular washing of turbine engines is a crucial maintenance practice, not merely a cosmetic one.
- Purpose: Over time, airborne contaminants like dirt, dust, salt (in marine environments), pollen, and pollutants are ingested by turbine engines and accumulate on internal components, particularly compressor blades and stators. This buildup disrupts airflow, reduces compressor efficiency, increases the Exhaust Gas Temperature (EGT) required for a given thrust level, decreases fuel efficiency, and can accelerate component wear and corrosion. Engine washing removes these deposits, helping to restore lost performance margins (e.g., lowering EGT), improve fuel efficiency, and extend the time-on-wing for engine components.
- Methods: Several methods are employed for engine washing, often requiring specialized equipment like spray ring manifolds inserted into the engine inlet:
- Water Wash: The simplest method involves spraying atomized quantities of clean, often demineralized, water into the engine while it is motored (rotated by the starter without ignition). The water helps to dissolve or dislodge contaminants.
- Chemical Wash: This method enhances cleaning effectiveness by mixing approved cleaning solutions (often meeting specifications like MIL-PRF-85704) with the wash water. These chemicals help break down more stubborn deposits like grease or baked-on grime. A thorough rinse cycle with clean water is essential afterward to remove all chemical residues.
- Dry Ice Blasting (CO2 Blasting): A more modern, waterless technique involves propelling small pellets of solid carbon dioxide (dry ice) at high velocity into the engine’s gas path. Upon impact with warmer engine components, the dry ice pellets sublimate (turn directly from solid to gas), and the rapid gas expansion creates a ‘micro-explosion’ effect that lifts contaminants off the surface. This method is non-abrasive, non-conductive, non-toxic, leaves no chemical or water residue (eliminating drying time and corrosion concerns from residual water), and generates no secondary waste. It is effective at removing oils, grease, carbon, and other deposits without requiring engine disassembly and is safe for sensitive parts.
Engine washing is a technical maintenance procedure directly impacting engine health and operational economics. The choice of method involves trade-offs between cleaning effectiveness, environmental considerations (water use, chemical disposal), cost, and potential risks (e.g., ensuring complete drying after water/chemical wash). Dry ice blasting represents an advanced, environmentally friendly alternative gaining traction in the industry.
Belly Degreasing: Tackling Stubborn Grime
The underside, or belly, of an aircraft is notoriously prone to accumulating heavy, stubborn contamination.
- Problem Area: This area collects a mixture of grease, engine oil blow-by, hydraulic fluid leaks, exhaust soot (especially near engines and APU exhausts), dirt, and runway grime. This buildup can become baked-on and difficult to remove with standard washing procedures.
- Importance: Besides being unsightly, heavy buildup on the aircraft belly can trap moisture against the skin, promoting corrosion. It can also conceal structural defects or leaks, hindering effective inspection, and adds unnecessary weight to the aircraft.
- Procedure: Effectively cleaning the aircraft belly typically requires heavy-duty degreasing agents formulated specifically for aviation use. These products must be potent enough to dissolve baked-on grease and soot but also compatible with aircraft aluminum alloys, paints, sealants, and composite materials. Look for products meeting relevant military specifications like MIL-PRF-85570 (Type 5 mentioned as effective exterior cleaner) or MIL-PRF-87937 (Type IV qualified for heavy-duty cleaning/degreasing). Commercially available examples mentioned by users or suppliers include Turbine Soot Master, Simple Green Extreme Aircraft & Precision Equipment Cleaner, Carbon X, or Cortec VpCI-415. The procedure generally involves:
- Applying the degreaser according to manufacturer instructions. Dilution ratios often vary depending on the severity of the contamination (e.g., 1:4 for heavy soils with MIL-PRF-85570 Type 5, or 20% solution for heavy cleaning with VpCI-415). Application can be via sprayer, brush, or foam generator.
- Allowing adequate dwell time for the chemical to penetrate and break down the grease and soot.
- Agitating stubborn areas with soft brushes or non-abrasive pads. Plastic scrapers may be used carefully for very thick deposits.
- Thoroughly rinsing with water (if the product requires it) or wiping clean according to product directions. Appropriate Personal Protective Equipment (PPE), such as gloves and eye protection, should always be worn when handling potent degreasers.
Belly degreasing requires a careful balance: using chemistry strong enough for the task while ensuring it is safe for the aircraft structure and compliant with environmental regulations.
6. Convenience on the Go: Mobile Aircraft Detailing Services
Recognizing the logistical challenges of moving aircraft solely for cleaning, many professional detailing providers offer mobile services, bringing their expertise and equipment directly to the aircraft’s location.
- Service Offering: Mobile aircraft detailing units operate as self-contained service providers, traveling to airports, FBOs (Fixed-Base Operators), or private hangars to perform cleaning and detailing tasks on-site. This eliminates the need for the owner or operator to reposition the aircraft specifically for detailing.
