Confined space cleaning operations represent some of the most hazardous tasks undertaken in industrial, commercial, and even residential settings. These are not routine cleaning jobs; they involve entering and working within spaces characterized by limited access and egress, and which are not designed for continuous human occupancy. The risks are manifold, ranging from life-threatening atmospheric conditions to severe physical injuries.
This guide provides a comprehensive overview of confined space cleaning, detailing the regulatory landscape, hazard identification, essential safety procedures, specific cleaning techniques, and critically, why such tasks are best entrusted to highly trained and properly equipped professionals.
Contact us!
I. Defining the Danger Zone: What is Confined Space Cleaning?
Understanding the precise definition of a confined space and the regulatory distinctions that apply is the first and most critical step in ensuring safety during cleaning operations. Misclassification or a lack of understanding can lead to inadequate precautions and potentially fatal consequences.
A. Understanding Confined Spaces: OSHA and International Perspectives
The term “confined space” is formally defined by occupational safety authorities worldwide, with a strong consensus on its core characteristics. These definitions are foundational to recognizing and managing the inherent dangers.
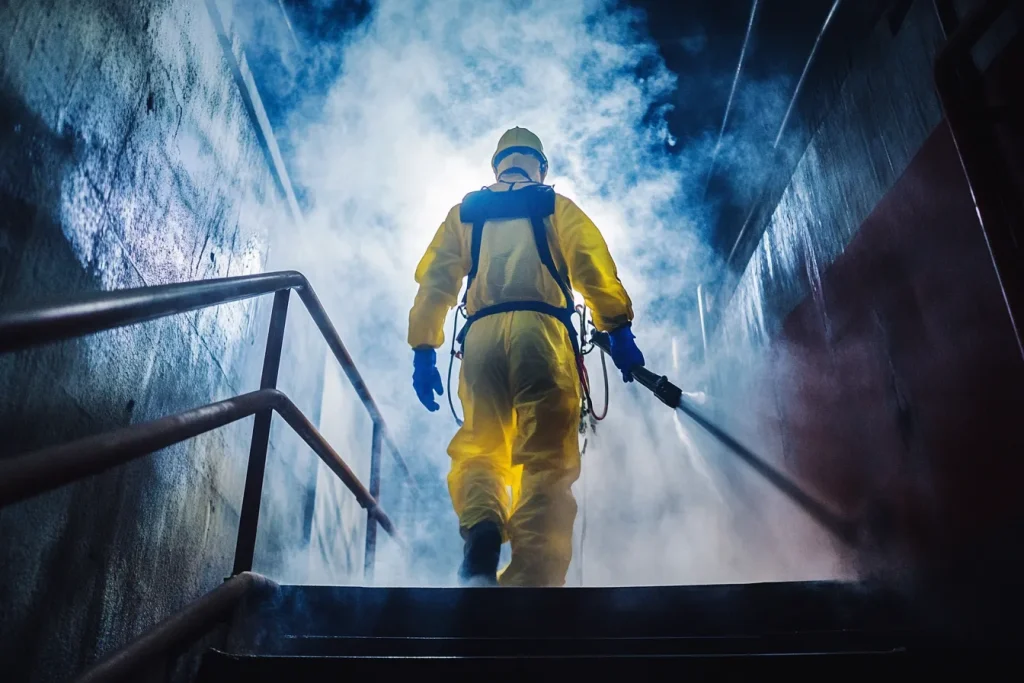
In the United States, the Occupational Safety and Health Administration (OSHA) provides a clear and legally binding definition for general industry under 29 CFR 1910.146. According to OSHA, a space is considered a “confined space” if it meets all three of the following criteria :
- It is large enough and so configured that an employee can bodily enter and perform assigned work.
- It has limited or restricted means for entry or exit (examples include tanks, vessels, silos, storage bins, hoppers, vaults, and pits).
- It is not designed for continuous employee occupancy.
The “configuration” aspect of the OSHA definition is particularly important. It’s not merely the size of the space but its internal layout—such as inwardly converging walls or complex internal structures—that can contribute to its hazardous nature, potentially leading to entrapment or complicating rescue efforts. This extends beyond the simple notion of limited entry or exit.
Furthermore, the criterion that a space is “not designed for continuous occupancy” signals inherent deficiencies for sustained human presence. Such spaces typically lack adequate natural ventilation, ergonomic design for work, or readily accessible emergency exits, meaning any entry necessitates special, non-routine safety measures.
This understanding of confined spaces is not unique to the U.S. International regulatory bodies offer similar definitions, underscoring the universal nature of the associated hazards.
- The UK Health and Safety Executive (HSE) defines a confined space as “a place which is substantially enclosed (though not always entirely), and where serious injury can occur from substances or conditions within the space or nearby (e.g., lack of oxygen)”. The HSE also identifies specified risks such as fire, explosion, loss of consciousness, asphyxiation, and drowning.
- Safe Work Australia describes a confined space as “an enclosed or partially enclosed space that: is not intended to be occupied by a person and is likely to involve risks to health and safety from: a lack of oxygen, contaminants such as airborne gases, vapours and dusts, or getting buried or crushed”.
- The U.S. National Institute for Occupational Safety and Health (NIOSH), while not a regulatory agency like OSHA, provides influential guidance and defines a confined space by emphasizing its limited openings for entry and exit, unfavorable natural ventilation which could contain or produce dangerous air contaminants, and its unsuitability for continuous worker occupancy.
The consistent themes of enclosure, restricted access, unsuitability for continuous human presence, and the foreseeable presence of serious risks across these international definitions highlight that the dangers are globally recognized. This implies that the fundamental principles for ensuring safety in these environments will also share common ground, emphasizing thorough risk assessment and meticulous control measures.
B. Permit-Required Confined Spaces (PRCS) vs. Non-Permit Confined Spaces: Critical Distinctions for Cleaning Operations
Within the broad category of confined spaces, OSHA makes a critical distinction that dictates the stringency of safety protocols: Permit-Required Confined Spaces (PRCS), often referred to as “permit spaces,” and Non-Permit Confined Spaces.
A Permit-Required Confined Space (PRCS) is a confined space that exhibits one or more of the following hazardous characteristics :
- It contains or has the potential to contain a hazardous atmosphere.
- It contains a material that has the potential for engulfing an entrant.
- It has an internal configuration such that an entrant could be trapped or asphyxiated by inwardly converging walls or by a floor which slopes downward and tapers to a smaller cross-section.
- It contains any other recognized serious safety or health hazard (e.g., unguarded machinery, exposed live wires, extreme temperatures).
Entry into a PRCS is subject to the comprehensive requirements of OSHA’s 29 CFR 1910.146, which mandates a written permit space program and a detailed entry permit for each instance of entry. Cleaning operations undertaken in such spaces are inherently high-risk and demand the utmost caution and adherence to these regulations. The emphasis on the “potential to contain” a hazard is significant.
Risk assessment for PRCS cannot be based solely on the conditions observed at a given moment but must consider what could develop. For example, cleaning activities might disturb settled materials, releasing toxic gases, or introduce flammable vapors from cleaning agents, thereby realizing a potential hazard. This proactive identification is vital for preventing incidents, as conditions within a confined space can deteriorate rapidly and unexpectedly.
A Non-Permit Confined Space, by contrast, is a confined space that does not contain, nor does it have the potential to contain (with respect to atmospheric hazards), any hazard capable of causing death or serious physical harm. While the regulatory burden for non-permit spaces is less stringent, entry still demands caution. It’s crucial to recognize that the classification of a confined space is not static.
A PRCS can be reclassified as a non-permit space if all hazards are eliminated and specific OSHA procedures are followed, including atmospheric testing even if the only perceived hazard is atmospheric and controllable by ventilation. Conversely, changes in the use or configuration of a non-permit space, or the introduction of new materials or processes (including cleaning), can transform it into a PRCS. This dynamic nature means that ongoing vigilance and hazard re-assessment are essential, particularly before and after cleaning operations which might alter the space’s internal environment or residues.
The “any other recognized serious safety or health hazard” clause in the PRCS definition serves as an important catch-all, compelling employers to adopt a broad perspective on hazard awareness. It means that assessments must extend beyond atmospheric or engulfment risks to include mechanical, electrical, thermal, and any other hazards that could cause serious harm.
For cleaning tasks, this could involve considering the chemical reactivity of cleaning agents with existing residues or the physical dangers posed by the cleaning equipment itself within the restrictive environment.
C. Common Confined Spaces Requiring Specialized Cleaning
Confined spaces are ubiquitous across numerous industries and can also be found in commercial and residential properties. Cleaning these spaces is often necessary for maintenance, inspection, product changeover, or hygiene. The user query specifically highlighted tanks, pits, sumps, trenches, manholes, vaults, and ductwork, all of which are common examples.
Other examples include, but are not limited to: vessels, silos, storage bins, hoppers, tunnels, equipment housings, pipelines, boilers, furnaces, septic tanks, crawl spaces, and attics. The U.S. Department of Labor provides extensive lists of such spaces found in diverse sectors like agriculture (grain silos), food processing (bins, cookers), manufacturing (chemical tanks, dust collectors), and utilities (manholes, vaults).
The purpose for which a confined space was designed and used largely dictates the types of residues, contaminants, and inherent hazards that cleaning personnel will encounter. For example, a grain silo presents significant risks of engulfment by flowing grain and potential for combustible dust explosions. A chemical storage tank, on the other hand, is more likely to harbor hazardous atmospheres from residual vapors and chemical exposure risks from sludge or wall residues. Sewer manholes often contain oxygen-deficient atmospheres, toxic gases like hydrogen sulfide and methane, and biological hazards from waste. Even spaces accessed for “routine” maintenance, such as HVAC ductwork or sumps, can pose severe risks; ductwork can harbor mold and airborne particulates , while sumps can accumulate hazardous sludge and develop dangerous atmospheres. The frequency of access to such spaces does not diminish the need for rigorous confined space entry procedures.
The following table illustrates some common confined spaces and their associated cleaning challenges:
Type of Confined Space | Common Contents/Residues | Primary Cleaning Challenges | Key Safety Concerns |
---|---|---|---|
Storage Tanks (Chemicals/Fuel) | Chemical residues, sludge, volatile organic compounds (VOCs) | Complete removal for product change/inspection, preventing reactions | Hazardous atmosphere (toxic/flammable), chemical exposure, fire/explosion, engulfment |
Sewer Manholes & Wet Wells | Organic waste, silt, debris, wastewater | Removal of blockages, sanitation, sediment removal | Oxygen deficiency, toxic/flammable gases (H$_{2}$S, CH$_{4}$), biological hazards, engulfment |
HVAC Ductwork | Dust, mold, bacteria, allergens, construction debris | Access to entire system, preventing contaminant spread | Airborne particulates, biological hazards, working in restricted positions |
Pits/Sumps (Industrial/Utility) | Water, sludge, oil, chemical residues, debris | Pumping out liquids, removing heavy solids, decontamination | Engulfment, slip/trip hazards, hazardous substances, oxygen deficiency |
Underground Utility Vaults | Water, mud, debris, cables, potentially leaking substances | Dewatering, debris removal, cleaning around sensitive equipment | Electrical hazards (if electrical), atmospheric hazards, engulfment, structural integrity |
Silos & Hoppers (Grain/Powders) | Grain, feed, powders, dust | Removal of hung-up material, cleaning walls, preventing bridging | Engulfment by flowable solids, combustible dust explosion, oxygen deficiency |
This table provides a snapshot, but each specific confined space requires its own detailed hazard assessment before any cleaning work commences, as emphasized by guidelines for tank cleaning which stress evaluating the purpose of the space and its cleaning requirements.
II. Unmasking the Risks: Comprehensive Hazard Identification
A paramount aspect of confined space safety is the thorough identification and assessment of all potential hazards. These hazards can be broadly categorized into atmospheric, physical, and chemical/biological, each capable of causing serious injury, illness, or death. Cleaning operations themselves can introduce new hazards or exacerbate existing ones.
A. Atmospheric Hazards: The Invisible Threats
Atmospheric hazards are often the most insidious and are a leading cause of fatalities in confined spaces. They are frequently invisible, may be odorless or cause olfactory fatigue (where the sense of smell is deadened), and can incapacitate a worker with alarming speed. It is crucial to understand that atmospheric conditions within a confined space are not static; they can change rapidly due to the work being performed (e.g., agitation of sludge, use of solvents), temperature fluctuations, or disturbances to residues. This dynamic nature underscores the necessity for continuous atmospheric monitoring in many scenarios, not just pre-entry checks. The inherent “unfavorable natural ventilation” of most confined spaces, as highlighted by NIOSH , means that any hazardous substances introduced or generated are likely to accumulate rather than disperse, thereby concentrating the danger and making forced ventilation a critical control.
Key atmospheric hazards include:
- Oxygen Deficiency: An atmosphere containing less than 19.5% oxygen by volume. This can be caused by the displacement of air by other gases (such as nitrogen or carbon dioxide used for purging, or methane generated by decomposition), consumption of oxygen through chemical reactions (e.g., rusting of metal surfaces ), biological processes (e.g., rotting of organic matter ), or combustion. Low oxygen levels can lead to impaired judgment, loss of coordination, nausea, unconsciousness, and ultimately, death.
- Oxygen Enrichment: An atmosphere containing more than 23.5% oxygen by volume. While less common, oxygen enrichment significantly increases the flammability of combustible materials. Some substances that do not burn in normal air may ignite vigorously or even spontaneously in an oxygen-enriched environment, posing a severe fire and explosion risk.
- Flammable/Explosive Atmospheres: These occur when flammable gases, vapors, or mists are present in concentrations exceeding 10% of their Lower Flammable Limit (LFL). Similarly, airborne combustible dust (from materials like grain, sugar, coal, wood, or certain metals) at a concentration that meets or exceeds its LFL can create an explosive atmosphere. OSHA notes that a combustible dust concentration may be approximated as a condition in which the dust obscures vision at a distance of 5 feet (1.52 m) or less. If an ignition source is present, a fire or violent explosion can occur, potentially causing severe burns, traumatic injuries from flying debris, and structural collapse.
- Toxic Contaminants: These include a wide array of gases, vapors, fumes, or dusts present at concentrations that exceed OSHA’s Permissible Exposure Limits (PELs) or other recognized occupational exposure limits, such as Threshold Limit Values (TLVs) from the American Conference of Governmental Industrial Hygienists (ACGIH). Common examples encountered during cleaning or from previous contents include:
- Carbon Monoxide (CO): A colorless, odorless gas produced by incomplete combustion. It interferes with the blood’s ability to carry oxygen.
- Hydrogen Sulfide (H$_{2}$S): A colorless gas with a characteristic rotten egg odor at low concentrations, but which causes olfactory fatigue at higher, more dangerous levels. It is highly toxic and flammable, often found in sewers, manure pits, and spaces where organic matter decomposes.
- Solvents: Vapors from cleaning agents like trichloroethylene, benzene, or other volatile organic compounds (VOCs) used for degreasing or cleaning can be toxic and may also be flammable.
- Process-Related Contaminants: Residues from materials previously stored or processed in the space, such as ammonia, chlorine, or acids, can release toxic gases or vapors, especially when disturbed during cleaning. Exposure to toxic contaminants can cause a range of acute health effects, from irritation and dizziness to severe respiratory distress, organ damage, incapacitation, or death.
- Immediately Dangerous to Life or Health (IDLH) Atmospheres: This refers to any atmospheric condition that poses an immediate or delayed threat to life, would cause irreversible adverse health effects, or would interfere with an individual’s ability to escape unaided from a permit space. An IDLH atmosphere could result from any of the above conditions (severe oxygen deficiency, high flammability, or high toxicity).
It’s also important to recognize the interconnectedness of these atmospheric hazards. For instance, a flammable vapor, if ignited, can rapidly consume oxygen, leading to an oxygen-deficient atmosphere, while simultaneously producing toxic combustion byproducts like carbon monoxide. A comprehensive risk assessment must consider these potential chain reactions.
B. Physical Hazards: Beyond the Air You Breathe
Beyond atmospheric dangers, confined spaces often present a multitude of physical hazards related to their structure, contents, or associated energy sources. Cleaning operations can inadvertently introduce new physical hazards or exacerbate existing ones. These hazards can cause immediate, severe trauma and can significantly impede self-rescue or assisted rescue efforts.
Key physical hazards include:
- Engulfment: This occurs when a person is surrounded and effectively captured by a liquid or a finely divided (flowable) solid substance, such as grain, sand, coal, sawdust, cement, or sludge. Engulfment can lead to death by asphyxiation (filling or plugging the respiratory system) or by crushing, strangulation, or constriction from the material’s force. This is a prominent risk in silos, bins, hoppers, tanks containing sludge, pits, and trenches where loose materials are present or can shift. The act of cleaning, such as dislodging caked material, can trigger an engulfment.
- Entrapment/Internal Configuration: The internal design of a confined space can itself be a hazard. Spaces with inwardly converging walls, or floors that slope downward and taper to a smaller cross-section, can trap an entrant, potentially leading to asphyxiation if movement is restricted. The limited entry and exit points characteristic of confined spaces also contribute to entrapment risks.
- Mechanical Hazards: These involve contact with moving parts of machinery or equipment within or connected to the confined space. Examples include unguarded agitators, mixers, augers, conveyors, or rotating shafts that could inadvertently activate while a worker is inside.
- Electrical Hazards: The presence of exposed live electrical wires, damaged insulation, faulty electrical equipment, or conductive surfaces can lead to electric shock or electrocution. Cleaning with water-based solutions in areas with electrical components presents a heightened risk.
- Thermal Hazards: Exposure to extreme temperatures, either hot or cold, can pose a significant risk. This can stem from the space itself (e.g., a boiler, furnace, or refrigerated unit), the processes conducted within or nearby, or the cleaning methods employed (e.g., steam cleaning ). Heat stress, heat stroke, or hypothermia can quickly incapacitate a worker.
- Falls: Workers can fall from a height into a confined space, or slip, trip, and fall within the space due to uneven, wet, or slippery surfaces often created during cleaning operations. The consequences of a fall can be compounded by the difficulty of rescue.
- Noise: Excessive noise levels generated by cleaning equipment (e.g., pressure washers, pneumatic tools, vacuums) or adjacent industrial processes can damage hearing and, critically, interfere with essential communication between the entrant and the attendant.
- Falling Objects: Tools, equipment, debris, or dislodged materials from the walls or ceiling of the space can fall onto entrants, causing impact injuries. Cleaning activities, such as scraping or high-pressure washing, can increase this risk.
- Limited Visibility: Inadequate lighting is common in confined spaces and can obscure hazards, leading to trips, falls, or contact with unseen dangers. Cleaning can also stir up dust or create mists that reduce visibility.
- Structural Hazards: The confined space itself may have compromised structural integrity, posing a risk of collapse. Accumulated materials or the forces applied during cleaning could also destabilize parts of the structure.
Physical hazards can directly worsen atmospheric conditions (e.g., engulfment by a fine powder creating a dust cloud) or severely hinder rescue efforts if a worker is injured or trapped. Furthermore, the cleaning equipment itself, such as hoses and power cords, can introduce trip hazards in an already congested environment. While not always formally categorized as “physical” hazards by regulatory bodies, psychological factors such as claustrophobia, or fear of darkness or heights, can significantly impair a worker’s judgment, ability to follow safety procedures, or capacity for self-rescue, thereby indirectly increasing the overall risk. This suggests the importance of careful worker selection and awareness of individual limitations.