- Logistics and Capabilities: These mobile units are typically equipped with the necessary tools, supplies, and a range of approved cleaning products to perform various services. Common mobile offerings include exterior dry washing, interior cleaning and detailing, leather conditioning, brightwork polishing, and sometimes more advanced services like paint sealant or ceramic coating application and cabin disinfection. The logistics involve transporting all equipment (buffers, vacuums, extractors, ladders/scaffolding), products, water (if needed for specific tasks and permitted), and waste containment systems. Mobile providers must also coordinate airport access, security badging, and adhere to all local airport operating procedures. Some providers may have defined service areas based on proximity to their home base.
- Advantages: The primary advantage is convenience. Mobile services minimize aircraft downtime associated with repositioning for cleaning and allow detailing to be scheduled more flexibly around the aircraft’s operational schedule. They provide access to professional detailing services even if the aircraft is based at an airport without dedicated FBO detailing facilities.
- Considerations: When choosing between a mobile detailer and an FBO’s in-house service, consider factors like cost, scope of services offered, and technician experience. FBOs might offer slightly lower pricing if the aircraft is already hangared there and may have dedicated infrastructure like wash racks with water treatment. However, FBO detailing staff might have broader line service duties, whereas mobile specialists often focus exclusively on detailing, potentially offering deeper expertise in advanced techniques like paint correction or ceramic coatings. It is essential to verify that any mobile provider has adequate insurance coverage and the necessary permissions to operate at the specific airport location.
Mobile detailing offers a valuable, convenient solution for aircraft owners and operators. While providing maximum flexibility, these services must navigate logistical complexities and ensure they consistently deliver the same high standards of quality, material compatibility, and regulatory compliance expected from any professional aircraft detailing operation.
7. Why Professional Aircraft Cleaning is Non-Negotiable
While the idea of saving costs through DIY cleaning or hiring less specialized services might seem tempting, the unique nature of aircraft materials, the stringent regulatory environment, and the paramount importance of safety make professional aircraft detailing services not just a luxury, but a necessity. Entrusting this task to qualified professionals mitigates significant risks and provides tangible benefits.
- Expertise in Regulations and Material Science: Professional aircraft detailers, particularly those employing or supervised by certified A&P mechanics where required, possess essential knowledge of the governing regulations (FAA/EASA) and the specific procedures mandated by Aircraft Maintenance Manuals (AMMs). They understand the critical importance of material compatibility, possessing the expertise to select the correct, aviation-approved chemicals and techniques for each specific surface – from sensitive cockpit displays and acrylic windows to various metal alloys, composites, leathers, and fabrics – thereby avoiding costly and potentially dangerous damage. This knowledge extends beyond simple cleaning to encompass proper disinfection protocols and environmental compliance.
- Access to Specialized Tools and Approved Products: Achieving professional results safely and efficiently requires specialized equipment that is often beyond the reach or justification of individual owners. This includes industrial-grade carpet extractors, specialized buffers and pads for paint correction and brightwork polishing, foam application systems, and potentially advanced tools like dry ice blasting equipment. Furthermore, professionals maintain inventories of specifically approved, often high-cost, aviation cleaning agents, degreasers, polishes, sealants, conditioners, and disinfectants that are not typically available in retail channels.
- Risk Mitigation: Avoiding Costly Damage: The potential for causing damage through improper cleaning techniques or incompatible products is substantial. Amateurs or non-aviation detailers unfamiliar with aircraft specifics risk:
- Corroding metal structures with improper chemicals.
- Damaging expensive paint finishes through aggressive buffing or harsh solvents.
- Irreversibly crazing or clouding acrylic windows.
- Staining or shrinking delicate interior fabrics or carpets.
- Drying out or discoloring leather upholstery.
- Damaging sensitive cockpit electronics or displays. Professional detailers are trained to avoid these pitfalls. Moreover, reputable companies carry substantial liability insurance to cover accidental damage, offering a level of financial protection often absent with unqualified providers.
- Ensuring Airworthiness and Safety Compliance: As established, aircraft cleaning is often classified as regulated maintenance. Using certified professionals ensures compliance with FAA and EASA regulations, particularly the requirement for A&P mechanic oversight and sign-off for Part 121 and 135 operations. Beyond mere compliance, proper cleaning performed by knowledgeable technicians directly contributes to safety by ensuring effective inspections can take place and by preventing material degradation that could compromise structural integrity or system function over time.
- Efficiency and Quality: Experienced professionals, equipped with the right tools and knowledge, can typically complete detailing tasks far more efficiently and to a significantly higher standard than amateurs. Their familiarity with different aircraft types and common problem areas allows them to work systematically and achieve consistent, high-quality results.
Aircraft are high-value, complex machines operating in a demanding environment governed by strict safety regulations. While professional detailing represents an operational cost, it is a critical investment in preserving the aircraft’s value, ensuring its safe operation, maintaining regulatory compliance, and optimizing its performance.
The potential costs associated with damage caused by improper cleaning – encompassing repairs, downtime, diminished value, regulatory penalties, and compromised safety – far outweigh the expense of hiring qualified, experienced, and certified professionals.
For the care and maintenance of your aircraft, accepting anything less than professional expertise is an unnecessary and potentially hazardous gamble!