C. Chemical and Biological Hazards in Cleaning Operations
Cleaning operations in confined spaces inherently involve dealing with unwanted substances, which may include residues from materials previously stored or processed, as well as the cleaning agents themselves. These can present significant chemical and biological hazards.
Chemical Hazards:
- Residual Materials: Tanks, vessels, pipes, and sumps may contain residues of chemicals such as acids, caustics, solvents, petroleum products, or other hazardous substances. These residues can be present as liquids, sludges, or even absorbed into the porous walls of the container, potentially leaching out or off-gassing during cleaning.
- Cleaning Agents: Many industrial cleaning agents are themselves hazardous. Solvents, degreasers, acids, alkalis, and disinfectants can release toxic or flammable vapors, especially in poorly ventilated confined spaces. Direct contact with corrosive cleaning agents can cause severe skin or eye burns.
- Chemical Reactions: A critical and often overlooked danger is the potential for hazardous chemical reactions. Cleaning agents might react with residual materials in the space, or even with each other if improperly mixed, generating toxic gases, flammable atmospheres, or excessive heat. For example, mixing chlorine-based cleaners with acidic cleaners can release highly toxic chlorine gas. The “cleaned” state of a space does not always equate to a “safe” state from a chemical perspective. Residual cleaning chemicals or substances leached from porous surfaces can continue to off-gas, requiring thorough ventilation and re-testing even after the bulk cleaning is complete. Workers may also face synergistic health effects if exposed to multiple chemicals simultaneously (e.g., residues and cleaning agents), where the combined impact is greater than the sum of individual effects. This complexity often requires expert industrial hygiene assessment.
Biological Hazards:
- Microbial Growth: Confined spaces that are damp, dark, or have contained organic matter are prone to biological contamination. This includes molds, fungi, bacteria, and viruses, which can thrive in environments like HVAC ductwork, sumps, cooling towers, sewers, and tanks that held food products or organic waste.
- Pathogens in Waste: Sludge, wastewater, and other deposits can harbor pathogenic microorganisms.
- Health Effects: Exposure to biological hazards can occur through inhalation of airborne spores or microorganisms, skin contact, or ingestion. This can lead to infections, allergic reactions, asthma attacks, or other respiratory illnesses. Cleaning processes, particularly those involving water, agitation, or high-pressure spraying (e.g., in duct cleaning ), can aerosolize biological contaminants, increasing their concentration in the air and heightening the risk of inhalation, even if initial contamination levels appeared low.
Understanding the specific chemical and biological nature of the contaminants and cleaning agents is essential for selecting appropriate personal protective equipment (PPE), choosing safe cleaning methods, and preventing adverse health effects or dangerous reactions.
D. The Importance of Thorough Risk Assessment Before Any Cleaning Commences
A comprehensive risk assessment is the bedrock of any safe confined space cleaning operation and is a mandatory requirement by regulatory bodies like OSHA and Safe Work Australia. OSHA specifically requires employers to evaluate the workplace to identify permit-required confined spaces, a task that must be performed by a “competent person” with the requisite training and authority to identify hazards and implement corrective actions.
The risk assessment process must be systematic and meticulous, identifying all potential hazards – atmospheric, physical, chemical, and biological – that are associated with both the specific confined space and the planned cleaning activities. This involves considering:
- The current and previous contents of the space.
- Any residues or sludges present.
- The structural integrity and internal configuration of the space.
- Potential sources of ignition.
- Hazards that could be introduced or generated by the cleaning work itself (e.g., vapors from solvents, dust from scraping).
- External factors that could affect the space (e.g., adjacent work activities, weather conditions).
The findings of this risk assessment directly inform the development of the confined space entry permit, the selection of appropriate hazard control measures (such as ventilation or isolation), the specific PPE required for workers, and the formulation of emergency and rescue procedures. A failure to conduct a thorough and accurate risk assessment is a primary contributing factor to confined space incidents and fatalities.
It is critical to understand that risk assessment is not a static, one-time checklist completed before entry. It is an iterative process. The assessment must be reviewed and, if necessary, revised whenever conditions change, if new hazards are identified during the work, or if the planned work activities are modified. If prohibited or unforeseen hazardous conditions arise during entry, the permit may be voided, and the space must be re-evaluated before re-entry is permitted. This dynamic approach ensures that safety measures remain relevant and effective throughout the entire operation.
Furthermore, a robust risk assessment must consider the potential interaction of various hazards. Hazards rarely exist in isolation. For example, using a flammable solvent (chemical hazard) in a poorly ventilated space (a condition that promotes atmospheric hazard accumulation) near a potential ignition source (a component of a physical hazard) creates a significantly higher risk profile than any of these factors considered individually. The competent person conducting the assessment must have the expertise to recognize these dangerous combinations and ensure appropriate controls are implemented. The quality and thoroughness of the entire confined space safety program hinge on the capabilities and diligence of this competent person.
III. The Safety Framework: Essential Procedures for Confined Space Cleaning
A robust safety framework, built upon established regulatory requirements and best practices, is indispensable for any cleaning operation involving confined spaces. This framework encompasses a formal permit-to-work system, meticulous pre-entry protocols, appropriate personal protective equipment, and well-defined roles and emergency plans.
A. The OSHA Permit-to-Work System: A Cornerstone of Safety
For all permit-required confined spaces (PRCS), OSHA mandates that employers develop and implement a comprehensive written permit space program, as detailed in 29 CFR 1910.146. A central and critical element of this program is the entry permit. This document is more than just paperwork; it is a formal authorization and a systematic safety checklist that verifies all necessary precautions have been identified, implemented, and are functioning correctly before any employee enters a high-hazard environment. The permit system serves to control entry strictly and ensures that all known and potential hazards are addressed.
Employer Responsibilities under the permit system are extensive and include:
- Developing, implementing, and maintaining a written permit space program.
- Identifying all PRCS in the workplace and informing exposed employees of their existence, location, and the dangers they pose. This is often achieved by posting clear danger signs (e.g., “DANGER—PERMIT-REQUIRED CONFINED SPACE—AUTHORIZED ENTRANTS ONLY”) at each access point.
- Taking effective measures to prevent unauthorized entry into PRCS.
- Ensuring that a fully completed entry permit is prepared before each entry, authorized by a designated entry supervisor, and prominently posted at the entrance to the permit space for the duration of the entry operations.
- Ensuring that the entry permit is voided and entry operations cease if conditions deviate from those specified on the permit or if new, unevaluated hazards arise.
The content of an OSHA-compliant entry permit is specified in 29 CFR 1910.146(f) and must include, at a minimum, the following information:
- Identification of the permit space to be entered.
- The specific purpose of the entry.
- The date of entry and the authorized duration of the entry permit.
- The names or an effective means of identifying all authorized entrant(s).
- The names or an effective means of identifying all attendant(s).
- The name of the current entry supervisor, with a space for their signature or initials.
- A comprehensive list of the hazards identified within the permit space.
- The measures implemented to isolate the permit space and to eliminate or control the identified hazards before entry (e.g., lockout/tagout procedures, purging, inerting, flushing, ventilation).
- The acceptable entry conditions that must be maintained within the space.
- The results of initial and periodic atmospheric tests, accompanied by the names or initials of the individuals performing the tests and the times the tests were conducted.
- The rescue and emergency services that can be summoned and the specific means for summoning them (e.g., communication equipment to use, emergency phone numbers).
- The communication procedures to be used by authorized entrants and attendants to maintain contact during the entry.
- A list of all equipment to be provided for the entry, such as personal protective equipment (PPE), testing equipment, communication equipment, alarm systems, and rescue equipment.
- Any other information deemed necessary by the employer to ensure employee safety.
- Any additional permits that have been issued to authorize work within the permit space, such as permits for hot work (welding, cutting, brazing).
This systematic approach ensures that all critical safety steps are methodically considered, implemented, and verified before personnel are exposed to the dangers of a PRCS. It formalizes lines of responsibility and channels of communication, which are vital in such high-risk operations. The permit is not just a pre-entry checklist; it functions as a “living document” throughout the entry, recording ongoing atmospheric test results and remaining valid only as long as the specified safe conditions are maintained. The requirement for signatures, particularly from the entry supervisor, drives accountability, creating a clear record of who authorized entry and under what verified conditions. A crucial go/no-go point is that the permit is not considered valid, and entry is prohibited, until all specified conditions and control measures are met and verified, regardless of whether the form itself has been filled out.
International regulations also emphasize formal systems for controlling entry into confined spaces.
- The UK HSE’s Confined Spaces Regulations 1997 and its associated Approved Code of Practice (ACOP) L101 heavily imply the need for a formal safe system of work, often fulfilled by a “Permit to Work”. Guidance suggests such permits are formal written documents specifying the work and precautions, detailing the task, location, work party, hazards, controls, PPE, approvals, validity period, and signatures for authorization, handover, and cancellation. This aligns closely with the elements of an OSHA entry permit. Companies operating under UK HSE regulations often require a signed permit-to-work before any confined space entry.
- Safe Work Australia also mandates an entry permit for most confined space entries under its model Work Health and Safety (WHS) Regulations. The model Code of Practice: Confined Spaces details the requirements for this permit system, which typically includes similar information to OSHA and HSE permits, focusing on space identification, the nature of the work, hazard identification and control, atmospheric monitoring results, personnel involved, emergency plans, and permit duration [ (Section 5.4)].
The following table compares key informational elements typically found on confined space entry permits under these major regulatory frameworks, demonstrating a high degree of international consensus on what constitutes a robust permit-to-work system:
Element | OSHA (29 CFR 1910.146(f)) | UK HSE | Safe Work Australia |
---|---|---|---|
Space Identification & Purpose of Entry | Yes | Yes (Description of task & exact location) | Yes |
Date & Authorized Duration | Yes | Yes (Time of issue and period of validity) | Yes |
Authorized Personnel (Entrants, Attendants, Supervisor) | Yes | Yes (Details of work party, person in charge) | Yes |
Hazard Identification | Yes | Yes (Details of potential hazards) | Yes |
Isolation & Control Measures Documented | Yes | Yes (Details of precautions given) | Yes |
Acceptable Entry Conditions Specified | Yes | Yes (Implicit in precautions/safe system) | Yes |
Atmospheric Test Results Recorded | Yes (Initial & periodic) | Implied | Yes (Monitoring conditions) |
Rescue & Emergency Plan & Contact Info | Yes | Implied | Yes |
Communication Procedures | Yes | Implied (Part of safe system) | Yes |
Required Equipment (PPE, Testing, etc.) | Yes | Yes (Details of protective equipment) | Yes |
Authorizing Signature(s) | Yes (Entry Supervisor) | Yes (Person issuing permit & person in charge) | Yes (Authorization to enter) |
Permit Cancellation/Closure | Yes (Implicit in duration & termination) | Yes (Declaration of work complete/incomplete, permit cancelled) | Yes (Permit closure) |
This comparison underscores that, despite minor variations in terminology or specific formatting, the core principles of a safe entry permit system—thorough hazard assessment, documented controls, clear responsibilities, and emergency preparedness—are universally recognized as essential for protecting workers in confined spaces.
B. Pre-Entry Protocols: Setting the Stage for Safety
Before any authorized personnel break the plane of entry into a permit-required confined space, a series of critical pre-entry protocols must be meticulously executed. These steps are designed to identify, evaluate, and control hazards, ensuring that the space is as safe as reasonably practicable for the planned cleaning operations.
- Atmospheric Testing: Sequence, Equipment, and Continuous Monitoring
Atmospheric testing is arguably the most critical pre-entry protocol, as unseen atmospheric hazards are a leading cause of fatalities in confined spaces. The purpose of this testing is twofold: to evaluate the potential hazards within the permit space and to verify that acceptable atmospheric conditions exist for entry.
OSHA mandates a specific testing order for atmospheric hazards :- Oxygen Content: The concentration of oxygen must be tested first. Normal atmospheric oxygen is approximately 20.9%. Acceptable levels for entry are typically between 19.5% (oxygen-deficient) and 23.5% (oxygen-enriched).
- Flammable Gases and Vapors: Next, the atmosphere is tested for the presence of flammable gases and vapors. These must be below 10% of their Lower Flammable Limit (LFL) for safe entry.
- Potential Toxic Air Contaminants: Finally, tests are conducted for known or suspected toxic air contaminants, such as carbon monoxide, hydrogen sulfide, or vapors from solvents. Concentrations must be below OSHA’s Permissible Exposure Limits (PELs) or other recognized occupational exposure limits (e.g., ACGIH TLVs).
This testing sequence is crucial because many flammable gas sensors require sufficient oxygen to operate accurately, and high concentrations of flammable gases can interfere with the readings of some toxic gas sensors.The equipment used for atmospheric testing must be appropriate for the hazards anticipated. Typically, multi-gas monitors capable of detecting oxygen, LFL, and common toxic gases (like CO and H$_{2}$S) are used, often equipped with an internal pump and probe to draw samples from different parts of the space without requiring initial entry. It is absolutely essential that this equipment is:
-
- Correctly calibrated according to the manufacturer’s recommendations before each day’s use, and bump tested (exposed to a known concentration of test gas) to verify sensor response. An uncalibrated or improperly functioning monitor can provide dangerously false readings, leading workers to believe a hazardous atmosphere is safe.
- Designed to detect the specific chemicals that may be present at concentrations well below their defined exposure limits.
- Operated correctly, allowing sufficient time for the air sample to be drawn into the instrument and for the sensors to react to any contaminants present. The “response time” of the equipment is a critical factor; workers must move slowly enough into untested areas to allow the monitor to analyze the atmosphere ahead of them.
Testing locations are also critical. Because different gases have different densities (some are heavier than air and sink, others are lighter and rise), the atmosphere must be tested at various levels within the space—typically top, middle, and bottom—to detect stratification. For deeper spaces or those with complex configurations or areas leading away from the entry point, the atmosphere may be layered or vary significantly in remote sections. In such cases, testing must be conducted in the area immediately surrounding the worker, often defined as a four-foot radius in the direction of travel and to each side. A quick “sniff test” at the manhole opening is dangerously insufficient.
Continuous monitoring of the atmosphere is often required throughout the duration of the entry, especially if conditions have the potential to change (e.g., due to the work being performed, temperature changes, or off-gassing from disturbed materials) or if forced air ventilation is being used as the primary means of controlling an atmospheric hazard.
If at any point during entry hazardous atmospheric conditions are detected by continuous monitoring or periodic retesting, all employees must immediately evacuate the space, and the space must be re-evaluated and hazards controlled before re-entry is permitted.
- Forced Air Ventilation: Techniques for Achieving a Safe Atmosphere
Forced air ventilation is a primary engineering control used to eliminate or control atmospheric hazards within a confined space, making it safe for entry and work. Its purpose is to replace contaminated, oxygen-deficient, or oxygen-enriched air with a continuous supply of fresh, breathable air, thereby reducing the concentration of flammable or toxic substances and maintaining safe oxygen levels. Under certain conditions, if the only hazard in a permit space is an actual or potential hazardous atmosphere that can be demonstrably made safe for entry using continuous forced air ventilation, OSHA allows for some relaxations of the full permit program requirements (e.g., no attendant or entry permit may be needed), though pre-entry atmospheric testing and verification of ventilation effectiveness are still mandatory.
Several ventilation techniques can be employed:- Positive Pressure Ventilation (PPV): This involves using a blower or fan to force fresh air into the confined space, thereby displacing the contaminated air, which is then pushed out through other openings. It is crucial that the intake air for PPV systems is drawn from a known fresh air source, well away from potential contaminants such as vehicle exhaust fumes or industrial emissions.
- Negative Pressure Ventilation (Exhaust Ventilation): This method uses a fan system to suck contaminated air out of the confined space. It is particularly useful if the space has only one opening. The exhausted air must be directed to a safe location where it will not pose a hazard to other workers or re-enter the confined space or other occupied areas.
- Combination (Push-Pull) Ventilation: This involves the coordinated use of both PPV to supply fresh air and exhaust ventilation to remove contaminated air, often providing more effective and controlled air exchange.
The general procedure for ventilation involves several steps :
-
- Test First: The atmosphere inside the confined space must be tested before ventilation begins. Ventilating prior to initial testing can dilute contaminants, potentially masking the true nature or source of a recurring atmospheric hazard.
- Purge: After initial testing, the space is purged with fresh air. The duration of this initial purge (often calculated to achieve a certain number of air changes, e.g., seven, or more if toxic gases were detected) depends on the volume of the space, the capacity (CFM – cubic feet per minute) of the ventilation equipment, and the nature and concentration of the contaminants. Nomographs or manufacturer data can help determine appropriate purge times.
- Retest: After the initial purge, the atmosphere must be retested to confirm that acceptable entry conditions have been achieved.
- Continuous Ventilation: For many entries, continuous ventilation is required throughout the occupancy of the space to maintain air quality, especially if work activities (like welding or using solvents) could generate new contaminants. An industry-accepted standard for continuous ventilation is often around 20 air changes per hour, though this can vary based on specific conditions.
- Proper Setup: Ductwork should be arranged to deliver fresh air directly to the area where employees are working or will be present. Care must be taken to avoid “short-circuiting,” where fresh air is exhausted before effectively ventilating the work zone. For long duct runs or those with multiple bends, booster fans may be necessary to maintain adequate airflow due to friction losses.
Ventilation equipment includes portable blowers, fans (which should be intrinsically safe if a flammable atmosphere is a potential risk ), and flexible ducting. It is important to realize that ventilation is an active control measure that requires ongoing management and verification. Simply turning on a fan is insufficient; the system’s effectiveness must be confirmed by atmospheric monitoring. Furthermore, the ventilation process itself can introduce hazards if not executed correctly, such as drawing in contaminated air or using non-intrinsically safe equipment in a flammable environment.
- Lockout/Tagout (LOTO): Isolating Hazardous Energy Sources
Isolating a confined space from all sources of hazardous energy and material ingress is a critical pre-entry step to prevent accidental activation of equipment or the release of substances that could harm entrants. This process is commonly referred to as Lockout/Tagout (LOTO). OSHA defines isolation as the process by which a permit space is removed from service and completely protected against the release of energy and material into the space.
Effective isolation methods include :- Blanking or blinding: Inserting solid barriers into pipelines or ducts.
- Misaligning or removing sections of lines, pipes, or ducts: Creating a physical break in the system.
- Double block and bleed system: Closing two valves in a line and opening a drain or vent valve between them to safely remove any leakage.
- Lockout or tagout of all sources of energy: This applies to electrical, mechanical, hydraulic, pneumatic, chemical, thermal, gravitational, or other stored energy sources that could affect the space.
OSHA’s standard 29 CFR 1910.147, “The Control of Hazardous Energy (Lockout/Tagout),” provides detailed requirements for LOTO procedures and is directly applicable to isolating energy sources connected to confined spaces. A comprehensive LOTO program involves more than just applying a lock and tag; it’s a system that includes :
-
- Written, often machine-specific, procedures for de-energization, isolation, and verification.
- Training for authorized employees (who perform LOTO) and affected employees (who operate the equipment).
- The use of standardized locks and tags.
- Periodic inspections of the procedures (at least annually).
- Clear assignment of responsibilities.
A crucial step in any LOTO procedure is the verification of isolation—physically attempting to start or operate the equipment after lockout to ensure it is truly de-energized and cannot be inadvertently activated. Isolation must account for all forms of hazardous energy that could impact the space, not just electrical power. This includes pipes carrying steam or chemicals, hydraulic or pneumatic systems, and even potential energy from suspended parts. For complex tasks involving multiple workers or trades, group lockout procedures are essential. These typically involve a group lockout box where each worker applies their personal lock; energy cannot be restored until every individual has completed their work and removed their lock, ensuring no one is endangered by premature re-energization.Failure to properly isolate hazardous energy sources can lead to instantaneous and fatal consequences for workers inside a confined space should equipment unexpectedly start or a hazardous substance be released.
C. Personal Protective Equipment (PPE): Tailoring to the Task and Hazards
Personal Protective Equipment (PPE) serves as the last line of defense for workers in confined spaces, employed when hazards cannot be entirely eliminated or controlled through engineering (like ventilation) or administrative (like procedures) means. The employer is responsible for providing all necessary PPE at no cost to the employee, ensuring it is appropriate for the identified hazards, properly maintained, and that employees are trained in its correct use, limitations, and care. The selection of PPE must be based on a thorough risk assessment of the specific confined space and the cleaning tasks to be performed. Using the wrong PPE can provide a false sense of security and be as dangerous as using no PPE at all.
Common PPE for Confined Space Cleaning includes:
- Respiratory Protection: This is often the most critical PPE due to the prevalence of atmospheric hazards. The type of respirator depends on the nature and concentration of contaminants and the oxygen level:
- Air-Purifying Respirators (APRs): These use filters or cartridges to remove specific contaminants (e.g., dusts, mists, certain vapors) from the air. They can only be used if there is sufficient oxygen (at least 19.5%) and the contaminant type and concentration are known and within the respirator’s capacity. Disposable dust masks (e.g., N95s) are a form of APR suitable for particulates.
- Supplied-Air Respirators (SARs): These deliver breathable air from a source outside the contaminated area (e.g., a compressor or air cylinders) through a hose. They are used when oxygen levels are deficient, contaminant concentrations are high, or the contaminants cannot be effectively filtered by an APR.
- Self-Contained Breathing Apparatus (SCBAs): These provide breathable air from a cylinder carried by the worker. SCBAs are essential for entry into Immediately Dangerous to Life or Health (IDLH) atmospheres, oxygen-deficient environments, or for rescue operations. Proper fit testing for respirators is mandatory to ensure a tight seal, and comprehensive training on use, donning, doffing, and maintenance is essential.
- Head Protection: Hard hats are necessary to protect against falling objects, bumps to the head from low ceilings or protrusions within the space.
- Eye and Face Protection: Safety glasses with side shields, chemical splash goggles, or full-face shields are required to protect against flying debris, dust, chemical splashes, and other impact hazards. Face shields should generally be worn in conjunction with safety glasses or goggles for enhanced protection.
- Hand Protection: Gloves must be selected based on the specific hazards. This can include:
- Chemical-resistant gloves (e.g., made of nitrile, neoprene, butyl rubber, or PVC) for handling cleaning chemicals or contaminated materials.
- Cut-resistant gloves (e.g., Kevlar® or high-performance polyethylene) for protection against sharp edges.
- Thermal gloves for protection against hot or cold surfaces or materials.
- General-purpose work gloves for abrasion resistance. In some situations, a combination of gloves (e.g., a chemical-resistant glove over a cut-resistant liner, or vice versa) may be necessary.
- Foot Protection: Chemical-resistant safety boots or shoes with slip-resistant soles and protective toe caps are typically required. Metatarsal guards may be needed if there’s a risk of objects falling on the top of the foot.
- Protective Clothing: The type of protective clothing depends on the nature of the contaminants and the work being performed. This can range from:
- Disposable coveralls to protect against dirt, dust, and minor splashes.
- Chemical-resistant suits or aprons for protection against hazardous chemical splashes or immersion.
- Flame-retardant clothing if there is a risk of flash fire.
- Waterproof clothing for wet environments or when dealing with biological hazards like black water.
- Fall Protection: If there is a risk of falling from a height into or within the confined space, or if retrieval is part of the emergency plan, a full-body harness and lifeline are essential. The lifeline may be attached to a retrieval system.
- Hearing Protection: Earplugs or earmuffs are necessary if noise levels from cleaning equipment or other sources exceed permissible exposure limits.
All PPE must be inspected before each use for any damage or defects, cleaned and disinfected if reusable, and stored properly according to manufacturer instructions. It is also important to consider that the PPE itself can impose burdens on the worker.
For example, SCBAs are heavy and can increase physical strain and heat stress; chemical suits can be hot and restrict movement; and respirators can make breathing more difficult and potentially cause claustrophobia. These factors must be incorporated into the overall risk assessment, including considerations for work duration, rest breaks, and worker suitability. Furthermore, the compatibility of multiple PPE items is crucial; for instance, a hard hat must not interfere with the seal of a respirator, and safety glasses should not cause fogging when worn under a face shield. All PPE items must function effectively together as an integrated system.
IV. The Human Element: Roles, Responsibilities, and Emergency Preparedness
Beyond procedures and equipment, the safety of confined space cleaning operations hinges critically on the human element: well-defined roles, clear responsibilities, effective communication, and robust emergency preparedness. OSHA’s regulations establish a team-based approach to confined space entry, ensuring multiple layers of oversight and support.
A. The Confined Space Entry Team: Defined Roles and Responsibilities (OSHA)
OSHA 29 CFR 1910.146 specifies distinct roles and responsibilities for personnel involved in permit-required confined space entries. These roles are interdependent, forming a system of checks and balances crucial for safety.
- Authorized Entrants
Authorized entrants are employees who have been explicitly authorized by the employer to enter a permit-required confined space. Their duties are critical for their own protection and include 1:- Knowing the hazards that may be faced during entry, including the mode, signs or symptoms, and consequences of exposure.
- Properly using all required equipment, such as atmospheric testing devices, communication systems, personal protective equipment, and any rescue equipment they are trained to use.
- Maintaining communication with the attendant as necessary to enable the attendant to monitor their status and to alert the attendant of any changes in conditions.
- Alerting the attendant immediately whenever they recognize any warning sign or symptom of exposure to a dangerous situation, or when they detect a prohibited condition within the space.
- Exiting the permit space as quickly as possible whenever an order to evacuate is given by the attendant or entry supervisor, an alarm is activated, or they perceive they are in danger.
- Being capable of conducting self-rescue if necessary and if they have been trained to do so.
Entrants are the individuals most directly exposed to the hazards of the confined space, and their awareness, training, and adherence to procedures are paramount.
- Attendants
Attendants are individuals stationed outside one or more permit spaces who continuously monitor the authorized entrants and perform all attendant duties assigned in the employer’s permit space program. The attendant acts as the entrants’ lifeline to the outside. Their responsibilities include 1:- Knowing the hazards that may be faced during entry, including information on the mode, signs or symptoms, and consequences of exposure, and being aware of the behavioral effects of hazard exposure in entrants.
- Maintaining an accurate and continuous count of authorized entrants in the permit space.
- Remaining outside the permit space during entry operations until relieved by another qualified attendant.
- Communicating with authorized entrants as necessary to monitor their status and to alert entrants of the need to evacuate the space. This can include using air monitoring equipment to keep a close watch on atmospheric conditions inside the space and communicating any observed changes.
- Monitoring activities inside and outside the space to determine if it is safe for entrants to remain in the space and ordering the entrants to evacuate immediately under any of the following conditions:
- If the attendant detects a prohibited condition.
- If the attendant observes behavioral effects of hazard exposure in an authorized entrant.
- If the attendant detects a situation outside the space that could endanger the authorized entrants.
- If the attendant cannot effectively and safely perform all their required duties.
- Summoning rescue and other emergency services as soon as the attendant determines that authorized entrants may need assistance to escape from permit space hazards.
- Warning unauthorized persons away from the permit space and informing them that they must exit immediately if they have entered the space.
- Performing no duties that might interfere with their primary duty to monitor and protect the authorized entrants. This means the attendant should not be involved in the work task being performed inside the space.
The attendant’s role is one of proactive monitoring and vigilance, not passive observation. The dangerous misconception that the attendant’s job is merely to stand by can lead to delayed responses in emergencies.
- Entry Supervisors
The entry supervisor is the person (such as the employer, foreman, or crew chief) responsible for determining if acceptable entry conditions are present at a permit space where entry is planned, for authorizing entry and overseeing entry operations, and for terminating entry as required. Their duties include 16:- Knowing the hazards that may be faced during entry, including information on the mode, signs or symptoms, and consequences of the exposure.
- Verifying, by checking that the appropriate entries have been made on the permit, that all tests specified by the permit have been conducted and that all procedures and equipment specified by the permit are in place before endorsing the permit and allowing entry to begin. The supervisor’s signature on the permit is a formal declaration that safety readiness has been achieved.
- Overseeing the entry operations to ensure they remain consistent with the entry permit and that acceptable entry conditions are maintained.
- Terminating the entry and canceling the entry permit when the entry operations covered by the permit have been completed, or when a condition that is not allowed under the entry permit arises in or near the space.
- Verifying that rescue services are available and that the means for summoning them are operable.
- Removing unauthorized individuals who enter or attempt to enter the permit space during entry operations.
An entry supervisor may also serve as an attendant or as an authorized entrant, as long as that person is trained and equipped as required for each role they fill, and provided these additional duties do not interfere with their primary responsibilities as a supervisor. This team structure creates an interdependent system where a failure in one role can compromise the safety of the entire operation.
B. Communication Protocols: Lifelines in Confined Spaces
Clear, reliable, and continuous communication between personnel inside and outside a confined space is essential for routine monitoring of conditions and vital for an effective emergency response. The employer’s permit space program must establish specific communication procedures to be used by authorized entrants and attendants.
Attendants are required to maintain continuous communication with entrants throughout the entry [ (for Safe Work Australia), ]. This communication can be achieved through various means, including visual contact, voice, telephone, or, most commonly, two-way radios. Entrants, in turn, must communicate their status, any recognized hazards, or warning signs to the attendant.
The communication equipment selected must be:
- Reliable and suitable for the specific environment. For instance, in potentially flammable atmospheres, all electronic equipment, including radios, must be intrinsically safe to prevent ignition. Using non-intrinsically safe equipment in such environments can be catastrophic.
- Hands-free in operation, if possible, to allow entrants and attendants to perform their duties without being encumbered.
- Wireless systems are often preferred to reduce the risk of entanglement from cables.
- Full-duplex systems, which allow all parties to talk and listen simultaneously (like a telephone call), are advantageous as they prevent messages from being missed if someone is already transmitting.
- Independently powered (e.g., battery-operated) to ensure communication is not lost if facility power fails.
- Integrated with hearing protection if used in high-noise environments, to ensure messages can be clearly heard.
Examples of intrinsically safe two-way radios suitable for confined space use include various models from manufacturers like Hytera (e.g., PNC460U, HP79XEx series, PT890Ex, UL913 certified models ), Motorola (e.g., Evolve IS model ), Kenwood (e.g., NX-P series IS models ), and ICOM (e.g., F52DUL, F62DUL ). The choice of equipment must be part of the risk assessment, considering factors like signal penetration through structures and potential interference. Continuous communication is more than just having functional equipment; it involves an active and regular exchange of information, including check-ins, acknowledgments, and immediate reporting of any changes or concerns from either the entrant or the attendant. A silent radio does not confirm safety.
Emergency communication procedures must be clearly defined, including how to summon rescue services (e.g., specific personnel to contact, dedicated emergency numbers, radio channels). The attendant is typically responsible for initiating the call for rescue. Evacuation alarms or signals must also be established and understood by all personnel.
C. Emergency Rescue: Planning and Execution
OSHA places a strong emphasis on emergency preparedness, requiring employers to ensure that adequate rescue services are available and capable of responding effectively before any entry into a permit-required confined space occurs. This is critical because self-rescue may not always be possible, and improperly attempted rescues by untrained individuals are a major cause of multiple fatalities in confined space incidents—often, would-be rescuers become additional victims.
Employer Duties for Rescue are comprehensive :
- Develop and implement written procedures for summoning rescue and emergency services, for rescuing entrants from permit spaces, for providing necessary emergency medical services to rescued employees, and for preventing unauthorized personnel from attempting rescues.
- Evaluate prospective rescue services (whether in-house or external) for their ability to respond in a timely manner appropriate to the identified hazards and for their proficiency with rescue-related tasks and equipment specific to the types of permit spaces on site.
- Select a rescue team or service that has the capability to reach victim(s) within a timeframe appropriate for the permit space hazard(s) and is adequately equipped and proficient in performing the necessary rescue services.
- Inform the designated rescue team or service of all potential hazards they may confront when called to perform a rescue at the site.
- Provide the rescue team or service with access to all permit spaces from which rescue may be necessary, enabling them to develop appropriate rescue plans and practice rescue operations.
Rescue Team Requirements and Responsibilities are also clearly defined :
- The rescue team must be available to respond while authorized entrants are inside a permit space.
- Team members must be properly trained in their assigned rescue duties, the correct use of PPE (including respirators like SCBAs), and rescue equipment. At least one member of the rescue team must hold current certification in basic first-aid and cardiopulmonary resuscitation (CPR).
- The team must practice making permit space rescues at least once every 12 months. These practice sessions should involve simulated rescue operations where dummies, manikins, or actual persons are removed from the actual permit spaces on site or from representative permit spaces that accurately simulate the opening size, configuration, and accessibility of the employer’s spaces. This ensures skills are maintained and teams are familiar with site-specific challenges.
- Each rescue team member must understand the specific rescue plan for each type of confined space they may be called to enter.
A Rescue Plan must be developed prior to any entry and should be space-specific, as a generic plan is insufficient. It should outline:
- Specific procedures for entry, rescue, and recovery.
- Communication protocols during the rescue.
- A list of all necessary rescue equipment.
- Methods for addressing the specific hazards of the space. If an employer relies on an off-site service like a local fire department (911), they cannot simply assume these services are prepared for confined space rescue. The employer has a duty to evaluate the service’s capability, including their equipment, response time, training for the specific site hazards, and their willingness to visit the site for familiarization and joint training exercises. If these criteria are not met, the employer must arrange for an alternative, capable rescue service.
Retrieval Systems are mandated by OSHA to facilitate non-entry rescue whenever an authorized entrant enters a permit space, unless the employer can demonstrate that the use of such equipment would increase the overall risk of entry or would not contribute to the rescue of the entrant. Non-entry rescue is always the preferred method as it avoids sending more personnel into a potentially hazardous environment. These systems typically involve:
- The entrant wearing a full-body or chest harness.
- A retrieval line attached to the harness (at the center of the back near shoulder level, above the head, or another point allowing for successful removal).
- The other end of the retrieval line secured to a mechanical device (such as a winch or hoist mounted on a tripod) or a fixed anchor point outside the space.
- A mechanical retrieval device must be available for retrieving personnel from vertical permit spaces more than 5 feet deep.
Specialized Rescue Equipment is essential for safe and effective rescue operations. This includes, but is not limited to: atmospheric monitors, fall protection gear, extraction equipment (tripods, winches, harnesses, ropes, rescue poles, specialized stretchers), SCBAs or SARs for rescuers, explosion-proof lighting, dedicated communication systems, and first aid supplies.
The overarching principle is that in a confined space emergency, time is of the essence. A well-planned, practiced, and properly equipped rescue capability, whether in-house or reliably provided by an external service, is critical to preventing tragic outcomes.
V. Cleaning Techniques for Specific Confined Spaces
The methods and precautions for cleaning confined spaces vary significantly depending on the type of space, the nature of the contaminants, and the cleaning objectives. However, a universal principle is to eliminate the need for entry whenever possible by using remote or automated cleaning methods. If entry is unavoidable, a thorough evaluation of the space—including its dimensions, entry/exit points, internal configuration, drains, construction materials, and any unusual requirements (e.g., specific hygiene standards for food industry applications)—must precede any cleaning activity. Key factors influencing contaminant removal include the mechanical action applied (such as pressure and volume of cleaning media), contact time, the use of chemical cleaning agents, and temperature. The materials to be cleaned must also be assessed for their properties: hazardous or non-hazardous, flammable, corrosive, or reactive with cleaning agents.
A. Tanks and Vessels: Addressing Residues and Contaminants
Storage tanks and process vessels are commonly encountered confined spaces in industries such as chemical manufacturing, petroleum refining, food and beverage processing, and pharmaceuticals. They may contain a wide variety of residues, including hazardous chemicals, fuel oils, food products, paints, sludges, and volatile organic compounds (VOCs). Cleaning is often required for product changeovers, internal inspections, repairs, or to remove built-up contamination that could affect product quality or operational efficiency. Industries like pharmaceuticals and paint manufacturing often have extremely stringent cleaning requirements, demanding 100% repeatable and consistent cleaning to avoid cross-contamination.
Cleaning Techniques:
- Non-Entry (Automated/Remote) Methods (Preferred): Driven by both safety concerns and the high costs associated with manual entry, there is a significant trend towards automated tank cleaning systems. These methods reduce or eliminate the need for personnel to enter the hazardous environment. Examples include:
- Permanently fixed spray nozzles or Clean-In-Place (CIP) systems: Integrated into the tank design for regular cleaning cycles.
- Mobile tank cleaning devices: These are inserted into the tank through existing openings. Examples include 360° rotating high-impact jet heads or robotic tank cleaning machines that can traverse surfaces. These systems can significantly reduce cleaning time, water/chemical consumption, and effluent generation.
- Manual Cleaning (Non-Entry if Possible): If the entire surface to be cleaned is visible from outside and can be reached without bodily entry, manual methods like using long-handled tools or pressure washers with extension wands may be employed. A very basic approach, though less effective for thorough cleaning, involves overflowing the tank with water.
- Manual Entry Cleaning (High-Risk): When entry is unavoidable, it must be performed under strict permit-required confined space procedures. Techniques include:
- Pressure Washing: Using water or cleaning solutions at pressures typically ranging from 1000 to 4000 psi. Specialized applications may use pressures up to 10,000 or 15,000 psi, but these are operated only by highly trained specialists due to the increased risks.
- Scraping, Wiping, and Squeegeeing: For removing stubborn residues or ensuring surfaces are dry.
- Chemical Cleaning: Applying solvents, degreasers, detergents, acids, or caustics to dissolve or loosen contaminants. Extreme care is needed to ensure chemical compatibility with the tank material and any remaining residues to prevent dangerous reactions.
- Steam Cleaning: Effective for sterilizing surfaces and removing certain types of greasy or oily residues.
- Ultra-High Pressure Waterjetting (Hydroblasting): Used for removing very tenacious or baked-on contaminants. This method requires a careful assessment of the tank’s structural integrity to ensure it can withstand the powerful shearing forces.
Specific Safety Considerations for Tank Cleaning:
- Thorough isolation (LOTO) of all inlet/outlet lines, mixers, and other energy sources is paramount.
- Continuous atmospheric monitoring for oxygen levels, flammable vapors (from residues or cleaning agents), and toxic gases is essential.
- Adequate ventilation must be provided, especially when using volatile cleaning chemicals.
- Appropriate chemical-resistant PPE, including respiratory protection, gloves, suits, and eye/face protection, must be selected based on the specific chemicals involved.
- For certain industries (e.g., pharmaceutical, food), the cleaning process itself must be validated to ensure no harmful residues remain, making the cleaning a quality-critical operation rather than just a labor task.
B. Pits, Sumps, and Trenches: Sludge and Debris Removal
Pits (such as sump pits, elevator pits, or excavation pits) and trenches are common in many industrial, commercial, and construction settings. They often accumulate water, sludge, oil, soil sediment, leaves, industrial waste, and other debris. Cleaning is necessary to maintain proper drainage, prevent pump clogs or failures, remove hazardous contaminants, and prepare the space for inspection or repair work.
Cleaning Techniques:
- Dewatering: The first step is usually to remove any standing liquid. This can be done using:
- Portable pumps or wet/dry shop vacuums for smaller sumps.
- Larger industrial pumps or vacuum trucks for more substantial pits and trenches.
- Solids Removal: Once dewatered, accumulated solids and sludge are removed.
- Vacuum Excavation: Vacuum trucks can be highly effective for removing sludges and semi-solid materials without requiring entry.
- Manual Removal: If entry is necessary, personnel may use shovels, buckets, and scrapers to remove remaining solids. This requires full adherence to PRCS procedures.
- Pressure Washing: After bulk material removal, pressure washing can be used to clean the walls, floors, and any equipment (like sump pumps) within the space.
- Disinfection: For some applications, such as sanitary sumps, a disinfectant like bleach or a specialized sump pump cleaner may be added to the water (following manufacturer’s instructions) to sanitize the area after cleaning.
Specific Safety Considerations for Pits, Sumps, and Trenches:
- Engulfment: Significant risk from water, sludge, or collapsing trench walls (if applicable).
- Atmospheric Hazards: Potential for oxygen deficiency, or the presence of toxic gases like hydrogen sulfide (H$_{2}$S) or methane (CH$_{4}$) from decomposing organic matter, or vapors from spilled chemicals. The risk profile can shift during cleaning; for example, an initial atmospheric hazard might be mitigated by pumping, but then engulfment or slip/trip hazards become more prominent during manual solids removal.
- Slip, Trip, and Fall Hazards: Surfaces are often wet, slippery, and uneven.
- LOTO: Any pumps, alarms, or other connected equipment must be properly locked and tagged out before entry.
- Structural Integrity: For trenches, shoring or sloping may be required to prevent collapse. Thorough cleaning is essential, as incomplete removal of debris from sumps or pits can lead to rapid re-contamination or system failures (e.g., pump clogging), negating the cleaning effort and potentially causing further damage or operational issues.
C. Manholes and Vaults (Utility, Electrical, Communication): Access and Cleaning Strategies
Manholes and underground vaults serve as access points to a wide range of utility systems, including sewers, steam and chilled water lines, electrical distribution networks, and telecommunication cables. Cleaning these spaces is often necessary to maintain access for inspection and repair, ensure the functionality of the utilities they house, and remove obstructions or contaminants. The specific cleaning approach and primary hazards vary drastically depending on the type of utility.
Common Contents/Residues: Silt, mud, gravel, leaves, roots, construction debris, concrete waste, animal nests, and water are common in many types of manholes and vaults. Specific types may also contain:
- Sewer Manholes: Sewage, organic sludge, grease, and potentially hazardous gases like H$_{2}$S, CH$_{4}$, and CO, along with oxygen-deficient atmospheres.
- Electrical Vaults: Water, mud, debris, and potentially oil from leaking transformers or CO from nearby combustion sources if ventilation is poor. The primary hazard is electrical.
- Communication Vaults/Manholes: Similar debris, but with a critical need to protect sensitive cables and connections.
- Steam/Chilled Water Vaults: Water, insulation debris, and potential for thermal hazards. Asbestos may be present in older manholes and vaults containing insulated pipes.
Cleaning Techniques:
- Debris Removal:
- Manual removal of larger items using hooks or grabbers from the surface if possible.
- Vacuum excavation (e.g., using a vacuum truck) is highly effective for removing accumulated soil, sediment, and smaller debris from the bottom of manholes and vaults.
- Pressure Washing: Often used to clean the walls, benches, and internal structures of manholes and vaults after bulk debris removal.
- Rodding/Jetting: For connected pipes (e.g., sewers), cleaning the manhole may be part of a larger pipe cleaning operation using high-pressure water jetting or mechanical rodding.
- Specialized Procedures for Electrical Vaults: Extreme caution is paramount. All electrical equipment must be de-energized and subjected to rigorous LOTO procedures before any cleaning begins. Cleaning methods must avoid damaging sensitive electrical components. While pressure washing may be used in some de-energized scenarios , the combination of water and electrical equipment demands expert protocols and thorough drying/verification before re-energization.
- Specialized Procedures for Communication Manholes/Vaults: The focus is on removing debris without damaging delicate fiber optic or copper cables and connections. Gentle cleaning methods may be required.
- Inspection and Testing: Cleaning is often a precursor to inspection and testing. For example, sanitary sewer manholes may undergo visual inspection for structural integrity and infiltration, followed by vacuum or exfiltration testing after cleaning is complete.
Specific Safety Considerations for Manholes and Vaults:
- Atmospheric Hazards: Critical for sewer manholes (H$_{2}$S, CH$_{4}$, CO, oxygen deficiency). Also a concern in other types, especially if organic matter is present or if there’s ingress from external sources. details specific manhole entry procedures including pre-entry and continuous gas monitoring, and forced ventilation.
- Electrical Hazards: The dominant hazard in electrical vaults. LOTO is non-negotiable.
- Engulfment: Possible in deep manholes or vaults if they are flooded or contain significant loose material.
- Falling Objects: Debris or tools from the surface.
- LOTO: Essential for all relevant utilities (electrical, steam, water) and any mechanical equipment within the space.
- Structural Integrity: Older manholes or vaults may have deteriorated structures.
- Access/Egress: Manhole openings are typically restrictive. The cleaning of manholes and vaults is often an enabling step for other critical asset management activities, such as inspections, repairs, or upgrades to the utility systems they serve.
D. Ductwork and Enclosed Areas: Dust, Debris, and Contaminant Control
HVAC (Heating, Ventilation, and Air Conditioning) ductwork, industrial ventilation systems, and other enclosed pathways can accumulate significant amounts of dust, lint, mold spores, fungi, bacteria, allergens, construction debris, and other contaminants over time. Cleaning these confined spaces is performed to improve indoor air quality, remove allergens and microbial contaminants, maintain HVAC system efficiency, and in some cases (like dryer exhaust ducts or industrial dust collection systems), reduce fire or explosion risks.
Cleaning Techniques: The primary approach for duct cleaning involves a “push-pull” method: dislodging contaminants from the duct surfaces and simultaneously collecting them with a powerful vacuum system to prevent their spread into the occupied space.
- Access: Cleaning is performed by accessing the duct system through existing vents, registers, and diffusers, or by creating temporary access openings. These openings must be properly sealed after cleaning is completed.
- Negative Air Pressure: A large, powerful vacuum collection device, typically equipped with HEPA (High-Efficiency Particulate Air) filters, is connected to the ductwork to create strong negative pressure (e.g., 4000 CFM or more). This ensures that all dislodged debris and contaminants are drawn into the collection unit and not released into the building. Truck-mounted vacuums may be used for larger commercial jobs, while portable units are used for areas inaccessible to trucks.
- Agitation Devices: Various tools are used to dislodge contaminants from the interior surfaces of the ductwork:
- Rotary Brushes: Flexible shafts with spinning brushes of different sizes and materials (e.g., soft nylon for lined ducts, stiffer nylon or silica carbide for unlined metal ducts) are inserted into the ducts to scrub the surfaces.
- Air Whips and Compressed Air Nozzles: These tools use blasts of compressed air to dislodge debris, particularly effective in corners, bends, and on uneven surfaces where brushes may not reach effectively.
- Manual Contact Vacuuming: For accessible components like air handlers, plenums, coils, drip pans, and registers, direct vacuuming with HEPA-filtered vacuums is employed.
- Cleaning Vent Covers and Registers: These components are typically removed, cleaned separately (e.g., washed or vacuumed), and then reinstalled.
- System Components: Beyond the ducts themselves, other HVAC system components like air handling units, coils, and drip pans should also be cleaned as part of a comprehensive service.
Specific Safety Considerations for Ductwork Cleaning:
- Respiratory Protection: Essential due to the high likelihood of aerosolizing dust, mold spores, and other particulates. N95 masks or more protective respirators may be required depending on the assessed level of contamination.
- Eye Protection and Gloves: To protect against dust, debris, and potential contact with sharp edges inside ductwork.
- Contaminant Control: Ensuring that the negative air system is functioning correctly and that all access points are sealed is crucial to prevent the spread of contaminants into the building.
- LOTO: The HVAC system (fans, air handlers) must be locked and tagged out before commencing cleaning work to prevent accidental startup.
- Working in Awkward Positions: Ductwork is often located in ceilings, crawl spaces, or other restricted areas, requiring work in cramped and awkward postures. The inherent complexity of duct systems, with their many “hard-to-reach areas” such as elbows and bends, means that specialized tools and techniques are essential for a thorough cleaning. A superficial cleaning of only easily accessible parts is generally insufficient to address widespread contamination.
VI. The Professional Imperative: Why Expert Services are Non-Negotiable for Confined Space Cleaning
While the allure of handling cleaning tasks in-house might seem like a cost-saving measure, the unique and severe dangers associated with confined spaces make professional intervention not just advisable, but imperative. The risks of injury, illness, fatality, regulatory non-compliance, and significant financial liability far outweigh any perceived savings from a Do-It-Yourself (DIY) approach. Entrusting confined space cleaning to qualified, certified, and experienced professional services is a critical investment in safety, compliance, and operational integrity.
A. Navigating Complex Regulations and Ensuring Compliance
Confined space operations are among the most stringently regulated activities in occupational safety. In the U.S., OSHA’s 29 CFR 1910.146 (Permit-Required Confined Spaces) sets forth detailed and legally binding requirements for general industry. Similar comprehensive regulations exist internationally, such as the Confined Spaces Regulations 1997 in the UK and the model Work Health and Safety (WHS) Regulations in Australia.
Professional confined space cleaning companies are deeply familiar with these intricate legal frameworks. Their expertise includes:
- Accurate identification and classification of confined spaces (permit-required vs. non-permit).
- Development and implementation of compliant written permit space programs and entry permits.
- Adherence to mandatory training requirements for all personnel roles (entrants, attendants, supervisors, rescue teams).
- Correct procedures for atmospheric testing, monitoring, and record-keeping.
- Proper implementation of hazard control measures, including isolation (LOTO) and ventilation.
- Understanding of emergency rescue obligations.
Failure to comply with these regulations can result in severe OSHA citations, substantial financial penalties, criminal charges in some jurisdictions, and crippling legal liabilities in the event of an incident. More importantly, non-compliance directly correlates with an increased risk of worker fatalities. Professional services stay abreast of regulatory changes and interpretations, ensuring that cleaning operations are conducted lawfully. The regulations themselves, such as OSHA 1910.146, were developed based on extensive data from past incidents and fatalities.
Adherence to these standards is therefore not merely about avoiding fines, but about implementing a proven system designed to save lives. Furthermore, the “performance-oriented” nature of some standards, like OSHA’s, means they specify what safety outcomes must be achieved but may not detail how to achieve them in every unique circumstance. This necessitates expert interpretation and application, which professionals provide through their specialized experience across diverse confined space scenarios.
B. Access to Specialized Training, Equipment, and Advanced Techniques
Effective and safe confined space cleaning demands a level of specialized training and equipment that is typically beyond the scope and resources of most facilities that do not specialize in such work.
- Specialized Training: Professional teams undergo rigorous and recurring training specific to confined space hazards and operations. This includes :
- Hazard recognition and risk assessment.
- Atmospheric testing and monitor calibration/use.
- Selection, use, and maintenance of PPE, including advanced respiratory protection like SCBAs.
- Lockout/Tagout procedures.
- Emergency response and rescue techniques (non-entry and entry).
- First aid and CPR.
- Specific cleaning methodologies for different types of contaminants and spaces.
- Role-specific training for entrants, attendants, entry supervisors, and rescue personnel.
- Specialized Equipment: Professionals invest in, maintain, and correctly deploy a wide array of specialized equipment, much of which is expensive and requires regular certification or calibration :
- Calibrated multi-gas atmospheric monitors (often costing over $1,000 each ).
- Forced air ventilation systems (blowers, ducting, intrinsically safe models for flammable environments).
- A comprehensive range of PPE, including SCBAs/SARs, chemical-resistant suits, and fall protection harnesses.
- Non-entry cleaning technologies, such as automated tank cleaning systems or robotic devices.
- Rescue equipment, including tripods, winches, retrieval lines, and specialized stretchers (rescue kits can cost thousands of dollars ).
- Industrial-grade cleaning tools like high-pressure washers, explosion-proof vacuums, and specialized agitation devices. The cost of acquiring, maintaining, calibrating, and certifying this equipment, coupled with the expense of comprehensive and ongoing training for personnel, is often prohibitive for organizations that only require confined space cleaning sporadically.
- Advanced Techniques: Professional services are versed in the latest and most effective cleaning methodologies suitable for diverse contaminants and space configurations. They understand how to perform these tasks safely and efficiently, adapting their approach to the specific challenges presented. This implies a commitment to continuous learning and adoption of new technologies (e.g., drone inspections for initial assessment ) and evolving safety protocols, offering a consistently higher standard of service.
C. Mitigating Extreme Risks: Protecting Lives and Assets
Confined space entry is inherently one of the most dangerous activities in any workplace. Asphyxiation due to hazardous atmospheres (oxygen deficiency, toxic gases, flammable vapors) is a leading cause of death. Engulfment by liquids or flowable solids is another major fatal hazard. Tragically, a significant percentage of confined space fatalities (often cited as high as 60%) are would-be rescuers—colleagues who rush in to help a fallen entrant without proper training, equipment, or a plan, only to become victims themselves.
Professional confined space cleaning services are acutely aware of these extreme risks and are structured to manage them systematically. Their entire operational focus is on identifying, assessing, and controlling these hazards to ensure the cleaning task is executed without incident. This includes having dedicated, trained, and practiced rescue teams and plans in place, which breaks the deadly chain reaction often seen in DIY rescue attempts. An incident in a confined space can have a devastating cascade effect. Protecting assets also extends beyond the immediate confined space; an explosion or uncontrolled chemical release can damage surrounding equipment, contaminate a wider area, and halt facility operations, leading to significant financial losses. Professional cleaning helps prevent such incidents, thereby safeguarding broader business assets and ensuring operational continuity.
D. Efficient and Thorough Cleaning by Experienced Professionals
Beyond the paramount concern of safety, professional cleaning services bring a level of efficiency and thoroughness that is difficult to achieve with in-house, non-specialized teams.
- Experience: Professionals have encountered a wide variety of confined spaces and contaminants, allowing them to quickly identify the most effective and safe cleaning strategies.
- Minimized Downtime: Their expertise and specialized equipment often allow them to complete cleaning tasks more rapidly, returning tanks, silos, vessels, or systems to service faster, which is crucial for production-dependent facilities. This efficiency is not achieved by cutting corners on safety but is rather a byproduct of meticulous planning, well-defined procedures, trained personnel who are proficient in their roles, and having the right tools readily available.
- Thoroughness: A professional, deep clean can prevent future operational problems, such as ongoing corrosion, product contamination from residual materials, or system blockages that might arise from an incomplete DIY job. This proactive thoroughness can save significant costs and operational headaches in the long run, particularly in industries with stringent quality or hygiene standards like food processing or chemical manufacturing.
E. Proper Management of Hazardous Waste Generated During Cleaning
Cleaning confined spaces frequently generates waste materials—such as chemical residues, contaminated sludge, or cleaning solutions—that may be classified as hazardous under environmental regulations. Professional cleaning companies are knowledgeable about and equipped for the proper characterization, containment, labeling, transportation, and disposal of such waste in full compliance with local, state, and federal environmental laws.
This includes understanding the critical first step of waste characterization (often involving laboratory testing) to determine if the waste is hazardous and, if so, its specific hazardous properties, which dictates the legally required disposal method.
The generator of hazardous waste (typically the facility owner) usually bears “cradle-to-grave” liability for its proper management. Engaging a reputable professional cleaning service that correctly handles and documents hazardous waste disposal helps the facility owner manage this significant liability, as the professional service becomes part of the documented chain of custody. Improper disposal of hazardous waste can lead to severe environmental damage, hefty fines, and serious legal repercussions.
F. The High Cost of In-House Attempts: Safety Lapses and Potential Liabilities
While attempting confined space cleaning with an in-house team might appear to offer initial cost savings, the potential financial and human costs of an accident are astronomical and far-reaching. A single confined space incident can lead to:
- Direct Costs: Multiple fatalities or severe injuries, extensive medical expenses, damage to equipment and the facility, and significant regulatory fines.
- Indirect Costs: Lost production and operational downtime, costs associated with incident investigation, hiring and training replacement workers, increases in insurance premiums, legal fees from lawsuits, irreparable damage to the company’s reputation, and severely diminished employee morale.
The investment in professional, certified confined space cleaning services is, therefore, a prudent investment in comprehensive risk mitigation. A “near miss” during a non-compliant DIY attempt should be viewed not as a success, but as a grave warning that critical safety barriers were either absent or failed; a subsequent attempt under similar circumstances could easily prove fatal. Furthermore, facility insurance policies may contain specific exclusions or stringent requirements for high-risk activities like confined space entry.
An incident occurring during a non-compliant DIY cleaning operation could lead to the denial of insurance claims, leaving the company to bear the full, potentially devastating, financial burden. Professional confined space cleaning companies typically carry specialized insurance coverage appropriate for the high-risk nature of their work.
VII. Conclusion: Prioritizing Safety in Confined Space Cleaning
Cleaning operations within confined spaces are unequivocally high-risk endeavors that demand an exceptional level of expertise, specialized equipment, and unwavering adherence to stringent safety regulations. The potential for life-threatening atmospheric hazards, engulfment, entrapment, and other severe physical or chemical injuries makes these tasks unsuitable for untrained or inadequately equipped personnel.
This guide has outlined the critical aspects of confined space cleaning, from understanding the fundamental definitions and regulatory landscape governed by bodies like OSHA, to the meticulous processes of hazard identification, risk assessment, and the implementation of comprehensive safety protocols.
Key elements such as the permit-to-work system, rigorous atmospheric testing, effective forced air ventilation, robust lockout/tagout procedures, and the correct selection and use of personal protective equipment are not merely procedural guidelines but are vital safeguards against catastrophic incidents.
The well-defined roles and responsibilities of the confined space entry team—authorized entrants, attendants, and entry supervisors—along with clear communication protocols and meticulously planned emergency rescue procedures, form the human-centric backbone of any safe operation. Furthermore, the cleaning techniques themselves must be tailored to the specific type of confined space, whether it be a tank, pit, manhole, or ductwork, always prioritizing methods that eliminate or reduce the need for human entry.
Ultimately, the complexities and inherent dangers of confined space cleaning underscore a critical conclusion: such tasks should be entrusted to professional, certified, and experienced confined space cleaning services. These specialists possess the in-depth knowledge of regulations, the specialized training and equipment, and the proven methodologies to perform these hazardous jobs safely and effectively.
Attempting to conduct confined space cleaning in-house without the requisite expertise and resources exposes workers to unacceptable risks and organizations to severe legal, financial, and reputational consequences.
Choosing professional services is not an admission of inadequacy but a demonstration of a profound commitment to worker safety, regulatory compliance, and operational excellence. The investment in expert confined space cleaning is an investment in preventing tragedies, protecting assets, and ensuring peace of mind. When faced with the need to clean a confined space, the safest and most responsible course of action is to engage those who are explicitly trained and equipped to navigate these danger zones.